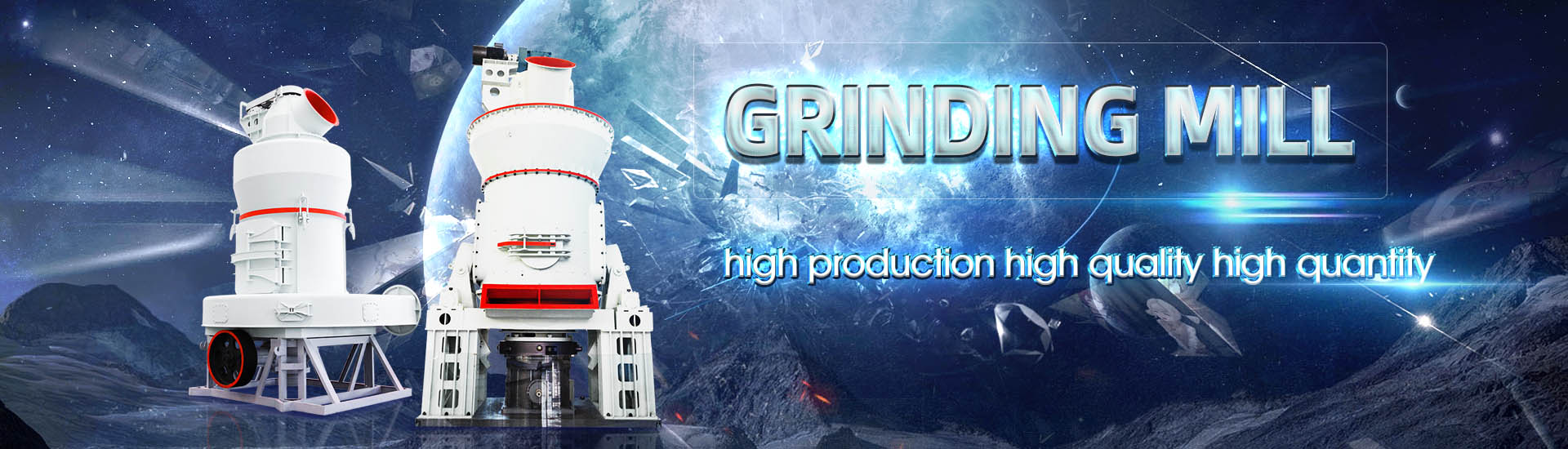
Highefficiency and energysaving 200 mesh coal powder mill Hubei
.jpg)
HighEfficiency Vertical Coal Mill Enhancing Coal
This coal pulverizer efficiently integrates coal grinding and drying, providing highperformance and energysaving features It is widely used in various industries such as cement, electric power, iron and steel, and metallurgyThe production of 200 mesh coal powder requires the selection of an appropriate vertical mill that meets the specific requirements of the application The choice of vertical mill should be based Choosing the right vertical mill for 200 mesh coal powder 2020年8月12日 Obtained results indicate that grinding pressure, primary air (PA) temperature and mill motor current have a tendency to rise by increasing coal feeding mass flow rates for all used coalAn investigation of performance characteristics and The roller mill’s ability to reduce materials to a uniform particle size provides more control of product characteristics and minimizes waste, as shown in Figure 1 The mill’s controlled Roller mills: Precisely reducing particle size with greater efficiency
.jpg)
200 Mesh Coal Activated Carbon Processing Technology And 200
Activated carbon is widely used in the field of environmental protection, such as sewage treatment, wastewater purification, flue gas purification, etc 200 mesh coalbased activated 2023年7月10日 The review concludes that stirred mills have significant potential for achieving the energyefficient ultrafine grinding of particles Stirred mills have unique designs and operations, which provide higher grinding efficiency, lower EnergyEfficient Advanced Ultrafine Grinding of Equipment running is more stable, more convenient for maintenance, higher production efficiency! HCQ improved reinforce milling Raymond millactivated carbon raymond grinding mill Hong Cheng Raymond mill processing 200 mesh activated carbon 2011年8月1日 We used triangular wave current to modulate the singlemode VCSEL to produce high optical frequency excursion, and used difference frequency Analog Phaselocked Loop Design and Application of HighEfficiency and EnergySaving Liner
.jpg)
Coal Mill an overview ScienceDirect Topics
