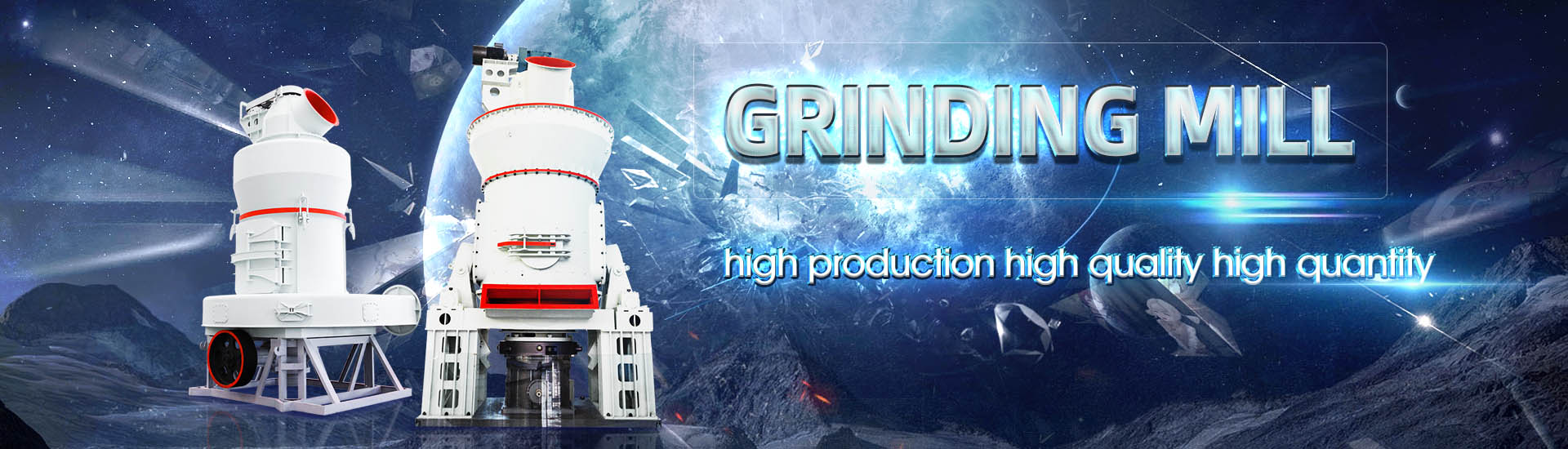
HOME→Grinding mill particle size analysis Grinding mill particle size analysis Grinding mill particle size analysis
Grinding mill particle size analysis Grinding mill particle size analysis Grinding mill particle size analysis
.jpg)
Effect of Solid Concentration on Particle Size
2024年6月11日 In this work, the purpose of this study was to investigate the effect of the solid concentration of stirred mills on the product size distribution of the grinding product The particle size distribution of the feed was divided into 2018年6月1日 In this article the effect of grinding media size distribution and feed material particle size distribution (PSD) on the product fineness requirements were investigated A Effect of ball and feed particle size distribution on the milling 2020年10月1日 In this paper, we report on a detailed experimental analysis of the longterm grinding behavior of silica sand as a model material in an oscillatory ball mill for a broad range Evolution of grinding energy and particle size during dry ball Abstract: Grinding is a process where the particle size of the material is reduced under the combined effects of the impact action and the abrasion action of steel balls (grinding medium) Research on the characteristics of particles size for grinding
.jpg)
MILLING ANALYSIS OF PARTICLES AUTUMN 2010 ETH Zürich
The changing particle size distribution of the milled good as a function of time is most easy to characterize qualitatively if the material has initially only one particle size At the start of milling 2024年10月8日 This comprehensive review delves into six crucial facets, offering a systematic appraisal: (1) the statistical framework and evaluation methodologies for characterizing particle A Comprehensive Review on Evolution Behavior of Particle Size 2024年6月26日 The statistical design of experiments was used to predict particle deformation in stirred media mill in terms of grinding media size and impeller rotational speedEffect of Milling Variables on Particle Deformation in a Stirred 2021年8月10日 The most relevant results were compared for the weight percentage for each size (WPES), cumulative weight undersize (CWU), or the use of particle size distribution models (PSDM), in terms of continuous Experimental Uncertainty Analysis for the Particle Size
.jpg)
AP42, Appendix B2 Generalized Particle Size Distributions
B21 Rationale For Developing Generalized Particle Size Distributions Coal fired a Impact mill 4 115 Refractory manufacturing Flash calciner a Bauxite grinding 4 1214 Secondary zinc processing 8 Aluminum hydroxide calcining 5 1215 Storage battery production b2020年1月3日 22 Grinding Studies Two kinds of mills, BBM and LBM, were used to achieve the desired P 80 passing percentage of 150 μm with an acceptable range of hematite liberation (> 75%) at optimum grinding time The BBM is a standard ball mill having a length and diameter of 300 mm × 300 mm with smooth liner as shown in Fig 2A rotating drum is attached to a Estimation of Grinding Time for Desired Particle Size Distribution The particle size distribution of the two minerals achieved through lowspeed grinding, relative grindability at different feed sizes, and the grinding kinetics analysis of lowspeed grinding are compared in this paper The difference in grinding characteristics between the two minerals is studied, and the grinding mechanism of the mill byResearch on the characteristics of particles size for grinding 2012年6月1日 Besides particle size reduction, A simple analysis and comparison between the massbalance model given by (5) approach is most frequently used in ball mill grinding circuitsGrinding in Ball Mills: Modeling and Process Control
