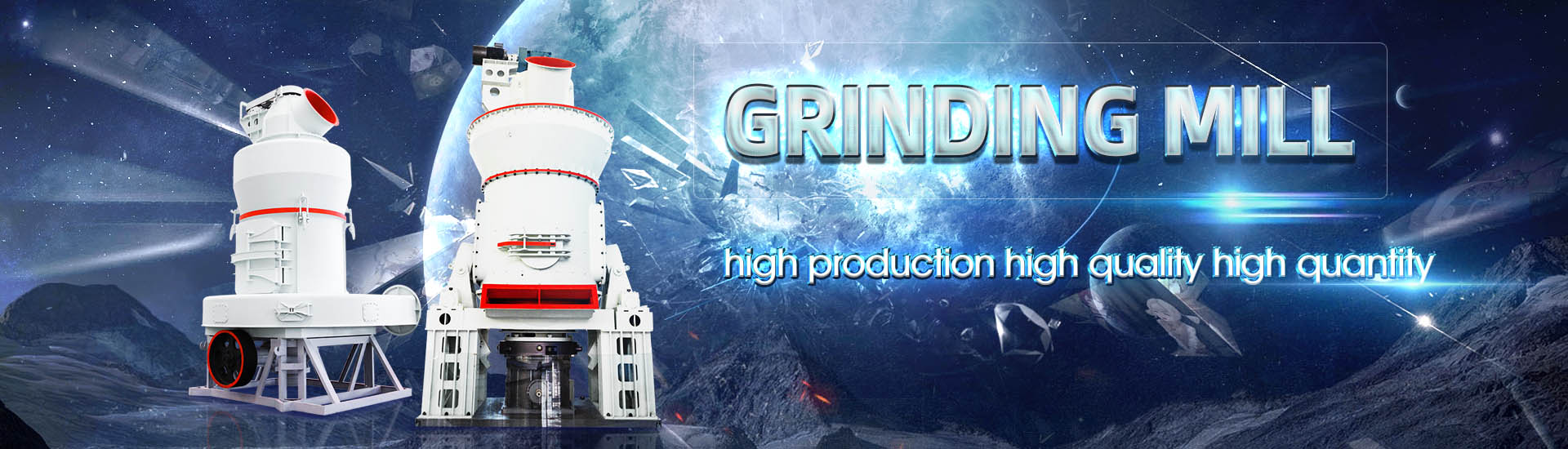
40100 method ore mill
.jpg)
AMIT 135: Lesson 7 Ball Mills Circuits
Size rated as diameter x length Feed System 1 One hopper feed 2 Diameter 40 – 100 cm at 30 ° to 60 ° 3 Top of feed hopper at least 15 meter above the center line of the mill Feeder 1 Single or double helical scoop feeder or a spout feeder 2 Double helical feeders used in closedcircuit with classifiers 3 Spout feeders 展开2015年6月19日 Use this online calculators for Motor Sizing and Mill sizing as well as mill capacity determinators In extracting from Nordberg Process Machinery Reference Manual I Ball Mill Design/Power Calculation 911Metallurgist2021年1月11日 the correct power required to grind ore in a SAG mill, by developing ore hardness variability functions for the ore body to be mined This paper describes the next step Choosing a SAG Mill to Achieve Design PerformanceThe IsaMill is a horizontal high speed stirred mill that operates with very high power intensities (up to 350 kW/m3) In comparison, the power intensity of a ball mill is about 20 kW/m3 The high ISAMILL FINE GRINDING TECHNOLOGY AND ITS INDUSTRIAL
.jpg)
AMIT 135: Lesson 6 Grinding Circuit – Mining Mill Operator Training
AG/SAG mills are normally used to grind runoffmine ore or primary crusher product Wet grinding in an AG/SAG mill is accomplished in a slurry of 50 to 80 percent solids The mill 2021年1月8日 Large pieces of ore are needed in an autogenous mill to make it grind at peak performance This may be true under certain conditions but it is not true under all conditions A CRITICAL REVIEW OF GRINDING DESIGN PROCEDURES FOR THE The design of the 40foot diameter SAG mill installed at the Cadia Gold Mine, New South Wales Australia, followed after two years of extensive laboratory and pilot plant testwork This Design of the 40 foot SAG Mill Installed at the Cadia Gold Copper the fine ore section, and the slime treatment section (Fig 3) Bernic Lake was the first tantalum mine in the western world to introduce flotation in its slime treatment section (Burt 1979) Processing of Tantalum and Niobium Ores Introduction
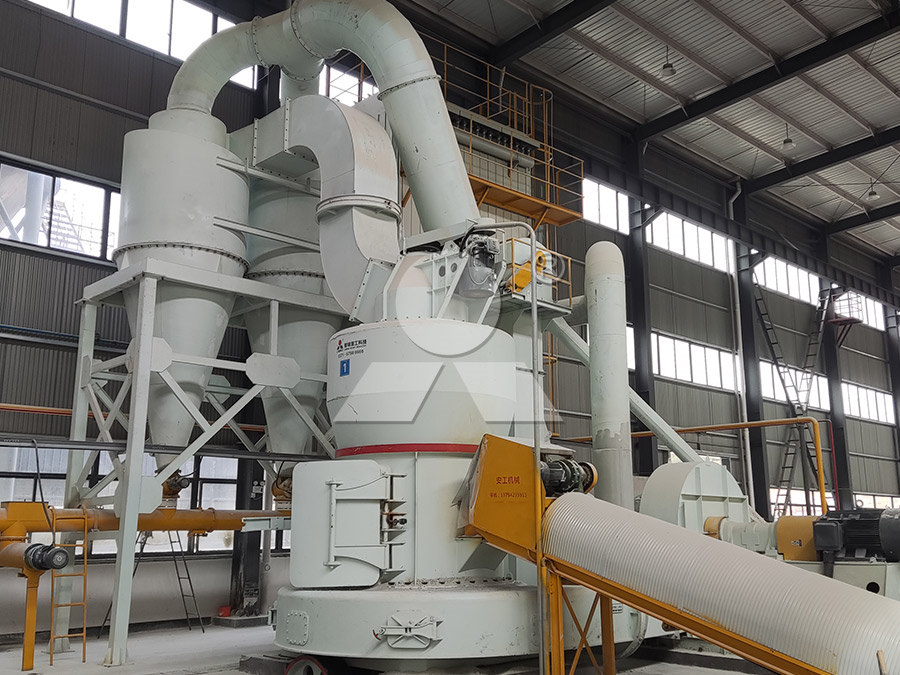
THE COMMINUTION CIRCUIT DESIGN FOR THE CONSTANCIA
