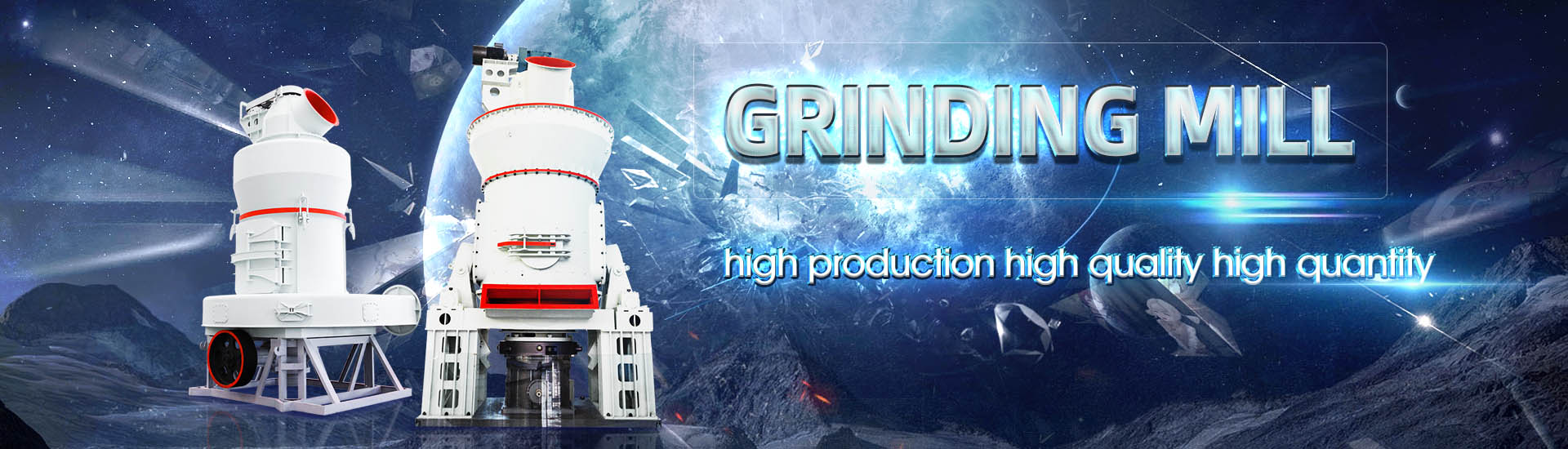
Wet selection and powder making process of quicklime ore
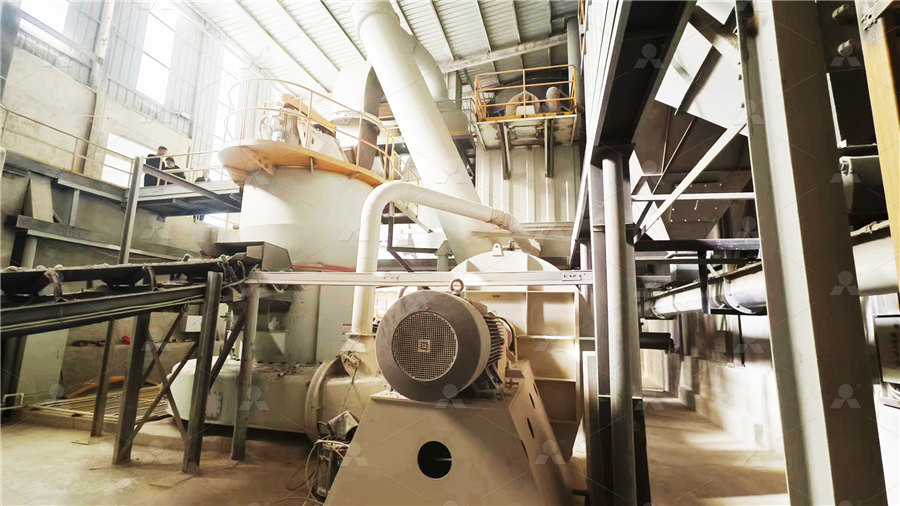
Optimum Water Content Estimation for Wet Granulation of Iron
In this study, we present a method to determine the optimum water content using the agitation torque of wet ore powder blended with quicklime First, we investigated the agitation torque for blending of various types and ratios of ore powders and quicklime2017年5月10日 In the industrial process fine iron ores should be wet agglomerated and sintered or pelletized to be used as feed in the blast furnace For instance, their surface wettability will Wettability in water/iron ore powder systems: To the universality 2023年1月19日 In this study, we present a method to determine the optimum water content using the agitation torque of wet ore powder blended with quicklime First, we investigated the Optimum Water Content Estimation for Wet Granulation of Iron Based on the obtained results by the investigation of the features of magnetite–hematite ores from the Mikhailovskoye deposit, a technological scheme of magnetoflotation beneficiation was Optimum Water Content Estimation for Wet Granulation of Iron
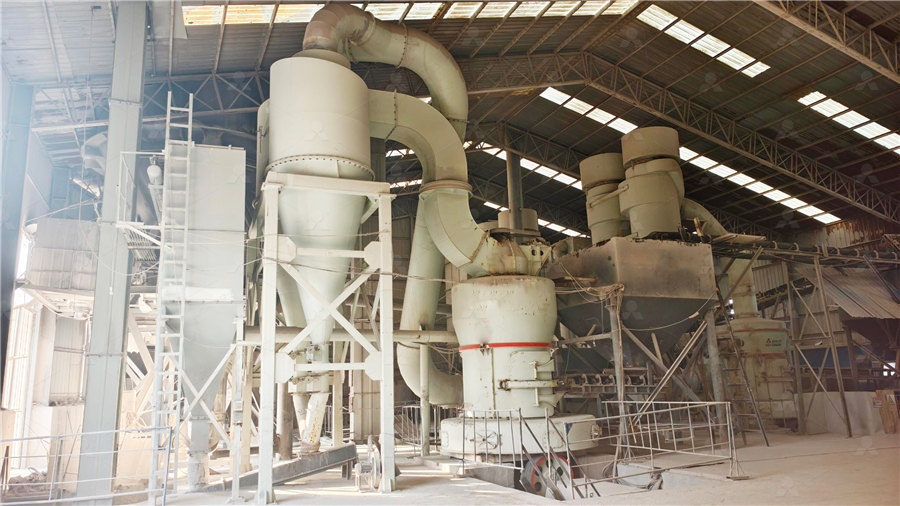
Modification of Wet Granulation Process During Iron Ore Sintering
2020年7月1日 Mixture of iron ore fines, limestone, dolomite, coke breeze, lime and metallurgical wastes are fused partially to form lumpy porous iron bearing mass called sinter 2021年10月1日 Wet granulation plays an important role in the processing of fine ore powder Water content is a critical process parameter that determines the granule properties during wet Influence of quick lime on pore characteristics of hightemperature In this study, we present a method to determine the optimum water content using the agitation torque of wet ore powder blended with quicklime First, we investigated the agitation torque for Optimum Water Content Estimation for Wet Granulation of Iron In this study, we present a method to determine the optimum water content using the agitation torque of wet ore powder blended with quicklime First, we investigated the agitation torque for Optimum Water Content Estimation for Wet Granulation of Iron
.jpg)
Importance of intensive mixing on sintering with finegrained iron
