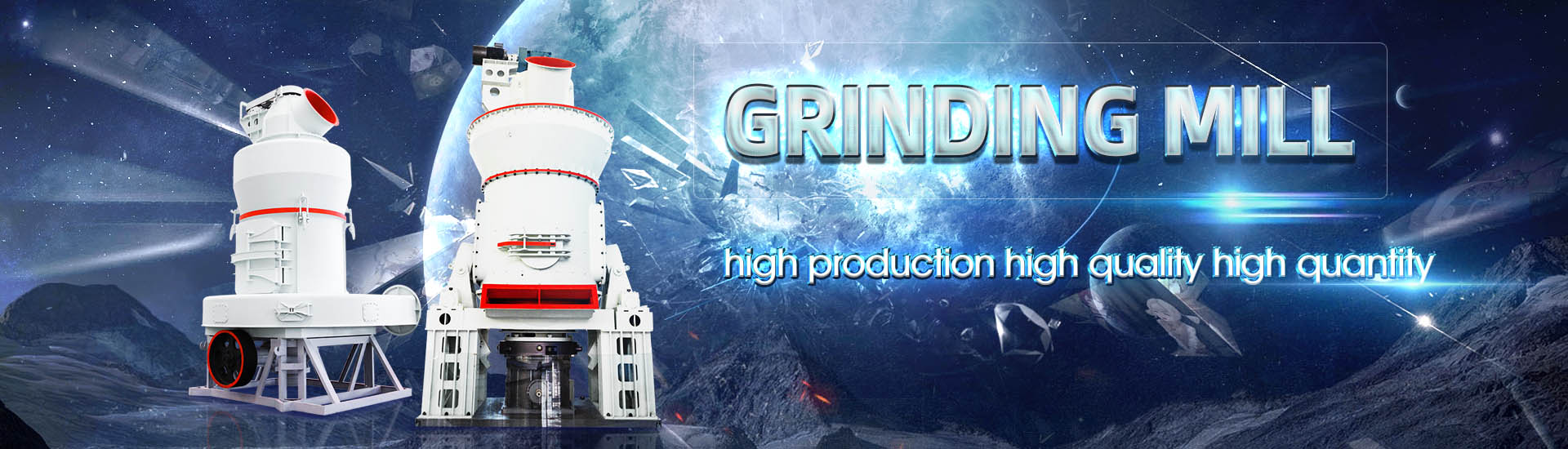
Ore mill dust particle size
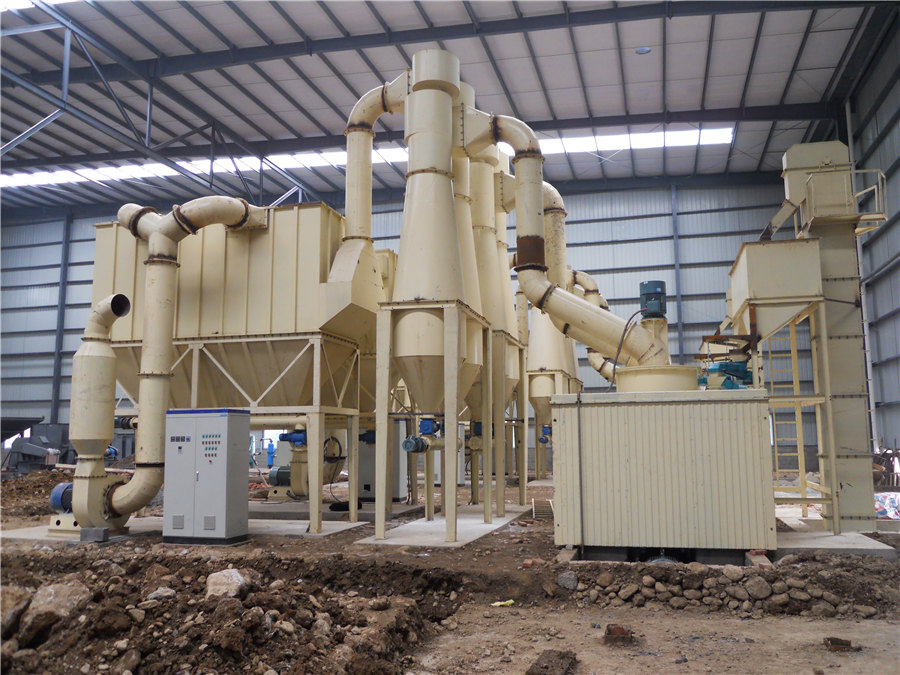
AN ASSESSMENT OF DUST GENERATION FROM ORES University
Particle size analysis of the produced dust fractions were found to be material dependent and varied considerably for the different ores Almost all materials produced significant amounts of 2017年9月1日 The objective of this work is to assess the influence of fine grinding in ball mills and stirred mills on valuable mineral liberation and particle shape characteristics of UG2 ore, a Fine grinding: How mill type affects particle shape characteristics 2024年4月1日 The microscopic features of ore powders, ie, wetting time, contact angle, particle size, specific surface area and pore structure, as well as microscopic morphology, are also Characterization of dust emission during ore unloading and 2022年12月6日 Results showed that Fe in iron ores was positively and significantly related to PCB 114 formation in dust and confirmed its cocatalytic effect on dioxin formation Concentrations of Al, Ti andInfluence of iron ore properties on dioxin emissions
.jpg)
An assessment of dust generation from ores
2006年5月1日 Particle size analysis of the produced dust fractions were found to be material dependent and varied considerably for the different ores Almost all materials produced significant amounts ofIn this article, alternative forms of optimizing the milling ef ciency of a laboratory scale ball mill by fi varying the grinding media size distribution and the feed material particle size distribution Effect of ball and feed particle size distribution on the milling 2020年1月1日 In this work the ore particle size distribution is estimated from an input image of the ore The normalized weight of ore in each of 10 size classes is reported with good Estimating Ore Particle Size Distribution using a Deep 2020年1月3日 Ball mills are progressively used to grind the ores for particle size reduction and to liberate valuable minerals from the ores The grinding of ore is a highly energyintensive Estimation of Grinding Time for Desired Particle Size Distribution
.jpg)
Research on Grinding Characteristics and Comparison
