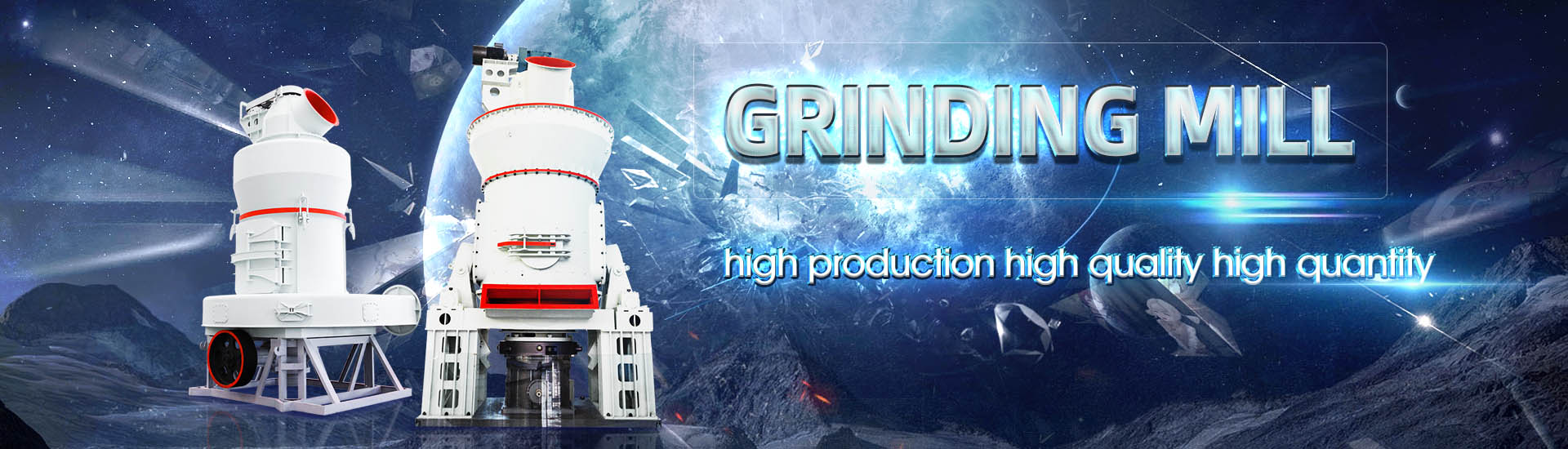
Crushed lithium carbonate recovery and processing equipment
.jpg)
Lithium processing technology Complete solutions that FLSmidth
Impurity removal from the salar brine is a critical step in the process flowsheet for production of batterygrade lithium Our MaxRTM technology provides the most advanced method in the industry, combining precipitation reactors with solidliquid separation, which allows the seeding SGS Minerals Services has experience with complete flowsheet development to recover high grade lithium products from hard rock lithium minerals SGS offers a multidisciplinary team Hard Rock Lithium Processing SGS2021年5月1日 Obtained lithium carbonate can be used for technical purposes that do not require high purity or processed into lithium hydroxide A higher degree of purification was achieved in Processing of lithium ores: Industrial technologies and case studies Bepex has been supplying processing technology for lithium carbonate or lithium hydroxide production since the early 1990s Now, with lithium producers straining to fulfill ever increasing demand, Bepex is pioneering systems to streamline Lithium Processing Systems and Equipment Bepex
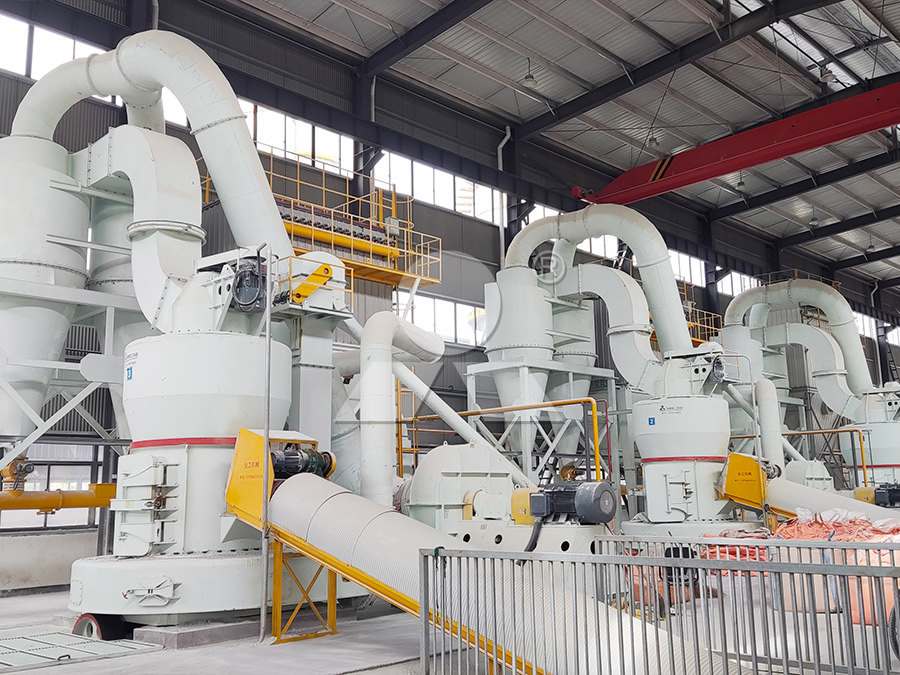
Lithium Processing Capabilities Veolia Water Tech
Veolia has supplied several process systems to leading lithium suppliers worldwide as well as having performed analytical, bench and pilotscale testing • Lithium brine concentration • This study successfully optimizes the lithium recovery process from spent lithiumion batteries through a reductive roasting and carbonation leaching technique By carefully controlling the Optimization of resource recovery technologies in the disassembly 2024年10月10日 We examine various lithium recovery methods, including conventional techniques such as hydrometallurgy, pyrometallurgy, and direct physical recycling, as well as emerging technologies like mechanochemistry, Critical Review of Lithium Recovery Methods: 2023年6月29日 Lithium is obtained mostly as lithium carbonate (Li 2 CO 3) from an evaporation process (Equation (1)), which consists of evaporating salty water for 12–18 months in ponds using solar energy The most interfering element is Lithium Production and Recovery Methods: Overview
.jpg)
Lithium extraction from hard rock lithium ores
2023年1月15日 It is found that the sulfuric acid method has a high lithium recovery rate, but with a complicated process and high energy consumption; alkali and chlorination methods can directly react with lithium ores, reducing lithium chloride Solids handling equipment, including a centrifuge and • Lithium Chloride (LiCl) • Lithium Carbonate (Li 2 CO 3) Byproduct recovery from lithium processing: • Potassium Chloride (KCl) • Sodium Sulfate (Na 2 SO 4) • Sodium Chloride (NaCl) • Potassium Sulfate (K 2 SO 4) • Boric Acid (H 3 BOLithium Processing Capabilities Veolia Water TechRecovery of Lithium Carbonate from Dilute LiRich Brine via Homogenous and Heterogeneous Precipitation Giuseppe Battaglia, Leon Berkemeyer, Andrea Cipollina,* José Luis Cortina,Recovery of Lithium Carbonate from Dilute LiRich BrineDownload scientific diagram Overview of main processing options for production of lithium carbonate from rock minerals from publication: Minerometallurgical processes for lithium recovery from Overview of main processing options for
.jpg)
What Is Lithium Extraction and How Does It Work?