The circuit consists of a 60 x 113 primary crusher, two 16 MW SAG mills and two 16 MW ball mills All four mills are twin pinion with wound rotor motor and gearbox drives Provision for Diameter 40 – 100 cm at 30 ° to 60 It has been recognized that the grindability of an ore in a ball mill is a function of both feed and mill parameters: Work index, W i; The Nordberg Method: P M = 2448 ABCL where A = Mill diameter AMIT 135: Lesson 7 Ball Mills Circuits – Mining 2016年6月6日 The ability to mill a broad range of ore types in various circuit 2006) A variant of this method is to direct pebblecrushing circuit product to the Simple repeatable work index tests are usually sufficient for rod mill and ball SAG Mill Grinding Circuit Design 911Metallurgist2021年1月14日 Specific Gravity Method Tested Avg of 6 By 12 3456 Hazen 256 235 237 235 240 242 241 Composite Number The first three results shown in Table 2 are in reasonable agreement with each other Wax coating Weight of ore in mill, grams 6739 6608 6921 7359 7087 6634 6889 6891Comparison of Ore Hardness Measurements for Grinding Mill
.jpg)
(PDF) Control of ball mill operation depending on ball load and ore
2023年12月12日 Ore can have various properties, such as hardness, density, moisture content, etc, which can affect the ore’s productivity and grinding efficiency Discover the world's research 25+ million members2017年12月21日 Hematite ore pellets require a much higher induration temperature than magnetite ore pellets because no exothermic heat is generated due to oxidation inside during indurationlike magnetite pellets(PDF) Mill scale as a potential additive to improve the quality BBM and laboratory ball mill (LBM) 2 Experimental Method 21 Samples In the present study, iron ore of three different chemical compositions was selected from Karnataka region These samples are typical raw materials used in JSW Steel, Ballari Pellet Plant, to produce pellets The selected iron ores are mainly classified into three groups Estimation of Grinding Time for Desired Particle Size DistributionMethod name: Ball mill abrasion test — This is an original method developed for industriallyrelevant high stress abrasive wear 1440 L: Mill nominal volume: 593 L: MILL OPERATION: Action space volume: 378 L: Critical speed Friction and wear of liner and grinding ball in iron ore ball mill Tribology International 2017; 115:506517 Ball mill abrasion test (BMAT): Method development and
.jpg)
Common Basic Formulas for Mineral Processing Calculations
