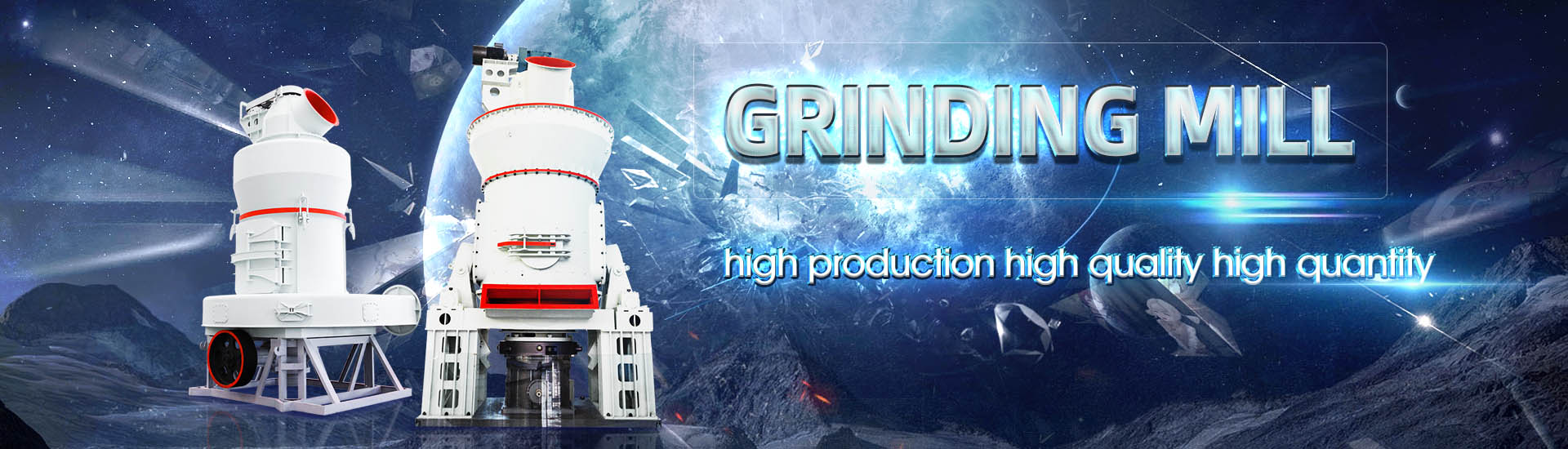
HOME→Autoclaved cement clinker powder making process Autoclaved cement clinker powder making process Autoclaved cement clinker powder making process
Autoclaved cement clinker powder making process Autoclaved cement clinker powder making process Autoclaved cement clinker powder making process
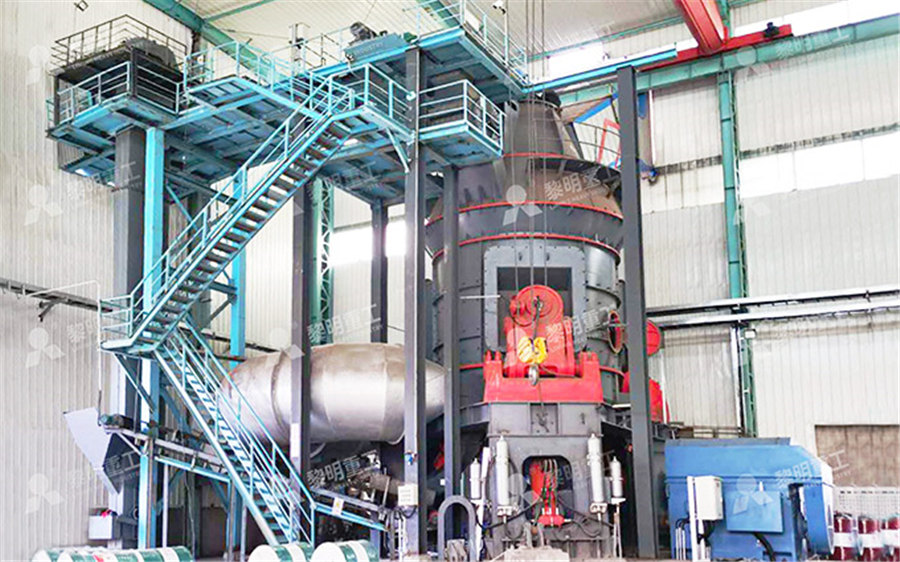
Belite cement clinker from autoclaved aerated concrete
2022年12月29日 The processing of belite cement clinker in a rotary kiln at about 1000 o C is a new recycling option for autoclaved aerated concrete (AAC) waste that otherwise must be landfilled The clinker produced can partially substitute Portland cement clinker is ground to a fine powder and used as the binder in many cement products A little gypsum and/or various supplementary cementing materials (SCMs) areProcess for producing a cement clinker at low temperature2024年4月1日 Increasing postdemolition autoclaved aerated concrete (pdAAC) waste is mainly landfilled due to its physical properties and lacking recycling processes A promising Recycling belite cement clinker from postdemolition autoclaved 2023年9月5日 The processing of belite cement clinker in a rotary kiln at about 1000 o C is a new recycling option for autoclaved aerated concrete (AAC) waste that otherwise must be landfilled(PDF) Belite cement clinker from autoclaved aerated
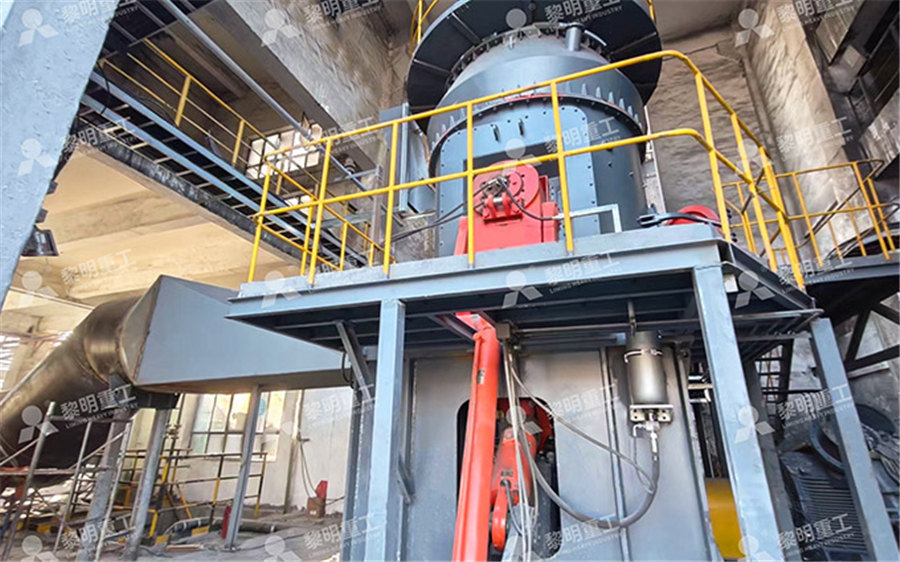
Cement Clinker Production an overview ScienceDirect Topics
The cement clinker manufacturing process traditionally involves intimate mixing and the subsequent heat treatment of a blend of calcareous rock, such as chalk or limestone, and 2024年3月1日 Thermodynamic simulation is a possible solution, which allows researchers to understand the phase assemblages of cement clinker and influences of raw material Toward smart and sustainable cement manufacturing process: 2023年10月16日 This study proposes a raw meal proportioning methodology for optimising coprocessing of natural feedstocks with alternative raw materials in clinker production, intending Thermodynamic modelling of cements clinkering process as a tool Purpose: Optimization of the oxyfuel clinker burning process based on process modeling verified by prototype results Oxyfuel principle: Air is replaced by recirculated COProcess characteristics of clinker and cement production SINTEF
