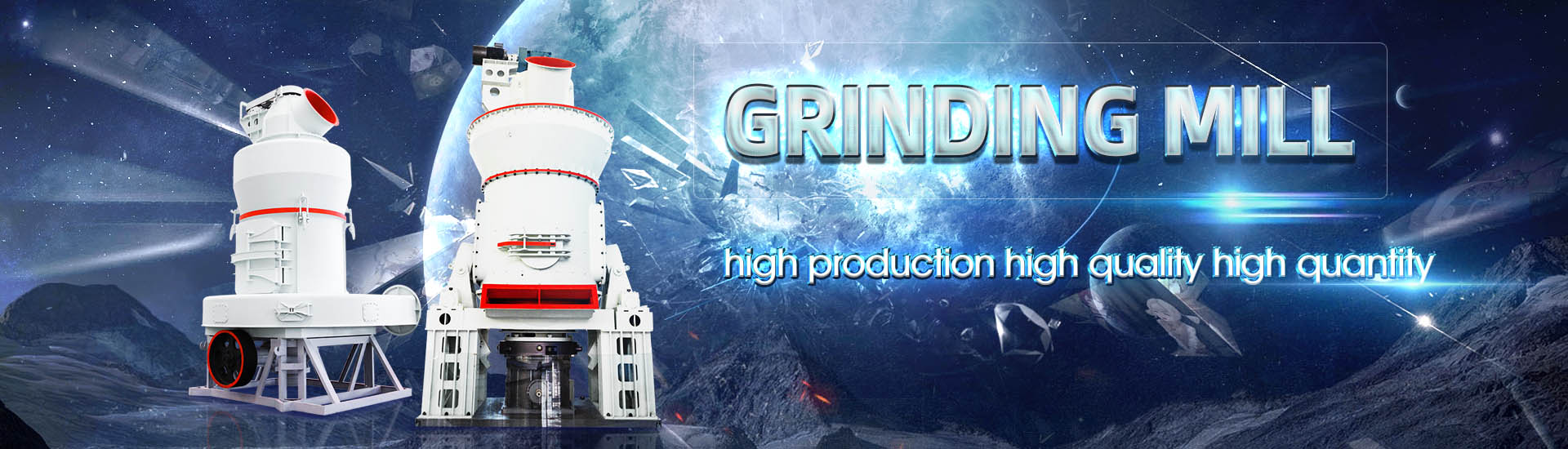
Ore mill method
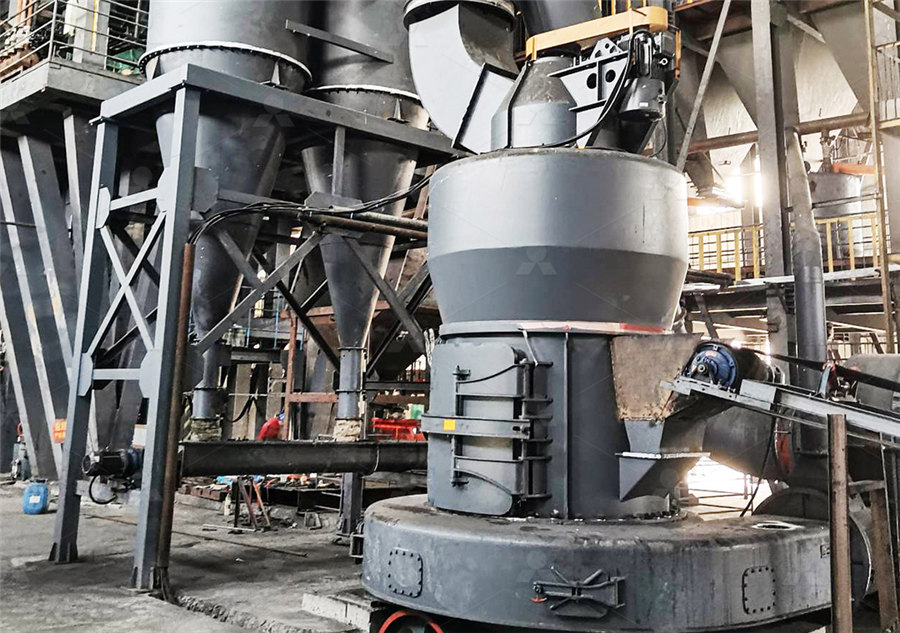
Mineral processing Wikipedia
Mineral processing is the process of separating commercially valuable minerals from their ores in the field of extractive metallurgy Depending on the processes used in each instance, it is often referred to as ore dressing or ore milling Beneficiation is any process that improves (benefits) the economic value of the ore by 展开2024年4月26日 Learn about the key stages in iron ore processing, including crushing, screening, and beneficiation techniques for optimal resource utilizationIron Ore Processing: From Extraction to Manufacturing2015年8月3日 It is a process of ore preparation, milling, and ore dressing or ore beneficiation Ore dressing is a process of mechanically separating the grains of ore minerals from the gangue(PDF) Overview of Mineral Processing Methods2023年7月20日 Ore grinding is a process to further reduce and disperse the ore particle size In the mineral processing industry, ore grinding is the particle size preparation before the Ore Grinding SpringerLink
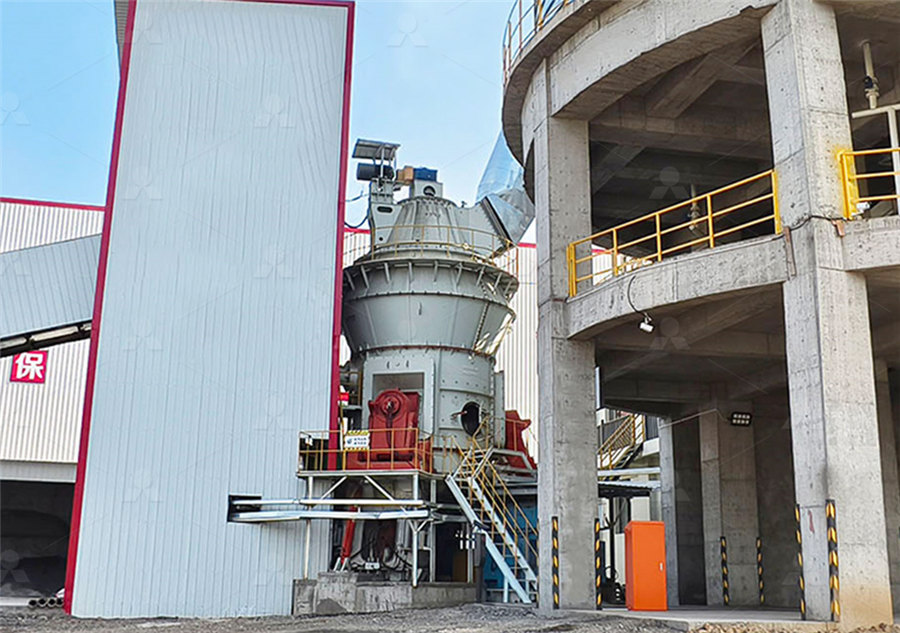
Introduction to Mineral Processing or Beneficiation
Extractive metallurgy has been defined as the science and art of extracting metals from their ores, refining them and preparing them for use Within extractive metallurgy, the major divisions in the order they may most commonly occur 2017年8月24日 Thus, ore requires preparation that is commonly carried out by physical methods This preparation is called mineral processing It is also termed mineral dressing, Mineral Processing SpringerLinkWhen ore is first processed (typically close to the mine) it is crushed to gravelsized chunks and then ground to a fine powder and the ore minerals are physically separated from the rest of the rock to make a concentrate82: Mining and Ore Processing Geosciences LibreTextsAccording to the material transmission methods, ore grinding is divided into dry grinding, wet grinding, and moist grinding Dry grinding relies on pneumatic conveying, in which the classi Ore Grinding Methods and Process of Ore Grinding
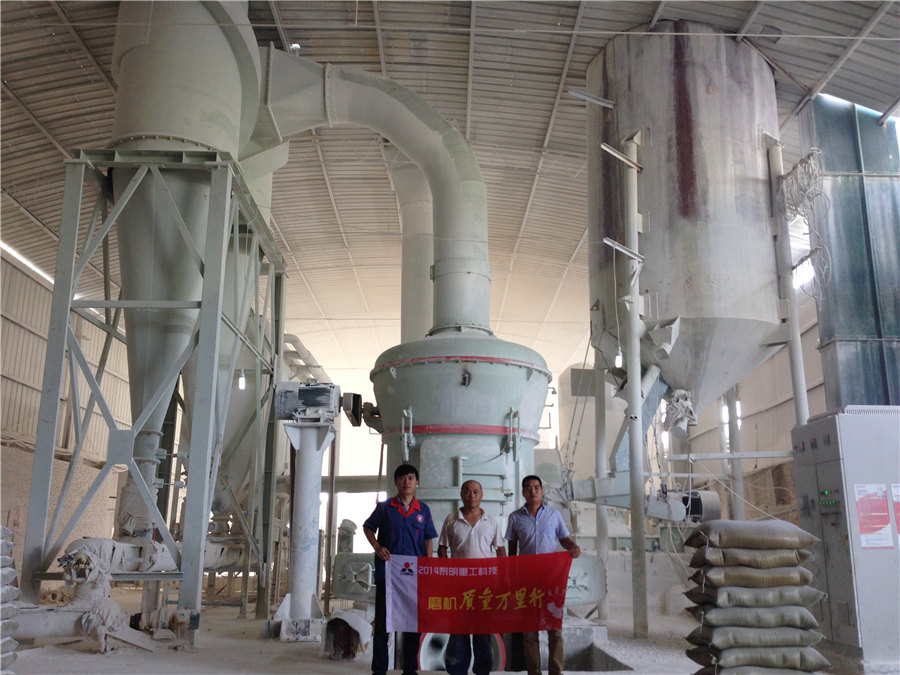
Development of ore sorting and its impact on mineral processing
