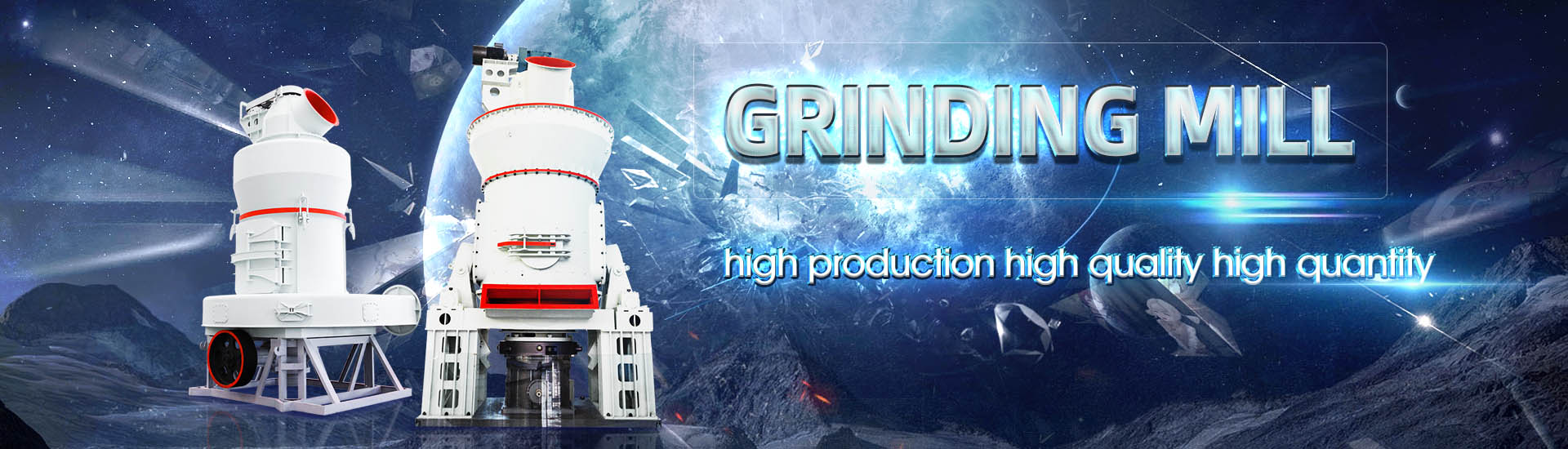
Ironmaking fluorite standard
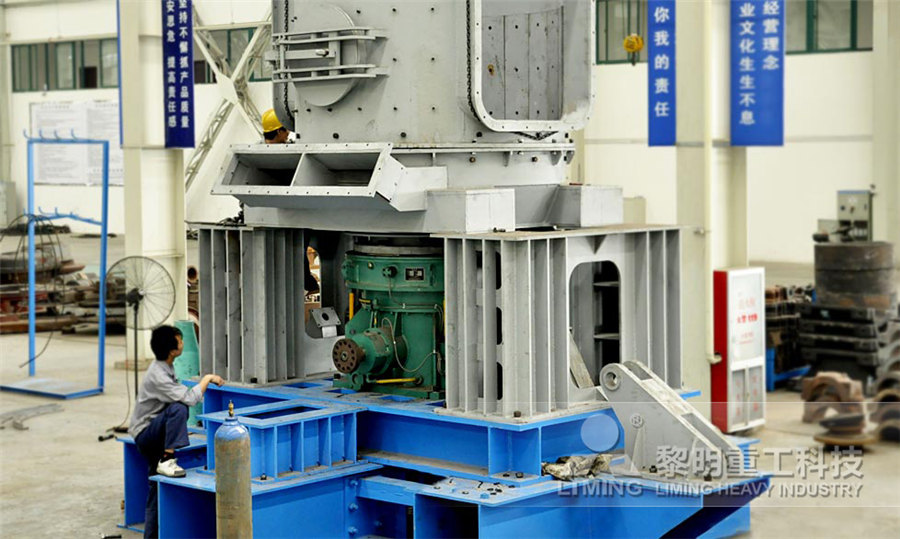
Lowering iron losses during slag removal in hot metal
2020年5月1日 Most common slag modifiers in industry contain fluoride as a fluidiser However, fluoride leads to a higher magnesium consumption and has health, safety and environment issues Fluoridefree alternatives like nepheline syenite (NS) and fly ash (or pulverised fuel For electrochemical ironmaking, two leading direct electrochemical pathways exist: molten oxide electrolysis (MOE) and electrowinning MOE is a hightemperature process producing liquid iron and parallels the existing aluminum Electrowinning for RoomTemperature Ironmaking: 2020年4月9日 Most common slag modifiers in industry contain fluoride as a fluidiser However, fluoride leads to a higher magnesium consumption and has health, safety and environment Full article: Lowering iron losses during slag removal in hot metal 2019年1月1日 These factors have contributed to the development of alternative technologies of ironmaking, of which Direct Reduction (DR) processes are expected to emerge as preferred A review of ironmaking by direct reduction processes: Quality
.jpg)
Fluorinecontaining Mineral Phases in Ironmaking and
2002年1月1日 Based on these results, H3BO3 may be adopted as an innovative additive replacing fluorite in the Mg production, to enhance sustainability and environmental soundness 2023年3月14日 An ionic conductor membrane composed of fluoritetype ZrO 2based doped solid electrolyte was installed on an electrolytic cell to separate the cathode and anode A Research progress in the preparation of iron by electrochemical Fluorspar is a common raw material used at ironmaking and steelmaking facilities Although it is a powerful fluxing agent, its benefits are to be weighed against health and environmental concerns Fluor can be lost from industrial Replacement of fluorspar in the desulfurization of hot Ironmaking is to convert iron ore or other ironbearing materials into a form that can be easily transformed into steel This is done primarily in a BF with other auxiliary facilities to smelt the Ironmaking Process an overview ScienceDirect Topics
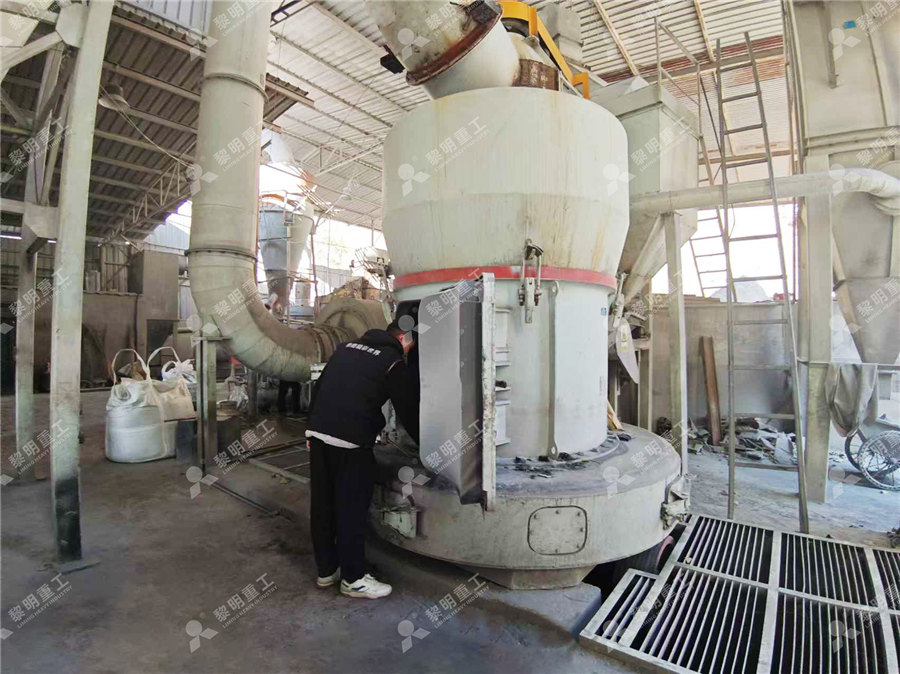
Quality requirements of iron ore for iron production
