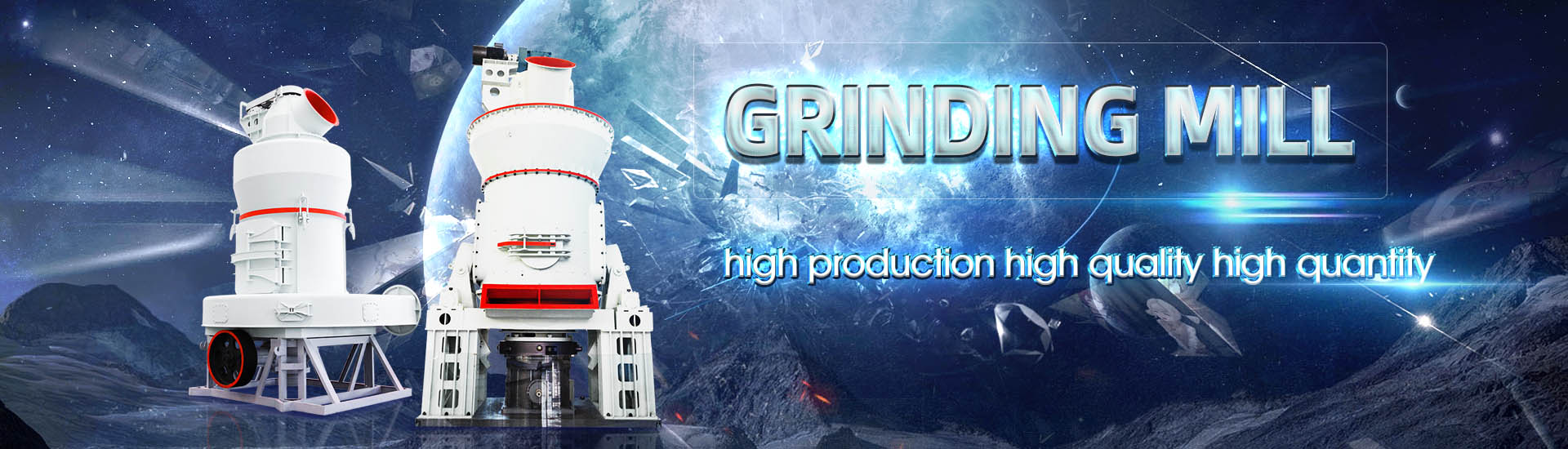
Powder grinding calcite ore dry separation process
.jpg)
Effective role of grinding aids in the dry grinding performance of
2023年8月1日 The usage of grinding aids prevents particle pelleting and leads to reduced energy consumption The work aims to research the impacts of three pure grinding aids from 2021年4月21日 The purpose of this study was to investigate the dry grindability of calcite powders in a vertically and horizontally orientable laboratory batch type stirred mill The The Influence of Stirred Mill Orientation on Calcite Grinding2024年3月15日 In arid and severely cold regions such as west China, a plenty of iron ores are difficult to be economically utilized due to water scarcity [1, 2], so that the utilization for such iron ores has an urgent demand for highefficient dry magnetic separation (DMS) technology [[3], [4], [5], [6]]A large portion of iron ores were currently processed in wet magnetic separation Development of a centrifugal dry magnetic separator for separation The results showed that, in the test of shaking table, when the grinding fineness was 0074mm 93%, the productivity of concentrate can reach 3224%; when grinding fineness was 0074mm 93%, after gravity concentrationmagnetic separation, 3025% of concentrate productivity can be attained; when the grinding fineness was 0074mm 85%, after gravity concentrationflotation, DRY MAGNETIC SEPARATION OF MAGNETITE ORES ScienceGate
.jpg)
Dry separation of particulate iron ore using density
2013年3月1日 Request PDF Dry separation of particulate iron ore using densitysegregation in a gas–solid fluidized bed A gas–solid fluidized bed has been used to separate particulate iron ore (+250 2021年1月19日 Moisture of bulk material has a significant impact on energetic efficiency of dry grinding, resultant particle size distribution and particle shape, and conditions of powder transport As a consequence, moisture needs to be measured or estimated (modelled) in many points This research investigates mutual relations between material moisture and particle classification MeasurementBased Modelling of Material Moisture and 2024年5月31日 This paper presents an industrial verification test, adding a high pressure grinding roll and magnetic separation operation after the thirdstage fine crushing operation to reduce the particle size of ball mill feed and improve the processing capacity of grinding operation The optimal process parameters of high pressure grinding roll and magnetic separation were High Pressure Grinding Roll and Magnetic Separation for Energy 2022年8月17日 Iron ore crushing process In the iron ore crushing process, the feeder, first crushing, secondary crushing, screening, fine crushing and dry selection are generally used For the sake of economy, generally the finer the ore particle size entering the dry separator, the higher the proportion of ironbearing ore that is dry selectedIron ore crushing equipment and process flow
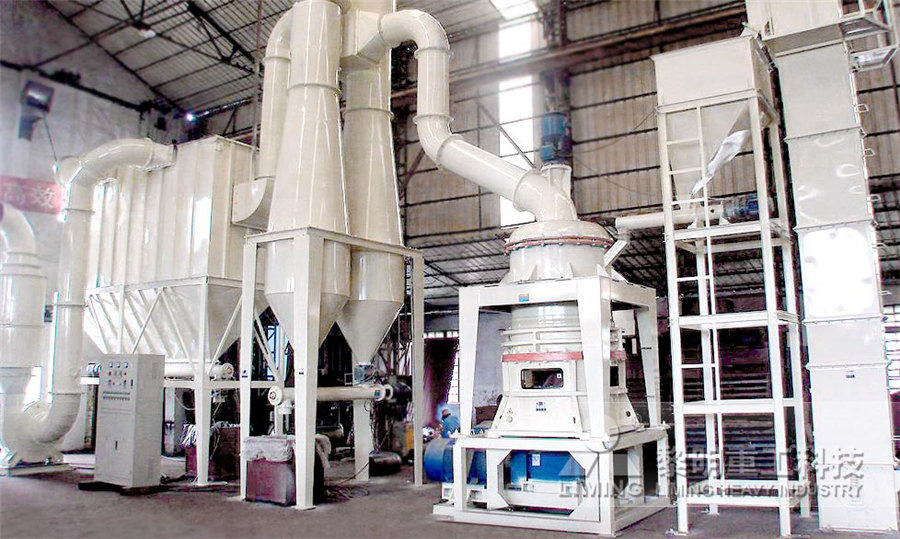
The six main steps of iron ore processing Multotec
When iron ore is extracted from a mine, it must undergo several processing stages Six steps to process iron ore 1 Screening We recommend that you begin by screening the iron ore to separate fine particles below the crusher’s CSS before the crushing stage2022年6月10日 In the crushing process, the threestage closedcircuit crushing is a more modern method suitable for the crushing of highhardness leadzinc ore, which can complete the work of ore crushing and partial dissociation, thereby improving the subsequent grinding efficiency In the grinding process, the twostage oneclosed grinding is an efficient Leadzinc ore crushing and grinding process SBM Ultrafine Powder between