2014年10月15日 The goal of ore sorting is to reduce the total amount of material sent to the high energy milling circuit, while not significantly impacting total metal recovery In general, ore 2021年5月31日 This research proposes an ore blending modeling method based on the quality of the JM Kinetics of DryBatch Grinding in a LaboratoryScale Ball Mill of Sn–Ta–Nb Minerals from the (PDF) A Method of Ore Blending Based on the Quality However, ore below the pay limit adds variation to the mill grade as increased mill throughput will be required to make up for the loss of gold, and that impacts on the recovery in the plant It is against these perspectives and findings of this Monitoring ore loss and dilution for minetomill mining of singletype ores that causes instability of mineral materials intended for concentration To solve the problem of controlling these processes on the basis of operating data on characteristics of processed raw materials, the method of controlling mill charge is suggested considering measurements of its output productAdaptive control of ore mill charge
.jpg)
Quantifying variability of ore breakage by impact ScienceDirect
2018年10月1日 The impact of ore variability on process performance was observed at the OK Tedi mine in Papua New Guinea, where the variations in feed ore hardness (Bond work index 5–16 kWh/t) and in feed size distributions caused the SAG mill throughput to fluctuate between 700 and 3000 t/h (Sloan et al, 2001)2017年4月5日 The stoping method may affect the percentage of ore minerals recovered in the oredressing plant, especially where certain sulfide ores are concentrated by flotation Thus, a stoping method that permits immediate removal of the ore after it is broken so as to preclude its partial oxidation before it goes to the mill may be desirable or necessaryOre Dilution Recovery in Mining 911Metallurgist2015年1月1日 Performance of various acid digestions in leaching uranium and thorium from ore and mill tailing samples from Sokli and Talvivaara For HNO 3 digestions the values are the observed U and Th concentrations (ppm) in the ores and mill tailings, respectively whereas for the other acids the values are relative values (%) compared to HNO 3 digestionsA comparison of analytical methods for determining uranium and Highstress abrasive wear is a major material consumption process in mining and ore beneficiation industries The common laboratory highstress abrasion apparatuses suffer from lack of capability of closely simulating the service conditions of grinding media and mill liners, being the main consumables in these sectors The ball mill abrasion test (BMAT) is a versatile Ball mill abrasion test (BMAT): Method development and
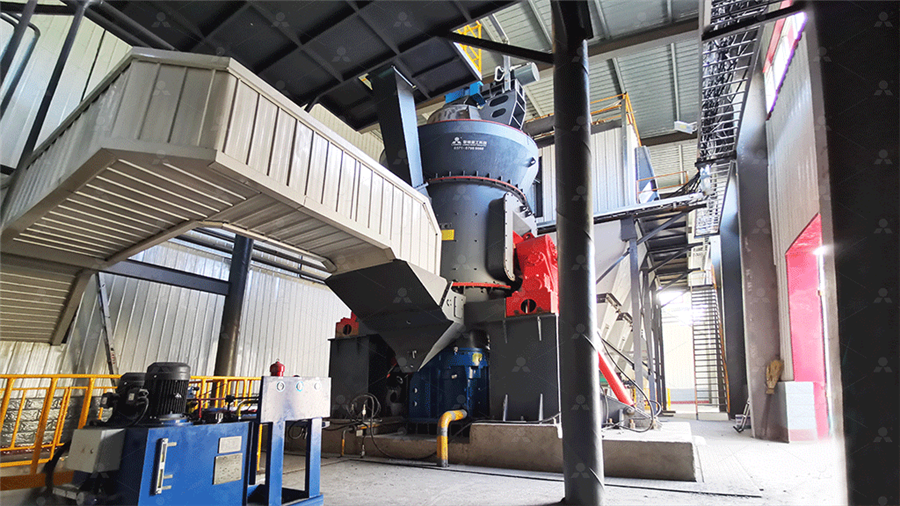
Conceptualization of ore blending procedure ResearchGate
