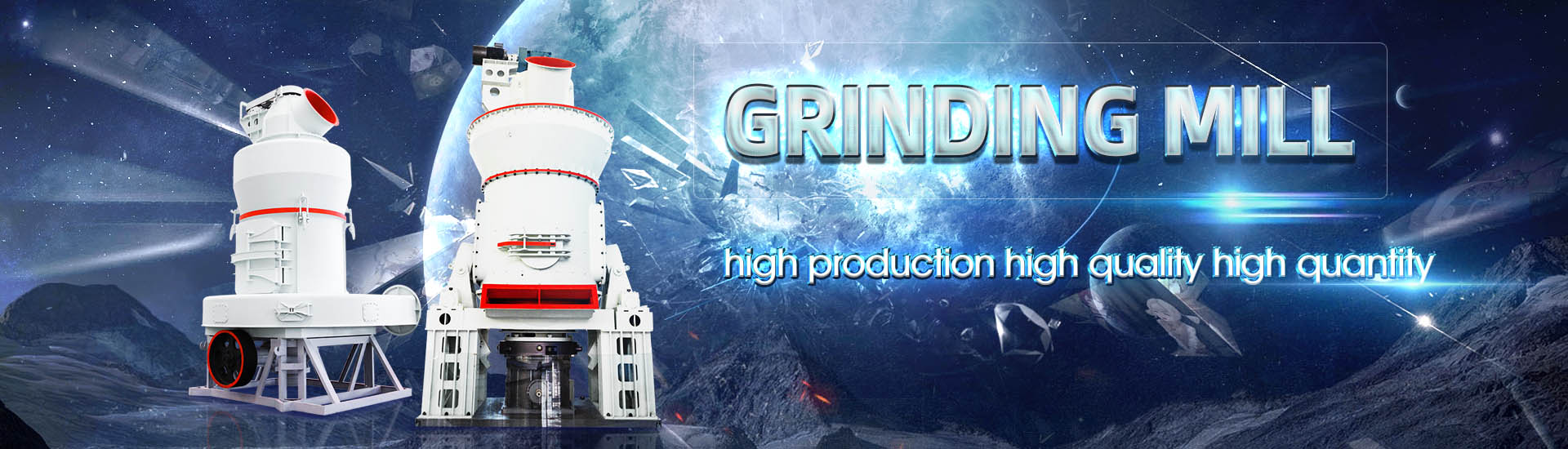
Principle and technology of ore mill
.jpg)
A Review of the Grinding Media in Ball Mills for Mineral Processing
2023年10月27日 Grinding media play an important role in the comminution of mineral ores in these mills This work reviews the application of balls in mineral processing as a function of the The IsaMill is a horizontal high speed stirred mill that operates with very high power intensities (up to 350 kW/m3) In comparison, the power intensity of a ball mill is about 20 kW/m3 The high ISAMILL FINE GRINDING TECHNOLOGY AND ITS INDUSTRIAL It is performed in cylindrical steel vessels that contain a charge of loose crushing bodies—the grinding medium—which is free to move inside the mill, thus comminuting the ore particles Grinding Mill an overview ScienceDirect TopicsRoasting, pressure oxidation, and bacterial oxidation all employ various degrees of temperature, pressure and catalysis to react the pyrite with oxygen to produce an iron oxide and sulphur by Microsoft Word Mill Operator's Paper FINALdoc Glencore
.jpg)
Stirred media mills in the mining industry: Material grindability
2020年6月1日 This review describes stirred media mill technologies and operating principles, and summarises stress intensity theory which can be used for selecting efficient operating Stirred milling was developed for fine grained ores that required an economic grind to sub 10 micron sizes The first examples were lead zinc deposits – McArthur River, George Fisher and Fine Grinding as Enabling Technology – The IsaMill2021年1月22日 Herein, an innovative approach for determining the grinding media system of ball mill based on grinding kinetics and linear superposition principle was proposed The Powder Technology2015年7月21日 A description is given of the principle of operation of bead mills and their main technological parameters (the size of the grinding medium, the speed of rotation of the Ultrafine Grinding in Contemporary Flow Diagrams for Mineral
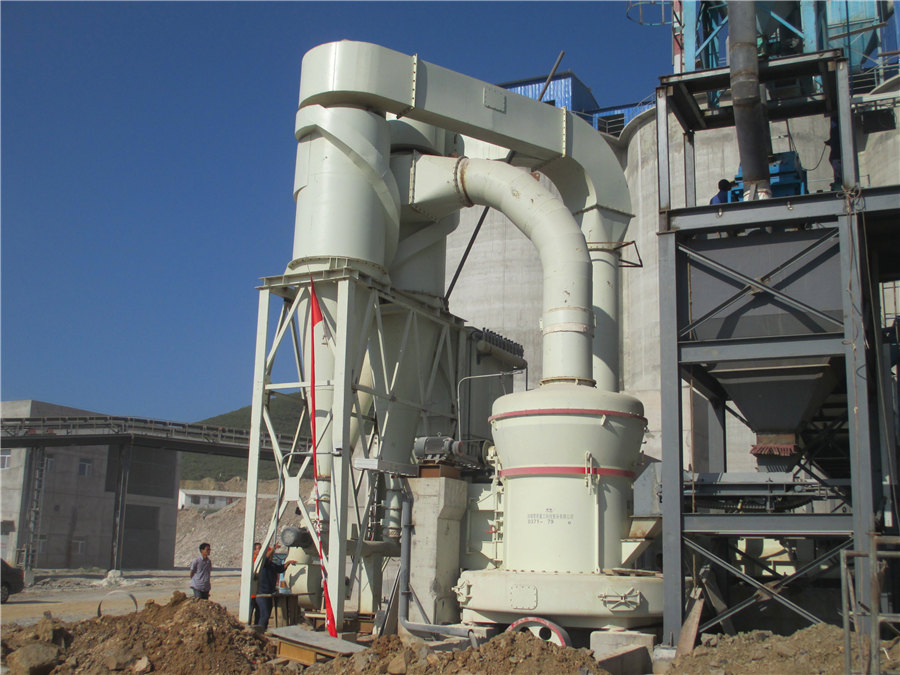
Ore Grinding SpringerLink