2016年3月21日 where R represents the ratio: % Pb in crude ore/% Cu in crude ore Formula (32) is very convenient for milling calculations on ores of this type Example: An ore contains 5% lead and 1% copper The ratio of perfect concentration for a concentrate of maximum grade and 100% recoveries of lead and copper would be:Optimization of Wet Grinding Parameters of Calcite Ore in Stirred Ball Mill Serkan ÇAYIRLI*1 1Niğde Ömer Halisdemir Üniversitesi, MATERIAL AND METHOD 1 Material The sample in this work was calcite powder (CaCO 3 040 0100 50 5 050 060 070 080 Powder filling ratio 0100 (fc) 0125 840 070 0050 50 5Optimization of Wet Grinding Parameters of Calcite Ore in Stirred Ball Mill2017年6月15日 Request PDF Friction and wear of liner and grinding ball in iron ore ball mill [36][37] [38] [39][40] The ballcratering method relies on performing small craters within tested materials Friction and wear of liner and grinding ball in iron ore ball millRevised: Mill scale is one of the byproducts which produced during the processing of 11 Mar 2021 Accepted: 28 Apr 2021 ore substitution by mill scale at 3%, the rate of production increases from 2194 to 2550 Keywords mill scale; sintering process; iron ore Abstract steelIt is richEffect of Partial Replacement of Iron Ore by Mill Scale on the
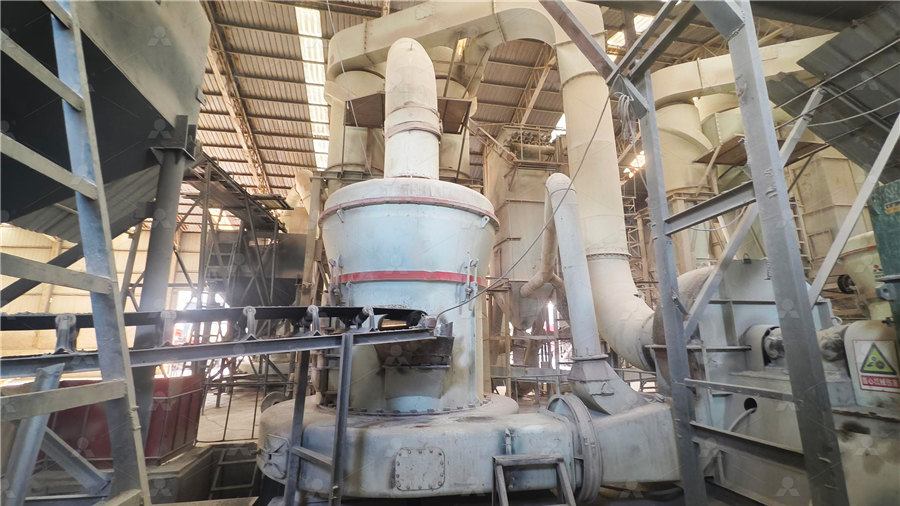
Predicting Mill Ore Feed Variability Using Integrated Geotechnical
current method in spatially and temporally predicting the key rock properties and the associated performance under constrained conditions for use by many agents— mine planners, metallurgists, blasting engineers and geologists Fig 2 Schematic of the proactive management system for BHX Predicting Mill Ore Feed Variability Using Integrated 年6月18日 focused on copper ore, bauxite, coal, iron ore, sphalerite, ilmenite, e t c T h es a m p l es i z es t u d i e dv aried between 10 and 250 g for − 10 mm particle sizesOre Pretreatment Methods for Grinding: Journey and Prospects2023年4月13日 The effect of ball size and interstitial filling on the performance of dry ball mill grinding was investigated for a limestonetype brecciated uranium oreOptimization of Ball Mill Grinding of a LimestoneType Brecciated 2013年7月15日 The ball mill in closed circuit with hydrocyclones is an industry standard, and well known methodologies exist for equipment sizing, selection and design(PDF) Energy Efficient Ball Mill Circuit – Equipment Sizing
.jpg)