.jpg)
MODELING OF SIZE REDUCTION, PARTICLE SIZE ANALYSIS AND
Fig 2 (a) Pin mill have a higher energy input than that for hammer mill and can generally grind softer materials to a finer particle size than that of hammer mill, while hammer mill performs better on hard or coarse materials [4] The pin mill used in the study is shown in Fig 2 (b), which was2019年10月1日 The efficiency of reduction of the particle size of the raw material during grinding depends on a number of variables, including the type of mill, the number of revolutions of the mill, the size Wet and dry grinding of coal in a laboratoryscale ball mill: Particle 2016年7月8日 UNTIL THE THIRD THEORY OF COMMINUTION of “Work Index” method of determining crushing and grinding mill size was introduced, there was no way of accurately figuring the most applicable, most economical size of crushing and grinding mill Naturally, with little or no factual operating data correlated in useful form, it was easy enough, even for the Equipment Sizing: Crusher or Grinding Mill 911MetallurgistEFFECT OF PARTICLE SIZE DISTRIBUTION ON GRINDING KINETICS IN DRY AND WET BALL MILLING OPERATIONS Figure 4 Variation of breakage distribution parameters with grinding time for Set1 data on wet EFFECT OF PARTICLE SIZE DISTRIBUTION ON GRINDING KINETICS IN
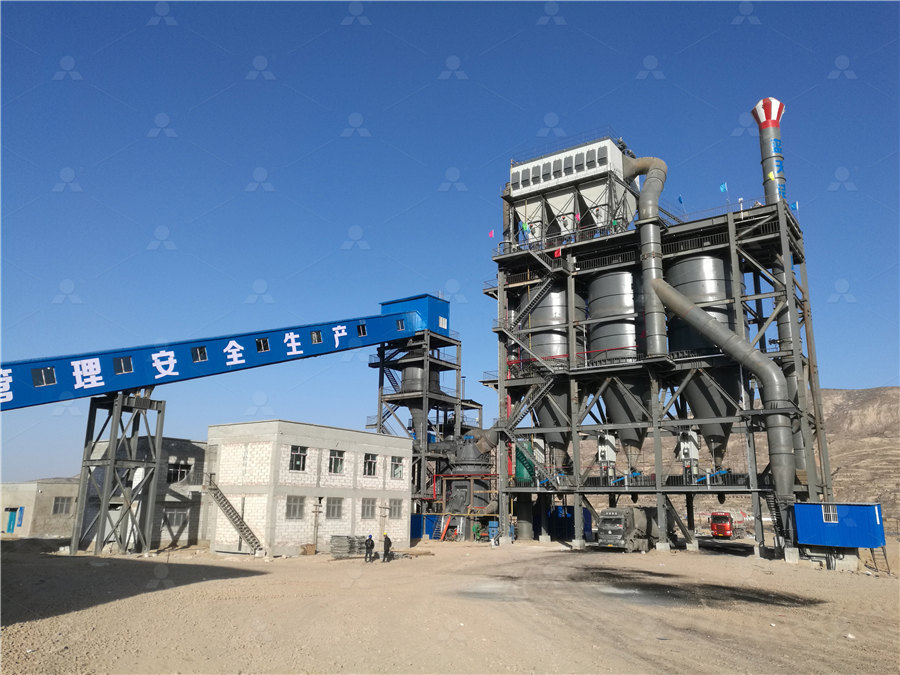
Grinding Mills for reliable size reduction tasks RETSCH
For sample preparation, Retsch's innovative and reliable grinding solutions can accommodate a broad spectrum of materials and applications When selecting a grinding mill, it's essential to define the intended use, the type of material to be processed, and the desired final particle size to ensure optimal resultsIn this context, the term average size depends on the method of measurement In the industry, screening or sieving is widely used to evaluate particle size distribution in granular materials and powders In case of coarse crushing the size reduction ratios is below 8:1 and in fine grinding it is more than 100:1Size Reduction1: Grinding – Unit Operations in Food Processing2020年1月1日 Wet and dry grinding of coal in a laboratoryscale ball mill: Particlesize distributions Author links open overlay panel Xiangning Bu a, Yuran Chen a Inner Mongolia, China) A narrow size fraction of −30 + 10 mm with a 758% ash was used for the grinding tests XRD analysis (Bruker D8 Advance, Karlsruhe, Germany) indicated Wet and dry grinding of coal in a laboratoryscale ball mill: Particle 2016年3月1日 Cone and quarter method of sampling was used to derive representative samples for MS tests An optimum grinding time of 16 min of ball milling and 1 and 15 min of GyRo milling were chosen for lignite and hard coal considering the amount of size fraction less than 300 μm for DIA testsThe GyRo mill used in the study (Fig 1) is a laboratory equipment (original name: Particle size distribution modeling of milled coals by dynamic
