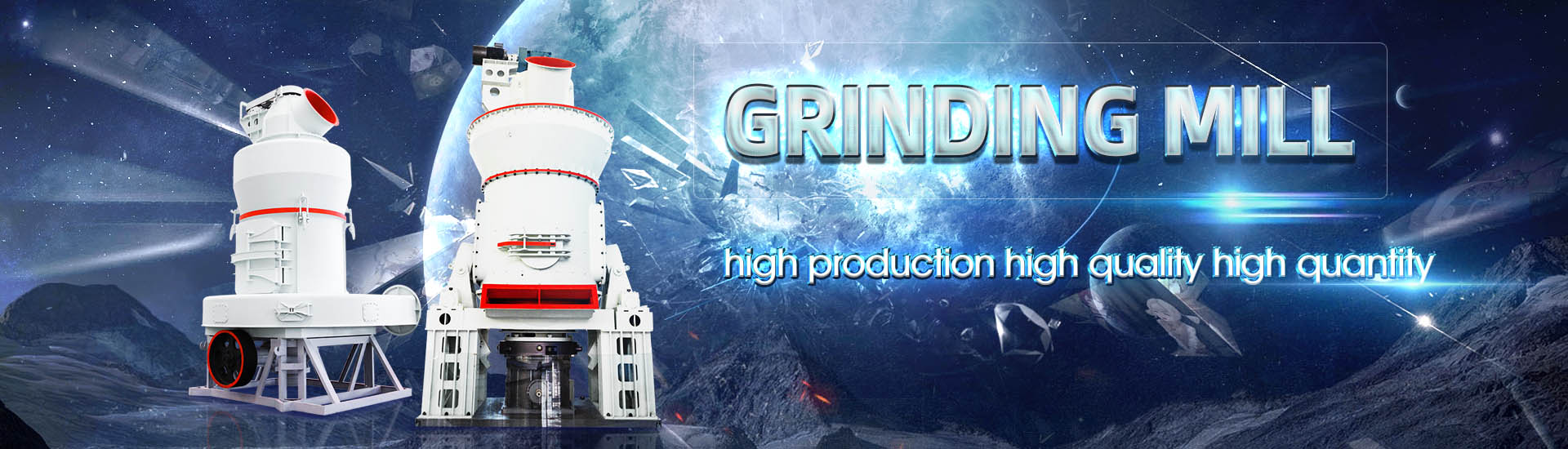
New cement mill with a diameter of 3.2 meters
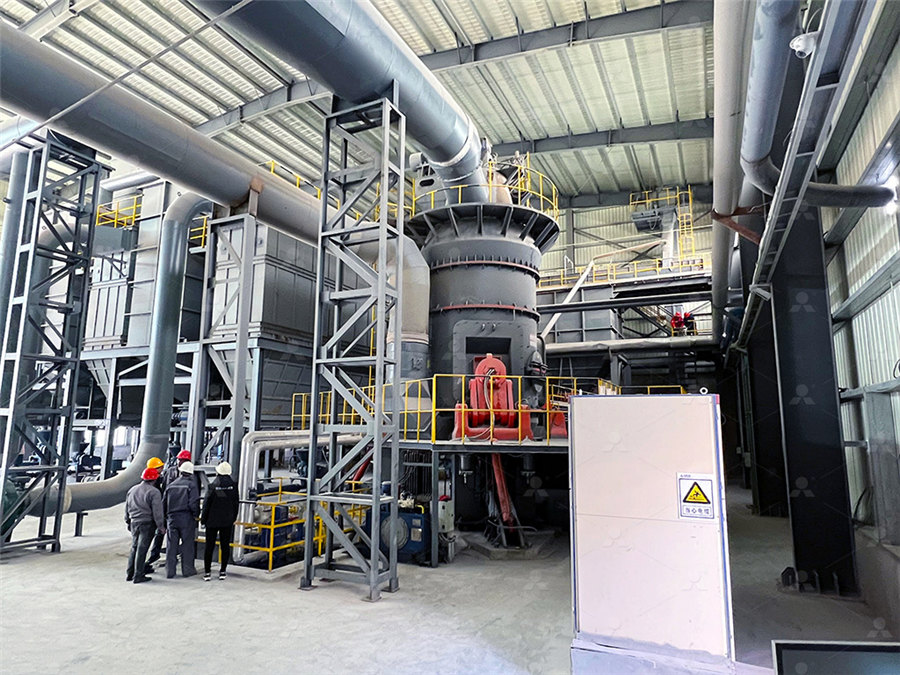
50 40 30 UBEマシナリー株式会社
Under this background, UBE has developed a new 6roller Slag / Cement Mill suitably designed for capacity maximization, higher efficiency and lower cost compared to the conventional This document contains calculations and specifications for a cement mill, including: Dimensions of the mill such as diameter, length, motor power, compartment lengths, and ratio of length to Mill Calculation: Plant: Date: Mill: Visa PDF Electric Power Scribd2024年1月26日 Cement ball mill is a well known machine to grind raw material (hard clinker) into grey powder: Cement A cement ball mill is a horizontal cylinder which is partly filled with steel Computation of charging media for a double compartment 2020年5月1日 In this work, a cement ball mill (CBM) of a new generation cement plant is considered as a case study in order to study its efficiency based on both first and second laws Energy and exergy analyses for a cement ball mill of a new
.jpg)
Case studies and operational results of modern MVR vertical roller
2017年1月1日 For decades vertical roller mills have been in use in the cement industry for the grinding of cement raw material and coal Since the 1980's this mill type has also been used 2 BALL MILLS INTERNATIONAL CEMENT REVIEW FEBRUARY 2021 aim of delivering a target mill discharge size at the end of the chamber, with a maximum residue of five per cent >2mm BALL MILLS Ball mill optimisation Holzinger Consulting2022年11月1日 The plant scale operation and specification of the referenced industrial cement ball mill were taken from Genc (2016) The fullscale mill had a diameter D of 35 m and a Impact of ball size distribution, compartment configuration, and 2019年3月8日 Replacing older ball mills with vertical roller mills or high pressure grinding rolls can reduce electricity consumption by 11 to 15 kWh per ton of raw materialIMPROVING THERMAL AND ELECTRIC ENERGY EFFICIENCY AT
.jpg)
OPTIMIZATION OF CEMENT GRINDING OPERATION IN BALL MILLS
OPTIMIZATION OF CEMENT GRINDING OPERATION IN BALL MILLS Several energy efficient options for cement grinding are available today such as vertical roller mills, roller presses HOLTEC has undertaken Performance Optimisation of the cement grinding circuits by doing process diagnostic studies in many cement plants The paper describes the approach for the PROCESS DIAGNOSTIC STUDIES FOR CEMENT MILL For more details of DEM data collection relevant to the simulation of mills see Cleary (1998b, 2001a,b, 2004) 3 Two chamber cement ball mill The outer mill shell diameter is 405 m long and the mill can have feed added at the feed end Ball motion, axial segregation and power 2022年12月23日 This review provides an indepth analysis of the complex chemistry of cement, offering valuable insights for researchers(PDF) An Insight into the Chemistry of Cement—A
