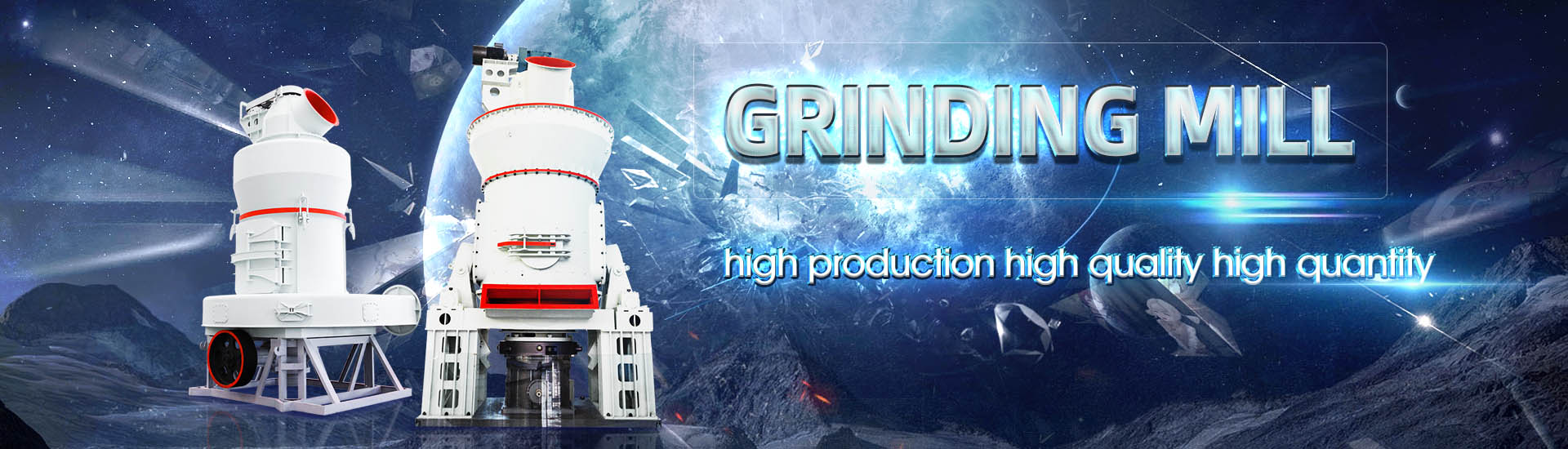
HOME→Nickel concentrate mineral grinding machine process flow Nickel concentrate mineral grinding machine process flow Nickel concentrate mineral grinding machine process flow
Nickel concentrate mineral grinding machine process flow Nickel concentrate mineral grinding machine process flow Nickel concentrate mineral grinding machine process flow

Process flowsheet development for beneficiation of nickel ore
2008年1月1日 A nickel concentrate containing 1232% Ni was produced with 897% recovery and final tailings with 0088% Ni can be disposed with 49% of metal loss A process flowsheet 2019年8月26日 Nickel processing description from its geology mineral property to how to extract mineral from rock and placer deposit, related processing plant flow chart and layout designNickel Processing Equipment, Process Flow, Cases JXSC Machine“Mineral processing is the first step in the solid mineral extractive process The goal is to produce granular material which meets a specific set of requirements in terms of material composition Mineral Processing DECHEMAThe conventional nickel ore beneficiation process is divided into four stages: crushing screening, grinding grading, flotation, dehydration dryingNickel Ore Processing Plant JXSC Mineral
.jpg)
Nickel Ore Mining Process Plant XKJ Group
The nickel ore dressing process can be applied to coppernickel ore or nickel oxide ore accompanied by pyrite and a variety of other gangue Process introduction Hybrid flotation 2024年1月19日 Nickel ore preparation involves a series of processes to prepare the ore for further processing, including crushing, grinding, and classification These steps help to reduce The Comprehensive Guide to Nickel Processing MiningpediaTeck has developed a novel hydrometallurgical process for treating low grade nickel concentrates and polymetallic concentrates with high magnesia content without the need for separation at Teck's CESL Nickel Process: Advancing Towards a Commercial 2007年11月14日 A nickel concentrate containing 1232% Ni was produced with 897% recovery and final tailings with 0088% Ni can be disposed with 49% of metal loss A process flowsheet PROCESS FLOWSHEET DEVELOPMENT FOR BENEFICIATION OF
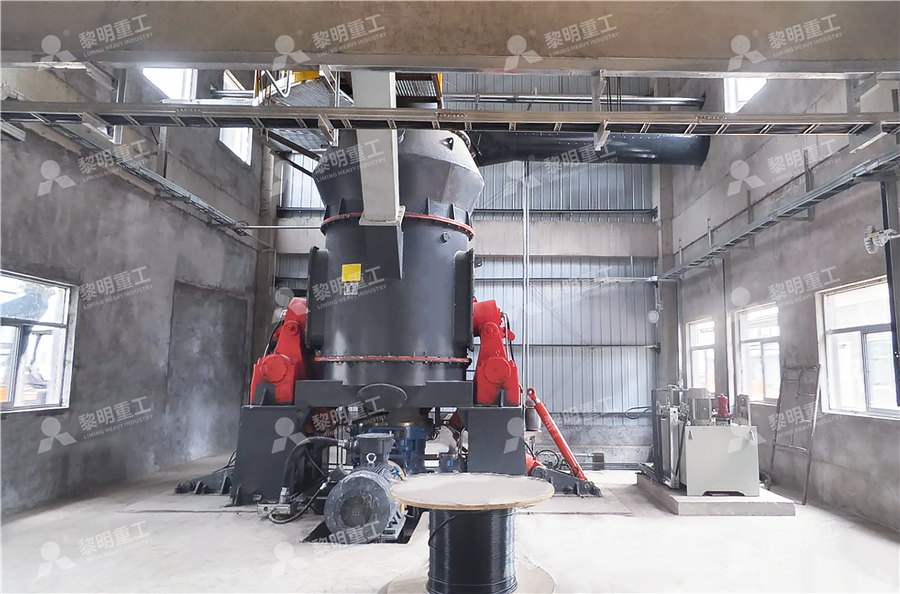
Production of Ferronickel Concentrate from LowGrade Nickel