A simple energy balance model of the coal mill is derived in (Odgaard and Mataji 2006), this model is based on a more detailed model found in (Rees and Fan 2003)In this model the coal mill is seen as one body with the mass m mThe following variables are defined: T(t) is the temperature in the coal dust flow in the mill, ṁ PA (t) is the primary air mass flow, T PA (t) is Abstract— This paper aims the development of highenergy milling equipment for use in powder metallurgy This kind of mill is used to obtain prealloyed powders and/or reduction size of powder particles After the steps of project and the construction, a preliminary test was performed using sand in a percentage of 2:1 with stainless steel ballsDevelopment of a HighEnergy Mill for Powder Metallurgy2020年8月12日 energetic efficiency of vertical roller coal mill, International Journal of Coal Preparation and Utilization, DOI: 101080/2020 To link to this article: https://doior An investigation of performance characteristics and Disadvantage: high investment cost 3Ring roller mill(HCH): It can produce ultrafine powder, low energy consumption low investment cost, large scale ring roller mill has good market prospect Disadvantage: low output 4Ball mill +classifying: High energy consumption, it is almost obsolete in nonmetallic mineral industryLimestone Mill High Efficiency, Large Capacity, 2002500 Mesh
.jpg)
Highefficiency and energyconservation grinding technology
DOI: 101016/jpowtec202110056 Corpus ID: ; Highefficiency and energyconservation grinding technology using a special ceramicmedium stirred mill: A pilotscale study2011年10月1日 Pulverized coal has been the dominate fuel used for 7212% passing 140 mesh (105 µm) and 5576% passing 200 mesh (74 µm) These are High Energy Efficiency Plateflow® Gasketed Plate Improved Coal Fineness Improves Performance, Reduces Emissions2 Steps for using coal powder for boilers 1)Coal powder preparation: Select suitable coal as raw material based on the combustion requirements and coal quality characteristics of the boiler; The raw coal is crushed into small pieces by a crusher and then sent to a coal mill for grinding to prepare coal powder that meets the requirements of boiler combustionGuilin Hongcheng HMM Series Bowl Coal Mill Promoting Efficient, 2012年6月1日 PDF The paper presents an overview of the current methodology and practice in modeling and control of the grinding process in industrial ball mills Find, read and cite all the research you Grinding in Ball Mills: Modeling and Process Control
