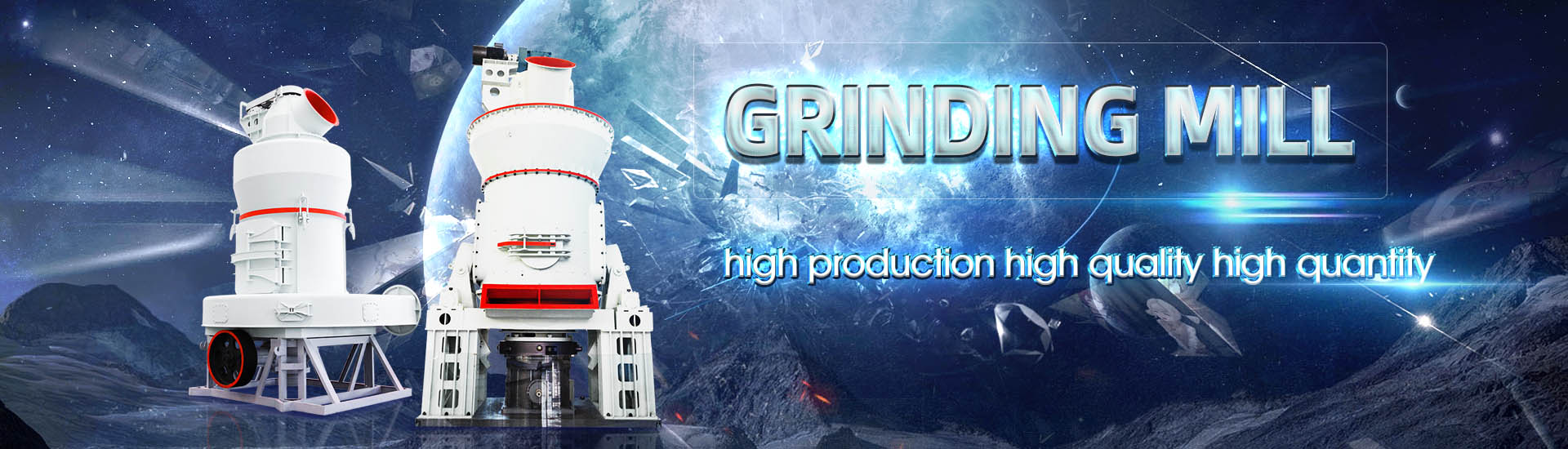
Cement raw material process regulations
.jpg)
GCCA Sustainability Guidelines for coprocessing fuels and raw
These guidelines for coprocessing of fuels and raw materials in cement manufacturing are part of a package of guidelines developed to support compliance with the GCCA Sustainability Charter 1 The GCCA Sustainability Charter has identified five key pillars which encompass the The Cement Plant Operations Handbook is a concise, practical guide to cement manufacturing and is the standard reference used by plant operations personnel worldwide Providing a The Cement Plant Operations Handbook International Cement Producing cement consumes both large quantities of raw materials and fuel, and produces substantial CO2 emissions The use of alternative fuels and raw materials in cement Guidelines for CoProcessing Fuels and Raw Materials in Cement All plants must have appropriate quality control systems in place to monitor and control the characteristics of raw materials and fuels In order to prevent critical environmental impacts, it Cement Environmental Directive Holcim
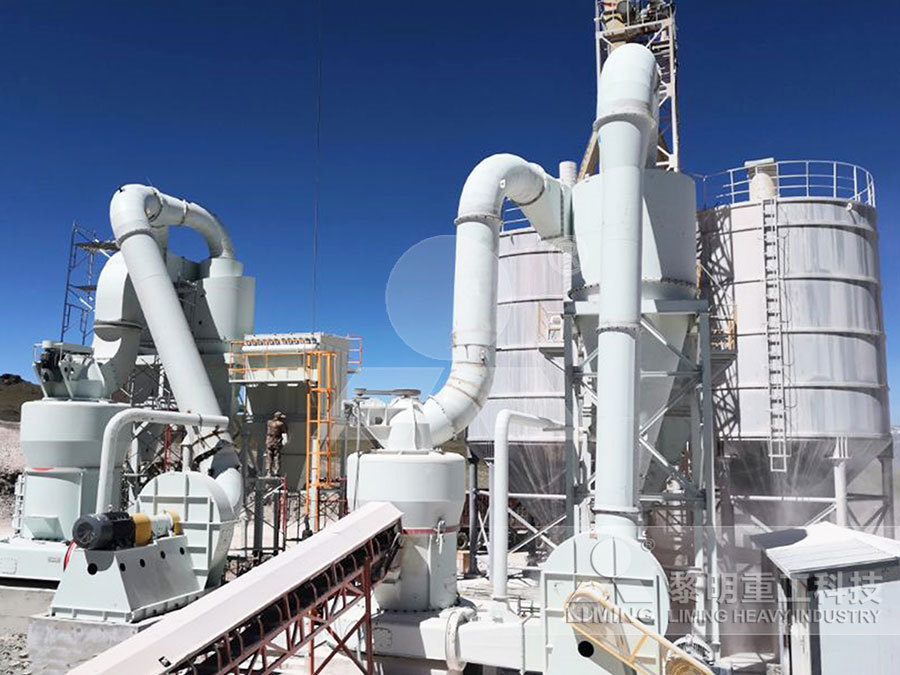
Summary Guidelines on Coprocessing Waste Materials in Cement
coprocessing of selected waste materials in the cement industry An efficient cement kiln can provide an environmentally sound and costeffective treatment/recovery option for a number These Guidelines are an update of the former GTZHolcim Guidelines on Coprocessing Waste Materials in Cement Production published in 2006 (GIZHolcim, 2006) In the past decade Guidelines on Pre and Coprocessing of Waste in Cement 2015年12月9日 Raw Materials processing included: Setting and curing and cement manufacturing process , Process Discretion: Wet process, Semidry process, Dry process and Finish process(PDF) Cement Manufacturing ResearchGate2024年6月1日 By setting specific requirements for emissions from the entire cement production process, including raw material extraction, fuel combustion and clinker production, Decarbonising cement and concrete production: Strategies,
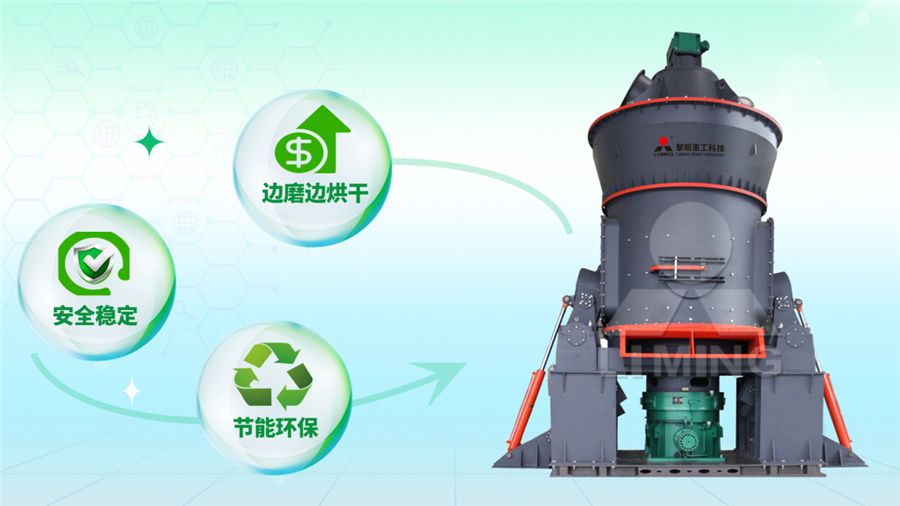
Roadmap to a netzero carbon cement sector: Strategies,
