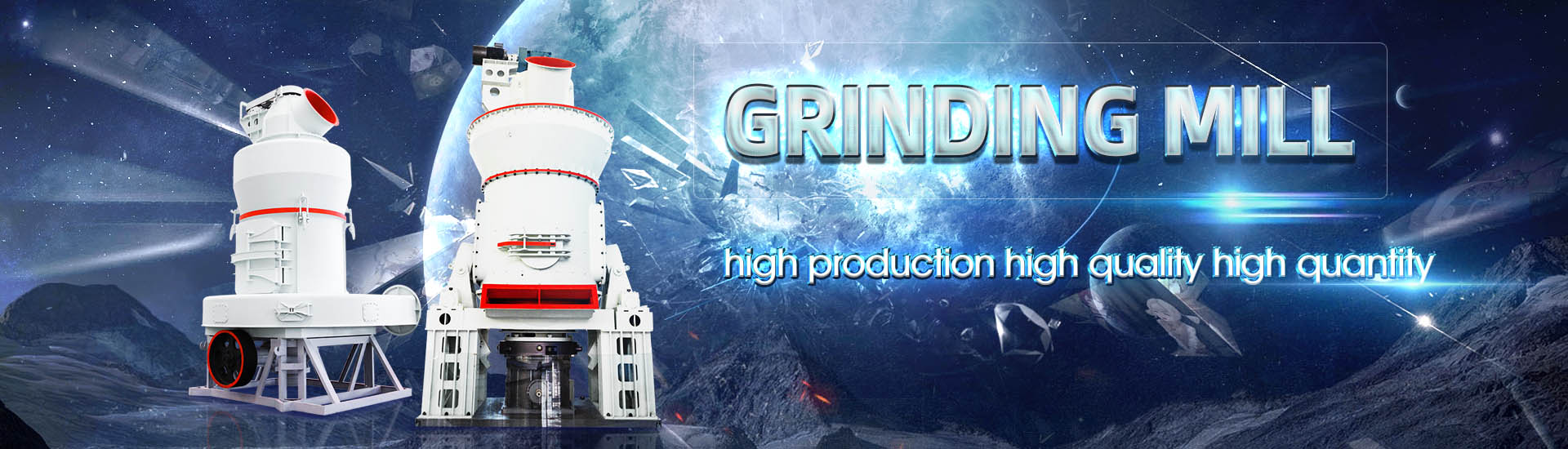
Coal mill production
.jpg)
Coal Mill an overview ScienceDirect Topics
Coal mills or pulverizers play a very essential part in the coalfired power production system Coal mills grind the coal into fine powder, and the primary air entering the mill dries and drives the coal into the power plant furnace for combustion Mills can be a bottleneck for the power generation Production of cement also requires a supply of electrical energy, expressed as Cement PlantThe Loesche coal grinding mill range is divided into two serial types: Small twin mills constructed to individual specifications (LM 122 D to LM 202 D), with table diameters from 1,200 to 2,000 LOESCHEMILLSWhen we manufacture a coal mill, we will comprehensively take into account the production scale, site, raw coal quality, operating conditions, and other aspects of the target project for reasonable design, so as to perfectly match the kiln Coal Mill in Cement Plant

Coal Mill Construction and Operation PDF Energy
This document provides an overview of coal mill construction and operation, focusing on bowl mills It discusses the types of mills including low, medium, and high speed mills as well as bowl, ball, and tube mills2012年5月1日 The paper presents development and validation of a coal mill model to be used for improved mill control, which may lead to a better load following capability of power plants Derivation and validation of a coal mill model for controlThere are two broad categories: (a) hard coal, which includes coking coal (used to produce steel) and other bituminous and anthracite coals used for steam and power generation; and (b) Coal Mining and Production2013年1月1日 Coal products, such as fly ash and furnace bottom ash, find application in the production of both cement and concrete While in cement manufacture, coal as a fuel is its Coal utilisation in the cement and concrete industries
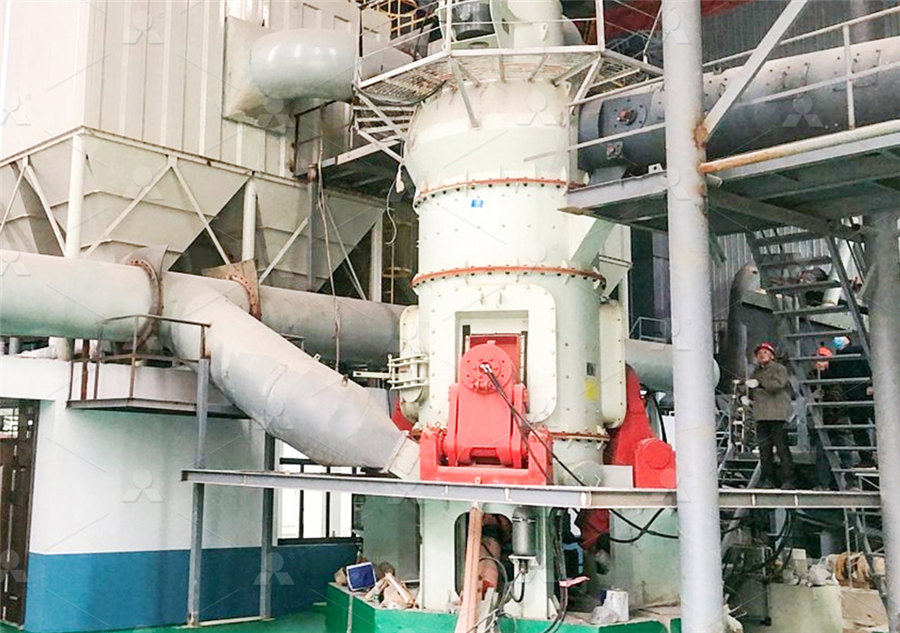
An investigation of performance characteristics and energetic
2020年8月12日 This study shows the performance of a currently running vertical roller coal mill (VRM) in an existing coalfired power plant In a power plant, the coal mill is the critical 2023年1月24日 Our open database on global coal and metal mine production 12 covers worldwide mining activities of metal ores and coal, on an individual mine level It comprises An open database on global coal and metal mine