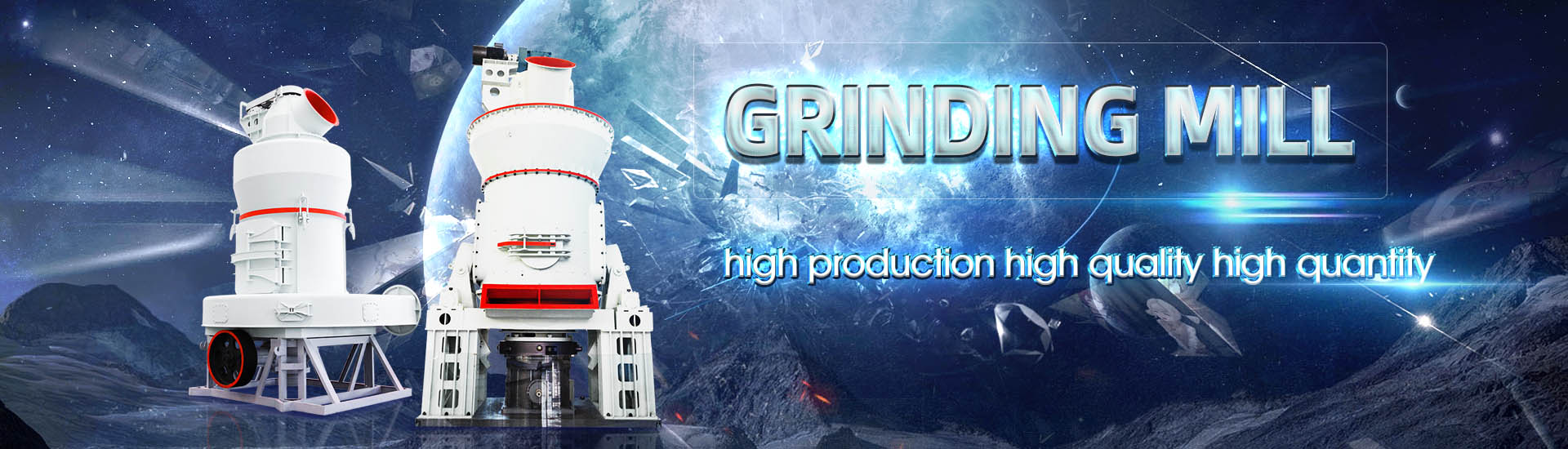
Coke equipment process flow
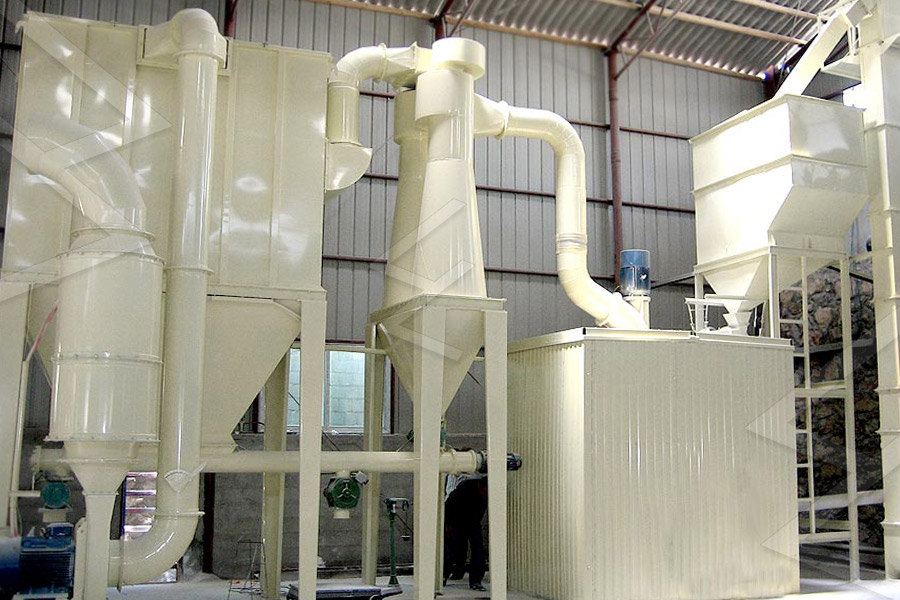
TKISAIST2015PaperUsing modern coke oven technology
The gas flows to the coke oven battery are conducted in the direction of battery length, oven length and oven height, which require an adaptable distribution of media The Hyundai Steel coke oven batteries are using the COMBIFLAME heating system which consists of special heating 100,000 coke ovens and associated gas treatment facilities and service machines worldwide, ThyssenKrupp Industrial Solutions offers its customers a palette of systems and processes Coke Plant Technologies ThyssenKrupp coke making plant consists of coal preparation, coke oven batteries and by product plant Coke making process flowsheet is given in Figure 2 Coke oven batteries are built withCoke making process flowsheet Download Scientific DiagramIn cokemaking, Paul Wurth ofers tailormade and stateoftheart solutions for your turnkey construction projects, modernisations, top to stamp charging conversion as well as hot COKEMAKING TECHNOLOGY Paul Wurth
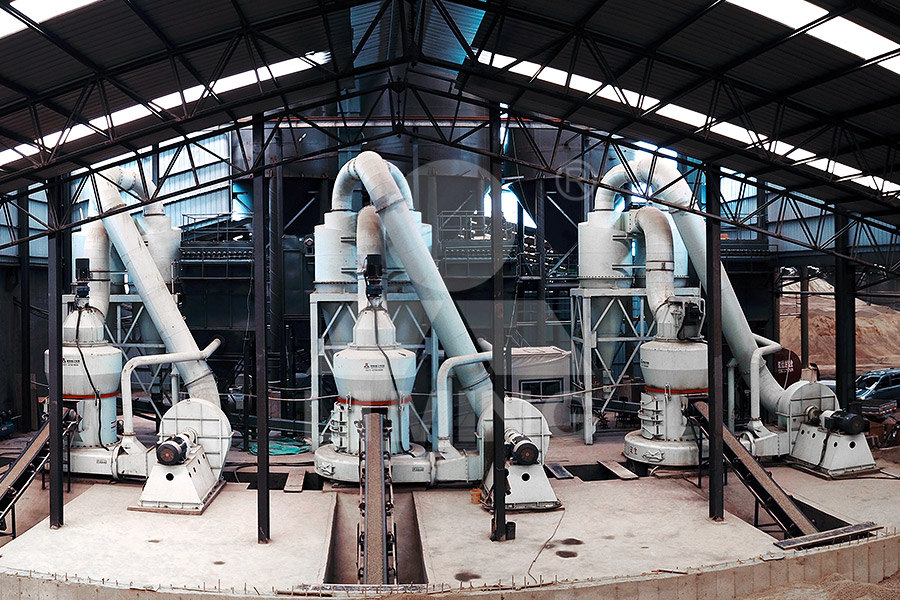
Technical Report UDC 662 741 SCOPE21 Cokemaking Process
the process comprises a fluidized bed coal dryer, a pneumatic preheater for rapid heating of coal to 330–380°C, and a hot briquetting machine for coal fine Commercial plants using the 2019年7月19日 The goals of coking process control are realizing steady heating of coke oven, enhancing production of coke oven and quality of coke, reducing energy consumption and Coke Making: Most Efficient Technologies for Greenhouse CDQ is a system to cool the hot coke brought out of coke ovens at a temperature of about 1,000 °C with inert gas and generate electric power by steam produced in the waste heat recovery INTRODUCTION OF CURRENT TECHNOLOGIES FOR COKE DRY 2017年12月15日 Three cases of coke production process based on the quenching mode and waste heat recovery are researched through thermodynamic, technoeconomic and CO 2 Modeling, thermodynamic and technoeconomic analysis of coke
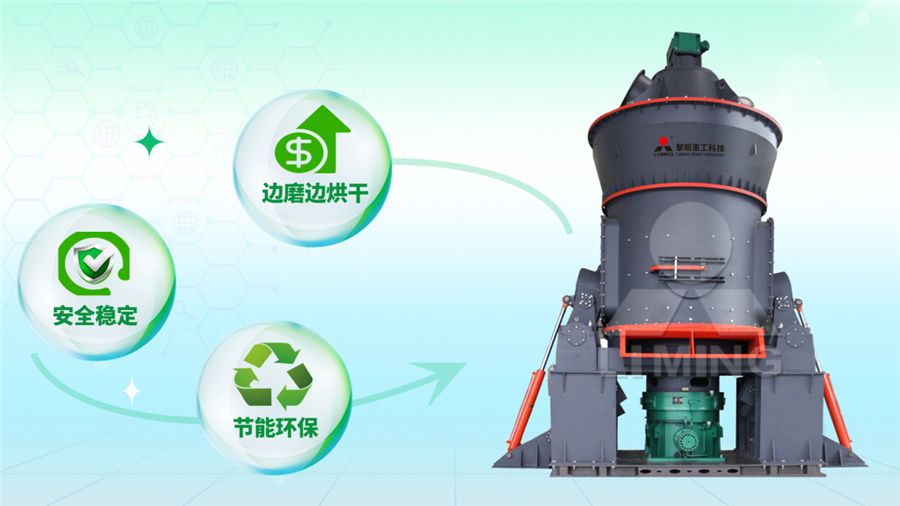
Comparison of Byproduct and HeatRecovery Cokemaking