OPTIMIZATION OF LATERITE ORE GRINDING PROCESS USING BALL MILL
2022年12月31日 OPTIMIZATION OF LATERITE ORE GRINDING PROCESS USING BALL MILL WITH RESPONSE SURFACE METHOD 40 50 60 +600 +500600 +425500 dry method so that the ore will quick ly move in This includes the primary crusher, coarse ore stockpile, conveyors, The SAG mill cost $122 million, whilst the SAG mill motor PHYSICAL PROPERTIES OF CADIA ORES Laboratory test work data, shown in Table 1, indicated hard and competent ores (monzonite, monzodiorites and volcanics), although not necessarily of such competency as to create concernDesign of the 40 foot SAG Mill Installed at the Cadia Gold Copper 2014年11月1日 The model previously implemented in Modsim™ has been successfully applied to represent the vertical mill operated with different ores 407 177 15Vertical mill simulation applied to iron ores ResearchGate2017年9月1日 The transitional change on the implementation of iso 14001: 2015 in Copper Ore Mill Case studyThe transitional change on the implementation of
.jpg)
Monitoring ore loss and dilution for minetomill
However, ore below the pay limit adds variation to the mill grade as increased mill throughput will be required to make up for the loss of gold, and that impacts on the recovery in the plant It is against these perspectives and findings of this 2014年1月1日 Population balance model approach to ball mill optimization in iron ore grinding considering 40% of ball load, 100% of slurry on the basis of the Bond method Population balance model approach to ball mill 2022年6月17日 Next, 4 00 g of ore and 2 0 0 m L of wa ter were p u t into a Φ 20 0 mm × 24 0 mm bal l mill in the l a bora t o ry The spe e d of the ba ll mill w a s 1 1 0 r/min and the volume w a s 7 5 LDifferences in Properties between Pebbles and Raw Ore from a SAG Mill 2019年8月14日 According to the experimental results, when the filling amount of the steel balls in the cylinder of the ball mill is 40%, 4 Siderite Ore Extraction Method (12:03:04) 8 Types of Iron Ore Magnetic Separator (04:03:13) Research on Vat Leaching Test of A Small Gold MineThe Ultimate Guide to Ball Mills Miningpedia
.jpg)
The Milling Techniques of the Gold Rush Argo Mill Tunnel Tour