The production of ferronickel concentrate from lowgrade nickel laterite ore containing 131% nickel (Ni) was studied by the nonmelting reduction magnetic separation process The sodium We ofer innovative and proven leaching, precipitation, solution purification, solvent extraction, and electrowinning technologies, as well as concentrator, sulfuric acid, and pyrometallurgical Hydrometallurgical nickel and cobalt plants and processes2024年11月21日 The nickel in the copper concentrate is lost in the smelting process, while the copper in the nickel concentrate can be recovered more completely Nickel oxide ore mostly uses processes such as crushing and Selection Of Nickel Ore Beneficiation ProcessThe grindingflotation electrorefining process has such disadvantages as metal dispersion, complex process flow, and low recovery rate This process has not been adopted in the newly emerging hydrometallurgical treatment facilities of highgrade nickel matte since the 1970s, but it still has industrial application in China, Russia, and CanadaNickel Metallurgy SpringerLink
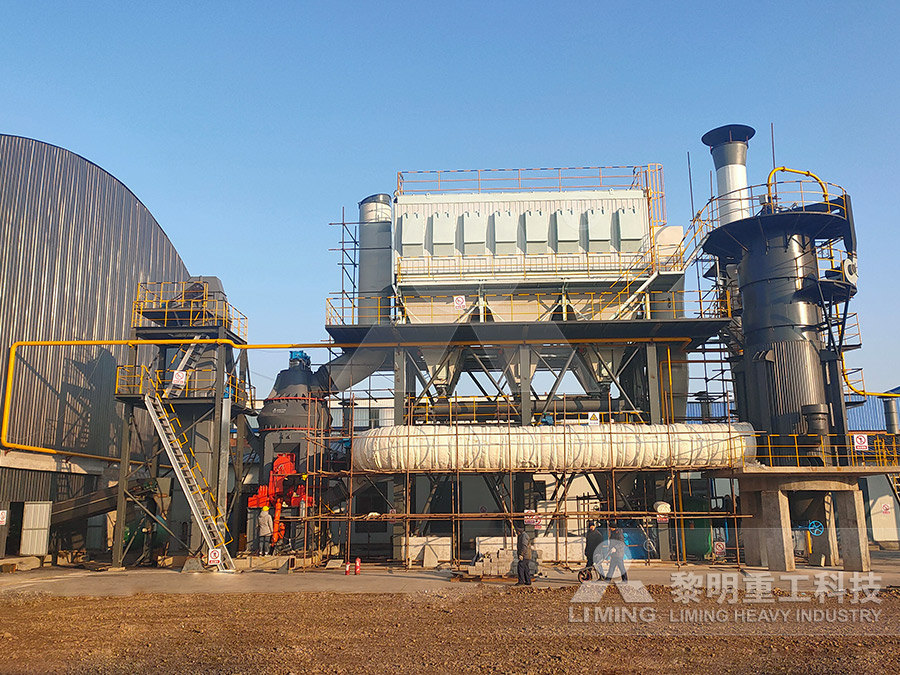
Nickel Ore Mining Process Equipment Flow Cases
Nickel ore mining process, how to extract mineral from rock and placer deposit, related processing plant flow chart and layout design read more Skip to content Menu Home; Because it is easier to recovery cooper from the nickel nickel powder can also be produced in autoclaves by using hydrogen reduction technology The new Metso Outotec anodeinabag technology for nickel electrowinning offers an environmentally friendly electrowinning process by significantly reducing nickel emissions and notably improving working conditions for operators This technology alsoHydrometallurgical nickel and cobalt plants and processesReasonable equipment and chrome wash process design to improve the grade of chrome concentrate and maximize the mineral recovery rate Free Flow Design 2 Rock Chromite Processing Plant For rock chrome ore processing, crushing, grinding machine and gravity the following is the specific equipment and process flow: Vibrating feeder; Jaw Chrome Processing Plant, Chrome Wash Plant, Chromite Process2021年7月6日 MLA tests showed that the particlebed breakage did not significantly improve the liberation degree compared to the ball mill grinding; the maximum difference of the proportion of 80100% Comminution a Heart of Mineral Processing ResearchGate
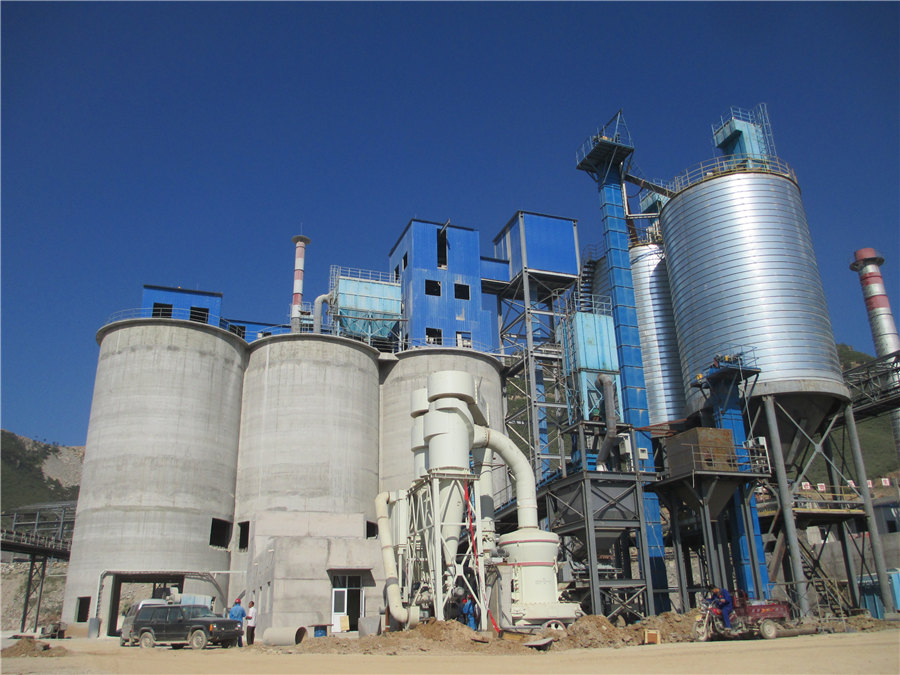
Copper Ore Processing Plants, Flow And Equipment