2024年5月1日 Cement production involves a complex process wherein raw materials like limestone, clay, and other substances are heated to high temperatures to produce clinker, the Deploying carbon capture and storage is unavoidable for deep decarbonisation due to the process emissions inherent to cement making Cement is the binding agent of concrete, the Deep decarbonisation of industry: The cement sector Europa2024年11月23日 Cement Extraction, Processing, Manufacturing: Raw materials employed in the manufacture of cement are extracted by quarrying in the case of hard rocks such as limestones, slates, and some shales, with the Cement Extraction, Processing, ManufacturingLime Component Limestone: Common forms of calcium carbonate used as raw material for cement manufacturing are limestone and chalkLimestone is of predominantly fine grained crystalline structure, its hardness is between 18 to 30 of the Mohs scale of hardness and specific gravity 2 To 28 Limestone usually contains admixtures of clay substance or iron compounds, Raw materials for cement manufacturing Cement Plant

From raw materials to cement
with the extraction of raw materials and ending with the finished product From raw materials to cement Extracting raw materials Crushing and transportation Raw material preparation I: Storage and homogenisation Raw material preparation II: Drying and raw grinding Burning The burning of the raw meal at approx 1,450°C is carried out2020年9月22日 Much of the processrelated water is consumed during the quarrying, crushing and washing of raw materials used in the production of cement and concrete; for example, water is used for dust Environmental impacts and decarbonization strategies in the cement The primary raw material for cement manufacture is calcium carbonate or limestone This is obtained from the quarry where, after the removal of overburden, the rock is blasted, loaded into trucks and transported to the crusher A multistage crushing process reduces the rock to stone less than 25 mm in diameterAll Pakistan Cement Manufecturars AssociationBulk material handling is a major activity and bins for raw materials, intermediate products and finished cement must reliably provide controlled flows of materials upon demand The tonnages of material to be stored at various process stages are outlined by Deolalkar in Chapter 13 of his book (Deolalkar,2009), while his Chapter 16 discusses the features of materials handlingsystemsCement Plant Raw materials INFINITY FOR CEMENT EQUIPMENT

