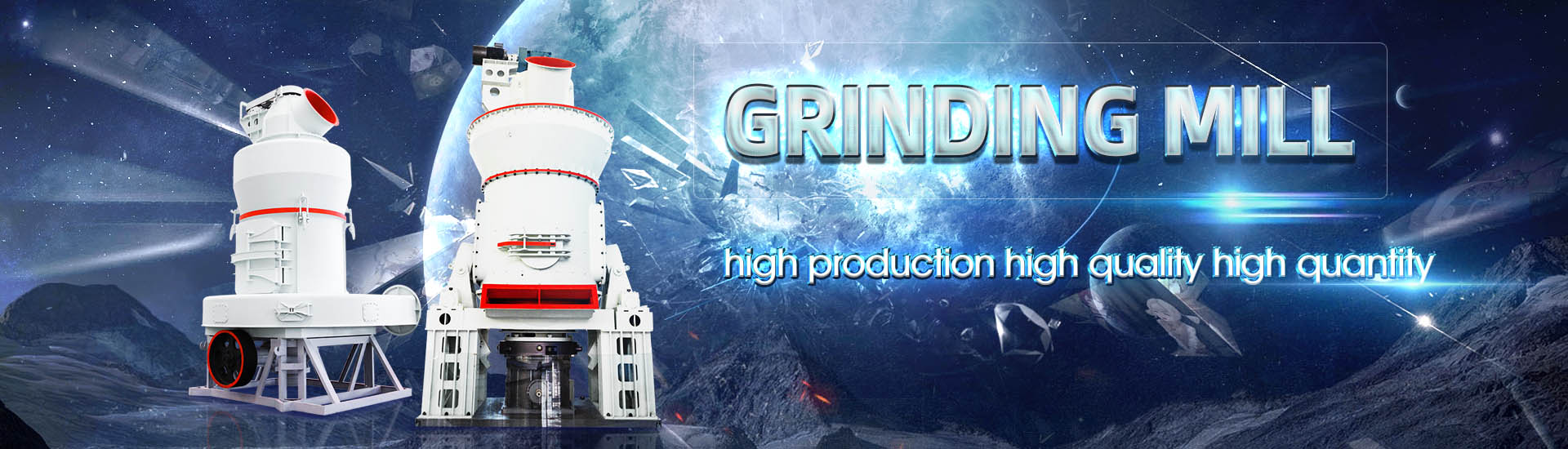
Coal equipment, threelayer grinding system
.jpg)
Coal grinding technology: a manual for process engineers
Four coal grinding devices three dry, one wet are discussed with the appropriate ancillary equipment for complete systems The mills examined are the: airswept ball mill, roll or ball BK has a grinding table diameter of 225m The three φ15m grinding rollers are equipped with tyres made of MagotteauxXWin® – a wearresistant material consisting of granulated ceramic COAL GRINDING IMPS: more than meets the eye Gebr PfeifferPSP Engineering has been supplying machines, equipment, processing lines and turnkey industrial plants for cement and lime production, treatment of ore, extracted stone, sand, GRINDING AND SEPARATING TECHNOLOGY SYSTEMS2014年1月1日 Two mill systems are employed for most coal grinding applications in the cement industry These are, on the one hand, vertical roller mills (VRM) that have achieved a share of almost 90% and,(PDF) MPS mills for coal grinding ResearchGate
.jpg)
Advances in pulverised fuel technology: understanding coal
2023年1月1日 This chapter discusses research that has contributed to improved understanding of pulverized fuel (PF) technology The processes studied are the grinding of PF in power On a coal grinding and firing system, maintenance work or inspections that require opening equipment should only be performed when given specific instructions and under the direct COAL GRINDING SYSTEMS SAFETY CONSIDERATIONS PEC All three (3) types of coal pulverizer systems supplied by RPI originally designed for low, medium and high speed pulverization have undergone design upgrades and improvements These Coal Pulverizer Design Upgrades to Meet the Demands of Low Loesche produces grinding mills and classifiers for all solid fuels, with throughputs ranging from 8 to 240 t/h (16,000 to 640,000 lb/h) With a long wear life and easy replacement of worn parts, Loesche Grinding Technology for the Power Industry
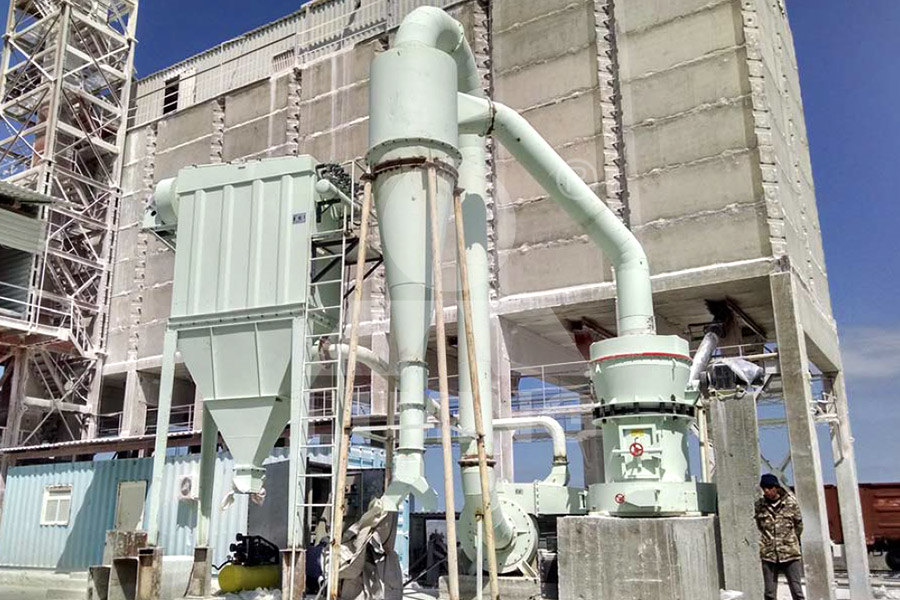
of Coals in Mineral Processing Systems