4 天之前 A single sulfide ore is usually treated by flotation process, using crushinggrindingclassificationflotationconcentration process to select a single copper sulfide ore as copper concentrate Copper ore beneficiation process The principle of priority flotation process is: crushing and screening→grinding and classification→priority The first rule deals with the conservation of mass The total flow of the material into the process plant equals the total flow out The second rule relates to the quality or grade of the concentrate product In practice, it is impossible to produce a concentrate consisting of only one mineral The third rule is a corollary of the secondIntroduction to Mineral Processing or BeneficiationCrushing, a form of comminution, one of the unit operations of mineral processing Mineral processing is the process of separating commercially valuable minerals from their ores in the field of extractive metallurgy [1] Depending on the processes used in each instance, it is often referred to as ore dressing or ore milling Beneficiation is any process that improves (benefits) the Mineral processing Wikipedia2024年1月1日 The grindingflotation electrorefining process has such disadvantages as metal dispersion, complex process flow, and low recovery rate This process has not been adopted in the newly emerging hydrometallurgical treatment facilities of highgrade nickel matte since the 1970s, but it still has industrial application in China, Russia, and CanadaNickel Metallurgy SpringerLink
.jpg)
Nickel Ore Beneficiation Process JXSC Machine
2023年2月2日 The main feature of this method is that it can directly obtain copper concentrate with low nickel content 2 Mixed Flotation The mix flotation process is suitable for separating the ore that is a copper grade lower than In order to determine the optimal process parameters of extracting metal from nickel concentrate by NaCl roasting and the primary and secondary factors affecting metal conversion in the roasting process, an L 9 (3 4) orthogonal experiment with four factors and three levels was designed by an orthogonal design assistant softwareThe experimental scheme is shown in Table 2, and the Effective recovery of Ni and Cu from lowgrade nickel sulfide 2022年8月3日 Nickel is a kind of nonferrous metal, it can form alloys with many metal elements, stainless steel, nickelbased alloys and other materials When the nickel content exceeds 3%, nickel can be directly smelted and used in the production of various materials However, when the nickel content is less than 3%, the ore needs to be sorted and purified through the What Mineral Processing