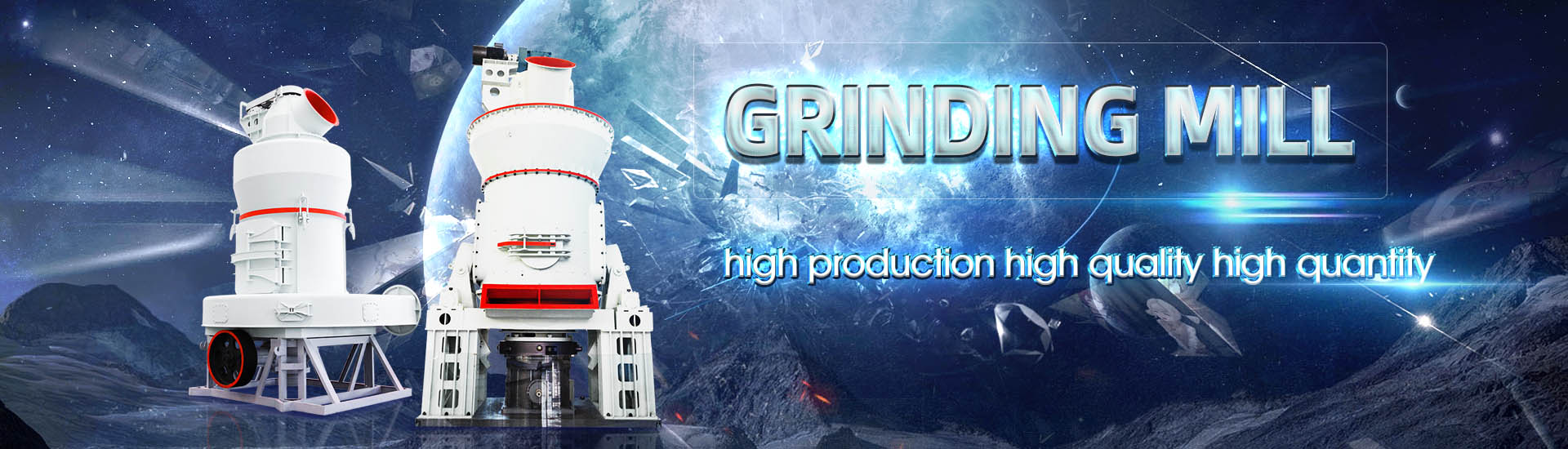
Ore grinding mill rotor sleeve material
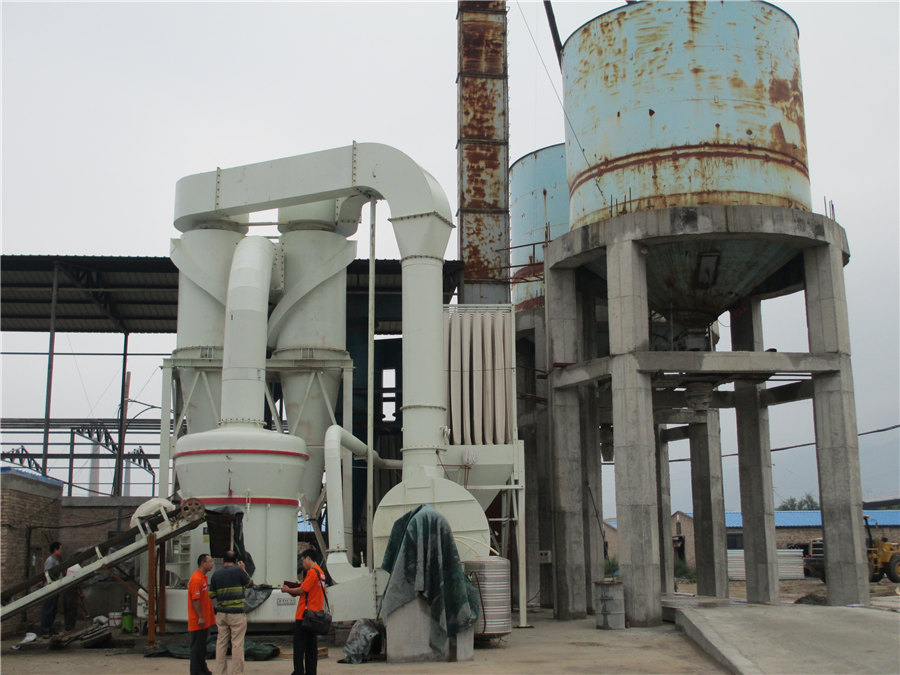
Retaining sleeves for high speed PM rotors: (a) metal sleeve; (b
Typical materials for nonferromagnetic sleeves are Inconel 718 (NiCoCr based alloy) with electric conductivity 08×10 6 S/m (138% ICACS) at 20 o C, titanium alloys, stainless steels, carbonThe valuable minerals are finely disseminated in the ore body requiring a primary circuit grind of 75µm Because of increasing primary mill throughput (>950t/h), the flotation feed grind Energy efficient rotor design for HIGmills Swiss Tower Mills The VPM vertical stirred grinding mill, which has recently been introduced by STM, is a further development of the wellknown and industry leading VRM milling technology The VPM mill RECENT DEVELOPMENTS IN COARSE GRINDING USING VERTICAL 2023年7月20日 According to the material transmission methods, ore grinding is divided into dry grinding, wet grinding, and moist grinding Dry grinding relies on pneumatic conveying, in Ore Grinding SpringerLink
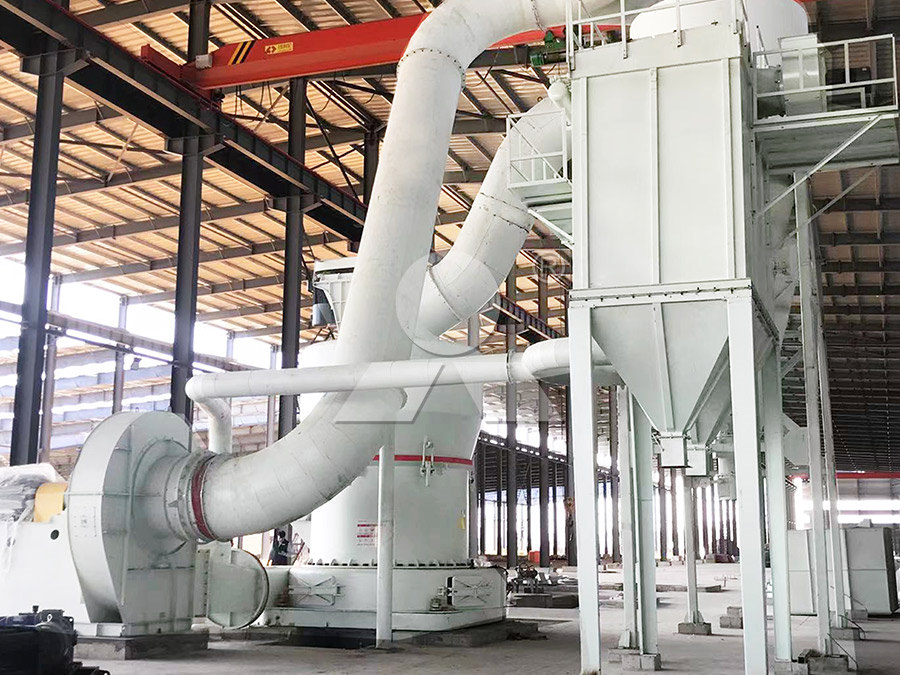
Operational parameters affecting the vertical roller mill
2017年4月1日 Pilot plant test results with various ores showed that low energy consumption feature of vertical roller mills is applicable to the ore industry Grinding test results for zinc ore We offer fit for purpose liners for all types of mills, including SAG mills, AG mills, ball mills, rod mills, and pebble mills Our liners are designed to fit the specific requirements of each mill, Mill liners Metsoer rotor mills Temporary overloads are easily balanced at continued output which ensures particularly effective grinding The extremely quick size reduction process increases sample Size reduction with Rotor Mills McCrone2015年3月15日 Verticalrollermills (VRM) are an energyefficient alternative to conventional grinding technology One reason is the dry inbed grinding principle Results of extensive test Research of iron ore grinding in a verticalrollermill
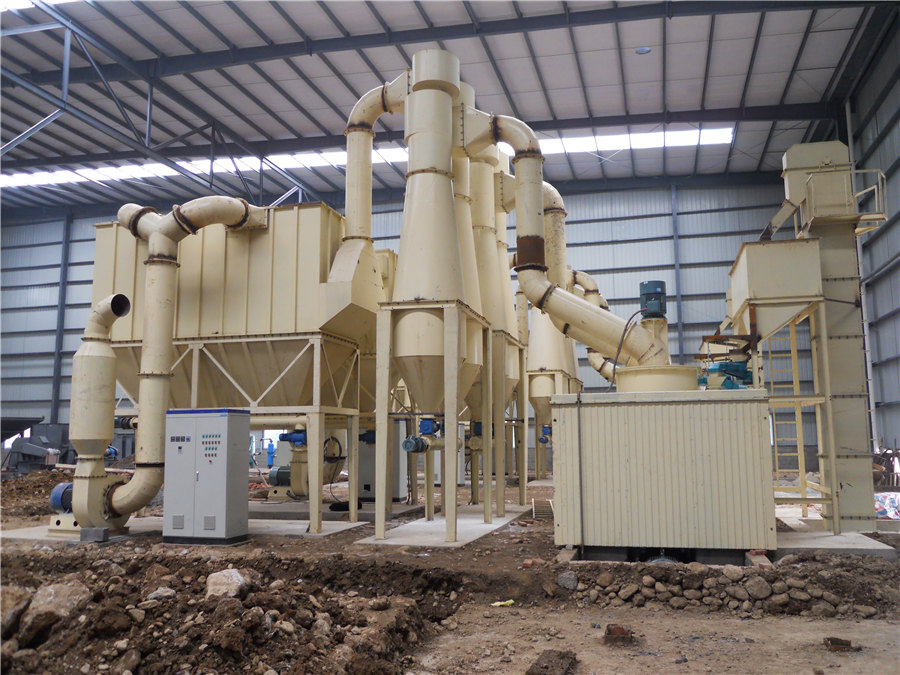
Roasting developments – especially oxygenated roasting
