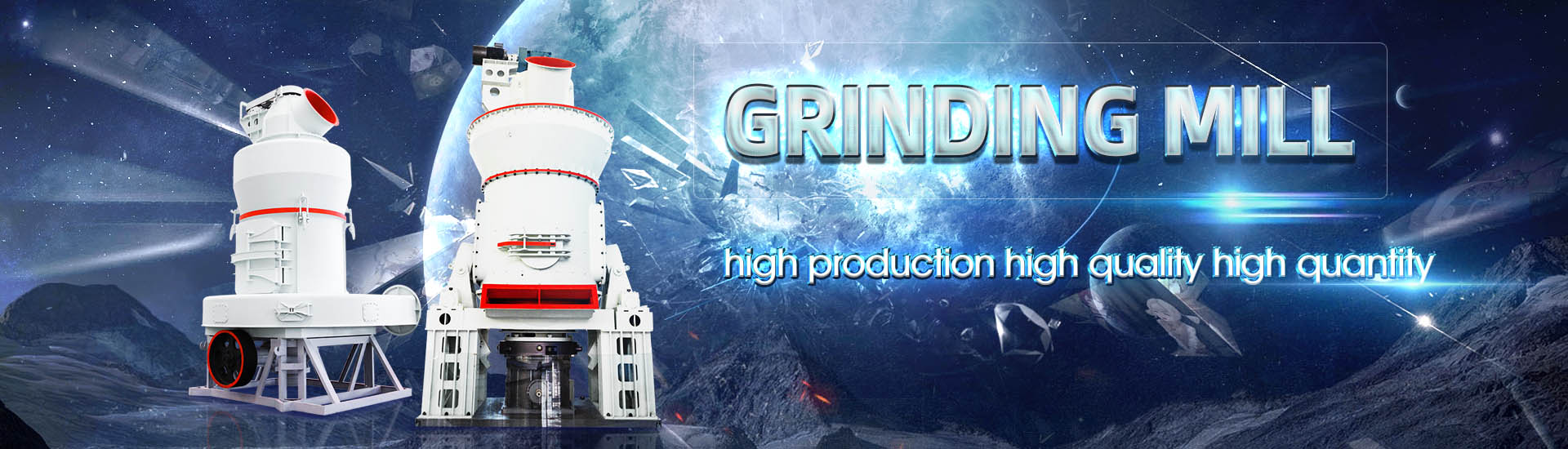
Wenshan cold roll powder production method
.jpg)
Densification mechanism of powders during cold
Cold spraying is a novel technology for preparing solidstate coatings Single Nicoated Al particles were deposited onto different substrates by cold spraying at differentIn this study, stainless steel sheets were coldrolled and the profiles of the partly rolled specimen were measured by a laser profilometer Meanwhile, data processing method to reveal the Experimental Study of Roll Flattening in Cold Rolling Process J 2022年1月1日 During compaction of powder at the meeting line of roll, particle rearrangement takes place and then deform to make cold bonding with adjoining particles The deformation of Experimental and mathematical analyses of process parameters In the process of Rolling the most significant aspect is the generation of heat through friction and deformation in the roll bite and in a typical Cold Tandem Mill, work roll temperatures normally Fundamentals of Roll Cooling and Control of Flatness at Primary
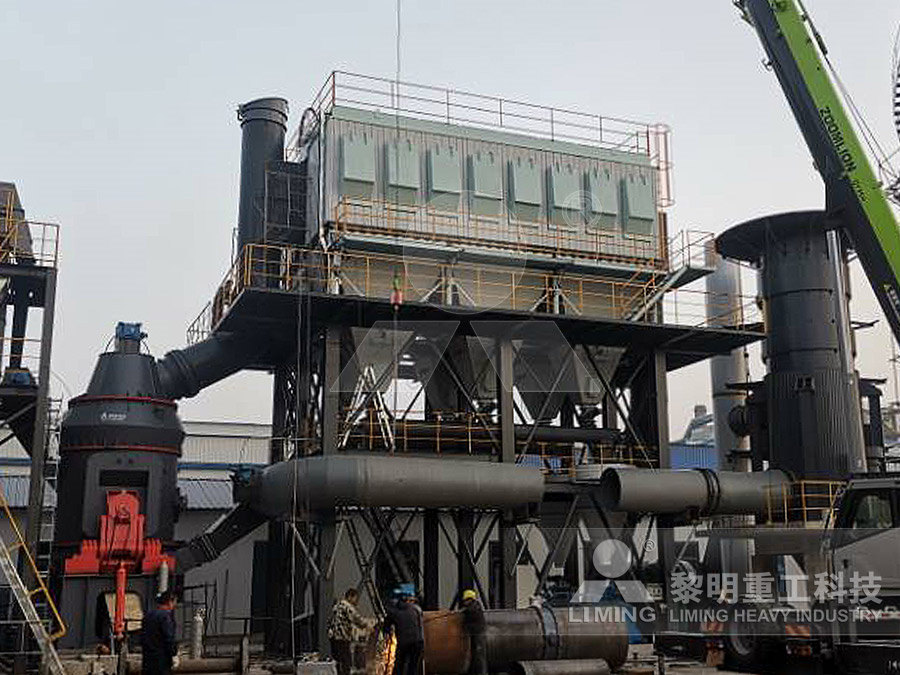
Introduction to Rolling Process Cambridge University Press
Cold rolling is generally done to produce flat rolled products like sheet, plate, strip, and foil When the length of the rolled product is too large, the material is wound and used in the coil form In It begins with comprehensive coverage of rolling processes and the mechanics of rolling, which is the theoretical content of the subject This is followed by a chapter on ‘rolling practices’ that Principles and Applications of Metal RollingMany different processes are used in the manufacturing of metal parts in cold condition, such as blanking and forming, punching, shearing, cold forging, cold extrusion, powder pressing and Cold Rolling ASSAB MalaysiaMany different processes are used in the manufacturing of metal parts in cold condition, such as blanking and forming, punching, shearing, cold forging, cold extrusion, powder pressing and Cold rolling ASSAB Hong Kong
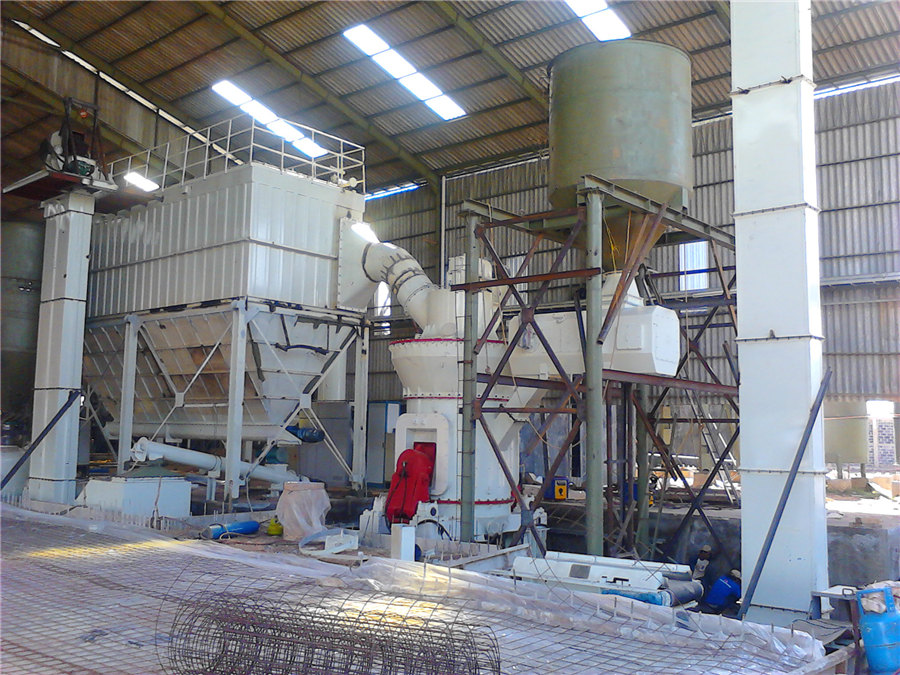
Making Metal Powder MPIF
There are four main processes used in powder production: solidstate reduction, atomization, electrolysis, and chemical In solidstate reduction, selected ore is crushed, typically mixed 2019年9月24日 PDF Highly performance methods for cold pressing (cold die forging) Herraiz Lalanaa, E Permanent magnets and its production by powder metallurgy Rev Metal 2018, 54, e121 9A ColdPressing Method Combining Axial and Shear 2016年9月1日 Download Citation Technology of roll production for cold rolling of strip using electroslag remelting method The article is concerned