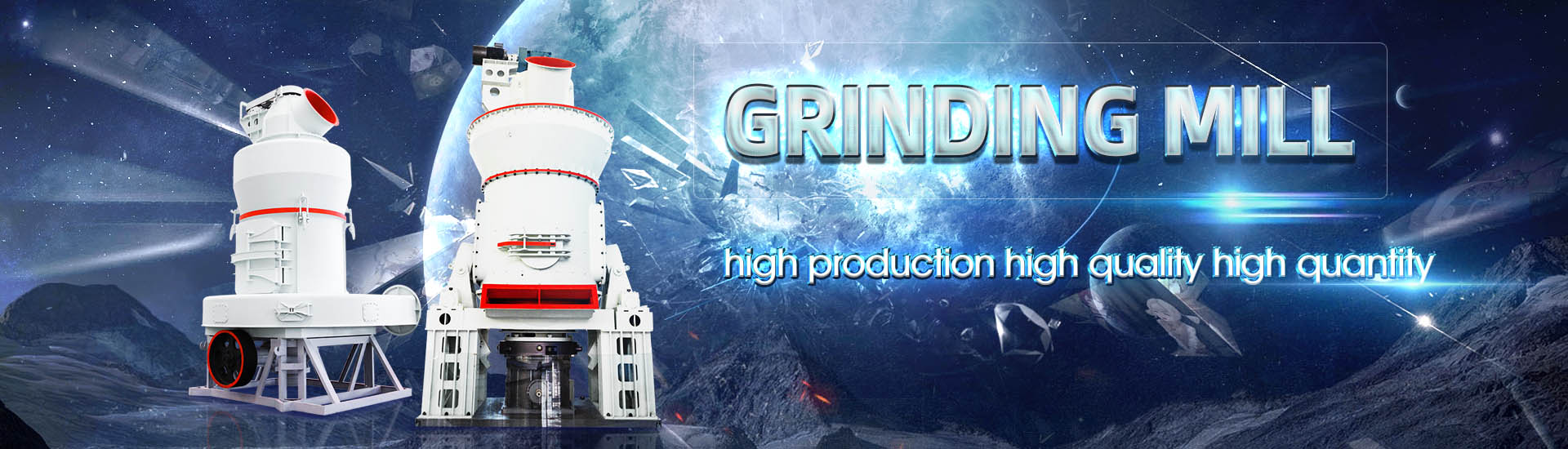
Grinding disc lining installation requirements
.jpg)
How to Install Grinding Discs: Complete Guide FlamingoTools
2024年8月14日 This guide will walk you through the steps of installing grinding wheels, highlight key considerations, and recommend some reliable models and parameters Understanding Grinding Discs Grinding discs, also known as abrasive wheels, are used with angle grinders, 2023年1月31日 Proper steps in mounting a grinding wheel are as follows: Handle and store grinding wheels in a careful manner Handle and store all grinding wheels as if they were made of glass! Select the proper grinding Proper Mounting of a Grinding Wheel Norton AbrasivesUnderstanding how to correctly install a cutting disc on a grinder is essential for safety and efficiency Always check the disc’s orientation, inspect for any damage, and follow proper Which Way Does a Cutting Disc Go on a Grinder?Grinding machines shall be equipped with flanges in accordance with paragraph (c) of this section Work rests On offhand grinding machines, work rests shall be used to support the work They shall be of rigid construction and designed to 1910215 Abrasive wheel machinery Occupational
.jpg)
Safety in the use of abrasive wheels
In addition to looking at essential training needs, the guide also focuses on details such as: wheel characteristics; safety in grinding machine operations; wheel mounting procedures and issues;2019年11月13日 The correct installation is to ensure the grinding wheel normal and lasting good operation of the basic work, if the grinding wheel installation error, not only will affect the normal work5 Steps For Proper Installation Of Grinding WheelBosch grinding and cutting discs comply with international standards and safety requirements such as EN 12413, FEPA and oSa The careful selection and combination of highquality raw Cutting Grinding and Brushing Bosch PTEnsure Proper Installation: Mount the disc correctly and securely on the grinder Improper installation can lead to disc detachment or breakage Check Compatibility with the Grinder: Verify that the disc is suitable for the speed and How To Use A Flap Disc For Grinding Red Label
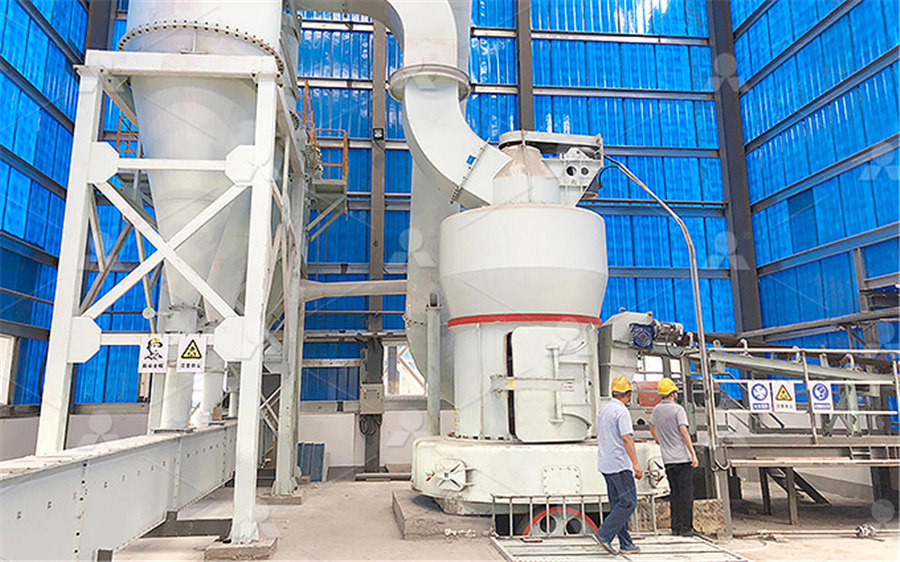
SAFETY RECOMMENDATIONS FOR THE USE OF CUTTING AND