dry and wet grinding depends on several factors If the final material is used as dry powder, the slurry must be dried after milling However, if the end product will be used as wet slurry or if the feed is already in the liquid phase, wet grinding is always a more economical process While typical products of dry milling are in the Optimization of Wet Grinding Parameters of Calcite Ore in 2016年1月8日 The first commercial production of phosphate rock began in England in 1847 A wide variety of techniques and equipment is used to mine and process phosphate rocks in order to beneficiate lowgrade ores and remove impurities The eighth chapter of this book deals with mining and beneficiation of phosphate ore The principle and operating conditions of important Mining and Beneficiation of Phosphate Ore IntechOpen
.jpg)
Ore Grinding SpringerLink
2023年7月20日 (2) Various working parameters of grinding mill, including fraction of critical speed for grinding mill, filling rate for grinding mill, grinding concentration, grinding cycle load, etc (3) And grinding material properties, including ore grindability, feeding particle size, etc Huge energy and steel consumption in ore grinding process greatly affect the subsequent separation process, the unit power consumption of dry process is low, which can be reduced by 3050% Features Small footprint, modular design, fast installation and movement The production cost per ton of fine powder is greatly reduced, which makes some lean iron ores economical Dry grinding process is short, avoid over grinding, no magnetic agglomeration oreintroduction of new type iron ore grinding and dry separation2018年7月15日 Request PDF Impact of grinding aids and process parameters on dry stirred media milling The demand on minerals with increasing product fineness is currently rising in many industrial applicationsImpact of grinding aids and process parameters on dry stirred media 2023年8月1日 The inefficiency of grinding, especially in dry grinding, is generally explained by the slowing effect caused by fine particles This may originate from the particle regrowth or rebuilding from smaller particles as a result of either agglomeration, including van der Waal's forces, or direct briquetting, or ball coating in order to provide soft surfaces [1, 7, 16, 17]Effective role of grinding aids in the dry grinding performance of calcite
.jpg)
Insight into Mineralogy of a LowGrade Manganese Ore for Separation
2019年8月1日 Abstract In this study, the use of XRF, XRD and other instruments found that the manganese content in the ore was 1453%, and the main forms were carbonate, iron manganese oxide and manganese oxide Because of the special magnetic susceptibility of these minerals, the magnetic separation method was chosen to improve the grade of manganese ore, and the 2012年1月1日 Request PDF Dry Fine Grinding of Calcite Powder by Stirred Mill The demand for fine powder is increasing in the many fields such as chemical, pharmaceutical and material industries Therefore Dry Fine Grinding of Calcite Powder by Stirred Mill2017年3月7日 ORE SEPARATION BY CLASSIFICATION the demands of almost any dry separation requir ement They are most commonly employed in closed circuit within grinding circui ts and are used (PDF) ORE SEPARATION BY CLASSIFICATION ResearchGate2024年8月26日 Limestone Powder Grinding Process 26/08 concrete coarse and fine aggregates, lime, calcium carbonate, etc Its crushing and grinding generally adopt dry process, and the corresponding process is selected according to different application fields: For limestone used in metallurgy and road construction, the ore is generally Limestone Powder Grinding Process ALPA Powder Equipment
.jpg)
Dry Permanent Magnetic Separator: Present Status and Future
