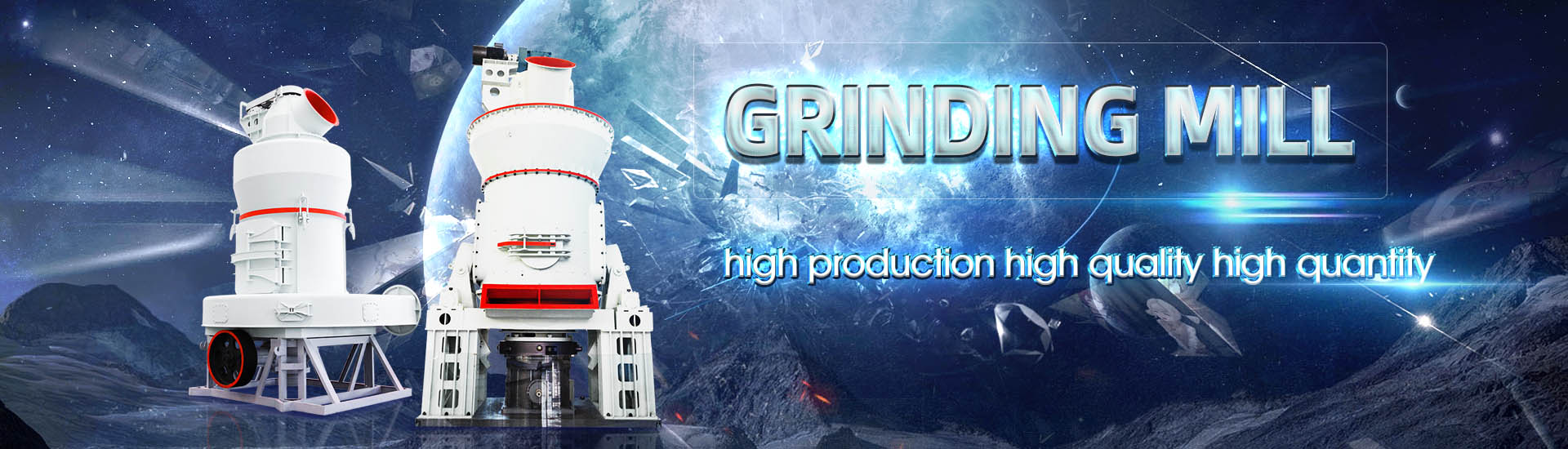
Ball mill power consumption meter Calculate, powder processing plant
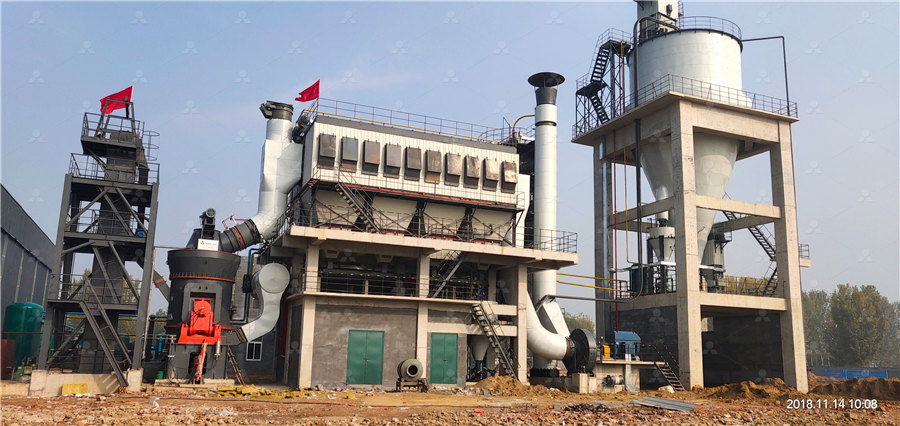
Ball Mill Design/Power Calculation 911Metallurgist
2015年6月19日 Use this online calculators for Motor Sizing and Mill sizing as well as mill capacity determinators In extracting from Nordberg Process Machinery Reference Manual I will also provide 2 Ball Mill Sizing (Design) example done ‘byhand’ from tables and charts Today, The document provides information on how to calculate ball mill design and sizing parameters It includes a small ball mill capacity and sizing table, as well as details on ball mill design and power calculations The document advertises Ball Mill Design Calculations How To PDF PDF Scribd2020年2月26日 Measurement results of two ball mills in a real ceramic manufacturing plant showed that the proposed calculation models could achieve an accuracy of more than 96% for Calculation method and its application for energy consumption of Therefore, the calculation of power (or energy) consumption of ball mills is one of the most important factors in estimating the operating costs of processing plants, determining the optimal Power consumption management and simulation of optimized
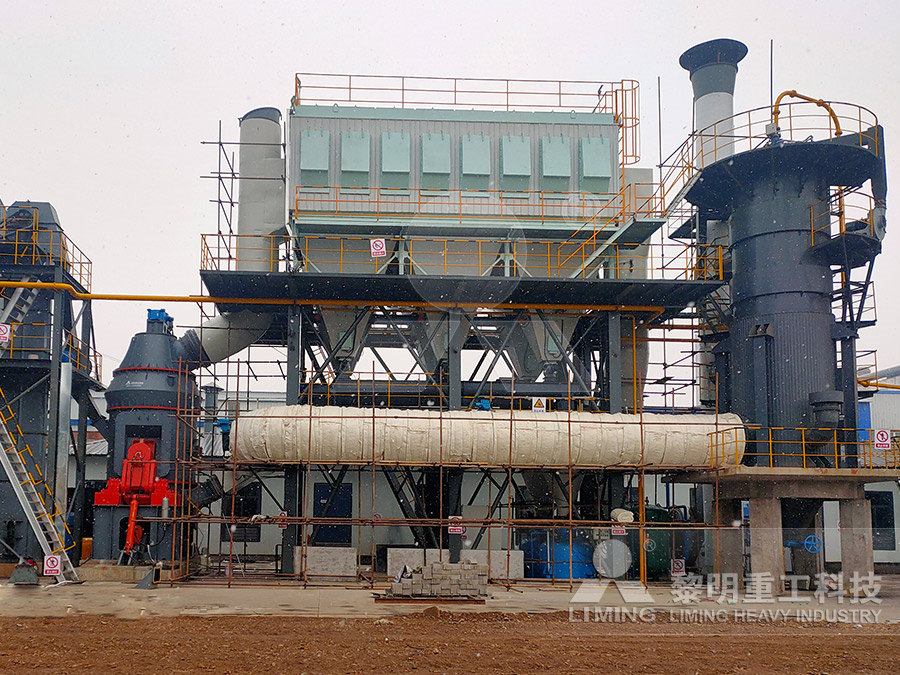
BALL MILLS Ball mill optimisation Holzinger Consulting
This paper will focus on the ball mill grinding process, its tools and optimisation possibilities (see Figure 1) The ball mill comminution process has a high electrical energy consumption, 2020年2月26日 Measurement results of two ball mills in a real ceramic manufacturing plant showed that the proposed calculation models could achieve an accuracy of more than 96% for Calculation method and its application for energy consumption of 2022年3月15日 Various operational parameters, such as mill speed, the ball charge composition, charge filling, lifter type, and lifter number, significantly impact ball milling grinding efficiency [3](PDF) Power consumption management and simulation size distribution and type of balls on the performance (energy) of the high energy ball milling has been investigated for the first time Furthermore, different scenarios that lead to an increase Optimization of the high energy ballmilling: Modeling and
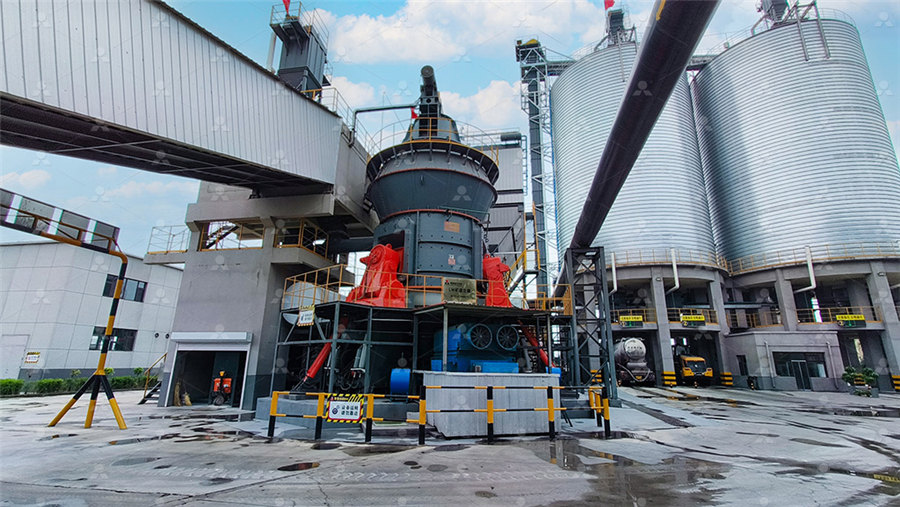
Ball Mill Parameter Selection Calculation Power,