2022年10月26日 Through the JK dropweight test, the batch grinding test, and the populationbalance kinetic model of grinding with the Simulink platform, the grinding characteristics of the two types of ores and the particlesize 2023年7月20日 According to the different grinding medium, the grinding mill is divided into three types: (1) ball mill – it is used widely, and almost all materials can be triturated by ball mill; (2) rod mill – its efficiency is relatively high with the feeding particle size less than 30 mm and the product particle size around 3 mm, and the produced product particle size is uniform with less Ore Grinding SpringerLinkB21 Rationale For Developing Generalized Particle Size Distributions Gas fired a Rotary ore dryer a Oil fired a Roller mill 4 Coal fired a Impact mill 4 Horizontal Soderberg a 132 Fugitive dust a 122 Coke manufacturing a 123 Primary copper smelting aAP42, Appendix B2 Generalized Particle Size Distributions2019年1月1日 This effect is well illustrated by a series of experiments on the grinding of coal in a small mill, carried out by Heywood 1 The results are shown in Fig 51, in which the distribution of particle size in the product is shown as a function of the number of revolutions of the millParticle Size Reduction and Enlargement ScienceDirect
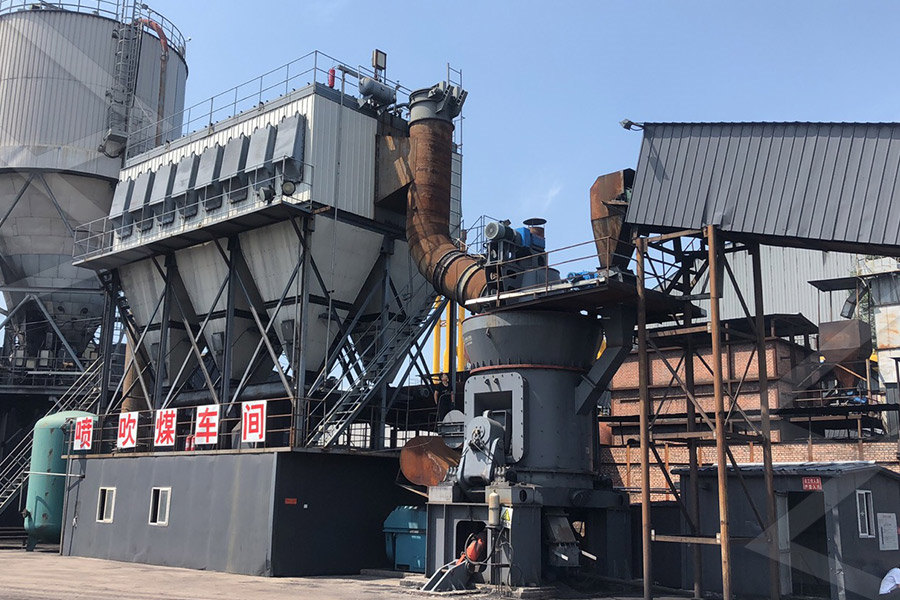
Study of the Technology for Gold Recovery from GravityFlotation
2022年6月13日 Goldcontaining ore processing technology has been developed by using chemical, Xray phase, mineralogical, Xray fluorescence analyses The results of experiments on the gold recovery from a concentrate with a particle size of 10 and 4 µm are presented, including options for direct cyanidation without preliminary oxygen oxidation, as well as with the use of 2024年4月26日 The crushed ore obtained from the crushing stage is typically in larger size fractions and needs to be further processed through screening 2 Screening Screening is the process of separating the crushed ore into various size fractions It involves passing the crushed ore through a series of screens with differentsized openingsIron Ore Processing: From Extraction to ManufacturingIn the paint and pigment industries particle size influences appearance properties including gloss and tinctorial strength Particle size of the cocoa powder used in chocolate