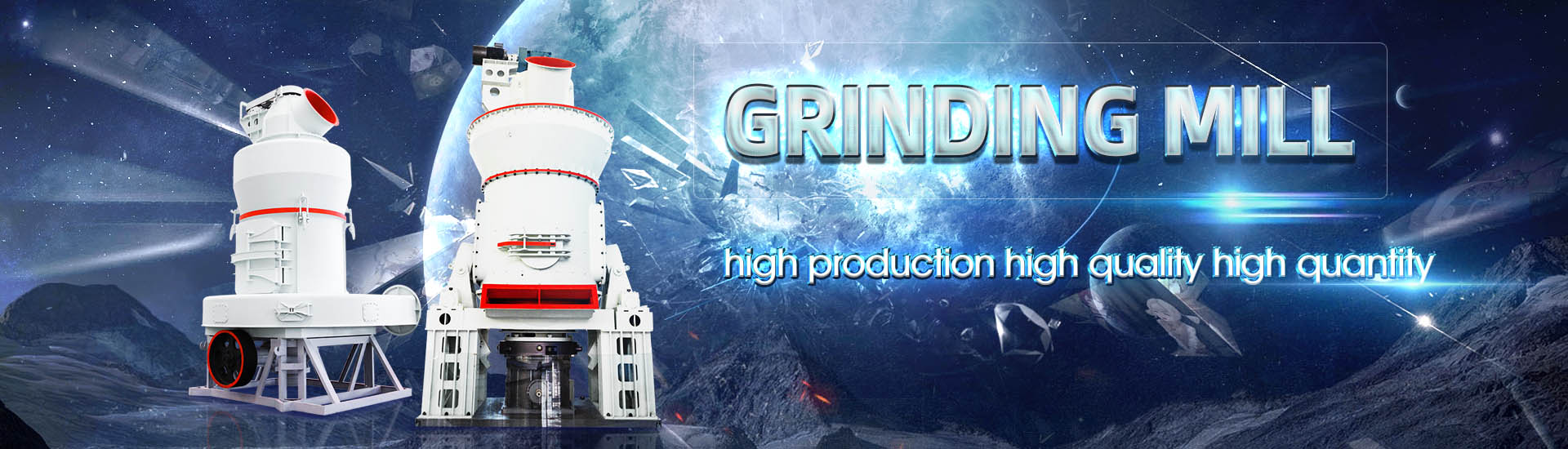
The function of mdd ore mill
.jpg)
UNDErsTaNDINg MINE TO MILL 911 Metallurgist
Mine to Mill is an operating strategy for mining operations to enhance the performance of mining and downstream processing activities Correctly implemented, Mine to Mill will provide: >> True integration of geology, mining and processing functions across an operation with intangible 2023年11月27日 Determining lost gold production based on the ore inputs into the mill ensures an accurate measurement of the time period when operations are impacted including any applicable waiting period, deductible, or daily valueRecognition of Lost Production at a Gold Mine MDDThis study was aimed at increasing mine output and profit margin by controlling fragment size distribution, managing grade variability, and ensuring that broken ore reaches the mill plant timeously Movement of rock, ore loss, and dilution Monitoring ore loss and dilution for minetomill 2016年2月1日 The purpose of this study is to understand how ore loss and dilution affect the mine call factor, with the aim of subsequently improving the Monitoring ore loss and dilution for minetomill
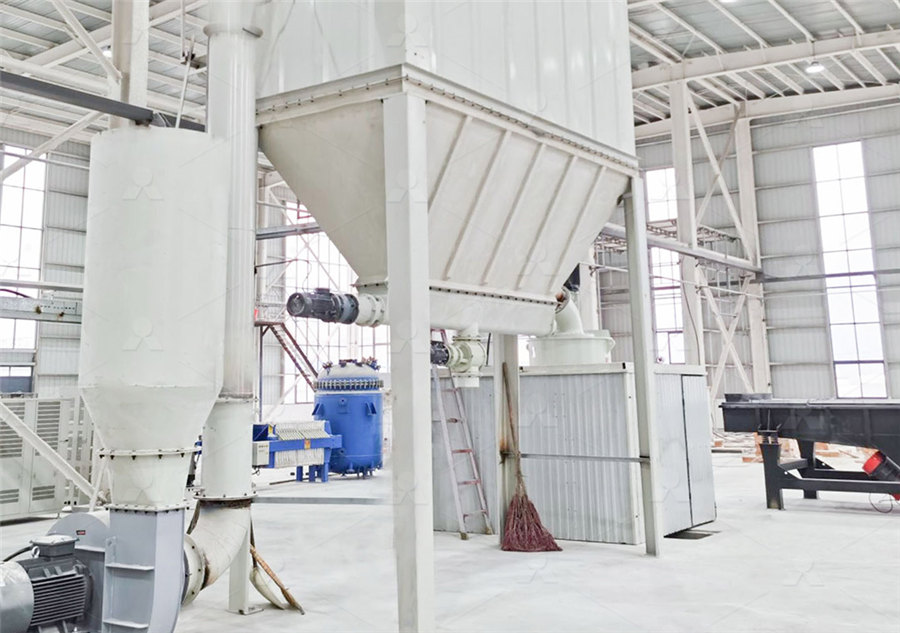
A Review of the Grinding Media in Ball Mills for Mineral Processing
2023年10月27日 Grinding media play an important role in the comminution of mineral ores in these mills This work reviews the application of balls in mineral processing as a function of the 2021年4月19日 Regarding this background, this article describes the feasibility of mine to mill optimization from three aspects: (1) different energy efficiencies between drillingblasting and(PDF) Feasibility and necessity of mine to mill2022年9月1日 The purpose of ore blending is simply to provide uniform mill feed which aids in improving production efficiency and reducing production cost Metso Minerals (2022) Towards waterless operations from mine to mill ScienceDirectA simple and novel nonlinear model of a runofmine ore grinding mill circuit, developed for process control and estimation purposes, is validated The model makes use of the minimum Analysis and validation of a runofmine ore grinding mill circuit
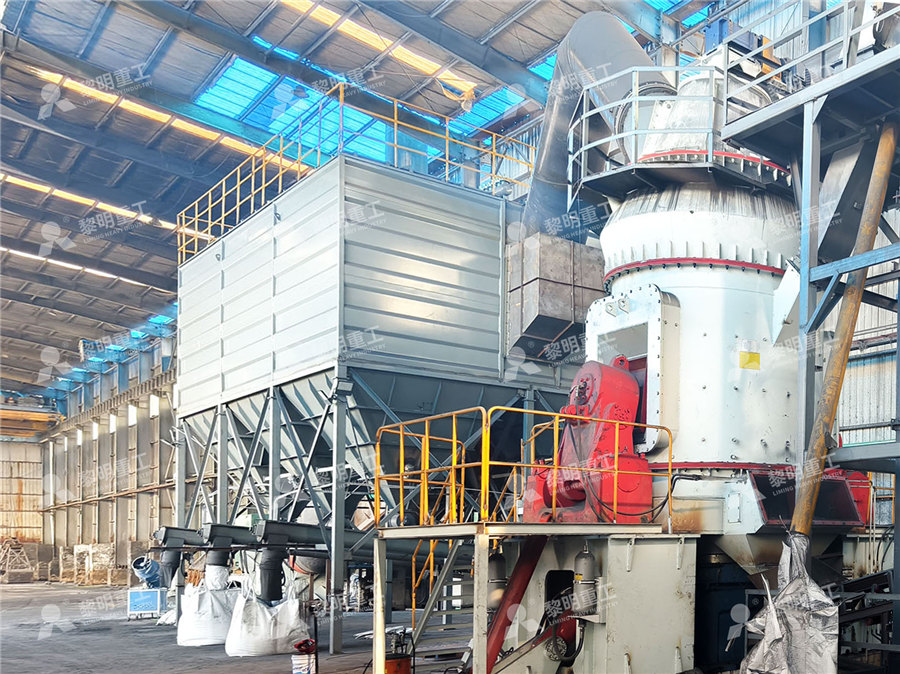
Ore Grinding SpringerLink
2023年7月20日 Ore grinding is a process to further reduce and disperse the ore particle size In the mineral processing industry, ore grinding is the particle size preparation before the 2020年12月3日 This study is conducted with the aim of investigating the efficiency of open and closedcircuit molybdenite ore comminution processes (primary and secondary mill, A process mineralogy approach to study the efficiency of milling However, ore below the pay limit adds variation to the mill grade as increased mill throughput will be required to make up for the loss of gold, and that impacts on the