2019年8月30日 How to do Ball Mill Parameter Selection and Calculation from Power, Rotate Speed, Steel Ball quantity, filling rate, etc read more2001年8月1日 In this paper, we analyse the effect of changes in particle size and shape distribution (for both balls and rocks), lifter pattern and profile, and fill level on power draw and Charge behaviour and power consumption in ball mills: sensitivity 2022年3月15日 Power consumption management and simulation of operating conditions of a ball mill in a copper processing plant in a beneficiation plant [2,3] As a result, calculating power (PDF) Power consumption management and 2015年8月24日 A nice and pretty sexy online Ball Mill Powerdraw Calculator was put live by one of the great prophets of grinding 911 Metallurgist is a trusted resource for practical insights, solutions, and support in mineral processing Ball Mill Power Calculations 911Metallurgist
.jpg)
Small Ball Mill Capacity Sizing Table 911Metallurgist
2016年2月14日 Do you need a quick estimation of a ball mill's capacity or a simple method to estimate how much can a ball mill of a given size (diameter/lenght) grind for 911 Metallurgist is a trusted resource for practical insights, solutions, and support in mineral processing engineering, helping industry professionals succeed with proven expertise Small Ball Mill Capacity 2023年4月23日 It consumes most of the energy used in mineral processing plants with grinding using up to 50% tumbling mills is the ball mill energy and material consumption in a ball mill(PDF) Grinding Media in Ball MillsA Review ResearchGateA survey of Australian processing plants revealed a maximum ball mill diameter of 524 meters and length of 884 meters (Morrell, Calculate the mill size required to handle the desired throughput: Solution: W = 10*1125 Mill Power Consumption Example Ball mill = 35 m x 35 m; Rubber lining = 75 mmAMIT 135: Lesson 7 Ball Mills Circuits – Mining Mill Operator 2014年3月1日 With a view to developing a sound basis for the design and scaleup of ball mills, a large amount of data available in the literature were analyzed for variation of the two key mill performance (PDF) Analysis of ball mill grinding operation using mill power
.jpg)
Rod Mill Design Power Draw 911Metallurgist
2015年10月19日 The rod mill motor power is in horsepower at the mill pinionshaft For different length rod mills power varies directly as rod length For difference between new and worn liners increase power draw by 6%, and adjust for bulk density per Table A Wet grinding rod mills are normally used in minerals processing plantsBall mill optimisation As grinding accounts for a sizeable share in a cement plant’s power consumption, optimisation of grinding equipment such as ball mills can provide significant cost and CO 2 emission benefits to the cement producer n by Thomas Holzinger, Holzinger Consulting, SwitzerlandBALL MILLS Ball mill