2005年1月1日 Dry grinding of crushed ore using two doublerotator mills to obtain 80% passing 74 μm Wholeore roasting of ground ore using two twostage, oxygen roasters to remove Download scientific diagram Retaining sleeves for high speed PM rotors: (a) metal sleeve; (b) carbongraphite sleeve from publication: Design of permanent magnet brushless motors for high speed Retaining sleeves for high speed PM rotors: (a) metal Ore grinding machines can be divided into many types according to different classification methods, each with significant characteristics The following is a general introduction to the types of oregrinding machines and their Ore Grinding Machines: Ball Mill, Rod Mil Grinding With its adjustable speed of 3,000 to 10,000 rpm the rotor beater mill SR 300 is intended for universal use: from sample preparation in laboratories up to preparing sample batches in pilot plants or production facilities The grinding chamber, the feed hopper and the material inlet are completely made from high quality stainless steelRotor Mills Glen Mills, Inc
.jpg)
Tower Mill Operating Work Index 911Metallurgist
2016年6月3日 The principal method of grinding in a Tower mill is attrition (scrubbing of particles off material being ground), with the possibility of some shearing and 911 Metallurgist is a trusted resource for practical insights, solutions, and support in mineral processing engineering, helping industry professionals succeed with proven expertise Tower Mill Operating Work IndexRequest PDF On Mar 15, 2015, Mathis Reichert and others published Research of iron ore grinding in a verticalrollermill Find, read and cite all the research you need on ResearchGateResearch of iron ore grinding in a verticalrollermillUltra fine vertical grinding mill is an advanced mill which combining our company several years of millproducing experiences, 1As the grinding principle of material layer, 11Both electronic and mechanical limit device not only prevent the direct touch between the roll sleeve ,mill stone and liner plates, LUMSeries Ultra Fine Vertical Grinding MillKefid Machinery2013年4月8日 3 Loesche technology – always one step ahead 2 The company Loesche has more than 100 years of experience in the comminution of coal, cement raw material, clinker, slag and minerals With consistently new developments, Loesche is always one step ahead Since 1961 Loesche mills have been successfully used in the ore industry 1961 Delivery of the first Loesche Mills for ores and mineral PDF SlideShare