affects color and flavor The size and shape of the glass beads used in highway paint impacts reflectivity Cement particle size influences hydration rate strengthA GUIDEBOOK TO PARTICLE SIZE ANALYSIS University of IowaThe shape of crushed ore affects the product particle size in a ball mill grinding circuit It has also been proposed that green pellet quality is directly related to the amount of fine particles in a pelletizing plant (Dwarapudi et al, 2008; Umadevi et al, 2008; Gul et al, 2014; Van der Meer, 2015) Particle size distributionInvestigation on the particle size and shape of iron ore pellet feed
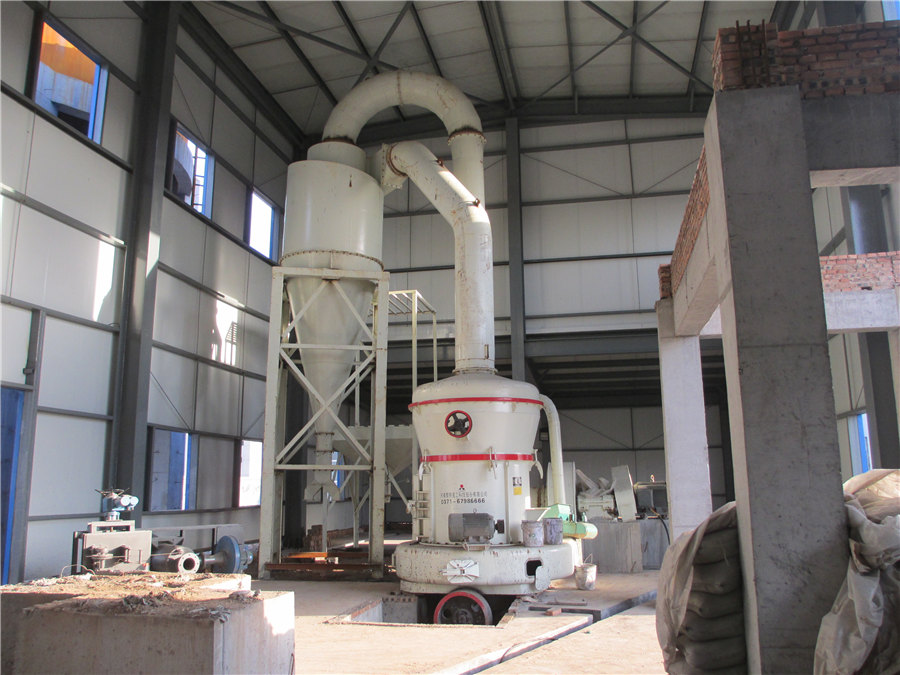
Investigation on the particle size and shape of iron ore pellet
2014年4月19日 DOI: 105277/PPMP Corpus ID: ; Investigation on the particle size and shape of iron ore pellet feed using ball mill and HPGR grinding methods @article{Abazarpoor2014InvestigationOT, title={Investigation on the particle size and shape of iron ore pellet feed using ball mill and HPGR grinding methods}, author={Armin Abazarpoor Single crystals of SFCAII with composition Ca 246 Fe 3+ 857 Fe 2+ 052 Al 545 O 24 have been obtained from synthesis experiments in the temperature range between 1300 and 1200°CParticle size distribution analysis of iron ores/% ResearchGatePDF On Nov 15, 2019, B Foggiatto and others published Material handling and flowsheet selection considerations for particlebased ore sorting Find, read and cite all the research you need on Material handling and flowsheet selection considerations for particle Demonstrate understanding of various method involved in measuring particle size Explain the importance of particle size analysis and its application AMIT 129: Lesson 12 Crusher and Mill Operation Safety; AMIT 129: Lesson 13 AMIT 135: Lesson 3 Particle Size Distribution –
.jpg)
Estimation of Grinding Time for Desired Particle Size Distribution
intensive process [1–4] In this process, the size of the particle obtained depends on the energy consumption of the ball mill The major challenge encountered in the process of iron ore grinding is to maintain the desired product particle size distribution (PSD) with sufficient liberation of valuable minerals The demand for desired•A dose conversion factor (mSv/unit intake) can be estimated for ore dust based on –particle size distribution of the dust (a standard default assumption is an AMAD of 5 μm); –The chemical form of each radionuclide in the dust determines the lung absorption type, a conservative approach of using the highest DCF can be usedExposure Pathways Long Lived Radioactive Dust (LLRD) Nucleus2023年11月30日 Pollen grains vary in size from approximately 10100 microns, placing them in the fine to coarse dust particle range The size of pollen grains depends on the plant species; for instance, ragweed pollen tends to be larger than grass Dust Particle Sizes: From Invisible to Significant2022年1月11日 ABSTRACT Resuspension of iron ore dust presents a constant hazard in the working environment within steel production plants Herein, the optimal operating parameters for maximum dust suppression efficiencies through a water mist generator and a conventional sprinkler for particulate matter (PM) originating from an iron ore pile measuring about 2 m in Suppression Efficiency for Dust from an Iron Ore Pile Using a
.jpg)
Effect of Particle Size and Grinding Time on Gold Dissolution in
2016年7月7日 A series of tests were performed in a laboratory ball mill using (i) three loads of single size media, ie, 40, 254, Ore with particle size of 2–5 mm was most suitable for column 2012年4月1日 The chemical analysis of mill scale is carried out using Xray fluorescence (XRF), and mill scale particle size and dispersion of mill scale is analysed by scanning electron microscope (SEM)Recycling of steel plant mill scale via iron ore sintering plant2015年8月21日 Particle Size Distribution Analyses are just one of the many services offeredA Particle Size Distribution Analysis (PSD) is a measurement designed to determine and report information about the (PDF) Particle size analysis and distribution ResearchGate2013年8月3日 In Grinding, selecting (calculate) the correct or optimum ball size that allows for the best and optimum/ideal or target grind size to be achieved by your ball mill is an important thing for a Mineral Processing Engineer AKA Metallurgist to do Often, the ball used in ball mills is oversize “just in case” Well, this safety factor can cost you much in recovery and/or mill liner Calculate and Select Ball Mill Ball Size for Optimum Grinding