2023年7月20日 Ore grinding is a process to further reduce and disperse the ore particle size In the mineral processing industry, ore grinding is the particle size preparation before the 2019年7月8日 While the deposit qualities for mineral raw materials are constantly decreasing, the challenges for sustainable raw material processing are increasing This applies not only to the demand for minimizing the SensorBased Ore Sorting Technology in 2016年11月15日 This paper attempts to portray the status of mine backfill technology for disposal/handling of mill rejects, more specifically the paste backfill (PB) type, a highly relevant aspect in modern day mining industry To date only a limited number of mines have implemented the PB systems all over the world and in India it is in nascent stage Characterization of the Paste Backfill Technology: Essential Characteristics and 2020年10月9日 In order to obtain the optimal operation parameters of a SAG mill, in this paper, the discrete element method (DEM) is used to simulate the breakage process of the particles by controlling three Operation Analysis of a SAG Mill under Different
.jpg)
(PDF) Principles and economic efficiency of ore mining technology
2015年1月1日 The problems of ore mill tailings disposals and ecoeconomic efficiency of their use are considered The paper provides the fundamentals of geomechanical control of the rock mass by lowstrength an ore body with different mineral structure is given in figure 1 This ore body requires wide process adaptability and flexibility to cope with the life of mine ore variability Outotec HIGmills; A Fine Grinding Technology H Lehto Outotec Finland Oy A Paz Outotec Pty Ltd, Perth, Australia I Roitto Outotec Finland Oy M ÅstholmOutotec HIGmills; A Fine Grinding Technology2016年3月30日 In book: Encyclopedia of Iron, Steel, and Their Alloys (pppp 10821108) Chapter: i) Direct Reduced Iron: Production; Publisher: CRC Press, Taylor and Francis Group, New York(PDF) i) Direct Reduced Iron: Production ResearchGate2019年4月16日 Conference: Applying a Successful Technology from the Cement Industry: Advantages of Grinding Ore in a VerticalRollerMill; At: Antalya, Türkey(PDF) LEARNING FROM OTHER INDUSTRIES; WHY THE VRM TECHNOLOGY
.jpg)
(PDF) Control of ball mill operation depending on ball load and ore
2023年12月12日 of the ball mill Ore can have various properties, a brief overview of the basic principles of m odeling the Engineering and Technology Vol 6, Issue 4, April 2019where Ω E is the energycorrected ball wear rate, g per kWh, d R is the diameter of the largest balls in the mill (the recharge size), mm, K d E is the linear wear rate of balls, µm per