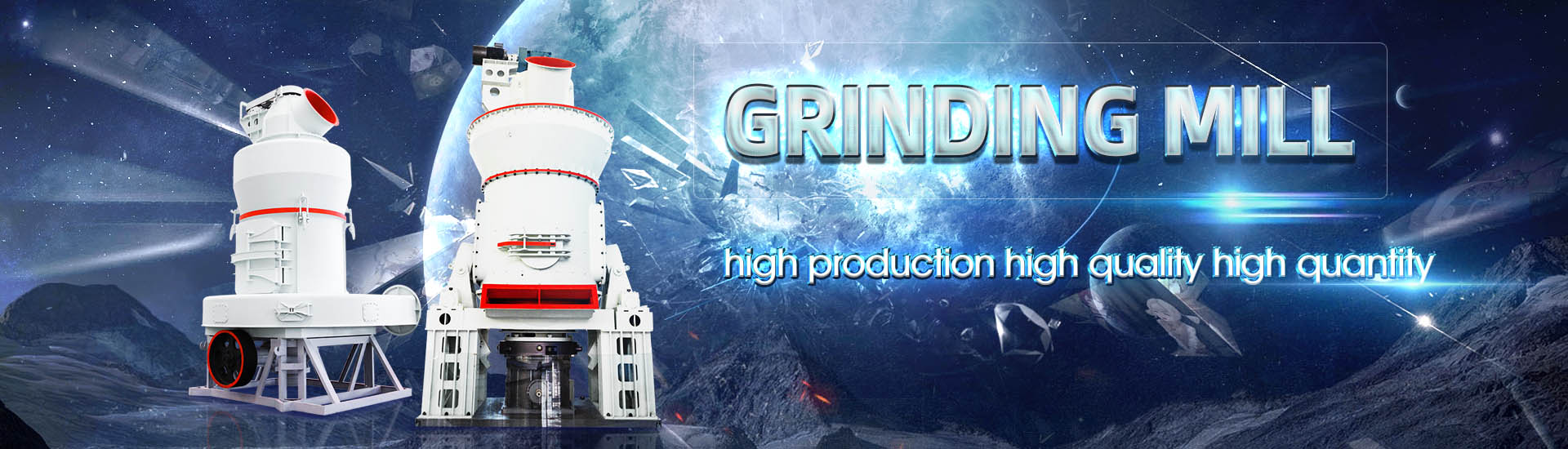
Gypsum crushing station powder making process low energy consumption
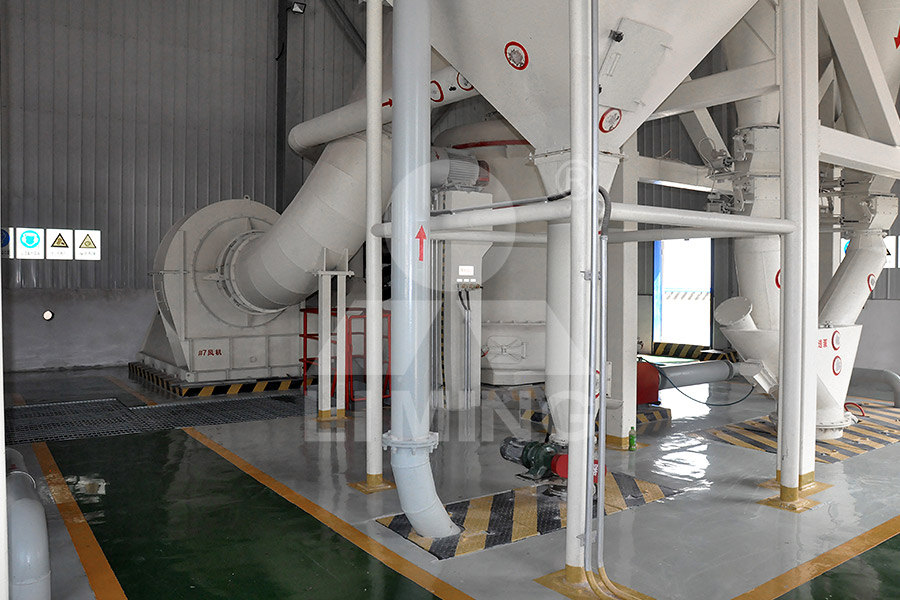
Professional Large Output Low Energy Consumption Gypsum
The gypsum powder machine manufacturer develops, manufactures,installs and commissions the gypsum powder production line The main process includes crushing system, grinding system, Suitable for coarse crushing of large gypsum blocks, with strong crushing ability and high crushing ratio; Impact crusher feed particle size ≤1300mm, production capacity in 302000t/h, suitable for small hardness, Mohs hardness of 2 grade Gypsum Powder Manufacturing Gypsum Powder 2024年1月23日 The production process of gypsum includes three processes: gypsum stone crushing, calcination, and grinding Firstly, the jaw crusher or impact crusher crushes the gypsum raw ore to around 30 millimeters Then Gypsum Powder Grinding And Processing Plant 2024年9月28日 The HGM micro powder grinding mill provides several benefits for gypsum powder processing: High Fineness: Achieves very fine particle sizes, essential for highpurity Gypsum Powder Manufacturing Process Using HGM Micro Powder
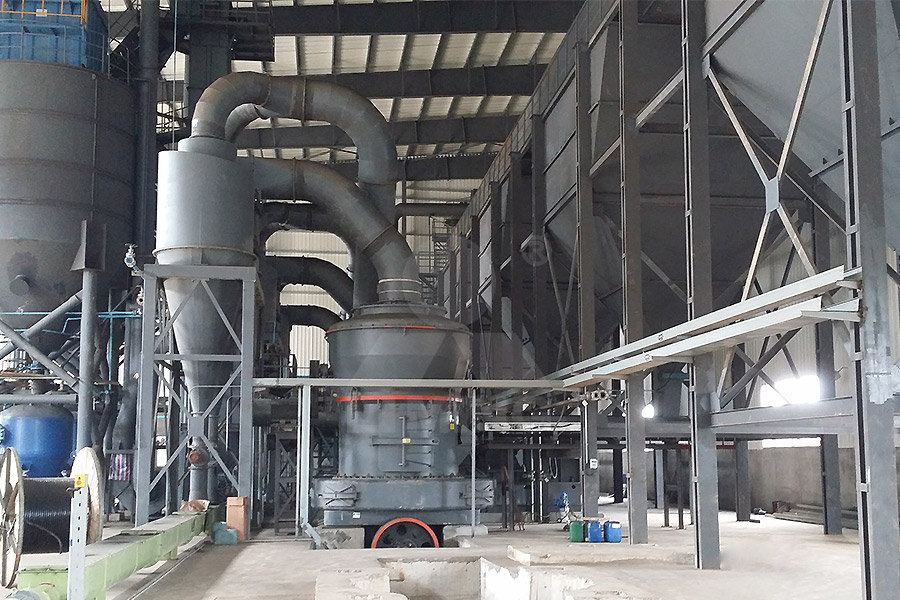
Preparation of Medium–Low Strength Hemihydrate Gypsum from
2024年10月14日 In this study, a medium–low strength (compressive strength 15 ~ 25 MPa) hemihydrate gypsum was prepared with reduced energy consumption to address this 2021年11月1日 FGD gypsum has the characteristics of low energy consumption, recyclability, a rapid production rate and no waste residue or waste water, making it very useful as a wall Production and resource utilization of flue gas desulfurized the calcining process also plays an important role A low purity degree of the feed material requires less water to be evaporated which causes the production rate of the gypsum kettle to Grinding and calcining of gypsum with Pfeiffer grinding plantsEnergy Mineral Equipment; Mining Machinery; Mine Mill; Gypsum powder making machine (9689 products available) Previous slide Next slide Gypsum Powder Manufacturing Process Gypsum Powder Making Machine Gypsum Powder Machines $8,70000$8,88000 $14,50000$14,8000040% Min Order: 1 set Previous slide Next slide Gypsum Chalk Powder Powerful Gypsum Powder Making Machine At Low Prices
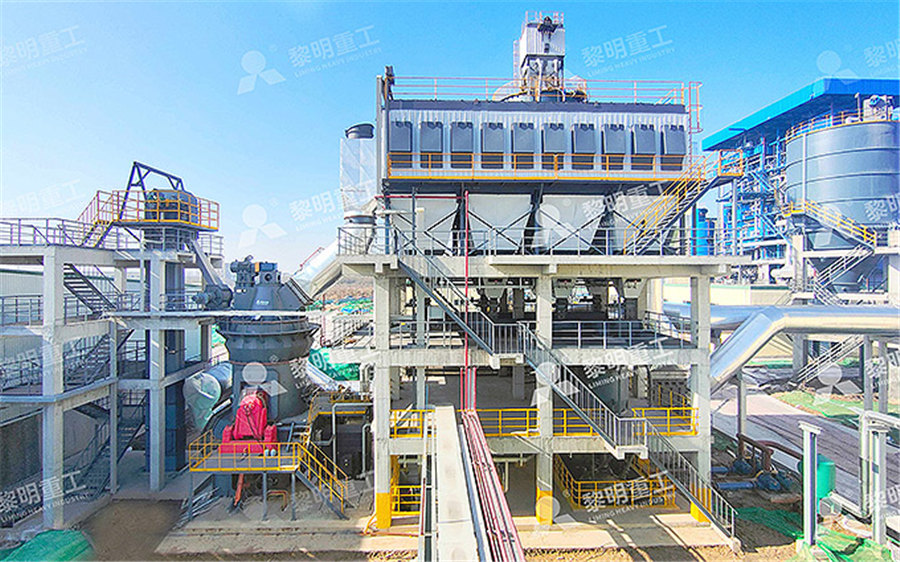
