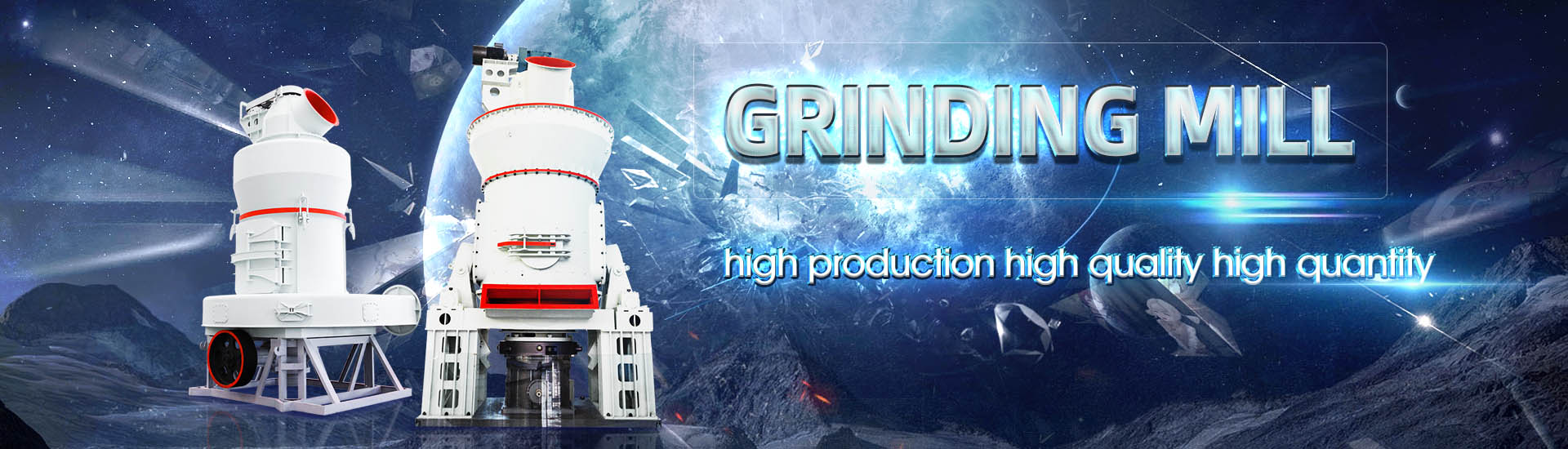
Coal Raw Coal Grinding Machine Conditions
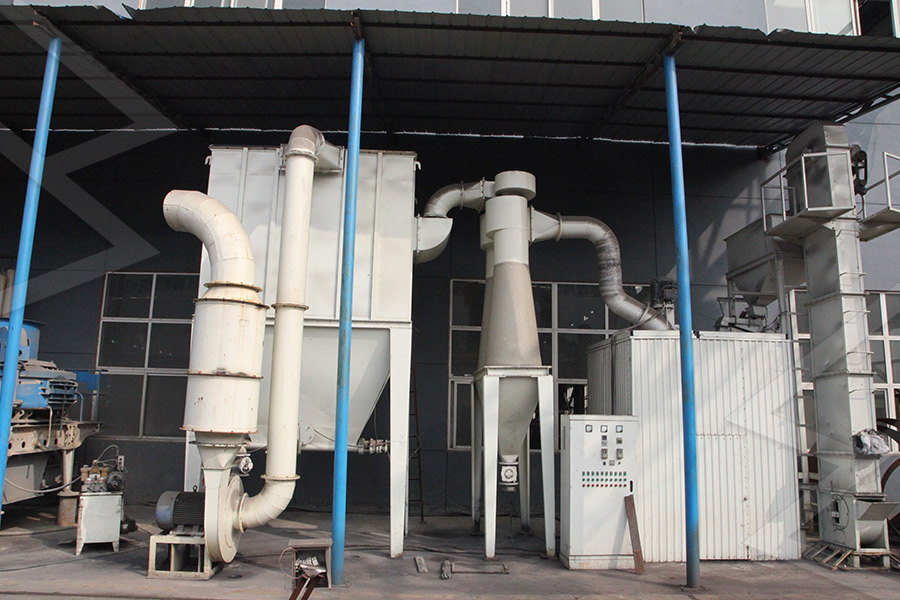
COAL GRINDING SYSTEMS SAFETY CONSIDERATIONS PEC
On a coal grinding and firing system, maintenance work or inspections that require opening equipment should only be performed when given specific instructions and under the direct supervision of authorized personnel Cutting or welding around or on a coal firing system can A HAZOP study of a typical operating coal grinding and firing system encompasses the following areas: 1 Fuel handling and storage – raw coal receiving, storage and handling 2 Fuel COAL2021年11月4日 This method enables facilitated testing procedures and a more exact simulation of grinding in vertical spindle coal mills Ballrace mills and Loesche roller mills were used(PDF) Technique to Investigate Pulverizing and AbrasiveThis handbook examines the intermediate and fine grinding of coal Four coal grinding devices three dry, one wet are discussed with the appropriate ancillary equipment for complete Coal grinding technology: a manual for process engineers
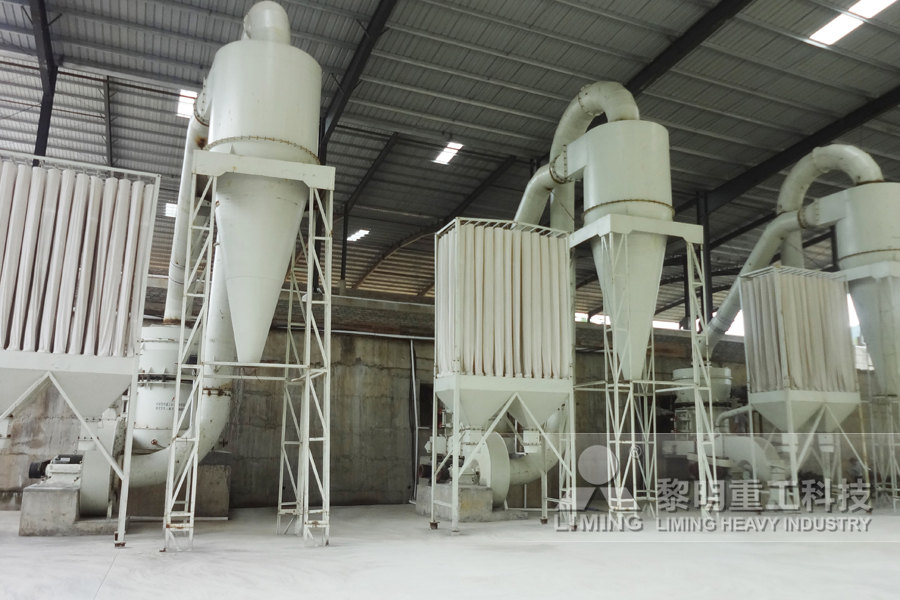
Indirect Firing Coal Grinding Systems: Enhancing Efficiency and
Indirect firing coal grinding systems offer significant advantages in terms of safety, efficiency, and operational flexibility By incorporating an intermediate storage stage, these systems provide 2021年11月4日 crush the coal depends on the grain size of the raw material and the required degree of grain grinding The use of fine coal grains obtained for this purpose, for example of Coals in Mineral Processing SystemsVertical roller mills are not only used for grinding cement raw materials but also find an application in grinding a wide variety of coal types in cement and power plants Gebr Pfeiffer SE (GPSE) COAL GRINDING IMPS: more than meets the eye Gebr PfeifferA HAZOP study of a typical operating Coal Grinding and Firing System encompasses the following areas: a) Fuel handling and storage – Raw coal receiving, storage and handling b) COAL GRINDING AND FIRING SYSTEMS HAZOP ANALYSIS PEC