kWh t −1, Ai is the Bond abrasion index determined in a laboratory test (unitless), F 80 is the feed 80% passing size of the ore, µm, and pH is the water acid/base measurement of the mill pulpBall Mill an overview ScienceDirect Topics2019年10月17日 In this post, we're going to learn more about rod mill We'll cover it from two aspects: 1 Working principle 2 Structure Let's dive right in! 1 Working Principle of Rod Mill Rod mill is a common equipment for grinding operation in mineral concentrator, which is mainly suitable for rough grinding operationThe Working Principle and Structure of Rod Milltheir mill with an inert media, given their prior experience in ultrafine grinding Netzsch, at the time, was an experienced fine grinding equipment supplier in the paint and food processing industry (Clark and Burford, 2004) The first mill that was used in The IsaMill™ 25 Years of Stirred Milling Glencore Technology
.jpg)
Mineral Processing Technology An Introduction to
Grinding tests were conducted on an oxidized coppercobalt ore using a pearshaped ball mill Twelve monosized ore fractions were prepared and wet ground batchwise The mill was run for 05 to 30 min intervals The shortest interval 2013年11月12日 The F2 factor usually relates received at mill (measured by the mill) tonnages, grades and metal content to delivered to mill production tonnages, grade and metal content The F3 factor is F1×F2 and enables a comparison of a mine’s (measured by mine) ability to recover the tonnage, grade and metal content estimated in ore reservesReconciliation principles for the mining industry: Mining Technology This paper discusses the IsaMill Technology and reports on the metallurgical performance of the IsaMills at Mount Isa Mines, including work done over the last 9 years to improve mill design, process efficiency and maintenance, which has resulted in the current stateoftheart IsaMill Technology INTRODUCTIONISAMILL FINE GRINDING TECHNOLOGY AND ITS INDUSTRIAL Principle of Fluid Energy Mill: It operates on the principle of impact and attrition The inlet and outlets are attached with the classifier which prevents the particles to pass until they become sufficiently fine, Fig1(a) It helps in the determination of particle size and shape The speed of air/inert gas is directly related to efficiencyFluid Energy Mill Principle, Construction, Working, and More
