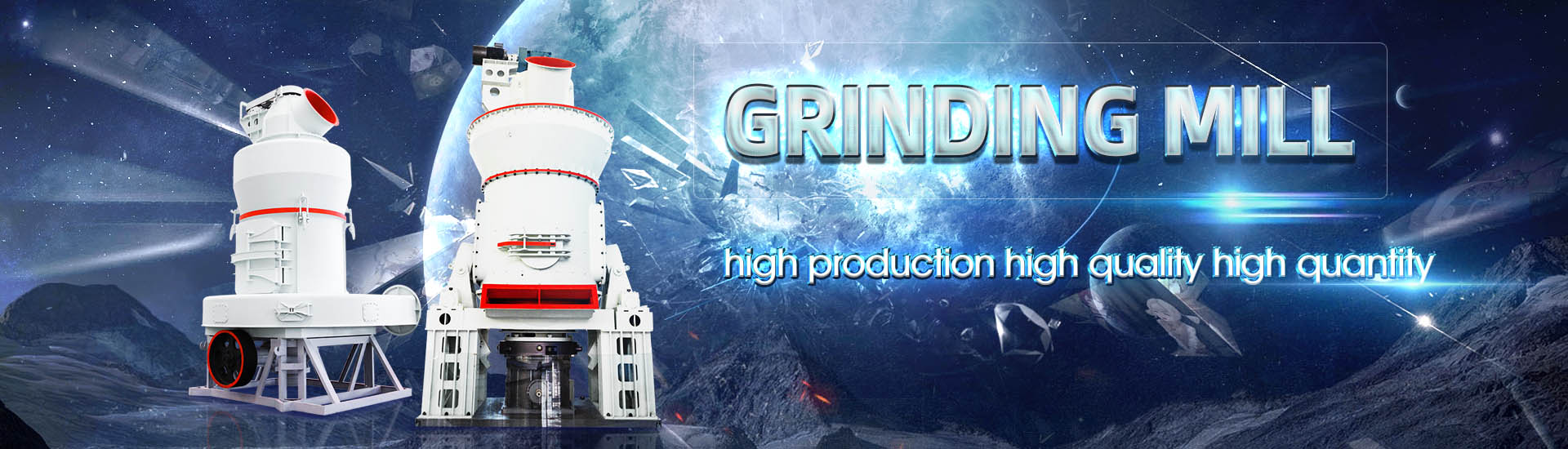
The temperature range of the calcining zone of the lime furnace is
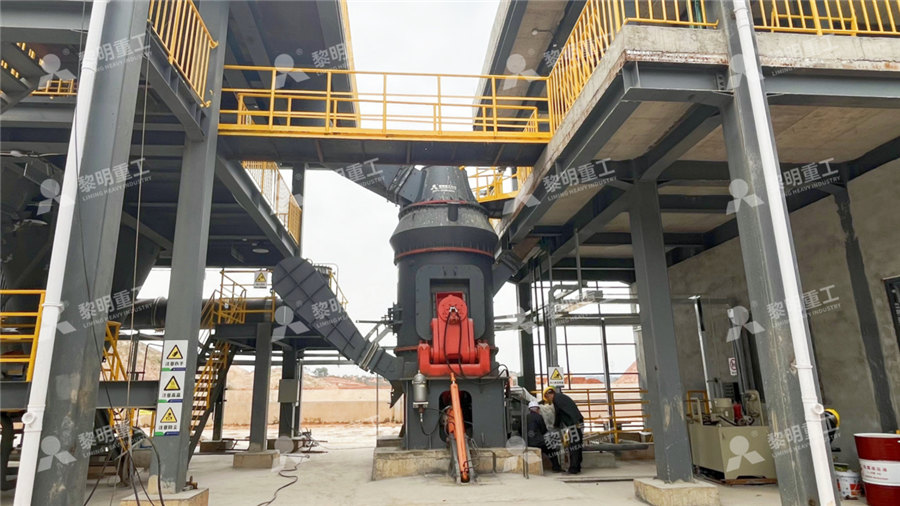
New PFR lime kiln process with blast furnace gas and oxygen
he typical average temperature in the burning zone is approximately 950 °C This is about 13 °C higher than the theoretical calcination temperature of the k by the parallel flow of combustion 2022年10月1日 The temperatures of the flue gas and the bed range between 1000 – 1400 °C and 800–1000 °C, respectively, in the burning zone, while the cooling leads to a final solid Decarbonising the lime industry: Stateoftheart ScienceDirect2001年4月1日 The optimum calcination temperature is ∼900°C, which was the temperature performed in traditional limekilns Concerning the quicklime, the reactivity is related to its The effects of limestone characteristics and calcination 2007年6月1日 Calcination of limestone in annular shaft kilns takes place in three zones: in the upper firing zone, in the middle firing zone, and in the uniflow zone below the lower burners In Analysis of calcination parameters and the temperature profile in
.jpg)
LIME KILNS, HEAT TRANSFER, CONTROL AND COMBUSTION
2 from 12% CO 2 near the burner to about 25% in the backend, the decomposition temperature varies from 800 to 820°C (1470 to 1510°F) During calcination, the temperature of the solids 2014年6月12日 The experiment confirmed that calcination temperatures from 850 to 1200 C can be used to produce natural hydraulic lime from the selected limestone The optimal calcination (PDF) Determination of optimal burning temperature ranges for 2021年3月3日 In fact, a transition (the lime spectrum — Fig 71) can be clearly established among air lime (manufactured at 1000 °C from pure limestone), hydraulic lime (1000–1200 °C Lime SpringerLink2022年6月30日 To investigate the effect of different particle size combinations on calcination, this study uses a porous media model and a shrinking core model to simulate the calcination Numerical Simulation Study of Mixed Particle Size Calcination
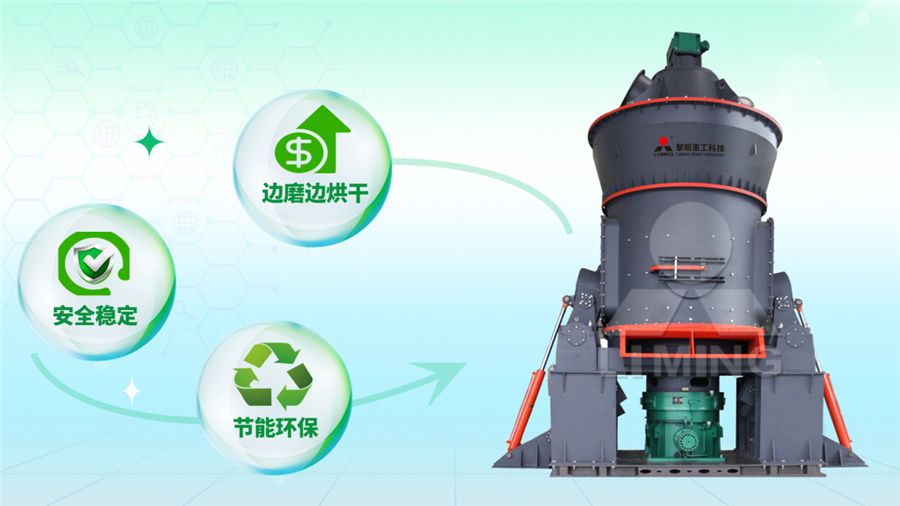
Everything you need to know about Kiln System
If this temperature is reached close to the discharge of the kiln (nose), the burning zone will be short; if this temperature is reached sooner, the burning zone will be longer When kiln feed is placed into the kiln system, the material temperature The division of the three zones of the annular shaft lime kiln: the preheating zone is about 9 meters, and the temperature range is from the top