Explanation of marking required by EN 12413 * * EN 12413 marking shows that the producer has followed the essential safety requirements of the European safety standard for reinforced Grinding is divided into three basic applications: • Precision grinding (die grinders) • Rough grinding and cutting off • Surface grinding (sanders and polishers) With this division, Pocket Guide to Grinding Technique Atlas Copco2022年8月2日 Care shall be taken during installation to avoid damage occurring to the CC Should the CC be damaged during installation and before hydration, the layer should be removed and replaced 60 Perimeter Edge Fixing It is essential that all exposed (ie unjointed) edges of the CC should be secured during the installation to preventINSTALLATION GUIDE: CHANNEL LINING Titan Environmental : Grinding disc AGD SP 180mm diameter 64mm thickness: 1 Request a demo, click here Request a quote, click here Contact me form, click here Metal grinding disc Hilti
.jpg)
Grinding Mills and Their Types – IspatGuru
2015年4月9日 The mill is normally used for grinding of ores Lining of the cylinder plays very important role It protects the mill from abrasions and at the same time it helps in lifting of the material from the bottom of cylinder The 2024年8月14日 Place the new disc onto the spindle, making sure it aligns with the center hole Hand tighten the flange nut and then use the wrench to secure it Be careful not to overtighten to avoid damage to the grinder disc or spindle Test the Installation: Rotate the disc by hand to ensure it moves freely without wobblingHow to Install Grinding Discs: Complete Guide – FlamingoToolsLearn more about double disc grinding on Requirements Key Requirements for Double Disc Operations Key aspects must be considered to ensure the smooth operation and precise output of double disc grinding processes Disc Material The choice of disc material is crucial for achieving desired results in double disc operationsDouble Disc – RequirementsIn this article you will find basic orifice plate installation guidelines, including: orifice plate tap orientation; orifice plate tapping locations; orifice tapping; etc This post is mainly a set of rules for the orifice plate installation like an orifice flow meter installation guidelinesHow to install an Orifice Plate? Installation Guidelines
.jpg)
Essential PPE for Sanding and Grinding Safety Binic Abrasive