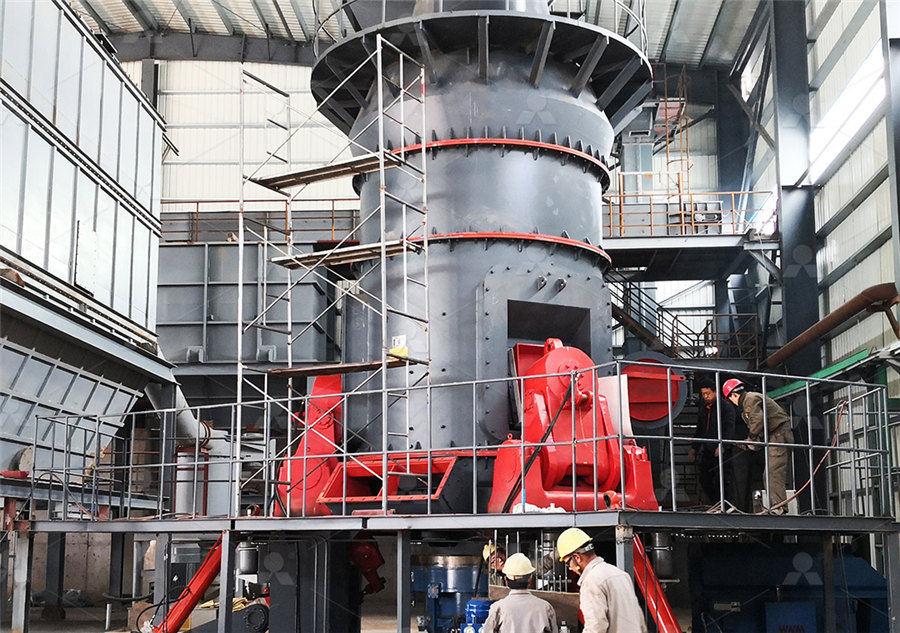
A Study on 500 MW Coal Fired Boiler Unit’s Bowl Mill
Section of coal bowl mill Table 1 Guaranteed coal conditions for mill performance evaluation Coal Moisture % 20 Coal HGI 55 Mill Outlet Temperarure °C 80 Mill Air Flow T/hr 102 Coal Fineness (% passing trough 200 mesh) 70% passing through 200 mesh and 90% passing through 50 mesh Differental Pressure 300 mmwc Coal Output from Mill 609 t/hrThe small 200mesh activated carbon ultrafine mill is a very common equipment in the field of nonmetallic mineral processing, especially in the activated carbon industry, where the general production capacity demand is not high, and generally a small 200mesh activated carbon ultrafine mill is enough Nowadays, with the continuous implementation of environmental Application of small 200mesh activated carbon ultrafine mill in 摘要: The world energy production and consumption is undergoing profound changesChina is indepth to motivate the energy revolution by giving efforts to promote energy production and utilization changes,optimize the energy supply structure,and develop clean coal and efficient utilization of technologyThe results of this study show that coal will be the leading energy Strategies of High Efficiency Recovery and Energy Saving for Coal Energy Saving 1500 Mesh Calcite Grinding Mill for Calcium Carbonate Powder Production Line, 200220: 180200: 135155: 120130: Input Size (mm) ≤10: ≤10: ≤15: ≤15: ≤20: the products covermicro powder grinding mill, high Energy Saving 1500 Mesh Calcite Grinding Mill for
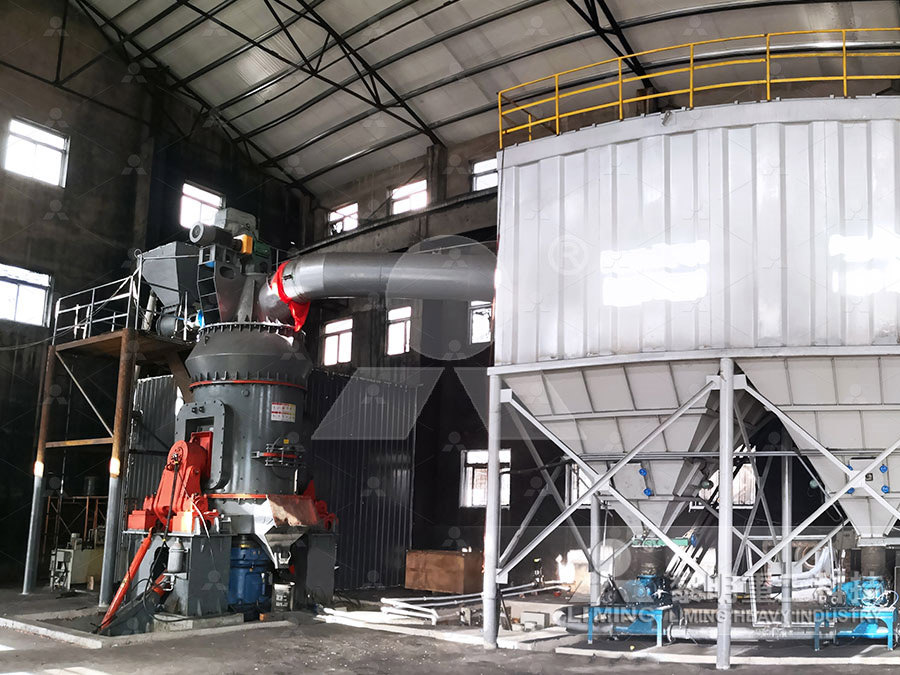
CPRI Online Coal Flow Balancing and Fineness Adjustment
ONLINE COAL FLOW MEASURING AND BALANCING (CONTROL) AND ONLINE COAL FINENESS MEASURING SYSTEM FOR COMBUSTION OPTIMISATION IN A THERMAL BOILER Suresh G Chandwani1, Dr Francesco Turoni2, Reinhardt Kock2, Dr Michael Haug2, Dr Michael Schreiber2 1NSGuzder Company Pty Ltd, Neville House, Currimbhoy Road, High Efficiency Ultrafine Calcium Carbonate Coal Slag Cement Vertical Roller Mill Fine Powder Production Plant, Find Details and