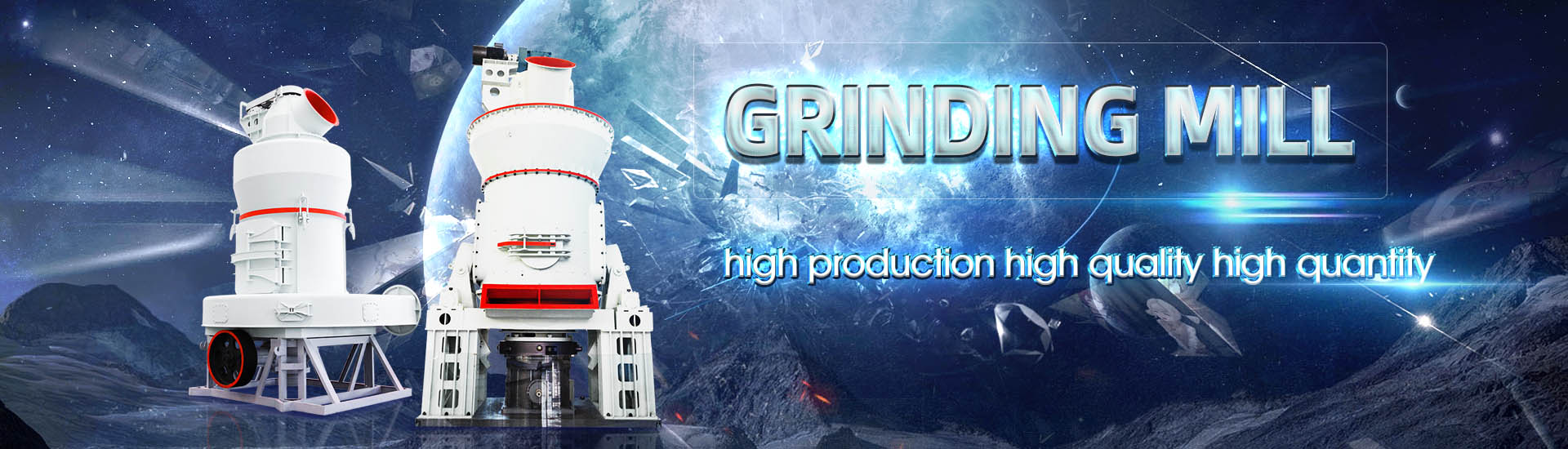
3 2m x 13m ball mill technical parameters
.jpg)
Ball Mill Design/Power Calculation 911Metallurgist
2015年6月19日 The basic parameters used in ball mill design (power calculations), rod mill or any tumbling mill sizing are; material to be ground, 2021年1月1日 According to the specifications and parameters of the ball mill, the general layout, grinding body, lining plate, partition device, support device, transmission part and feeding and Design of Threechamber Ball Mill IOPscience2021年2月19日 The ball mill process parameters discussed in this study are ball to powder weight ratio, ball mill working capacity and ball mill speed As Taguchi array, also known as orthogonal array design, adds a new dimension to conventional experimental design, therefore, Orthogonal array (L9) was carefully chosen for experimental design to understand the effects Comparative Study on Improving the Ball Mill Process Parameters 2015年6月19日 The basic parameters used in ball mill design (power calculations), rod mill or any tumbling mill sizing are; material to be ground, characteristics, Bond Work Index, bulk density, specific density, desired mill Ball Mill Design/Power Calculation 911Metallurgist
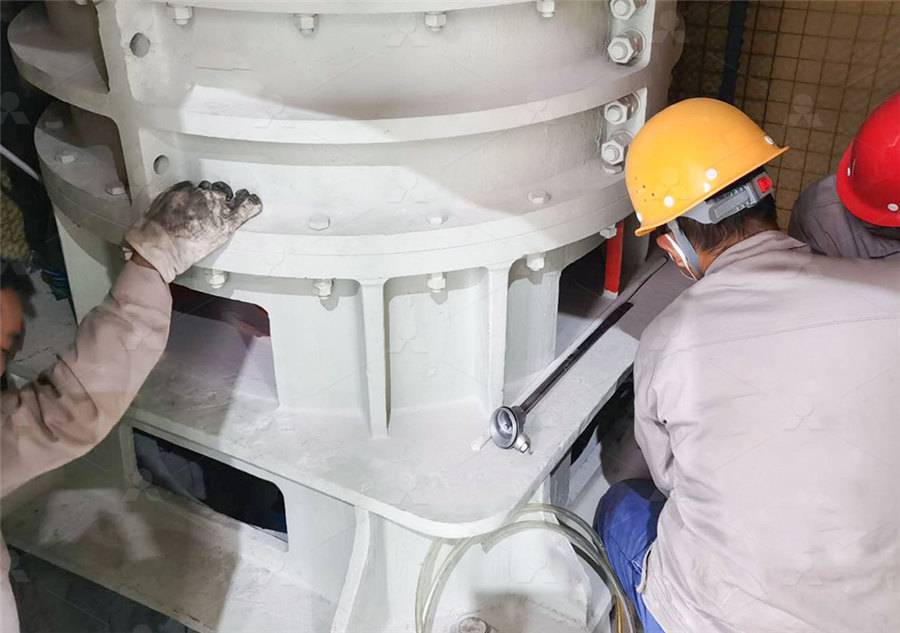
Optimization of the ball mill processing parameters
2016年1月1日 The aim of this study was to determine the effect of main milling variables, ie agitator shaft speed (50%, 75%, and 100%, which is 25 rpm, 375 rpm, and 50 rpm) and milling time (30, 45, and 60 2021年1月1日 Comchambered with the design of Φ 35 × 13m threechamber ball mill, the design process of ball mill is described in detail General arrangement of the mill Filling rate of grinding body in each (PDF) Design of Threechamber Ball Mill ResearchGate2011年1月31日 An experimental study on the fine grinding of calcite powder (d50=6216μm) using a 075l laboratory stirred ball mill has been carried out The effects of various operating factors, such as A study on the effect of process parameters in stirred ball mill2014年3月1日 The object of the study reported here is the grinding process in a tumbling mill where the mechanism of destruction by crushing is implemented, which is caused by the mechanism of compression loading(PDF) Analysis of ball mill grinding operation using mill power
.jpg)
Effect of Milling Parameters on DEM Modeling of a Planetary Ball Mill
