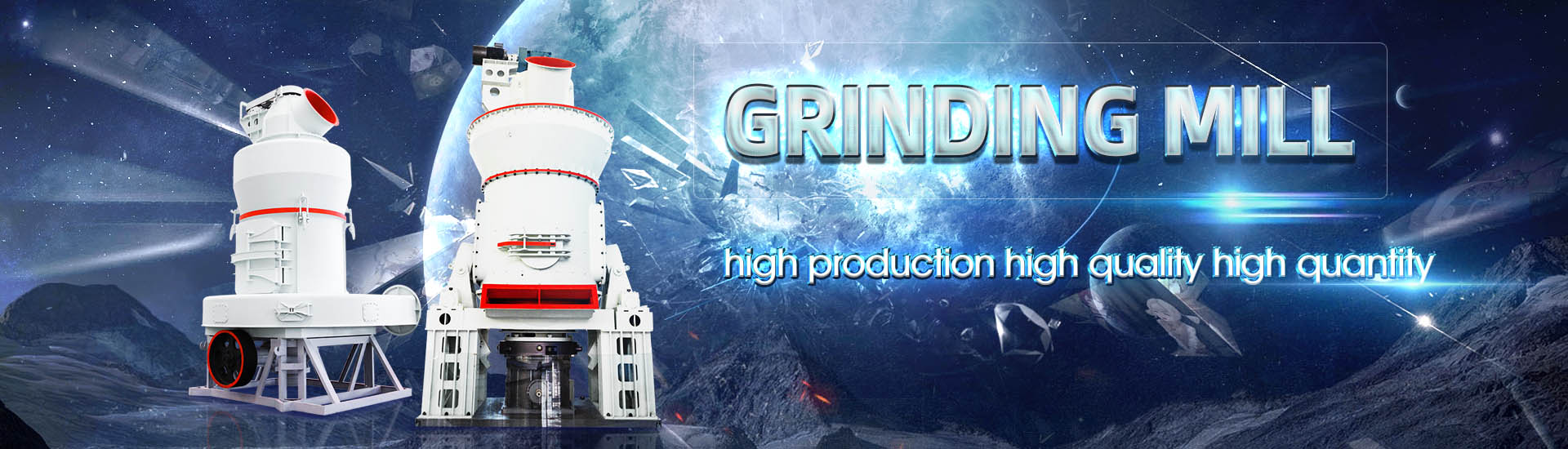
Raw material vertical mill design drawing
.jpg)
Vertical roller mill for raw Application p rocess materials
Vertical roller mills are adopted in 20 cement plants (44 mills) in Japan In the vertical roller mill which is widely used in the raw material grinding process, raw materials input grinding table common solution to grind raw materials and cement Roller presses are used mainly in combination with a ball mill for cement grinding applications and as finished product grinding BALL MILLS Ball mill optimisation Holzinger ConsultingRecent decades have proven the great effectiveness of a vertical roller mill for grinding raw materials Its effectiveness, combined with the implementation of drying, grinding andDesign parameters of vertical roller mill Download Tablevertical mill design involves different product specifications, due to technical limitations, it is impossible to form a standardized design Obviously, 2D design cannot meet the requirements Solid Edge’s Application in Vertical Mill Design Springer
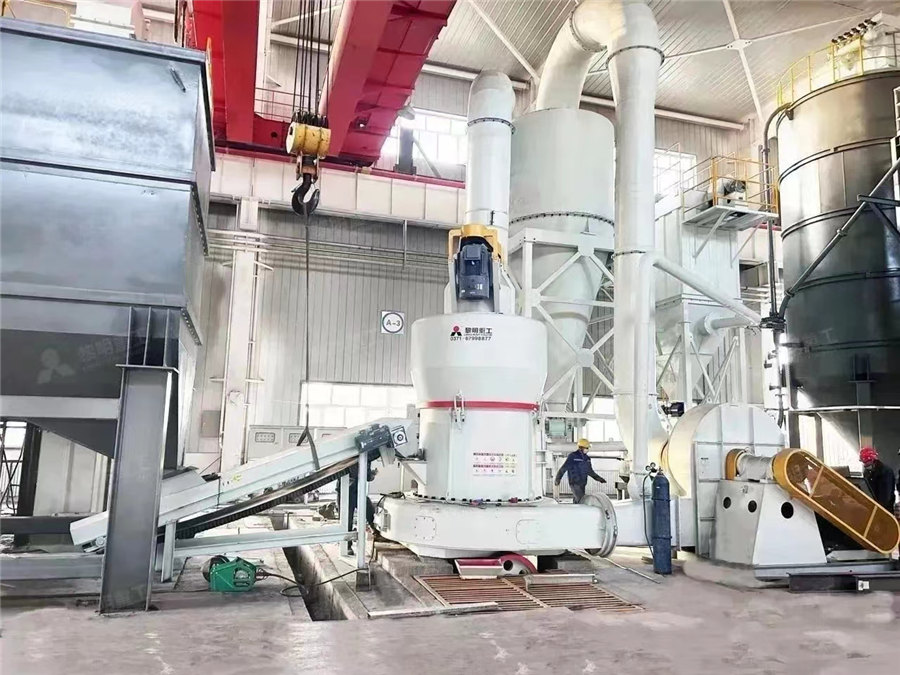
(PDF) Performance Evaluation of Vertical Roller Mill in
2017年9月11日 In this study, an extensive sampling study was carried out at vertical roller mill of ESCH Cement Plant in Luxemburg Samples were collected from mill inside and around the circuit toUBE Machinery Corporation Ltd, Japan to manufacture supply stateoftheart UBE Vertical Roller Mills for grinding applications related to Raw material, Coal, Clinker and Slag The mill VERTICAL ROLLER MILLS AMCLThe quadropol® vertical roller mill by thyssenkrupp Industrial Solutions takes a holistic approach to modern grinding systems in terms of its simple and compatible design Describing the key VERTICAL ROLLER MILLS A holistic VRM approachVertical Roller Mills (VRM) have a clearly higher energy eficiency than ball mills, even if the ball mill is combined with a roller press This and further arguments led to the increased share of SikaGrind® for vertical roller mills
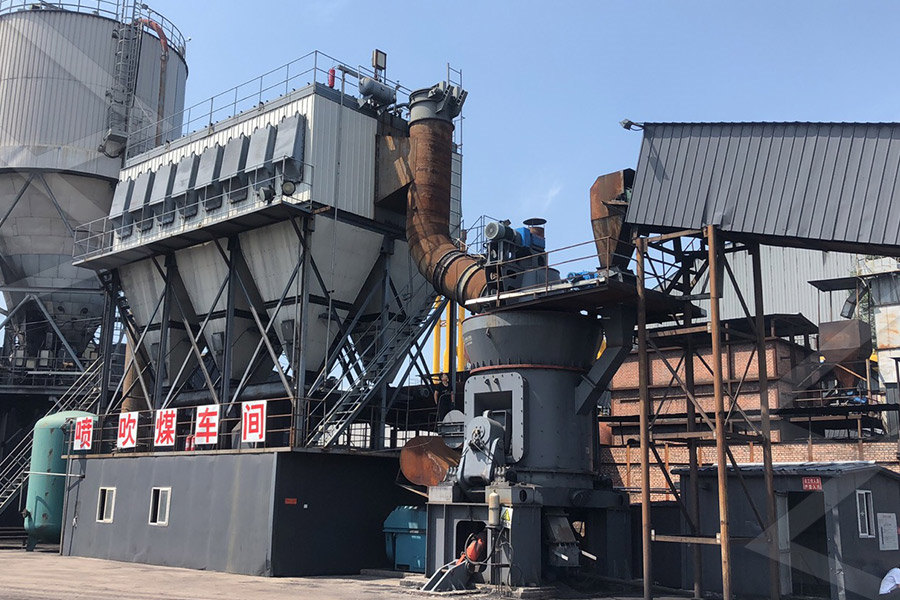
Modeling and simulation of vertical roller mill using population