recovery in the plant It is against these perspectives and findings of this Monitoring ore loss and dilution for minetomill Selection andbreakage functions are lumped into a steadystate mill matrix This steadystatemill matrix is multiplied (on the right side) by the feed matrix which describes the particle size distribution entering the mill This multiplication yields the mill product matrix which describes the size distribution of the particles exiting the millAssessment of the Functionality of Selection and Breakage Rate
.jpg)
Winning the Metal: Ore Mills of the West Western
It is almost impossible to describe, let alone do justice to, the variety of processes that have been used to mill ore The importance of mills cannot be understated since no money was made until the minerals were stripped of their metal 2016年2月1日 The purpose of this study is to understand how ore loss and dilution affect the mine call factor, with the aim of subsequently improving the quality of ore mined and fed to the millMonitoring ore loss and dilution for minetomill integration in Ball mill = coarse particles (in the plant ball mill) grinding efficiency Ore grindability (in the lab ball mill) The units of "ball mill grinding efficiency" will be covered in detail in the first part of the module Alternatively, we can say that: Specific grinding rate = Ball mill x Ore grindabilityMODULE #5: FUNCTIONAL PERFOMANCE OF BALL MILLING2017年9月1日 The transitional change on the implementation of iso 14001: 2015 in Copper Ore Mill Case study September 2017; Journal of Ecological Engineering 18(5) functions and physical The transitional change on the implementation of iso 14001:
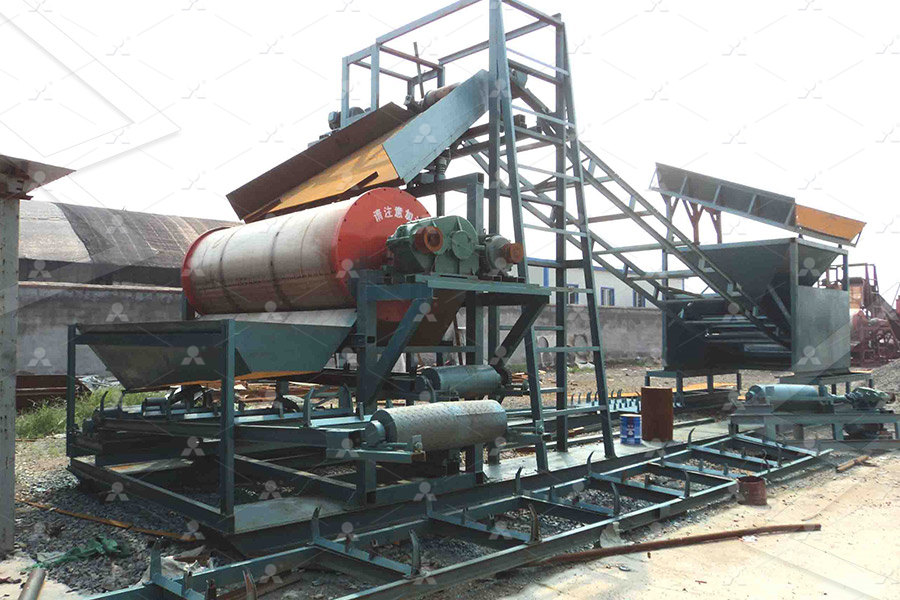
Effect of ball and feed particle size distribution on the milling
2018年6月1日 A number of researchers (Deniz, 2012; Bwalya et al, 2014; Petrakis et al, 2016) carried out studies about the effect of feed particle size and grinding media size on the grinding kinetics of different oresKhumalo et al, 2006 postulated that generally larger sized grinding media would break larger particles quicker but a finer product would be obtained by use of Technology and technics of ore preparation processes 5 The ore pretreatment flow charts in use at most highproductive processing plants designed in the last decade are based on semiautogenous (SAG) milling and involve as a rule primary wet autogenous mill (WAM) and a series of ball mills WAM is customary chosen either based on examinationCALCULATION OF THE REQUIRED SEMIAUTOGENOUS MILL 2023年5月3日 Center Periphery Discharging Rod Mill The center periphery discharging rod mill feeds the material through the journals at both ends of the mill, and discharges the grinding products through the circular orifice in the middle of the cylinder (Fig 3)Ore pulp is characterized by short