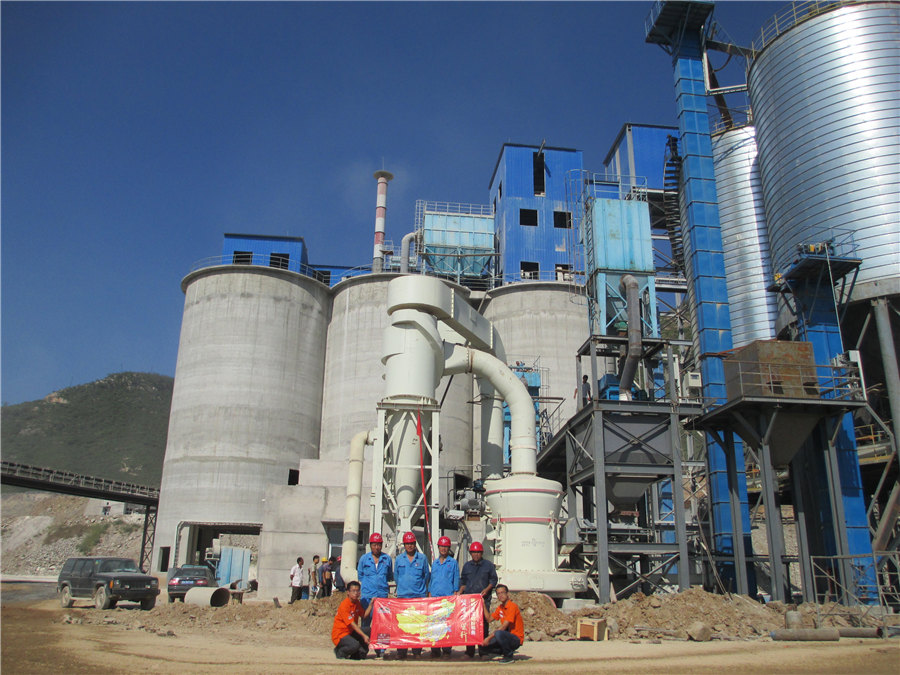
Cement and Clinker Production by Indirect
As a result of the indirect mechanosynthesis process, the clinker produced is in powder form This result will impact the reduction in the energy used for the milling clinker when the gypsum is introduced for cement productionLowtemperature electrochemical cement clinker (eclinker) production is a promising technology for reducing carbon dioxide (CO 2) emissions in the cement industry This Perspective provides an overview of the process and the LowTemperature Electrochemical Cement Clinker 2014年1月1日 Portland cement clinker burning, 22 The phase systems important for cement chemistry, 23 The clinkering process in industrial mixes, confirmed it However, the XRD examination of the powder around the Al 2 O 3 pulley, It has insignificant effect on clinkering process and clinker properties, Portland Cement Clinker SpringerLink2022年9月21日 With this process, we manufactured cement and clinker from industrial and laboratory raw mixes, ball/powder ratio of 4 and a milling time of 15 min, and the rotation speed of the disc andCement and Clinker Production by Indirect
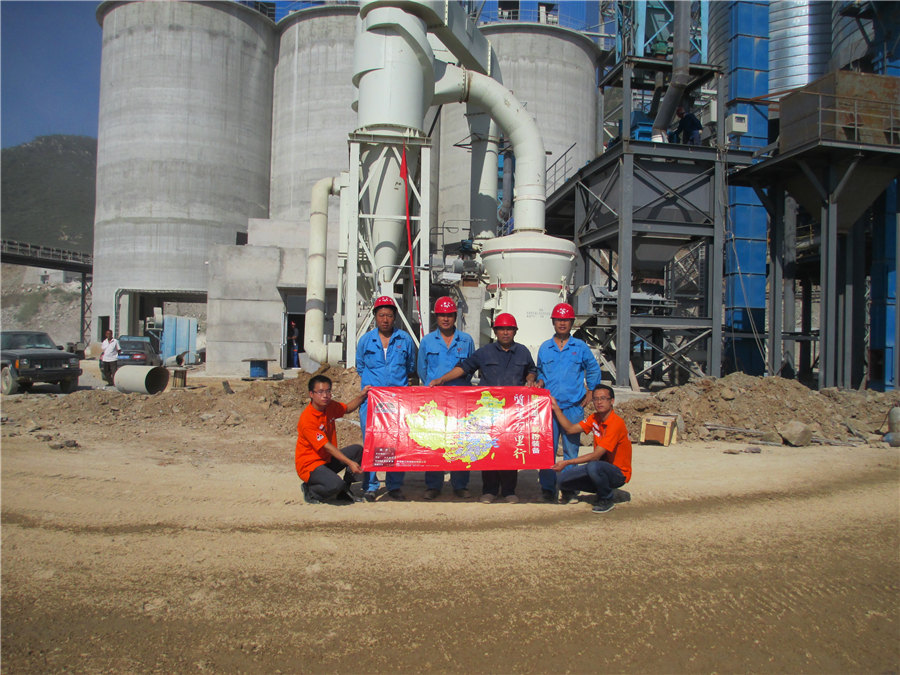
Manufacturing of Portland Cement – Process and
4 天之前 During this process, these materials partially fuse to form nodular shaped clinker by broking of chemical bonds of the raw materials and recombined into new compounds The clinker is cooled and ground to a fine powder with 2013年1月1日 CaCO 3 ðsÞ ! CaO ðsÞ þ CO 2 ðgÞ A reduction in carbon dioxide emissions from combustion can be achieved by replacing fossil fuels with alternative fuels, optimising the burners and Modelling the cement process and cement clinker qualityThe Portland clinker essentially consists