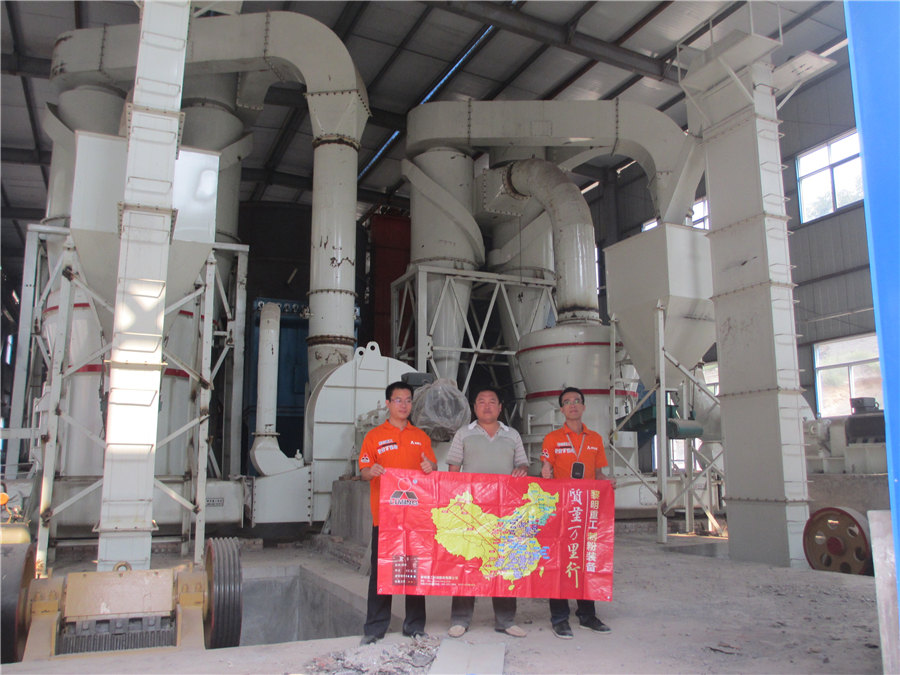
A Study on the Hard Coal Grindability Dependence on
2021年12月5日 Coal that requires large energy inputs during grinding has a low Hardgrove index value The high values of the Hardgrove index testify to the ease of grinding the coal There is also no simple relationship between the value of 2023年8月15日 Coal has a variety of physical properties, including: Color: Coal can range in color from black to brown to grayish; Hardness: Coal can range in hardness from very soft and crumbly, like graphite, to very hard, like Coal Properties, Formation, Occurrence and Usesfor grinding cement raw material, clinker and granulated blast furnace slag The MPS technology, however, is also applied and legal standards for coal grinding Important conditions were attached to the order The new coal mill had to be integrated into the present plant layoutCOAL GRINDING IMPS: more than meets the eye Gebr PfeifferIt pulverizes coal by applying hydraulicallyloaded grinding pressure through three grin ding rollers onto a rotating bed of coal Grinding pressure can be adjusted to account for variations in coal grindability and desired product fineness Raw coal is fed through a centrally located feed pipe to the center of the grinding tableA Comparison of Three Types of Coal Pulverizers Babcock Power
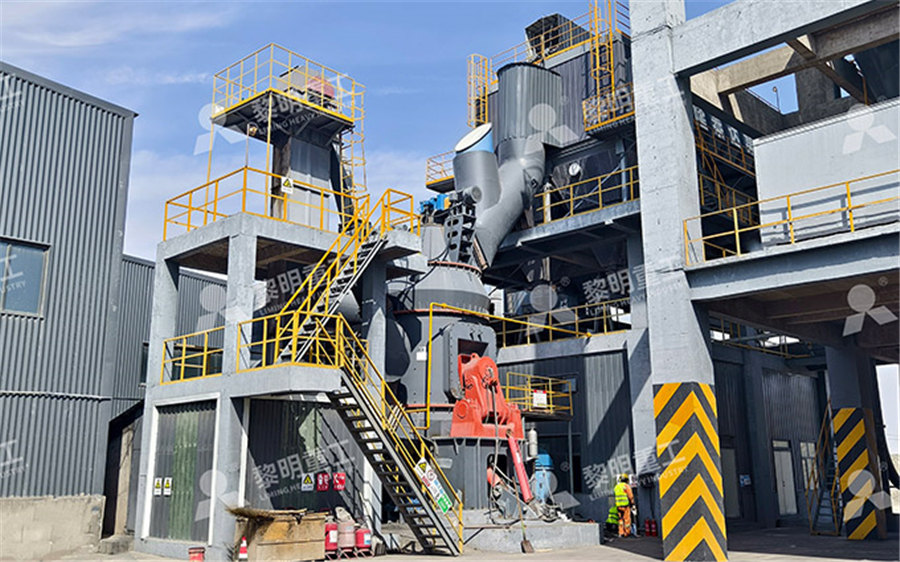
Coal Mill in Cement Plant Vertical Roller Mill AirSwept Ball Mill
The ball mill is a traditional coal pulverizer machine, which has been widely used since it was invented In the cement plant, the new dry process cement manufacturing requires the moisture content of coal powder to be 05% ~ 15%, while that of raw coal is 15% ~ 40%To convert raw coal into fine coal powder, coal grinding mills are essential Coal grinding mills are specialized equipment designed to break down coal into fine particles suitable for combustion The coal grinding process involves crushing and grinding coal into small particles, which are then heated to high temperatures in a furnace, producing steam that drives a turbine