2021年7月22日 There are three proven processes for the manufacture of metallurgical coke: the byproduct process, the heatrecovery process and the beehive process The heatrecovery 2021年1月1日 A synergy model of material and energy flow analysis for the calcination process of green petroleum coke in rotary kiln January 2021; Material and energy flows analysis ofthe major equipments A synergy model of material and energy flow analysis Reduction in coke rate in blast furnaces; SINTERING PROCESS A Sinter Plant typically comprise the following subunits as shown below SINTERING PROCESS The raw materials used are as follows After melting, the reduction process is completed as hot Coke OvensSinterBFBOF Route SAILBy using existing equipment from the complex and incorporating other process efficiencies, WTL’s preliminary design study for the proposed needle cokeDCU integration project presented TCOR a Design integrates delayed coking, needle coke
.jpg)
122 Coke Production US Environmental Protection Agency
%PDF16 %âãÏÓ 133 0 obj > endobj xref 133 96 00000 n 00000 n 00000 n 00000 n 00000 n 00000 n 00000 n 00000 n 00000 n 00000 n 00000 n 00000 n 00000 n 00000 n The coke so produced inside the heater tubes provides additional resistance to heat transfer between the flue gas and the process fluid Since the coil outlet temperature (COT) is to be kept constant, one may end up by firing more fuel to achieve the desired COT, thereby increasing the tube skin temperature or tube metal temperature (TMT) due to the additional resistance Process flow determines coker heater performance2019年11月14日 Coking is a complex process It features a large time constant, strong nonlinearities, and timevarying characteristics To achieve good control performance, it is important to obtain a precise COT in a realtime fashion; but this is difficult owing to restrictions imposed by the structure of a cokeoven and operating costsIntelligent Optimization and Control of Coking Process2015年3月9日 Fig 1 Typical flow diagram of a byproduct coke oven plant Environmental issues The coke oven is a major source of fugitive air emissionsThe coking process emits particulate matter (PM), volatile organic compounds (VOCs), polynuclear aromatic hydrocarbons (PAHs), methane, at approximately 100 gm/ton of coke, ammonia, carbon monoxide, hydrogen sulfide Understanding Coke Making in Byproduct Coke Oven Battery
.jpg)
Coal cokefired power plant equipment Qlar