.jpg)
Attrition Grinding Mill Design 911Metallurgist
2017年6月9日 As part of its mission to advance minerals technology, the Federal Bureau of Mines has conducted investigations to determine the feasibility of producing subsievesize material by an attrition grinding method The Bureaupatented technique involves the intense agitation of a slurry composed of the material to be ground, a granular grinding medium, and a Grinding Mills Barry A Wills, James A Finch FRSC, FCIM, PEng, in Wills' Mineral Processing Technology (Eighth Edition), 2016 71 Introduction Grinding is the last stage in the comminution process where particles are reduced in size by a combination of impact and abrasion, either dry, or more commonly, in suspension in waterGrinding Mill an overview ScienceDirect TopicsCeramic Ball Mill Processing ability: 005–15 tons per time Reference Power: 22–75 kw Applied material: quartz, iron ore, copper ore, gold, etc The Description and Function of Ceramic Ball Mill: Ceramic Large mill, Large grinding mill All industrial manufacturersFeed material: soft, mediumhard: Material feed size* 25 mm: Final fineness* 50 µm: Speed at 50 Hz (60 Hz) 3,000 10,000 min1 (in steps of 500 min1) Rotor peripheral speed: 22 72 m/s: Types of rotors: standard / distance: Material of Rotor Beater Mill SR 300 RETSCH
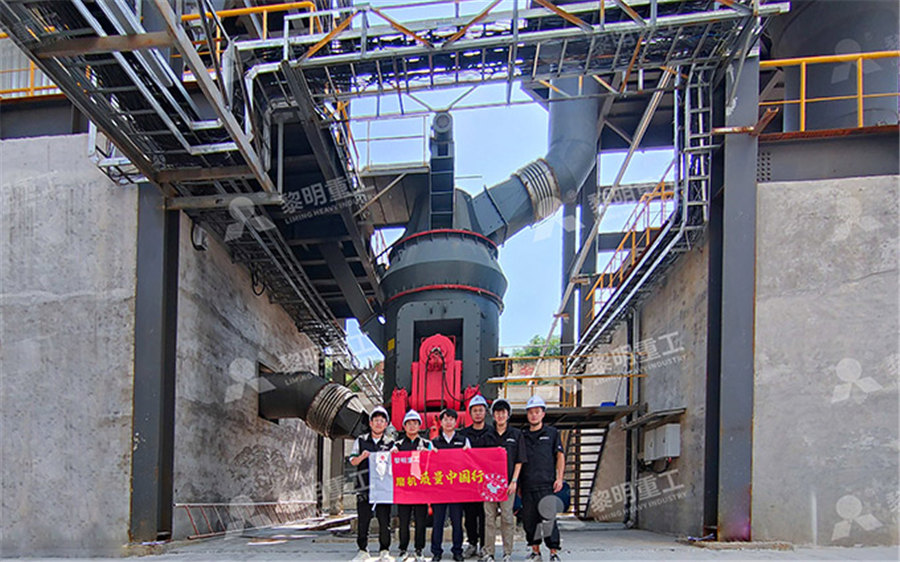
Grinding Mills and Their Types – IspatGuru
2015年4月9日 Material grinding is quite often an integral part of an industrial process, whether carried out on a large or small scale and in some cases the grinding mill may be the single most costly item for in the process of operation 3 A 62 m x 20 m mill shell on its way from France to Malaysia With an extensive range of grinding systems, consisting of x tube mills, x rod mills, x autogenous and semiautogenous mills, x AEROFALL mills, x roller mills and x POLYCOM® highpressure grinding rolls including x separators, x cement coolers, x dryers and x expert systems for automatic process control, Tube