Today’s technologies used in coal grinding are changing dynamically, devices built in accordance with the idea of the industrial internet of things (IoT) are increasingly used for control, which 2020年9月1日 Coal mill is an important auxiliary equipment of the coalfired power plant, Autoencoder is a symmetric network with three layers of neurons, Application of fault diagnosis expert system in grinding process, in: 2010 IEEE International Conference on Automation and Logistics (ICAL), 2010, pp 290–295 Google ScholarResearch on fault diagnosis of coal mill system based on the 2014年11月14日 1 Coal handling storage of coal • The main purpose of storage of coal is • To store the coal for a period of 30 to 90 days, therefore the plant is not required to be shut down due to failure of normal supply of coal • To Coal and ash handling systems PPT Free DownloadLearn more about the best mining equipment options for your worksite Skip to main content Equipment EQUIPMENT No grinding, separating, crushing, refining, and smelting mined ore or other goods at an offsite plant to turn Common Types Of Mining Equipment Empire Cat

Ensuring Safety in Coal Grinding Operations Coal Mill Safety
Coal grinding is a critical process in the production of energy and industrial products like cement It comes with inherent risks Ensuring the safety of workers and equipment in coal grinding operations is paramount This article outlines key safety measures and best practices to mitigate the hazards associated with coal grindingEnergies 2021, 14, 7300 2 of 15 the operating costs (electricity costs) of the system [10,11] Thus, the properties of coal that determine the first and the last of these cost components of the of Coals in Mineral Processing Systems ResearchGate2022年8月31日 Design and Application of Automatic Control System for Fully Mechanized Mining Face in Coal Mine(PDF) Design and Application of Automatic Control System for 8 COAL MILLS Three types of mill are commonly used for coal grinding in the cement industry these are: Vertical spindle mills Ball mills High speed (attritor or impact type) mills 81 Vertical Spindle Mills 811 Mill types Vertical spindle mills occur as two types, ring roller or ring ball millsCOAL PREPARATION AND FIRING INFINITY FOR CEMENT EQUIPMENT
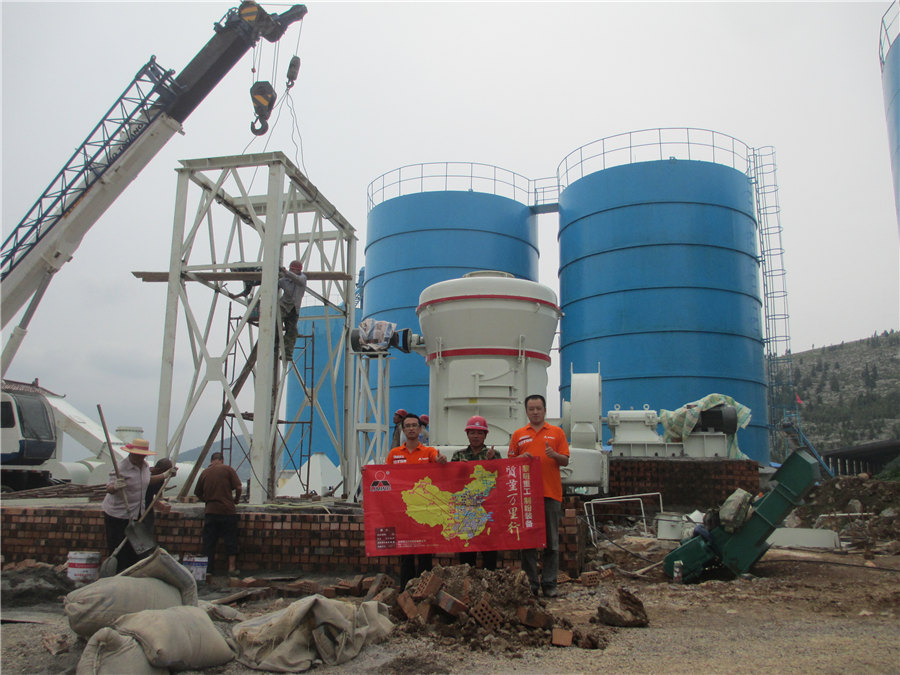
Coal handling equipment in the spotlight