with the description of the manufacture of rolls for cold Technology of roll production for cold rolling of strip using 2019年12月1日 Roll compaction has been investigated for many metals, including titanium and its alloys In the case of titanium, there has been a longstanding interest in using powder metallurgy processing routes in general to reduce overall cost, as described by many authors, for example, Fang et al [] and Froes []Titanium is of great interest for many applications due to Effects of powder material and process parameters on the roll
.jpg)
Titanium: An Overview of Resources and Production Methods
2021年12月16日 Many powder production processes are at various stages of development There are two general approaches for Ti metal production: electrochemical and thermochemical methods The wellknown example of the electrochemical methods is the Fray, Farthing, and Chen (FFC) or Cambridge process [ 12 ], which is based on the electrolysis reduction of 2023年1月1日 Average powder diameter and the maximum possible production rate for the Ti4Al6V alloy as a function of ultrasonic frequency and atomisation temperatureComparison of ultrasonic and other atomization methods in metal powder Making Metal Powder The first step in the overall powder metallurgy (PM) process is making metal powders There are four main processes used in powder production: solidstate reduction, atomization, electrolysis, and chemical SolidState ReductionMaking Metal Powder MPIFMany different processes are used in the manufacturing of metal parts in cold condition, such as blanking and forming, punching, shearing, cold forging, cold extrusion, powder pressing and cold rolling Most popular grade for this application is our ASSAB XW42, being traditional D2type of material (DIN standard 12379, JIS SKD 11)Cold Rolling ASSAB Global

Commercial Methods for Powder Production Springer
Commercial Methods for Powder Production A B Backensto Glidden Co Hammond, Indiana Just as each human being is marked individually to some ex tent by the family that produced him and the environment he devel oped in, each metal powder is marked by the process used in its production This variation is fortunate in some respects because2011年3月1日 In this new method, the production of TiH2 powder at low temperature was investigated, which can be used for further dehydrogenation process to produce lowcost Ti powderProduction of titanium metal powder by the HDH process2021年12月16日 Many methods are used for the production of T i metal powder Ti powder is, there fore, the product of extraction processes that produce primary metal by using titaniumTitanium: An Overview of Resources and Production MethodsBoth of these factors are influenced by the process used for making powder There are numerous ways for powder production which can be categorized as follows Mechanical methods of powder production: i) Chopping or Cutting ii) Abrasion methods iii) Machining methods iv) Milling v) Coldstream Process 2PRODUCTION OF METAL POWDERS Weebly