2015年1月1日 This chapter first gives an overview of the BF and various emerging alternative ironmaking technologies and then discusses the quality requirements of ironbearing raw 2021年6月25日,《Nature》子刊《Nature Sustainability》在线刊登了我院汤铃教授、博士生贾敏(2021级)和薛晓达(2019级)及其合作者的研究论文“Effect of strengthened standards on Chinese ironmaking and steelmaking emissions( 《Nature Sustainability》刊发我院汤铃教授团队最新研 1 1 Effect of strengthened standards on Chinese ironmaking and 2 steelmaking emissions 3 4 Xin Bo1,2, Min Jia3, Xiaoda Xue4, Ling Tang4*, Zhifu Mi5*, Shouyang Wang6,7*, 5 Weigeng Cui8, Xiangyu Chang9, Jianhui Ruan3, Guangxia Dong10, Beihai Zhou2, and 6 Steven J Davis11,12 7 8 1 Appraisal Center for Environment and Engineering, Ministry of Ecology and Environment,Effect of strengthened standards on Chinese ironmaking and 2017年3月22日 Sulphur removal in the ironmaking and oxygen steelmaking process is reviewed A sulphur balance is made for the steelmaking process of Tata Steel IJmuiden, the NetherlandsSulphur removal in ironmaking and oxygen
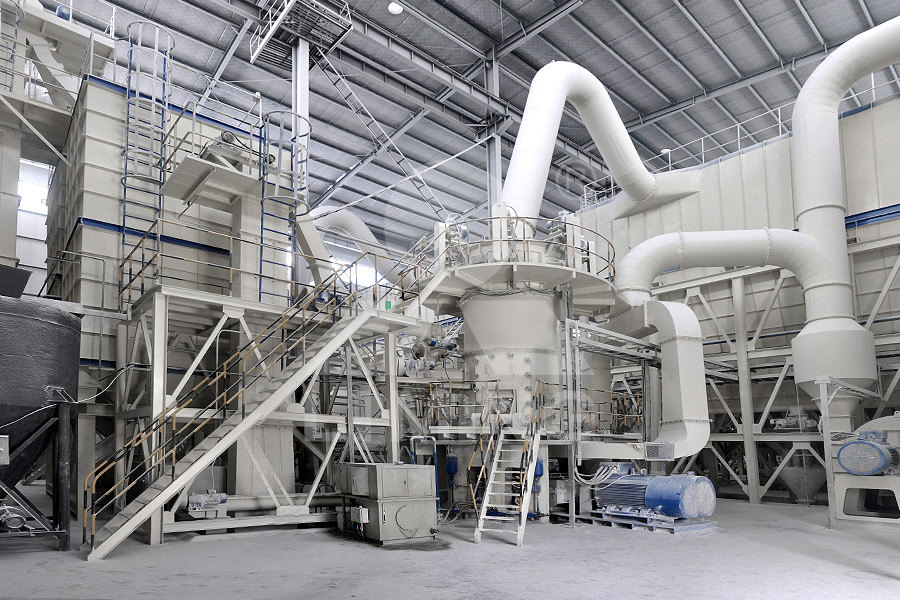
A REVIEW OF IRONMAKING BY DIRECT REDUCTION
2023年11月10日 These factors have contributed to the development of alternative technologies of ironmaking, of which Direct Reduction (DR) processes are expected to emerge as preferred alternatives in the future学术期刊 Ironmaking and Steelmaking:期刊短名:J Iron Steel Inst (London),期刊 ISSN: 03019233, 17432812。Ironmaking Steelmaking: Processes, Products and Applications monitors international technological advances in the industry with a strong element of engineering and product related material First class refereed papers from the international iron and steel Ironmaking and Steelmaking J Iron Steel Inst (London) 期刊影 To reduce such emissions, China imposed new emission standards in 2015 and promoted ultralow emission standards in 2019 Here we use measurements from China's continuous emissions monitoring systems (covering 6991% of national iron and steel production) to develop hourly, facilitylevel emissions estimates for China's iron and steel industryEffect of strengthened standards on Chinese ironmaking and 2024年4月26日 The final stage in iron ore processing is ironmaking, where the iron ore is transformed into molten iron through a process called reduction The most common method of ironmaking is the blast furnace route In a blast furnace, iron ore, coke (carbon), and fluxes (limestone or dolomite) are loaded into the furnace from the topIron Ore Processing: From Extraction to Manufacturing