PDF On Jan 1, 2023, Mohsen Mhadhbi published Effect of Milling Parameters on DEM Modeling of a Planetary Ball Mill Find, read and cite all the research you need on ResearchGateBall filling ratio tests Parameters Variable Mill Speed (% of Nc) 70 Ball filling ratio (J) 020, 030, 035, 040, 045 Ball size distribution of 40, 32, 20, 12 mm (%) 30302020 (3rd group) Powder filling ratio (fc), (U) 0125, 100 Grinding aid dosage (g/Mg) 0 Grinding time (min) 10 Ball size distribution tests Parameters Variable Mill Influences of operating parameters on dry ball mill performance2023年10月27日 The ball mill is a rotating cylindrical vessel with grinding media inside, which is responsible for breaking the ore particles Grinding media play an important role in the comminution of mineral ores in these mills This work reviews the application of balls in mineral processing as a function of the materials used to manufacture them and the mass loss, as A Review of the Grinding Media in Ball Mills for Mineral 2016年5月30日 Shafts with rubber wrapping connected to metal block with bearing The metal blocks we fabricated have dimension of 72*72*38 mm 3 At first, we got 75*75*40 mm 3 mild steel blocks from store and DESIGN AND FABRICATION OF MINI BALL MILL (PART 3) (edited)
.jpg)
(PDF) Effect of ball size distribution on milling
2009年9月23日 E1 Determination of milling parameters in each ball size interval 100 E2 Predicted EQMand OEMBSD’s selection functions 100 Diameter of the ball leaving the mill after being worn downparameters of both distributions are equal in Eqs 7 and 9: m c (10) In the second part of the paper, we will investigate the hypothesis defined by Eqs 8, 9 and 10 3 Experimental Investigations were carried out in a laboratory ball mill having the size of DxL = 160x200 mm with a ribbed inside surface of the drum The mill ball loading was 40%THE OPTIMAL BALL DIAMETER IN A MILL 911 Metallurgist2020年10月9日 In order to obtain the optimal operation parameters of a SAG mill, in this paper, the discrete element method (DEM) is used to simulate the breakage process of the particles by controlling three Operation Analysis of a SAG Mill under Different Conditions Based on 2013年12月1日 Percent passing of milled Al 2 O 3 powder as a function of particle size for varying ball diameter Rotation speeds are (a) 50 rpm, 100 rpm, and (c) 153 rpmEffect of ball size and powder loading on the milling efficiency
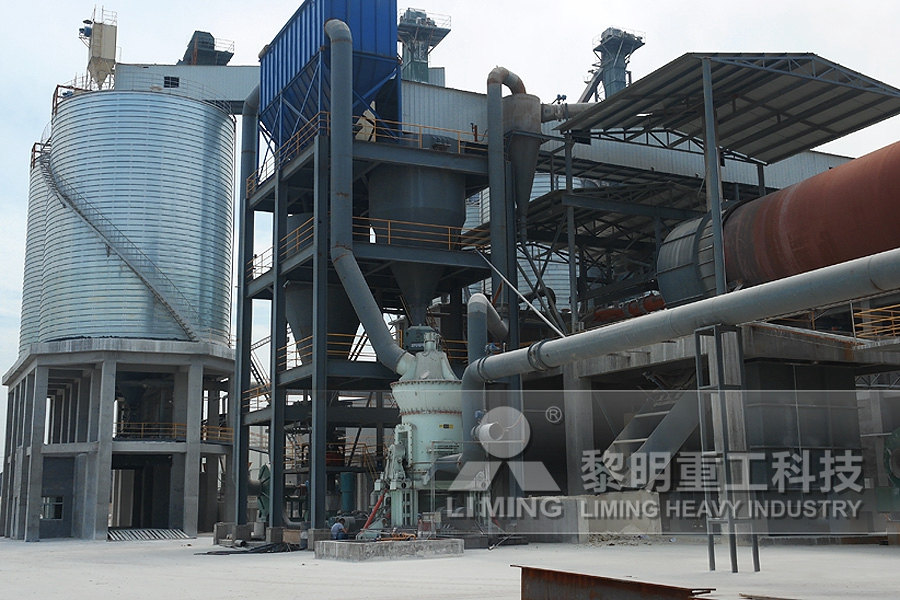
(PDF) Parameters optimization in the planetary ball milling of
2008年7月1日 For example, a lower balltopowder ratio results in less efficient grinding and longer grinding times (BeginColin et al, 2000) Planetary, attritor, and vibration mills are different types of 2010年9月27日 Load of the ball mill affects the productivity, quality and energy consumption of the grinding process But sensors are not available for the direct measurement of the key parameters for mill load (PDF) Modeling of operating parameters for wet ball mill2023年9月9日 In recent years, because of the decreasing liberation