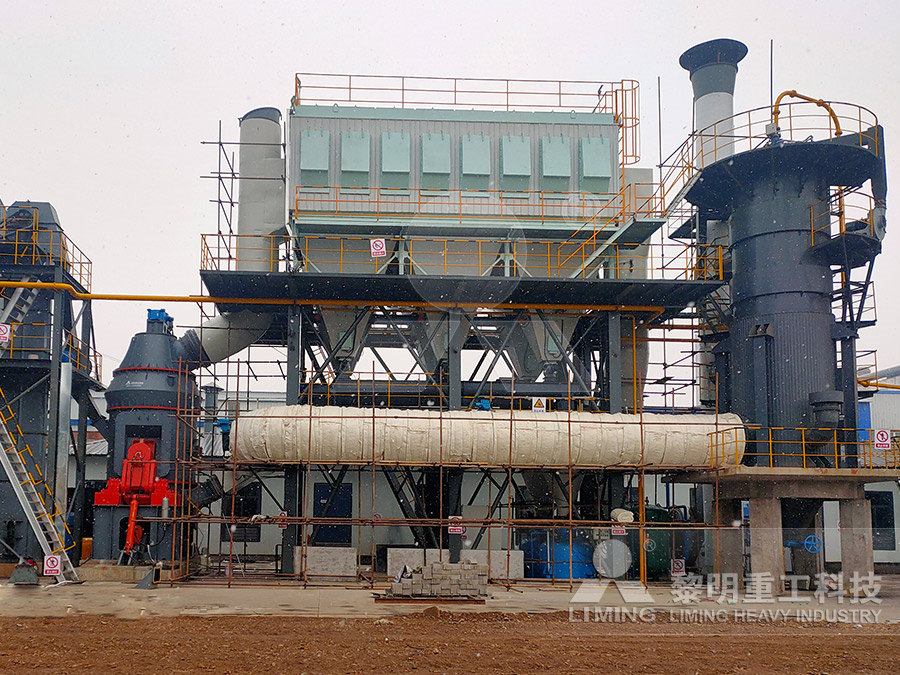
Estimating Respirable Dust Exposure from Inhalable Dust Exposure
Smaller particles are able to reach the gasexchange region of the lungs and form the respirable dust fraction In words of particle size, the limit for entering the alveolar region is between 10 and 15 µm (WHO, 1999; metal/metal ores/slag/metallic shot (n = 5069) lacquers/paint (n = 108) electronic waste (n = 92) Group C: fiberdominated2017年2月1日 HPGR effect on the particle size and shape of iron ore pellet feed using inhalable dust in a the disaggregation method with the sieve size 0045 mm or with Jar mill offered HPGR effect on the particle size and shape of iron ore 2018年6月1日 A number of researchers (Deniz, 2012; Bwalya et al, 2014; Petrakis et al, 2016) carried out studies about the effect of feed particle size and grinding media size on the grinding kinetics of different oresKhumalo et al, 2006 postulated that generally larger sized grinding media would break larger particles quicker but a finer product would be obtained by use of Effect of ball and feed particle size distribution on the milling 2017年9月1日 The shallow stirred mill PSDs with a coarse tail are possibly due to the media size being too fine to cause breakage of the top size ore particles It should be noted that, in continuous stirred milling devices with internal classification, a steeper particle size distribution would be expected (Ye et al, 2010)Fine grinding: How mill type affects particle shape characteristics
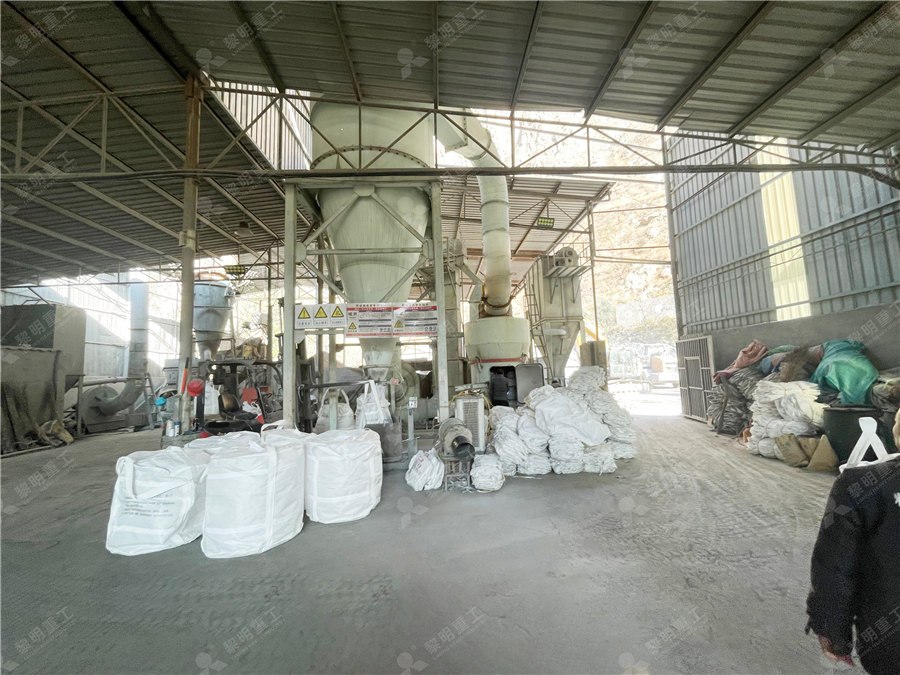
(PDF) Estimation of Grinding Time for Desired Particle Size
Comminution Characterization studies 1 Introduction Ball mills are progressively used to grind the ores for particle size reduction and to liberate valuable minerals from the ores The grinding of ore is a highly energyintensive process [1–4] In this process, the size of the particle obtained depends on the energy consumption of the ball mill2020年5月21日 There is significant iron deposition in the oceans, approximately 14–16 Tg annually from mineral dust aerosols, but only a small percentage (approx 3%) of it is soluble and, thus, bioavailable In this work, we examine the effect of