stroke, steep slope, and it can be coarsely ground with fewer fine particles and low Rod Mill SpringerLink2011年2月1日 The overflow ball mill utilized in the sampling survey has an inside diameter of 7312 m and length of 96 m and is run in open circuit It is used in secondary grinding of UG2 Platinum ore The mill is equipped with 44 rubber lifter bars with height of 100 mm Forged steel balls of diameter 40 mm are used asModeling the RTD of an industrial overflow ball mill as a function
.jpg)
INVESTIGATION OF EFFECTS OF GRINDING MEDIA
2015年10月20日 The ball mill is a rotating cylindrical vessel with grinding media inside, which is responsible for breaking the ore particles Grinding media play an important role in the comminution of mineral 2024年5月27日 Ball mills are crucial for grinding and pulverising ores and other materials in this article, we unpack the function of Ball Mills, introducing MechProTech’s Ball Mill OEM equipment The General Function of Ball Mills Ball Mills in the Mineral Processing Industry2018年10月1日 The degree of fragmentation or the breakage function of an ore is described by ‘t nfamily’ of curves A detailed description of this approach is given by Narayanan and Whiten WJ, 1983 Breakage characteristics of ores for ball mill modelling In: Proceedings AusIMM, vol 286, June, pp 31–39 Google Scholar Pauw and Quantifying variability of ore breakage by impact ScienceDirect2021年1月22日 GGS function was also preferred to RRB function in some crushing equipment, such as jaw and cone crusher In recent years, Swebrec function, a more complicated mathematical function, has been introduced to fit the fine material, which overcomes the problem that RRB function was highly dependent on the investigated data set [[11], [12], [13], [14]]Impact of ball filling rate and stirrer tip speed on milling iron ore
.jpg)
Predicting the effect of operating and design variables in
2021年7月1日 Vertical stirred mills may be classified according to the speed of the stirrer in two groups: gravityinduced or fluidized mills [[1], [2], [3]]In the gravityinduced mills, the stirrer, generally of the screw type, turns so that the grinding charge exhibits an ascending convective motion at the center, descending from the edges of the screw and close to the mill shell, owing 2017年8月29日 Not necessarily Amortization of a mill at a site may be on a unit of production basis, particularly if the ore body size is clearly known But are we entitled to take a saving related to mill depreciation against the revenue from the production shortfall Probably notMining BI Insurance and the Principle of Indemnity MDD2015年4月9日 Typically this type of mill can deliver a product with a fineness of less than 01 mm Testing of material is needed before hand to determine the suitability of the ore for processing in an autogenous mill The