CEMENT RAW MATERIALS BLENDING PROCESS BY USING
2023年2月1日 Raw material blending is an important process affecting cement quality The aim of this process is to mix a variety of materials such as limestone, shale (clay), sandstone and iron to produce Raw Material” (AF/ARM), conducted on 79 June 2016 This technical report highlights the training provided with respect to the use of alternative fuels and alternative raw materials within the Indian cement sector It covers the various aspects of coprocessing, includingALTERNATIVE FUELS AND ALTERNATIVE RAW MATERIALSThe major raw materials used in the manufacture of cement are Calcium, Silicon, Iron and Aluminum These minerals are used in different form as per the availability of the minerals Table shows the raw materials for Portland cement manufacture The mixing procedure of the manufacture of cement is done in 2 methods,Manufacture of Cement Materials and Manufacturing Process of 2014年11月1日 Request PDF Modelling and simulation of raw material blending process in cement raw mix milling installations A series of multivariable models composed from linear differential equations Modelling and simulation of raw material blending process in cement raw
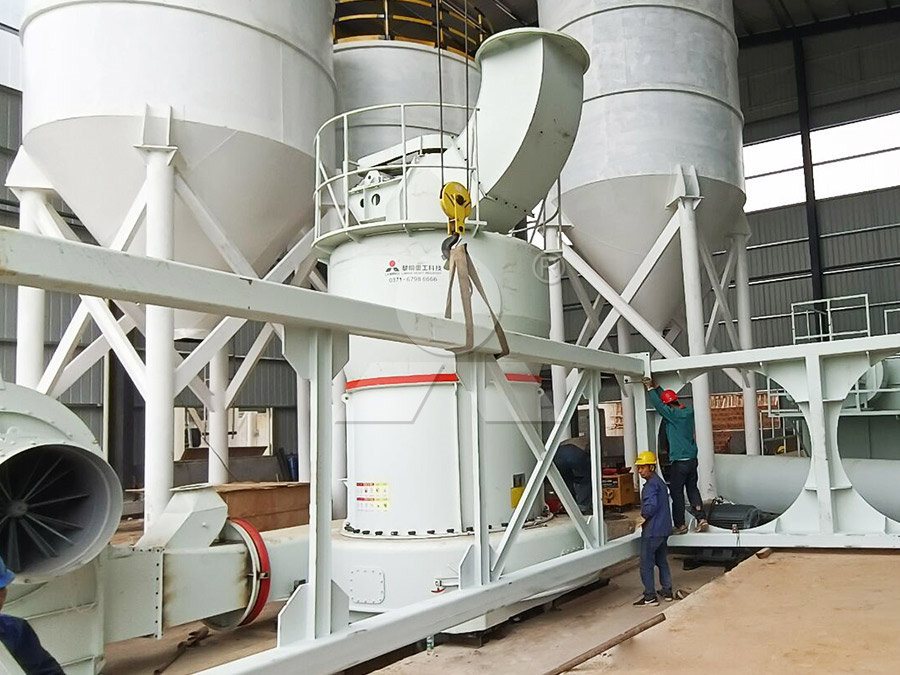
Calcium Aluminate Cements Raw Materials, Differences, Hydration
2012年5月24日 Calcium aluminate cement (CAC) has been explored as a sustainable alternative to Portland cement, the most widely used type of cement However, the hydration reaction and mechanical properties of 2004年6月1日 Request PDF Identification and control of the raw material blending process in cement industry The regulation is mainly obtained via PID [2, 3] and adaptive controllers Identification and control of the raw material blending process While each cement plant may differ in layout, equipment, and appearance, the general process of manufacturing portland cement is the same: crushed limestone and sand are mixed with ground clay, shale, iron ore, fly ash and How Cement is Made Portland Cement Association2023年10月13日 Among those, raw material shortages (the availability of limestone, the primary raw material for cement production, can influence production levels) and age of facilities (older facilities might Global database of cement production assets and upstream