sizes of the minerals, processes such as grinding need to be evaluated in more detail As is well known, size reduction processes are very important both in mineral processing and in many industrial applications However, to increase the efficiency of the processes after size reduction, variations in particle The Effects of BallMill Grinding Parameters on Lignite Influences of operating parameters on dry ball mill performance Serkan Cayirli Nigde Omer Halisdemir University, Nigde, Central Campus, 51240, Turkey Corresponding author: (Serkan Cayirli) Abstract: The paper is aimed to investigate the influence of operating parameters on dry fine grindingInfluences of operating parameters on dry ball mill performance
.jpg)
(PDF) Performance optimization of an industrial ball mill for
2017年1月1日 An increase of over 10% in mill throughput was achieved by removing the ball scats from a single stage SAG mill These scats are non spherical ball fragments resulting from uneven wear of balls Ball mill can be provided in MS/SS/Alloy Material with or without rubber lining Jacketed arrangement for heating or cooling applications BALL MILL – CYLINDRICAL MAIN TECHNICAL PARAMETERS: Weight (t) 900×1800 900×3000 1200×3000 1200×4500 1500×3000 1500×5700 1830×3000 1830×6400 1830×7000 2100×3600 2200×4500 2200×6500 2200× Ball Mill Catalogue2017年2月13日 The apparent difference in capacities between grinding mills (listed as being the same size) is due to the fact that there is no uniform method of designating the size of a mill, for example: a 5′ x 5′ Ball Mill has a working Ball Mills 911Metallurgistinside the mill into three steps and then studied each one separately [19] In this work, the effect of the operating parameters of tumbling mill, slurry filling, ball filling, and mill speed on the load orientation was experimentally investigated using a largepilot mill The present workprovidesfurtherExperimental observations of mill operation parameters on
.jpg)
AMIT 135: Lesson 7 Ball Mills Circuits – Mining Mill Operator
Ball Mill Design Parameters Size rated as diameter x length Feed System Ball mill = 35 m x 35 m; Rubber lining = 75 mm % Mill volume charge = 40%; Grinding balls diameter = 70 mm; Mill operational speed = 176; Calculate the optimum power consumption to operate the mill Solution:2011年1月1日 An experimental study on the fine grinding of calcite powder (d 50 = 6216 μm) using a 075 l laboratory stirred ball mill has been carried outThe effects of various operating factors, such as grinding time (min), stirrer speed (rpm), slurry density (wt%) and ball filling ratio on fine grinding was studied under batch wet conditions using alumina balls, 95% purity with A study on the effect of