Accurate fuel flow and the resulting improved control of NOx emissions are essential for modern power plants With accurate flow management and precise weighing accountability, you’ll get safe, reliable, uninterrupted material flow And that’s going to increase efficiency, eliminate downtime and keep your business running smoothlyCoke oven gas is a byproduct of the steel industry produced by the degassing of coal Once the gas is used in the process it is typically recovered and used as fuel In this case the areas that use the gas are billed by the utility department for their usage The main gas line is presently measured and each plant is billed equally for usageBHCS39447 Panametrics Coke Oven Gas Flow Measurement App 2017年11月19日 It then provides the overall reaction and a process flow diagram depicting the major steps These steps include: 1) ammonia absorption into salt water, 2) production of carbon dioxide from limestone, 3) carbonation to form sodium bicarbonate, 4) thermal decomposition to produce sodium carbonate, 5) regeneration of ammoniaSoda ash manufacturing and process flow diagram PPTSee a stepbystep process for restoring carbonation due to loss of water when the fountain dispensing system is only dispensing high pressure air Check the water supply in a few simple steps After water flow is restored to the Self Help CokeSolutions
.jpg)
PROCESS ECONOMICS PROGRAM SP Global
46 Petroleum Coke by Delayed Process Flow Sheet 227 47 Typical Weight Loss Profile During Coke Calcination 98 48 DualGasification 48 Petroleum Coke by Delayed Process Major Equipment 92 49 Petroleum Coke by Delayed Process Utilities Summary 2024年2月12日 In this paper, the characteristics of flowinduced noise in ethylene cracking furnace tubes were analyzed, under both pre and postcoking conditions, using the LargeEddy Simulation (LES) and generalized Lighthill's acoustic analogy model The results revealed that the flowinduced noise was broadband noise, with rapid attenuation occurring in the frequency Analysis of flowinduced noise characteristics of ethylene cracking 2021年1月1日 Evaluation and analysis of exergoeconomic performance for the calcination process of green petroleum coke in vertical shaft kiln January 2021 Thermal Science 26(00):294294Evaluation and