The matrix model was used to simulated vertical roller mills in cement clinker and coal grinding lines The pressure breakage function, B, was determined from the laboratory test data with a 2019年1月17日 Through the analysis of the main structure of the vertical mill, we use the assembly function of the solid edge threedimensional solid software to implement the Solid Edge’s Application in Vertical Mill Designavailable for raw grinding, ensure the ability to meet all possible capacity requirements in a single mill even for the hardest materials The wellknown reputation of the OK mill as a reliable machine that is easy to operate and maintain continues with the OK raw mill In addition to the roller design features, the OK mill retains the abilityOK RAW AND CEMENT MILL2017年9月11日 Due to the compact design and material transportation system of vertical roller mills (VRM), some important streams (total mill feed and discharge, dynamic separator feed and reject) remain in the (PDF) Performance Evaluation of Vertical Roller Mill
.jpg)
Vertical Cement Mill
With the incensement of moisture of the raw material, the powder consumption will decrease obviously The vertical mill saves 30%40% of energy consumption compared to the ball mill Vertical mill has less noise than ball mill, about 20 Vertical Roller SINOMALY produces cement raw material grinding mills in various specifications These machines are suitable for grinding mill production lines with an output of 2500t/d, 3200t/d, 4000t/d, 5000t/d, 6000t/d and 8000t/d The vertical grinding mill is utilized for the grinding of raw materials, mixed cement, and slag powderVertical Roller Mill for Cement Raw Material SINOMALYFIGURE 4 Particle size distributions of collected samples (Survey 2) Bond work indices and breakage characteristics under compression were determinedPerformance Evaluation of Vertical Roller Mill in Cement With these developments of design and operation, vertical roller mills now have been operated with raw materials containing more than 20% moisture Brundick, H, “Drying and grinding of extremely moist cement raw materials in the Loesche mill,” ZKG International, No2, 1998, pages 6471Brundick, Horst, and Schäfer, HeinzUllrich, Everything you need to know about cement Materials Preparation and Raw
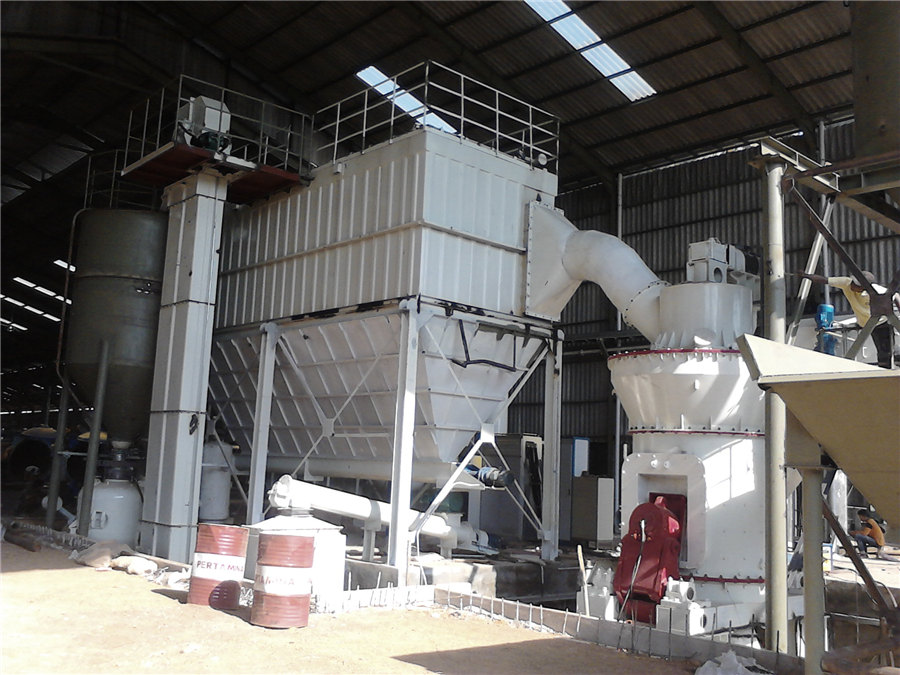
Optimization of Vertical Raw Mill Operation PDF