.jpg)
IRISH CEMENT LIMERICK INVESTING IN OUR FUTURE
at all stages of the cement manufacturing process RAW MATERIALS Limestone, quarried on site, is the main raw material Clay overburden, also from the site, with shale and small quantities of bauxite and iron ore are also required These raw materials are crushed, ground and homogenised to produce a blend called ‘raw meal’ This raw2015年12月9日 Raw materials are used to produce the main cement elements (Mohsen, 2015) • Quarry The process of obtaining raw materials for cement manufacturing involves mining and quarrying natural materials (PDF) Cement Manufacturing ResearchGate1 Which type of secondary materials are used in the clinker / cement / concrete manufacturing? The secondary materials used in the cement industry are: Alternative raw materials (ARM), which are defined as waste materials or byproducts from other (mainly industrial) processes or societal sectors and used in clinker production to substitute USE OF SECONDARY RAW MATERIALS IN THE EU CEMENT 2024年8月20日 Raw Materials Used in the Manufacturing of Cement The preparation of cement using the raw materials involves the following process: Step 1: MiningThe extraction of raw materials such as limestone and clay from mines and quarries Step 2: Grinding processThese raw materials are grinded and crushed into a fine powderlike form This is called Understanding the Raw Materials for Manufacturing Cement
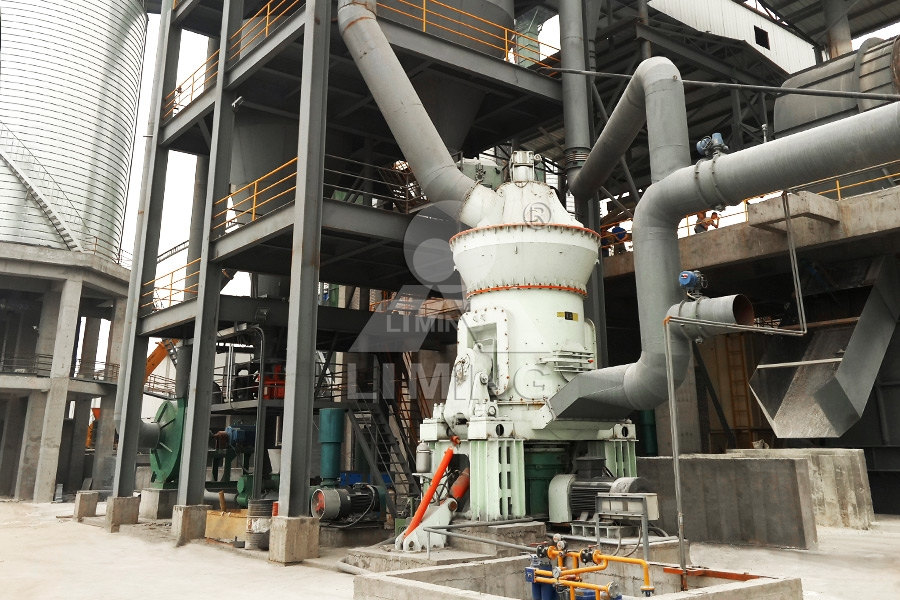
PROCESS INSTRUMENTATION ANALYTICS Cement
Cement From raw materials preparation to the finishing mill, environmental regulations Siemens solution: SITRANS F M MAG 3100 • High accuracy of 02 % ±1 mm/s • Available in sizes from DN15 to DN 2000 (½” to 78”) Cement Process Control 2020年1月1日 The demand for cement, which is one of the key components of concrete, is high in Ethiopia, but it is the most expensive and environmentally unfriendly construction materialAssessment on Cement Production Practice and Potential Cement The principal raw materials for cement manufacturing are: Limestone; Silica and alumina from basalt , shale or sand; Iron from iron ore or steel mill scale Sand stone; Pumice (volcanic ash for Portland Pozzolana cement ) Gypsum Cement Manufacturing Process INFINITY FOR The homo and stock silo transfer functions are given by the first order equations (8) and (9) respectively: Q = U U , J 1 1 + ∙ O (8)Effective Optimization of the Control System for the Cement Raw