mills for dry grinding PolysiusIndex Terms: Cycloconverter, multilevel Inverter, and Gearless Mill Drive INTRODUCTION For ore grinding operation in Mines, large Grinding mills are used air gap between the stator and the rotor is in the range of 1520 mm, +/ 3 mm The Frozen Charge detection and management: At standstill, the material inside the mill tends to OVERVIEW OF MV DRIVE TECHNOLOGIES IN MINES AND FUTURE Find Grinding Mills and Pulverizers on GlobalSpec by specifications Grinding Mills and Pulverizers are machines that grind materials into fine powders, tiny shards, shapes, or granules on a continuous basis Often, they are used to process items that are 2 inches (5 cm) in sizeGrinding Mills and Pulverizers Specifications GlobalSpec
.jpg)
Size reduction with Rotor Mills
– Cyclone Mill TWISTER 10 – Technical data 11 – Order data 12 Rotor Beater Mills – Applications 13 – Rotor Beater Mill SR 200 14 – Rotor Beater Mill SR 300 14 – Technical data 15 – Order data 16 Cross Beater Mills – Applications 17 – Cross Beater Mill SK 100 18 – Technical data 19 – Order data 20 Ultra Centrifugal Mills2020年6月3日 The design of such grinding mills is extremely critical, requiring sophisticated software tools, proprietary calculation worksheets, and experienced technical engineers and drafters This blog will review how the mill design process has changed over the last 30 years While most of the changes have been positive, new issues and problems have risen in the How grinding mill design changed over the last 30 years2023年7月22日 Ore crushing provides suitable particle size of material for subsequent ore grinding, beneficiation or smelting, which is the preparation process before beneficiation or smelting It is widely used in the basic industries of national economy such as metal ore beneficiation, metallurgy, chemical industry, building materials, coal, thermal power Ore Crushing SpringerLinkCFD MODELLING OF A STIRRED BEAD MILL FOR FINE GRINDING Graeme L LANE CSIRO Minerals, Box 312, Clayton Sth, Victoria 3169 AUSTRALIA a series of distinct mixing cells between the rotor discs It appears that material is drawn through the holes and redistributed between compartments, available ore bodies are increasingly finegrained andCFD MODELLING OF A STIRRED BEAD MILL FOR FINE GRINDING