temperature of 90140°C to the junction of preheating and calcination at 850900°C; the calcining Annular Shaft Lime Kilns, One of the Most Popular Calcining Biomass ash abstract The influence of calcining temperature on the pozzolanic properties of elephant grass ash (EGA) for application as a supplementary cementitious material is reported Five different calcining temperatures were used (ranging from 500 to 900 C for 3 h at 100 C increments) after a first calcining step at 350 CInfluence of calcining temperature on the pozzolanic Hot gasses from the calcining zone migrate upward, warming the stone in the preheating zone Finished lime drops into the cooling zone, where cool air is blown through it Air blown into the cooling zone carries recovered heat upward into the calcining zone, where it also provides air for Combustion Cooled lime is removed from the bottom Comparison of lime kiln types Blitzco
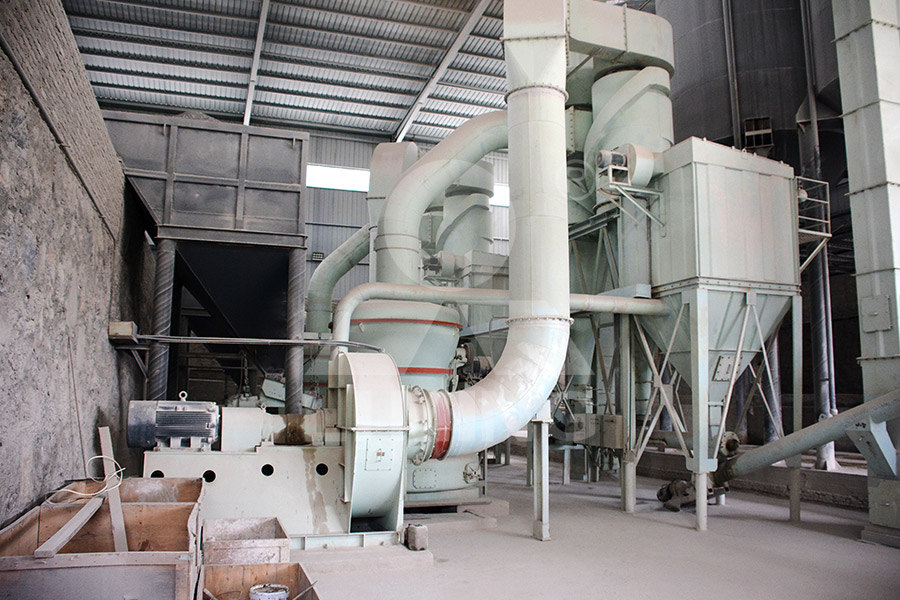
(PDF) Influence of Calcining Temperature on the Activation of
2007年1月7日 The present paper describes a study of the influence of calcining temperature (800 and 1000°C) on the activation of sugarcane bagasse The reaction kinetics in a bagasse ashlime system were Calcination is usually carried out in furnaces, retorts or kilns, and often, materials are racked over or stirred to make sure the product is uniform One of the common arrangements that is used for calcination is the reverberatory furnace The typical construction and Calcination Definition, Examples, Process, Calcination of 2015年11月1日 Mixtures of LMP and cement presented the highest available lime content After calcining at 8001200 °C, mixtures of 90 wt % LMP and 10 wt % fly ash contained lime (CaO) and dicalcium silicate Dewatering of waste lime mud and after calcining its applications the flow of air through the discharge door into the kiln helped to recoup heat from burnt lime The exhaust gas temperature was in the range of 38 – 440c he size of the various zones of the kiln are given in Table 3 Table 3: Size of kiln zones Zones Parameters t k H k Di V k m 3 Preheating zone 014m 081m 020m 254x103FUNDAMENTAL APPROACH TO THE DESIGN OF VERTICAL SHAFT LIME
.jpg)
22 Lime Kiln Principles And Operations TAPPI
