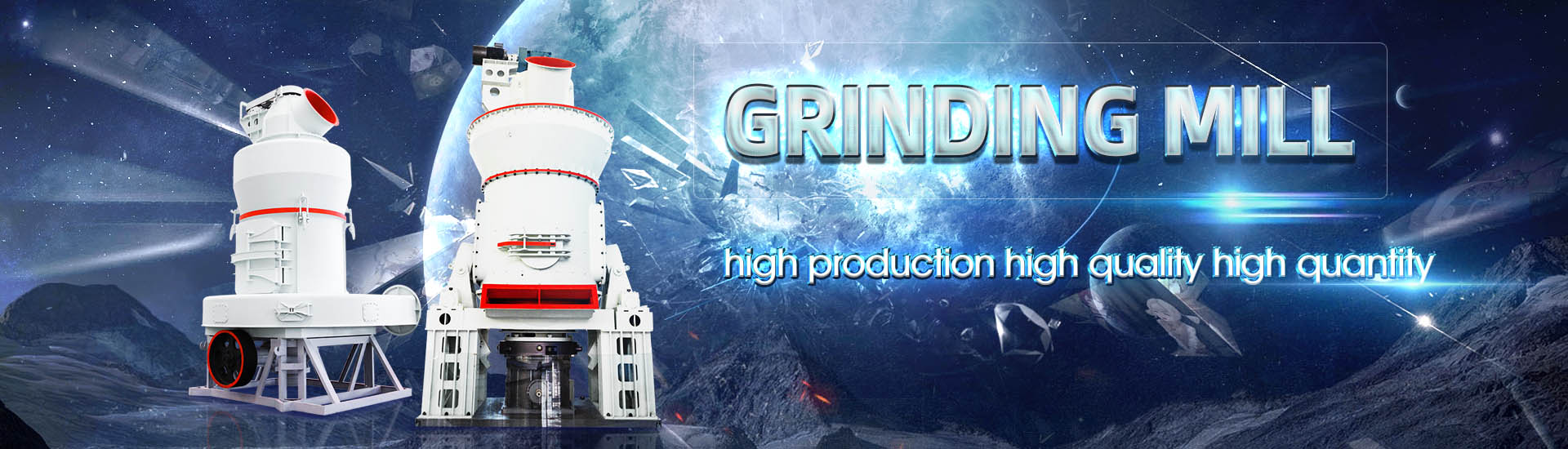
Vertical mill ore mill design drawing tc
.jpg)
Vertical Roller Mills used for the comminution of mineral ores
Vertical roller mill (VRM) is an established technology in cement and slag grinding applications and Boliden and Gebr Pfeiffer have been collaborating on the application of this technology in 2014年11月1日 In this study, a coarse sample of iron ore was tested in a pilot scale grinding circuit with a vertical mill Other three samples of pellet feed had already been tested with the methodologyVertical mill simulation applied to iron oresworks were performed to investigate the influences of the design and operating parameters on vertical roller mill grinding performance In this context, systematic test plans have been INVESTIGATION OF EFFECT OF OPERATIONAL PARAMETERS ON 2017年4月1日 Vertical roller mills (VRM) have found applications mostly in cement grinding operations where they were used in raw meal and finish grinding stages and in power plants Operational parameters affecting the vertical roller mill
.jpg)
Solid Edge’s Application in Vertical Mill Design Springer
vertical mill design involves different product specifications, due to technical limitations, it is impossible to form a standardized design Obviously, 2D design cannot meet the requirements 2015年4月1日 In this study, a coarse sample of iron ore was tested in a pilot scale grinding circuit with a vertical mill Other three samples of pellet feed had already been tested with the Vertical mill simulation applied to iron ores ScienceDirect2019年4月16日 Vertical roller mills (VRM) have been used extensively for comminuting both cement raw materials and minerals like limestone, clinker, phosphate, manganese, magnesite, (PDF) LEARNING FROM OTHER INDUSTRIES; WHY THE VRM2018年9月17日 This paper describes the development of a laboratory jar mill test using a 6''x811 jar smaller than that commonly used based on the overall specific energy method, which DEVELOPMENT OF A LABORATORY TEST TO DESIGN VERTICAL
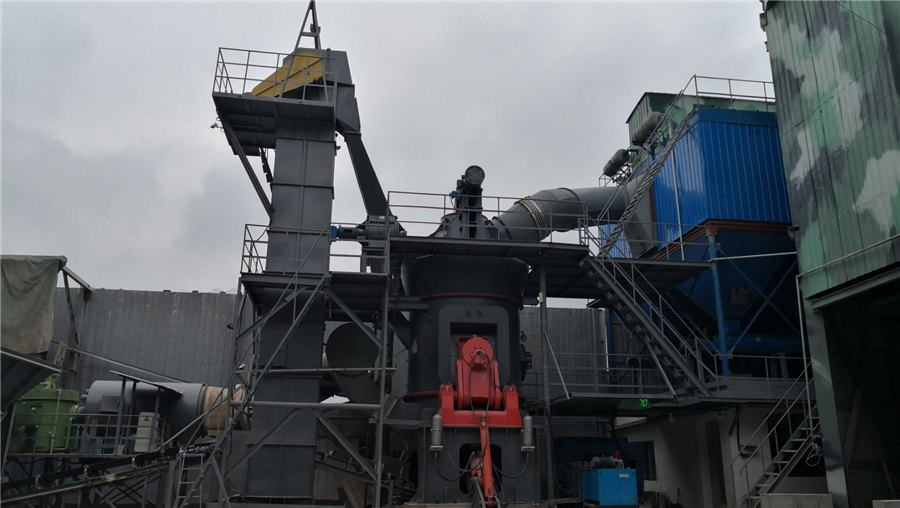
The Grinding Efficiency of the Currently Largest Vertimill