.jpg)
Modeling the powder roll compaction process: Comparison of
This study compares the nip angle, normal stress at the roll gap, and the maximum material relative density computed from 2D finite element method (FEM) simulations and the 1D Johanson's model Download Citation On Dec 31, 2009, Irina B Murashova published Electrochemical methods of metal powder production Find, read and cite all the research you need on ResearchGateElectrochemical methods of metal powder production2023年10月5日 method in powder production, invol ving Hemant Panchal etal Powder manufacturing techn iques: a review International Journal of Research and Review (ijrrjournal) 153Powder Manufacturing Techniques: A Review ResearchGateCold rolling contributes to achieving a smooth surface finish and resistance to surface defects The process minimizes imperfections, making the metals more reliable for critical applications Different Cold Working Methods There are several different cold working methods, including cold extrusion, precision stamping, and roll formingWhat is Cold Rolling Drawn Metal
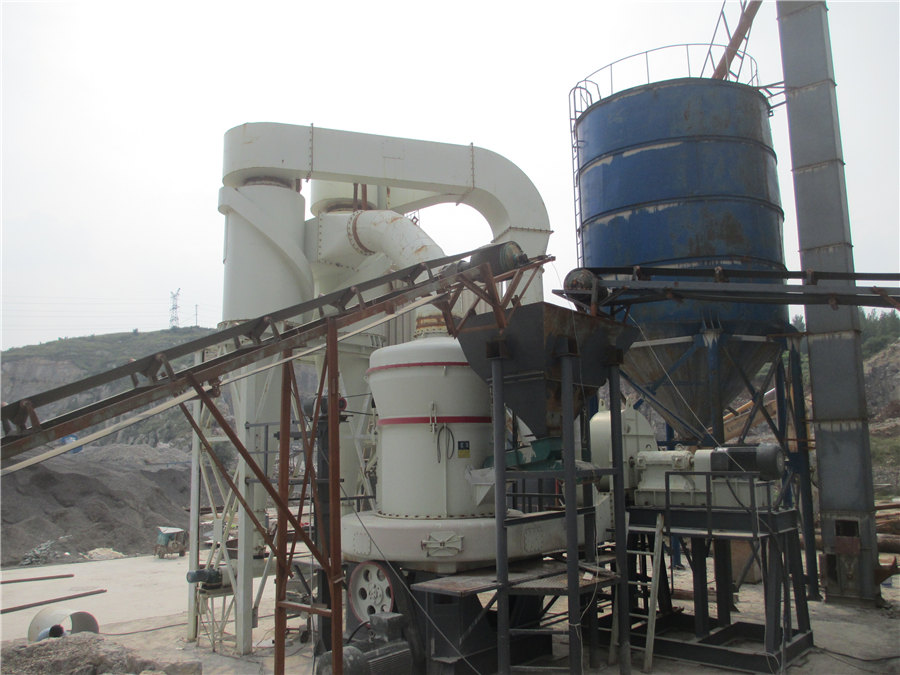
Powder Metallurgy PDF
Production of Metallic Powders •In general, producers of metallic powders are not the same companies as those that make PM parts •Virtually any metal can be made into powder form •Three principal methods by which metallic powders are commercially produced 1 Atomization 2 Chemical 3 Electrolytic •In addition, mechanical methods are These are the methods used for high production rate Best examples of mechanical production methods are the Milling Process and Cold Stream Process Milling: The basic principle of milling process is the application of impact and shear forces between two materials, a hard and a soft, causing soft material to be ground into fine particlesME306 ADVANCED MANUFACTURING TECHNOLOGY Rajagiri Today CPAO is produced also in Chile, South Africa, Kenya, Israel, Samoa and other countries Subsequently they built a complete processing plant to Figure 2 Flowchart of the traditional mechanical extraction method for avocado oil production Figure 3 Flowchart of the coldpressing mechanical extraction method from Alfa Laval(PDF) Avocado oil extraction processes: method for coldpressed 2017年5月12日 The Al/Ni multilayer powder materials used in this study were fabricated by the following methods Figure 1 shows a schematic of the procedure of the fabrication of Al/Ni multilayer powder materials Commercially available pure Al (>995%) and pure Ni (>999%) foils, whose dimensions were 50 mm 2, were preparedTo obtain an atomic ratio of , 30µmthick Temperature behavior of exothermic reaction of Al/Ni multilayer powder