production2016年3月1日 According to the International Energy Agency’s (IEA) ‘Coal Information 2015’ report, global coal production fell by 065% yearonyear to 802Bnt in with coal for cement production Similarly, in October 2014, Misr Beni Suef Cement announced plans to build a US$279m coal mill by the end of 2015 Next, in November Coal for cement: Present and future trends2013年1月1日 This chapter seeks to explore the relevance of coal in the production of cement, The vast majority of coal mill designs are based upon a 50 to 55 HGI design point However, grindability is a complex issue and such factors as coal moisture content, required fineness (high volatile coals can require a coarser grind) Coal utilisation in the cement and concrete industries
.jpg)
Air Swept Coal Mill Coal Mill In Cement Plant
Air Swept Coal Mill Working Principle First, the raw coal is fed into the feed chute by the feeding device Then, the hot air with a temperature of about 300 ℃ enters through the air intake pipe and begins to dry the raw coal while they are falling2023年1月1日 Coal has been the main stay of Portland cement production and remains so with coal providing around 90% of the energy consumed by cement plants around the world It takes 200–450 kg of coal to produce 1 ton of cement In 2015 the cement industry consumed around 4% of global coal production, around 330 Mt/year (Global Cement, 2016)Coal utilization in the cement and concrete industriesMultiobjective Optimization of Coal Mill Outlet Temperature Control Using MPC Zengji Zhang1, Yicheng Zhang2, Wei Shen2, BOE Xukang Lyu3,∗ 1Sinoma International Engineering Co, Ltd, Nanjing, Jiangsu, China 2College of Computer Science and Technology, Zhejiang SciTech University, Hangzhou, Zhejiang, China 3Zhejiang New Rise Digital Technology Co, Ltd, MultiObjective Optimization of Coal Mill Outlet Temperature 2022年12月30日 A coal mill works by grinding coal into a fine powder using large metal rollers Cost of hydrated lime production equipment Aug 26, 2024How does a coal mill work? LinkedIn
.jpg)
Vertical Coal Mill for Coal Grinding in Cement Plant Power Plant