The Argo Mill was completed in the early 1900s, soon after the 10year Argo Tunnel operation was completed In its time, the stateoftheart milling techniques of the Argo processed over $100 million worth of gold ore! The prices per ounce ranged from $18 to $35, meaning the mill operations were hard at work each and every day2017年2月16日 The ore is conveyed to the mill over a distance of seven miles by a 2foot gauge railway The method employed to loosen a pulley of Blanton design is as follows: these going to the calciner pits and yielding a 30 to 40 per cent, tin oxide concentrate, while the tail of the jig feeds a Wilfley, Tin Ore Processing 911Metallurgist2022年1月31日 The determination of the metallic iron content in the reduced iron ore concentrates is essential to evaluate the reduction efficiency in the process metallurgy field In this study, a redox microtitration method was developed to determine the metallic iron content in the reduced micronsized iron ore concentrate particles The effects of the dissolving time, Development of a Redox Microtitration Method for the 2022年12月15日 It can be concluded that the HPGRStirred mill combination was a more energyefficient grinding circuit than the HPGRBall mill combination for PGE bearing chromite oreSize reduction performance evaluation of HPGR/ball mill and
.jpg)
Estimation of Grinding Time for Desired Particle Size Distribution
2020年1月3日 Iron ores obtained from different sources differ in their chemical and physical properties These variations make the process of grinding a difficult task The work carried out in this context focuses on three different samples of iron ore, viz, high silica high alumina, low silica high alumina, and low silica low alumina The grinding process for all the three iron ores is 2016年7月8日 UNTIL THE THIRD THEORY OF COMMINUTION of "Work Index" method of determining crushing and grinding mill size was introduced, Sizing a Ball or Rod Mill Sizing a Crusher using >1200 Wi of Ores from Equipment Sizing: Crusher or Grinding Mill2013年6月1日 Based on this, an identification method of mill scale in iron ore was established by Xray diffraction method Two aspen bark piles, 40 feet by 40 feet by 20 feet high, Identification of mill scale doped in iron ore by Xray diffraction method2011年1月1日 Infect only a few investigators worked on the kinetics of mill scale reduction [24][25][26][27][28][29][30]In previous studies on the use of the catalyst for iron ore or mill scale reduction (PDF) Recycling of mill scale in sintering process
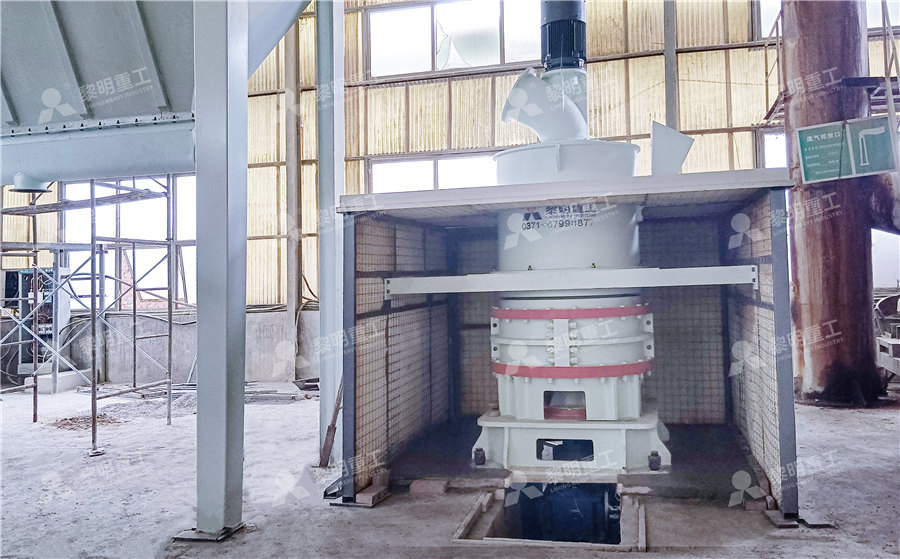
Impact on Grinding Mill Design of Recent New Discoveries