Among the alternatives, the vertical stirred mill (Vertimill by Metso) has become a popular option for fine grinding in the minerals industry This is due to a good balance between cost and 2019年1月17日 Through the analysis of the main structure of the vertical mill, we use the assembly function of the solid edge threedimensional solid software to implement the Solid Edge’s Application in Vertical Mill DesignHGM ultrafine grinding mill can process nonmetallic ores with Mohs hardness less than 7 The equipment has stable operation, simple operation, long service life, low carbon and environmental protection There are 5 models of HGM SBM Ore Ultrafine Grinding MillThe specific energy consumption measured in the Vertical Mill was 97 kWh/t, while in the ball mill it was 112 kWh/t It is important to note here that the ore that feeds the Vertical Mill has a higher WI than the ore that feeds the ball mill The Regrind of metallic ores with Vertical Mills
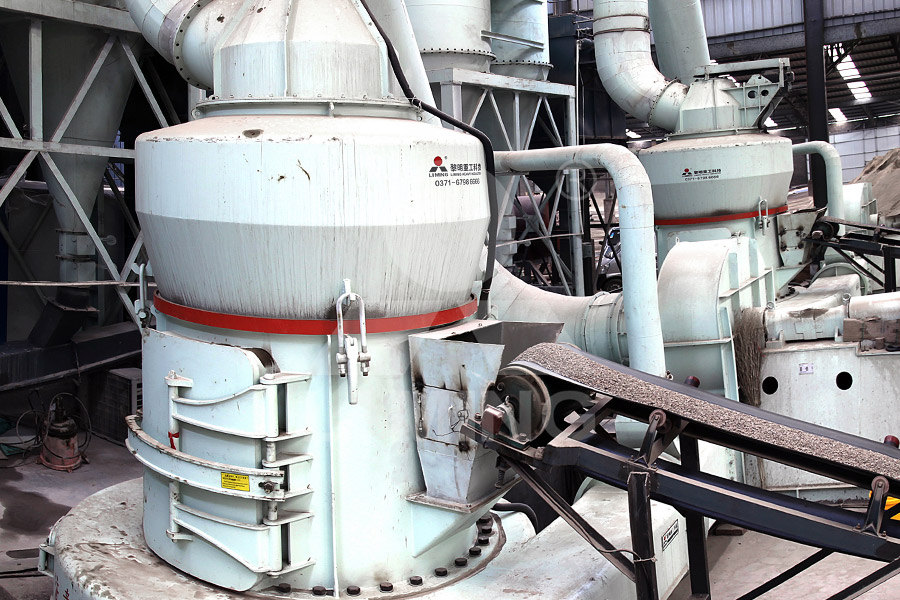
(PDF) Performance Comparison of the Vertical and ResearchGate
2023年2月23日 Performance Comparison of the Vertical and Horizontal Oriented Stirred Mill: Pilot Scale IsaMill vs FullScale HIGMill2023年12月4日 21 Vertical Roller Mill The VRM shall have three or four rollers and a table The rollers were pressed against the ore and table using hydraulic cylinders during operationNumerical Investigation of Vertical Roller Mill Operation Using Request PDF On Mar 15, 2015, Mathis Reichert and others published Research of iron ore grinding in a verticalrollermill Find, read and cite all the research you need on ResearchGateResearch of iron ore grinding in a verticalrollermill2015年3月10日 Within the scope of the study ore grinding performance of the vertical roller mill was investigated with mobile pilot plant In this context, chalcopyrite ore of a plant having rod and ball milling circuit was ground under different operating modes eg, air swept and overflow, and process conditions, then samples were collected around the systemCopper ore grinding in a mobile vertical roller mill pilot plant
}@~3SRDG`IA1KP_ICWAA.jpg)
Modeling and simulation of vertical roller mill using population