to generate What is a Coal Grinding Mill2015年3月1日 Comparison of energy input for grinding between the original tests and tests with removal of fines for sample sizes of À 4 þ 28 mm and À 2 þ 125 mmEnergySize Reduction of Coals in the Hardgrove MachineEnergies 2021, 14, 7300 3 of 15 A = f2(G, B) (2) where G is the coal grindability within the specified system, M means the mechanical properties of the coal, r is the coal porosity, q determines the hard particles mechanical and geometrical characteristics, w is the moisture, T is the temperature, h is the overall efficiency of the grinding system, A is the coal abrasiveness, of Coals in Mineral Processing Systems
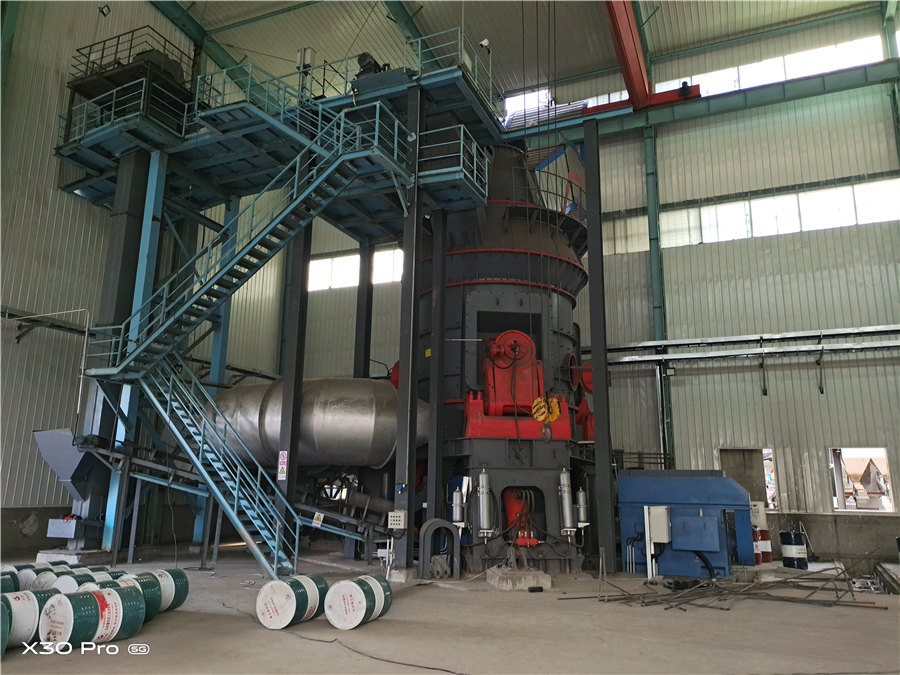
of Coals in Mineral Processing Systems
Energies 2021, 14, 7300 3 of 15 A = f2(G, B) (2) where G is the coal grindability within the specified system, M means the mechanical properties of the coal, r is the coal porosity, q determines the hard particles mechanical and geometrical characteristics, w is the moisture, T is the temperature, h is the overall efficiency of the grinding system, A is the coal abrasiveness, 【Coal Pulverizer Structure】 The coal injection machine mainly comprises coal hopper, shell, main shaft, coal hammer, liner, fan, separator, and motor 【Coal Pulverizer Injection Machine Working Principle】The raw coal enters the grinding area of the grinding roller and the grinding disc and grinding into coal powder under the rolling and grinding of grinding rollersCoal Pulverizer Injection Machine JXSC MachineIntroduction This article concerns itself with vertical grinding mills used for coal pulverization only (coal pulverizers), although vertical grinding mills can and are used for other purposes The 3D model in the saVRee database represents a vertical grinding bowl millOther grinding mill types include the ball tube mill, hammer mill, ball and race mill, and , roll and ring millVertical Grinding Mill (Coal Pulverizer) Explained saVRee2024年10月15日 21 Cashew Nutshell and Raw Coal Analysis As the data shows in Table 3, the raw coal LHV is about 23,500 kJ/kg, the sued cashew nutshell LHV is about 26537 kJ/KG the moisture of the coal is high due to open storage, for CNS is still in the target The mixing percentage is 57% of total raw coalCashew Nutshell and Raw Coal Cogrinding for Sustainability