Given these risks, appropriate PPE is not just a regulatory requirement but a fundamental aspect of workplace safety Essential PPE for Sanding and Grinding 1 Respiratory Protection Dust Masks and Respirators When using a sanding disc or 2022年9月30日 Classification of lining plates The shape of the ball mill lining plate can be divided into 9 shapes according to different requirements, namely wedge shape, wave shape, planoconvex shape, flat Function, classification and installation requirements of lining 2024年6月14日 I look for signs of uneven wear, cracks, or damage on the lining surfaces Additionally, I examine the lining surfaces for any signs of contamination or glazing, which can indicate exposure to oils, greases, or brake fluid Lining Thickness Measurement Using a brake lining gauge or a caliper, I measure the remaining thickness of the liningsWhat is Brake Lining? A Comprehensive Guide to Brake LiningsView our complete flat grinding services, including double disc grinding We handle all plate needs with expertise, efficiency, precision Call 180037GRIND • WeCanDoIt@ArrowGrinding We Can Handle Just About Any Plate Requirements A complete flat grinding department; lapping, surface grinding, blanchard grinding, double discExpert Double Disc Grinding – For Any Plate Requirement
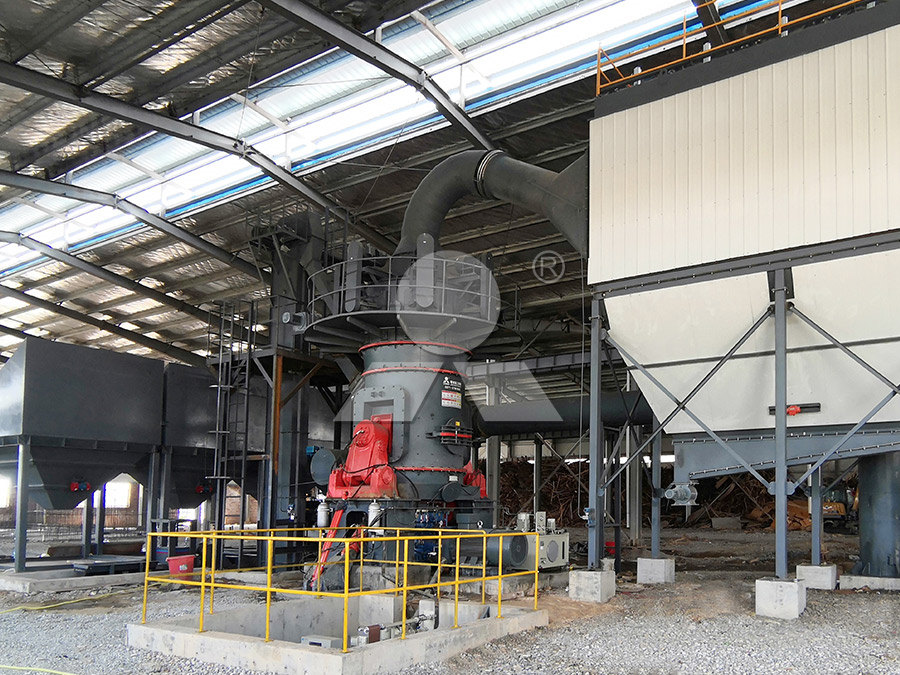
Selecting the right Cutting and Grinding Disc for your
When it comes to your operation, choosing the right abrasive wheel for your grinder will make your job easier! Choosing the right abrasive wheel will help to have well prepared joints, welds that are not cross contaminated and lasting Flexovit® Metal Grinding Disc offers general purpose cutting and grinding with aluminium oxide grain Buy now Bowens The Builders Choice Internal Lining Tools General Hardware Paints Stains Home Garden Roofing Safety Flexovit® Metal Grinding Disc BowensInstalling and removing a disc on an angle grinder can be a tricky task, but with the right tips and tricks, it can be made much easier Here are some tips to help you with disc installation and removal: 1 Use a Hilti KwikLock flange: Switching out the stock flange with a Hilti KwikLock flange can make disc installation and removal a breezeHow To Put A Disc On An Angle Grinder TheHandyBeeInspection and Planning: Before installation, we conduct a thorough inspection of the mill and assess its condition We develop a detailed plan tailored to your specific mill type, liner design, and operational requirements Removal of Old Liners: We safely remove the worn or damaged liners, ensuring minimal disruption to your operations Preparation of Mill Surface: The mill Mill Liner Installation service in Australia Grinding Mill Liners