process parameters in stirred ball millaccording to packing list, and if the ball mill, power pack and ball milling tank are damaged in transportation 72 Reading Read the User’s Manual carefully, carry out nonload test running of the ball mill as per the steps described in the Manual, and check if the operation of frequency converter and ball mill is normal 73 Loading TankSFM1 (QM 3SP2) High Speed Shimmy Ball Mill Operational balls were of 999 % purity with a ball diameter of 03 mm and a density of 6030 kg m 3 Calcite powder (CaCO 3, S500, median diameter x 50 = 1082 m, density =2720 kg m 3, specific surface area S w0 = 139 m 2 g 1), was used as a grinding test sample In the grinding experiments, two sets of tests were carried out to determine the effect of theUltrafine grinding of inorganic powders by stirred ball mill: Effect
.jpg)
GP MA Ford
x Not Possible Slotting End Mill Diameter (mm) 8 10 12 16 20 25 25% 50% 100% Max Air MMS vc m/min Increase speeds by 30% for ALtima® coated tools fz mm/tooth High Temp Alloys Nimonics, Inconel, Monel, Hastelloy S up to 42 Rc x x 25 20 20 0200 0230 0300 0380 0480 0630 Titanium Alloys 6Al4V, 5Al25 Sn,Çukurova Üniversitesi Mühendislik Mimarlık Fakültesi Dergisi, 33(3), ss 225236, Eylül 2018 Çukurova University Journal of the Faculty of Engineering and Architecture, 33(3), pp 225236, September 2018 ÇÜ Müh Mim Fak Dergisi, 33(3), Eylül 2018 225 Optimization of Wet Grinding Parameters of Calcite Ore in StirredOptimization of Wet Grinding Parameters of Calcite Ore in Stirred Ball Mill(PB = 78 X 10 3 kg/m3) Alumina (35 X 103 ) Glass (25 X 103 ) *Steel shot selected by an inclined plate 8 4 2 1* 10 5 14 4 15 balanced mill bodies are mounted on a casing cover and are carried by the cover revolving around the central axis At the same time, rotation gears mounted at the mill bodies biteThe Mechanism and Grinding Limit of Planetary Ball Millingt J 2015年4月24日 2 Ball mill consist of a hollow cylindrical shell rotating about its axis Axis of the shell horizontal or at small angle to the horizontal It is partially filled with balls made up of Steel,Stainless steel or rubber Inner surface of the Ball mill PPT Free Download SlideShare
.jpg)
Optimization of the makeup ball charge in a
1992年3月1日 Batch grinding parameters a T 063 min −1 γ 080 α 137 Λ 47 β 62 Φ 0 060 δ 01 a T 112 mm Table 2 Average input values for the fullscale mill and their corresponding interval ranges THE EFFECT OF BALL MILL PARAMETERS ON MINERAL LIBERATION Hector E Rojas Committee Chairman: Dr GT Adel Mining and Mineral Engineering (ABSTRACT) In previous studies, the analysis of ball mill ° operating parameters and their effects on breakage phenomena has been limited to