mineralogy, particle size, and surface area on iron solubility in pure mineral phases to simulate atmospheric processing of mineral Mineral Dust and Iron Solubility: Effects of Composition, Particle Size 2024年2月8日 Many process industries, including the chemical, food, plastics, power, wood, metallurgical, agricultural and pharmaceutical industries, use mills to reduce the particle size of bulk solid materials Historical data points to milling and size reduction equipment as often being involved in combustible dust explosions in processing plantsReducing the risk of dust explosions in mills and size reduction 2022年10月31日 Considering that the ball mill had a lowball mill loading (10%) in contrast to standard ball milling (50%), the ball mill was used to simulate a semiautogenous grinding mill Figure 2Lithium deportment by size of a calcined spodumene ore
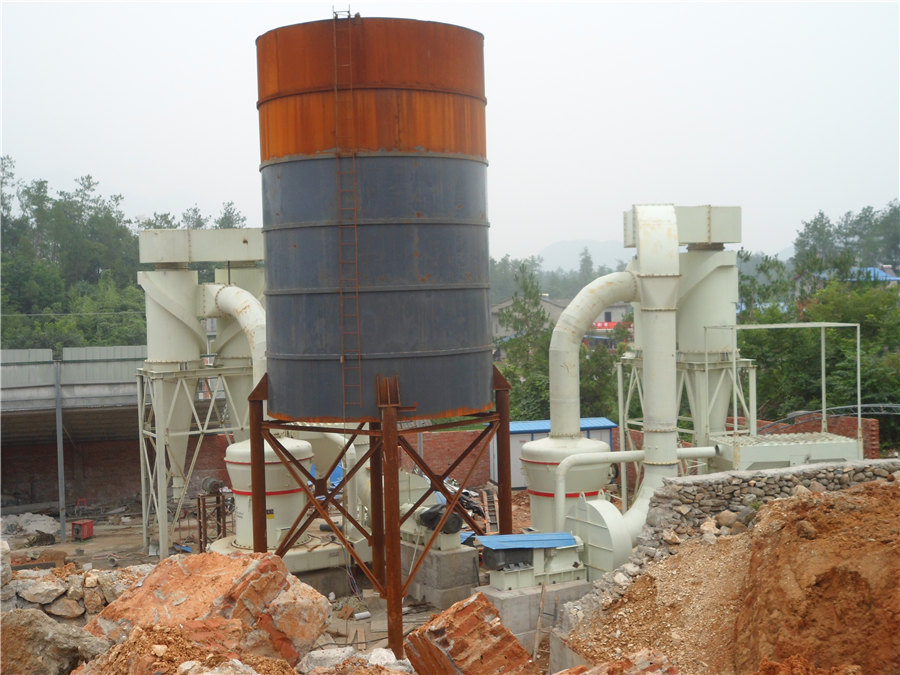
Characteristics of Iron Ore Pellets and their Influence on Dust
2015年5月12日 Moreover, the dust generated during wear experiments has been analyzed to obtain particle size distributions a) Typical iron ore pellets; b) dust particles observed on PTFE film filter Figures finished particle size is the screen Any material that enters the grinding chamber must be reduced to a size small enough to pass through the screen that covers the mill's discharge opening Because of this the screen size generally provides 70% or more of the control over the finished particle sizeIntro to Size Reduction Schutte HammermillPellet feed; HPGR; particle shape; particle size; image analysis; factorial design Introduction Iron ore pellet feed typically needs a size less than 106 µm after fine grinding Magnetic and HPGR effect on the particle size and shape of iron ore pellet feed An effect of a grinding method, that is ball mill and high pressure grinding rolls (HPGR), on the particle size, specific surface area and particle shape of an iron ore concentrate was studied The particle size distribution was meticulously examined Investigation on the particle size and shape of iron ore pellet
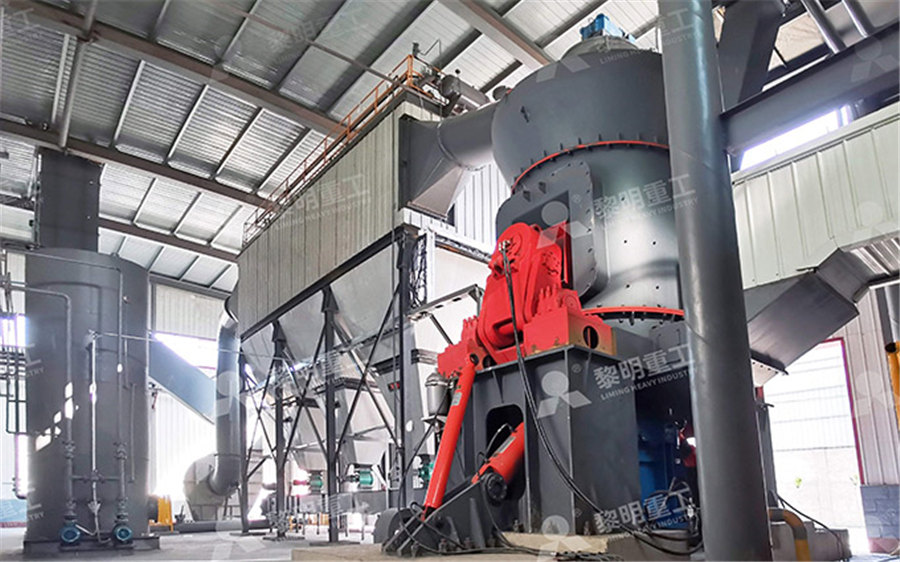
Rod Mills Grinding Mills DOVE