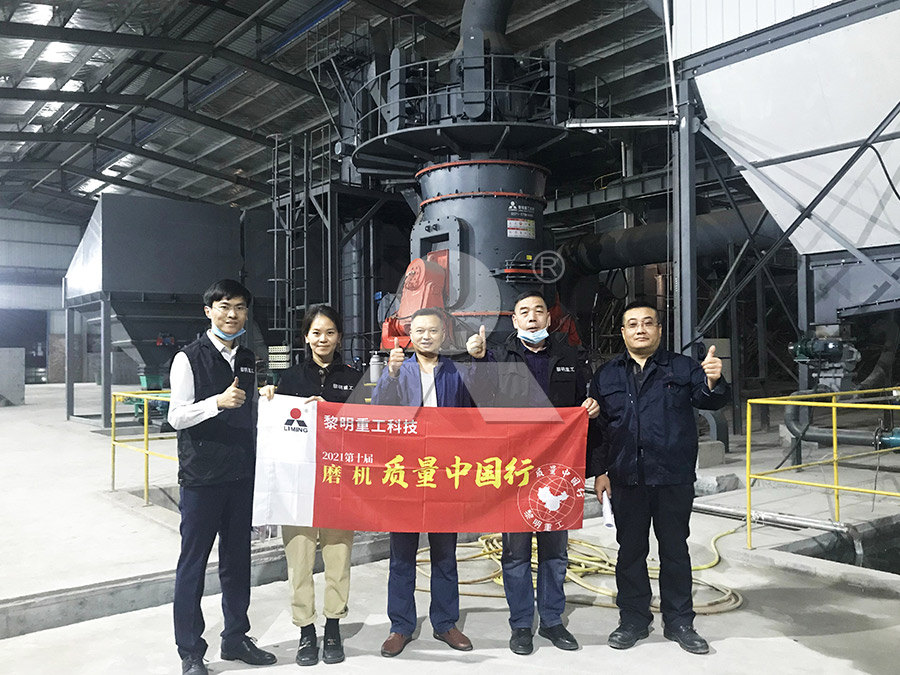
Sieve Analysis Determine Grain Size Distribution Free Guide
Particle Size Analysis Methods: Typical Particle Size Rangers: Sieve Analysis: Dry sieving; Wet sieving; Air jet sieving; 40 μm—125 mm 20 μm—20 mm 10 μm—02 mm: Static Image Analysis (SIA) 05 μm—15 mm: Dynamic Image Analysis (DIA) 1 μm—30 mm: Static Light Scattering (SLS) or Laser Diffraction (LD)Particle Size Analysis Techniques 15 LA960V2 laser diffraction technique The importance of optical model Building a state of the art laser diffraction analyzer 18 LA350 laser diffraction technique Compact optical bench and circulation pump in one system 19 ViewSizer 3000 nanotracking analysisA GUIDEBOOK TO PARTICLE SIZE ANALYSIS University of IowaThe analysis of the particle shape also plays a key role in particle size analysis for the product development of coffee and for the development of coffee grinders and grinding machines Dynamic image analysis with QICPIC and dry disperser RODOS records around 1 million particles within one minute and thus provides excellent statistical reliability of the Coffee Particle Size and Shape Analysis Sympatecparticle size reduction is the result of both chipping and fragmentation in the mill [4] Grinding conditions in the spiral jet mill have been extensively studied, with the consensus agreeing that particle feed rate and grinding pressure are the two most influential parameters [1,5–9] In general, increasing theAnalysis of holdup and grinding pressure in a spiral jet mill
.jpg)
Grinding Mill an overview ScienceDirect Topics
The mean residence time of solid in the bed is typically a few minutes to 30 minutes or more depending on the desired degree of size reduction A detailed analysis of ball mill operations, the major variables and their effect on performance is given by Austin et al (1984) A brief overview is presented by Austin and Trass (1997)The P80 passing for all three iron ore samples was 96 μm at 14 min, 87 μm at 11 min, and 75 μm at 10 min Fig 8 Particle size analysis for LSHA product sample Fig 9 Particle size analysis for LSLA product sample Hence, the retention time of the LBM was further reduced to obtain the desirable P80 passing of 150μm particles(PDF) Estimation of Grinding Time for Desired Particle Size 2018年2月1日 Feed size was divided into two fractions of (+238 −4) and (+2 −238) millimeters, from which different feeds with different weight and size percent values were fed to mill at three feeds of Effect of ball and feed particle size distribution on the milling 2011年1月31日 The specific steps are as follows: 1 According to the particle size to be used for screening analysis of grinding test products, calculate the multiple xx of each particle size relative to each Influence of dry and wet grinding conditions on fineness and
R)8OC`6F[ZIB.jpg)
Particle Size Reduction Kansas State University