of four minerals: two calcium silicates, alite (Ca 3 SiO 5) and belite (Ca 2 SiO 4), along with tricalcium aluminate (Ca 3 Al 2 O 6) and calcium aluminoferrite (Ca 2 (Al,Fe) 2 O 5)These main mineral phases are produced by heating at high temperature clays and limestone [3]The major raw material for the clinkermaking is usually limestone Cement clinker Wikipedia2017年10月30日 On the other hand, aerated concrete contains no coarse aggregates and is relatively homogeneous compared with lightweight aggregate concrete [10]Aerated concrete, also known as cellular concrete, foam concrete, porous concrete, and so on, is produced with a cement or lime mortar, in which air voids are generated by a gasforming or foaming process A comprehensive study on the production of autoclaved aerated concrete
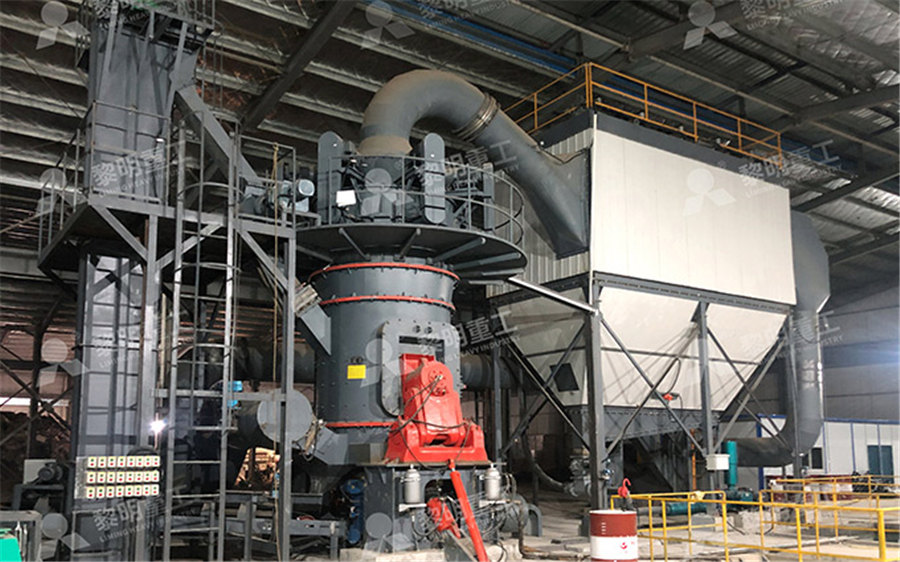
The Cement Manufacturing Process Thermo Fisher Scientific
2023年12月20日 The clinker is ground to a fine powder in a cement mill and mixed with gypsum to create cement The complex process of making cement starts with the mining of raw materials like limestone and clay, which are then ground into a fine powder known as raw meal and heated in a cement kiln to a sintering temperature as high as 1450 °C2023年7月10日 The cement manufacturing process involves the extraction and processing of raw materials, such as limestone, clay, and shale, which are then heated in a kiln at high temperatures to form clinkerCement Manufacturing Process and Its Environmental ImpactCement manufacturers may also purchase clinker if the raw materials needed to make cement are scarce or unavailable in their area Advantages And Disadvantages Of Cement Clinker Cement clinker is a common material used in the production of cement It is formed by sintering limestone, clay and other additives together at high temperaturesWhat Is Cement Clinker? Composition Uses Of Cement ClinkerThis concept is used in producing a type of clinker with up to 30% less carbon dioxide emission Energy efficiency improves and the electricity costs for the manufacturing process are about 15% lower as well Use of Clinker: Conversion to Cement Clinker, combined with additives and ground into a fine powder, is used as a binder in cement productsWhat is Cement Clinker? Composition, Types Uses