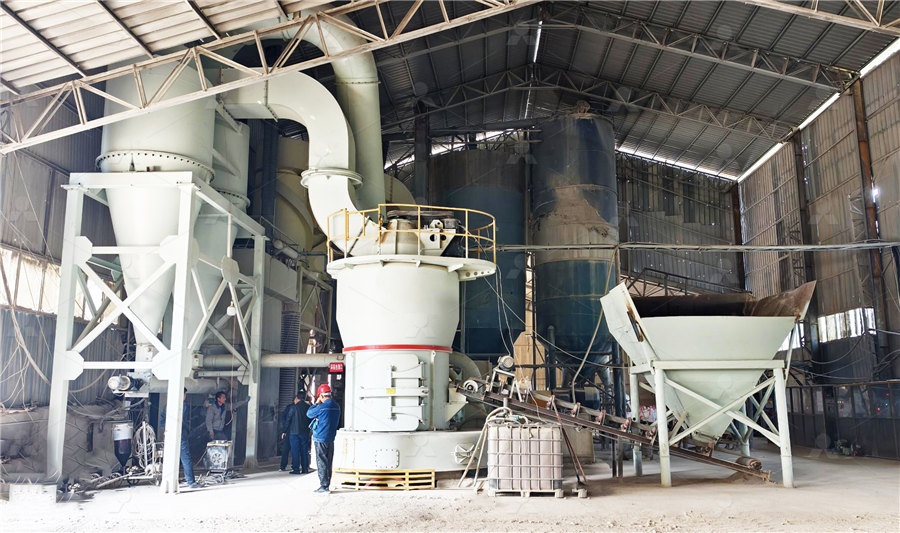
COAL
1 Fuel handling and storage – raw coal receiving, storage and handling 2 Fuel preparation – raw coal grinding 3 Fuel conveying – fine coal storage and conveying for an indirect firing system 4 Fuel conveying – fine coal conveying for a direct firing system 5Spillage and unsafe conditions at coal mill Kiln burner (firing system)2002年9月1日 This paper presents a novel coal mill modeling technique using genetic algorithms (GA) based on routine operation data measured onsite at a National Power (NP) power station, in England, UKCoal Mill Modeling by Machine Learning Based on onSite Coal mill hot air inlet temperatures should never be more than 600 F and the outlet temperature should not exceed 200°F on Raymond coal mills If the flow of raw coal to the coal mill is interrupted for any reason (for example: plugging, failure of the coal feeder, etc), the outlet temperature of the coal mill can quickly climb to dangerous Coal Grinding Systems Safety Considerations PEC Consulting Feeding device sends raw coals into drying oven; drying oven is equipped with special lifting plate to scatter coal and make coal get strong heat exchange so that raw coal is dried; dry raw coal is sent into grinding storehouse via doublecompartment plate is equipped with grinding balls so that raw coal can be crushed and ground into coal powder in this compartment, while, a Air Swept Coal Mill Cement Plant Machinery
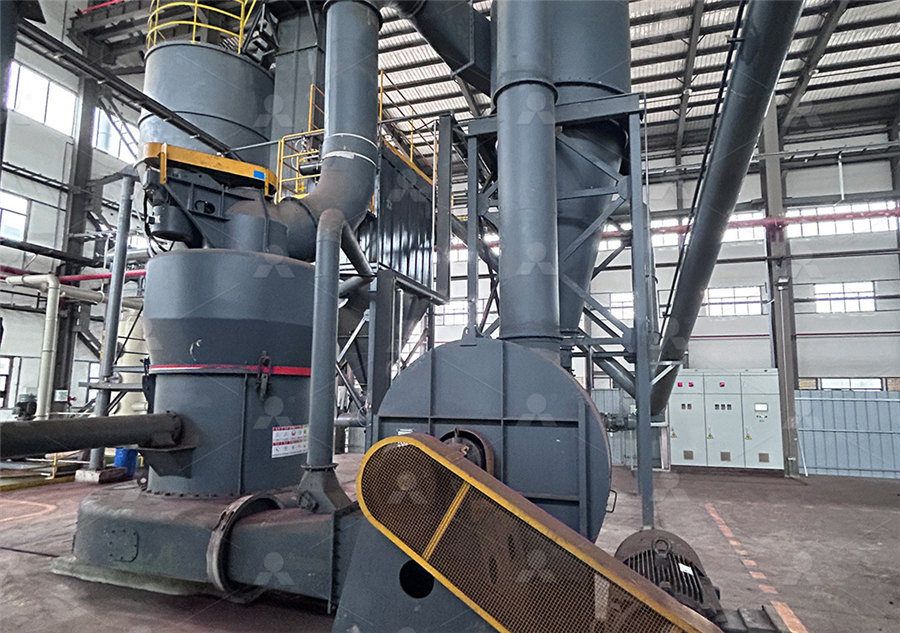
Coal mills for all requirements Gebr Pfeiffer