Price about Vertical Roller Mill Coal Mill from High Efficiency Ultrafine Calcium Carbonate Coal Slag Cement Vertical Roller Mill Fine Powder Production Plant Baichy Heavy Industrial Machinery Co, LtdHigh Efficiency Ultrafine Calcium Carbonate Coal Slag Cement Introduction Air swept coal mill is an ideal coal processing equipment that can both grind and dry, with characteristics of high efficiency, energy saving, environmental protection, 85% and above of its grinding coal can pass through the 200 mesh screen, and the water content can be under 2% Airswept coal mill is the key equipment to grinding coal for the rotary kiln and industrial furnaceHenan Zhengzhou Mining Machinery1 Low operation cost (1) Low energy consumption: the grinding roller is used to directly roll and grind the materials on the grinding plate, which has low energy consumption and saves 30% ~ 40% energy consumption compared with the ball milling systemEnergySaving Coal Pulverizer Cement Clinker Mill Plant Flyash
.jpg)
News What Is The Output Of The Energysaving And
Coal is my country's main power fuel resource, which is related to the stable development of the national economy Coal grinding into pulverized coal is inseparable from coal grinding mill, and vertical grinding mill are one of them HCMilling(Guilin Hongcheng)'s coal vertical roller mill to grind coal has the advantages of cleanliness, high efficiency, intelligence and safetyTwo major parameters which decide the mill capacity and performance are the hardness of coal and the total moisture level in coal The mill outlet temperature of coalair mixture is maintained between 65 to 90 degree centigrade in the case of low and medium volatile coal In the case of high volatile coal while the lower limit generally remains as 65 degree centigrade, the upper Boiler Performance and Mill Outlet Temperature Bright Hub 2021年11月1日 Request PDF Highefficiency and energyconservation grinding technology using a special ceramicmedium stirred mill: A pilotscale study A pilotscale grinding technology of ceramic medium Highefficiency and energyconservation grinding technology 2022年9月15日 In recent decades, PCMs have been widely studied in temperature regulation and energy savings of buildings due to their constant phase change temperature and high energy storage density [9] At present, the main reasons limiting the practical application of PCMs are leakage in the process of solid–liquid phase change and their low thermal conductivity [ [10] , Highefficiency energysaving buildings utilizing potassium