LIME KILN PRINCIPLES AND OPERATIONS Terry N Adams, PhD Technical Consultant 900 Lenora Street Unit 200 Seattle WA 98121 ROTARY LIME KILNS Slides 1 and 2 are the title and outline for the presentation Slide 3, below, shows a schematic of the exterior of a modern rotary limereburning kiln Slide 4 shows a schematic of the interior features of aThe cycling produces a long burning zone of constant, relatively low temperature (around 950 °C) that is ideal for the production of high quality soft burned reactive lime With exhaust gas temperatures as low as 120 °C and lime temperature at kiln outlet in 80 °C range the heat loss of the regenerative kiln is minimal, fuel consumption is as low as 36 MJ/kgLime kiln WikipediaFigure 51 shows the different use of lime (CaO) [1] World production of lime in 2017 was 350 million ton [2] 52 Process Lime is produced by calcinations of limestone (CaCO 3) at a temperature around 950 °C CaCO 3 decomposes at high temperature according to the reaction 51 to produce lime (CaO) CaCO 32 ˜˚Heat CaOC˜ O (51)Chapter 5 Refractories for Lime Calcination Springer2018年9月1日 Gas temperature and specific heat capacity at the end of the reaction zone t g = 570 °C, c g = 12053 kJ/kgK Temperature of the dolomite at the end of the reaction zone(PDF) Energy optimisation of vertical shaft kiln
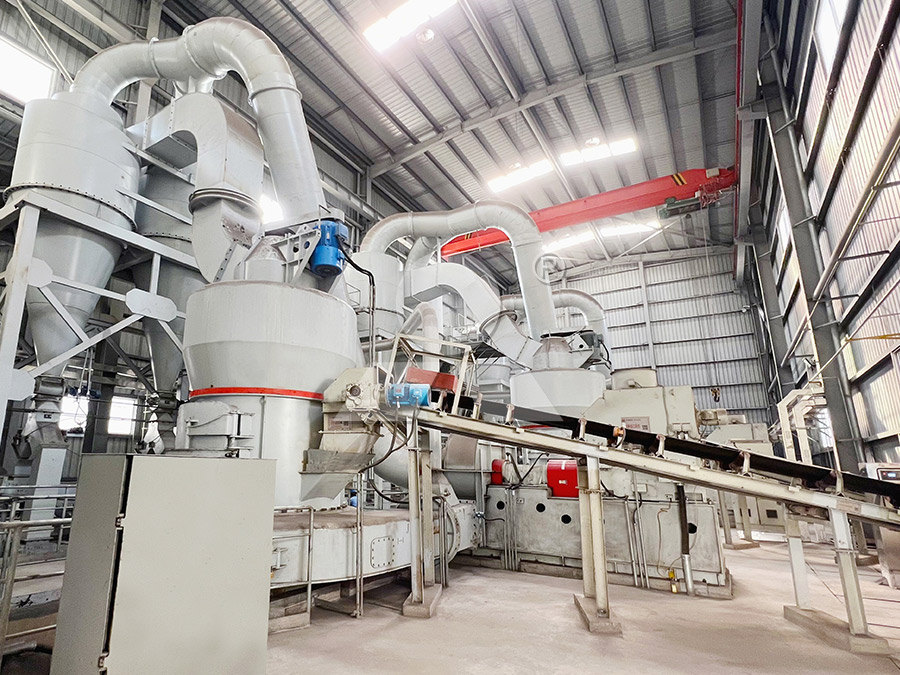
Its Processing and Application in Iron and Steel Industry
2017年7月7日 Application of limestone and lime in iron and steel plant During the production of iron by blast furnace (BF) route, limestone is added either in the process of sintering or as a direct feed in the blast furnace Limestone is normally added during ironmaking for obtaining either neutral or slight basic BF slagThe annual world lime production amounts to approximately 350 million tons The most efficient and ecological way to calcine limestone and dolomite is the use of modern shaft kilnsOperating principle and temperature profile of the HPS lime kilnIn the calcining process, the kiln is usually divided into three zones, ie, preheating zone, calcining zone and cooling zone, as shown in Fig 1 The preheating zone is at the beginning of the Schematic diagram of the calcining process in a carbon rotary Calcination is thermal treatment of a solid chemical compound (eg mixed carbonate ores) whereby the compound is raised to high temperature without melting under restricted supply of ambient oxygen (ie gaseous O 2 fraction of air), generally for the purpose of removing impurities or volatile substances and/or to incur thermal decomposition [1]Calcination Wikipedia
.jpg)
Clinkerization Cement Plant Optimization