.jpg)
How Is Cement Produced in Cement Plants Cement
The cyclone preheating system Phase IV: Calcination The calcination is the core phase of the cement making dry process The calcination of the preheated raw meal takes place in the rotary kiln of the cement plant The rotary kiln is a Report of UNEP SBCI WORKING GROUP ON LOWCO2 ECOEFFICIENT CEMENTBASED MATERIALS Ellis Gartner, Tongbo Sui, in Cement and Concrete Research, 2018 1 Introduction The term “alternative cement clinker ” as used here refers to a manmade mineral material that, when ground to a fine powder, is capable of reacting sufficiently rapidly with water and/or CO 2 Cement Clinker an overview ScienceDirect TopicsIn portland cement manufacturing process, the quality of cement clinker directly affects the quality of the finished product cement The following are several important factors affecting the cement clinker quality In the process of clinker production, strict control of these factors can ensure the production of highquality, highyield clinker 1Cement Clinker Quality Control During Clinker Production Process 2024年3月1日 Cement plants have used new grinding equipment, dryprocess instead of the wetprocess kiln, modern clinker kilns, and multistage preheaters that can save energy [1] The use of blends with renewable fuel and fossil fuel [ 2 ] or the use of solar calcination reactors [ 3 ] can reduce emissions and save energy in cement manufacturingToward smart and sustainable cement manufacturing process:
.jpg)
Cement Clinker: Production, Composition, Types, and Impact