.jpg)
(PDF) Case studies and operational results of
2017年1月1日 The new line (No 3) includes a 5stage preheater precalciner kiln system with a rated capacity of 3000 tpd clinker, a raw material crushing and preblending system sized to handle the requirements Previous Post Next Post Contents1 Ball charge optimization2 1 How to use the BP21 2 Description of the main indicators used in this BP2101 The residue on 2mm/4mm before partition wall2102 Material filling level and ball charge expansion211 Cement mill specific power 1st compartment 212 Raw mill specific power 1st compartment Ball charge Ball charge optimization INFINITY FOR CEMENT EQUIPMENT2024年1月15日 Sun et al [9] carried out study of a roller mill (HRM 4800 by Hefei Zhong Ya, China) and analysed air flow patterns in the mill to improve the energy efficiency of the mill Shah et al [ 10 ] used modelling to optimise the performance of a coal pulveriser by studying the influence of variation in inlet vane angles on the collection efficiency of the powder and desired Optimisation of the performance of a new vertical roller mill by 2022年11月1日 With a steadystate population balance model (PBM), their simulation results (Genc, 2016) suggested that for a given cement product fineness, the twocompartment mill yielded approximately 10 % higher mill capacity compared to the threecompartment mill, which contradicts the traditional design in the cement industry of operating threecompartment ball Impact of ball size distribution, compartment configuration, and
.jpg)
The essentials of electrical systems in cement plants EEP
2020年9月14日 Separator for cement mill: For example if similar plants are consuming 95100 kWh/ton of cement, it may be assumed that the new plant will also consume the same amount and total power to be drawn calculated as shown in subsequent paragraphs Energy meters must of course be calibrated periodically2020年9月10日 The major features of the Project, the 345 MW Power Plant, included 7 km (44 miles) of tunnels and subsurface galleries, an 85 meter (28 feet) diameter by 1200 meters long (3900 feet) power tunnel and lined penstock, and 55 meter (18 feet) diameter by 1400 meters (4600 feet) long midlevel release tunnelConcrete Mixture Design SpringerLink2018年7月1日 Among the industries, the nonmetallic industry was reported as the third largest energy user and accounted for about 12% of the global energy use [1]Within this portion, cement