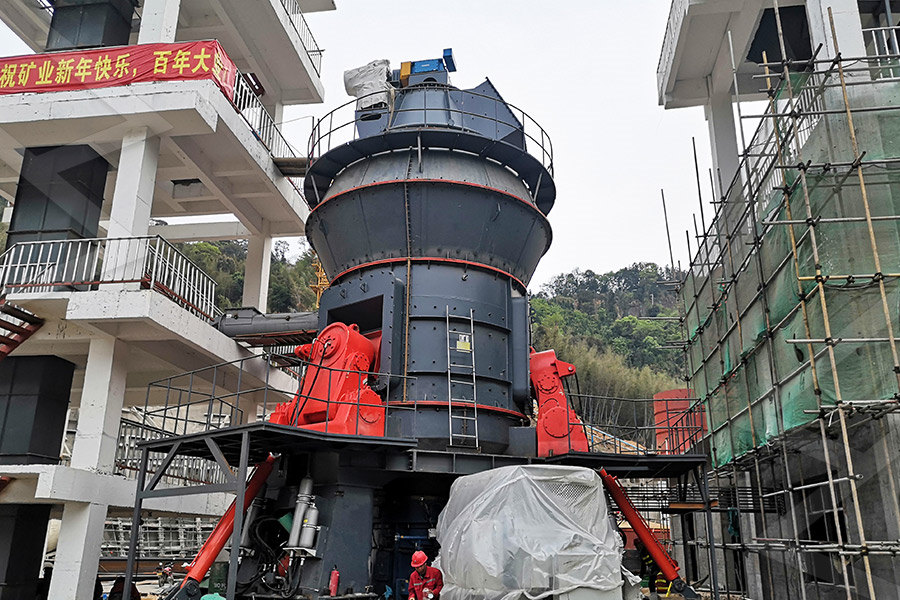
Grinding Machines: Types and Selection Principles Miningpedia
2020年9月22日 Grinding machine has been widely used in gold mines in South Africa since 1905 At that time, the grinding machine used river pebble as the grinding medium, which was essentially a gravel mill Later, in order to improve the production capacity of the mill, cast iron balls were used as the medium, so normal gravel mills were evolved into ball mills and rod millsore sources Outcomes from reconciliation studies may be put into two categories; misclassification of significant tonnages of ore grade material (common), and discovery of problems in postmining processing and documentation (less common) A definite consequence of the former is the haulage of misclassified ore to waste dumps or waste to the Ore Grade Reconciliation Techniques – A Review Mining 2024年4月26日 The final stage in iron ore processing is ironmaking, where the iron ore is transformed into molten iron through a process called reduction The most common method of ironmaking is the blast furnace route In a blast furnace, iron ore, coke (carbon), and fluxes (limestone or dolomite) are loaded into the furnace from the topIron Ore Processing: From Extraction to ManufacturingI INTRODUCTION AND PRINCIPLES In this presentation we will discuss the principle of the Attritor and its applications The Attritor is a grinding mill containing internally agitated media It has been generically referred to as a “stirred ball mill” There are quite a few types of Attritors; we can categorize them as dry grindWe will discuss the principle of the Attritor and its applications
.jpg)
Basic Principles of Metallurgy and Metalworking CED Engineering
are found in ore, a mineralbearing rock, that requires heating or other processes to liberate the metal Gold, workable as it is found, required no technology beyond a stone hammer and anvil to work the metal This is a result of gold's properties of malleability and ductilityIn the mill, the mixture of medium, ore, and water, known as the mill charge, is intimately mixed, the medium comminuting the particles by any of the above methods Apart from laboratory testing, grinding in mineral processing is a continuous process, material being fed at a controlled rate into one end of the mill and discharging at