2020年11月1日 The flux (quicklime) is evenly distributed, and it can also optimize the mineralization process because iron oxides can easily contact CaO and generate calcium In this study, we present a method to determine the optimum water content using the agitation torque of wet ore powder blended with quicklime First, we investigated the agitation torque for Optimum Water Content Estimation for Wet Granulation of Iron 2022年12月29日 Iron ore granulation is an indispensable process in the production of sinter that can influence and regulate the yield, efficiency and quality(PDF) Iron Ore Granulation for Sinter Production: PDF On Jul 11, 2018, Sandra Lúcia de Moraes and others published Iron Ore Pelletizing Process: An Overview Find, read and cite all the research you need on ResearchGateIron Ore Pelletizing Process: An Overview
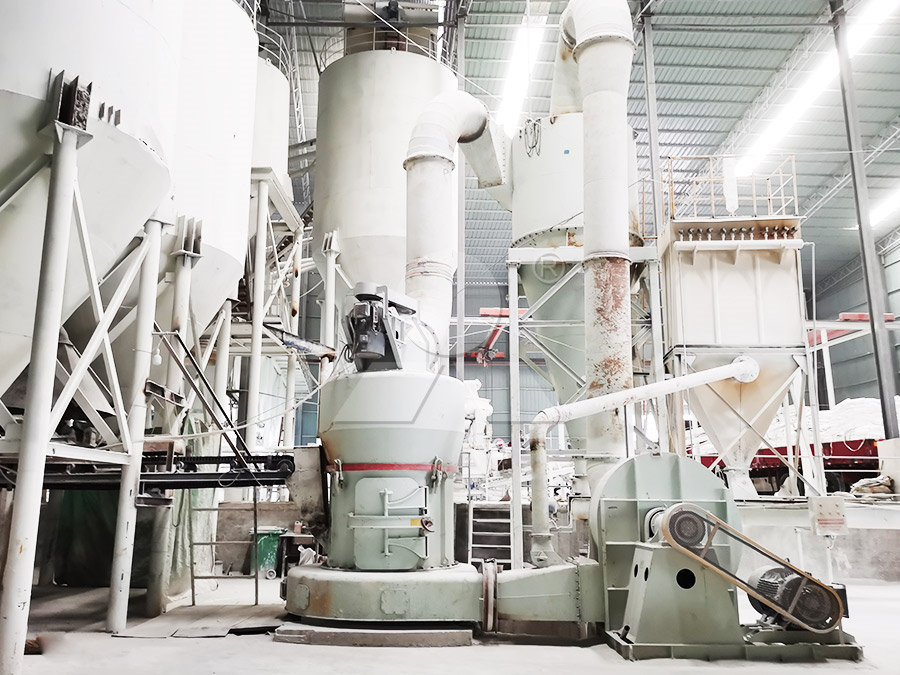
Type Selection of Quicklime Deep Processing Equipment
2022年12月22日 CLIRIK has been committed to the research and development of energysaving and environmentally friendly grinding equipment The vertical mills, highpressure mills, and micropowder mills developed and produced by CLIRIK have won high praise from users in quicklime processingAccording to the quicklime mesh and output, the following suggestions are given for the selection of quicklime powder grinding mills for reference only Quicklime Powder 1 Raymond mill is used for quicklime powder making It is recommended to use Raymond mill for the processing of quicklime with an output of 1 to 9 tons and a mesh of 80 to How to choose quicklime powder grinding mill?Quicklime (calcium oxide) is used in the steel making process You will find out a bit more about this in a later page in this section Slaked lime (calcium hydroxide) is used to neutralise acid soils It is more expensive than using limestone, but is faster acting Where would you like to go now? To the large scale chemistry menu limestone, quicklime and slaked lime chemguide2023年2月4日 What is lime Lime, also known as quicklime or burnt lime, is mainly composed of calcium oxide, molecular formula CaO, which is a white block or powder cubic crystal The lime commonly used in industry will be dark gray due to impurities such as magnesium oxide, aluminum oxide and ferric oxide The relative density is 325338g/cm3, the true density is Lime/quicklime for metallurgy – how producing and briquetting