2023年6月6日 The unique properties of clinker also contribute to essential hardening quality in cement, which make it one of the most valuable building materials in existence Production Process of Clinker Cement manufacturers create clinkers through a multistep process that includes ingredient selection, heating, and grinding2020年8月25日 A full cement production process includes the cement crushing process, raw mill process, clinker process, and cement grinding process, cement packing process, and related process Find more! Skip to content +86 s the clinker is ground to a fine powder along with other materials, Cement Production Process Cement Manufacturing Process AGICO CEMENT2022年10月1日 The processing of belite cement clinker in a rotary kiln at about 1000 o C is a new recycling option for autoclaved aerated concrete (AAC) waste that otherwise must be landfilledBelite cement clinker from autoclaved aerated concrete waste – 2023年9月5日 The processing of belite cement clinker in a rotary kiln at about 1000 • C in a CO 2 atmosphere is a new recycling option for Autoclaved Aerated Concrete (AAC) waste that otherwise must be (PDF) Belite cement clinker from autoclaved aerated concrete
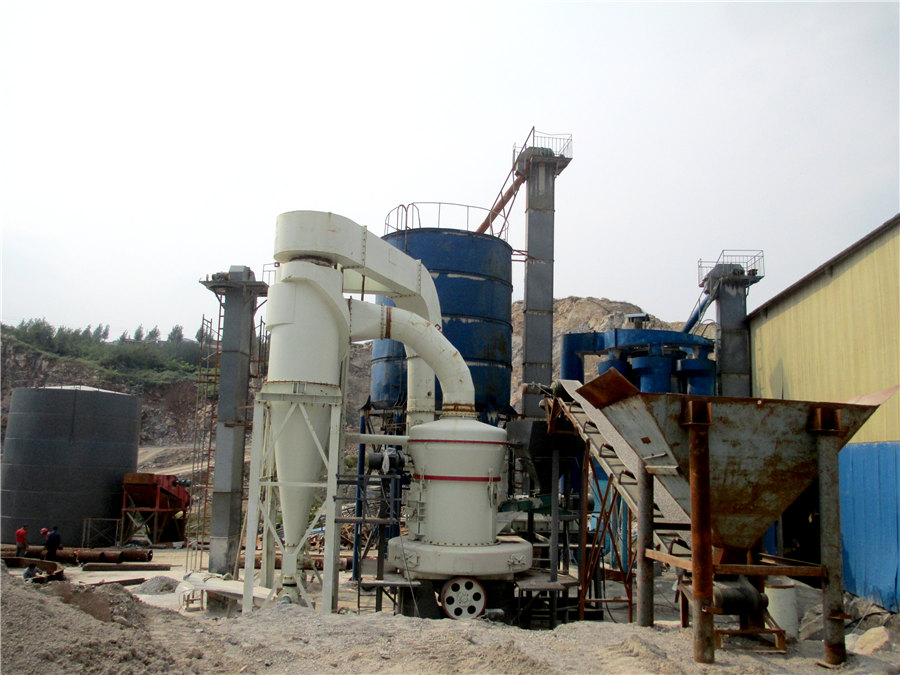
Effects and Control of Chemical Composition of Clinker for Cement
2020年10月15日 Again, in addition to the four major compounds present in Portland cement such as tricalcium silicate (C 3 S), dicalcium silicate (C 2 S), tricalcium aluminate (C 3 A) and tetracalcium Continuous high temperature process in the cement industry: Calcination and cement clinker burning Calcination of raw material CaCO 3 => CaO + CO 2 Process emissions of raw material: = 054 t CO 2 /t clinker Endotherm reaction at 950 °C ca 1700 MJ/t clinker ≈ 50% of energy Cement clinker burning at 1450 °C formation of hydraulicProcess characteristics of clinker and cement production SINTEFSulfate Resistant Clinker – The composition of this type of clinker is alite 76%, belite 5%, tricalcium aluminate 2%, tetra calcium aluminoferrite 16%, and free calcium oxide 1% In recent years the production of this type of clinker has What is Cement Clinker? Composition, Types Uses2023年10月19日 Clinker grinders are an important part of the cement manufacturing process They are used to grind clinker into a fine powder and are typically located at the end of the cooler in a cement plant Clinker is a nodular Clinker Grinding Techniques in Cement Manufacturing