industry had the majority of the utilization with 85–12% [1], [2]US Energy Information Administration (EIA) [7] named cement industry as the most energy intensive among the Energy and cement quality optimization of a cement grinding circuitBallFillingDegreeMillCalculation Free download as Excel Spreadsheet (xls), PDF File (pdf), Text File (txt) or read online for free This document contains calculations and specifications for a cement mill, including: Dimensions of the mill such as diameter, length, motor power, compartment lengths, and ratio of length to diameterMill Calculation: Plant: Date: Mill: Visa PDF Electric Power Scribd
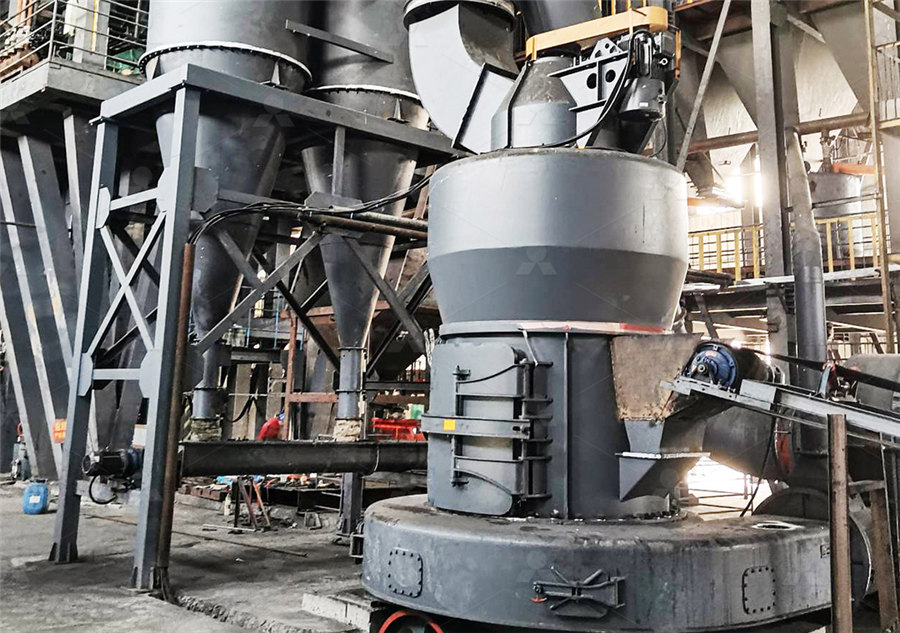
Utilization of tailings in cement and concrete: A
One of the advantages of cement and the cement concrete industry in sustainability is the ability to utilize large amounts of industrial solid wastes such as fly ash and ground granulated blast furnace slag Tailings are solid wastes 2022年10月20日 Cement production plants are one of the extremest CO2 emissions, and the rotary kiln is a cement plant’s most energyconsuming and energywasting unit Thus, enhancing its operation assessments (PDF) Modeling operational cement rotary kiln 2022年9月24日 The diameter of a cement silo is mainly restricted by the transportation conditions, such as the limits of railroad vehicles, buildings, loading, bridges, and tunnels; Therefore, the diameter of the cement silo is Cement Silo Design Manufacturing Dry Mortar Plant2020年4月29日 In the present paper we propose a new 3,2 26 , 1 30 4,4 0% 10% 20% 30% 40 the power input per ball is dependent on the ball diameter to the third power and only slightly dependent CONVENTIONAL CLINKER GRINDING A NEW APPROACH TO
.jpg)
cementmill PDF Free Download SlideShare
2015年6月23日 cementmill Download as a PDF A new design of mill liner where only every other liner is bolted on and the intermediate liner is locked in neighboring liners, reducing the number of bolts by Example: Two compartment cement mill Diameter = 405 m Length = 12 m Filling degree = 196 tons at 30% filling degree Mill speed = 16 1999年11月1日 Ca(OH) 2 content on portland cement basis as function of time Measured on ISORILEMmortar by thermogravimetric analysis Curves represent values for 30% replacements with PFA0 (fly ash as (PDF) Blended fly ash cements A review ResearchGate2021年1月22日 In the whole process of cement production, the electricity consumption of a raw material mill accounts for about 24% of the total Based on the statistics of the electricity consumption of the raw A Survey and Analysis on Electricity Consumption of Raw Material Mill and best performing cement mill in the market The OK mill by FLSmidth has been proven for over 20 years and with 120 global references to be the premier solution for finish grinding of Portland cement, slag and blended cements Figure 1 OK 42 cement mill The OK mill was originally designed by Onoda Cement and Kobe Steel in the early 1980sOK Mill: The 3: Mechanical optimized and 31: Grinding concept