.jpg)
Applications of Quicklime Hydrated Lime
If a precisely controlled amount of water is added to quicklime, a (violent) reaction ensues with much evolution of heat In the chemical reaction with water, the lumps of quicklime break down to a dry fine white powder known as hydrated lime or lime hydrate Quicklime + (a controlled amount of) water > hydrated lime (also called lime hydrate)2010年6月30日 Wet beneficiation of minerals necessarily requires removal of large amounts of water—typically contaminated—before further processing of the concentrated ores can be carried outDewatering and Drying in Mineral Processing Industry: Potential for 2023年1月1日 Hence, to meet the growing steel demand, the demand for iron ore is also increasing While, on one side reserves of good quality iron ore are depleting, on the other side the steel companies require better quality of iron ore with lower gangue content due to the addition of higher capacity blast furnaces for higher productivity, lower hot metal cost, and Iron ore beneficiation: an overview ScienceDirect2012年5月5日 Small and medium enterprises in the metallurgical sector face a particularly difficult situation due to development constraints resulting from low levels of capital, high maintenance costs, lack Application of the new mixing and granulation technology of
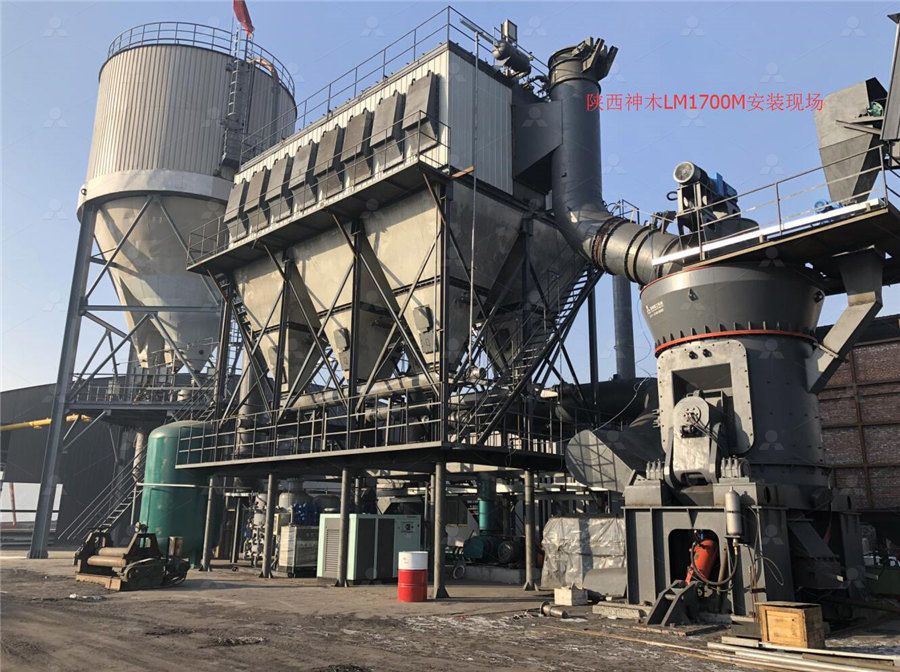
Quicklime Natural Selection Natural Lime Products
Quicklime is limestone (a rock rich in calcium carbonate) that has undergone a chemical change in a kiln, liberating it of all the carbon and water it holds, creating a very unstable material (calcium oxide) which needs to hydrate2024年6月23日 Production Process of QuickLime The production process of Quick Lime, also known as Calcium Oxide, involves high temperatures and chemical reactions Here’s a breakdown of how this super substance is made: QuickLime 101: Everything About This Super 2016年1月8日 The first commercial production of phosphate rock began in England in 1847 A wide variety of techniques and equipment is used to mine and process phosphate rocks in order to beneficiate lowgrade ores and remove Mining and Beneficiation of