.jpg)
Autoclaved aerated concrete (AAC, Aircrete)
Autoclaved aerated concrete (AAC, Aircrete) Autoclaved aerated concrete is a versatile lightweight construction material and usually used as blocks Compared with normal (ie: “dense” concrete) aircrete has a low density and excellent 2024年11月23日 Cement Extraction, Processing, Manufacturing: Raw materials employed in the manufacture of cement are extracted by quarrying in the case of hard rocks such as limestones, slates, and some shales, with the aid of blasting when necessary Some deposits are mined by underground methods Softer rocks such as chalk and clay can be dug directly by Cement Extraction, Processing, Manufacturing Britannica2020年7月15日 The Autoclaved aerated concrete (AAC) is a product of fly ash which is mixed with lime, cement, and water and an aerating agent The AAC is mainly produced as cuboid blocks and prefabricated panels(PDF) Analysis of Autoclaved Aerated Concrete (AAC) Blocks 2019年8月27日 The major raw materials used as a source of CaO for cement manufacturing are limestone, chalk, marl, etc These raw materials by virtue of their natural occurrence contains other mineral impurities eg, MgO, SiO 2, Al 2 O 3, Fe 2 O 3, alkali compounds, and sulfidesThese impurities play an important role to influence the cement manufacturing Cement Manufacturing and Process Control SpringerLink
.jpg)
Portland cement clinker overview Understanding Cement
Portland cement clinker overview Portland cement clinker is a dark grey nodular material made by heating ground limestone and clay at a temperature of about 1400 °C 1500 °C The nodules are ground up to a fine powder to produce cement, with a small amount of gypsum added to control the setting properties This page gives a thumbnail sketchGlobal cement production has reached 39 billion tons However, the clinkerization process, which is the basis of cement production, is responsible for an approximate annual