OptimizationofVerticalRawMillOperationpdf Free download as PDF File (pdf), Text File (txt) or view presentation slides online The document discusses optimization and operation of vertical roller mills (VRMs) Key points include: 1) Continuously monitor and adjust process parameters to find the optimum operating conditions of highest capacity and lowest power consumptionvertical planetary gear reducer At the same time, raw material is dried by hot gas induced through the louver ring installed at outer side of the table Construction This Machine is a vertical type roller mill which performs drying grinding classification and pneumatic transportation simultaneously Material is fed at aVERTICAL ROLLER MILLS AMCLThe cement mill can be used as a raw mill or cement grinding mill, AGICO Cement provides vertical cement mill, For spare parts: size and dimensions, material and weight, and your drawings with details, you can send the drawing to t Mill Cement Ball Mill Vertical Cement Mill Factory Price2019年8月4日 Vertical ball mill; it also called with basket mill this ty pe has more efficiency than the horizontal type, also it only uses ceramic balls which give his its efficiency , figure (36) show the Paints Industry: Raw materials unit operations Equipment
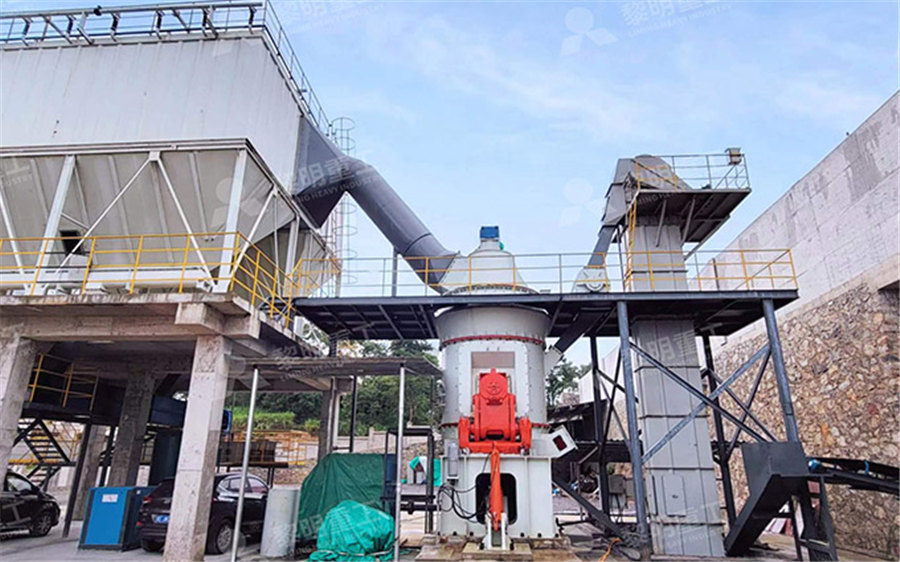
Raw Material DryingGrinding Cement Plant Optimization
Dry Grinding: Open circuit Ball mill, closed circuit Ball mill, vertical roller mill, Roll Press or Roll press in circuit with ball mill However, it would be seen that the most significant process and types used for raw material grinding operations in modern cement industry are: Process: Dry Closed circuit drygrinding Type of mill: Ball and The cement raw materials (lime, silica and iron ore) enter the circuit through two apron feeders The raw materials are crushed in a hammer crusher to D 95 of 80mm The raw materials are mixed in a certain proportion and fed into a vertical roller mill (LOESCHE mill) The vertical roller mill grinds the marital to D 85 of 90µmModeling and simulation of vertical roller mill using population in combination with a ball mill for cement grinding applications and as finished product grinding units, as well as raw ingredient grinding equipment in mineral applications This paper will focus on the ball mill grinding process, its tools and optimisation possibilities (see Figure 1) The ball mill