Phosphate OreWet granulation plays an important role in the processing of fine ore powder Water content is a critical process parameter that determines the granule properties during wet granulation However, in the ironmaking industry, various types of iron ore powder imported from different regions are blended, quicklime powder is added as a binder, and Optimum Water Content Estimation for Wet Granulation of Iron Ore
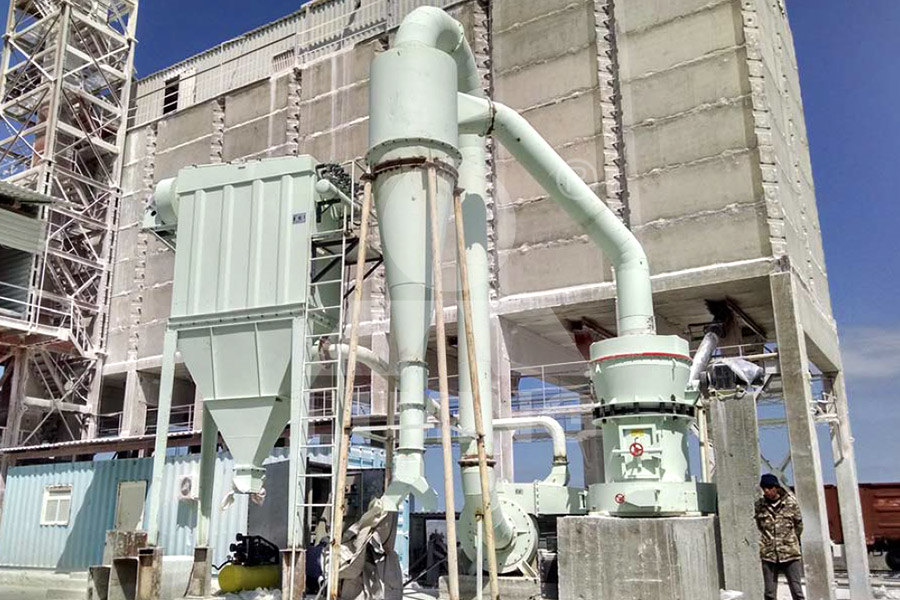
Iron Ore Sintering: Raw Materials and Granulation ResearchGate
2016年10月28日 Sintering is an agglomeration process that fuses iron ore fines, fluxes, recycled products, slagforming elements and coke The purpose of sintering is to obtain a product with suitable Wet granulation plays an important role in the processing of fine ore powder Water content is a critical process parameter that determines the granule properties during wet granulationSpecific surface areas of ores Download Scientific Diagram2020年11月1日 In the wet granulation process for pig iron, water is added to agitate the ore powders in a granulator, such as a drum mixer, and fine ore powders are agglomerated with coarse ore particles using Importance of intensive mixing on sintering with finegrained iron ore During the sintering process, Mini Pellets are blended with ironore fine and coke as an iron source We receive dry and wet dustladen steel from JFE Steel Corporation West Japan Works We then dezinc, dehydrate, and form granules of this material, which is then supplied back to JFE Steel Corporation West Japan WorksQuicklime and Mini Pellets JFE Mineral Alloy Company,Ltd
.jpg)
Modeling of Bauxite Ore Wet Milling for the Improvement of Process
The specific energy ε (kJ/kg) input, ie, the energy input E (kJ) divided by the total mass M (kg) of the feed material, can be expressed as a function of grinding time t as: ε¼ P∙t M ð12Þ Table 1 Chemical composition (wt%) of bauxite ore Al2O3 Fe2O3 SiO2 TiO2 CaO LOI* Total 5795 2239 165 394 023 130 9916 * Loss on ignition after heating of the ore at 1050 °C for 3 h Circular 2001年4月1日 This study has examined the effects of limestone characteristics (microstructure and texture) and calcination temperature on the reactivity of the produced quicklime(PDF) The Effects of Limestone Characteristics and