Gypsum calcination process MECRU Heavy Industry
Gypsum products are widely used in construction, building materials, power plants, medicine and other fields Because of their green, environmental protection, energy saving, lightweight and other characteristics, they are Gypsum Powder: 80200mesh Composition: Content of βCaSO41/2H2O (mass fraction) in calcined gypsum should be not less than 75% The Initial Setting Time: Shall Not Be Less Than 3 Minutes, The Final Setting Time: Shall Not Be More Than 20 Minutes 2 Main Technology Gypsum Powder Plant(Nature Gypsum Rock)Gypsum Powder Making Machine Phospho Gypsum Powder 2022年7月20日 Process flow of limestone sand production line 1 Process flow of limestone manufactured sand Sand making: Through the crushed limestone, part of it is directly sent to the stockpile as a finished product, and the other part is crushed and made sand by the sand making machine Screening: The vibrating screen is also responsible for distinguishing the finished Limestone crushing, sand making and grinding processDownload Table Energy consumption in cement making processes and process types a from publication: Carbon Dioxide Emission from the Global Cement Industry The cement industry contributes about Energy consumption in cement making processes and process
.jpg)
Gypsum Powder Making Machine Gypsum Powder Production
Gypsum Powder Making Machine, chamber boiling furnace technology can effectively prevent the mixing of raw materials with gypsum powder in the process of calcining Traditional calcining technologies such as vertical boiling furnace , the motor 24 hours consumption of electricity is 45X24=1080 degrees 3Maintenance costMultiple processes are taken in production of the plant First, gypsum ores are being crushed, conveyed and stored into raw material bin, and then the crushed gypsum ores get grinded into powder with fineness required by the raymond mill, and the gypsum powder is then conveyed into calcining section via metering feeding device to get calcined, and the calcined gypsum gets Gypsum Powder Plant Iron Powder Making MachineIn the process of gypsum production and processing, a gypsum powder ultrafine grinding mill is indispensable Generally speaking, the process of the gypsum production line is as follows: first, crush the gypsum ore to meet the particle