.jpg)
Hot metal dephosphorization process using calcium ferrite slag
The average hot metal dephosphorization rate of fluorite slagging is 777% The slag melting temperature during calcium ferrite slagging is 1137°C on average, which is lower than the melting temperature of fluorite slagging, and the slag melting temperature during fluorite slagging is 1296°C on average2023年10月6日 Flux is an auxiliary raw material for blast furnace ironmaking, which is required by blast furnace slagging system Common fluxes include limestone (CaCO 3), dolomite [Ca (Mg) CO 3], etc Coke is the main fuel of blast furnace ironmaking and also serves as the reducing agent, skeleton, and carburizing source of blast furnace smeltingBlast Furnace Ironmaking SpringerLink2024年3月8日 The basic oxygen steelmaking process is based on the CaOFeOSiO2 ternary slag system, characterized by a high melting point and low lime dissolution rate, often becoming one of the key factors limiting the efficiency of the converter The bulk solid waste red mud, produced by the Bayer alumina process and rich in Fe2O3/Al2O3/Na2O, significantly reduces Properties of FluorineFree Steelmaking Flux Prepared Using Red 2011年1月1日 From a customer perspective, it is the behaviour of iron ores in downstream processing that gives them their value; their impact on the sintering or pelletising process and subsequently blast Calculating the value of iron ores in ironmaking and steelmaking
.jpg)
Ironmaking Steelmaking,IRONMAK STEELMAK投稿指南及影响
Ironmaking Steelmaking IRONMAK STEELMAK: 期刊ISSN: Publishing Ethics The journal adheres to the highest standards of publishing ethics, with rigorous processes in place to ensure this is achieved Taylor Francis is a member of Committee of Publications Ethics (COPE) 2020年6月3日 A new route for making steel from iron ore based on the use of hydrogen to reduce iron oxides is presented, detailed and analyzed The main advantage of this steelmaking route is the dramatic reduction (90% off) in CO2 Hydrogen Ironmaking: How It Works MDPI2021年2月14日 PDF The development of a novel ironmaking technology based on fine iron ore concentrate in a flash