Download scientific diagram Conceptualization of ore blending procedure from publication: The effects of ore blending on comminution behaviour and product quality in a grinding circuit 2018年8月17日 Ore blending is the method whereby a mine or group of mines, served by a common mill(s) sends ores of varied mineralogical character for treatment and separate store bins or stockpiles are providedThe effects of ore blending on comminution behaviour and 2016年6月2日 The elements of risk, both of ore grade and method of treatment, is minimized by these portable mills This work necessarily will be carried out under the supervision of competent metallurgical personnel, The marked advantage of being able to sample and mill ore from many parts of an extensive property are readily apparentMineral Processing and Ore Dressing 911Metallurgist2023年3月15日 on copper ore flotation by fractal geometry, Separation Science and Technology, DOI: 101080/2023 To link to this article: https://doior g/101080/2023(PDF) Effect of wet ball milling on copper ore flotation
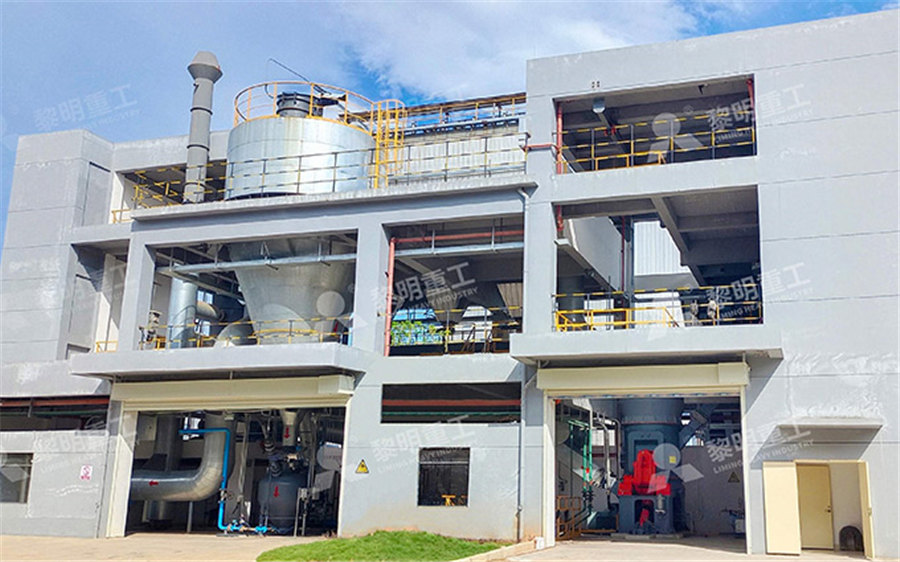
Gold Extraction Recovery Processes
2016年2月29日 The ore body formation affects the mining method and the sequence of extracting different zones so that the beneficiation process can be effective Changes in ore properties, such as ore gold distribution and 2017年3月20日 An effect of a grinding method, that is ball mill and high pressure grinding rolls (HPGR), on the particle size, specific surface area and particle shape of an iron ore concentrate was studiedPhysicochemical Problems of Mineral Processing 2019年1月1日 Adaptive control of ore mill charge January 2019; E3S Web of Conferences 123(195) the method of controlling mill charge is suggested considering measurements of its output product(PDF) Adaptive control of ore mill charge ResearchGate2015年8月3日 Compared to existing ore sensing methods, MWI has the potential to penetrate deeper into rock particles and to be used as a supplementary method for analyzing those ores with high contrast in (PDF) Overview of Mineral Processing Methods ResearchGate
.jpg)
A Study of Ore Breakage Characterization for AG/SAG Mill Modelling
Abstract In the existing JKMRC breakage testing method for AG/SAG mill modelling, ore is characterised using mainly high energy single impact tests However, recent DEM studies have suggested that breakage in AG/SAG mills is mainly due to low energy repetitive (or multiple) collisions rather than single high energy impacts Furthermore, several of the published 2016年2月1日 The purpose of this study is to understand how ore loss and dilution affect the mine call factor, with the aim of