size requirements of the mill; then use the ultrafine mill for grinding treatment; then enter the boiling furnace for heating treatment, and finally do store Gypsum Powder Ultrafine Grinding Mill2021年8月4日 CLIRIK gypsum grinding mills are specialized in the production process of 303000 mesh gypsum powder The gypsum powder production process is obtained by grinding natural dihydrate gypsum ore (green gypsum) or industrial byproduct gypsum (desulfurized gypsum, phosphogypsum, etc) through a special mill and heating and calcining at a certain CLIRIK gypsum grinding mill for gypsum powder production process
.jpg)
MATERIAL AND ENERGY BALANCE OF PRODUCTION OF GYPSUM FLUIDIZATION PROCESS
2009年10月16日 Relatively little energy is spent for the production of gypsum binders, about 20 % compared to the other building binders (cement, lime) The reason for this is quite lower temperatures in the Environmental protection: The grinding process uses a closedloop circulation system with negative pressure to minimize dust and noise With a fullpulse dust collector, 99% of dust is removed Low energy consumption: Small footprint, Highefficient Raymond Mill Fote Machinerythe consumption of fuels and from the calcination of limestone This report briefly describes the various stages in the cement production process Details on energy consumption in the US cement industry in 2009 and 2010 are provided, followed by an assessment of various energy efficiency measures applicable to US cement plants 2Energy Efficiency Improvement and Cost Saving Opportunities for 2023年11月2日 Setting up a gypsum powder production line requires careful planning and a good understanding of the overall process Gypsum powder is widely used in the construction industry for making drywall, plaster, and other building materials +29 such as reusing waste materials or reducing energy consumption, How To Set Up a Gypsum Powder Production Line From Scratch
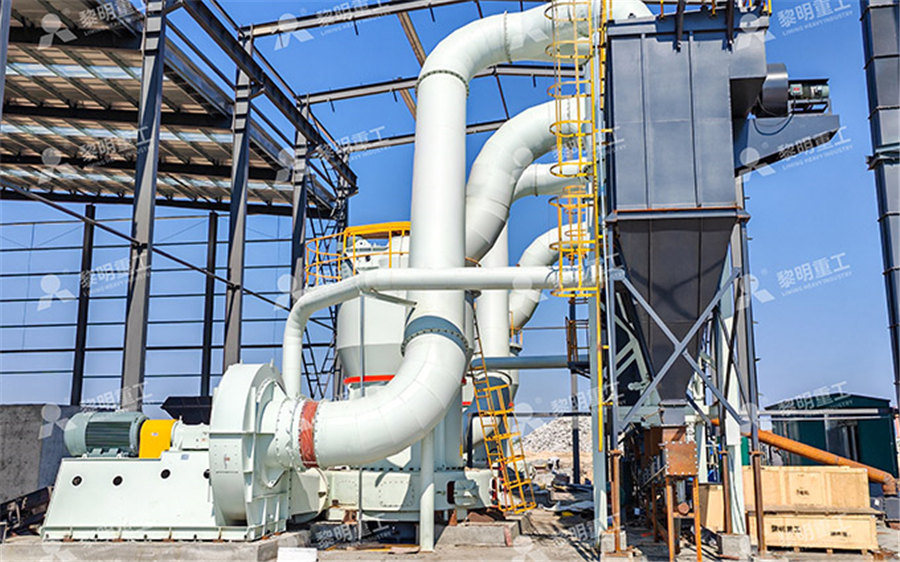
Low Energy Consumption Gypsum Granulator Machinery With