Lower Cyclone Temperature is considered most important and stable temperature in preheater to control precalciner fuel rate It is generally maintained manually or by PID loop in the range of ±10 0 C, in the range 850900 0C to ensure calcination between 90% to 95 % Burning Zone Temperature is monitored by2020年11月16日 The reheating furnace of the steel industry was evaluated in the present study, which uses the gas mixture from coke oven (COG), steelmaking process “LinzDonawitz” (LDG) and blast furnace (BFG)(PDF) REHEATING FURNACES IN THE STEEL INDUSTRY2017年6月28日 Stage 1 – CaCO3MgCO3 = CaCO3 MgO + CO2 (in the temperature range of 550 deg C to 700 deg there exists an imbalance between the heat available from the calcining zone and heat required in the it is used in calcined form As a fluxing material, it has a dual role In its first role it is a source of some lime (CaO) Dolomite – Its Processing and Application in Iron and IspatGuru2023年9月15日 As can be seen from the process described in Fig 3, the implementation process of the proposed soft sensing model is as follows Step 1 Collect the production data of the lime rotary kiln, including gas flow, gas pressure, primary exhaust gas temperature, etc Data preprocessing removes abnormal data And according to a certain proportion to generate Soft sensing of calcination zone temperature of lime rotary kiln
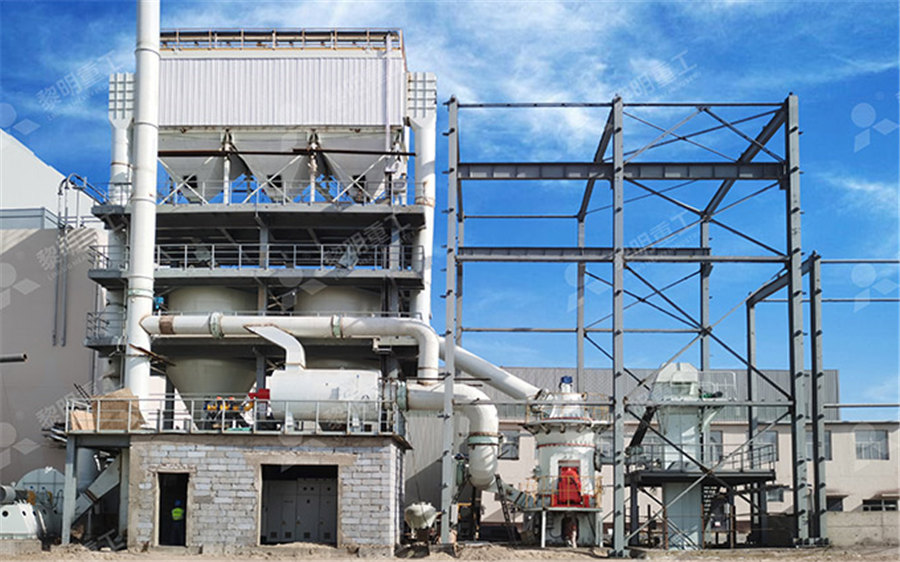
The effects of limestone characteristics and calcination
Analyses were performed in samples of limestone and lime putty in static air atmosphere at a temperature range of 30± 1000°C and a gradient of 10°C/ min (Netzsch 409 EP DTA/TG) Mercury intrusion porosimetry (Fisons, 2016年1月6日 The complex nature of the lime calcining process with its long time delays, variable feed zone and final temperature of sintering zone is 1300°C and use of rotary kiln in speed is 1 to 3 rpmthe lime industry at calcinations temperature in the zone of 950 1000°C According to LesA Review on Design and Thermal Analysis of Rotary Kiln for Lime THE SEMIDRY (LEPOL) KILN The drying, the dissociation of the chemical water, the preheating to calcining temperature, and even partial calcination in this system takes place outside the rotary kiln, ie, in the grate preheaterHence, EVERYTHING YOU NEED TO KNOW ABOUT 2021年1月1日 Lime is a product derived from the thermal decomposition of limestone (mainly calcium carbonate, CaCO3) into quicklime (CaO) and carbon dioxide (CO2), also called calcination(PDF) Natural and enhanced carbonation of lime in its different
.jpg)
The Effects of Limestone Characteristics and Calcination Temperature on
