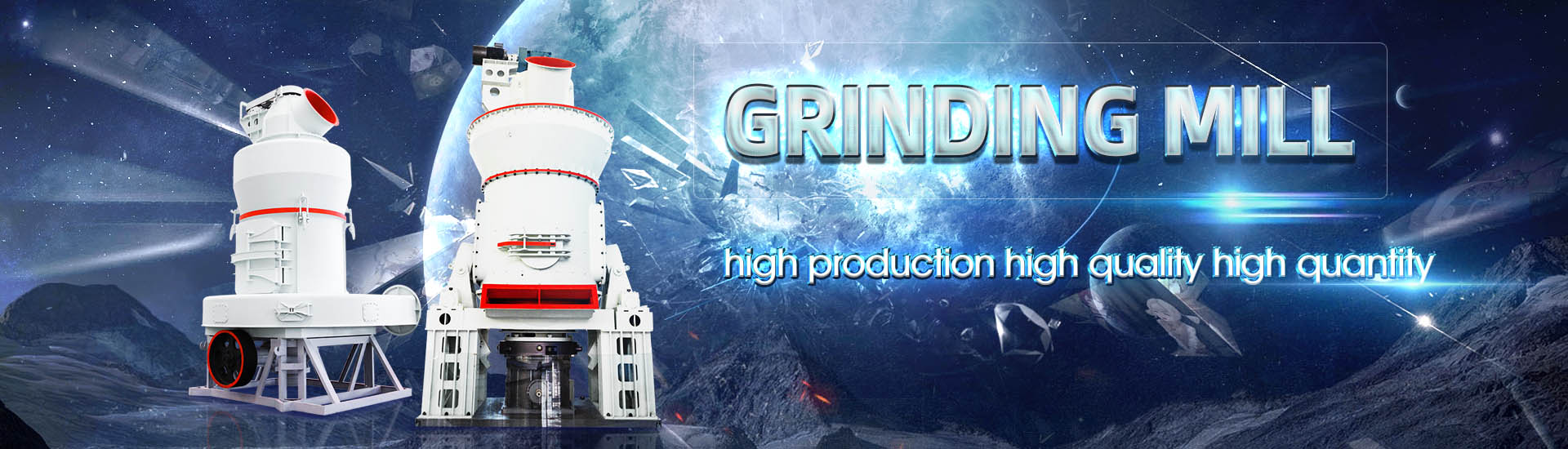
Raw material vertical mill 0 02mm screen residue fineness runs coarse
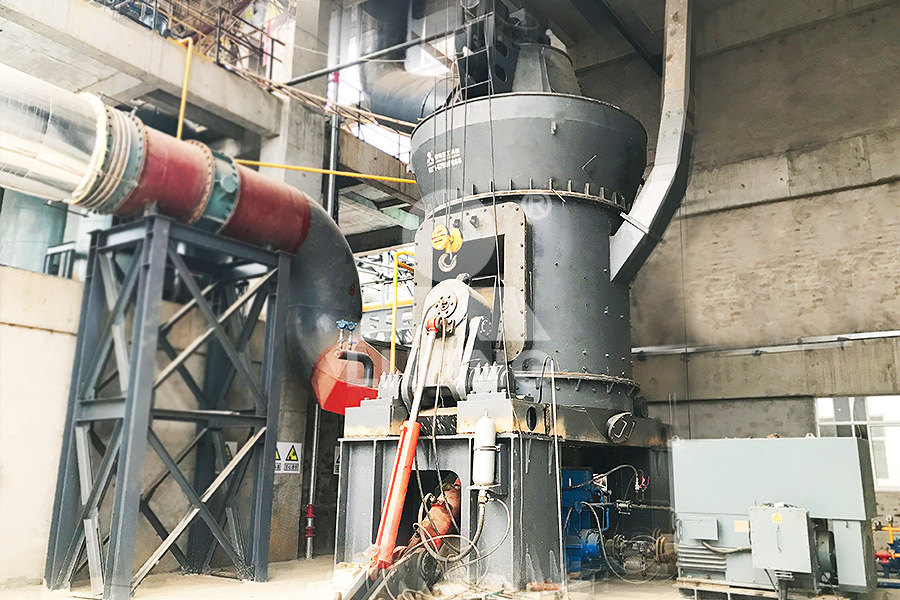
Soft Measurement of 02mm Fineness Screen Residue Based on
This article quantifies the correlation between mill variables and 02mm fineness screening rate through grey correlation degree(GRA), eliminates redundant attributes, and uses genetic The fineness of raw materials used to be controlled at the level of several percents of 90 micron residue in the old wet process or others As the burning method changed toVertical roller mill for raw Application p rocess materials2023年7月11日 The fineness screening rate of raw materials is a key parameter that is of great concern in cement production sites, providing guidance for the grinding and kiln operation Soft Measurement of 02mm Fineness Screen Residue Based on Vertical Roller Mills • Do not believe screen values unless you have checked them • Continuously change Process Parameters and document results to find Optimum • Optimum is highest Optimization of VRM Operation RUCEMRU
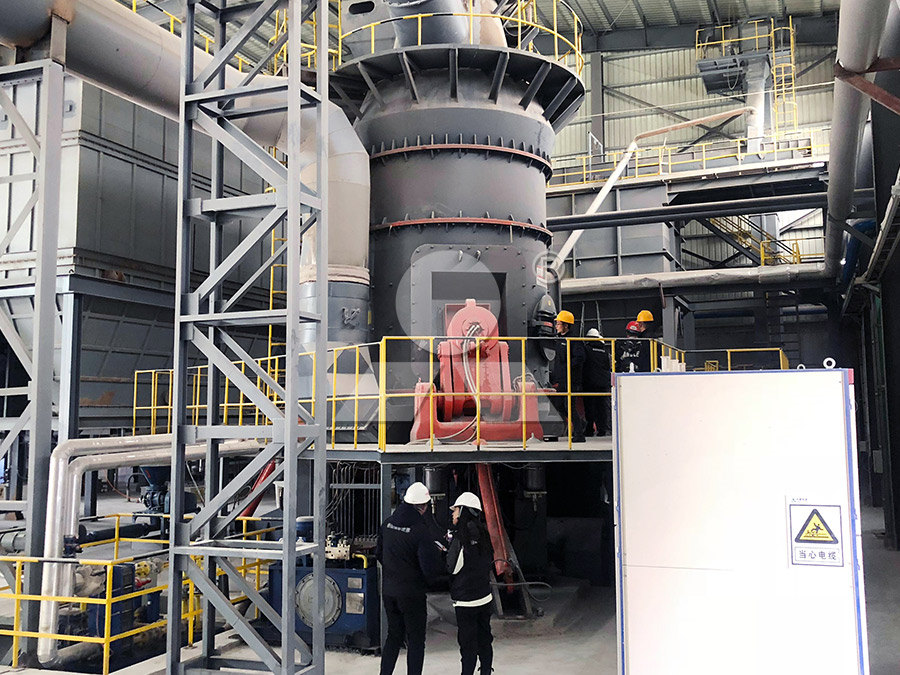
Vertical raw mill Cement Plant
Vertical raw mill is one kind of raw mill, generally used to grind bulk, granular, and powder raw materials into required cement raw meal in the cement manufacturing plantVertical raw mill is an ideal grinding mill that crushing, drying, grinding, 2019年6月22日 Introduction: Raw milling is one of the most important and integral component of cement production process; it is the stage which produces the most important intermediate product ieOptimizing Raw Mills Performance ; the Materials In order to convert these raw materials into clinker and cement, it is necessary to produce a raw mix with a top size of about 02 mm The reduction ratio required for most raw materials is consequently 10002000:02 or 500010,000 It is Everything you need to know about cement Materials This mill, designated the LM 606 has a grinding table with a diameter of 600 m and an installed drive rating of 4 650 kW Even with poor grindability of the raw material this mill is expected to produce an output of 640 t/h at a raw meal fineness corresponding to a residue of about 15 % on a 009 mm sieve The first Loesche mill equipped with sixRedundancy and interchangeability – large vertical roller mills