Low Energy Consumption Gypsum Granulator Machinery With Advanced Calcium aluminate, TSP, SSP, Carnallite stone, Metal powder, Fillers, Feed additives, Nicotinic acid, Nicotinic acid amine, Pharmaceutical easy maintenance, simple operation, short process, low energy consumption, high efficiency, low failure rate Control 2023年7月10日 Cement is the primary material for building and civil engineering constructions Therefore, the cement manufacturing sector plays a vital role in the nation's economic developmentCement Manufacturing Process and Its Environmental ImpactOrdinary Portland cement (OPC) is the most widely used binder material, but the OPC calcination process consumes a lot of energy [12]It has been reported that the total CO 2 emissions generated during cement production account for 8 % of the total global CO 2 emissions [11]Compared with silicate cement, geopolymer has the advantages of large raw material Investigation on the compressive strength of desulfurization gypsum 2022年9月6日 The first stage is crushing: The large pieces of gypsum material need to be crushed by the jaw crusher to the fineness that can enter the grinding mill high separation efficiency and low energy consumption the above mentioned gypsum powder making machine can also be used to process many other materials, such as limestone, Gypsum Powder Making Machine Zenith Crusher
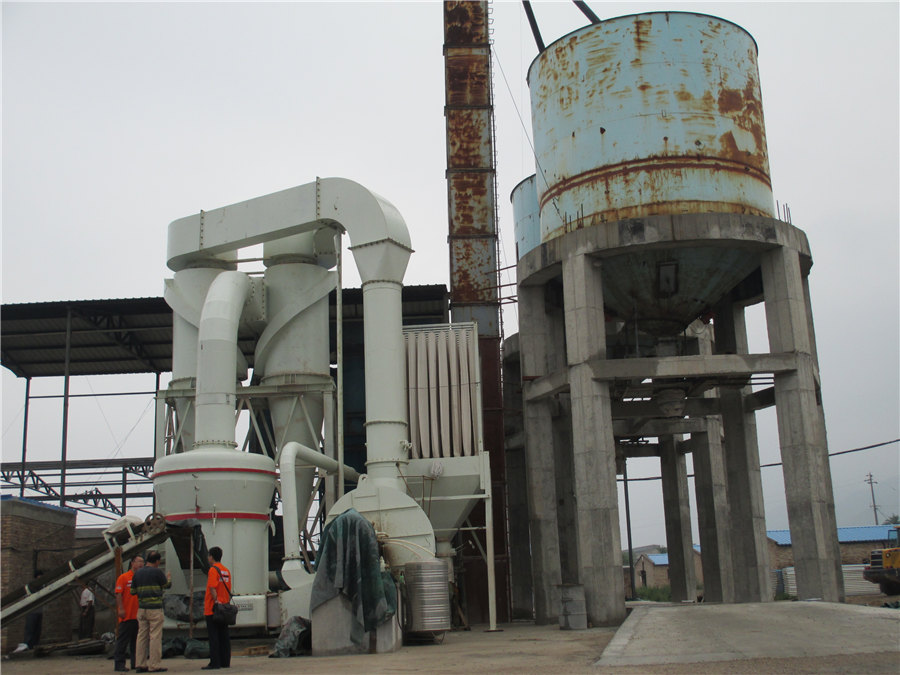
How Does The Gypsum Powder Production Line work?CLIRIKGypsum Making
2021年6月15日 Gypsum Powder Production Line The gypsum crusher machine crushes the large gypsum ore into small particles of less than 30mm and conveys them to the gypsum powder machine for grinding Gypsum powder that reaches the required fineness of the product after grinding is sent to the gypsum making machine boiling oven for calcination A piece is returned 2024年6月28日 Wide application: Suitable for both dry and wet crushing, for materials with up to 15% moisture Onetime forming: Eliminates the need for primary and secondary crushing, reducing costs by approximately 40% Large feed opening: Handles feed sizes up to 1000 mm, making it ideal for coarse crushing Nonclogging: Designed to ensure smooth flow of high What Crusher Should You Choose for Primary Crushing?2016年10月22日 The primary impact of the maximized incorporation of recycled gypsum observed in Fig 2 is a 29 % increase of electricity consumption, which, given the low share of electrical energy in the total energy demand of the process (see Fig 1), results in negligible overall net effect (01 % increase) and total energy consumption remains practically invariable Energy Analysis of the