Vertical coal grinding mill integrates crushing, drying, grinding, powder selection and conveying; It has simple system and compact structure Vertical coal mill covers an floor area about 50% of the coal ball mill with the same specification; Coal vertical mills can work in openair environments, greatly reducing the cost of investment The design of the vertical coal mill system is simple The coal vertical mill, also referred to as the vertical roller coal mill, is an advanced equipment developed by our company It combines modern technology with our extensive experience in powder manufacturing This coal pulverizer efficiently integrates coal grinding and drying, providing highperformance and energysaving featuresHighEfficiency Vertical Coal Mill Enhancing Coal PulverizationIn order to control the energy production of the plant, the coal flow into the furnace is an very important factor Unfortunately, it is not possible to measure the coal flow from the coal mill to the furnace The coal flow out of the mill is often estimated based on the incoming coal flowCoal Mills SolidsWikiThe influence of pulverizing process parameter, such as electrical current of the driving motor, mill capacity, boiler production, coal types on mill vibration are investigated to identify the potential malfunction of beater wheel mills and their associated components for Pulverizer Wikipedia
.jpg)
Coal Ball Mill Grinding for Different Kinds of
20tph Coal Ball Mill For Clean Coal Powder Production Line In Vietnam Read More 85tph Cement Ball Mill Put Into Operation In Indian Cement Plant Read More Previous slide Next slide Free Material Testing Home » Product Our ATOX® Coal Mill has large rollers with great grinding capability of virtually all types of raw coal The rollers work harmoniously with a highlyefficient separator and feed sluice to consistently and reliably deliver coal meal to your desired ATOX® Coal Mill FLSmidth CementCoal Mills are used to pulverize and dry to coal before it is blown into the power plant furnace Operation The coal is feed into the coal mill through a central inlet pipe where gravity is used to lead the coal to the bottom of the mill, where the Coal Mills SolidsWikiOperators can adjust grinding variables, such as coal flow and mill rotation speed, Bauxite Grinding Mill: Unveiling the Role in Aluminum Production; Copper Ball Mill: A Comprehensive Guide; Coal Mill Pulverizer in Thermal Power Plants; Contact Info Phone: +86 +86 :Coal Mill in Thermal Power Plant: Enhancing Efficiency and
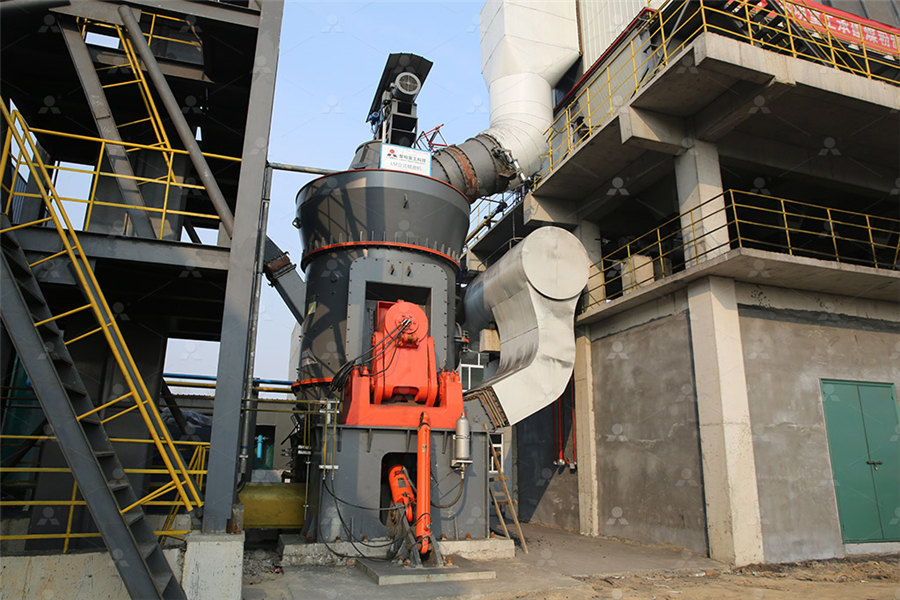
Coal mill pulverizer in thermal power plants PPT SlideShare