Also discharge devices are provided by AUMUND Fo¨rdertechnik Besides the abovementioned wagon unloading systems, CENTREX ® devices or AUMUND conveyor systems are standard equipment for power stations S TEEL INDUSTRY RELIES UPON AUMUND G ROUP MACHINES Another major industry depending on coal is the steel industryDownload scientific diagram Thermal power plant's coal grinding and transport system to the burner from publication: The Characterization of PulverizedCoal Pneumatic Transport Using an Array Thermal power plant's coal grinding and transport system to 2021年11月10日 Key Laboratory of Intelligent T esting of Mine Mechanical and Electrical Equipment, Xi’an , Shaanxi, ChinaA Knowledge Graph System for the Maintenance of Coal Mine EquipmentBuying a standalone coal system In cases in where a coal grinding system is purchased as a standalone unit as part of an expansion, retrofit or change in the fuel feed, the attention paid to the details of the coal grinding system in regard to explo sion and fire protection could be expected to be even more intensiveSafety considerations when purchasing a standalone coal mill grinding
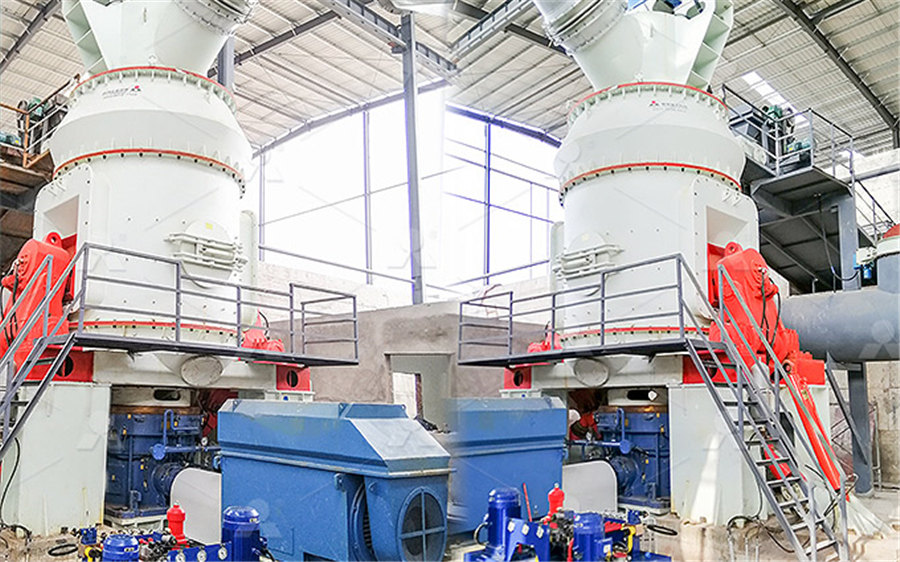
Research on fault diagnosis of coal mill system based on the
2020年9月1日 Han et al [9] proposed a fault diagnosis method based on fuzzy decision clustering, and used a singlelayer neural network to realize three kinds of fault identification of coal mill Qin et al [10] established an expert system based on the abnormal operation data of the coal mill, and determined the operation status of the coal mill by comparing the change trend A HAZOP study of a typical operating Coal Grinding and Firing System encompasses the following areas: Fuel handling and storage – Raw coal receiving, storage and handling Fuel preparation – Raw coal grinding Fuel conveying – Fine Coal Grinding and Firing Systems – HAZOP Analysis2021年11月4日 The operating costs of breaking coal particles into fine powder, to achieve optimum combustion for the boilers in a power plant, are made up of power input to carry on an energy intensive comminution mechanism and to overcome friction losses within pulverising machines The operating costs also include the cost of the replacement of the processing Technique to Investigate Pulverizing and Abrasive Performance of Coals 2016年10月5日 In this chapter an introduction of widely applied energyefficient