Effects of HighLevel Reincorporation of 2024年8月2日 Here is a list of the essential machinery used in this process: Essential Machinery: Basalt Rock Powder Making MachinesPrimary Crusher: Jaw Crusher: Suitable for primary crushing of large basalt rocks Basalt Powder MachinesSecondary Crusher: Cone Crusher: Used for secondary crushing, reducing the size of the basalt furtherBasalt Rock Powder Making Machines
.jpg)
Assessing the energy efficiency of a jaw crusher ScienceDirect
2014年9月1日 It is well known and taken for granted that the efficiency of energy use by comminution (ie breaking, crushing, grinding) equipment is very low, typically less than 10% Most of the process input power is dissipated as heat and noise and ineffective deformation of the material to be processed and the device itself200tpd Gypsum Powder Calcining Machine with Low Energy Consumption Technology, Find Details and Price about Gypsum Powder Machinery Gypsum Powder Equipment from 200tpd Gypsum Powder Calcining Machine with Low 200tpd Gypsum Powder Calcining Machine with Low 2023年11月1日 The ball mill on site, has problems such as uneven product particle size, low grinding efficiency, insufficient dissociation degree of useful mineral monomers, and high grinding energy consumption[[20], [21], [22], [33], [34]]The existing technological process of the first beneficiation workshop of Gongchangling Concentrator is as follows: twostage crushing, Energy conservation and consumption reduction in grinding The main process of gypsum gypsum powder machine includes crushing system, grinding system, The gypsum powder machine manufacturer has been making this machine for past 20 years The advantage of the gypsum powder machine includes low energy consumption, high automatic level, small installation space, and easy operationNatural Gypsum Powder Production Line Supplier
.jpg)
Types of Crushers: Choosing the Right One for Each Stage
2024年7月17日 Medium crushing: Employ cone crushers or impact crushers in secondary crushing to further reduce material into smaller particles Fine crushing: Utilize sand making machines, roll crushers, fine crushers or compound crushers in tertiary crushing to produce fine sand or powder 4 Capacity requirements Determine the hourly capacity needed2021年7月28日 This ultrafine powder mill can grind solid materials into a