2001年4月1日 temperature range of 30 Therefore, lime putty was dried out in a furnace and DTA/ TG was performed in samples of lime powder in order to estimate the Ca(OH) 2 content Since this content was2001年4月1日 Analyses were performed in samples of limestone and lime putty in static air atmosphere at a temperature range of 30–1000°C and a gradient of 10°C/min (Netzsch 409 EP DTA/TG) • Mercury intrusion porosimetry (Fisons, Porosimeter 2000) was used to measure the microstructural characteristics of limestone, quicklime, and solid lime puttyThe effects of limestone characteristics and calcination temperature to 1975年6月23日 Control Engineering Laboratory, University of Oulu has been active in lime kiln modelling and control area since the very early modelling studies in 70's [Uronen et al, 1975 [Uronen et al (PDF) Simulation study of the lime kiln ResearchGateThe annual world lime production amounts to approximately 350 million tons The most efficient and ecological way to calcine limestone and dolomite is the use of modern shaft kilnsFunctional principle of the mixedfeed lime kiln
.jpg)
Chemistry of the Ironmaking by Blast Furnace Process
2013年11月22日 In the high temperature zone of the BF, these compounds are volatized and as they rise toward the top of the furnace they condense around cooling plates and cause corrosion They can also condense in uptakes and downcomers where they form accretions which can eventually restrict the passage of the top gas, or react to form HCl (hydrochloric) acid and 2020年4月14日 It shows that the best burning temperature as can be seen is around 740 °C, and calciner temperature can be controlled accurately, and the range of temperature fluctuation is very small Fig 7 Mortar strength, reactivity index and Research and Design of Suspension Calcining Technology and 2021年9月2日 The calcining zone of shaft kiln has the highest operating temperature that necessitates the selection of higher quality basic brick to optimize the refractory campaign life Refractories of arch and connecting channel areas are most failure prone due to the load on the arches which support the entire flue chamber of the kilns and high temperature at the Improving Health and Productivity of Calcining Kiln Through 2016年10月15日 Also, the paper reports on the influence of calcining temperature (500, 600 and 700 °C) on the pozzolanic activation of the bamboo leaves The results show good pozzolanic properties of bamboo leaf ashes for temperatures between 500 and 700°C, and only a little difference on the activation of bamboo leaf ash as a function of the calcining temperature appliedPozzolanic Characterization of Cuban Bamboo Leaf Ash: Calcining