.jpg)
How to operate an air classifier mill to meet your fine grinding
cyclone or filterreceiver when required This mill’s classifier wheel and impact rotor have independent drives, and the mill can handle the same grinding applications as the vertical mill Combined drive In this classifier mill, as shown in Figure 2b, the classifier wheel and rotor disc are mounted on one shaft and rotate at the same speed2015年3月10日 Within the scope of the study ore grinding performance of the vertical roller mill was investigated with mobile pilot plant In this context, chalcopyrite ore of a plant having rod and ball milling circuit was ground under different operating modes eg, air swept and overflow, and process conditions, then samples were collected around the systemCopper ore grinding in a mobile vertical roller mill pilot plantOverall, ball size and shape are important factors to consider when choosing a mill for ore grinding Singlestage ball mills are designed for grinding small quantities of a particular material They have one grinding chamber that holds the material to be ground and a rotating drum that does the grindingFactors affecting ores grinding performance in ball millsVideo credit: shsbjq / CC BYSA 40 Specifications Important specifications when selecting grinding mills and pulverizers include, The size of the mill can range from pilot/lab to production, eg, 35 to 1600 cu ft; Feed size, material, and Grinding Mills and Pulverizers Selection Guide:
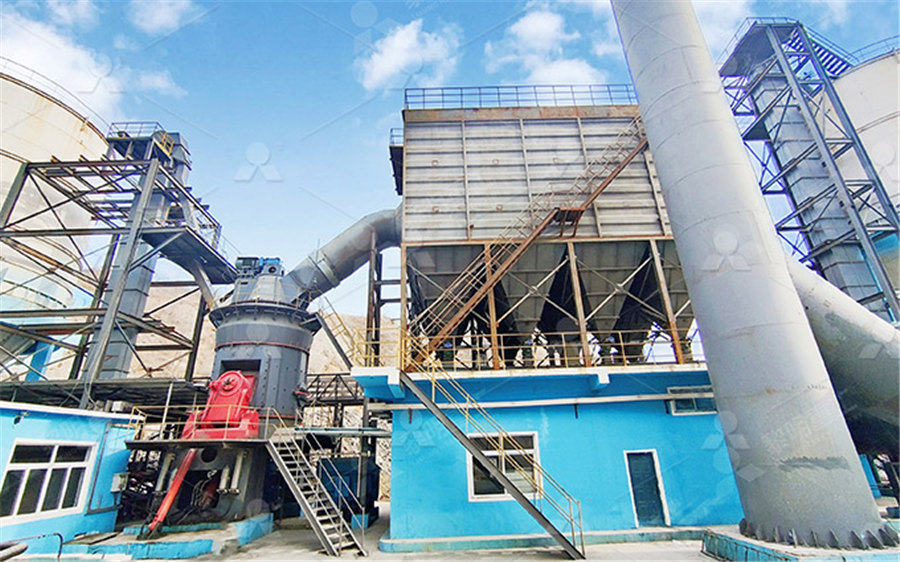
Copper Ore Grinding in a Mobile Vertical Roller Mill Pilot Plant
2014年10月1日 In a test performed in the Loesche test center in Germany, copper slag grinding saved 229% energy in an airswept model and 344% energy in an overflow model [13,14]– Cyclone Mill TWISTER 10 – Technical data 11 – Order data 12 Rotor Beater Mills – Applications 13 – Rotor Beater Mill SR 200 14 – Rotor Beater Mill SR 300 14 – Technical data 15 – Order data 16 Cross Beater Mills – Applications 17 – Cross Beater Mill SK 100 18 – Technical data 19 – Order data 20 Ultra Centrifugal MillsSize reduction with Rotor Mills Lab