Soft Measurement of 02mm Fineness Screen Residue Based on
2023年7月11日 This article quantifies the correlation between mill variables and 02mm fineness screening rate through grey correlation degree(GRA), eliminates redundant attributes, and uses genetic algorithm(GA) algorithm to optimize the kernel function parameter and penalty coefficient in the least squares support vector machine LSSVM model using RBF kernel function The 2020年10月24日 Raw meal fineness is the percentage content of 80 µm sieving residue after the cement raw material is ground The accurate prediction of raw meal fineness in the vertical mill system is very Prediction of raw meal fineness in the grinding process of cement raw 1 A 5000t/d cement production line EPC turnkey project in South Africa adopts GRMR5341 raw material vertical mill of CHAENG 2 A 5000t/d cement production line in Henan, China adopts GRMR5341 raw material vertical mill of CHAENG 5000t/d cement production line of Henan Meng Electric Group adopts GRMR5341 raw material vertical mill of CHAENGVertical Raw Mill CHAENGAfter the cement raw material is crushed, it will be sent into the raw mill for further grinding until a certain degree of fineness is reached, and then enter the clinker calcination process From the production experience of many cement plants, the selection of cement equipment , especially raw mill, will directly affect the project investment, production schedule and economic benefitsRaw Mill – Raw Mill In Cement Plant AGICO Cement Raw Mill
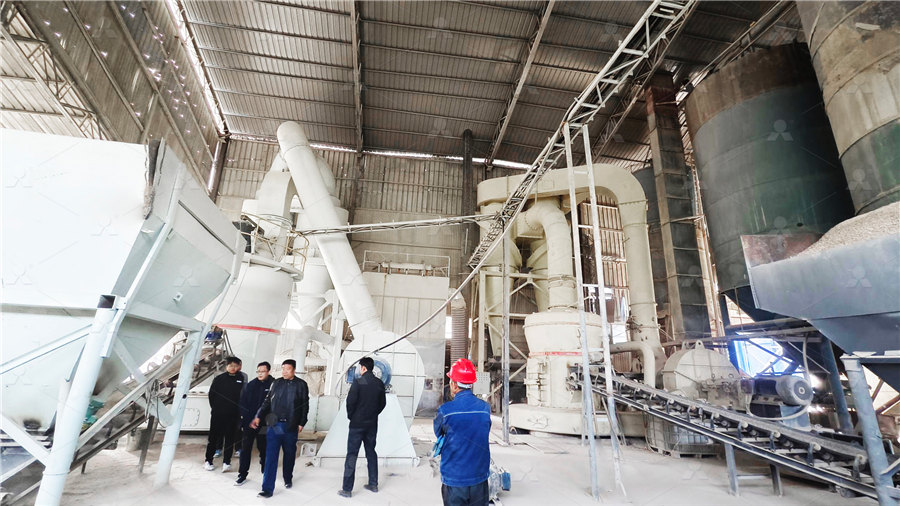
Efficient machine learning model to predict fineness, in a vertical raw
2023年3月1日 This work aims to develop a soft sensor for raw meal fineness in a vertical roller mill of a cement plant The MSE performance for validation data drops down from 003720 to 007019 when model is built without material quality characteristics Modeling vertical roller mill raw meal residue by implementing neural networkThe results of LSF, SM, and AM calculations can be seen in Table 4 Table 4 shows that cement clinker from the raw material substitution of 5, 10, 15, and 20% coal sintered at 1100, 1200, and 1300 The Effect Of Raw Material's Fineness And Lime Saturation The document discusses optimization and operation of vertical roller mills (VRMs) Key points include: 1) Continuously monitor and adjust process parameters to find the optimum operating conditions of highest capacity and Optimization of Vertical Raw Mill Operation PDFRaw mill is generally called cement raw mill, raw mill in cement plant, it refers to a common type of cement equipment in the cement plantIn the cement manufacturing process, raw mill in cement plant grind cement raw materials Raw mill Cement Plant