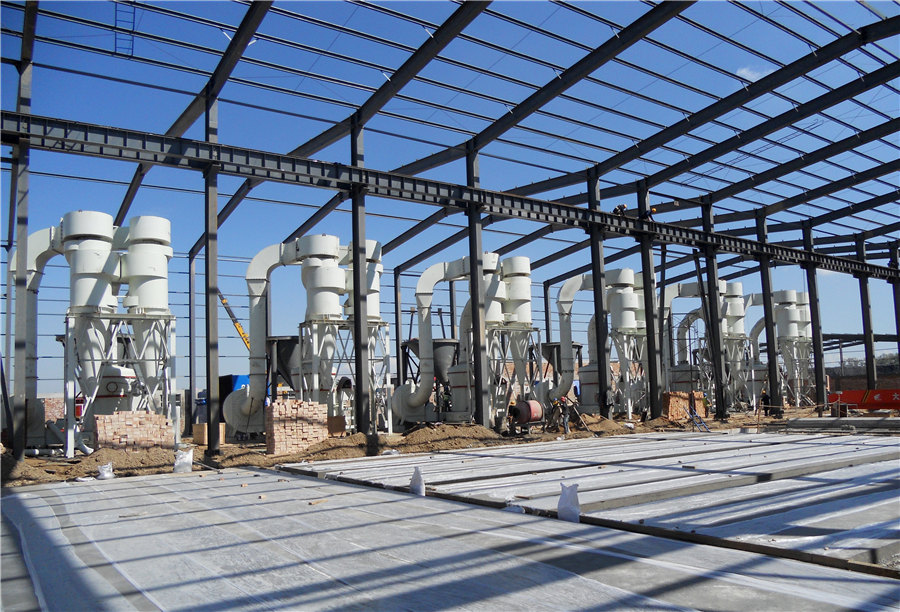
Highefficiency and energyconservation grinding technology using
2022年1月1日 A pilotscale grinding technology of ceramic medium stirred mill was proposed in this study Based on the specific productivity and grinding efficiency, the appropriate grinding parameters were ascertained as follows: material ball ratio of 07, ceramic ball medium size ratio (10 mm: 15 mm: 20 mm = 3:2:5), stirring speed of 110 rpm, grinding concentration of 50%, The plasma ignition and tinyoil ignition techniques developed and applied in recent years can save lots of oil However, the combustion efficiency in the startup period is quite low (the burnout rate is about 50–65 %), and the soot with richer carbon is very likely to accumulate and cause severe accidents such as furnace explosion and burning of the SCR catalyst, the air preheater The High Efficiency and Clean Combustion of Coal Based on2023年4月23日 high speeds of about 90%, causing breakage o f large ore particles wh ilst reducing the mill’s energy efficiency The num ber of cataracting media increases as mill speed increases [ 62 ] (PDF) Grinding Media in Ball MillsA Review2023年5月29日 In December 2019, a novel coronavirus broke out in Wuhan City, Hubei Province, and, as the center of the coronavirus disease 2019 (COVID19) epidemic, the economy and production throughout Hubei Province suffered huge temporary impacts Based on the input–output and industrial pollution emissions data of 33 industrial industries in Hubei from Research on the Optimal Energy Saving and Emission Reduction
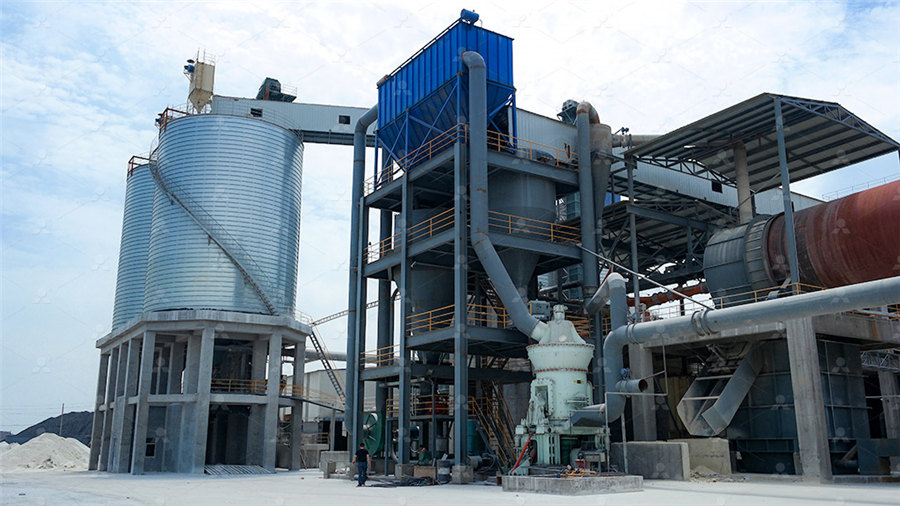
Energy Efficiency Analysis of Copper Ore Ball Mill Drive Systems