By definition, lithium extraction is a set of chemical processes where lithium is isolated from a sample and converted to a saleable form of lithium, generally a stable yet readily convertible compound such as lithium carbonate Most lithium extraction processes entail some form of mining to reach underground deposits of lithiumrich minerals 2021年2月1日 Request PDF Processing of lithium ores: Industrial technologies and case studies – A review Recently, there has been a steady increase in demand for lithium (Li) and its compounds Processing of lithium ores: Industrial technologies and case studies A high lithium ore, containing approximately 6% lithium, is the main raw material used in the production of lithium salts (lithium hydroxide or lithium carbonate) from hard rock sources Building on globally diverse lithium conversion sites in the Americas, Australia and China, Albemarle has invested in both added capacity as well as new strategic processing locations around the worldLithium Resource Processing Albemarle2022年1月1日 Lithium extraction from hard rock lithium ores (Spodumene, Lepidolite, Zinnwaldite, Petalite): Technology, resources, environment(PDF) Lithium extraction from hard rock lithium ores: technology
.jpg)
Critical Review of Lithium Recovery Methods: Advancements
2024年10月10日 The integration of lithium into technological applications has profoundly influenced human development, particularly in energy storage systems like lithiumion batteries With global demand for lithium surging alongside technological advancements, the sustainable extraction and recovery of this critical material have become increasingly vital This paper DOI: 101016/JHYDROMET201710022 Corpus ID: ; Recovery of lithium carbonate by acid digestion and hydrometallurgical processing from mechanically activated lepidolite[PDF] Recovery of lithium carbonate by acid digestion and Bepex has been supplying processing technology for lithium carbonate or lithium hydroxide production since the early 1990s Now, with lithium producers straining to fulfill ever increasing demand, Bepex is pioneering systems to streamline lithium production while also reducing the energy needed and emissions resulting from processingLithium Processing Systems and Equipment Bepex2021年2月22日 carbonate production process, BMED tech nology was introduced into the above process to recycle the waste salts, as shown in Figure 1; the waste salt (sodium sulfate) can beRecovery of Acid and Base from Sodium Sulfate
.jpg)
Lithium Processing Battery Recycling Solutions
As a worldwide leader in the supply of lithium brine treatment technologies and chemical processing systems, Veolia Water Technologies helps lithium producers and recyclers meet the technical challenges associated with the rising 2023年10月6日 How is lithium carbonate produced from extracted lithium? The extraction and processing of lithium ores can result in soil erosion, habitat destruction, and water pollution if not properly managed Additionally, the Sustainable Lithium Extraction: How is Lithium Mined Over 12 to 18 months, concentration of the brine increases to 6,000 ppm Li through solar evaporation When the lithium chloride reaches optimum concentration, the liquid is pumped to a recovery plant and treated with soda ash, precipitating lithium carbonate, which is then filtrated, dried, and shipped Lithium UsesLithium Mining Processing Equipment Flow Chart JXSCLithium brine ponds: concentrating and precipitating impurities from geological lithium brines via evaporation pondsA highly concentrated lithium solution is subsequently refined and converted into lithium carbonate or hydroxide These lowcost operations are ideal for the convergence of rich lithium brines and arid climates, such as South America’s ‘lithium triangle’Lithium Extraction and Refining Saltworks Technologies
.jpg)
Lithium Production and Recovery Methods: Overview of Lithium