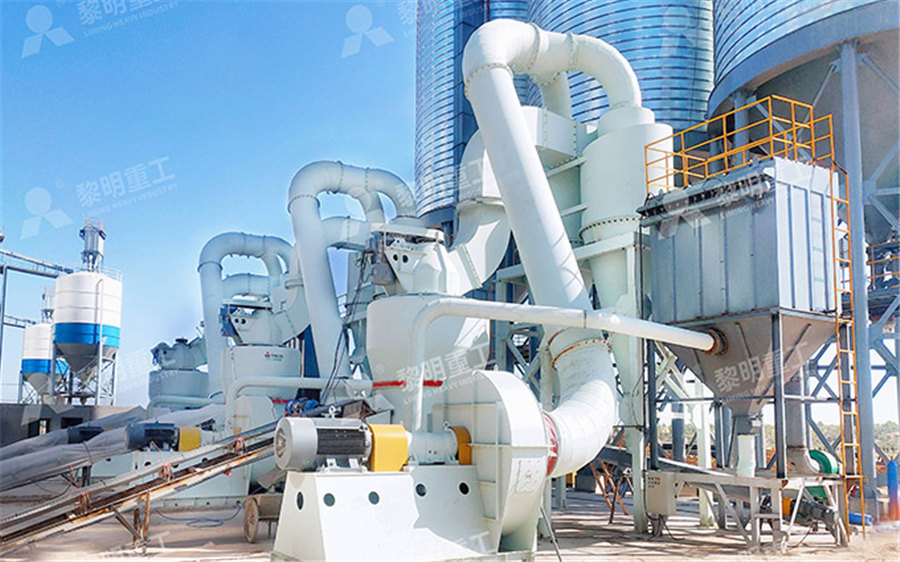
Brake Lining: Ensuring Vehicle Safety and Performance
2024年7月23日 It’s important to note that the choice of brake lining material depends on factors such as the vehicle type, intended use, braking system design, and regulatory requirements Manufacturers carefully select the appropriate material to ensure optimal braking performance, safety, and compliance with applicable standardsrequirements to resist erosion and wind uplift Consult the construction drawings INSTALLATION GUIDE: BUND LINING 3050mm 100mm 50mm CC approved adhesive sealant Typical CC screwed/screwed and sealed overlap joint Screw inserted through CC Ltd approved adhesive sealant bead 3050mm 100mm 100200mm* CC approved adhesive sealant Direction of INSTALLATION GUIDE: BUND LINING Titan Environmental Safety while grinding work: Most injuries reported during grinding work are cuts to fingers and eye injuries from flying objects such as metal parts or sparksGrinding is the process of finishing the workpiece to remove sharp edges or maintain surface quality or maintain shape and dimensionsGrinding Safety Dos and Don’ts EHS HSE and Fire protection Rotor Clip’s doubledisc grinding process makes hardtocreate tolerances possible Rotor Clip strives to give its customers a perfectly fitting part But because not every tolerance requirement can be met through standard processes, we can also customgrind parts to precise tolerances using modern, efficient doubledisc grinding equipmentDoubleDisc Grinding Rotor Clip
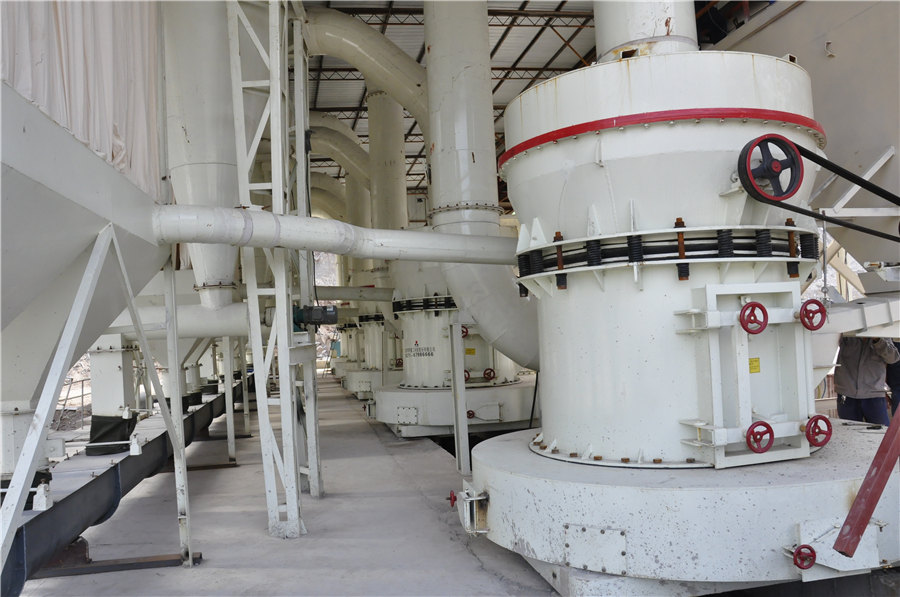
Grinding Disc Kasweld
UserFriendly Design: Kasweld Grinding Discs feature a userfriendly design allowing easy installation and hasslefree operation With their ergonomic shape and lightweight construction, Grinding Disc 7: InStock: Add to Quote: 10: Grinding Disc 7: InStock: Add to Quote: Related Products Wire Brush with 4 Row Twist Wire Bevel Brush 5 INSTALLATION OF TIMBER LININGS 17 51 Lining installation horizontal direct fixing to interior framed wall 17 52 Lining installation vertical direct fixing to interior framed wall 18 53 Lining installation diagonal direct fixing to