Hard coal is a sedimentary rock which was formed by deposition and carbonization of plant remains It is hard and resistant More than 50% of its weight is made up by carbon Therefore it is classified as highrank coal Other fossil fuels like subbituminous coals with high moisture contents as well as brown coal and lignite are lower ranked2011年10月21日 In the case of coalgrinding or storage (as one might find in a cement plant) it is not possible to remove the fuel (coal) or ignition source (grinding energy, heat, static charges) and so one has to concentrate on removing the third necessary component O 2 This fact has given rise to inerting systems that rely on the use of inert gasesEmergency inerting systems for coalgrinding applicationsThe grinding roller is driven by a motor to make the grinding disc rotate in the coal mill shell The coal is placed between the grinding discs, and due to the relative movement of the grinding rollers and the grinding discs, the coal is crushed and ground into fine powderAir Swept Coal Mill Cement Plant Equipment Coal Grinding Millangle, the dissociation characteristics of coal slime under different grinding conditions were studied The grinding method was determined by wet grinding, and UCC was prepared by shear flocculation flotation 2 Materials and methods 21 Materials The slime sample was collected from a coal preparation plant located in Shanxi Province, China Influence of grinding methods on the preparation of ultraclean coal
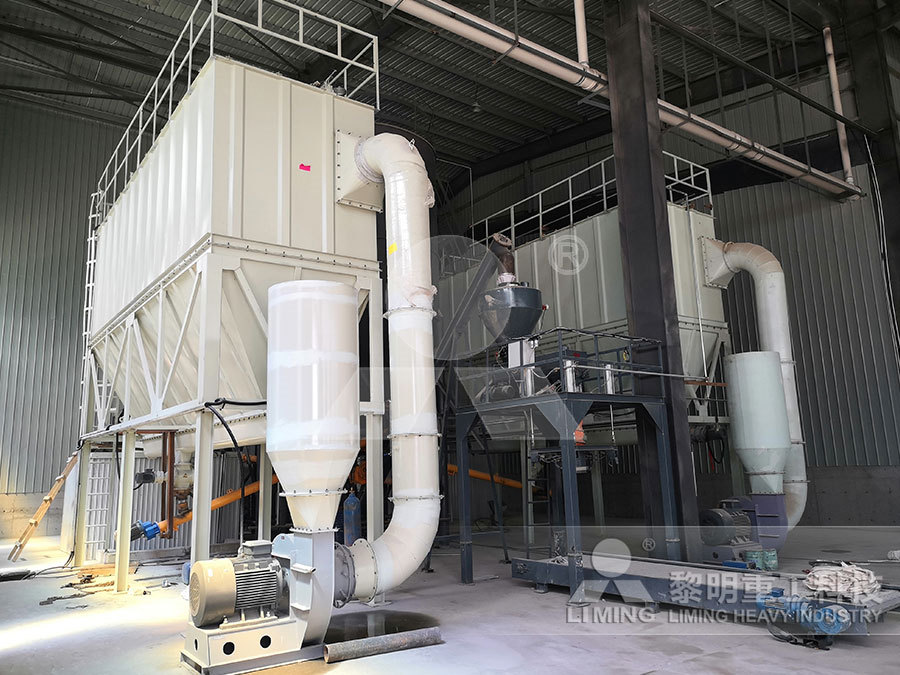
Design of coal preparation plants: problems and solutions
Coal particle size after grinding simulation Grades, mm Raw coal After grinding yield % ash % yield % ash % 150200 7,4 11,8 4,3 14,6 100150 24,0 21,3 13,8 26,4 Over 100 postsimulation of grindability by machine grades (GOST 1010084) Due to changes in particle size washability varies by machine size grades (GOST 1010084)2003年1月1日 The factors affecting pulveriser performance include grindability of coal, moisture content of coal, size of input coal, wear condition of grinding elements and classifier, fineness of pulverized Coal mill modeling by machine learning based on onsite measurements Type 2: Coal grinder machine Coal crusher is referred to as a vertical composite crusher It is also known as a stone pulverizer and compound crusher It not only cleverly adopts the working principle of