the other end after a suitable dwell (residence) timeGrinding Mill an overview ScienceDirect Topics2021年1月22日 Grinding operation is used extensively in the industry of beneficiation, metallurgy, chemical engineering, and electric power Assisted by the impact and abrasion between media (steel ball, steel rod, gravel, ceramic ball) and ore, the grinding operation reduces the particle size in the mill [[1], [2], [3]]To produce the qualified size and high liberation of Powder Technology2021年1月22日 Request PDF An innovative approach for determining the grinding media system of ball mill based on grinding kinetics and linear superposition principle Herein, an innovative approach for An innovative approach for determining the grinding media
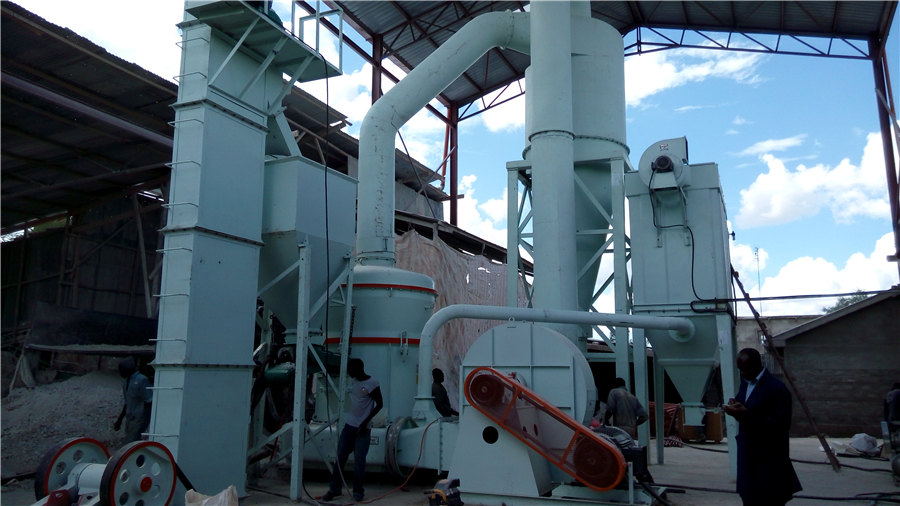
A review of intelligent ore sorting technology and equipment
2022年7月25日 Under the background of increasingly scarce ore worldwide and increasingly fierce market competition, developing the mining industry could be strongly restricted Intelligent ore sorting equipment not only improves ore use and enhances the economic benefits of enterprises but also increases the ore grade and lessens the grinding cost and tailings Working principle and characteristics of vertical mill Working principle The working principle of a vertical mill involves the rotation of a grinding table with rollers attached to it Raw materials are fed into the table and ground between the rollers and table The ground materials are then blown by hot air through an outlet in the mill's Working principle and characteristics of vertical mill2015年3月15日 The total energy consumption for ore comminution will further increase within the next decades One contribution to minimise the increase is to use more efficient comminution equipment Verticalrollermills (VRM) are an energyefficient alternative to conventional grinding technology One reason is the dry inbed grinding principleResearch of iron ore grinding in a verticalrollermillThis article aims to describe the working principle of a jet mill A jet mill, Jet milling is a highly effective technology for reducing particle size of inhalation and other drug products where Bauxite, Gypsum, Graphite, Mica, Talc, Tentalum ore etc Paints: Carbon black, Fluorescent pigment, Titanium dioxide etc Pharmaceuticals Jet mill working principle