more maintenance time and frequent particle size analysis Figure 3 Roller mill (from Heimann, 1999) 01g) Figure 4 Roller configuration for roller mills (from Heimann, 1999) Monitoring and Testing Particle Size Sample collection Daily grab sampling should be performed to visually assess particle size looking for evidence of1 examining the particle size reduction of coarse clayey samples using primary, secondary crushing and grinding methods and 2 subsequent separation and size analysis of the obtained polydispersed powders Materials and Equipment 1 Silica sand 2 Balance 3 Sieves 4 Mechanical sieve shaker 5 Oven 6 Mortar and pestle 7 Ball mill 8Lab 3 – Particle Size Reduction, Screening and Size Analysis2018年7月23日 Critical check point in Grinding Particle Size and Distribution; Both particle size and particle size distribution are important for animal performance and feed mill productivity The research data recommend to have Art of GrindingParticle size reduction Benison MediaIf your processes require particle size reduction machinery, rely on particle size reduction equipment from Prater to do the job right Request a Quote (877) 2475625; Contact Us ; Products Our Mega Mill Hammer Mill provides uniform grinding with less heat buildup, Particle Size Reduction Solutions Prater Industries
.jpg)
Particle Size Analysis in Pharmaceutics: Principles, Methods
2006年12月27日 Abstract Physicochemical and biopharmaceutical properties of drug substances and dosage forms can be highly affected by the particle size, a critical process parameter in pharmaceutical production The fundamental issue with particle size analysis is the variety of equivalent particle diameters generated by different methods, which is largely Abstract: An effect of a grinding method, that is ball mill and high pressure grinding rolls (HPGR), on the particle size, specific surface area and particle shape of an iron ore concentrate was Investigation on the particle size and shape of iron ore pellet feed Effect of ball and feed particle size distribution on the milling efficiency of a ball mill: An attainable region approach N Hlabangana a, G Danha b, *, E Muzenda b a Department of Chemical Engineering, National University of Science and Technology, P O Box AC 939, Ascot Bulawayo, Zimbabwe b Department of Chemical, Materials and Metallurgical Engineering, College of Effect of ball and feed particle size distribution on the milling Keywords: HPGR, ball mill, particle size, particle shape, image analysis, SEM Introduction Particle size and shape are important parameters that can significantly affect mineral processing plants and pelletizing plant performances (Brozek and Surowiak, 2007) For example, using finer particles (with a certain size) in magnetic separation couldInvestigation on the particle size and shape of iron ore pellet feed
.jpg)
The Vertical Mill Slag MicroPowders' Particle Size Distribution
In this paper, through the industry vertical mill grinding GGBS carried out a detailed analysis of particle size, on this basis, using the attached to the sample preparation method, obtained the differences between hammermill and roller mill ground corn Hammermill: Particle size = 841 µm; std deviation (sgw) = 2449 841 µm ÷ 2449 = 343 µm 841 µm × 2449 = 2,060 µm Thus, 67% of the material would be between 343 and 2,060 µm Roller mill: Particle size = 841 µm; std deviation (sgw) = 2134 841 µm ÷ 2134 = 394 µmGrinding considerations