stone beating stone Moreover, it also Charcoal Shredder Coal Grinder Machine Shuliy A HAZOP study of a typical operating Coal Grinding and Firing System encompasses the following areas: a) Fuel handling and storage – Raw coal receiving, storage and handling b) Fuel preparation – Raw coal grinding c) Fuel conveying – Fine coal storage and conveying for an indirect firing systemCOAL GRINDING AND FIRING SYSTEMS HAZOP ANALYSIS
.jpg)
Improved coal grinding and fuel ow control in thermal power plants
The unground coal consists of the raw coal supplied by the feeder belt and coal rejected in the classi cation process The mass of pulverized coal on the table is dependent on the grinding rate Mass of coal suspended in the pneumatic transport, m cair (t) is in uenced by the primary air ow with ne coal particles from the table, w pc (t), and The effect of wetgrinding on coal mechanochemical predesulfurization Jinting Liua, Jing Zhaob, Suqian Gua, and Xiaoheng Fua aSchool of Chemistry and Environmental Engineering, China University The effect of wetgrinding on coal mechanochemical pre 2016年10月5日 In this chapter an introduction of widely applied energyefficient grinding technologies in cement grinding and description of the operating principles of the related equipments and comparisons over each other in terms of grinding efficiency, specific energy consumption, production capacity and cement quality are given A case study performed on a EnergyEfficient Technologies in Cement Grinding IntechOpenThe raw coal and lump coal are coarsely crushed by the crusher and crushed to 3mm to meet the feed size of the CWS ball mill The cleaned coal obtained by flotation is mixed and stirred in a mixing tank by adding a certain proportion of water Cleaned coal grinding The mixed slurry of clean coal is sent to the coal water slurry ball mill for Coal Water Slurry Ball Mill
.jpg)
(PDF) MPS mills for coal grinding ResearchGate