global CO2 emission of 2 billion tons As part of CEMBUREAU’s 5C strategy, the European cement industry aims to achieve carbon neutrality throughout the cementconcrete value chain by 2050 This article is Cement and Clinker Production by Indirect Mechanosynthesis Process 2024年9月5日 The Manufacturing Process of Cement Now, let’s explore the steps involved in the cement production process in more detail: 1 Mining and Crushing The process of making cement begins with mining, where raw materials are extracted from quarries Huge machines called excavators dig the limestone out of the earthA Comprehensive Guide to the Cement Manufacturing ProcessManufacturing of cement involves various raw materials and processes Each process is explained chemical reactions for manufacture of Portland Cement Cement is a greenish grey colored powder, made of calcined mixtures of clay and limestone When mixed with water becomes a hard and strong building materialManufacture of Cement Materials and Manufacturing Process of
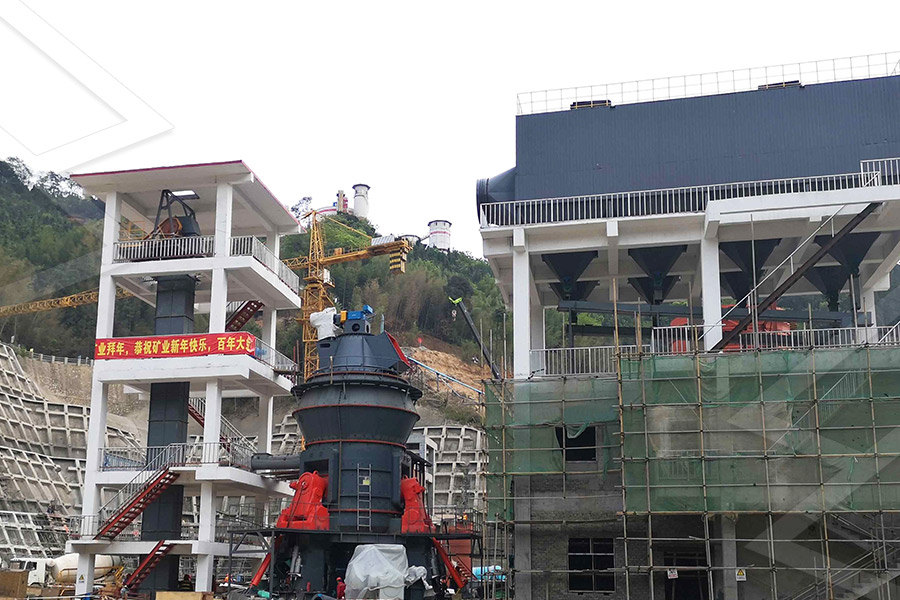
Cement manufacturing process PPT Free Download
2014年6月10日 It begins with an overview of what cement is and how it is used to make concrete It then describes the industrial process for manufacturing cement, involving grinding raw materials like limestone and clay at high Portland cement PC Aïtcin, in Science and Technology of Concrete Admixtures, 2016 Abstract Portland cement is at the same time the fruit of simple technology and a complex science It consist in firing at 1450 °C very simple pulverized raw materials having a very specific composition to produce an intermediate product called Portland cement clinker or simply clinkerPortland Cement Clinker an overview ScienceDirect Topics2023年1月1日 The substitution of Mg into cement clinker phases has been studied by isothermal annealing, followed by Xray diffraction, electron microscopy and analysis and infrared spectroscopy of the productsFormation of cement phases and kinetics of clinker formation2019年1月1日 They are not treated hereIn addition to the concrete applications, significant trends of innovation in cement science concerning the chemistry and engineering of the production process are Modeling of cement clinker chemistry and engineering of cement