comminution process has a high electricalBALL MILLS Ball mill optimisation Holzinger Consulting2016年9月1日 Vertical roller mill (VRM) is a largescale grinding equipment, which is used to grind raw materials from block/granule into powder Due to harsh production environment and inconsistent raw Operational parameters affecting the vertical roller mill
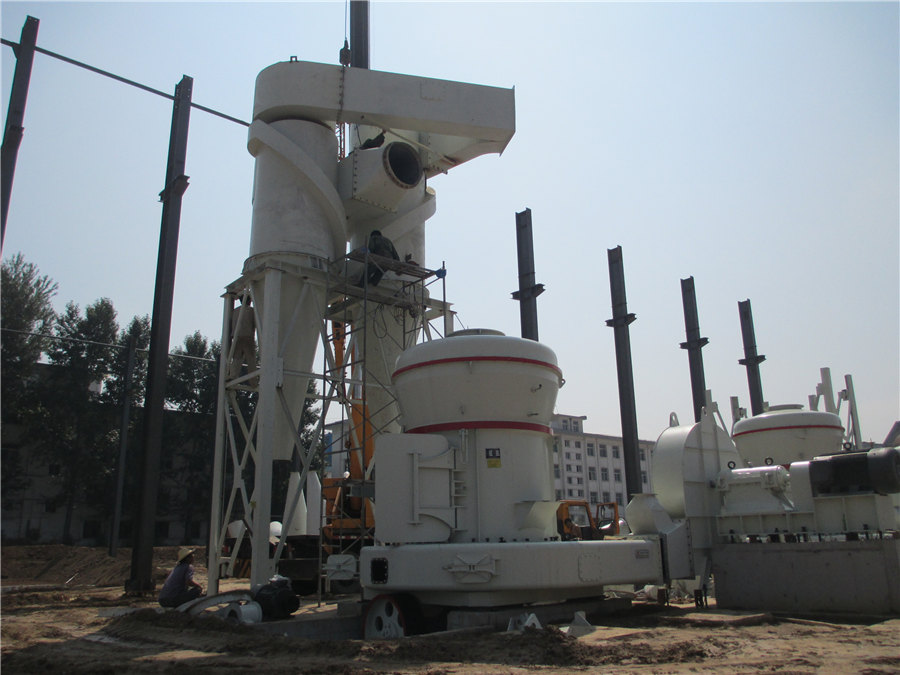
Coal mill, gypsum mill, clay mill, etc Pfeiffer MPS mills
MPS vertical mill from Pfeiffer is the ideal allrounder Grinding of coal, petcoke, clay, limestone, Design measures preventing pulverized coal deposits: 6: Rollers can be lifted off: 7: MPS 5000 B mill for raw material grinding, Turkey Tracim, Turkey MPS 5300 B 2021年1月1日 For the past three decades the vertical roller mill has emerged to be the preferred choice for grinding raw materials With the grinding capacity of a vertical roller mill and the ability to dry, grind and sort in a single unit, the vertical roller mill offers a definite advantage over the ball mill system [10]Review on vertical roller mill in cement industry its 2018年9月10日 The simulator was used for the thermodynamic performance of a raw mill (RM) and raw materials preparation unit in a cement plant in Nigeria using actual operating data The raw mill has a capacity (PDF) Thermodynamic Analysis of Raw Mill in Cement2 Raw materials management system – 22 Concrete problems 16 1 Raw materials – 2 Raw mix – 3 Reserves – 4 Crushing – 5 Drying – 6 Preblending – 7 Storage and handling 3 Raw milling and blending 3 Computerised Maintenance Management Systems 30 1 Raw milling – 2 Blending – 3 Kiln feed 4 Flames and fuels 38 1The Cement Plant Operations Handbook International Cement
.jpg)
Analysis of vertical roller mill performance with changes in material
2022年5月31日 Mineral crushing is the main source of energy consumption in mineral processing According to statistics, this consumption accounts for about 35–50% of the total cost of the mine (Curry et al, 2014), or even higherIt may also account for 18% of the global electrical energy consumption (NapierMunn, 2015)More efficient crushing equipment needs to be 2022年10月3日 Raw materials grinding process is a first step of cement production which is has an important role in the first grinding step Vertical Raw Mill