reactor is summarized of 11 standard liters per minute (SLPM) was used as the carrier gas(PDF) Design of Novel Flash Ironmaking Reactors for 1 1 Effect of strengthened standards on Chinese ironmaking and 2 steelmaking emissions 3 4 Xin Bo1,2, Min Jia3, Xiaoda Xue4, Ling Tang4*, Zhifu Mi5*, Shouyang Wang6,7*, 5 Weigeng Cui8, Xiangyu Chang9, Jianhui Ruan3, Guangxia Dong10, Beihai Zhou2, and 6 Steven J Davis11,12 7 8 1 Appraisal Center for Environment and Engineering, Ministry of Ecology and Environment,Effect of strengthened standards on Chinese ironmaking and
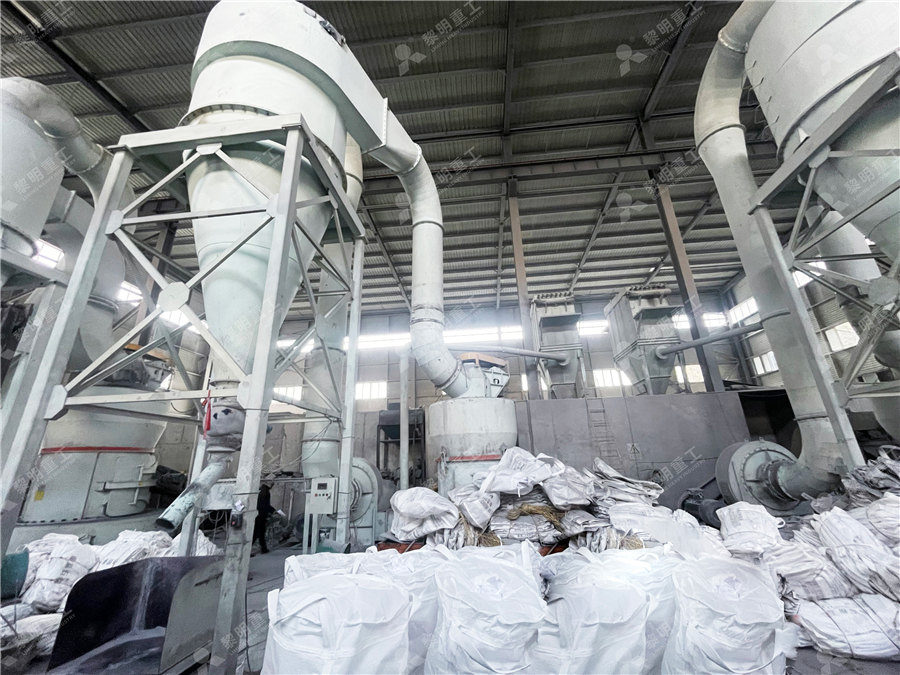
(PDF) Hydrogen Ironmaking: How It Works ResearchGate
2020年7月9日 PDF A new route for making steel from iron ore based on the use of hydrogen to reduce iron oxides is presented, detailed and analyzed The main Find, read and cite all the research you need China has produced roughly half of the world’s steel in recent years, but the country’s iron and steel industry is a major source of air pollutants, especially particulate matter, SO2 and NOx emissions To reduce such emissions, China imposed new emission standards in 2015 and promoted ultralow emission standards in 2019 Here we use measurements from China’s Effect of strengthened standards on Chinese ironmaking and Metals 2020, 10, 922 4 of 15 970 kgCO2eq/tHRC, halves the CO2 emissions of the standard BFBOF route, the hydrogen route reaches far lower levels, 25 to 200 kgCO2eq/tHRC, ie, an 89–99% Hydrogen Ironmaking: How it Works ResearchGateABSTRACT To solve environmental pollution caused by using fluorite slagging in the process of hot metal dephosphorization, this paper applies premelted calcium ferrite slag in the production of stainless steel powder injection and oxygen dephosphorization process to replace fluorite slagging The results show that the average hot metal dephosphorization rate of calcium ferrite Hot metal dephosphorization process using calcium ferrite slag
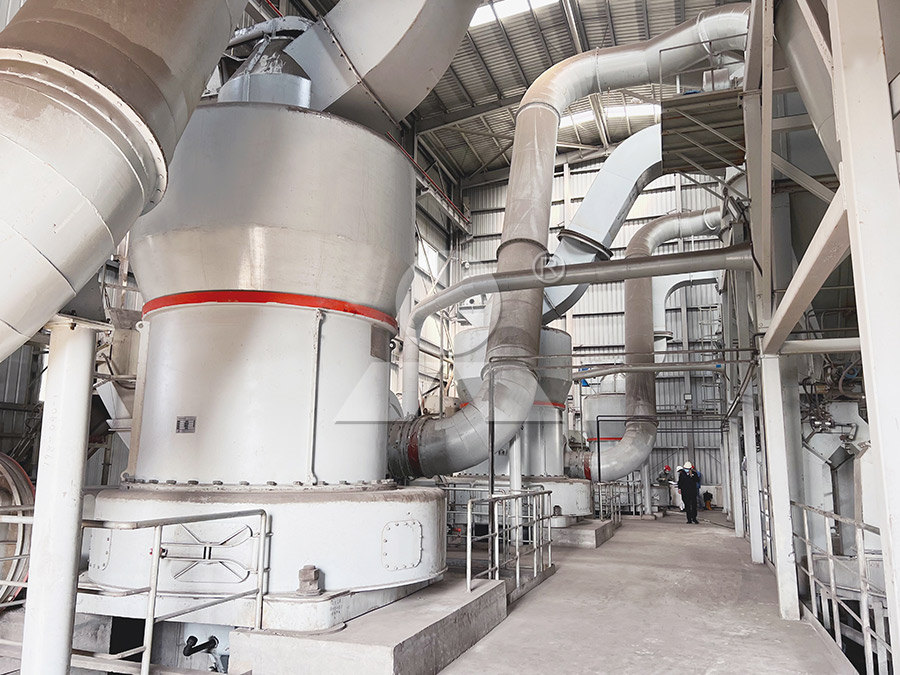
The World Leader in Ironmaking Solutions Primetals Technologies