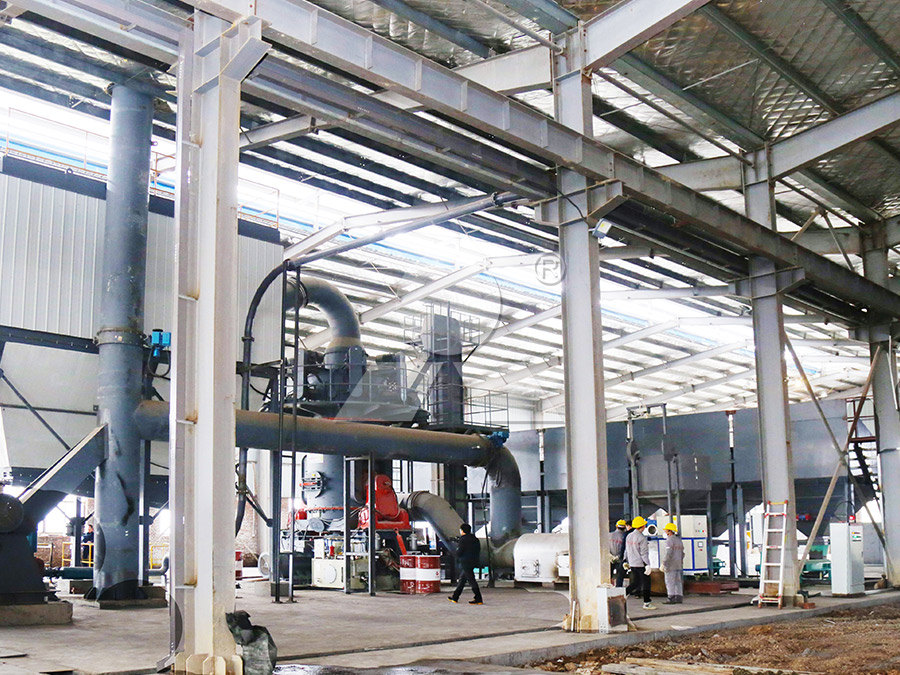
An Introduction to Autoclaved Aerated Concrete (AAC) IJESI
AAC was developed in mid 1923 in Sweden It is also known as Autoclaved Cellular Concrete (ACC) or Autoclaved Lightweight Concrete (ALC) Production process of AAC is fairly simple It has become one of the most used building materials in Europe and is rapidly growing in many other countries around the world It is made with made with a mixture 2020年2月2日 watercement ratio of 06 In this research, the specimen is tested with and w ithout lime Gypsum is constantly used in the entirePreparation of Autoclaved Aerated Concrete (AAC) Block by 2023年9月21日 Alexanderson et al [1], Petrov et al [2] and Prim et al [3] investigated the microstructure of aerated concrete and found that the pore structure of aerated concrete was mainly divided into Study on the Preparation and Properties of Glass Powder Autoclaved 2022年1月19日 By utilizing residual materials from industrial procedures, including expanded perlite waste (EPW) [15], efflorescent sand and phosphorescent slag [30], iron ore tailings [31], aircooled slag [32 Mechanical properties and development of light weight concrete
.jpg)
Cement Clinker Calcination in Cement Production Process AGICO Cement
The cement clinker calcination is an important step in the cement production During the grinding, 23% gypsum powder is added as retarder so that when cement contacts with water, its solidification speed will not Clinker Calcination Process The cement manufacturing processes can be totally classified into dry method process and wet 2019年3月1日 Request PDF Novel modifications in a conventional clinker making process for sustainable cement production The current investigation proposes modifications in a clinker making process to Novel modifications in a conventional clinker making process for