Machine Can Be Used for Nickel nickel processing, preparation of the metal for use in various products Although it is best known for its use in coinage, nickel (Ni) has become much more important for its many industrial applications, which owe their importance to a unique combination of properties Nickel has a relatively high melting point of 1,453 °C (2,647 °F) and a facecentred cubic crystal structure, Nickel processing Extraction Refining Techniques Britannica
.jpg)
Utilization of limonitic nickel laterite to produce ferronickel
2018年11月1日 One of them known as the laterite segregation process, has now reached a successful conclusion; it has been confirmed that with this process 50–60% nickel concentrate can be achieved on a steady 2017年8月24日 Haldar described mineral processing «as the valueadded processing of raw material (runofmine ore) to yield marketable intermediate products (eg copper concentrate) or finished products (eg silica sand) containing more than one valuable minerals and separation of gangue (tailing)»The runofmine components consist of the following:Mineral Processing SpringerLink2020年7月6日 Mixed hydroxide precipitate (MHP) is a nickel intermediate product that has economical benefits to downstream leaching of lateritic marginal ores Usually, this product is subsequently processed and refined to produce nickel by hydrometallurgy, but an alternative route can be made integrating hydrometallurgy and pyrometallurgy Assessing the overall Agglomeration and Characterization of Nickel ConcentrateNickel processing Extraction, Refining, Alloying: The extraction of nickel from ore follows much the same route as copper, and indeed, in a number of cases, similar processes and equipment are used The major differences in equipment are the use of highertemperature refractories and the increased cooling required to accommodate the higher operating temperatures in nickel Nickel processing Extraction, Refining, Alloying Britannica
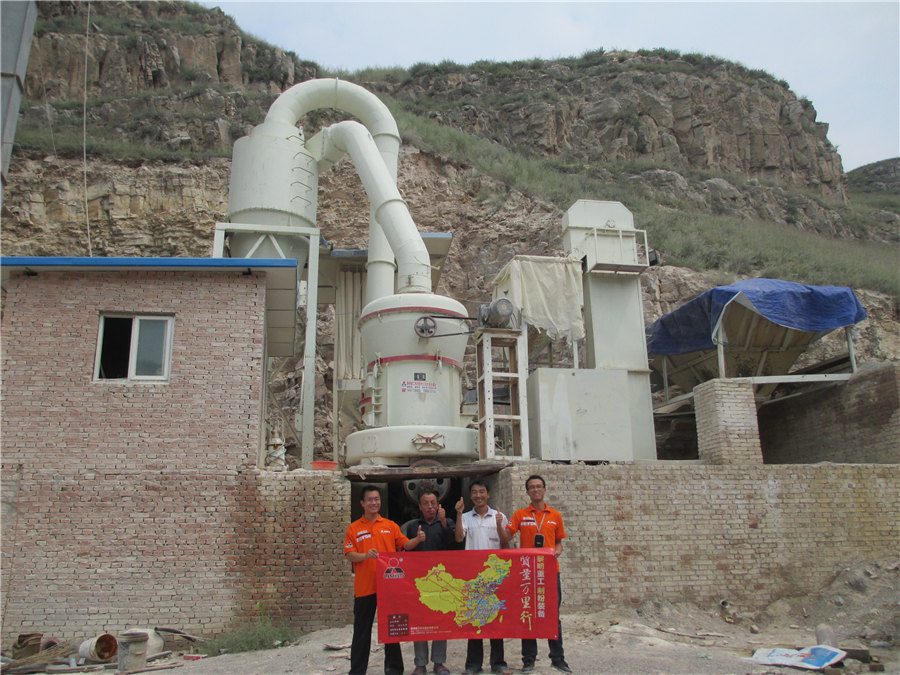
Solid State Extraction of Nickel from Nickel Sulfide Concentrates
2020年5月5日 Pyrometallurgical smelting and refining is the dominant method of extracting Ni from sulfide concentrates [14, 15]Prior to refining, the concentrate is smelted in an oxidizing atmosphere to yield a Nirich matte while simultaneously oxidizing the iron to iron oxide; the iron oxide is fluxed with silica to form an iron silicate slag that is immiscible with the matte [[16], replaced by lowgrade nickel ore