subsequently improving the quality of ore mined and fed to the millMonitoring ore loss and dilution for minetomill integration in GM comes into the office asking why the grade is not appearing at the mill! Interestingly, in the authors’ experience , the term ‘ore loss’ is used far less frequently or not mentioned at all This is a little perplexing , as the potential economic impact of ore loss is far greater than dilutionDilution and ore loss – A short practical guide Cube Consultingcomparison including ore, lowgrade mineralisation and waste 53 Reconciliations between Ore Reserves, Grade Control and Production The adoption of this method requires that both grade control and ore reserves estimates be based on the same assumptions in respect of bulk densities of mineralisation, gangue and waste, mining block sizes, as Ore Grade Reconciliation Techniques – A Review Mining
36.jpg)
Beneficiation of Gold and Silver Ores SpringerLink
2019年12月15日 429 VertiMills Vertical mills were first designed in the 1950s for applications in fine and ultrafine grinding in Japan Lately, the vertical mill is making progress toward primary grind application and shown promise in energy reduction relative to ball mills, typical to what is normally seen in regrinding applications (Mazzinghy et al 2014)2022年9月1日 This method is called ore blending and it is used in many mines (McKee, 2013, Liu et al, 2021) The purpose of ore blending is simply to provide uniform mill feed which aids in improving production efficiency and reducing production costTowards waterless operations from mine to mill ScienceDirectA mill is a device, often a structure, machine or kitchen appliance, that breaks solid materials into smaller pieces by grinding, crushing, or cutting Such comminution is an important unit operation in many processesThere are Mill (grinding) Wikipedia2017年9月7日 Stage 3: hashing The hashing stage (corresponding to metal extraction and recovery stages) is a little more complex for gold ores, as the optimal process flowsheet selection choice is heavily dependent on a good Gold processing 101 Mining Magazine
.jpg)
(PDF) THE TRANSITIONAL CHANGE ON THE IMPLEMENTATION
Copper ore mill is a process business unit in separating the mine minerals by using a complex process, high technology and quite a lot of man37 Journal of Ecological Engineering Vol 18(5), The method to collect data was observation method with documentation study where data collection was done by systematically collecting 4 天之前 The main advantage of using this method is that it can efficiently recover