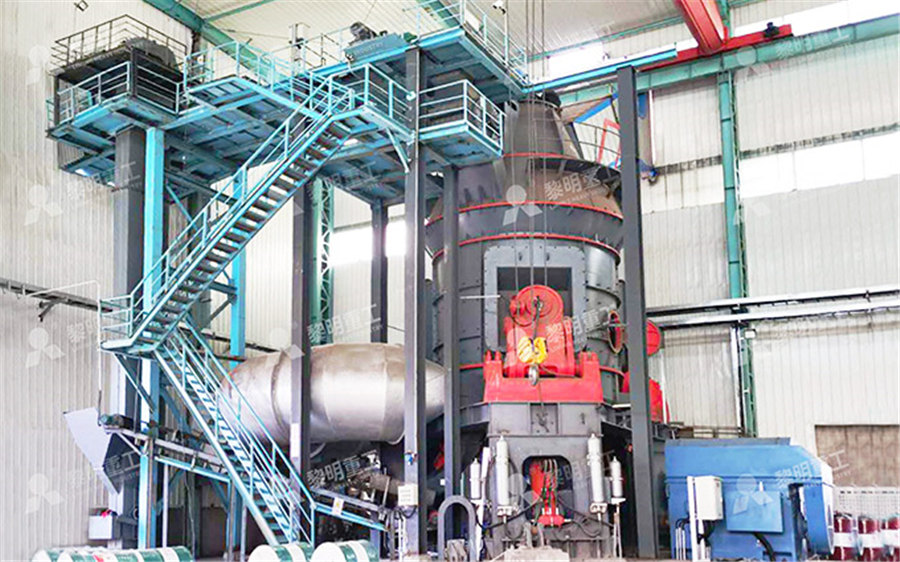
Sustainable Clinker and Cement Production by Using Alternative Fuels
The use of alternative fuels in both combustion and production processes is known as coprocessing in cement manufacturing Waste is now being used to substitute primary fuel sources like coal, petroleum, and gas in the combustion process They are usually from combustible municipal waste, refusederived fuels, biomass, or nonhazardous industrial and commercial 2021年3月3日 Cement is produced by a hightemperature (about 1500 °C) reaction in a rotary kiln of carefully proportioned and blended ratios of lime (CaO), silica (SiO 2), alumina (Al 2 O 3), and iron oxide (Fe 2 O 3)The production of cement is a chemical process requiring an accurate blend of the previously cited four key organic oxides and the limitation of several undesirable Cement SpringerLink2023年8月15日 Steps of Manufacturing Cements Extraction of Raw Materials The production of cement involves the utilization of a blend of raw materials, typically comprising calcium, silicon, In the cement manufacturing process, the raw mix undergoes a drying process to reduce its moisture content to less than 1% This dried mixture, Cement: History, Types, Manufacturing Process Science Info2020年8月25日 Cement raw material preparation: Limestone is main raw materials for cement manufacturing, and most cement plants are located next to the quarry to reduce the transportation cost; Using explosion or getter loader to mine raw materials; sending raw materials to the cement crusher to crush or hammer; crushed raw materials are stored to prevent from environment Cement Production Process Cement Manufacturing Process AGICO CEMENT
.jpg)
Microsoft Word GHG BACT paper for Cement October 6finaldoc
3000°F in the kiln Rotary kilns are divided into two groups, dryprocess and wetprocess, depending on how the raw materials are prepared In wetprocess kilns, raw materials are fed into the kiln as a slurry with a moisture content of 30 to 40 percent To evaporate the water contained in the feedstock, a wetprocess4 天之前 The manufacture of Portland cement is a complex process and done in the following