Calcination 2018年8月31日 PDF The EU28 total lime demand in 2017 was estimated at about 20 million tons, out of which about 40% are consumed in the iron and steel industry Find, read and cite all the research you (PDF) Management of Lime in Steel ResearchGateHigh Calcium Quicklime Pebble and Powder, used for making lime putty and hotmixed or hotlime Mortars Quicklime is Limestone (a rock rich in calcium carbonate) that has undergone a chemical change in a kiln, liberating it of all Quicklime High Calcium Quicklime Pebble and
R)8OC`6F[ZIB.jpg)
Determining Optimum Water Content for Iron Ore Granulation
3) Therefore, the handling of fine ore powder is a critical issue in the ironmaking process4–7) In the manufacturing process of pig iron, wet granulation has often been performed prior to the sintering process to reduce fine ore particles In the wet granulation process, the fine ore particles are agglomerated with coarse ore particles by2024年11月21日 Nickel ore mainly includes sulfide coppernickel ore and nickel oxide ore (latterite nickel ore) The beneficiation and processing methods of the two are quite different: different beneficiation methods are selected according to the grade of nickel sulfide ore, and then nickel is prepared in different ways; the smelting methods of nickel oxide ore are generally Selection Of Nickel Ore Beneficiation Process Equipment2022年2月28日 ① Grinding stage The calcined lime raw material is directly (or once crushed) continuously and uniformly sent to the main machine grinding chamber through the feeder after being cooled in transit, and the ground fine powder is classified by the classifier under the action of the air flow of the fan and then sent to the main machineHow to do a good job of grinding in the lime industry?2019年8月3日 In the treatment of goldbearing polymetallic sulfide mineral ores with high content of valuable heavy metals (such as goldcontaining polymetallic sulphide ores containing copper, copper, zinc, lead, zinc, antimony, arsenic, etc), since these ores contain To eliminate harmful factors, in order to eliminate unfavorable factors, in the actual production process, the flotation Lime in Gold Ore Mining Process Flotation, Cyanidation JXSC
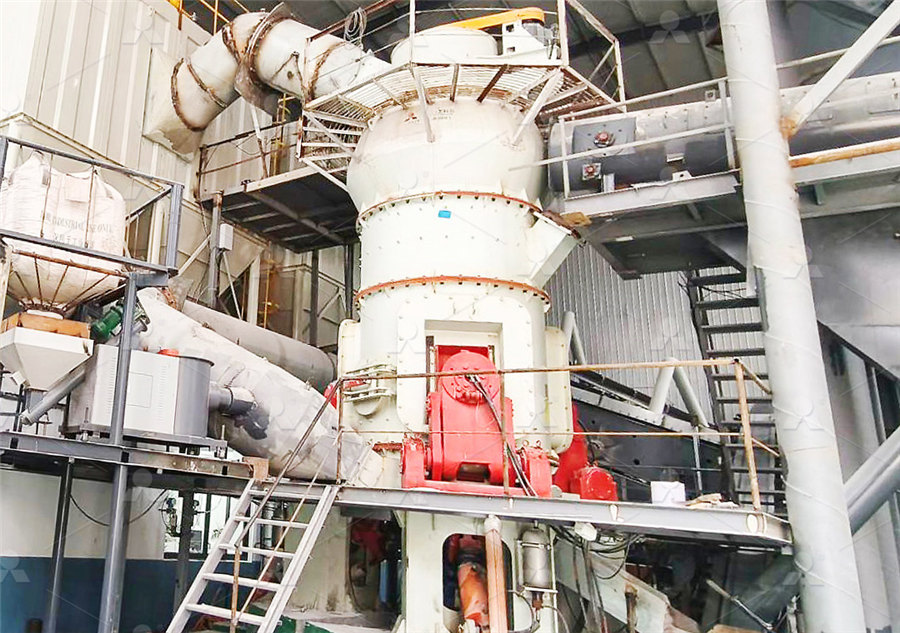
(PDF) A systematic review of gold extraction: Fundamentals