gold from lowgrade or refractory ores, which are challenging to process using traditional methods Additionally, flotation offers flexibility in choosing reagents and optimizing conditions to Gold Extraction Methods From Three Types of Ore2017年9月1日 The objectives of this research is to describe and analyze the stages done by copper ore mill This research used concept analysis method, The transitional change on the implementation of iso 14001: Media Attributions; Metal deposits are mined in a variety of different ways depending on their depth, shape, size and grade Relatively large deposits that are quite close to surface and somewhat regular in shape are mined using openpit mine methods (Figure 815 in Section 81)Creating a giant hole in the ground is generally cheaper than making an underground 82: Mining and Ore Processing Geosciences LibreTexts
.jpg)
Ball Milling in Lithium Ore Processing: A Comprehensive Guide
2023年5月27日 In this article, we will mainly introduce the lithium ore ball mill Let’s start! 01 Ball Milling Process In conclusion, ball milling is an effective and efficient method for processing lithium ores It is a lowcost method that has a high efficiency rate and can process a large amount of ore in a short amount of time2021年7月6日 For decades the minerals industry has been challenged by inherent variability of ore deposits Quantifying this characteristic of orebodies is becoming increasingly important because the mining Comminution a Heart of Mineral Processing ResearchGate2021年5月31日 DOI: 103390/APP Corpus ID: ; A Method of Ore Blending Based on the Quality of Beneficiation and Its Application in a Concentrator @article{Liu2021AMO, title={A Method of Ore Blending Based on the Quality of Beneficiation and Its Application in a Concentrator}, author={Bingyu Liu and Zhang Dingsen and Xianwen Gao}, journal={Applied [PDF] A Method of Ore Blending Based on the Quality of 2004年4月17日 Gold process mineralogy addresses all issues related to gold ore processing by the detailed study of an ore or a mill product A pretreatment method for upgrading gold from a polymetallic Gold process mineralogy: Objectives, techniques,
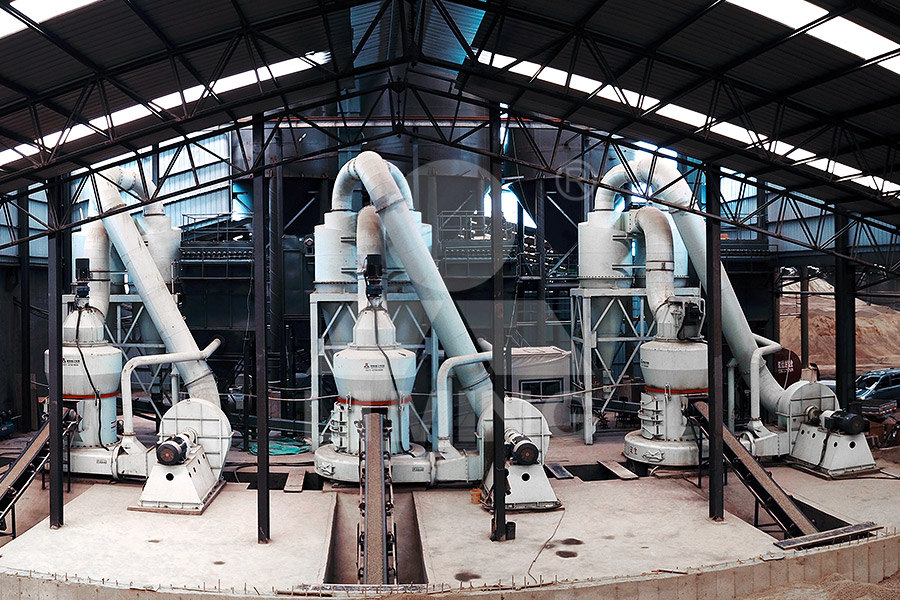
Metallurgists Mineral Processing Engineers 911Metallurgist