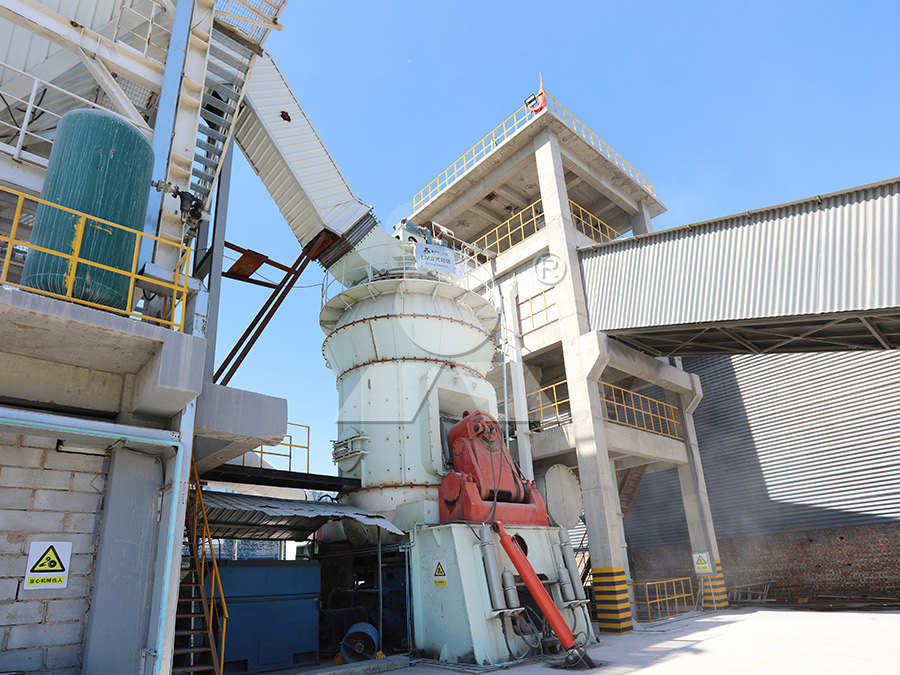
Raw Material Preparation in Cement Manufacturing
In addition, its energysaving effect is better than the vertical mill system The power consumption is about 1350 kWh/t In the areas with small annual rainfall and low water content materials, the roller mill grinding system is gradually Process introduction Vertical coal mill, also known as vertical roller coal mill or vertical coal grinding mill, is a mechanical equipment for crushing and grinding coal into coal powerMainly used for grinding raw coal, bituminous coal, and other fuels into coal powder, which is supplied to rotary kiln and other kilns in the cement plant and thermal power plantcoal grinding machine CHAENG2016年9月1日 At similar millclassifier conditions, characteristic particle sizes of 050 mm for comminuted I1 pellets (compared to 083 mm for material within I1 pellets) and of 056 mm for comminuted I2 Operational parameters affecting the vertical roller mill PROCESS TRAINING for operators of Vertical RAW Mills Heating of mill and grinding For drying the wet raw material it is necessary that prior to the mill start up the grinding plant isheated for some timeOtherwise the cold grinding plant would take away too much heat from the drying process fineness of product, residue on 90)1 sievePROCESS TRAINING for operators of Vertical RAW Mills
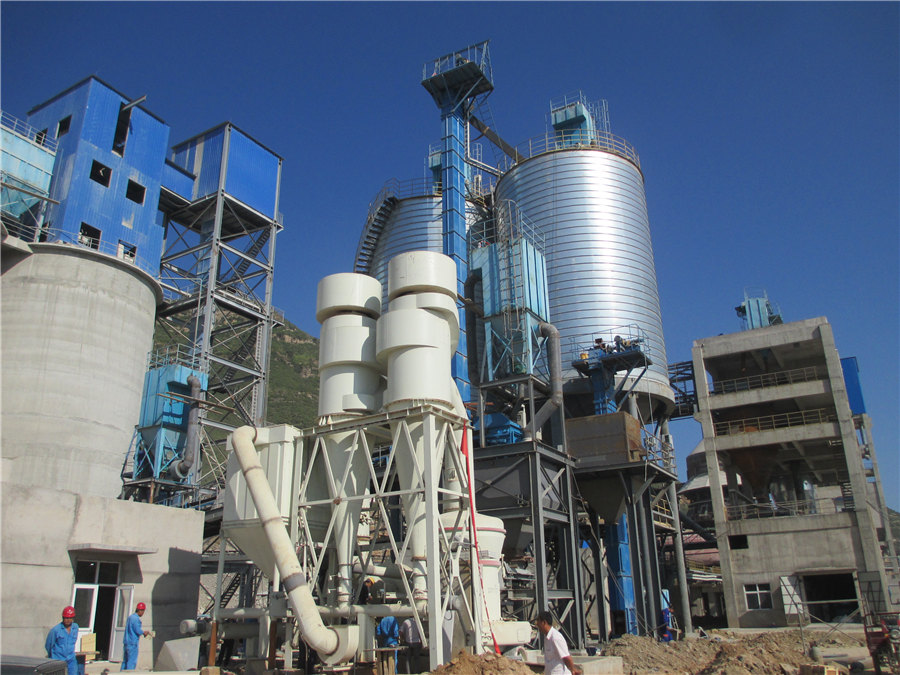
CLUM Ultrafine Vertical Grinding Mill
Raw material: crushing, jaw crushing, hammer crushing, etc Raw material conveying: hoists, belt scales, buffer bins, starshaped feeding valves, screw conveyors, etc Superfine grinding and classification: Superfine vertical grinding mill main machine and multirotor powder separator: Finished product collection: Air box pulse bag filter2020年10月24日 Raw meal fineness is the percentage content of 80 µm sieving residue after the cement raw material is ground The accurate prediction of raw meal fineness in the vertical mill system is very helpful for the operator to control the vertical