UnlimitedCarbon black is a light, loose and fine black powder that contains carbon substances It can be used as a black dye to make ink, paint, rubber material, etc Carbon black ultrafine mill is also called (threering fourring) mediumspeed ring roller microgrinding machine It adopts a graded continuous grinding method to grind the material Coarse Powder Grinding Mill SBM Ultrafine Powder TechnologyA crushing plant delivered ore to a wet grinding mill for further size reduction The size of crushed ore (F 80) was 40 mm and the SG 28 t/m 3 The work index of the ore was determined as 122 kWh/t A wet ball mill 1 m × 1 m was chosen to grind the ore down to 200 micronsGrinding Mill an overview ScienceDirect Topics
.jpg)
impact crusher rotor assembly Mining Quarry Plant
2013年4月18日 Rotor,Crusher Rotor,Impact Crusher Rotor, Hammer crusher assembly of crusher hammers on rotor,Ore Crusher,Grinding mill equipment,Crusher plant Impact crushers – Patent # – PatentGenius2024年10月30日 Ore is a deposit in Earth’s crust of one or more valuable mineralsThe most valuable ore deposits contain metals crucial to industry and trade, like copper, gold, and iron Copper ore is mined for a variety of industrial uses Copper, an excellent conductor of electricity, is used as electrical wire Copper is also used in constructionOre National Geographic Societya)Single rotor to 15:1 b)Double rotor to 15:1 c)Hammer mill to 20:1 Speciality crushers a)Rod mill b)Ball mill The reduction ratio is defined as the representative feed size by representative product size The sizes are usually defined as the 80% passing size of the cumulative size distributionCERAMIC MATERIALS I2022年8月31日 Dear Colleagues, The grinding process, as a primary stage of ore/raw material processing, is a necessary operation in beneficiation plants It not only provides the appropriate particle size for subsequent separation Grinding Modeling and Energy Efficiency in Ore/Raw
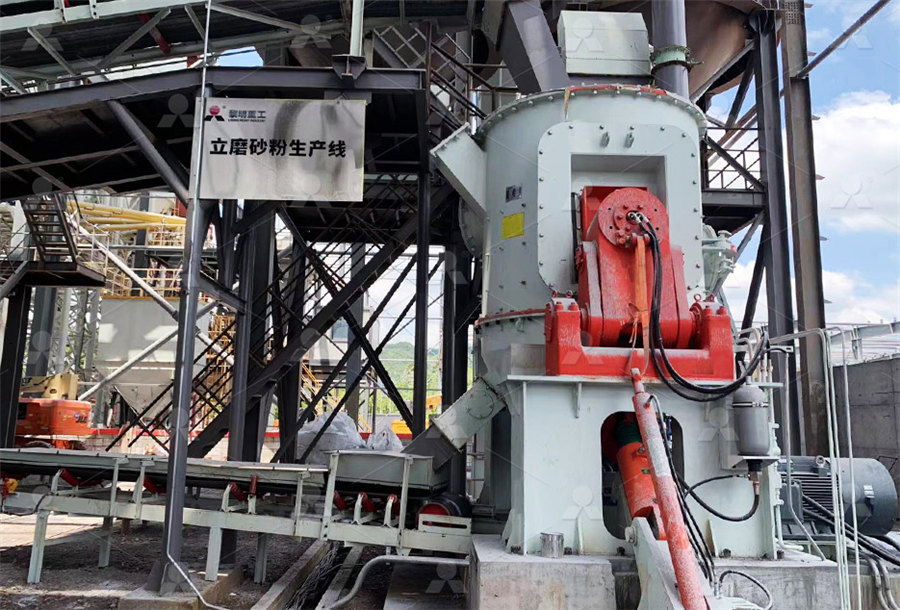
(PDF) Grinding Media in Ball MillsA Review