optimisation Holzinger Consulting2017年1月1日 The SMC and Bond ball work index experiments as well as the Morrell model indicated that the order of the specific energy consumption of comminution was “Jaw crusher + HPGR mill + ball mill Performance optimization of an industrial ball mill for chromite processing2001年8月1日 Request PDF Charge behaviour and power consumption in ball mills: Sensitivity to mill operating conditions, liner geometry and charge composition Discrete element method (DEM) modelling has Charge behaviour and power consumption in ball mills:
.jpg)
Power consumption management and simulation of optimized
The amount of comminution or fineness of minerals in a mill can be described by various parameters, the most important of which is d 80 (80% passing size) The purpose of this study is to investigate and simulate the optimal operating conditions of a 2016年3月21日 Pulp Densities Pulp densities indicate by means of a tabulation the percentages of solids (or liquidtosolid ratio) in a sample of pulp This figure is valuable in two ways—directly, because for each unit process and operation in Common Basic Formulas for Mineral Processing 2015年6月20日 A Ball Mill Critical Speed (actually ball, rod, AG or SAG) is the speed at which the centrifugal forces equal gravitational forces at the mill shell’s inside surface and no balls will fall from its position onto the shell The imagery below helps explain what goes on inside a mill as speed varies Use our online formula The mill speed is typically defined as the percent of the Ball Mill Critical Speed 911Metallurgist2022年1月1日 The effect of ball load composition, by varying the grinding media size distribution (eg alternatively by mixing four groups of 195, 38 mm; 195, 50 mm; 38, 50 mm and 195, 38, 50 mm), on the Effect of grinding media on the milling efficiency of a ball mill
.jpg)
Metallurgists Mineral Processing Engineers 911Metallurgist
911 Metallurgist can enter the scene and see what you have become blind to We can fix issues in ways you never thought possible Our fresh eyes will open new opportunities for your plant Each mineral processing plant has varied ore types, mining equipment, (crusher, ball mill, flotation, tailings), and management (operating) philosophyThe evaluation and prioritization of variables 2017年5月8日 If now ξ is the ratio of the power to drive the mill charged with balls and powder to the power to drive the same mill with a ball charge only, then: ξ = Wt of ball charge x Wt of powder charge/Wt of ball charge If also it is assumed that the porosity of the ball charge and of the powder is 04 in each case, then:Grinding