interior framed wall 18 54 Face fixing of lining 19 55 Secret fixing of lining 19Product installation guide PentarchCare shall be taken during installation to avoid damage occurring to the CC Should the CC be damaged during installation and before hydration, the layer should be removed and replaced 60 Perimeter Edge Fixing It is essential that all exposed (ie unjointed) edges of the CC should be secured during the installation to preventINSTALLATION GUIDE: CHANNEL LINING GeofabricsBall Mill Liners By Qiming Casting® Ball mill liners are essential wear parts that need to be replaced periodically They are made using durable materials like manganese steel, CrMo alloy steel, and Nihard steelBall mill liner Wear Parts For Industry Qiming Casting
.jpg)
NEWSFIRSTA,CERAMIC WEAR LINING,CERAMIC GRINDING BALL
Rubber wear liner: 300*300*63, 500*500*64mm, etc3Steel pipe with ceramic lining4PU lining, polyurethane lining5Ceramic grinding ball: 1)Alumina grinding ball Rolled type: 0530 mm Pressed type:3070 mm 2)ZTA grinding ball: 513 mm 3)Zirconium silicate grinding ball:0513 mm 4)Cerium zirconium grinding ball:0434 mm 5)Yttrium zirconium grinding ball:01 Australian Mining Product and Services offer premium quality grinding mill liners, liner installation, grates pulp discharge system Call +61 497 744 770Grinding Mill Liners liner installation Australian Mining ServicesThe replaceable disc lining is supported by a disc block which is divided into several segments and tops the wedged edge of the outer edge of the disc block The inner ring lining plate is fixed with a pressure plate The vertical grinding roller is hydraulically pressurized, with a Solid Edge’s Application in Vertical Mill Design SpringerCylindrical grinding, Centreless grinding, Internal grinding, Surface grinding , Tool and Cutter grinding, Thread grinding, Crankshaft and Camshaft grinding A Grinding Wheel is basically a precision tool composed of abrasive grains held together by a bonding material or ' bond' The abrasive grains provide the wheel with its cutting points , whichGrinding Wheels Master Abrasives
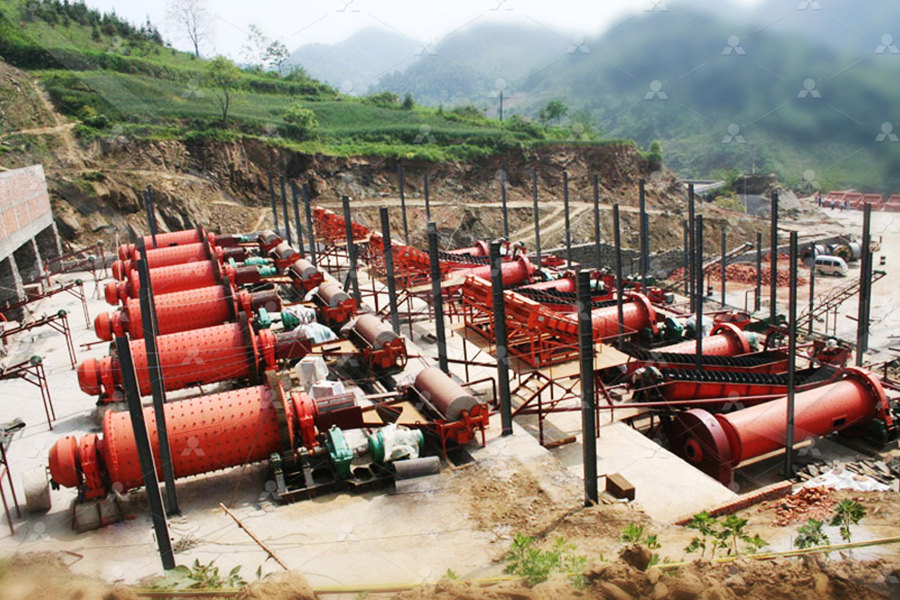
IsaMill Technology Used in Effecient Grinding Circuits