2022年8月1日 A systematic review of gold extraction: Fundamentals, advancements, and challenges toward alternative lixiviants2020年4月1日 Variability in the ore, together with upstream process dynamics, creates a challenging environment in which to achieve optimal recovery of a gravity concentrate with accurate grade controlProcess optimization of a chrome ore gravity concentration plant 2021年1月1日 Natural Carbonation Rate (NCR) over time for pure airlime mortars (top left), mixed airlime mortars (top right), hemplime (bottom left) and steel slags (bottom right)(PDF) Natural and enhanced carbonation of lime in its different 2013年3月3日 Quicklime: Quicklime is dangerous to handle and store because it is highly reactive It heats rapidly and undergoes a violent reaction when water is applied This process is called slaking If the water is applied slowly and in measured quantity, the quicklime will fall into a very fine powder of hydrated limeUnderstanding Lime: an introduction to forms of lime and
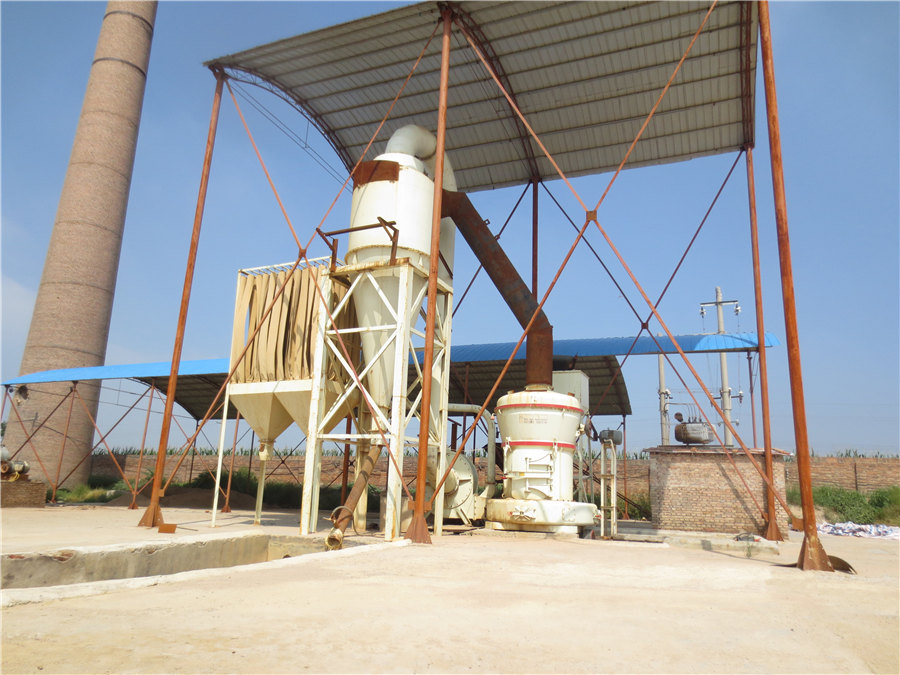
How to Make Quicklime: 10 Steps (with Pictures)
2024年4月16日 Safety is extremely important when making or dealing with quicklime Quicklime is extremely dangerous and is reactive to moisture When making or handling quicklime, you must wear safety material Specific dangers Laboratory Compaction Characteristics of Soil Using Modified Effort (56,000 ftlbf/ft 3 (2,700 kNm/m 3)) 1 This standard is issued under the fixed designation D1557; the number immediately following the designation indicates the year of Standard Test Methods for Chemical Analysis of silica from bauxite ore and for causticization in the manufacturing of alumina Dolomitic quicklime is used to produce metallic magnesium by thermal reduction which reduces magnesium oxide Lime is also used in the processing of ores and the subsequent smelting and refining of copper, zinc, lead, and other nonferrous ores EnvironmentalQUICK LIME AND BYPRODUCTS PEC Consulting GroupWet granulation plays an important role in the processing of fine ore powder Water content is a critical process parameter that determines the granule properties during wet granulation However, in the ironmaking industry, various types of iron ore powder imported from different regions are blended, quicklime powder is added as a binder, and Optimum Water Content Estimation for Wet Granulation of Iron Ore