fine powder, and the finesse of the product can be adjusted between 3002500 meshes HGM series powder mills have a lot of advantages: Small footprint low energy consumption simple operation saving labor costs Costeffective Special materials, the long service life of accessoriesDolomite Grinding Mill SBM Ultrafine Powder Technology2023年3月6日 As experience shows, when one determines the energypower parameters of crushing and grinding processes by using the existing methods, the power of motors used in drives of existing crushers of various types often turns out to be excessive [10, 11]In this case, the drive will operate at a relatively low load (ratio of the power consumed by the working body Study of the EnergyPower Parameters of the Crushing Process Highgrade gypsum is mostly used as raw material for the production of special gypsum products, such as food, medical, artwork, models and chemical fillers; gypsum mines with calcium sulfate dihydrate content of less than 60% are rarely used; more than 60% The gypsum ore, depending on its content, is used in various fields such as building materials and constructionGypsum Powder Production Line
.jpg)
Lime Powder Making Machine
2021年12月21日 Lime powder making machine can grind limestone into a fine powder lower energy consumption During the operation of the entire crushing system, there is low noise and no dust pollution CLUM vertical roller mill Product features: higher capacity, better powder quality, better overall performance Input size: 010mm2014年4月1日 One thing is certain: the process of crushing entails high energy consumption (Tęsiorowski [15], Numbia et al [19]), and wear off the crusher components (Mierzwa et al [18]), which aggravates Optimal energy management for a jaw crushing process in deep mines2023年12月14日 Compared to ball mills, gypsum grinding mill has higher powder output, higher efficiency, and lower energy consumption The entire production process has a high degree of automation, which saves labor and Feldspar Powder Crushing Grinding Production Line Download Table Energy consumption values of each crusher per tonne from publication: Development of a model estimating energy consumption values of primary and secondary crushers Most of the Energy consumption values of each crusher per tonne
.jpg)
Gypsum plasters for energy conservation