analysis of exergoeconomic performance for the be charged into the ovens to the delivery of coke in suitable fractions to the final users Complemented by the most advanced automation and control systems along the entire coking process, our plants and equipment meet the highest standards in terms of coke productivity and quality, emission control, energy consumption, user friendliCOKEMAKING TECHNOLOGY Paul Wurth
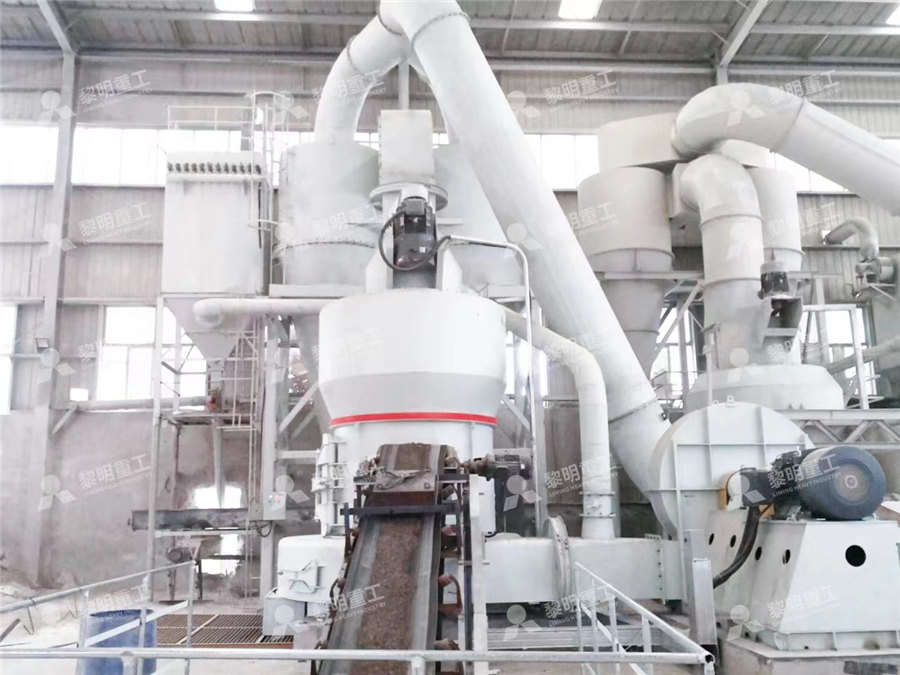
Automation, Control, and Measurement System of Coke Oven
2021年8月3日 The important characteristics of the coke production are (i) coking process is a batch process and operation of each coke oven is to be based on integrated operational planning, (ii) coking process needs a minimum time which is quite large and hence coke oven plant has a high inertia, (iii) coking process has a directional flow and it is temperature and time Process variables, factors and Process interaction Air flow rates; Kiln hot gases pass upward in countercurrent to fed meal flow The hot gases have vital role in controlling thermo chemical process These gases can be divided into two categories: primary air, and tertiary airCement Manufacturing Process INFINITY FOR CEMENT EQUIPMENTfirst and then describes the nonrecovery process along with the major differences between the two that affect emissions Figure 1221 illustrates the major process equipment in a schematic diagram of a byproduct coke oven battery Flow diagrams are provided in Figures 1222 and 3 to give an overview of the process122 Coke Production US Environmental Protection Agency2024年5月18日 The CocaCola supply chain and manufacturing process represent one of the most extensive, complex, and efficient operations in the global beverage industry, encompassing key steps in CocaCola’s supply chain As a brand that’s recognized worldwide, coca cola’s ability to manage its operations seamlessly across different continents, cultures, and markets is Coca Cola Supply Chain Management And Manufacturing
.jpg)
Crushing Equipment for Petroleum Coke Plant by feng li Medium