with high content of alkaline gangue [5] Due to the sludging of gangue in the beneficiation process, the produced concentrate has lower nickel grade and higher MgO Corresponding author: Wenning MU, Tel: +86, Email: danae2007@163 DOI: 101016/S10036326(23)664490Simultaneous extraction of metals from nickel concentrate via 2024年4月17日 Abstract Facing the situation of nickel resource shortage and increasing nickel demand, it is an important task for the development of nickel industry to realize efficient utilization of lowgrade nickel sulfide ore In this work, the process of NaCl roastingwater leaching was proposed to simultaneously extract valuable metals from lowgrade nickel concentrate Based Efficient Extraction of Ni, Cu and Co from Mixed Oxide–Sulfide Nickel Download scientific diagram Coral Bay Nickel Corporation process flow sheet showing the HPAL process [9] from publication: The Production of Critical Materials as By Products The issue of Coral Bay Nickel Corporation process flow sheet
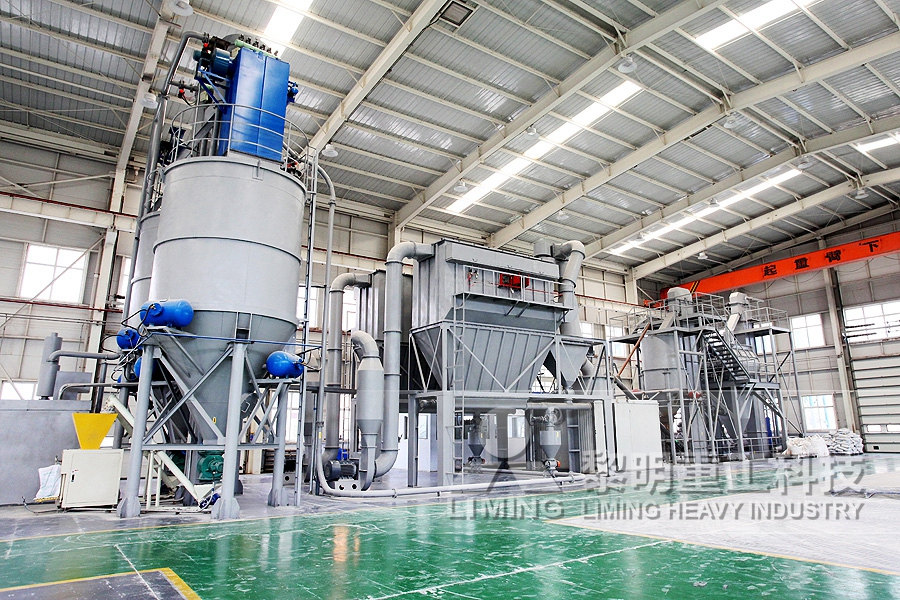
Extraction of Metals from Nickel Concentrate by Low
2023年5月30日 Aiming at the problems of high energy consumption and low metal recovery in traditional smelting of nickel concentrate, a novel process, namely NH4HSO4 roasting followed by water leaching to simultaneously extract metals and then separate them step by step, was proposed The effect of some key factors on the extraction of metals was investigated by 2022年5月16日 Simplified process flow diagram of the Outokumpu HIKO process used at the Kokkola refinery (Finland) for processing of nickel sulfide concentrates via low temperature pressure oxidation and The Direct Leaching of Nickel Sulfide Flotation Concentrates – A 2016年3月21日 and % Pb in perfect concentrate = 11545 x 5 = 577% and % Cu in perfect concentrate = 11545 x 1 = 1154% or, directly by (32), % Pb = 8658 x 5/5 + 25 = 577% Similar formulas for other mineral associations, for example, galena and chalcocite or chalcopyrite and chalcocite are easily worked mon Basic Formulas for Mineral Processing Calculations2024年11月21日 Add different agents in the flotation machine to separate other minerals The flotation process has a threestage flotation separation, which is to maximize the mineral grade 4 Concentrate filtration system: After obtaining mineral concentrates from the flotationSulfide Mineral Flotation Beneficiation Methods And Flow
.jpg)
Simultaneous extraction of metals from nickel concentrate via