.jpg)
Optimization of an industrial scale open circuit threecompartment
2016年9月10日 1 Introduction Portland cement clinker is a black nodular hydraulic material It is made by burning in a rotary kiln (pyroprocessing), at least to sintering a precisely specified mixture of raw materials containing CaO, SiO 2, Al 2 O 3 and Fe 2 O 3 at temperatures of about 1400 °C Following the clinkering process in the kiln, clinker is cooled down in coolersCement Mill Ball Mill Dynamics Free download as Word Doc (doc / docx), PDF File (pdf), Text File (txt) or read online for free The document summarizes key aspects of ball mill fundamentals: 1) Ball mills reduce materials through comminution mechanisms like fracture, chipping, and abrasion caused by ball movement inside the rotating millCement Mill Ball Mill Dynamics PDF Mill (Grinding) Heat 2016年4月25日 In cement industry about 110 kWh of electrical energy is consumed to produce one ton of cement and about 26% of the total electrical power is used during farine productionDetermination of correlation between specific percentage, r is effective mill radius in meters, h is (H –r) in meters, H is free height in meters, and is angle subtended at mill axis by charge surface whereby cos 1 2 K U The ball mill media charge wear rate is given by Equation (3) b A t m b W = k (3) d(m ) d(t) where, W t The Effects of Temperature, Vibration and Dosage on the
.jpg)
A NEW SETUP FOR RAPID DURABILITY SCREENING OF NEW BLENDED CEMENTS
2017年3月8日 We produced mortar samples with dimensions of 8 cm × 8 cm and a thickness of 6 mm Each sample contained an embedded reference electrode (Ag/AgCl), 5 carbon steel electrodes of diameter 05 mm With the introduction to the market of the MVR mill in 2010, a new concept was available for very high throughput rates By using a larger diameter, a larger contact area resulting from roller size and/or number of rollers, a faster rotational speed and higher hydraulic grinding forces, the mill capacity can be increasedReprint Sonderdruck aus Cement International 62021 Gebr2015年4月1日 1 Introduction Airswept raw meal ball mills introduced by the cement mill manufacturers FLSmidth ® (Smidth, 2002), Polysius ® (Polysius, 2002) and KHD Humboldt Wedag® are the most commonly used onesKHD Humboldt Wedag® manufactured fully airswept raw meal mills which have two compartments