rod mill (Fig 1) is a tumbling mill which is having a large percentage of its volume (30 % to 40 %) loaded with steel rodsGrinding Mills and Their Types – IspatGuruThe Millstone is a more basic equivalent of the Crushing Wheels, and is most likely the first of the two that the Player will construct It is capable of applying milling recipes to any valid items inserted from above There are 2 variables that effect the processing speed of the Millstone: RPM and recipe duration The recipe duration is a number assigned to each recipe to determine is Millstone Create Wiki Fandom
.jpg)
Unlocking the Secrets of Gold Ore Mill: A Comprehensive Guide
Definition and Overview of Gold Ore Mill A gold ore mill is a facility where the raw mined goldbearing ore is crushed into fine particles through various mechanical means These particles are then further processed to extract the valuable metal within them Gold ore mills have evolved over time to improve efficiency and increase recovery rateswater that drove the mill to be managed (Figure 1A) In other cases the mill stood on a natural watercourse, modified with a dam and a bypass channel (Figure 1B) Sometimes a weir was constructed to direct water into the mill race/ bypass channel The millstream had three parts: the millrace above the mill, the wheelrace flowingMills Historic EnglandLet us consider the transfer function of the object under study to be the firstorder relaxation circuit звеном (Fig 1) The input value Х(t) conditioning mill capacity is a controlled variable which is correlated with the mill charge Р(t) Input product sorting results in part of the product being returned for regrindingAdaptive control of ore mill charge1983年6月1日 Breakage characteristics for ores for ball mill modelling June 1983; Authors: S This function can be incorporated into the existing comminution modelling so that the accuracy of the mineral Breakage characteristics for ores for ball mill modelling
.jpg)
Hybrid nonlinear model predictive control of a runofmine ore
The fraction of the mill volume lled with water, ore and steel balls is represented by J T The mill is the most power intensive element in a grinding mill circuit and the power draw of the mill motor is represented by P mill [4] The slurry mixture of ground ore and water in the mill is discharged into the sump through an enddischargeYou’ll find the glass manufacturing plant under Processing Buildings right beside the ore grinding mill Your delivery trucks will then start to supply your glass manufacturing plant with ore to turn into glass A similar but more productive building, the fibreglass plant, is unlocked at level plete Ore Industry Area Guide for Cities: SkylinesSelection function, breakage function, mill critical speed, Platinum ore, milling kinetics, breakage rate iii Dedication This work is