2022年9月30日 Dry permanent magnetic separators have been widely used in the mineral and coal processing industries due to their simple operation and high separation efficiency2021年1月19日 1 Introduction Grinding is one of the most important technological processes used in many branches of industry For example, in the construction industry, grinding is used to crush components of building materials; in metallurgy–for metal ores; in the chemical and pharmaceutical industries–for substrates and reaction products; in the food industry–for food MeasurementBased Modelling of Material Moisture and Particle 2015年12月1日 Öksüzoglu and Uçurum [27] studied the ultrafine grinding of gypsum ore in a dry ball mill In their grinding tests, the mill speed was varied from 50 to 90% of the critical speed for gypsum oreAn experimental study on the ultrafine grinding of gypsum ore in a dry 2022年5月24日 It is suitable for grinding ore such as iron ore, gold ore, copper ore and leadzinc ore and other metal beneficiation, used to grind the ore below 0075mm for subsequent beneficiation process According to different Copper ore crushing processNEWSCLIRIK ultrafine
.jpg)
(PDF) Coproduction of DRI Powder and Semicoke
2015年11月26日 Effective utilization of low grade iron ore and low rank coal by excessive coalbased direct reduction process to coproduce DRI powder and semicoke can be one of the solutions to cut the high 2023年2月15日 The mined talc can be purified by the dry production process or the wet production process The dry production process is used for the highgrade talc deposits, while the wet production process is used for the lowgrade talc deposits At present, the industry mainly uses the dry production process to produce ultrafine talc powder, and seldom How to Process Talc (the Softest Mineral)? FTM MachineryWould you be a confirmed Engineer, a new graduate looking for information on the process he has 1st to work on, or a student, please access below articles on unit operations and equipment that, we hope, will be useful for you PowderProcess also hosts Process Engineer's Tools, a new online ressource for Process Engineers, not limited to Powder Processing This powderprocess Engineering resources for powder Media Attributions; Metal deposits are mined in a variety of different ways depending on their depth, shape, size and grade Relatively large deposits that are quite close to surface and somewhat regular in shape are mined using openpit mine methods (Figure 815 in Section 81)Creating a giant hole in the ground is generally cheaper than making an underground 82: Mining and Ore Processing Geosciences LibreTexts
.jpg)
Chemical Grinding Aids for Increasing Throughput in the Wet Grinding
Effective role of grinding aids in the dry grinding performance of calcite Powder Technology 2023, 426 , A comparative study on the effect of chemical additives on dry grinding of magnetite ore South African Journal of Chemical Engineering 2020, 34 , 135141 You’ve supercharged your research process with ACS and Mendeley 2024年4月1日 The beneficiation methods of RE ores mainly include gravity separation, magnetic separation, electrostatic separation and froth flotation Ores are generally wet in the beneficiation process, but the operation of electrostatic separators requires materials to be dryRecent process developments in beneficiation and metallurgy of 2000年9月1日 The effect of dry and wet grinding on the flotation of complex sulfide ores from the Merensky Reef in South Africa was investigated Topographical examination of the ground particle surfaces by A comparison of the flotation of ore from the Merensky Reef after 2023年2月15日 Hematite, also spelled haematite, is a weakly magnetic iron ore with better floatability than magnetite and wide distributionIt is one of the most important raw materials for the extraction of iron Its composition is complex In addition to containing a small amount of magnetite, the impurity embedding of haematite has uneven particle size and high content of How to Extract Iron from Hematite: Methods and Plants