millPrediction of raw meal fineness in the grinding process of cement raw 2024年3月4日 1 Vertical Roller Mills • Do not believe screen values unless you have checked them • Continuously change Process Parameters and document results to find Optimum • Optimum is highest capacity at lowest power consumption • Be sensitive to changes of feed material and adapt parameters • Focus on Relevant Process Parameters only • Optimize Optimisation of Pfeiffer raw mill for cement plant PPT SlideShare2021年1月22日 In the whole process of cement production, the electricity consumption of a raw material mill accounts for about 24% of the total Based on the statistics of the electricity consumption of the raw A Survey and Analysis on Electricity Consumption of Raw Material Mill
.jpg)
Modeling Vertical Roller Mill Raw Meal Residue by
Request PDF On Jun 1, 2019, Hendri Fernandes and others published Modeling Vertical Roller Mill Raw Meal Residue by Implementing Neural Network Find, read and cite all the research you need on Prediction of raw meal fineness in the grinding process of cement raw material: A twodimensional convolutional neural network prediction method Proceedings of the Institution of Mechanical Engineers, Part I: Journal of Systems and Control Engineering ( IF 16) Pub Date : , DOI: 101177/65447Prediction of raw meal fineness in the grinding process of cement raw 2022年10月3日 Raw materials grinding process is a first step of cement production which is has an important role in the first grinding step Vertical Raw Mill is a main equipment that is used in grinding or (PDF) ANALISA KINERJA ALAT VERTICAL RAW MILL PABRIK II PT A new raw mill dassifier is now invariably of the ‘highefficiency’, rotating cagetype: the rotational speed controls product fineness at constant gas flow Raw milling can consume 10 30kWh/t; depending upon the materials and equipment, and developments aim to reduce this figureRaw milling and blending INFINITY FOR CEMENT EQUIPMENT
.jpg)
Review on vertical roller mill in cement industry its