is a main equipment that is used in grinding or (PDF) ANALISA KINERJA ALAT VERTICAL RAW MILL PABRIK II PT UBE Vertical mill will meet these needs UBE Vertical Mill Video Strong Points Energy Saving (Less than 30% compared to Ball Mill) Possible to carry out simultaneously with grinding, drying and classifying; Raw materials are UBE Vertical Mill UBE Machinery Corporation, Ltd2021年1月22日 In the whole process of cement production, the electricity consumption of a raw material mill accounts for about 24% of the total Based on the statistics of the electricity consumption of the raw A Survey and Analysis on Electricity Consumption of Raw Material Mill
.jpg)
Bridgeport Vertical Mill Manual DocsLib
Abstract axis of shaft and the vertical axis of end mill cutter are In manufacturing industry there are different types of perpendicular to each other; also the vertical axis of shaft and machining processes are required to convert raw material in to vertical axis of tool are coinciding with each other final productVertical raw mills are widely used in the cement industry due to their high efficiency, low energy consumption, and compact design The Role of Vertical Raw Mills in Cement Production: 1 Grinding Limestone: The primary function of a vertical raw mill is to grind limestone, the main raw material in cement production, into a fine powderThe vertical raw mill: A key component in cement productionFor the preparation of cement raw material, cement, and granulated blastfurnace slag with small to medium output rates, the MVR mill with conventional drive is the right choice This mill type is by the way the core piece of our modular ready2grind systemMVR vertical roller mill with planetary gearbox Gebr PfeifferThe vertical roller mill (VRM) is a type of grinding machine for raw material processing and cement grinding in the cement manufacturing processIn recent years, the VRM cement mill has been equipped in more and more cement plants around the world because of its features like high energy efficiency, low pollutant generation, small floor area, etc The VRM cement mill has a Vertical Roller Mill Operation in Cement Plant
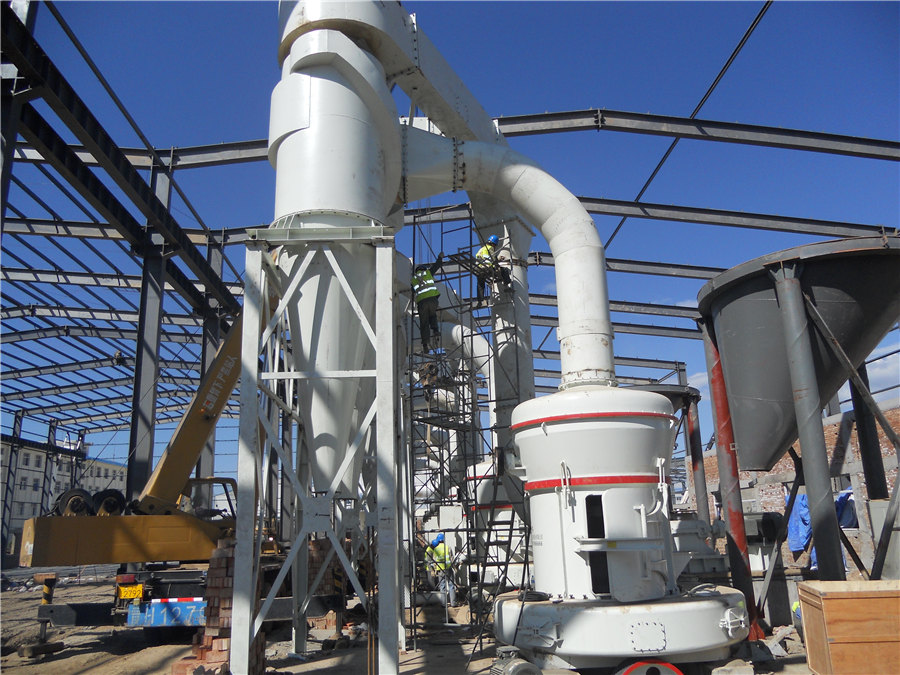
Application of Vertical Roller Mill in Cement Production