used for drying and grinding processesOptimization of a fully airswept dry grinding cement raw meal capacity In the case of ‘Table 1’, the conventional mill is a UM464SN (table diameter: 4,600 mm), while the new mill is a UM436SR (table dia: 4,300 mm), or one full model size smaller in terms of Table diameter In this case, by adopting the 6roller mill with new design subrollers support, compared with the50 40 30 UBEマシナリー株式会社
.jpg)
Everything you need to know about Kiln System Operations in Cement
6 The mill hot air inlet temperature should not exceed 315°C on systems using ambient air 7 The mill outlet temperature should not exceed 95°C on direct fired systems; the maximum outlet temperature on indirect systems is generally lower than that for direct fired systems using the same solid fuel 8 If a fire occurs in the mill:The shaft kiln in a modernized form is still used in some countries, but the dominant means of burning is the rotary kiln These kilns— up to 200 meters (660 feet) long and six meters in diameter in wet process plants but shorter for the dry process—consist of a steel, cylindrical shell lined with refractory materialsStudy and Review of Ordinary Portland Cement Academia2017年8月1日 Supposing that the maximum velocity of a ball is its terminal velocity when it falls from rest to the bottom of the mill, ie v r = 2 gh = 1066 m/s, where h is equal to the diameter of the mill, we can determine its maximum overlap percentage (with respect to the diameter) of a 70 mm diameter ball (Section 322)A generic wear prediction procedure based on the discrete MECHANICAL ELEMENTS OF TUBE MILLS this is a part of ASEC Academy training Courses SUMMARY the mechanical elements of a tube mill could be separated into elements which have a direct function with the grinding process (ie grinding media, liners, diaphragms) and into elements which can be considered as individual units which are connected to each other to a MECHANICAL ELEMENTS INFINITY FOR CEMENT EQUIPMENT
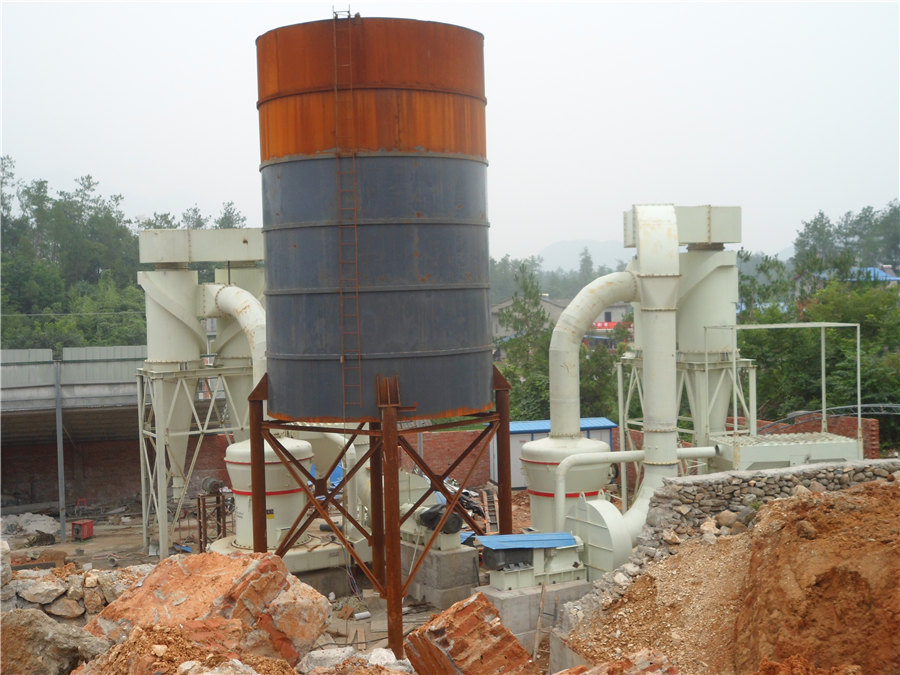
Mechanical activation of cement in stirred media
2013年2月1日 Stirred media mill is one of the most energyefficient types of grinding equipment for wet ultrafine grinding Nevertheless, in a dry mode several problems arise, such as aggregation Roller mills are now operated with throughput capacities of more than 500 tons per hour of cement raw mix (Loeschemill, Polysius double roller mill, Pfeif ferMPSmill, SKET/ZABroller mill) The working principle of roller mills is based Roller mills INFINITY FOR CEMENT EQUIPMENTREVIEW Review of recent developments in cement composites reinforced with fibers and nanomaterials Jianzhuang XIAOa, Nv HANa, Yan