2016年12月12日 FLM1000 grinding machine is suitable for petroleum coke, including crusher, conveyor equipment (including auger and powder pneumatic conveying),grinding machine Simple process flow diagram Purchase Coke Equipment Repair Parts Find Your Local Contact Want to Serve Coke®? Find out how to get vending machines, CocaCola Freestyle®, dispensers more Please select Please The CocaCola Company has the Equipment CokeSolutionscontributors Process flow schemes, emission characteristics, and emission control technology are discussed for each process Tables 511 and 512 list the emission s factors for direct process emissions in petroleum refineries Factors are expressed in units of kilograms per 1000 liters (kg/103 L) or51 Petroleum Refining1 US Environmental Protection AgencyCoke Plant Technologies Pioneering coke plant technologies are part of our daily business The effi ciency and environmental performance of our plants are renowned worldwide Tailor made complete coke oven plants from a single source – that’s our commitment and your advantage gained from a partnership with us 500 coking plants worldwideCoke Plant Technologies ThyssenKrupp
.jpg)
EVALUATION AND ANALYSIS OF EXERGOECONOMIC
important equipment in the process, TD is used to remove the oxygen out of the demineralized water to reduce the corrosion on the interface of the equipment Figure 1 A schematic of the calcination process Mathematical model of exergy flow To analyze the exergy flow of the calcination process, the formulation of the exergyPDF On Jan 1, 2014, Aliasghar Rohani and others published Calcinations of Petroleum coke Find, read and cite all the research you need on ResearchGate(PDF) Calcinations of Petroleum coke ResearchGate2012年7月20日 The present disclosure provides for processes including a coke catcher that may be emptied during normal operation or steam standby, thereby overcoming the deficiencies in the prior design as discussed above, the coke catchers and process flows disclosed herein protecting the secondary transfer line exchanger from foulant while not limiting the time between heater Coke catcher Justia PatentsThe CDQ process mainly consists of a CDQ furnace, loading device, coke discharge device, elevator, electric locomotive and coke tank trolley, coke tank, primary dust collector, secondary dust collector, CDQ process boiler unit, and circulating fan, dust removal ground station, water treatment unit, automatic control part, power generation part, etc Depending on the design, What is coke dry quenching? DBM Metallurgical Intelligence