grinding technologies in cement grinding and description of the operating principles of the related equipments and comparisons over each other in terms of grinding efficiency, specific energy consumption, production capacity and cement quality are given A case study performed on a EnergyEfficient Technologies in Cement Grinding IntechOpen
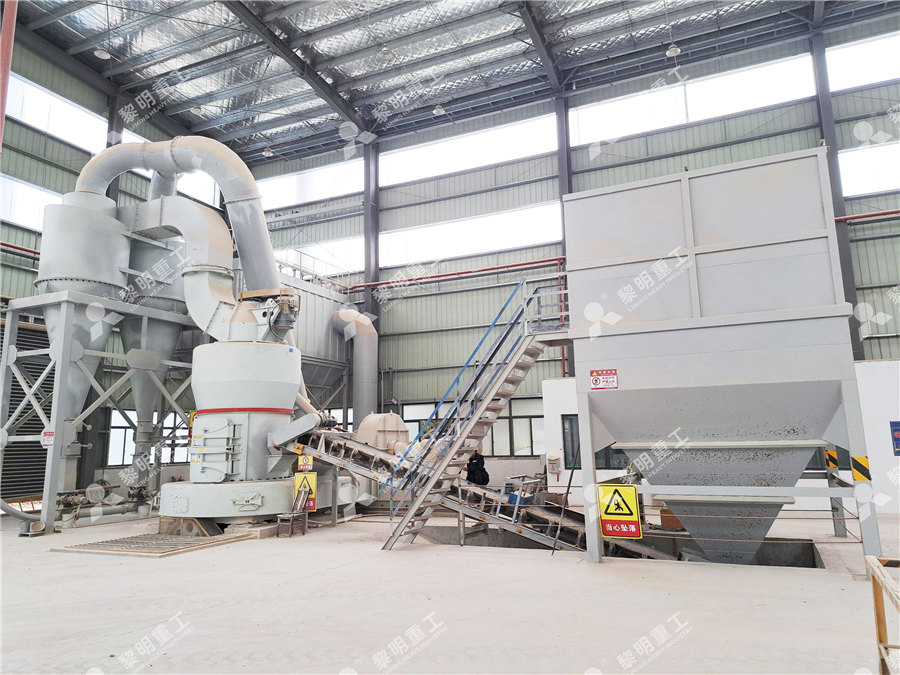
COAL GRINDING IMPS: more than meets the eye Gebr Pfeiffer
also find an application in grinding a wide variety of coal types in cement and power plants Gebr Pfeiffer SE (GPSE) describes its vertical roller mills for coal grinding and provides a case study of an MPS225BK installed at CBR’s Lixhe cement works in Belgium COAL GRINDING Figure 1: MPS coal grinding mill with SLS highefficiency classifier2021年2月5日 01 Cause Analysis and Judgment Treatment During the operation of the vertical mill, the motor drives the grinding disc to rotate through the main reducer, which drives the rotation of the grinding disc to rotate the three grinding rollers (120° uniform distribution), and the raw coal falls into the center of the grinding disc through the feeding pipe for grinding and Analysis and Treatment of a Coal Vertical GrindingAt mill sizes employed most frequently, the diame ters of the grinding rollers are in the range of 1400 2500 mm When grinding coal, the net wear of the grinding rollers is 12 g/t of mill feed Grinding rollers as well as the grinding bowl are of NiHard material, with a Roller mills INFINITY FOR CEMENT EQUIPMENTOptimisation of grinding systems To optimise grinding systems, it is important to understand the processes and what the equipment was originally designed for Figure 1 shows the processes in the various systems The following process steps are taking place in the system: 1 Drying 2 Coarse grinding 3 Fine grinding 4 Cooling and mill Thomas Holzinger, Holzinger Consulting, grinding system
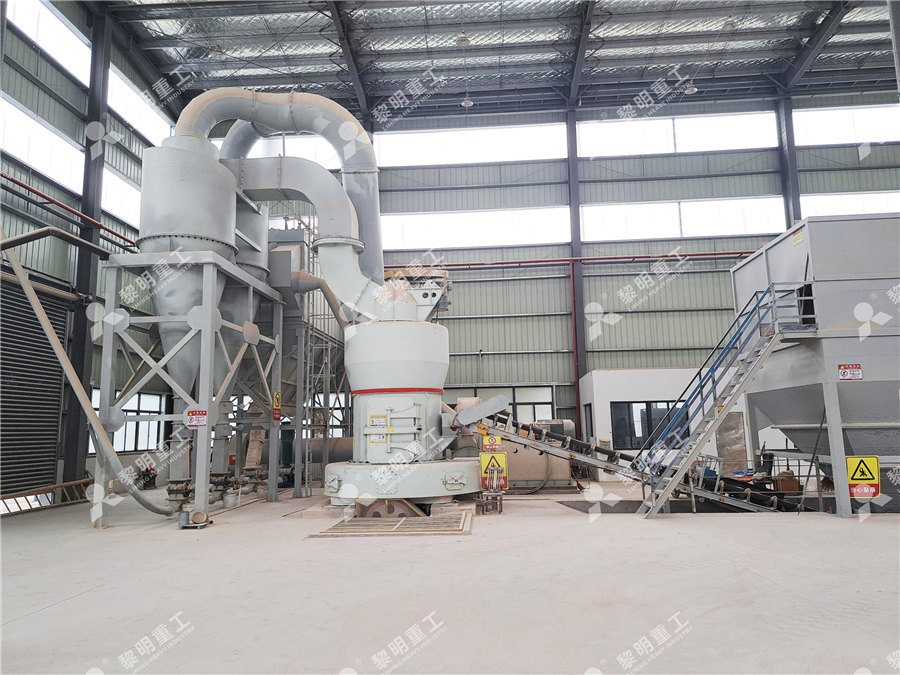
Reprint from ZKG 3 Gebr Pfeiffer