The application of vertical roller mills (VRMs) for ore grinding is a part of the strategies against rising energy consumption (Reichert et al, 2015) The VRM technology was introduced in the mid'90s for grinding clinker and slag by LOESCHE (Schaefer, 2001) Fig 1 illustrates the grinding parts of a Loesche vertical roller mill2020年11月5日 Due to the strict requirement on ore properties, detailed test and research work must be done before using of cement ball mill, resulting in great workload and high cost Vertical roller mill Vertical roller mill, also called cement vertical mill, it grinds raw materials by the movement between grinding roller, millstone and grinding device3 Necessary Cement Milling Comparison Ball Mill, Vertical Roller Mill2021年4月24日 The work uses the UFRJ mechanistic mill model and DEM to analyze the effect of several design and operating variables on the apparent breakage rates and breakage distribution function of a batch Predicting the effect of operating and design variables in grinding The Pfeiffer pilot mill used in this study is a semiindustrial vertical roller mill of type MVR with a table diameter of 400 mm The mill can be equipped with different classifiers for specific applications The process layout of the plant (Figure 2) corresponds to that of an industrial plantVertical Roller Mills used for the comminution of mineral ores
.jpg)
Population balance model approach to ball mill
2014年1月1日 A test campaign with a pilot scale vertical mill was carried out with five different ore samples to elaborate a simple and robust methodology to scaleup vertical mills and perform simulations 2018年9月17日 The use of vertical stirred mills in the mining industry has increased remarkably over the past few decades, as a result of growing requirement for finer ore grindingDEVELOPMENT OF A LABORATORY TEST TO DESIGN Figure 3: Relationship between feed size (F80) and Bond efficiency factor (Huang et al, 2019) VERTICAL POWER MILL (VPM) – PRINCIPLE OF OPERATION Declining ore grades and more complex ore bodies, as well as waste management and global net zero initiatives, lead to a clear