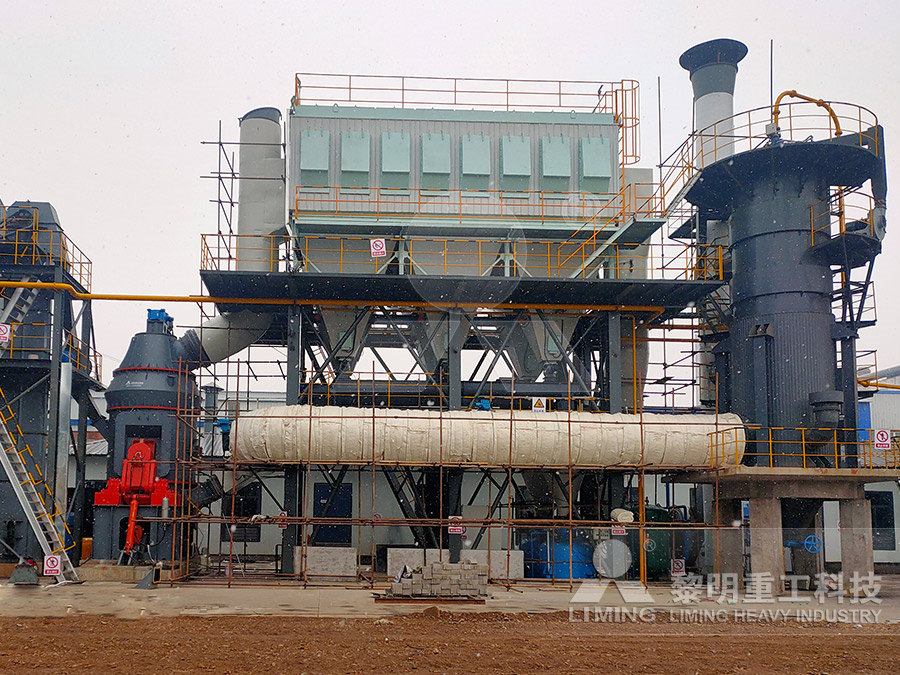
Evaluation of the best suitable purification method to purity Calcite
calcite micro powder Electromagnetic separation method and Precipitated Calcium Carbonate method are identified as the best available methods to enhance the quality to a high level But these processes are very costly at present Therefore the micro powder grinding process was examined and sampling was done with several rotating2013年12月18日 Fine grinding, to P80 sizes as low as 7 μm, is becoming increasingly important as mines treat ores with smaller liberation sizes This grinding is typically done using stirred mills such as the Isamill or Stirred Energy Use of Fine Grinding in Mineral Processing2016年3月23日 PDF Mineral and morphological characteristics of chromite ore strongly affect the separation efficiency while upgrading the low grade deposits Find, read and cite all the research you need (PDF) Processing of Ferruginous Chromite Ore by 2010年1月25日 A series of wet grinding experiments using calcite, pyrophyllite, and talc powder by a vertical type planetary ball mill, in which the size and distribution of grinding balls were varied with the Grinding kinetics of amorphous powder obtained by sol–gel process
.jpg)
Effect of blunging process on purification of halloysite ore from
2024年4月14日 Secondly, dry magnetic separation was applied to the washed 2+0212 mm size fraction after drying at room temperature to evaluate the coarse particlesized halloysite ore that was gained by We can use the gravity separation when the raw ore is coarsegrained fluorite lump ore When the raw ore has a high mud content and is accompanied by impurity minerals or the valuable minerals are embedded in fine particles, we can use the flotation process Fluorite often coexists with quartz, barite, calcite, sulfide ore, and other mineralsFluorite Beneficiation Process JXSC Mineral2023年6月25日 Crushing: The calcium carbonate stones just mined from the quarry are relatively large, and they need to be crushed by a jaw crusher and a hammer crusher in turn to the feed fineness (10mm20mm) that can enter the mill Grinding: Use a bucket elevator to send the crushed small pieces of calcium carbonate to the silo, then use a vibrating feeder to send them Guide to Calcium Carbonate Grinding: Mills, Tips, and Uses2024年3月15日 Dry magnetic separation (DMS) has low selectivity for fine magnetic ores, due to the difficult dispersion of fine particles in the separation process To address this problem, a novel centrifugal dry magnetic separation (cDMS) method was proposed to enhance the separation efficiency for fine particlesDevelopment of a centrifugal dry magnetic separator for separation
.jpg)
The effects of dry grinding and chemical conditioning during grinding
2022年11月1日 Dry processing of metal containing ores is often easily discarded as a viable option because of the higher energy consumption of dry grinding and several other challenges introduced from the 2024年4月26日 AG/SAG mills are typically used for coarse grinding, where large pieces of ore are efficiently broken down The grinding process reduces the ore size, which enhances the efficiency of subsequent beneficiation processes by increasing the surface area available for chemical reactions and physical separations 2 BeneficiationIron Ore Processing: From Extraction to Manufacturing