2012年11月17日 2 1Introduction Coal continues to play a predominant role in the production of electricity in the world, A very large percentage of the total coal is burned in pulverized form Pulverized coal achieved its first commercial success in the cement industry At Wisconsin Electric Power Company, the use of pulverized coal was also shown to be a viable fuel for Coal Mill Safety: A Critical Aspect of Power Plant Operations Introduction Coal Mill Safety In Cement Production Industries Ideas on Emergency Inerting Comparison: CO₂ inerting – CO₂ fire extinguishing Turnkey Safety Concepts for Preventive Explosion Protection Coal Mill Safety: A Critical Aspect of Power Plant Operations Coal 2020年8月12日 This study shows the performance of a currently running vertical roller coal mill (VRM) in an existing coalfired power plant In a power plant, the coal mill is the critical equipment, whose An investigation of performance characteristics and energetic Safe operation of coal grinding systems: Raw coal silo protection against fire and explosions Safe operation of coal grinding systems: Raw coal yard management The purchasing process for coal grinding systems needs changes Talk at a virtual seminar, November 2023 Accept the probability that the fire and explosion safety of your coal grinding system is nothing more than a mirageFire and explosion protection of coal grinding systems Where are
.jpg)
coal grinding machine CHAENG
Vertical Coal Mill is specially used for ultrafine grinding of raw coal and bituminous coal materials in cement, power plants, iron and steel plants and other fields The GRMC coal vertical mill produced by CHAENG adopts special structural design and production process, which is energysaving and environmentally friendlyIn discussion: Coal Mill Safety At best, coal mill safety is not well understood and, at worst, it is ignored When it comes to coal mill systems, most cement plant operators just presume that the supplier of the equipment knows all of the standards and rules and is 100% capable of making a system that conforms to these and is therefore safeIn discussion: Coal Mill Safety Coal Mill Safety, Explosion and In this episode of the DustSafetyScience Podcast, we interview Vincent Grosskopf, founder of Coal Mill SafetyHe has over 40 years of experience in bulk material handling industries, 25 of which were spent in dust explosion DSS055: Coal Mill Safety In Cement ProductionUnder a given production running condition, the electricity current intensity of the coal mill decreases from 479 AM to 465 AM, which is a remarkable achievement for the coal mill running process This method may provide a feasible online solution for coal mill optimizationA Modeling and Optimizing Method for Electricity Current