dedicated to my sweet family: Figure 28 Specifics rate of breakage of clinker ore as a function of feed size for various fraction of critical speedEFFECTS OF MILL ROTATIONAL SPEED ON THE BATCH GRINDING 2015年6月19日 The basic parameters used in ball mill design (power calculations), rod mill or any tumbling mill sizing are; material to be ground, characteristics, Bond Work Index, bulk density, specific density, desired mill tonnage capacity DTPH, operating % solids or pulp density, feed size as F80 and maximum ‘chunk size’, product size as P80 and maximum and finally the type of Ball Mill Design/Power Calculation 911Metallurgist
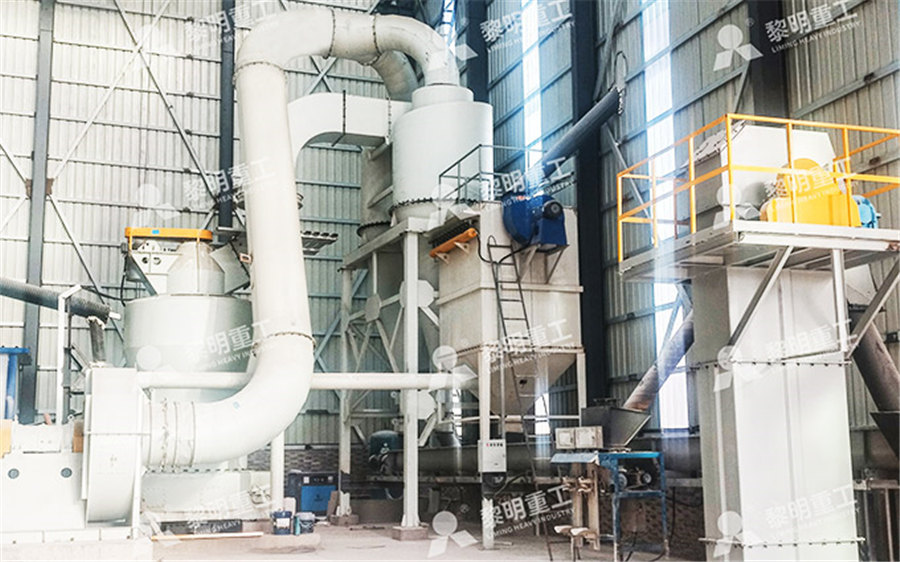
Assessing the dependency of selection function parameters with
2019年10月1日 The copper ore was found to be normalisable for either mill; in other words, the breakage function parameters (β, γ, and Φ) did not significantly change in value with milling conditions and mill design The selection function parameters, on the other hand, led to diverging patterns: two parameters (α and Λ) were not affected by mill design 2023年10月27日 The ball mill is a rotating cylindrical vessel with grinding media inside, which is responsible for breaking the ore particles Grinding media play an important role in the comminution of mineral ores in these mills This work reviews the application of balls in mineral processing as a function of the materials used to manufacture them and the mass loss, as A Review of the Grinding Media in Ball Mills for Mineral Processing 2017年10月1日 The effect of particle size on the kinetics of gold cyanidation was investigated for a gold ore from the Abitibi region (Canada) Six size fractions representative of the plant operation were used (PDF) Determining optimum wet milling and leaching parameters for 3 BALL MILL MODEL The population balance model may be expressed by Equation (1): > @ ¦ i1 1 i b ij m j j i j i S Ht dt d H m t (1) where: S i (t) is the size discretized selection function for Population balance model approach to ball mill optimization in iron ore
.jpg)
Functional Performance of Ball Milling Circuits AusIMM
It is normalised based upon the ore resistance to breakage, so it provides feedback about the health' of the milling process under varying operating conditions and ore types Mill grinding efficiency is measured at the same time as CSE through circuit samplingFunctional performance analysis combines CSE and mill grinding efficiency to provide 2024年4月26日 Learn about the key stages in iron ore processing, including crushing, screening, and beneficiation techniques for optimal resource utilization +86 ; xlyin@ The choice of grinding mill depends on factors Iron Ore Processing: From Extraction to ManufacturingOre from the open pit went to the crusher and mill, while lowergrade ore went into a stockpile for