refining, lithium is precipitated as lithium carbonate High lithium carbonate solubility (15 g/L) and high liquid to solid leaching ratios require costly and avoidable operations to be implemented in order to enhance lithium concentration Therefore, it is suggested that more studies should focus on multistage leaching with lower L/S ratios3 primary lithium batteries along with coke and flux are fed into a shaft furnace Umicore is also able to add alkaline primary batteries that contain significant amounts of zinc to the furnaceHydrometallurgical Recovery of Materials from Lithium ion 2019年5月29日 The process allows the recovery of lithium but not the production of technical lithium hydroxide of lithium carbonate Another step, such as carbonation or electrodialysis is needed ( Figure 11 ) Concerning the lithium production from brines, the process revolves around concentrating the brines up to 6 wt% Li and removing the impurities one after the other ( Spodumene: The Lithium Market, Resources and Processes2017年10月1日 Request PDF Recovery of lithium carbonate by acid digestion and hydrometallurgical processing from mechanically activated lepidolite Lithium extraction from hardrock ores has regained Recovery of lithium carbonate by acid digestion and
.jpg)
The Lithium Mining Process
2023年3月15日 Treated with sodium carbonate, known also as soda ash, to remove lithium carbonate Lithium carbonate is then washed and dried into end product This lithium mining process also tends to consume large quantities of fresh water This water is largely drawn from aquifers, rivers, wells, or other water sources used for drinking or irrigation2014年1月1日 The acid process can be further divided into sulfuric acid (Bishimbayeva G et al, 2018;Ellestad RB and Milne LK, 1950), hydrofluoric acid (Rosales GD et al, 2016, hydrochloric acid (Margarido F (PDF) Minerometallurgical processes for lithium How it’s used for lithium recovery Brine mining is by far the most common method of lithium recovery used today But what is it, and how is brine mining used for lithium recovery? In this chapter, we’ll look at how and why brine mining relates to lithium production and explore how the principles of brine miningUnderstanding the Basics of Lithium Extraction2022年8月30日 Recovery of Lithium Carbonate from Dilute LiRich Brine via Homogenous and Heterogeneous Precipitation Giuseppe Battaglia, Leon Berkemeyer, Andrea Cipollina, * Jos é Luis Cortina,(PDF) Recovery of Lithium Carbonate from Dilute Li
.jpg)
(PDF) Research Progress of Lithium Carbonate Preparation and
2018年2月12日 Lithium carbonate (Li2CO3) was synthesised by adding sodium (Na) and magnesium (Mg) ions into a lithium chloride solution at different concentrations, followed by the addition of an appropriate 2023年1月15日 Lithium recovery process of βspodumene by sodium carbonate autoclave method (modified from Chen Y et al, 2011a, 2011b) Figure 5 Process for lithium recovery from lepidolite by sodium sulfate roasting method (modified from Li H et al, 2019; Yan QX et al, 2012c) Figure 6Lithium extraction from hard rock lithium ores (spodumene, 2023年12月19日 Evaporation ponds containing lithium carbonate in Salar de Atacama, Chile Credits: Tom Hegen By Max Werny, Yair Reem, Iris ten Have, and Fernanda Bartels The status quo — hard rock mining and The technology overview: closing the lithium supply gap with 2024年9月1日 The equipment of this process is complex and the effect on improving purity is not particularly good The principle and key factors of solidliquid reaction crystallization needs to be studied in depth to control the reaction process for the enhancement of recovery rate and purity of lithium carbonateCrystallization of batterygrade lithium carbonate with high recovery
43.jpg)
Hydrometallurgical recovery of lithium carbonate and iron
2023年12月11日 The recycling of cathode materials from spent lithiumion battery has attracted extensive attention, but few research have focused on spent blended cathode materials In reality, the blended materials of lithium iron phosphate and ternary are widely used in electric vehicles, so it is critical to design an effective recycling technique In this study, an efficient method for 2020年4月7日 During the mass recycling of spent lithiumion battery (LIB) packs, the packs that have not been disassembled are heattreated to remove organic substances; further, the valuable metals obtained in the burnt product are recovered in the leaching process Numerous methods have been reported for the efficient