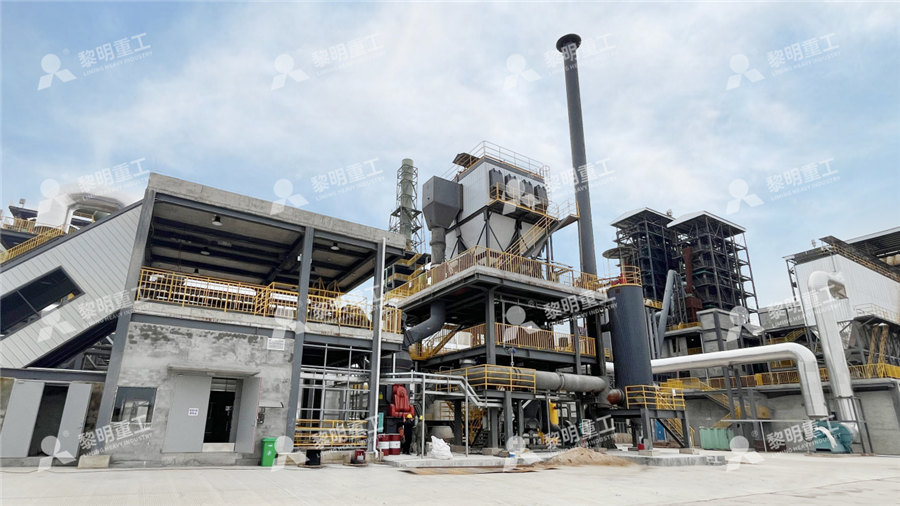
Powder Metallurgy SpringerLink
2024年1月13日 After Germany, the United States, the Soviet Union, and Japan used powder metallurgy technology to produce cemented carbide; and iron powder was produced by vortex grinding, solid carbon reduction, and molten metal atomization; powder metallurgy ironbased parts were developed; sintered friction materials were put into production; and metal button 2024年6月5日 The pressed powder is known as green compact, and the process is generally carried out at room temperature There are two main methods of compacting metal powders: (1) with a punch and die and (2) isostatically Selection of the method depends upon the complexity of the part to be produced Mechanical pressing is mostly used for simple partsPowder Metallurgy SpringerLinkthe modern production Powder metallurgy oers proven advantages as an alternative production route for conventional metalforming technologies due to its high exibility regarding the processes, materials, shapes and products [2] One of the major applications of powder metallurgy is the production of sintered precision parts, used in automotiveNumerical Modelling of the Powder Metallurgical Manufacturing This has been for long the most widely used method for the production of iron powder Selected ore is crushed, mixed with carbon, and passed through a continuous furnace where reaction takes place leaving a cake of sponge iron which is then further treated by crushing, separation of nonmetallic material, and sieving to produce powderPowder Metallurgy – Powder Processes (Solid State Reduction

Mould Powder Development for Continuous Casting of Steel
2013年7月3日 Mould powders significantly determine the stability of the continuous casting process of steel at all casting speeds The main functions of mould powders are to provide strand lubrication and to control the mould heat transfer in the horizontal direction between the steel shell and the copper mould The composition, properties and operational performance of mould 2023年5月15日 Because the outer material is refined by electroslag, it has high cleanliness and can meet the requirements of cold rolling, so it can be used as a cold rolling work roll Hitachi, Japan produced coldrolled semihighspeed