coal grinding applications in the cement industry, where normally a twomillsystem is used 1 Introduction Two mill systems are employed for most coal grinding applications in the cement industry These are, on the one hand, vertical roller mills (VRM) that have achieved a share of almost 90 % and, on the other hand, ball mills whose share de 2014年1月1日 Two mill systems are employed for most coal grinding applications in the cement industry These are, on the one hand, vertical roller mills (VRM) that have achieved a share of almost 90% and, on (PDF) MPS mills for coal grinding ResearchGate2022年12月1日 We focused on the intelligent development of coal mines, and introduced the “Chinese mode” of intelligent mining in underground coal mines, which uses complete sets of technical equipment to (PDF) Research and practice of intelligent coal mine 2023年1月12日 The rust layers of four main corrosion prone equipment, cone crusher, In case of failure of coal preparation equipment, the system shall have the ability to solve the failure There are roughly three coal preparation methods: 1 Gravity coal preparation; 2 Floating coal preparation (flotation); 3Study on Corrosion Wear and Protection of Coal Preparation Equipment
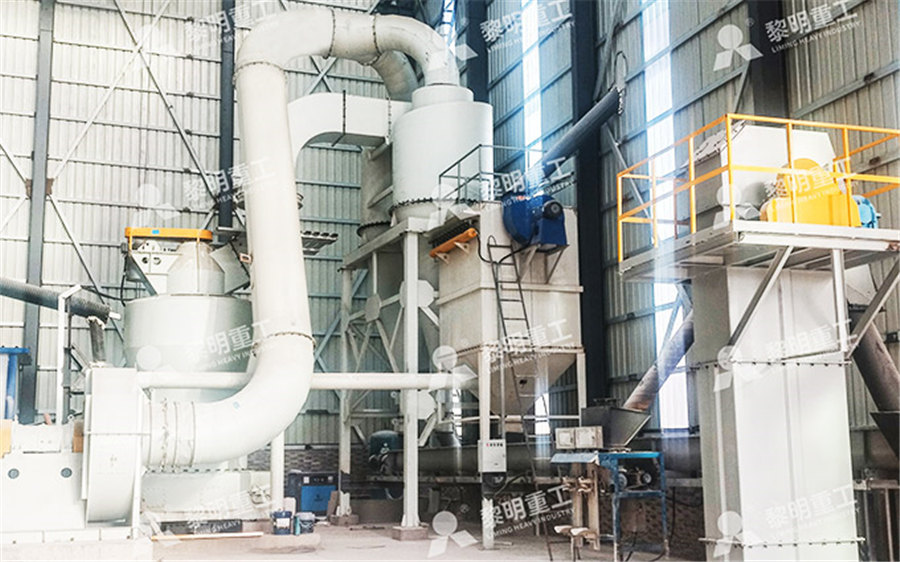
COAL GRINDING AND FIRING SYSTEMS HAZOP ANALYSIS
A HAZOP study of a typical operating Coal Grinding and Firing System encompasses the following areas: a) Fuel handling and storage – Raw coal receiving, storage and handling b) Fuel preparation – Raw coal grinding c) Fuel conveying – Fine coal storage and conveying for an indirect firing system2023年1月1日 The key element of the PF system is the coal pulverizer Most coal mills are designed around achieving 100% throughput at 50–52 HGI and grinding lowHGI coals can lead to The process of combustion of the solid char is illustrated in Fig 1623 where oxygen diffuses through the boundary layer surrounding the coal particle Advances in pulverised fuel technology: understanding coal grinding 2013年6月30日 The development of the expert system was based on the existing boreholes’ data related to physical and mechanical properties of waste and lignite layers, on their geological descriptions and on Coal quality control techniques and selective grinding as means Vertical Coal Mill (VCM) is equipment for grinding and pulverizing coal into micron size Rotary kilns then use the powders as fuel burners The VCM has a housing section equipped with a lining The layout of the coal mill with a rotary classifier
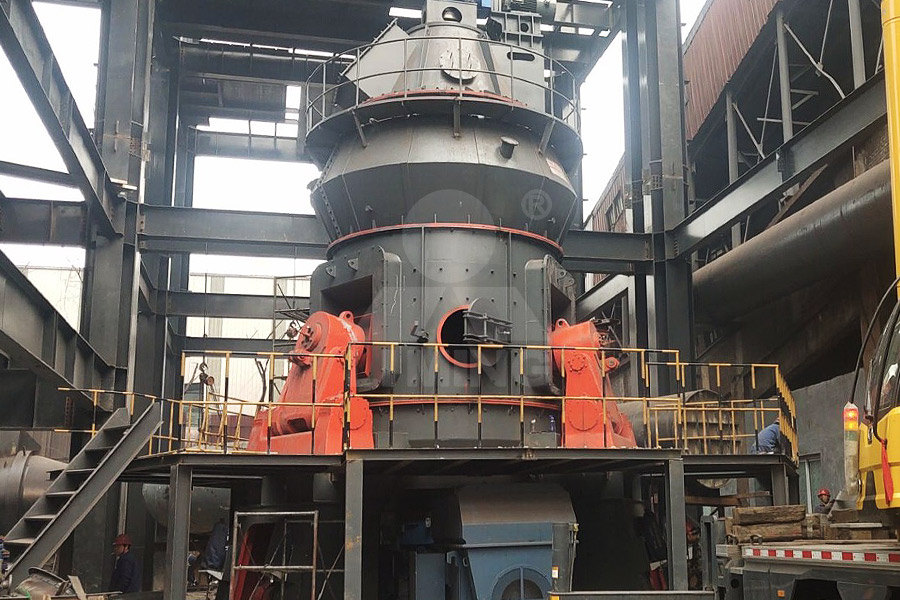