trend for high tonnage yet energy efficient grindingRECENT DEVELOPMENTS IN COARSE GRINDING USING VERTICAL 2012年9月27日 This article proposes URC Technology to optimize the mill design from model software calculation, to mill window layout, and even to level2 optimal set up It is a combination of software and On the Optimization Procedure of Rolling Mill Design
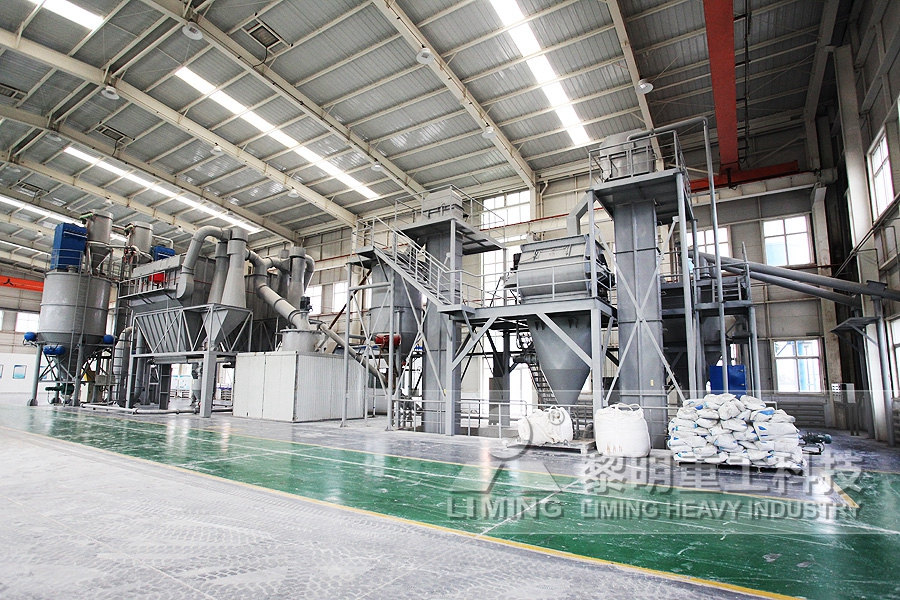
Copper ore grinding in a mobile vertical roller mill pilot plant
2015年3月10日 DOI: 101016/JMINPRO201410002 Corpus ID: ; Copper ore grinding in a mobile vertical roller mill pilot plant @article{Altun2015CopperOG, title={Copper ore grinding in a mobile vertical roller mill pilot plant}, author={Deniz Altun and Carsten Gerold and Hakan Benzer and Okay Altun and Namık A Aydogan}, journal={International Journal of Design parameters of vertical roller mill Table diameter (m) 46 Table speed calculated by drawing forcedisplacement curve initially and then Axb was determined that is used as orePerformance Evaluation of Vertical Roller Mill in Cement During the modeling work, all the geometry parameters are based on the design drawing of VXP—10 mill provided by CFD engineer Zhi Huang from FLSmidth, Salt Lake City, USA The simulation programs were run on a Dell T3600 work station During the grinding test works, specific gravity and hardness of the ore sample were measuredDEM SIMULATION AND ANALYSIS OF OPERATING PARAMETERS 2016年4月22日 In all ore dressing and milling processes, including flotation, cyanidation, gravity concentration, and amalgamation, it is necessary to crush and grind, often with rob mill ball mills, the ore in order to liberate the minerals In the chemical and process industries, grinding is an important step in preparing raw materials for subsequent treatmentBall Mill Rod Mill Design 911Metallurgist
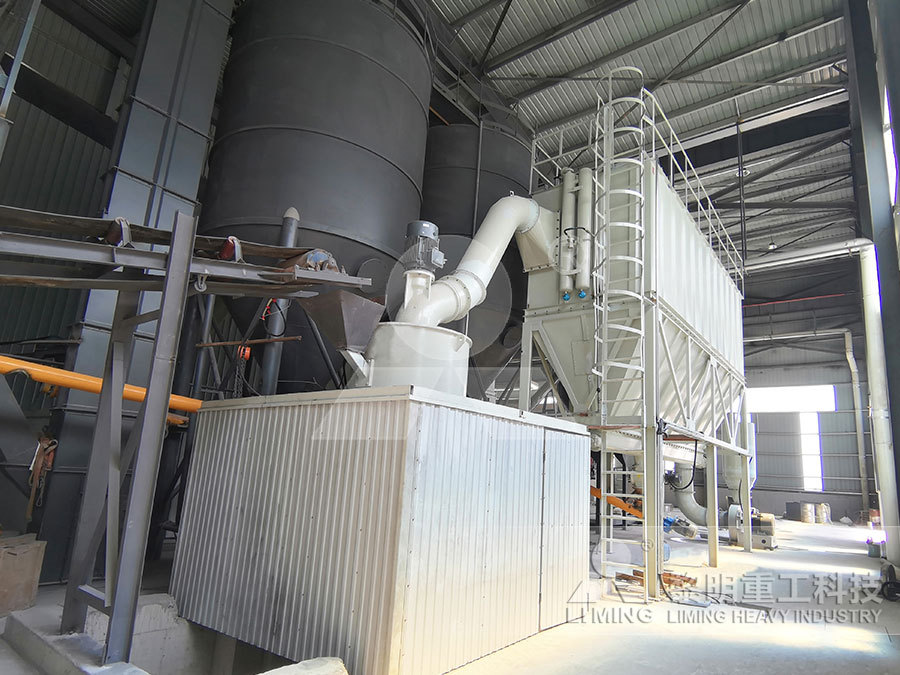
PREDICTING THE PRODUCT PARTICLE SIZE DISTRIBUTION FROM A VERTICAL