replaced by lowgrade nickel ore with high content of alkaline gangue [5] Due to the sludging of gangue in the beneficiation process, the produced concentrate has lower nickel grade and higher MgO Corresponding author: Wenning MU, Tel: +86, Email: danae2007@163 DOI: 101016/S10036326(23)6644902020年6月18日 Considering that the low recovery efficiency and the massive loss of valuable metals by the traditional pyrometallurgical process smelting low‒nickel matte Therefore, this paper focuses on Efficient Synchronous Extraction of Nickel, Copper, and Cobalt » Liberation / fine grinding » Sorting » Agglomeration, etc of the concentrate » Management of the residue (gangue, slurry, process fluids) These steps can be viewed and described as macro mechanical process engineering operations The end product of mechanical mineral processing is an ore concentrate which is then put through a Mineral Processing DECHEMA2024年1月23日 The amount of pressure applied during grinding impacts the material removal rate, wheel wear, and potential for thermal damage Optimizing grinding pressure is vital for efficient and accurate grinding Machine Rigidity The rigidity of the grinding machine influences its ability to resist deflection under loadWhat is Grinding: Definition, Process, Types Specifications
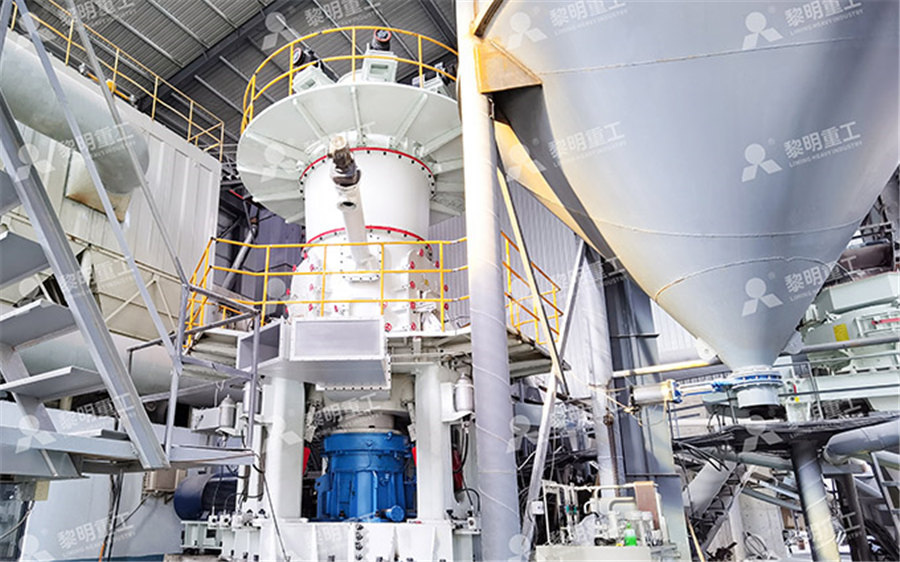
Future of Mining, Mineral Processing and Metal Extraction Industry
2019年8月16日 Mining, mineral processing and metal extraction are undergoing a profound transformation as a result of two revolutions in the making—one, advances in digital technologies and the other, availability of electricity from renewable energy sources at affordable prices The demand for new metals and materials has also arisen concurrently This necessitates 2016年3月8日 The Mineral Processing Flowsheets shown on the following pages are based on actual data obtained from successful operating plants Metallurgical data are shown in these flowsheets which incorporate Crushers, Grinding Mills, Flotation Machines, Unit Flotation Cells, and Selective Mineral Jigs as well as other standard milling equipment The Flotation Machine, Mineral Processing Flowsheets 911Metallurgist2020年4月14日 The pressure oxidation of lowgrade nickel sulfide concentrate with high iron sulfides content generates significant amounts of sulfuric acid that must be neutralized This acid can be utilized to leach metal values from ores The High Temperature CoProcessing of Nickel high nickel concentrate from tropical low grade nickel laterite ore obtained from Indonesia in this paper Research of the effect of process parameters on reduction was carried out of lowgrade nickelSTUDY ON SELECTIVE REDUCTION AND MAGNETIC SEPARATION