recovery of valuable metals in the leaching process; Recovery Rates of Used Rechargeable LithiumIon Battery2024年7月29日 The proposed Li recovery process outlined in this study is The parameter ranges were selected based on consideration such as solubility of CO 2 and lithium carbonate, equipment capabilities Earlystage recovery of lithium from spent batteries via COCarbonation Process to Manufacture Lithium Carbonate from Lithium Sulfate DongHyeon Choi and JeiPil Wang* Department of Metallurgical Engineering, Pukyong National University, Busan 48513, Korea *Corresponding author: Abstract This study focuses on producing Li 2 CO 3 powder from Li 2 SO 4,Carbonation Process to Manufacture Lithium Carbonate from Lithium
.jpg)
Review of Lithium as a Strategic Resource for Electric Vehicle
2024年10月23日 This article presents a comprehensive review of lithium as a strategic resource, specifically in the production of batteries for electric vehicles This study examines global lithium reserves, extraction sources, purification processes, and emerging technologies such as direct lithium extraction methods This paper also explores the environmental and social impacts of 1 Introduction Discussions regarding lithiumbased technology have dominated the field of energy research in recent years From the first commercialization in 1991, the lithiumion battery has been a core energy technology and it has Technologies of lithium recycling from waste lithium 2024年3月18日 Efficient separation of smallparticlesize mixed electrode materials, which are crushed products obtained from the entire lithium iron phosphate battery, has always been challenging Thus, a new method for recovering lithium iron phosphate battery electrode materials by heat treatment, ball milling, and foam flotation was proposed in this study The difference in Efficient recovery of electrode materials from lithium iron 2019年6月21日 The process known as "carbonate precipitation" is more likely to occur in brine that has low magnesium to lithium ratios (below six), since in this scenario the lithium is precipitated as lithium Integrated Direct Carbonation Process for Lithium Recovery from
.jpg)
(PDF) Priority Lithium recovery from spent Liion batteries via
2023年2月22日 process can effectively recover more than 93% of lithium as lithium hydroxide or carbonate at a purity greater than 995% The effect of aluminium and copper impurities on the lithium recovery 2023年10月20日 The second step of ESLR is based on this Li 2 CO 3 formation Selective recovery of produced Li 2 CO 3 is carried out by water leaching of the black mass fraction Since the other black mass components, except parts of Al and F [22, 27, 28], are not water soluble under the given conditions in significant values, a Li salt with a purity >92% [24, 28] can be Efficient Lithium Recovery from EndofLife Batteries in 2021年9月19日 In this study, a process for preparing batterygrade lithium carbonate with lithiumrich solution obtained from the low lithium leaching solution of fly ash by adsorption method was proposed(PDF) Preparation of BatteryGrade Lithium Carbonate with Lithium 2017年1月12日 A closedloop process to recover lithium carbonate from cathode scrap of lithiumion battery (LIB) is developed Lithium could be selectively leached into solution using formic acid while aluminum remained as the metallic form, and most of the other metals from the cathode scrap could be precipitated out This phenomenon clearly demonstrates that formic Lithium Carbonate Recovery from Cathode Scrap of Spent Lithium
.jpg)
Lithium Processing Solutions Services Veolia Water
Our lithium processing capabilities are reinforced by a global team of scientists and engineers that design solutions for the production of high purity lithium System Designs Veolia has a wide range of evaporation and crystallization system designs specific for lithium processing Filtration and membrane, ion exchange, lithium brine concentration