LIb*, Zhongsen ZHANGb, Surendra P SHAHc a College of Civil Engineering, Tongji University, Shanghai , China bSchool of Aerospace Engineering and Applied Mechanics, Tongji University, Shanghai , China c Center for Review of recent developments in cement composites reinforced 2020年3月1日 The scaleup effect on size reduction is confirmed with cement mill data cement mills in reasonable agreement The equation of the grinding performance alone, however, does not evaluate the mill diameter and the length individually nor guarantee the powder (5b/3)2 a 0 constant defined in Eq (D12), − a 1 constant A scaleup and design basis of continuous tube mills in cement
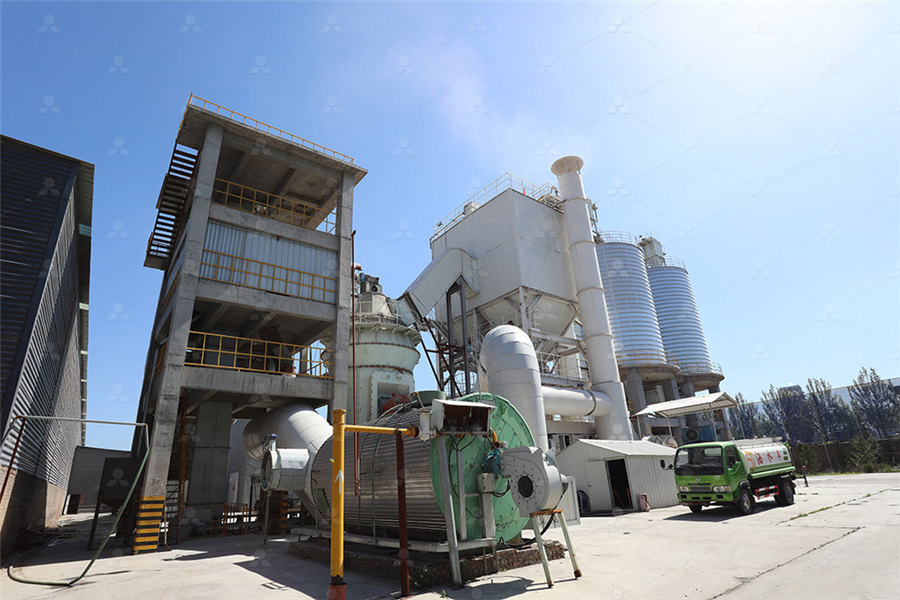
Latest trends in modular cement grinding plants Cement Lime
The R2G 2500 C4 with 1450 kW drive achieves up to 79 t/h for cements with 4000 Blaine (Figure 5) The largest so far used VRM is the R2G 3000 C4 with 1640 kW installed drive and 90 t/h for cements with 4000 Blaine The MVR mill enables cement producers to grind all types of cement as well as slag, limestone, gypsum and many other materialswhere: where Q is heat of hydration (amount of heat released by the sample in Jg1); m c the mass (g) of the mortar tested; t (h) hydration time; C (JºC) the total heat capacity in the calorimeter and the mortar tested; (Jh1ºC1) the global thermal transmission coefficient; and t (°C) the difference between the calorimeter readings for the test and reference materials atDURABILITY OF NEW CEMENTS ADDITIONED WITH RECYCLED 12 Details of process emissions Process emissions from crusher section, raw mill section, kiln section, cement mill section and emissions from roads 13 Proposed air pollution control device Bag Filters for crusher section, raw mill section, cement mill section etc and ESP for Rotary Kiln 14 Cost of the Project: Rs (in Crores) 14698 CroresPREFEASIBILITY PROJECT REPORT FOR 1200 MT/DAY ( MT/ANNUM) CEMENT 223 Mill internal diameter The mill internal diameter is defined as the mill shell internal diameter (D) reduced by twice the liner average thickness (e e) As already defined in chapter “tube mills” there are many different types of liners Figure 3 shows typical liner thicknesses for first (C1) and second (C2) chamber as a function of Dimensioning of Tube Mills Archive
.jpg)
Concrete Cylinder Calculator
2024年6月30日 Let's say we need to make 10 concrete cylinder specimens for compressive strength testing of a new cement brand, and we decide to use concrete cylinders measuring 4 inches in diameter and 8 inches in heightWe want to know if the new cement brand can reach a compressive strength of 2,900 psi using a 1:15:3 cement mix ratioHere are the steps to find