911 Metallurgist can enter the scene and see what you have become blind to We can fix issues in ways you never thought possible Our fresh eyes will open new opportunities for your plant Each mineral processing plant has varied ore types, mining equipment, (crusher, ball mill, flotation, tailings), and management (operating) philosophyThe evaluation and prioritization of variables 2021年2月26日 Milling is among the most energyconsuming technological stages of copper ore processing It is performed in mills, which are machines of high rotational masses The start of a mill filled to capacity requires Energy Efficiency Analysis of Copper Ore Ball Mill When the material exits the mill, the iron ore is classified using cyclones or vibrating screens that separate fine and large particles The large particles are diverted back into the crusher and the fine particles will undergo a spiral gravity separation process 5The six main steps of iron ore processing Multotec2017年5月18日 Aiming at addressing the load behavior of iron ore particles in a ball mill, a design of experimental method was used to define a series of discrete element method simulation conditions with two Discrete element method simulations of load behavior with mono
.jpg)
Grinding in Ball Mills: Modeling and Process Control
2012年6月1日 The mill is driven by a girth gear bolted to the shell of (ore, rock, etc) and the grinding media (balls), 52 • The choice of a control method and control system structure for a 2023年4月20日 The paper presents a method for the calibration of industrialscale ball mill model parameters from laboratory Keywords: Comminution, Grinding, ball mill model, powerbased model, Iron Ore and Simulation of industrial PGM and iron ore ball milling circuits from 2015年10月15日 The load estimation method has you physically measure distances in the mill Follow the charts below and pull them into this calculator 911 Metallurgist is a trusted resource for practical insights, solutions, and support in mineral processing engineering, helping industry professionals succeed with proven expertise Estimate Charge Volume of a Grinding Mill Estimate Charge Volume of a Grinding Mill (Method 1)Understanding Mine to Mill is presented in five parts Part A – Setting the Scene provides some definitions of Mine to Mill (M2M) and the historical background A chronology of Mine to Mill developments is followed by brief descriptions of the very wide range of Mine to Mill applications which have been implemented over the last 15 yearsUNDErsTaNDINg MINE TO MILL 911 Metallurgist
.jpg)
Copper Ore Processing Methods 911Metallurgist
2017年4月11日 These ores respond to gravity concentration of the coarser particles of copper, and the finer particles may be recovered by flotation or, as at Calumet Hecla Conglomerate mill, the sand portion of the gravity plant tails may be leached and the slime portion may be