steps: grinding the raw materials, mixing them in certain proportions depending upon their purity and composition, and burning them to sintering in a kiln at a temperature of about 1350 to 1500 ⁰C During this process, these materials partially fuse to form nodular shaped clinker by Manufacturing of Portland Cement – Process and MaterialsAll over the world, cement is one of the most important building materials Whether for houses, bridges or tunnels, we cannot imagine our modern world without it Join us for a short tour to experience how cement is made: starting with the extraction of raw materials and ending with the finished productHow cement is made Heidelberg MaterialsHowever, it would be seen that the most significant process and types used for raw material grinding operations in modern cement industry are: Process: Dry Closed circuit drygrinding Type of mill: Ball and tube mills Vertical Roller Mills (VRM) Horizontal roller mill (Roll Press) Roller press with Ball millRaw Material DryingGrinding Cement Plant Optimization
.jpg)
Cement Manufacturing Process The Engineering
2018年8月28日 CEMENT MANUFACTURING PROCESS PHASE 1: RAW MATERIAL EXTRACTION Cement uses raw materials that cover calcium, silicon, iron and aluminum Such raw materials are limestone, clay and sand 2022年4月6日 The cement manufacturing process involves 8 steps starting from the mining of limestone to the packing of cement We will discuss one by one all the 8 steps 1 Mining of Limestone: • Cement manufacturing process starts with the mining of limestone, which is the main raw material for the production of cementFrom raw materials to 8 steps of cement manufacturing, read2023年9月5日 Process control experts in the cement industry need to be wellversed with the process flow, the chemical reactions, and the physical transformations that occur in a cement plant They need to understand the Mastering Process Control Instrumentation in Cement 2024年5月1日 Cement production involves a complex process wherein raw materials like limestone, clay, and other substances are heated to high temperatures to produce clinker, The discussed references highlight the pivotal role of policies and regulations in steering the cement industry towards lowCO 2 emission strategiesRoadmap to a netzero carbon cement sector: Strategies,