2021年1月1日 Stacking Reclaiming of Raw material: Swing type stacker Reclaimer: Limestone other raw material are stored in open area into a longitudinal storage unit called stockpile through Stacker These are then extracted transversely from the stockpile through reclaimer: 3: Raw Meal Grinding Homogenization: Grinding Mill Vertical Roller Mill Process introduction GRMC coal vertical mill produced by CHAENG adopts a special structure design and production technology, and the quality is up to the leading level in China It is the first choice equipment for grinding raw coal and bituminous coal 1 The raw coal is screened from the raw coal storage yard and then dropped onto the belt conveyor through the grid screenCOAL VERTICAL MILL Xinxiang Great Wall Machinery Co, Ltdraw material grinding, a modular vertical roller mill with 5 m table diameter and 4 rollers was added The existing kiln systems were partly modernized, one kiln system was replaced by new system Grinding Process Optimization Featuring Case Studies and A vertical roller mill is an energysaving mill that meets market demand The finished product fineness The raw material moisture The finished product moisture Main motor power(kW) HLM1300K 1040 084037mm (20400 mesh) ≤15% ≤1% 200 HLM1500K 1350 280 HLM1700K 1870 400 HLM1900K Energysaving and Efficient Vertical Roller Mill Fote Machinery
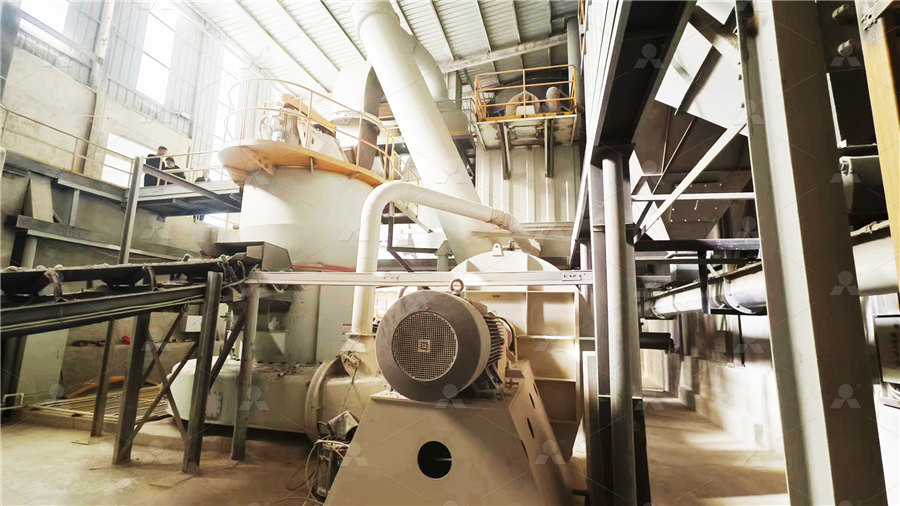
A Survey and Analysis on Electricity Consumption of Raw Material Mill
Sustainability 2021, 13, 1126 3 of 11 Sustainability 2021, 13, x FOR PEER REVIEW 4 of 11 At present, the diameter of the ball mill has reached 5 6 m, and the unit output can reachPart Three: Raw Mill Process of Raw Mill The proportioned raw material is feed first to a grinding mill In the mill, particles ground in to very fine sizes In the grinding unit, drying, grinding and mixing takes place simultaneously Hot gas from clinker burning unit is passed into the grinding unit to assist the drying and grinding processCement Manufacturing Process INFINITY FOR CEMENT EQUIPMENTThe advantages of the vertical roller mill include high grinding efficiency and low energy consumption For raw materials and cement clinker, the vertical roller mill is an excellent grinding solution due to its relatively low installation cost, ease of operation and maintenance, energy savings, and good product qualityVertical roller mill DARKOVertical Roller SINOMALY produces cement raw material grinding mills in various specifications These machines are suitable for grinding mill production lines with an output of 2500t/d, 3200t/d, 4000t/d, 5000t/d, 6000t/d and 8000t/d Vertical Roller Mill for Cement Raw Material
.jpg)