Mill Power 911Metallurgist2016年1月1日 The possibility of predicting energy consumption for ball mill concentrator when implementing intelligent forecasting system Compiled model to determine the power consumption of the electric Modeling of power consumption of ball mill Request PDF2012年6月1日 The feed material is typically composed of the BFRs and the catalyst, both in powder form As the cylinder starts to rotate, the grinding balls inside the cylinder crush and grind the feed Grinding in Ball Mills: Modeling and Process Control
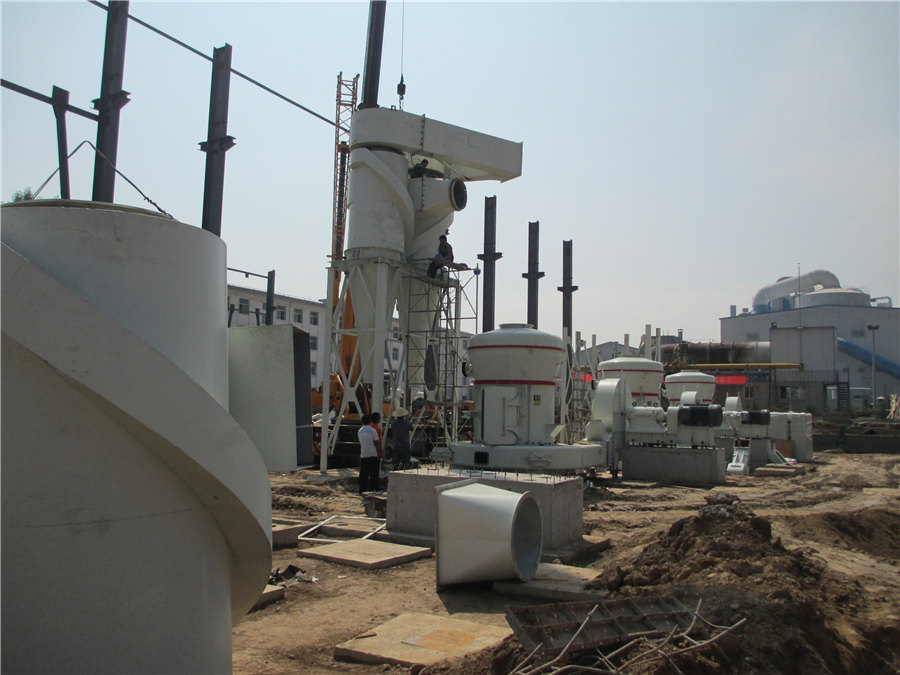
Factors Affecting Ball Mill Grinding Efficiency
2017年10月26日 The following are factors that have been investigated and applied in conventional ball milling in order to maximize grinding efficiency: a) Mill Geometry and Speed – Bond (1954) observed grinding efficiency to be a function of ball mill diameter, and established empirical relationships for recommended media size and mill speed that take this factor into 2017年1月17日 Excessive mill speeds caused more power consumption but resulted in reduced grinding rate Based on the simulation data, two scaleup models were proposed to predict power draw and grinding rateBreaking down energy consumption in industrial grinding mills2019年8月30日 1 Calculation of ball mill capacity The production capacity of the ball mill is determined by the amount of material required to be ground, and it must have a certain margin when designing and selecting There are many Ball Mill Parameter Selection – Power, Rotate Speed, 2015年9月15日 A) Total Apparent Volumetric Charge Filling – including balls and excess slurry on top of the ball charge, plus the interstitial voids in between the balls – expressed as a percentage of the net internal mill volume (inside liners) B) Overflow Discharge Mills operating at low ball fillings – slurry may accumulate on top of the ball charge; causing, the Total Charge Ball Mill Motor/Power Sizing Calculation 911Metallurgist
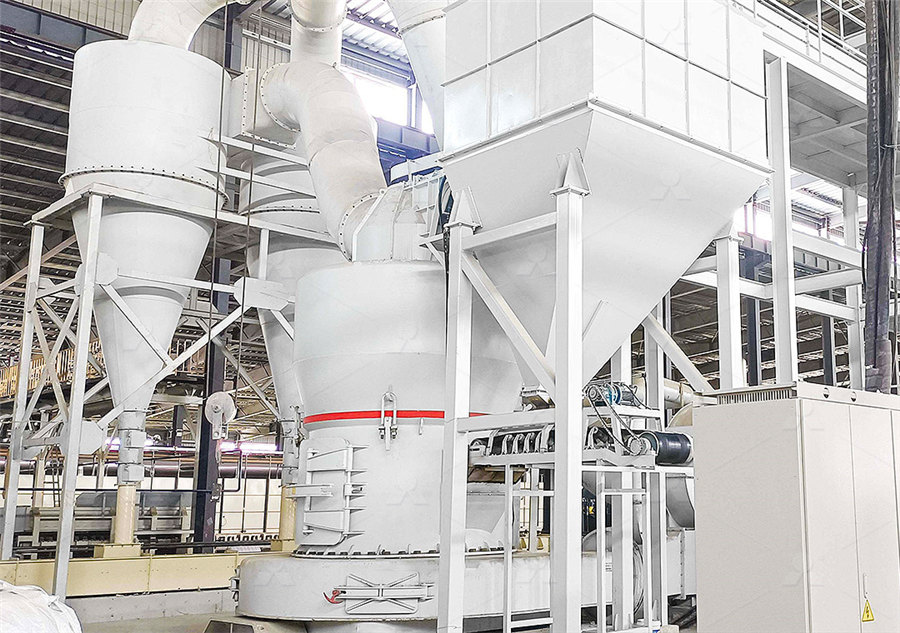
Ball Mill Motor Power Draw Sizing and Design
2015年10月19日 The following equation is used to determine the power that wet grinding overflow ball mills should draw For mills larger than 33 meters (10 feet) diameter inside liners, the top size of the balls used affects the power drawn 2018年4月8日 Unlock the principles of ball mill design with 911 Metallurgist This guide offers detailed calculations and practical tips to ensure your mill is optimized for performance, efficiency, and effective mineral processingBall Mill Design Calculations How to 911Metallurgist2013年7月15日 A powerbased method is first utilised