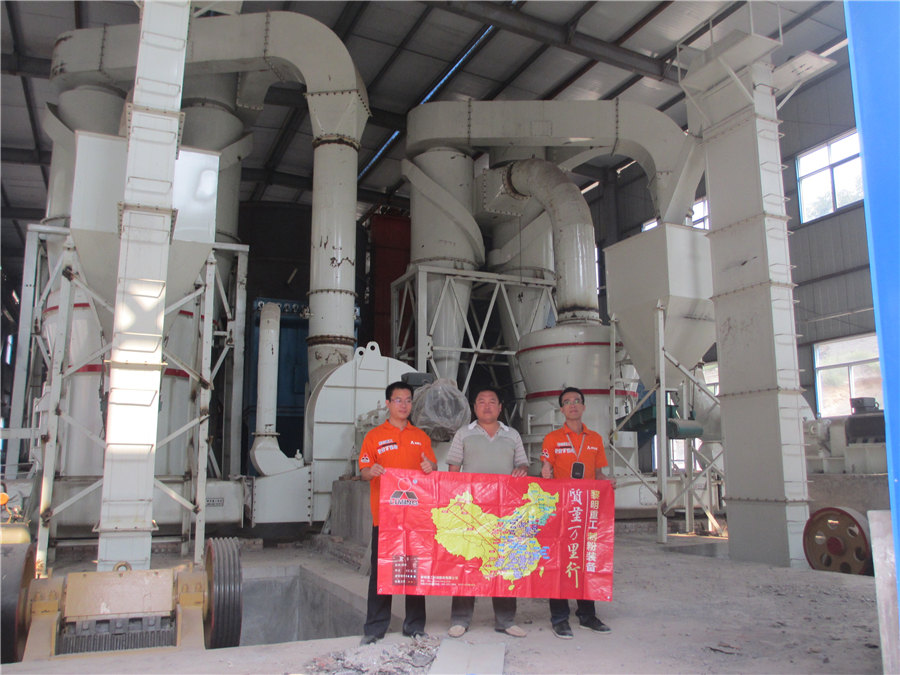
Coal Dust Explosion Protection: Ensuring Safety in industries using
Coal dust explosions are among the severe hazards in industries using coal, posing significant risks to personnel and infrastructure These explosions occur when fine coal particles become airborne and come into contact with a heat source in an enclosed environment, leading to a rapid combustion event Given the catastrophic potential of such incidents, robust measures for coal 2020年8月12日 To understand the performance of a vertical roller coal mill, the real operational tests have been performed considering three different coal sources Obtained results indicate that grinding pressure, primary air (PA) temperature and mill motor current have a tendency to rise by increasing coal feeding mass flow rates for all used coalAn investigation of performance characteristics and energetic Coal mills, essential components in power generation and various industrial processes, pose significant safety risks if not properly managed These mills, used to grind coal into a fine powder for combustion, present potential hazards such as fire, explosion, and mechanical failures This article outlines best practices and precautions to ensure thBest Practices and Precautions Coal Mill Safety, Explosion and In coal combustion, the efficiency and safety of the process are paramount Indirect firing coal grinding systems play a critical role in optimizing these aspects, especially in industrial applications such as power plants and cement manufacturing This article explores the components, advantages, and operational considerations of indirect firing cIndirect Firing Coal Grinding Systems: Enhancing Efficiency and
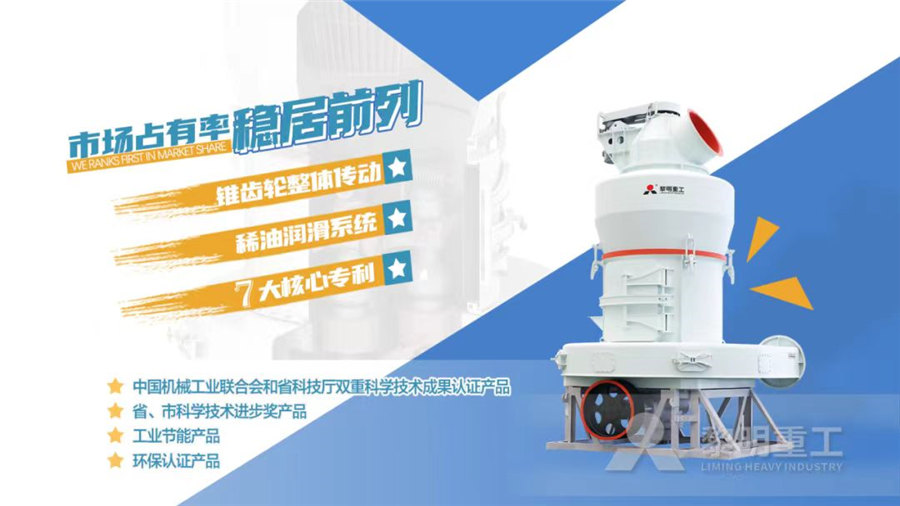
Optimisation of coal mill systems, with fire and explosion
We help operators of coal, lignite and petcoke grinding systems to make production of cement and lime products SAFE About Optimisation of coal mill systems, with fire and explosion protection This talk pertains to indirect firing systems in form of airswept mill systems, both horizontal ball mill and vertical roller mill systemsThe mediumspeed coal mill can handle different types and