Application of Vertical Roller Mill in Cement Industry Vertical roller mill (VRM) technology has become an integral part of the cement industry, offering several advantages over traditional grinding mills Today, this type of grinding machine is becoming more and more popular in both the raw material grinding process and the cement grinding 2019年1月17日 The standardization of mechanical design makes the application of threedimensional design easy to promote, and at the same time greatly improves the design efficiency Because vertical mill design involves different specifications, it is difficult to form a standardized design, which makes the difficulty and workload of 2D design greatly improvedSolid Edge’s Application in Vertical Mill DesignNo matter what type of material has to be ground – cement raw material, cement clinker or granulated blastfurnace slag – and how different their grindability and abrasiveness may be, the MVR mill ensures throughput rates of a different dimension, around the clock, reliably and on the long term Forget about downtimeCement mills and raw mills for high throughput rates Gebr Pfeiffer2012年12月31日 PDF a Distributed Control System(DCS) of cement raw materials is presented for the vertical roller mill by the application of ABB's IndustrialIT The Find, read and cite all the research Design and Realization Of Roller Mill Control
.jpg)
Design and Realization Of Roller Mill Control System
438 QianHong Wang et al / Physics Procedia 33 ( 2012 ) 437 – 443 Among the rest, stable operation of the vertical mill vertical means that to ensure the material layer thickness of the disc 2023年7月4日 3 Raw material grinding: The crushed raw materials are ground into a fine powder, called raw meal, using grinding equipment like ball mills or vertical roller mills 4 Pyroprocessing: The raw meal is heated in a rotary kiln Vertical Roller Mill in Cement Manufacturing PlantThe grinding table is the key part of vertical mill, mainly composed of table body, lining plate, press block, retaining ring, scraper plate, air ring, and wind deflector, etc Weight Material Application Customizable 1132T Carbon steel, silicon manganese steel Vertical roller mill Yes, based on user's drawings GREATWALL STEEL CASTING W Chat Now 133 Leave Message Grinding Table For Vertical Roller Mill DirectIndustryWe can design and manufacture vertical roller mills of diversified specifications and models for raw meal, cement, and slag comminuation systems in cement clinker production lines with capacity up to 10,000t/d To continuously meet the needs of grinding various materialsVertical Roller Mill (VRM)SinomaLiyang Heavy Machinery Co, Ltd