The mill is filled with a suitable grinding media and the area between each disc is essentially an individual grinding chamber As a result the mill is effectively 8 grinding chambers in series The media is set in motion by the action of the grinding discs which radially accelerate the media towards the shellA guide to grinding mill installation: Ensuring efficient and troublefree operation Grinding mills are critical components in many industrial processes, responsible for reducing the size of materials and achieving desired particle sizes The successful installation of a grinding mill is essential for ensuring efficient and troublefree A guide to grinding mill installation: Ensuring efficient and Care shall be taken during installation to avoid damage occurring to the CC Should the CC be damaged during installation and before hydration, the layer should be removed and replaced 60 Perimeter Edge Fixing It is essential that all exposed (ie unjointed) edges of the CC should be secured during the installation to prevent water ingressINSTALLATION GUIDE: CULVERT LINING Geofabrics116 Surface grinding machine – face grinding, rotary table (vertical spindle; table has a vertical axis of rotation) 3 117 Surface grinding – face grinding, Double disc surface grinding machine (includesSafety Requirements for Grinding Machines ANSI Webstore
.jpg)
Rubber Lining for Ore Grinding Mills and Mining
The lining not only protects the mill from premature failure, but also directly participates in the grinding process, providing effective mixing Traditionally, mining equipment uses metal lining However, the transition to rubber Typical installation requirements include: the machine spindle should be free of burrs or damage (Figure 2) ensure grinding is carried out in an area away from other workers and the working area around the grinding operations are kept Safe use of abrasive wheels fact sheet SafeWork 2023年10月31日 Grinding wheels with damaged (or cracked) appearance cannot be used In addition, both ends of the grinding wheel are required to be flat without obvious skew 3 Check and identify internal cracks in the grinding wheel components Hold the grinding wheel in your hand, tap the grinding wheel lightly with a wooden hammer, and listen for the soundSteps to inspect and identify grinding discs before installationCare shall be taken during installation to avoid damage occurring to the CC Should the CC be damaged during installation and before hydration, the layer should be removed and replaced 60 Perimeter Edge Fixing It is essential that all exposed (ie unjointed) edges of the CC should be secured during the installation to preventINSTALLATION GUIDE: CHANNEL LINING Geofabrics