steel rolls with a High Speed Steel Roll Manufacturing Method LMM RollsThe basic operations in milk powder production consists of receiving and selecting milk, filtration/clarification, cream separation/standardization, preheat treatment, condensing, homogenisation, drying, packaging and storing of powder Production of skim milk powder differs slightly from whole milk powder production i StandadizationUNIT 14 METHOD OF MANUFACTURE OF SPRAY AND ROLLER DRIED MILK POWDER 2018年3月28日 This paper is about the great modification of Roll Powder Sintering (RPS) additive manufacturing technology and possibility of definition a point’s location in 3D space within a single value by spiral coordinate system A new algorithm of sequence manufacturing is shorter than previous one and provides higher performance of RPS machine Proposed methods Advanced roll powder sintering additive manufacturing technology

Technology of roll production for cold rolling of strip using
2015年12月16日 The article is concerned with the description of the manufacture of rolls for cold rolling of strip using electroslag remelting process and decommissioned rolls It also describes modes of initial and final thermal treatment of work rolls providing the necessary hardness of the roll barrel and depth of the hardened layer The article offers the scheme and experimental 2019年8月29日 The concept of coldformed light steel (CFS) framing construction has been widespread after understanding its structural behavior and characteristics through massive research works over the yearsManufacturing, Applications, Analysis and Design of Cold 2016年7月13日 In fact, this is not the method for the production but method of additional treatment of non‐spherical powder, which allows to change the shape of particles to ideal spheres(PDF) Metal Powder Additive Manufacturing ResearchGateBoth of these factors are influenced by the process used for making powder There are numerous ways for powder production which can be categorized as follows Mechanical methods of powder production: i) Chopping or Cutting ii) Abrasion methods iii) Machining methods iv) Milling v) Coldstream Process 2PRODUCTION OF METAL POWDERS Weebly
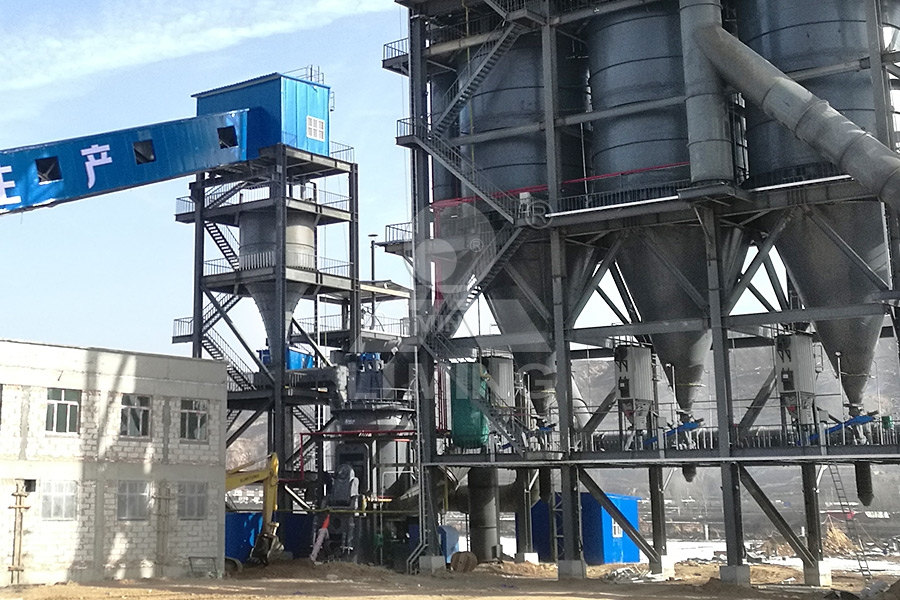
Effects of powder material and process parameters on the roll