quality of coal, which can adapt to different coal supply and production needs Energy Efficient and Low Cost Our ZGM MPS coal vertical mill uses highefficiency pulverizing technology to MPS ZGM Coal MillGrinding Equipment YingYong MachineryRingRoll (BowlMill) and BallRace Mills comprise most coal pulverizers currently in service at pulverized coal power plants The grinding rolls are stationary in this design, while a worm gear drive rotates the ring (commonly known as the bowl) With lost production of approximately 864 MWh per day, Coal Pulverizer – Power Plant Pall Corporation2016年11月16日 Syngas is an essential platform chemical for producing chemicals and fuels, whose market volume is expected to grow strongly Today, syngas is mainly produced from fossil resources and thus emits large amounts of greenhouse gases (GHGs) The GHG emissions of syngas can be reduced by alternative feedstocks such as biomass, CO2, and steel mill off Syngas from What? Comparative LifeCycle Assessment for Syngas
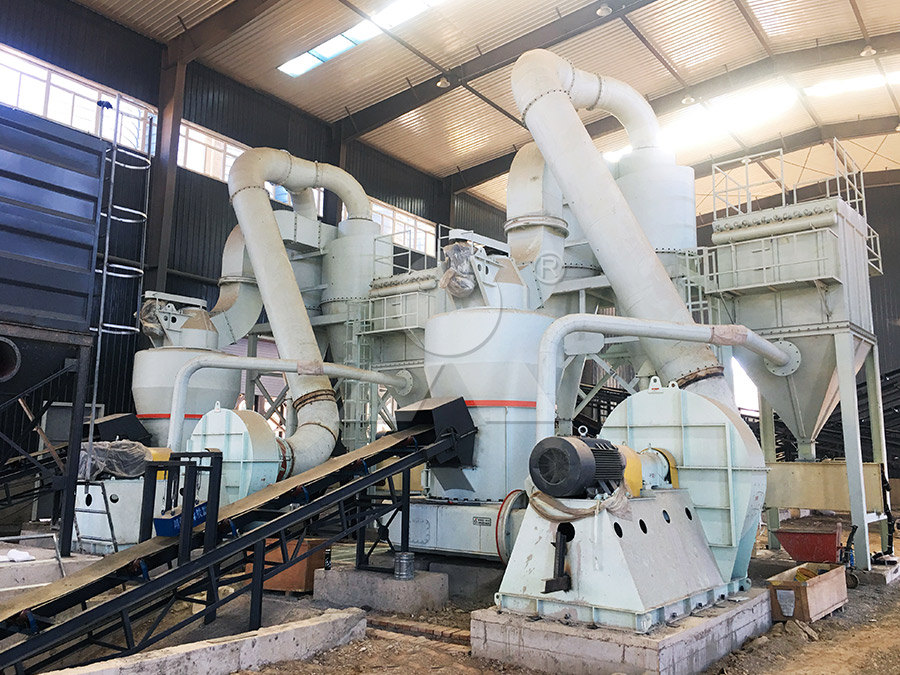
MPS mills for coal grinding AYS Engineering
2021年3月12日 This mill is installed in the US and in operation since 2002 The production rate is 24 t/h with a power consumption of 168 kWh/t at a fineness of 5% R0090 mm As second product coal is ground to 85% R0090 mm with a From the coal yard, the coal is transfer to the mill bunkers through conveyor belt The bunkers are sized for an effective capacity of twelve (12) hours at BMCR with design coal Each mill bunker has one hopper, connected to the feeders Mills operate when the bunker coal gate valves are opened, coal is allowed to flow to the gravimetric feedersAnalysis of the Coal Milling Operations to the Boiler Parameters2022年1月27日 Coal mill production should be carried out at the lowest temperature The temperature control of the inlet area of the mill should be combined with the situation of volatile matter, DISCUSSION ON SAFETY PRODUCTION OF COAL MILLING A coal mine mantrip at Lackawanna Coal Mine in Scranton, Pennsylvania Coal miners exiting a winder cage at a mine near Richlands, Virginia in 1974 Surface coal mining in Wyoming, US A coal mine in Frameries, Belgium Coal mining is the process of extracting coal from the ground or from a mine Coal is valued for its energy content and since the 1880s has been widely used Coal mining Wikipedia
.jpg)
What is the role of a coal mill in the clinker manufacturing process?