Prediction of raw meal fineness in the grinding process of cement raw
2020年10月24日 A twodimensional convolutional neural network method is proposed that is used to predict raw meal fineness during the grinding process of raw material and is proved to be very effective by comparing with the stateoftheart methods Raw meal fineness is the percentage content of 80 µm sieving residue after the cement raw material is ground The This study proposes a method for modeling the Vertical Roller Mill (VRM) to predict residue 90 micron and residue 200 micron of the raw meal product using Back Propagation Neural Network (BPNN) The modelling step is input preparation, Artificial Neural Network (ANN) structure determination, optimizer and loss function selection, training ANN and model evaluation In Modeling Vertical Roller Mill Raw Meal Residue by Implementing Neural 2022年12月1日 The procedure runs in linear time with 80 µm sieving residue after the cement raw material is ground The accurate prediction of raw meal fineness in the vertical mill system is very Efficient machine learning model to predict fineness, in a vertical raw 2014年4月1日 For decades vertical roller mills have been in use in the cement industry for the grinding of cement raw material and coal Since the 1980's this mill type has also been used for combined or (PDF) The latest innovative technology for vertical roller mills
.jpg)
ANALISA KINERJA ALAT VERTICAL RAW MILL PABRIK II PT
Roller; Roller pada Vertical Raw Mill berfungsi sebagai media penggilingan material ke meja Roller Vertical Raw Mill berjumlah empat buah dengan diameter 2,5 m2019年9月1日 The main difference between the two equipment is that ball mill can be regarded as a homogeneous phase along the radial direction, but material and gas in VRM are usually heterogeneous and the working conditions are much more complex than ball mill Besides, fineness of raw meal at the outlet of VRM is greatly affected by various factors, such A distributed PCATSS based soft sensor for raw meal fineness Adaptive Dynamic Programming in Raw Meal Fineness Control of Vertical Mill Grinding Process Based on Extreme Learning Machine Lin Xiaofeng, Kong Weikai (Guangxi University, Nanning , China) Abstract: The grinding process of vertical mill raw meal in cement industry features nonlinear, strongAdaptive Dynamic Programming in Raw Meal Fineness Control of Vertical