Learn about cuttingedge technologies for ironmaking and automation provided by Primetals Technologies ᐅ Over 300 successful ironmaking projects dust, phenols, sulfides, and ammonia, so emission values come in below the maximum values permitted by European standards Furthermore, wastewater emissions are far lower compared with the 2023年3月14日 For decades, the steel production industry has been one of the largest sources of CO2 emissions, accounting for 7% of global CO2 emissions, of which 70% is emitted in the ironmaking process Currently, the main lowcarbon iron production route is hydrogen metallurgy, which uses renewable energy to generate electricity, electrolyze water to produce hydrogen, Research progress in the preparation of iron by electrochemical 2021年3月2日 The phase changes during ironmaking were investigated, along with the removal techniques of such impurities and their environmental impact Thus, satisfying the standard(PDF) Effect of Lead and Zinc Impurities in Ironmaking 2017年10月10日 Ironmaking Blast Furnace Iron is made by reacting iron ore (iron oxide and impurities), coke (a reductant) and limestone (CaCO 3) in a blast furnace Iron ores with lower iron content such as taconite are first processed Ironmaking 101 – From Ore to Iron with Blast Furnaces
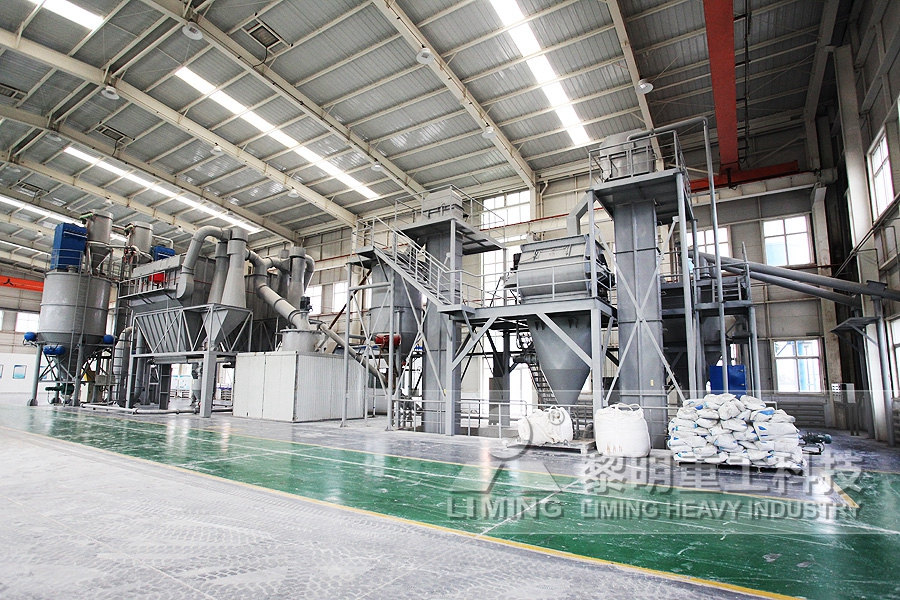
Development and Problems of Fluidized Bed Ironmaking Process:
2023年10月9日 Comprehensive control of greenhouse gas emissions and response to climate change are concerns of countries around the world to protect living homes The steel industry is responsible for over 10% of global CO2 emissions, with approximately 80% of these emissions coming from the ironmaking process Great efforts have been made in both blast furnace (BF) 21 Introduction of Modern Ironmaking Technology Historically, iron was produced in Japan by a smallscale ironmaking method called the tatara 92) process with iron sand as the main raw material Use of the blast furnace process 93) began on December 1, 1857 following the construction of a westernstyle blast furnace in Kamaishi by T Oshima In commemoration of Ironmaking Technology for the Last 100 Years: Deployment to 2021年4月5日 Carbon included in coke and coal was used as a reduction agent and fuel in blast furnace (BF) ironmaking processes, which released large quantities of carbon dioxide (CO2)Abstract and Figures ResearchGateDigitalization and Automation: Ironmaking in the Industry 40 Era The integration of digital technologies and automation is reshaping ironmaking operations From advanced process control systems to predictive maintenance algorithms, digital solutions enhance efficiency, safety, and decisionmaking in steel plantsFrom Ore to Alloy: Navigating Ironmaking in Modern Steel