to determ ine the required ball mill power consumption to achieve the required product P80 This would give the required ba ll mill power in closed circuit(PDF) Energy Efficient Ball Mill Circuit – Equipment Sizing 2017年4月29日 It may develop however, when more data are collected, that the wear, instead of being proportional to the cube of the diameter, will be proportional to some slightly higher or lower power Ball Mill Ball Wear Projection In any mill, the rate at which the weight of any ball decrease is directly proportional to its weightGrinding Media Wear Rate Calculation in Ball Mill

Power Consumption of Cement Manufacturing Plant
Nowadays, in the field of cement grinding system of the world cement industry, the major cement grinding equipments include loop flow ball mill, roller press, ball mill semifinishing system, and vertical mill system, in which ball mill and vertical mill are 2 major cement grinding systems in Cement Manufacturing Plants2020年3月14日 The first step in this procedure is to calculate from the following formula the work index, which is the kwhr required to grind one short ton of material from a theoretically infinite size to 80 pct passing 100 microns: where Wi = the work index Gbp = Bond ball mill grindability Pi = micron size of the mesh of grind For 200 mesh, Pi = 74 Cement Plant Grinding Mills Power ConsumptionComparison of typical energy consumption figures for various mills systems are given below Mill System Mill only Kwh / ton Fan Auxiliaries Kwh / ton Total Kwh / ton Air swept ball mill 145 40 185 Double Rotor ball mill 116 48 164 Short single chamber bucket elevator mill 46 45 161Optimizing Electrical Energy Consumption In Cement Process Plants PDF On Apr 28, 2014, Huynh Xuan Kho and others published Planetary Ball Mill Process in Aspect of Milling Energy Find, read and cite all the research you need on ResearchGatePlanetary Ball Mill Process in Aspect of Milling Energy
.jpg)
Analyzing the influence of lifter design and ball mill
2023年10月30日 Ball mills are the foremost equipment used for grinding in the mineral processing sector Lifters are placed on the internal walls of the mill and are designed to lift the grinding media (balls 2023年9月23日 Controlling the Ground Particle Size and Ball Mill Load Based on Acoustic Signal, Quantum Computation Basis, and Least Squares Regression, Case Study: Lakan LeadZinc Processing Plant September Controlling the Ground Particle Size and Ball Mill Load 2019年11月7日 Comprehensive treatment,we should have a test on the 300 MV unit steel ball coal mill pulverizing systemAt the same time,analyze the main operating parameters before modificationTransform the Optimization and transformation of 300MV units steel ball coal mill 2022年2月24日 mal power plants running on ball drum mill grinding systems In [2], it is stated that this share of energy is classified as very significant compared to the modern onesImproving the efficiency of the coal grinding process in ball drum