2021年1月18日 testing/calculation method suited the ore the client’s ore and the mill design is specific to that ore 40 50 60 70 80 90 100 0 2 4 6 8 10 12 14 16 18 20 22 24 26 28 30 32 34 36 Bond Ball Mill Work Index, kWh/t Cum Dist% of Tests Done Database Soft Oremilling (12100mm) with a much higher installed power per mill unit volume (Table 1) Table 1 Typical Mill Grinds and Power Intensities Type of Mill Typical Lower Grind Size P80 µm Power Intensity kW/m3 Ball Mill 75 20 Tower Mill 20 40 UFG Mill 5 280 Two basic types of UFG mills are available, the vertical stirred mill and the horizontal Microsoft Word Mill Operator's Paper FINALdoc2013年4月16日 ABSTRACT In this study, ultrafine grinding of a refractory silver ore tailings was studied A laboratory scale pintype vertical stirred mill and ceramic beads were employed for the grinding tests(PDF) Investigation of some parameters affecting the Ultrafine 2016年2月14日 Do you need a quick estimation of a ball mill's capacity or a simple method to estimate how much can a ball mill of a given size No BWi Bond Work Index required here BUT be aware it is only a crude approximation for “most soft ores” from F80 1 cm to P80 700um Ball mill design power example calculation Calculate Ball Mill Small Ball Mill Capacity Sizing Table 911Metallurgist
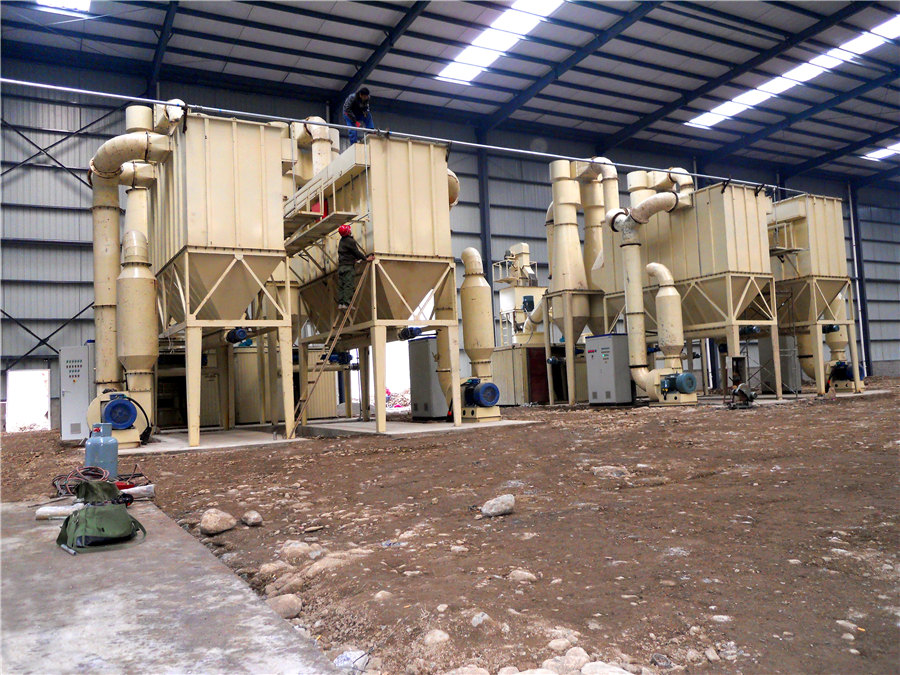
Ball Mills 911Metallurgist
2017年2月13日 q is the charge volume in fraction of mill volume (40 % = 040) nc is the mill speed in fraction of critical speed; Li and Di are length and diameter inside shell lining respectively (in meters) For a mill with more than 21 m (7′) diameter the total power is obtained by dividing net power by 085 The graph is based on 40% charge volumeEstimation of Grinding Time for Desired Particle Size Distribution and for Hematite Liberation Based on Ore Retention Time in the Mill The new method Type of ore F80 (μm Venkatesh KB (2018) Ore pretreatment methods for grinding: journey and prospects Miner Process Extr Metall Rev 40:1–15 Shi FN, NapierMunn TJ, Asomah IK (2007 (PDF) Estimation of Grinding Time for Desired Particle Size 2016年1月1日 In wet grinding practice, highstress abrasion occurs over a small region when ore particles are trapped between the grinding balls and the mill liner, and the load is sufficient to fracture A comparison of wear rates of ball mill grinding media