2021年3月23日 New ball mill drive system with the prototype energysaving SMH motor [37] Startup of the LSPMSM SMH1732T motor with a filled ball mill after two hours of downtime: (a) active power, (b 2009年6月1日 Request PDF Comparison of energy efficiency between ball mills and stirred mills in coarse grinding Stirred mills are primarily used for fine and ultrafine grinding They dominate these Comparison of energy efficiency between ball mills and stirred 即时翻译文本完整的文档文件。为个人和团队提供准确的翻译。每天有数百万人使用DeepL进行翻译。DeepL翻译:全世界最准确的翻译 DeepL TranslateIt adopts special air supply guiding structure with multinozzles which can effectively form trap heat of high temperature service@tdaxy 86 (Wechat/WhatsApp) Wechat high efficiency energy saving type fan coal mill; Tray Dryer Room Steam Mesh Belt Dryer Micro Powder Dryer Strength Swirl Coal Powder Burner – Zonelion Taeda Rotary Dryer

THE BENEFITS OF HIGH CLASSIFICATION EFFICIENCY IN CLOSED BALL MILL
2013年1月1日 The specific energy consumptions of the grinding equipment and the standard bond work indexes, used 100μm screen, of raw materials are given belowCircuitBond work index (kWh/t)Specific energy Flyash 10 mesh 50% 251µ media ratio: If the ratio of materialC Hematite 1st Pass 50% 415µ C 2nd Pass 50% 288µ Hydrated Lime 216% +270 mesh 50% 496µ C Magnetite Ore 10% +325 mesh 50% 377µ C Manganese Dioxide 60 mesh 50% 062µ C Oat Fiber 91% +200 mesh 98% 200 mesh C Potato Powder 100 mesh 55% 200 mesh CAttrition Dry Milling In Continuous And Batch Modes Union 2021年6月1日 Taking a 200 MW coalfired power plant in North China with a limestonegypsum wet desulfurization system transformation project as an example, the effect of energysaving transformation of the (PDF) Technical Transformation and Energy saving Analysis of 2020年8月12日 In the modern economy, each of the energy resources is highly critical Ultimately, the energetic efficiency of coal mill has been investigated and performance value has been found to be a maximum value of 962% KEYWORDS: Vertical roller coal mill; energetic performance; coalfired power plant;An investigation of performance characteristics and energetic
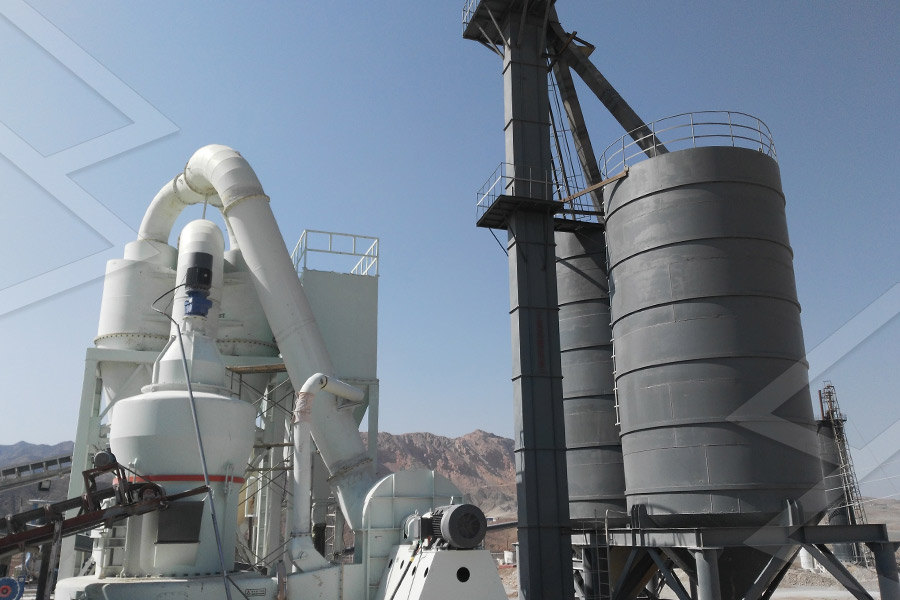
Energy Use of Fine Grinding in Mineral Processing
2013年12月18日 Fine grinding, to P80 sizes as low as 7 μm, is becoming increasingly important as mines treat ores with smaller liberation sizes This grinding is typically done using stirred mills such as the Isamill or Stirred 2008年1月1日 Higher ballmill energy is benefit for amorphization, ultrafine grain and lattice distortion, and the grain size could reach to 25 nm by ball milling