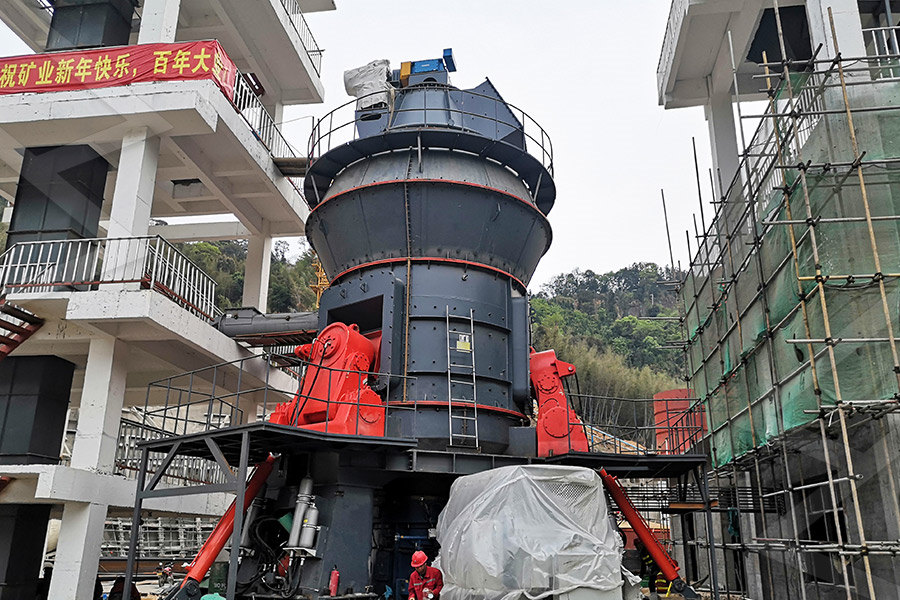
Power consumption management and simulation of optimized
mill, mill charge amount, the amount of grinding media and its density, the rotational speed of the mill, the type and design of the liners, etc are among the factors that determine the amount of energy consumed in mills Energy consumption in different units of a mineral processing plant varies depending on the type and effiComparison with Rod Mill Grinding Media: Ball mills use balls, while rod mills use long steel rods Particle Size Distribution: Ball mills produce finer particles, while rod mills produce more uniform and coarser particles Power Consumption: Ball mills generally have higher power consumption compared to rod mills for the same capacity Ball Mill TAYMACHINERY2020年1月11日 Here the structure means the ratio of ball mill length to its diameter According to the industrial tests, the capacity varies with the ball mill types; Even from the same type of ball mill, the energy consumption and milling efficiency are different One of the factors is the function of the diameter and length5 Ways to Improve the Ball Mill Efficiency FTM2023年10月27日 The ball mill is a rotating cylindrical vessel with grinding media inside, which is responsible for breaking the ore particles Grinding media play an important role in the comminution of mineral ores in these mills This work reviews the application of balls in mineral processing as a function of the materials used to manufacture them and the mass loss, as A Review of the Grinding Media in Ball Mills for Mineral Processing

formula to calculate ball mill volume loading KOOKS
TECHNICAL NOTES 8 GRINDING R P King Mineral Tech the mill is used primarily to lift the load (medium and charge) Additional power is required to keep the mill rotating 813 Power drawn by ball, semiautogenous and autogenous mills A simplified picture of the mill load is shown in Figure 83 Ad this can be used to establish the essential features of a model for mill 2011年1月1日 The digital energy meter was previously tested and evaluated in Bond ball mill Work Index testing where direct measured comminution energy of ores processed in the Bond ball mill were compared Measurement of electrical energy consumption in a Bond ball mill