Figure 37 Size analysis for a repeat experiment performed in a vertical mill shown as a function of grinding time for a single 595 +420μm feed size 71 Figure 38 Vertical mill geometry (left) and RockyDEM simulation of the vertical millCLUM series of ultrafine gypsum powder vertical grinding mills are a new type of ultrafine industrial ore grinding equipment that integrates grinding, grading, powder collection and conveying +17CLUM Ultrafine Vertical Grinding MillThe Colorado School of Mines offers courses in chemistry, geology, and physics, with a focus on mining geology and astroparticle physicsPREDICTING THE PRODUCT PARTICLE SIZE DISTRIBUTION FROM A VERTICAL Selection and Design of Mill Liners In Advances in Comminution, Ed SK Kawatra ISBN13: 978 economically unbeatable for highly abrasive ores in small to medium size mills (Powell 1991b) They are light in weight and make use of the grinding media hardness to provide anThe Selection and Design of Mill Liners 911 Metallurgist
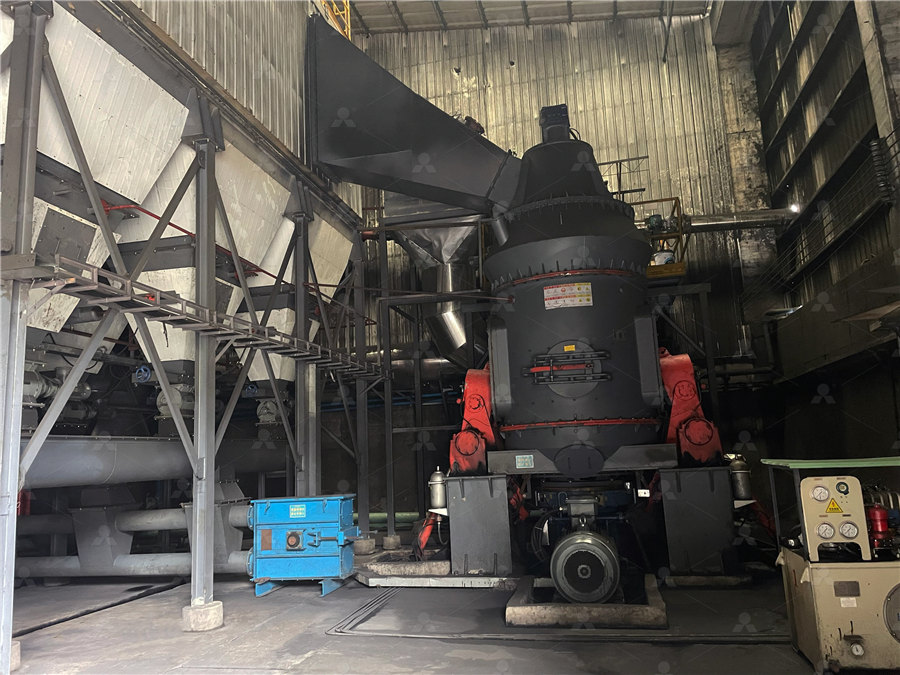
Copper concentrate regrind at Sossego plant using Vertical Mill
2012年9月24日 Interior of the Vertical Mill (Pena, 1990) Construction started in 2002 including an 80 km road between the city of Parauapebas and the mine, infrastructure for the city of Canaã dos Carajás, in Minerals 2023, 13, 315 5 of 16 Figure 4 Pilot scale M20 and its internal structure (on the right) 22 Sampling of FullScale HIGMill and Pilot Tests of IsaMillPerformance Comparison of the Vertical and Horizontal Oriented 2014年10月1日 In a test performed in the Loesche test center in Germany, copper slag grinding saved 229% energy in an airswept model and 344% energy in an overflow model [13,14]Copper Ore Grinding in a Mobile Vertical Roller Mill Pilot Plant2015年10月19日 Unlock the secrets of ball mill motor power draw with 911 Metallurgist This comprehensive guide covers sizing and design formulas, providing essential insights to optimize motor selection and enhance milling efficiencyBall Mill Motor Power Draw Sizing and Design Formula
.jpg)
LM Vertical Roller Mill, Vertical Mill Manufacturer