Hydrogen Ironmaking: How It Works univlorraine
Metals 2020, 10, 922 2 of 15 made from C or from CH4) produces CO2The basic concept of hydrogen ironmaking is to substitute C (or CO) reductant with H2, replacing Fe2O3 + 3 2 C = 2 Fe + 3 2 CO2 (1) or Fe2O3 +3 CO = 2 Fe +3 CO2 (2) with Fe2O3 +3 H2 = 2 Fe +3 H2O (3) thus releasing harmless H2O instead of the greenhouse gas CO2 in the chemical reduction step In 2019年1月1日 These factors have contributed to the development of alternative technologies of ironmaking, of which Direct Reduction (DR) processes are expected to emerge as preferred alternatives in the future This study reviews the different DR processes used to produce Direct Reduced Iron, providing an analysis on the quality requirements of ironbearing ores for use in A review of ironmaking by direct reduction processes: Quality Moore, 1981, Szekely et al, 1989) In ironmaking and steelmaking, slags are basic, and the primary flux added is limebearing, although some acidic components are sometimes added In nonferrous pro cesses slags and fluxes are acidic with silica as the primary com ponent, and although the use of basic flux such as limestone or limeMETALLURGICAL USES FLUXES FOR METALLURGY** (STP) means standard temperature (0 °C) and standard pressure (1013 bar abs) *** FR includes small size coke (030 mm, approx 50100 kg/t HM COAL The major criteria for an initial evaluation of coals or coal blends suitable for the FINEX® Process are: • fix carbon content at a minimum of 55% • ash content up to 25%THE FINEX® PROCESS ECONOMICAL AND ENVIRONMENTALLY SAFE IRONMAKING
.jpg)
Use of DRI/HBI in ironmaking and steelmaking
2016年4月1日 Microstructures displayed by the thermally treated for 10 minutes at 1200° C (A), 1300° C (B), 1400° C (C), 1500° C (D) and for 20 minutes at 1500° C (E) samples2016年5月31日 It can be partially substituted for fluorite (CaF 2 ) in Arc furnaces for steelmaking [10], or used as an additive in pig iron and rock wool production [11,12]Using SPL (Spent PotLining) as an Alternative Fuel in Metallurgical According to the International Energy Agency (IEA), the industrial sector is responsible