future use Ore from both the open pit and underground mine went to the mill for processing At the mill, the ore went through several Precious Metals Mining Loss Calculation MDDThe primary function of gold mining ball mills is to grind and crush ore materials to a fine powder This powder is then processed to extract the gold through various techniques such as cyanidation or flotation The ball mill contains a hollow cylinder and a rotating shaft, with the grinding balls mounted on the shaftThe significance of gold mining ball mills in the modern mining
.jpg)
Control of ball mill operation depending on ball load and ore
Size, hardness and density of ore particles according to M M Protodiakonov scale It is a system that can measure ore content on 4 inputs and includes realtime measurement of pulp density The rate at which fresh ore from the belt conveyor enters the mill From the electromagnetic measurement of the consumption water coming to the millBall mill for spodumene lepidolite processing: Process The ball mill is a key equipment for the spodumene lepidolite processing It is mainly used to grind the ore into small pieces and to remove the impurities The ball mill can also be used to preparing other minerals for market Ball mill for spodumene lepidolite processing: FeaturesWhat is the function of ball mill for spodumene lepidolite The parts of a ball mill Ball mills are used to grind various ores and other materials into a fine powder In order for the mill to function properly, it requires accurate and consistent grinding There are a number of factors that affect the grinding performance of ball mills, some of which are discussed belowFactors affecting ores grinding performance in ball millsThe rod mill is another type of grinding mill used in the copper ore mining process This machine uses steel rods as the grinding media instead of balls, which are commonly used in ball mills The rods grind the ore by tumbling within the mill, similar to the action of a rotating drumUnderstanding the SAG Mill in Copper Ore Mining Process
.jpg)
Optimization of Solids Concentration in Iron Ore Ball Milling
E, termed the specific selection function for the ith size interval, is considered to be independent of mill design and operating conditions [9], H is the mill hold up, and P is the mill power In addition, the breakage functions bij has been demonstrated to be, to a good approximation, invariant with respecting the pdf becomes equivalent to the functional description of the posterior pdf The posterior density function at time t may then be approximated as [13]: p(xtYt) ≈ XNs i=1 wi tδ(xt − x i t) (9) where Ns is the number of particles and {xi t,w i t} Ns i=1 is the set of particles and associated weights These weights are defined to be Dual particle filters for state and parameter estimation with