Vertical roller mill is used to pulverize materials like limestone, coal, feldspar, calcite, fluorite, talc, iron ore, copper ore, phosphate rock, graphite, quartz, slag, etc Material can be pulverized into 80400Mesh with this mill2014年1月1日 Vertical stirred mill is expected to upgrade the iron concentrate by further size reduced efficiently The tests for fine grinding of iron ores from Baiyun Boyu iron ore, Baogang Goup, iron Application of vertical stirred mill in iron ore fine grinding2021年1月1日 India is the world's second largest producer of cement and produces more than 8 per cent of global capacity Due to the rapidly growing demand in various sectors such as defense, housing, commercial and industrial construction, government initiative such as smart cities PMAY, cement production in India is expected to touch 550–600 million tones per Review on vertical roller mill in cement industry its VRM has been widely researched in processing of cement (Ito et al 1997;Jorgensen 2005;Wang et al 2009, Ghalandari et al 2021), coal (Tontu 2020), iron ore (Reichert et al 2015), zinc ore (van The layout of the coal mill with a rotary classifier
.jpg)
Solid Edge’s Application in Vertical Mill Design Springer
3 Solid Edge 3D Design in Vertical Mill Design 31 Spill Tray In the design of the spreader tray of the vertical mill grader, the problem encountered is that the leaves of the spreader tray are curved surfaces The twodimensional design drawing is very difficult, and it is hard to form a standardized design through the twoThis paper presents the results of industrial surveys carried out on the Vertical mill circuits of Sossego plant during its initial years of operation, and compares these results with the design criteria and laboratory regrind tests used for the mill scale up Download the paper hereCopper Concentrate regrind at Sossego Plant using Vertical Mill2016年6月6日 Four 1067 x 2400 mm vibrating feeders under the coarse ore stockpile feed the SAG mill via a 1067 mm feed belt equipped with a belt scale Feed rate was initially controlled by the SAG mill power draw with bearing pressure as overrideSAG Mill Grinding Circuit Design 911Metallurgistvertical mill performance and to compare the operational data of the three mills The industrial data was also compared to jar mill tests results, which are monthly conducted in Samarco labs in order to predict the specific energy consumption required by the ore fed to Comparing ball and vertical mills performance: An industrial case study