.jpg)
MINIMUM REQUIREMENTS for MOTOR Vehicle Brake LININGS
Minimum Requirements To meet minimum requirements a brake lining shall have: 51 A normal friction coefficient over 25 based on the average of five tests 52 A hot friction coefficient over 15 based on the average of five tests 53 A coefficient of friction of 15 or over on each of the five tests at the following points: 531 Between 200F and 550F, inclusive, on the second fade run The Installation Instructions apply to the following accessories: Order number Original accessory DK5GD***** 1 × ground disk 2 Authorized installation personnel Authorization to carry out installation depends on the measuring device's approval type The table below shows the authorized group of people in each caseInstalling ground disks Endress+HauserHowever, if you don’t have the right equipment, this new material could create challenges in brake disc manufacturing Our expert engineers have developed new working parameters and wheel specifications using our current grinder product range that will meet the grinding requirements of the new dustfree composite coating materialBrake Discs Precision grinding machines for brake discs Fives 116 Surface grinding machine – face grinding, rotary table (vertical spindle; table has a vertical axis of rotation) 3 117 Surface grinding – face grinding, Double disc surface grinding machine (includesSafety Requirements for Grinding Machines ANSI Webstore
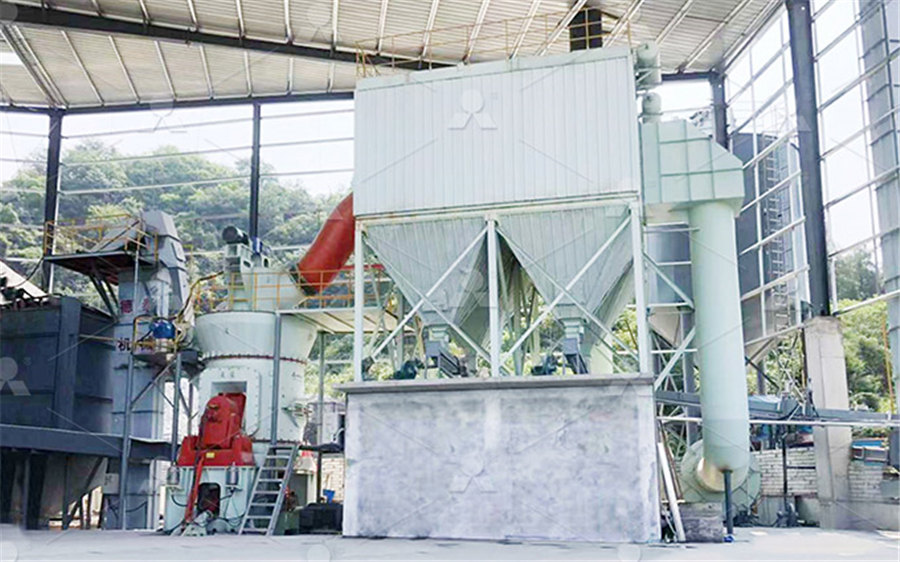
What Are Grinding Discs and What Are They Used For?
2023年6月2日 What Are Grinding Discs Used For? Grinding Discs can be used across multiple applications and with various machines but can typically be found being used in sanding machines for the purpose of refining and sanding flooring There is an abundance of different sanding machines available on the market today, all designed to perform different jobs, but the Concrete Canvas aim to support contractors throughout the installation process and offer comprehensive technical guidance in a variety of forms Lining Installation; Concrete Canvas (CC) Channel Lining Maintenance; Concrete Canvas (CC) Slope Protection Installation; The 4 Principles of Concrete Canvas Installation;Installation Guidance Concrete Canvas®