.jpg)
(PDF) A comprehensive review on the grinding process:
June 2022; ARCHIVE Proceedings of the Institution of Mechanical Engineers Part C Journal of Mechanical Engineering Science 19891996 (vols 203210) 236(2):年4月18日 In anticipation of future demands, a comprehensive understanding of the chemical and mineralogical characteristics of nickelbearing minerals is a prerequisite to devising effective nickel beneficiation methods Of particular importance are markers in the mineralogy of the flotation concentrate that inform beneficiation strategies to improve concentrate grades, Characterization of a Nickel Sulfide Concentrate and Its MDPI2015年7月21日 This article discusses the range of application of ultrafine grinding for processing mineral raw materials and presents examples of the successful use of this technology in the concentration of polymetallic ores and the hydrometallurgy of gold A description is given of the principle of operation of bead mills and their main technological parameters (the size of the Ultrafine Grinding in Contemporary Flow Diagrams for Mineral 2020年2月14日 High temperature pressure oxidation of a lowgrade nickel concentrate was examined to demonstrate the potential benefits and shortcomings of this approach The high iron sulfide content ensured that acid generation was much greater than for higher grade concentrates This results in the formation of basic iron sulfate phases and a significant High Temperature Pressure Oxidation of a LowGrade Nickel
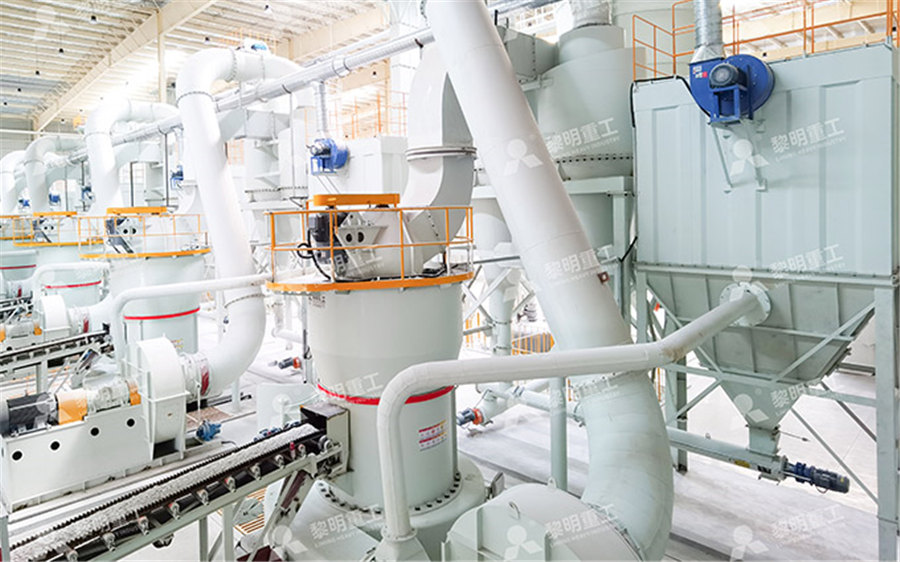
Teck's CESL Nickel Process: Advancing Towards a Commercial
022% nickel, to an acceptable concentrate grade of 10 to 20% nickel Concentrate smelting produces a high grade nickel matte which is then refined hydrometallurgically With the majority of the world’s nickel supply coming via pyrometallurgical processes, the technology has proven to be quite robust over the yearsA certain coppernickel ore is a large metal symbiotic coppernickel sulfide oreA suitable mineral processing process was designed for it, that is, the process flow of three—stage and oneclosedcircuit ore crushing, stage grinding, coppernickel mixingseparation flotation, threestage dehydration of nickel concentrate, and twostage Nickel Ore Mining Process Plant XKJ Group