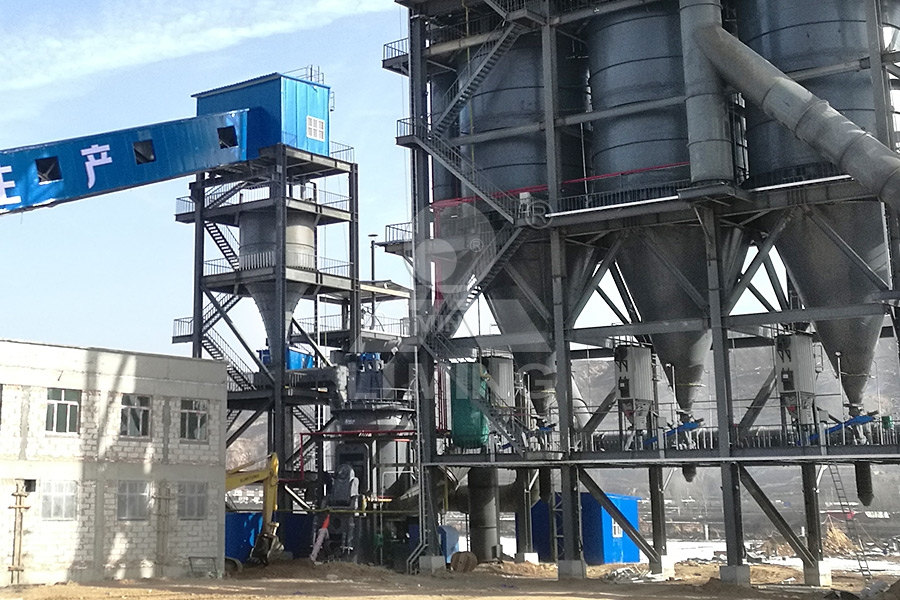
(PDF) ORE DILUTION AND ORE RECOVERY ResearchGate
2019年10月5日 The F2 factor usually relates received at mill The F2 factor enables a check on unplanned dilution entering the ore stream between ore control and the mill The design principles for a The rod mill is another type of grinding mill used in the copper ore mining process This machine uses steel rods as the grinding media instead of balls, which are commonly used in ball mills The rods grind the ore by tumbling within the mill, similar to the action of a rotating drumUnderstanding the SAG Mill in Copper Ore Mining Process2024年2月1日 At present, there are few methods to optimize grinding media Jianwen Yu et al [20] determined the grinding media system of ball mill used the iron ore based on the principle of grinding dynamics and linear superposition, and found average grinding rate increased with a decrease in media sizesMeanwhile the optimal media size for −2 + 045 mm, −045 + 015 Powder TechnologyBy understanding these aspects, readers can gain a comprehensive understanding of ball mill technology and its significance in various industrial processes Ball Mill Working Principle The working principle of a ball mill is Ball Mill Grinding Machines: Working Principle, Types,
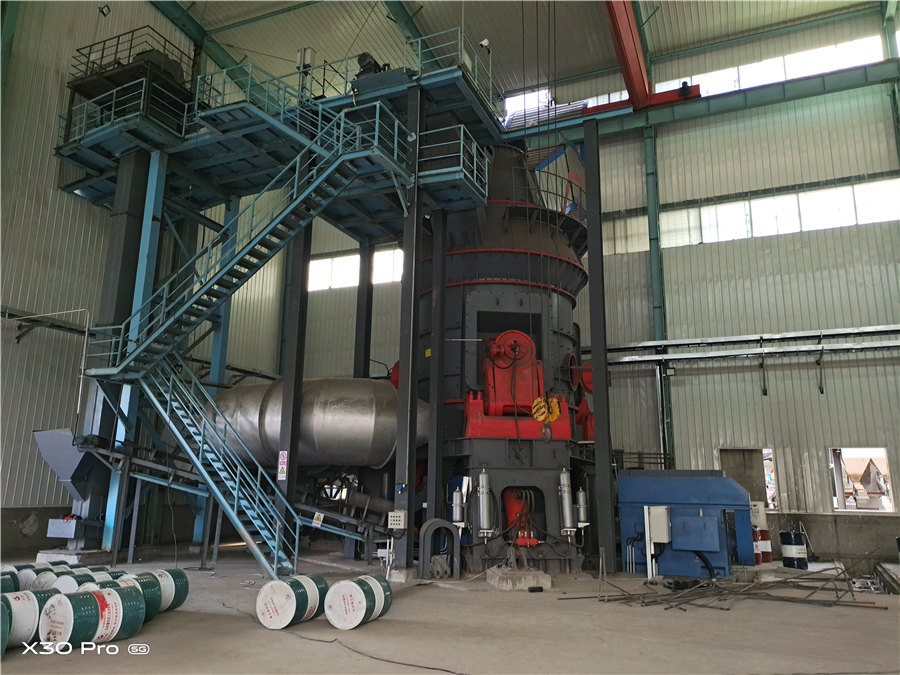
Autogenous Mill SpringerLink
2023年6月7日 The operating principle of autogenous mill is essentially the same as its classification system is simpler than that of dry autogenous mill, and the ore with high content of slime can be processed by wet autogenous Yang JW (2006) Crushing and grinding technology Metallurgical Industry Press, Beijing Google Scholar 2016年2月26日 Operational Characteristics: The method of operation has a considerable effect upon the nature of the productWhen minimum fines are a requirement, the hammer mill should always he operated in closed circuit with a screen, or screens; the circulating load should be fairly high; speed should be as low as is consistent with physical structure of the material; and Hammer Mill Operating Principle 911MetallurgistTechnology and technics of ore preparation processes 5 The ore pretreatment flow charts in use at most highproductive processing plants designed in the last decade are based on semiautogenous (SAG) milling and involve as a rule primary wet autogenous mill (WAM) and a series of ball mills WAM is customary chosen either based on examinationCALCULATION OF THE REQUIRED SEMIAUTOGENOUS MILL 2023年10月27日 The ball mill is a rotating cylindrical vessel with grinding media inside, which is responsible for breaking the ore particles Grinding media play an important role in the comminution of mineral ores in these mills This work reviews the application of balls in mineral processing as a function of the materials used to manufacture them and the mass loss, as A Review of the Grinding Media in Ball Mills for Mineral Processing
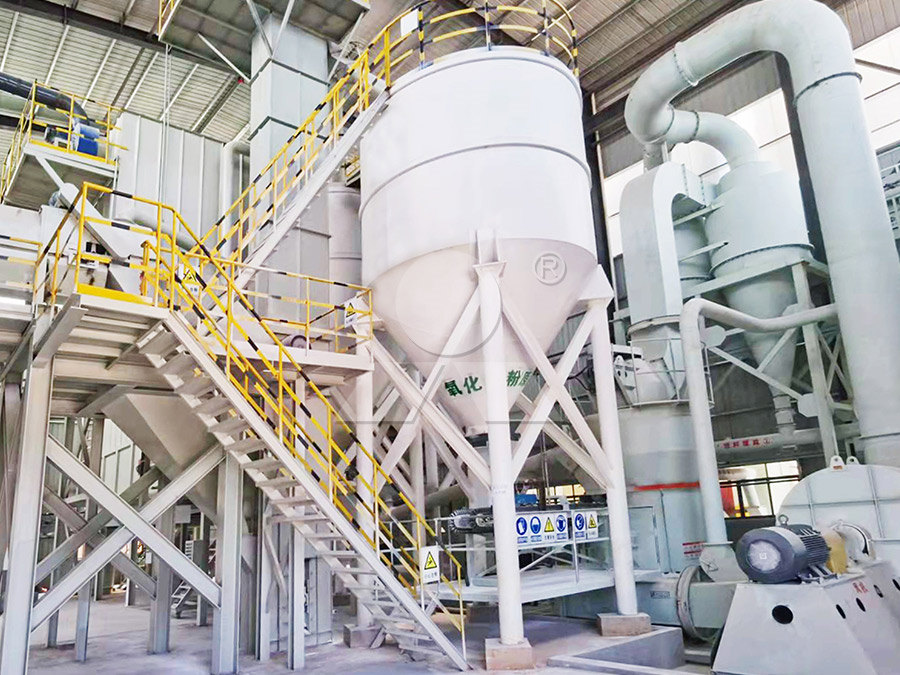
TECHNOLOGY SELECTION OF STIRRED MILLS FOR ENERGY
The coarse portion of the mill overflow is recycled back into the bottom of the mill through a variablespeed pump The benefit of the recycle system is that it can reduce the cyclone circulating load by allowing the mill to preferentially grind the coarse material Also, the upward velocity within the mill can be controlled by the recycle2016年7月1日 The mill was then emptied through a screen to retain the balls The collected powder was riffled to obtain suitable samples for size analysis by screening The entire material was then returned to the mill with the ball charge The mill was then operated for an additional time period, and the aforementioned steps were repeatedSimulation and optimization of a twostage ball mill grinding 2023年4月23日 Comminution is a very important and resultdetermining step in mineral processing This is because further downstream processes in the beneficiation chain depend entirely on it(PDF) Grinding Media in Ball MillsA Review ResearchGateThe general focus of this document will be on metaliferrous ores represented by runofmine material described in category 3 above An exception to the above discussion of mineral processing arises when the valuable component of the Introduction to Mineral Processing or Beneficiation
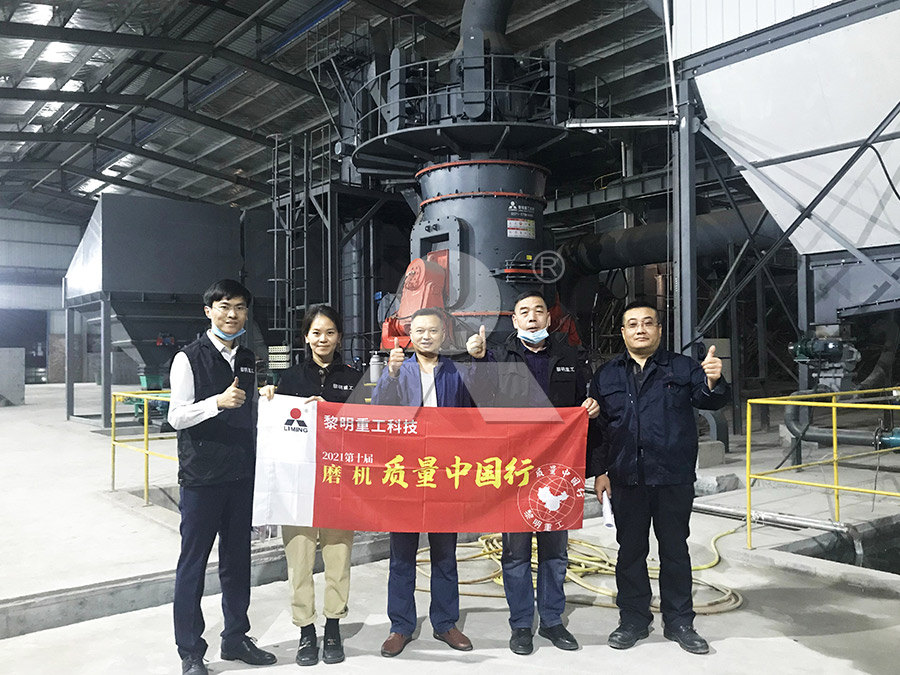
What Is a Ball Mill and How Does It Work? Certified MTP Blog
2024年7月12日 Unlock ball mill technology are essential in ball mills, as they help to reduce the size of the ore particles through both attrition and The ball mill works on the principle of impact and attrition Size reduction occurs as the small balls drop from near the top of the shell What is the difference between a ball mill and