for 23% of global energyrelated CO 2 emissions, and iron and steel accounts for 30% of the sector’s total (Figure 1)That is 26 gigatons of CO 2 Fueling the Future of Ironmaking: MIDREX Flex™2015年1月1日 Although this is large by today's standards, it is relatively small compared with the 135 Mt demand predicted for the year 2050 Campos de Assis et al (2008) and Valladares and Scherer (2012) showed that Brazilian pig iron production from charcoalfired miniBFs has varied somewhat in recent years but has averaged around 10 Mt/year, from up to 172 furnacesUtilization of biomass as an alternative fuel in ironmaking
.jpg)
Fluoride standard solution Merck
Fluoride standard solution traceable to SRM from NIST NaF in H₂O 1000 mg/l F Certipur® Find MSDS or SDS, a COA, data sheets and more information It appears that your browser has JavaScript disabled2021年3月10日 However, the ironmaking process causes environmental problems The growing need for a dramatic reduction of greenhouse gas emissions leads to the development of innovative technologies to reduce energy consumption and emissions in this process 11 Ironmaking Process Fe is extracted from Fe ore and converted into alloysIronmaking Process Encyclopedia MDPI2023年11月29日 1 Dr Hassan Z Harraz hharraz2006@yahoo Autum 2023 “Iron Ore is more Integral to the Global Economy than any Other Commodity, Except Perhaps Oil” Christopher LaFemina, mining analyst at Barclays Capital (In 2011 the Financial Times quoted) @Hassan Harraz 2023 IRONMAKING By DR Process A REVIEW OF IRONMAKING BY A REVIEW OF IRONMAKING BY DIRECT REDUCTION 2016年3月30日 In book: Encyclopedia of Iron, Steel, and Their Alloys (pppp 10821108) Chapter: i) Direct Reduced Iron: Production; Publisher: CRC Press, Taylor and Francis Group, New York(PDF) i) Direct Reduced Iron: Production ResearchGate
.jpg)
Iron and SteelMaking Process SpringerLink
2020年6月10日 In consideration of ironmaking processes, chemical reactions and temperature profile, the furnace is divided in the following zones, along the vertical length, as shown in the Fig 24 Stack: It is usually considered from stock line to mantle level《GB/T 505672022》 炼铁工艺炉壳体结构技术标准 Technical standard for shell structure of ironmaking furnace 本标准适用于新建、改建和扩建的有效容积为1000m~5000m级的高炉、热风炉、重力除尘器、粗煤气管道壳体的结构设计与施工。GB/T 505672022 炼铁工艺炉壳体结构技术标准 Technical