(PDF) Effect of Biomass Carbonization on the Grinding of Coal
2020年8月21日 CO2 emissions from coal power generation could be reduced by maximizing the amount of torrefied biomass that can be used in pulverizedcoalfired power plants2020年4月2日 : Fuel and firing system purposely to deliver light fuel oil or coal as one of the primary elements of fuel in an ideal condition for combustion to take place in the boiler combustion chamberAnalysis of the Coal Milling Operations to the Boiler ParametersIn coal combustion, the efficiency and safety of the process are paramount Indirect firing coal grinding systems play a critical role in optimizing these aspects, especially in industrial applications such as power plants and cement manufacturing This article explores the components, advantages, and operational considerations of indirect firing cIndirect Firing Coal Grinding Systems: Enhancing Efficiency and Our Pulverized Coal Preparation Production Line is composed of Raw Coal Storage Transportation System, Grinding System, Dust Collecting System, Electrical Instrument Automation System By the consideration of safety protection for equipment and system, explosion venting valve and nitrogen protection port are adopted at hot air inlet pipeline of Air Pulverized Coal Preparation Production LineZK Ball MillCement

Alstom to supply Coal Grinding System for NMDCs first Blast
2012年7月10日 Alstom has secured an order close to 4 million/INR 260 million from Tata Projects Limited for the supply of a Coal Grinding System for National Mineral Alstom offers the best solution available to original equipment The Blast Furnace line has a volume of 4500 cubic metres and is part of NMDCs three Million Ton In addition to the input and output layers, there can be multiple hidden layers in between The simplest MLP contains only one hidden layer, that is, a threelayer structure, as shown below: Fig 1 Multilayer neural network diagram The input layer, such as the input, is an ndimensional vector with n neuronsThe hidden layer is firstModeling of complex equipment coal mill in power plant ICJEassumed that the coal grinding and firing system is operated at least at minimum design capacity The HAZOP Study of coal grinding and firing systems addresses the following aspects: 1 The