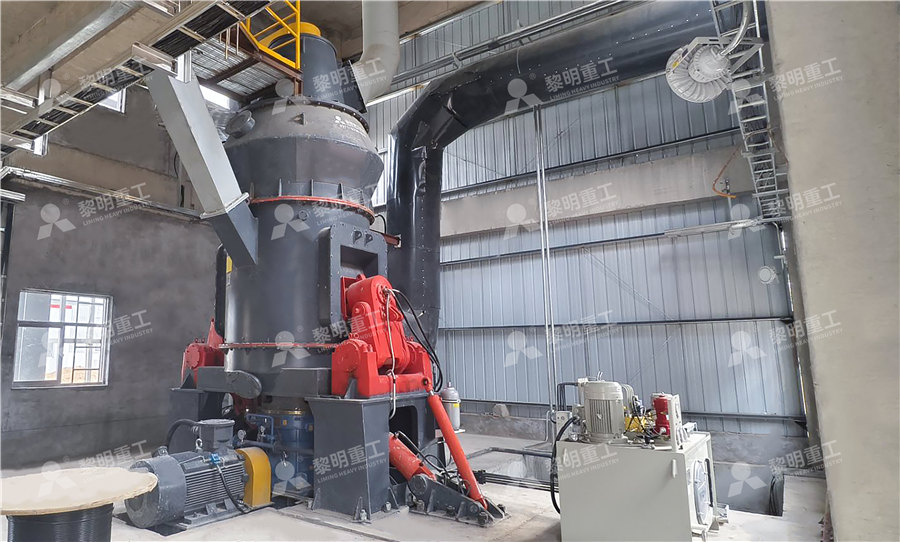
Cement Standards and Concrete Standards Standards Products
These ingredients are mixed with water to create concrete which is used as a primary construction material in buildings These cement and concrete standards allow laboratories all over the world to test and C786/C786M24 Standard Test Method for Fineness of Hydraulic Cement and Raw Materials by the 300μm (No 50), 150μm (No 2 (1) These Regulations apply to the activities of public and private entities that operate in the cement industry (2) Without limiting subregulation (1), the activities referred to in subregulation (1) are (a) the manufacture of cement; (b) the production of raw materials for cement; and (c) the supply, sale and distribution of cementGHANA STANDARDS AUTHORITY (MANUFACTURE OF CEMENT) REGULATIONSCoprocessing refers to the utilization of suitable waste material in the manufacturing process for the purpose of energy and/or resource recovery and resultant reduction in the use of conventional fuels and/or raw materials The clinker and cement manufacturing system has certain operational features that make it eminently suitable for co Alternative fuels and raw materials INFINITY FOR CEMENT EQUIPMENTIn order to convert these raw materials into clinker and cement, it is necessary to produce a raw mix with a top size of about 02 mm The reduction ratio required for most raw materials is consequently 10002000:02 or 500010,000 It is obvious that such a degree of comminution cannot be achieved through a single machine or a onestage operationEverything you need to know about cement Materials Preparation and Raw

Cement manufacturing process
Portland cement raw material mainly consists of limestone and clay Regulation of raw materials Silos for raw materials automatic systems, has witnessed tremendous advances in the 160 year history of manufacturing its own Some of the cement production process like Alumina Cement, 2014年6月10日 Evolution of the cement Process • Wet process easiest to control chemistry better for moist raw materials • Wet process high fuel requirements fuel needed to evaporate 30+% slurry water • Dry process kilns less fuel requirements • Preheater/Precalciner further enhance fuel efficiency allow for high production ratesCement manufacturing process PPT Free Download SlideShare