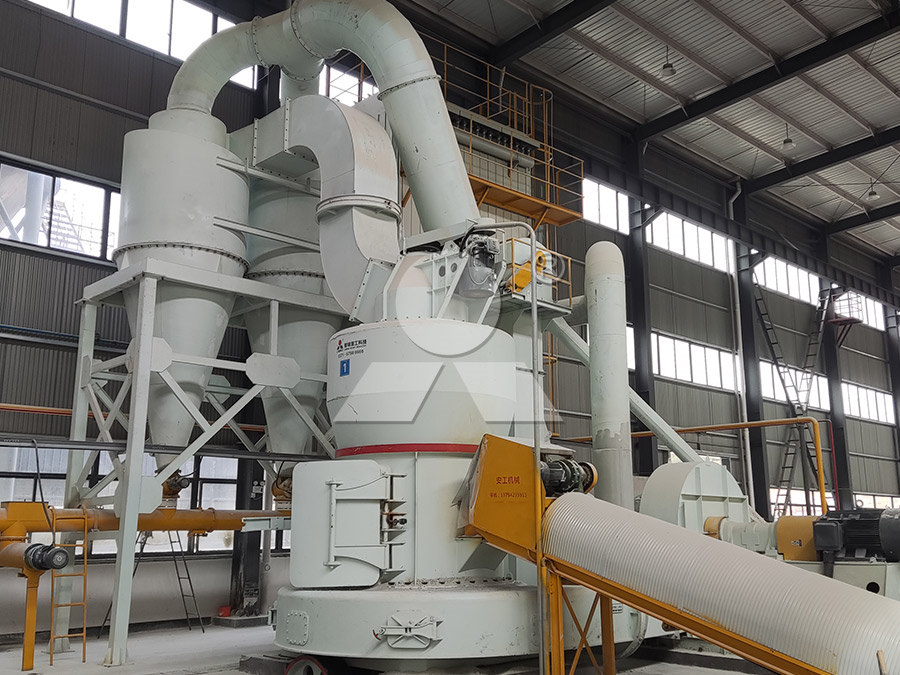
Development of Steelmaking Process for Stainless Steel by Top
the LDRHOB process for equipment of LDRHOB Fig 2 Schematic converter flow diagram of coke addition in LD Table 2 Ch emica 1 composition and size of coke Technical Report temperature up to the bath temperature, the heat of carbon solution, and the heat of carbon oxidation When the coke materials like iron ore, base mix, sinter, coke, fluxes (limestone / quartzite), etc also air blast / O2 In blast furnace the process is also known as “Counter current process” as solid raw material is being charged from the top and hot air is being blown from bottom During the process theRECOMMENDED GUIDELINE FOR IRON STEEL SECTOR2014年12月20日 Calcined petroleum coke is used for the production of carbon anodes in the HallHéroult aluminum smelting process due to a combination of low impurity levels, ready availability, and relatively low cost This article provides a review of the history and use of calcined petroleum coke for anode production and describes the different calcining technologies used The History and Future Challenges of Calcined Petroleum Coke Production 2024年6月15日 Concurrently, as coke ratios decrease, coke deterioration becomes more pronounced; this significantly affects the smelting process and increase the demand for highquality coke Coke plays an irreplaceable role in blast furnaces (BFs), acting as both the skeleton of the stock column and the permeable layer of the gas flowPhysical and chemical properties of metallurgical coke and its
.jpg)
Delayed coker Wikipedia
A 4drum delayed coking unit in a petroleum refinery A delayed coker is a type of coker whose process consists of heating a residual oil feed to its thermal cracking temperature in a furnace with multiple parallel passes This cracks the heavy, long chain hydrocarbon molecules of the residual oil into coker gas oil and petroleum coke [1] [2] [3] 2013年3月16日 Fig 2 Principle of direct reduction process Gas based process In the gas based reduction processes, a vertical shaft kiln is used in which iron ore is fed into the top of the kiln and finished sponge iron is drawn off from the Direct Reduced Iron and its Production Processes – CONTENTS 1 INTRODUCTION, 1 2 SUMMARY * , Economic Aspects Petroleum Coke SP Global2021年1月22日 Coke dry quenching (CDQ) technology for recovery of waste heat from hot coke to generate process steam and power is well established and adopted worldwide that meets these objectives of Design and Engineering Challenges for Installation of Coke Dry