2023年6月29日 The coal mill is primarily used to grind and dry the moist raw material that is added to the process providing the necessary heat energy for the production of clinkerThe ball mill is a device that grinds materials up to a consistent size, including pulverizing coal for combustion in power generation, cement production, and other industries The Ball Mill for Coal PulverizationHow Is Coal Pulverized in a Ball Mill?2023年5月1日 Coalbased fuels are coupling to largely the world carbon emissions; the global coal consumption in iron and steel production has been estimated to be about 9,305 TWh in 2022 [10] Life cycle assessment of steel produced in an Italian integrated steel mill Sustainability, 8 (8) (2016), p 719 Crossref View in Scopus Google To what extent could biochar replace coal and coke in2012年5月1日 Sensors for coal flow measurement from the mill to the furnace have become available on the market (Blankinship, 2004, Department of Trade and Industry, 2001, Laux et al, 1999)Unfortunately the equipment tends to be expensive and requires frequent calibration; thus it cannot be used directly for control purposes at this time of writingDerivation and validation of a coal mill model for control
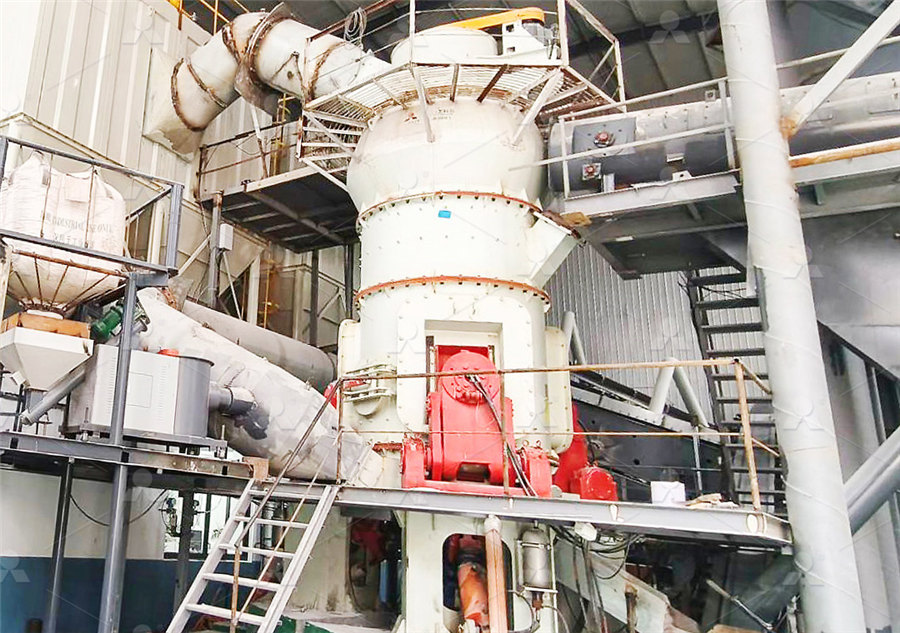
Act NOW to make your system safe! Coal Mill Safety, Explosion
This website has been specially developed for operators of coal, lignite and petcoke grinding systems for the production of cement and lime products Asking CoalMillSafety for assistance is a good idea both in the early stage of planning and when a system is already in operation Should you be in doubt about the correct fire and explosion protection of your system, you very likely 2024年10月24日 The Dolvi steel mill, located in Maharashtra, is one of JSW Steel’s key production sites Operational since 1994, the mill has undergone several upgrades to embrace cuttingedge technologies The upcoming blast furnace promises to be a paragon of innovation, incorporating the latest advancements with an emphasis on ecological sustainabilityJSW Steel to Boost Production with new Blast Furnace at Dolvi Mill