2023年4月23日 grinding media in a grinding mill with about 2630 wt% chrome by Chen et al [37] using a phosphate ore in a modified ball laboratory ball mill whose electrochemical potential could be controlledThe grinding material is comminuted in the Loesche roller grinding mill between the rotating horizontal The bar caged with bar rotor and variablespeed drive is mounted on the mill The hydraulic swingingout device for the roller simplifies and speeds up maintenanceLoesche Mills for industrial mineralsSAG MILL TESTING AN OVERVIEW OF THE TEST PROCEDURES AVAILABLE TO CHARACTERIZE ORE GRINDABILITY AUTHOR: FO VERRET, G CHIASSON AND A MCKEN SGS KEYWORDS Comminution, grindability, grinding, SAG mill, AG mill, milling, HPGR, work index, pilot plant INTRODUCTION The resistance of ore samples to breakage (or hardness) is SAG Mill Testing Test Procedures to Characterize Ore 2016年3月11日 The screen bypasses any material fine enough to enter the grinding section and delivers the oversize to a cone crusher, the discharge of which joins the undersize of the screen and is taken by a belt conveyor to the fine ore bin ahead of the grinding section The fine ore bin can be designed to hold two days’ supply of ore, but the coarse Crushing Plant Flowsheet DesignLayout 911Metallurgist
.jpg)
Ultra Centrifugal Mill ZM 200 Thomas Scientific
The ZM 200 UltraCentrifugal Grinding Mill rapidly reduces soft to mediumhard and fibrous materials to analytical sample size Grinding takes place by impact and shearing action between the rotor and the fixed ring sleeve Feed material passes through the funnel with splashback protection onto the rotorFind your rotor mill easily amongst the 280 products from the leading brands (WAMGROUP, IKA, Fritsch Unique grinding chamber geometry The sample material is comminuted according to the cutting principle of scissors between the cutting edges of the rotor and the fixed into the grinding chamber of the rotor mill through the feed hopperRotor mill, Rotor lump breaker All industrial manufacturersgrinding of SAG mill discharge, which enables open circuit SAG milling Fig 1 Number of HPGR in service in various mineral processing by years: 1 — diamond ore; 2 — iron ore; 3 — hard rocks Fig 2 Standard fine crushing with HPGR: 1 — medium crusher; 2 — HPGR; 3 — ball mill The number of operated HPGR, unit YearsHIGH PRESSURE GRINDING ROLLS—A PROMISING AND COST