Micropolis – Production and Development of Powder Polymers, Braga, Portugal 1 INTRODUCTION ABSTRACT: Energy conservation in buildings, through materials thermal storage, is relatively low relying only on sensible heat There are however other materials, phase change materials2024年9月28日 The HGM micro powder grinding mill provides several benefits for gypsum powder processing: High Fineness: Achieves very fine particle sizes, essential for highpurity applications Energy Efficiency: Operates with reduced energy consumption, lowering operational costs Versatility: Capable of processing various materials, adapting to market Gypsum Powder Manufacturing Process Using HGM Micro Powder Use of Gypsum Powder Gypsum powder is one of the five major geltype decorative materials It is widely used in many industries and application fields such as construction, building materials, industrial molds and art models, chemical industry and Gypsum Powder Making MachineNatural gypsum powder is made of dihydrate gypsum (CaSO42H2O) after crushing, grinding, the capacity of Raymond mill can up to 20 t/h, and the fineness powder making range is between 50 mesh to 450 mesh, can meet most customers high productivity, low energy consumption, [] How to Overhaul Raymond MillNatural dihydrate gypsum (CaSO42H2O) powder production line
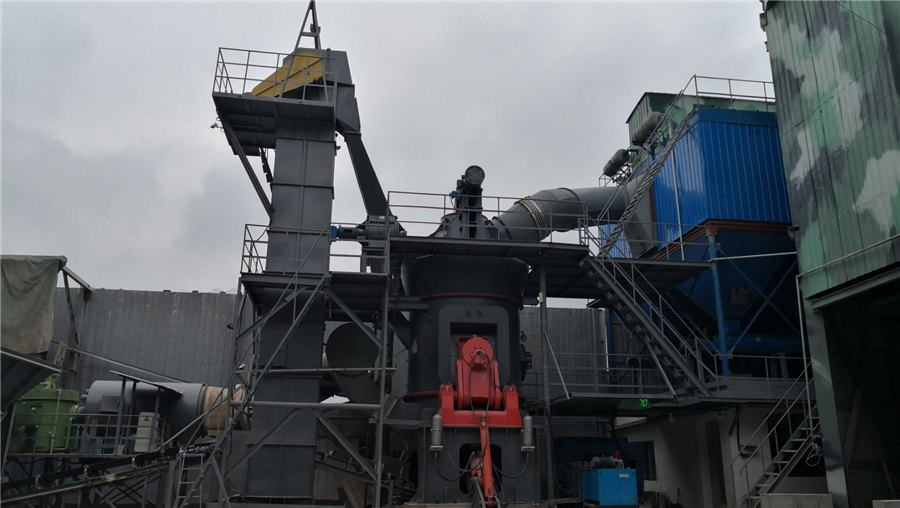
Design and Fabrication of Gypsum Board Making Machine
The main significance out of this is to prevent health related problem that faced on workers, and in addition to this making low cost and it can purchase each individual person 111 Gypsum powder and board There are two types of gypsum powder is produced; a) Gypsum Mold (Ceiling); It used to decorate building construction, It used as a 2003年1月1日 This research project has been done in Sungun copper open pit mine in seven different benches and investigated the effects of increasing powder factor on work index and mill energy consumption The Effects of Blasting on Crushing and Grinding Efficiency and Energy Low energy consumption: The lime kilns are equipped with a vertical preheater and waste heat recovery system, effectively utilizing the hightemperature flue gas generated during the calcination process This minimizes fuel consumption and reduces operating costsLime Kiln for Lime Production Fote Machinery