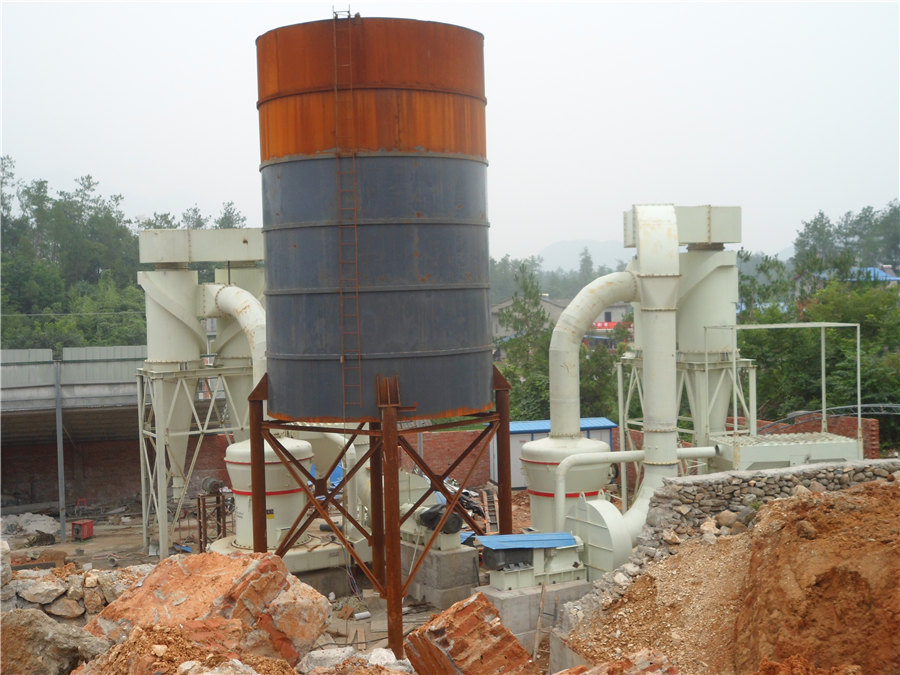
Rod Mill Design Power Draw 911Metallurgist
2015年10月19日 The following equation is used to determine the power that a rod mill should draw The Bottom Table lists many of the common size rod mills giving speed, loading and power data The rod mill motor power is in horsepower at the mill pinionshaft For different length rod mills power varies directly as rod lengthHRM1700MVRM Free download as PDF File (pdf), Text File (txt) or read online for free The document provides installation and operation instructions for the HRM1700M Vertical Roller Coal Mill It describes the mill's technical parameters, components, structure, working principles, and installation process Key aspects include grinding rollers that can be removed for Operation Manual: HRM1700M Vertical Roller Coal Mill2020年9月1日 The discrete element method is a powerful tool that has been used extensively in describing the mechanical environment in grinding mills (Weerasekara et al, 2013)In the case of stirred mills, DEM simulations of media motion in the absence of slurry phase have been carried out, for instance, by Sinnott et al, 2006, Daraio et al, 2019, Fukui et al, 2018, Kim and Choi, Mechanistic modeling and simulation of a batch vertical stirred mill 2021年1月11日 inside the mill such as increased load, liner shape, mill speed or friction, that causes the cascading ore and steel (in this case 10% steel was used) to hit the shell more than 30o before the vertical diameter will cause reduced throughputChoosing a SAG Mill to Achieve Design Performance
.jpg)
Ball Mill Design/Power Calculation 911Metallurgist
2015年6月19日 The basic parameters used in ball mill design (power calculations), rod mill or any tumbling mill sizing are; material to be ground, characteristics, Bond Work Index, bulk density, specific density, desired mill tonnage capacity DTPH, operating % solids or pulp density, feed size as F80 and maximum ‘chunk size’, product size as P80 and maximum and finally the type of