.jpg)
PFEIFFER MILLS FOR THE CEMENT INDUSTRY
7 // Almost any plant for the grinding of cement raw material is a combination of machines specially adapted to the particular physical properties of the material to be ground As a result, our plants work efficiently without any trouble » Highly efficient grinding, drying, and separating in one unit » Outstanding production capacities exceeding 1,400 t/h in one single millSecondly, concerning the technology updated project of the TRM534 raw material vertical roller mill owned by YongDeng Qilianshan Cement Ltd Co, the industry application scheme adopted in this project is presented, and the practical application effects are studied in detail, which show that this technology can increase the production of the raw material vertical mill system by 5~10%, Industrial application of system integration updated technology2023年6月2日 SILO DESIGN Silos can be divided into two main categories: Raw material storage silo (before processing) Process silo (bins inside the industrial process) Raw material storage silos The following parameters need to be analysed to determine the correct design of storage silos: Number of filling and emptying cycles; Concrete or corrugated steel Silo design and construction Milling and GrainOver the last three decades the vertical roller mill has become the preferred mill for grinding of raw materials The grinding efficiency of the vertical roller mill combined with an ability to dry, grind and classify within a single unit gives the vertical roller mill a decided advantage over a ball mill system However, despite these benefits,Cement grinding Vertical roller mills versus ball mills
.jpg)
PROCESS OPTIMISATION FOR LOESCHE GRINDING PLANTS
vertical roller grinding mills for grinding: • Coal • Cement raw material • Clinker / granulated slag • Industrial minerals, and • Ores The core elements of these plants are the Loesche vertical a vertical roller mill (VRM) • Surpasses the classic methods if the controlled