.jpg)
(PDF) Improving the rotary kilnelectric furnace
2021年9月16日 PDF Ferronickel contains 60–80 wt% Fe and 40–20 wt% Ni and is a feedstock for manufacturing stainless steel and other ferrous alloys The primary Find, read and cite all the research Download scientific diagram Main zones, chemical reactions, and energy use in a shaft kiln [21, 22] Figure 4 Zones and temperature profiles in the shaft kiln from publication: Energy Main zones, chemical reactions, and energy use in aTraditional shaft kilns operate continuously and are fired with fuel introduced into the calcining zone Fig 2 shows temperature profiles of dolomite surface and gases in the preheating, reacting Schematic presentation of vertical shaft kiln; (a) preheating zonecalcining temperature of 900 and 1000 C, the serious aggregation or sintering phenomena during calcining process is harmful to the following sintering process Thus the powder calcining temperature has a great influence on ceramic microstructures Densities of ceramic samples are listed in Table 1, and the density of ceramic increases andCalcining temperature dependence on structure and dielectric
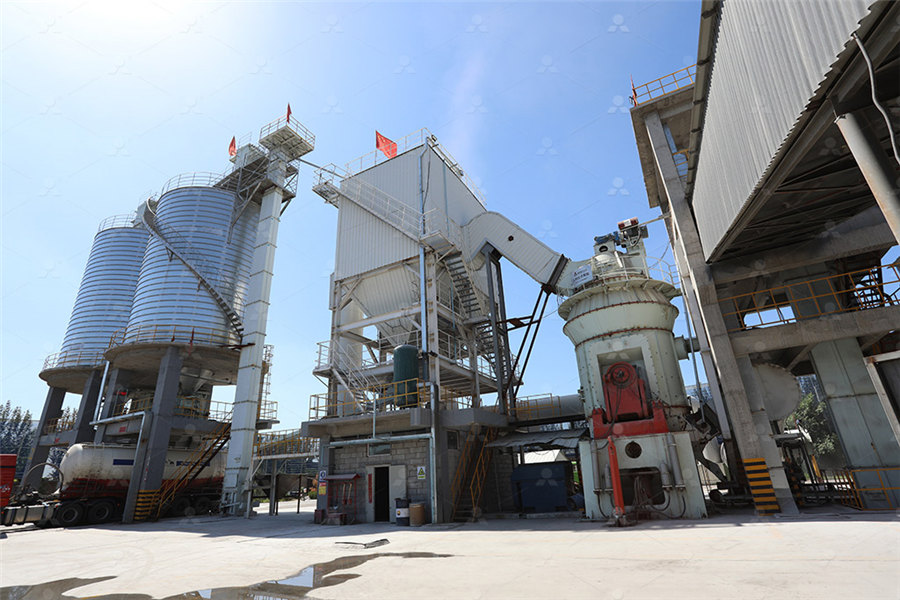
Influence of calcination temperature on the structure and
2020年11月30日 As emphasized above, the calcination temperature is crucial for producing MgO used in cement industry Reactive MgO, which is usually produced by sintering at about 650 ~ 1000 ℃, belongs to caustic calcined and has the similar hydration rate to PC [16]Hence, it can be used alone as reactive MgO cement or cured by accelerating carbonate to produce 2023年1月9日 Control of Precalciner Temperature in the Cement Industry: A Novel Method of Hammerstein Model Predictive Control with ISSA(PDF) Control of Precalciner Temperature in the Cement Industry: the temperature range of 800 or 1000 C However, the maximum activation of this waste is reached by calcining at 800 C Other studies [12, 15] in paper sludge wastes show that paper sludge wastes activated in the range 500–700 C for 2 h have high and similar pozzolanic reactivity Paper sludge waste can be confirmed to be an environmentallyPozzolanic Characterization of Cuban Bamboo Leaf Ash: Calcining temperature of calcining zone can't accurate detection, at present mainly through high temperature the data range using average data method, pretreatment effect is shown in figure 1 2159 0 200 400 600 800 900 1000 outlet temperature of Research on Typical Working Conditions of Calcining Zone Temperature