for 20 h with 350 r/min Changing routes of Development of planetary mill and its energysaving mechanism2011年8月1日 The process of liner wear and the changing characteristics of the ability of crushing and grinding in the coal pulverizer are analyzed, a new type of cylinder liner is developed, which has a multistep wave crest The small balls on the liner are stuck by the steps, in this way, the wear of the liner wave crest is lightened, so it can keep a longterm stability, it Design and Application of HighEfficiency and EnergySaving The roller mill’s ability to reduce materials to a uniform particle size provides more control of product characteristics and minimizes waste, as shown in Figure 1 The mill’s controlled reduction action requires less energy than other grinding methods, improving production efficiency and saving energy dollars Roller mill components and Roller mills: Precisely reducing particle size with greater efficiency
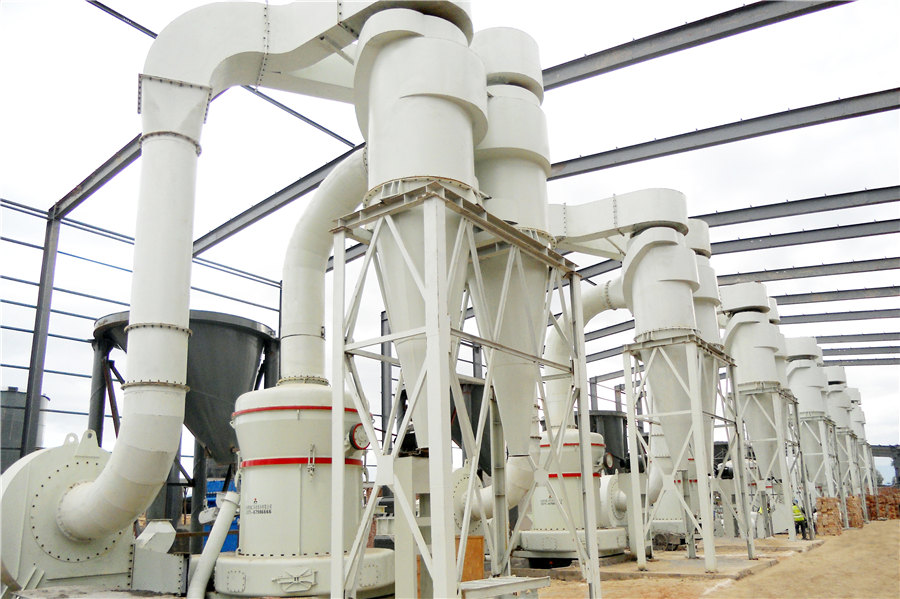
Design and Application of HighEfficiency and EnergySaving
2011年8月1日 Download Citation Design and Application of HighEfficiency and EnergySaving Liner in Coal Pulverizer The process of liner wear and the changing characteristics of the ability of crushing and It can reduce energy consumption by 30% and increase the capacity by 1520% AGICO offers highefficiency energy saving ball mills Skip to content [gtranslate] info@ballmillmachines +86 Home; Ball Mill Application Menu Toggle Cement Ball Mill; Gold Ball Mill; Coal Ball Mill; Limestone Ball Mill; more than 200 kinds of raw High Efficiency Energy Saving Ball Mill For Sale AGICO Ball Mill water savings was approx 20%, which allowed shutting off one of the three highpressure pumps Electrical energy saving amounts to 9,300,000* kWh/ year At the current energy costs this is equivalent to 000 TL 2,100,/ 641,700 EUR** Additional advantages are seen such as reduced material cooling and the lower wear of theEnergy saving and process optimization in a conventional hot strip mill 2002年11月1日 Unfortunately, the energy efficiency is extremely low in mining operations For instance, the energy efficiency is about 10% in percussive rock drilling (Carrol 1985), 35% in rock crushing The energy efficiency of ball milling in comminution