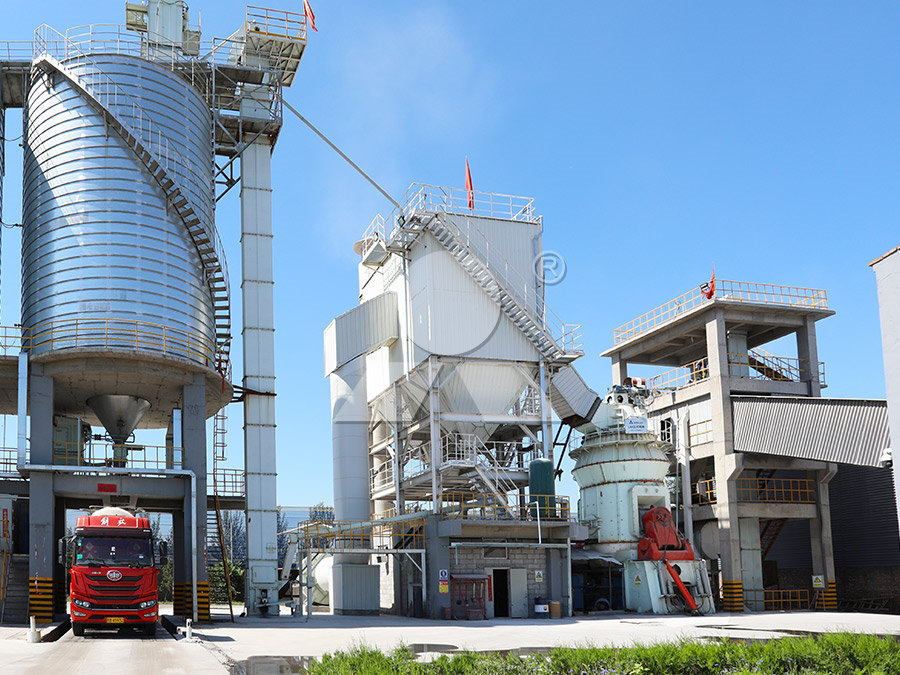
Abstract Process Economics Program Report 274 SP Global
71 Fuel Alcohols and Power Cogeneration from Petroluem Coke Process Flow Diagram 82 Fuel Alcohol Power from Pet Coke, 55% Recycle Major Equipment 84 83 Fuel Alcohol Power from Pet Coke, 55% Recycle Utilities Summary 2017年12月15日 As the penetration of CDQ technology in China is 36% in 2014 [2], the coke production process mainly uses CWQ technology and is characterized by significant heat waste due to the flue gas and the quenched water used for cooling the incandescent coke and raw COGAbout 37–48% of thermal energy is lost from the incandescent coke at temperature of Modeling, thermodynamic and technoeconomic analysis of coke production The coke calcining process is a timetemperature function concerning three main step process involving: drying, removing of volatile matters (VM) and densification These three major steps transform the coke structure into a more ordered, electrically conductive form of carbon Important control variables are heating rate, air flow rate and final calcination temperatureCalcined Coke – Marlin Energy Group2021年7月22日 The Coke Oven ByProduct Plant Contributed by Mick Platts, ThyssenKrupp EnCoke USA Table of Contents What is it and what does it do? Coke oven / byproduct plant interface Composition of coke oven gas Duties of the byproduct plant The byproduct plant gas train Primary cooler Tar precipitators Exhauster Ammonia removal Steelmaking: The Coke Oven ByProduct Plant accci
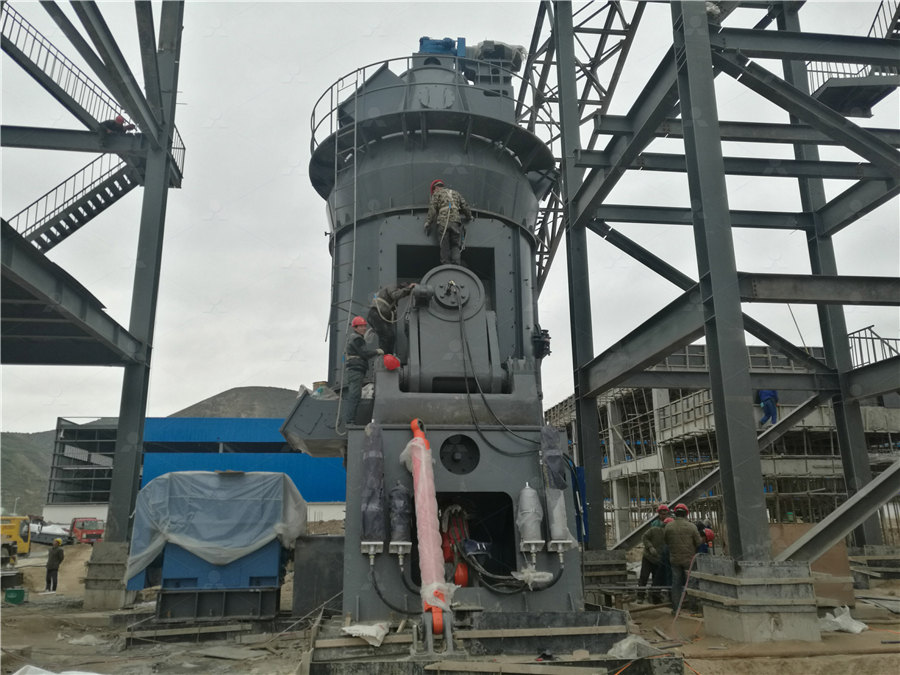
Recovery of Ammonia during Production of Coke from Coking
2019年1月26日 Recovery of Ammonia during Production of Coke from Coking Coal satyendra; January 26, 2019; The process equipments of the ammonium sulphate process are described below If excess flushing liquor is used in the water wash process, the flow rate of the blow down effluent stream is increased to maintain the circulating liquor