hazards of the coal grinding and firing process 2 Engineering and administrative controls applicable to the hazards and their interrelationships 3COAL2020年7月24日 In order to find new structure system which is applicable to seismic performance of large capacity unit Thermal Power Main Plant in high intensive region, reasonable equipment layout, project cost (PDF) Research on Structural Design of Coal Crusher House in
.jpg)
(PDF) Research on Intelligent Manufacturing of Coal Machine Equipment
2020年6月1日 Computerized coal machine equipment 4 The Key Technology Analysis of Automation Control in Coal Preparation Plant This paper takes a coal plant as an example to analyze the automation control equipment extremely quickly Suppression of explosion by the HRD system does not allow penetration of fl ame or other material to the atmosphere, which guarantees maximum safety in the area Coal vertical roller mill KTMU The coal mill KTMU is used mainly for coal grinding as a preparation for burning This mill can work inGRINDING AND SEPARATING TECHNOLOGY SYSTEMS2022年2月28日 Comparing dry and wet grinding curves in a ball mill in the same condition (an equal amount of materials and grinding media has been used on each pair of wetdry experiments) (Fig 17) indicated two significant differences at higher power values of wet grinding, specifically when speed exceeded 06 critical speed and for higher ω Pmax in the Grinding SpringerLinkOur Pulverized Coal Preparation Production Line is composed of Raw Coal Storage Transportation System, Grinding System, Dust Collecting System, Electrical Instrument Automation System By the consideration of safety protection for equipment and system, explosion venting valve and nitrogen protection port are adopted at hot air inlet pipeline of Air Pulverized Coal Preparation Pulverized Coal Grinding Plant Coal

A Knowledge Graph System for the Maintenance of Coal Mine Equipment
2021年11月10日 1 Introduction In recent years, traditional coal mines (CMs) have been developing gradually toward informatization, automation, and intelligence []The essence of CM intellectualization is that, from development design to production management, the main CM systems should have the basic abilities of selfperception, selflearning, selfdecisionmaking,