.jpg)
Iron Ore Sintering SpringerLink
2024年1月1日 Iron ore sintering is the iron ore powder agglomeration process that changes fine iron ore powder into the lumpy iron (limestone, dolomite, quicklime, etc), fuel (coke powder and anthracite), additives (roll scale and some recycled materials), return Primary mixing is intended to mix the materials uniformly and wet them 2021年1月1日 Compared to traditional drymilling, wet grinding shows higher efficiency and can avoid dust generation Since most of IOTs are directly discharged into the river or exposed to rainwater, wet Different Effects of Wet and Dry Grinding on the Activation of Iron Ore 2021年9月5日 Size reduction is a necessary operation in mineral processing plants and provides the desired size for separation operations and the liberation of the valuable minerals present in ores Estimations on energy consumption indicate that milling consumes more than 50 % of the total energy used in mining operations Despite the fact that ball milling is an efficient Modeling of Bauxite Ore Wet Milling for the Improvement of Process 2019年1月1日 ScienceDirect Available online at sciencedirect Procedia Manufacturing 35 (2019) 242–245 23519789 © 2019 The Authors Published by Elsevier BV Peerreview under responsibility of the organizing committee of SMPM 2019 101016/jpromfg201905034 101016/jpromfg201905034 23519789 © 2019 The AuthorsA review of ironmaking by direct reduction processes: Quality
.jpg)
Binding mechanisms in wet iron ore green pellets with a bentonite
2006年11月13日 This way, the deformation values are independent of the green pellet strength 1 daN was chosen for the calculation of plastic deformation because it is generally known that wet iron ore green pellets must withstand this pressure in Wet granulation plays an important role in the processing of fine ore powder Water content is a critical process parameter that determines the granule properties during wet granulation However, in the ironmaking industry, various types of iron ore powder imported from different regions are blended, quicklime powder is added as a binder, and Optimum Water Content Estimation for Wet Granulation of Iron Ore