when pelleting livestock feeds2015年3月1日 Wet grinding of CaCO 3 with a stirred media mill: Influence of obtained particle size distributions on pressure filtration properties Author links open overlay panel Teemu Kinnarinen a , Ritva Tuunila a , Mikko Huhtanen a , Antti Wet grinding of CaCO3 with a stirred media mill: Influence of 2014年12月25日 Comparative study using RosinRammlerSperlingBennet (RRSB) and RosinRammler model parameters, including particle size analysis and flow characterization helps in identifying whether hammer mill MODELING OF SIZE REDUCTION, PARTICLE SIZE
.jpg)
(PDF) Effects of Ball Size Distribution and Mill Speed and Their
2020年7月2日 The main goals of this study were to solve this problem by adjusting operating condition so that (a) hydrocyclone overflow particle size can be increased from 942 µm to 100 µm and (b) increase 2022年1月1日 Stirred mills have been wildly used in mineral processing, chemical products, and other industries due to their higher tip speed, higher filling rate, and smaller media size etc, especially in particle size of ground products below 100 µm (Heath et al, 2017, Jankovic, 2003, Tang et al, 2022)The main evaluation of stirred mill performance includes four aspects: time Effect of operating conditions on the particle size distribution and 2023年4月23日 Grinding is the final stage of comminution, which reduces particle size to micron size level The size re duction is achieved by attrition, abrasion, and impact between the ore itself and between (PDF) Grinding Media in Ball MillsA Review ResearchGateEstimation of Grinding Time for Desired Particle Size Distribution and for Hematite Liberation Based on Ore Retention Time in the Mill Harish Hanumanthappa1 Harsha Vardhan1 Govinda Raj Mandela1 Marutiram Kaza2 Rameshwar Sah2 Bharath Kumar Shanmugam1 Received: 27 August 2019 /Accepted: 16 December 2019Estimation of Grinding Time for Desired Particle Size Distribution
.jpg)
Particle Size Analysis in Pharmaceutics: Principles, Methods
2007年3月1日 This review offers an indepth discussion on particle size analysis pertaining to specific pharmaceutical applications and regulatory aspects, fundamental principles and terminology 2014年3月1日 An analysis of the kinetics of dolomite grinding in a dry ball mill reveals that the following approximations apply for the parameters of the batch grinding model: the size discretized selection (PDF) Analysis of ball mill grinding operation using mill power Grinding Mills: Ball Mill Rod Mill Design PartsCommon types of grinding mills include Ball Mills and Rod Mills This includes all rotating mills with heavy grinding media loads This article focuses on ball and rod mills excluding SAG and AG mills Although their concepts are very similar, they are not discussed herePhotographs of a glass ended laboratory ball mill show Grinding Mills 911Metallurgist2022年5月20日 Where d GM is the grinding media particle size diameter, ρ GM is the grinding media density, and v t is the tip speed of the stirrer in the mill (Kwade 2003) Although this model does not consider process parameters to estimate product quality, it was shown to work on hard inorganic materials (Kwade and Schwedes 2002)Mechanical ParticleSize Reduction Techniques SpringerLink