2019年12月1日 In this study, experiments were carried out to investigate the effects of powder type and size on the roll compaction and subsequent sintering and cold rolling behaviour of titanium powder Powders used ranged in upper sieve sizes from 015 to 3 mm Strip density was found to increase with decreasing powder size while thickness decreasedThe severe directionality which is common in wrought foil can easily be avoided by the direct powder rolling process The method is adaptable to most alloy compositions For example, highstrength Ti6AI2Sn4Zr2Mo alloy foil has been produced The powderrolling process is particularly attractive as a production method for titanium alloy foilThe Direct PowderRolling Process for Producing Thin Metal StripExplore the benefits and applications of powder metallurgy, a unique metalforming method that allows for the production of highquality, complex parts with close tolerances Learn about the use of copper and copper alloy powders in various industries, the production of granular and flake powders, and the sintering processproduction and properties of copper powders Total Materia2014年12月20日 12 b) Filing: Filing as a production method has been frequently employed, especially to alloy powders, when supplies from conventional sources have been unobtainable Such methods are also used for manufacture of coarse powders of dental alloys Filing can also be used to produce finer powder if its teeth are smaller * commercially not feasiblePOWDER METALLURGY PPT Free Download SlideShare
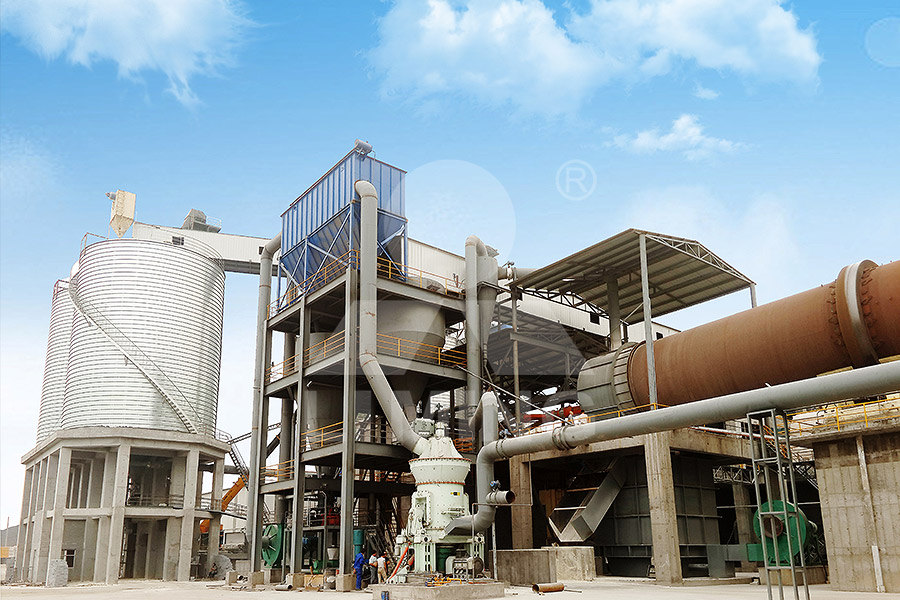
Powder Metallurgy: What Is It? Processes, Parts, Metals Used
Powder metallurgy is an environmentally friendly production method, with an impressive 97% of the material used becoming part of the final product This process generates minimal waste and no scrap, as all powder used is incorporated into the finished component2016年11月1日 A novel method was developed to produce spherical Ti6Al4V powder for advanced nearnetshape manufacturing processes including additive manufacturing and powder injection moldingA novel method for production of spherical Ti6Al4V powder Many different processes are used in the manufacturing of metal parts in cold condition, such as blanking and forming, punching, shearing, cold forging, cold extrusion, powder pressing and cold rolling Most popular grade for this application is our ASSAB XW42, being traditional D2type of material (DIN standard 12379, JIS SKD 11)Cold Rolling ASSAB Indonesia2003年2月1日 Recently used models relating basic properties of the feed material, roller press design and its operating parameters are reviewed In particular, we discuss the rolling theory for granular solids Comparison of various modeling methods for analysis of powder
.jpg)
Development of production technology for preparation of beetroot powder
PDF On Dec 1, 2020, Durga Shankar Bunkar and others published Development of production technology for preparation of beetroot powder using different drying methods Find, read and cite all the