homogeneous materials Though these ßTHE EFFECT OF BALL MILL OPERATING PARAMETERS ON MINERAL LIBERATION(10) In the second part of the paper, we will investigate the hypothesis defined by Eqs 8, 9 and 10 3 Experimental Investigations were carried out in a laboratory ball mill having the size of DxL = 160x200 mm with a ribbed inside surface of the drum The mill ball loading was 40% by volume, the rotation rate was equal to 85% of the critical THE OPTIMAL BALL DIAMETER IN A MILL AcademiaTECHNICAL SPECIFICATION OF WET BALL MILL AND HYDROCYCLONE 00 311020 UDAY / P V S BABU AMAN SG REV DATE PREPARED CHECKED APPROVED Bharat 2 Parameters Design Capacity of Mill 302 TPH Media to be Handled Limestone Limestone Analysis Refer Clause No 6TECHNICAL SPECIFICATION OF WET BALL MILL AND HYDRO
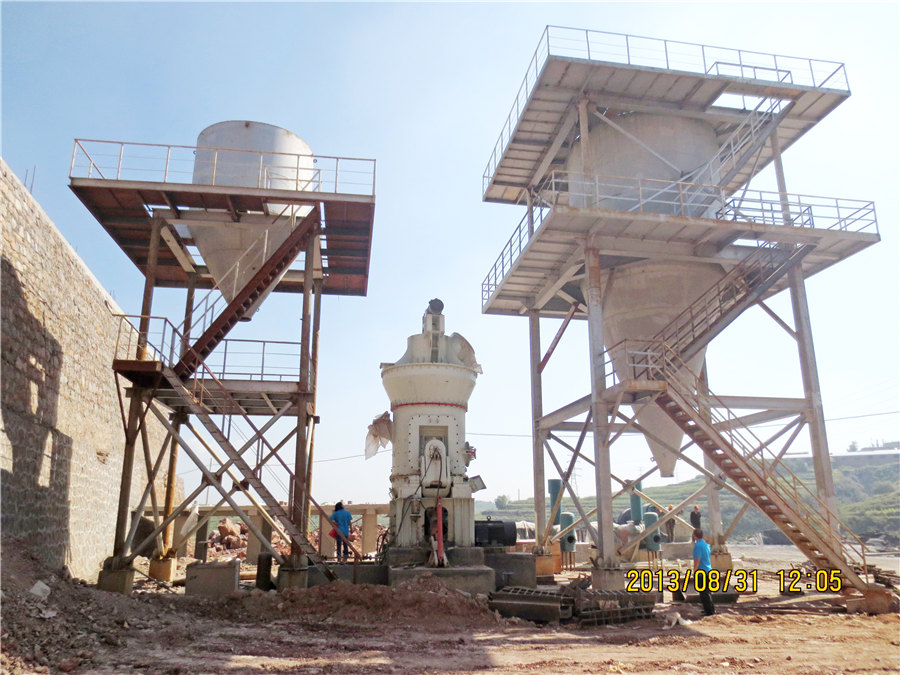
Investigating grinding mechanisms and scaling criteria in a ball mill
ing powders in a ball mill is a complex operation in which many parameters, such as geometrical factors [2], filling ratios [3], powder properties [4] or the energy transferred to the vessel [5] can influence the characteristics of the resulting powder The effect of each parameter on the resulting ground powder is usually inves2013年5月1日 The influence of several grinding parameters such as charged material volume, ball filling ratio, and mill rotation speed on energy efficiency of fine grinding of hydrated lime and the product (PDF) Effect of ball mill grinding parameters of hydrated lime Ball Mill, Wet Ball Mill Lubrication system, Mill circuit tank with an agitator, Mill circuit Pump, Mill Hydro cyclone, 3way distributor and accessories The Wet Ball Mill is the wet horizontal type The Process water is supplied to Wet Ball Mill and Wet Mill circuit Tank Slurry from the Wet Ball Mill flows by gravity to the Wet Mill Receiver TECHNICAL SPECIFICATION OF WET BALL MILL EQUIPMENT2023年4月28日 The primary goal of this work is to investigate the relationship between particle size and purity and ball milling parameters (milling speed, milling time, ball to powder ratio, and ball size) Changing a number of variables to see how affect the end result is what a parametric analysis of a fourstation ball mill for making ultrafine particles would entailParametric study on four station ball mill for synthesis of ultrafine
36.jpg)
OPTIMIZATION OF THE BALL MILL PROCESSING PARAMETERS
DANICA B ZARIĆ3 1Faculty of Technology, University of Novi Sad, Novi Sad, Serbia 2Institute of Food Technology, University of Novi Sad, Novi Sad, Serbia 3IHIS Tehno Experts doo, Research Development Center, Beograd, Serbia SCIENTIFIC PAPER UDC 660638:660123 OPTIMIZATION OF THE BALL MILL PROCESSING PARAMETERS IN THE FAT FILLING