DOVE Rod Mill present an excellent replacement option, as it can grind the ore from 2030 mm particle size to 610 mesh, results in reduce operating cost, faster processing time and fine dust removalPrater’s Hammer Mills are widely used throughout a variety of industries for processing many different materials within a wide selection of particle reduction applications requiring high capacities, power efficiency, and uniform particle Particle Size Reduction Solutions Prater Industries2020年1月3日 Ball mills are progressively used to grind the ores for particle size reduction and to liberate valuable minerals from the ores The grinding of ore is a highly energyintensive process [1,2,3,4]In this process, the size of the particle obtained depends on the energy consumption of the ball millEstimation of Grinding Time for Desired Particle Size Distribution The efficiency of the mill to break ore is a function of both the feed size distribution and the relative hardness of the ore When the feed size of a SAG mill becomes coarser, ie α r increases Correlation Between F80 and Mill Performance for a SAG Mill
.jpg)
Effect of particles size range on iron ore flotation ResearchGate
2013年6月1日 Thus, it was established that Itakpe iron ore is best processed using PAX at pH 11 and particle size of 125 µm yielding concentrates assaying 6766% Fe2O3 at a recovery of ~90% while for Agbaja A new method, staged flotation for effectively increasing the recovery of ultrafine copper oxide ore with a new type of collector (ZH1, C35 carbon chain xanthate) is proposed for the first timeParticle size distribution (PSD) of the mill feed2013年7月30日 For a great presentation on How to Interpret Particle Size Distribution Data D50 D80 D90 and D10 you need to 911 Metallurgist is a trusted resource for practical insights, solutions, and support in mineral processing engineering, helping industry professionals succeed with proven expertise How to Interpret Particle Size Distribution DataHow to Interpret Particle Size Distribution Data2019年9月20日 The size fractions depend on the aerodynamic diameters of the dust particles and are classified based on the dust median particle size with \ Jönsson, PG: Evaluation of dust generation during mechanical wear of iron ore pellets ISIJ Intl 56(6), 960–966 (2016) Google ScholarTowards a theoretical understanding of dustiness