2014年1月1日 The kiln tail, coal mill, crushing and cement mill mainly emitted larger particle sand their size distribution were related to the physical properties such as crushing and grinding of raw 2020年4月7日 flow, decrease of grinding capacity or high coal powder moisture, which cause that the raw coal in the mill cannot be ground immediately or t he coal powder in the mill cannot be brought out quicklyModeling of Coal Mill System Used for Fault Simulation2021年3月12日 The grinding plant may be operated under noninert conditions, when grinding low explosive coal types With noninert operation exhaust air from the clinker cooler could be used for drying the coal As a common safety precaution the coal grinding system is operated under inert conditionsMPS mills for coal grinding AYS Engineering2022年2月24日 Coals from the bunkers are transported to the raw coal feeder (RCF), which controls the degree of loading of the mill From the RCF , coal enters the throat of the Sh25A mill,Improving the efficiency of the coal grinding process in ball drum
.jpg)
Sustainability of coal mines: Separation of clean coal from the fine
2021年1月31日 However, the desulfurization rate was almost zero by drygrinding The specific surface area of coal samples and its contents of FeSO 4 , and Fe 2 (SO 4) 3 changed from 3570 m 2 g −1 , 0159% The raw material of coal powder is coal with various hardness, and it drying in the coal mill grinding process to obtain finished coal powder which can be efficiently burned Coal ball mills are widely used in the cement industry and thermal Coal Ball Mill Grinding for Different Kinds of Coal is crushed to desired fineness between spheres or cylindrical rollers After that, air from the boiler is heated to around 330°C (650°F) The raw coal is then fed into the pulverizer where it is ground into fine coal particles What are the Advantages of Pulverized Coal? Pulverized coal produces a larger amount of heat than traditional coalCoal Crushers Coal Pulverizers Mills Williams Crusher2020年8月21日 For raw bark, much less grinding energy is required compared to those for raw stem wood and stump, and torrefaction has minor effects on the grindability of bark(PDF) Effect of Biomass Carbonization on the Grinding of Coal
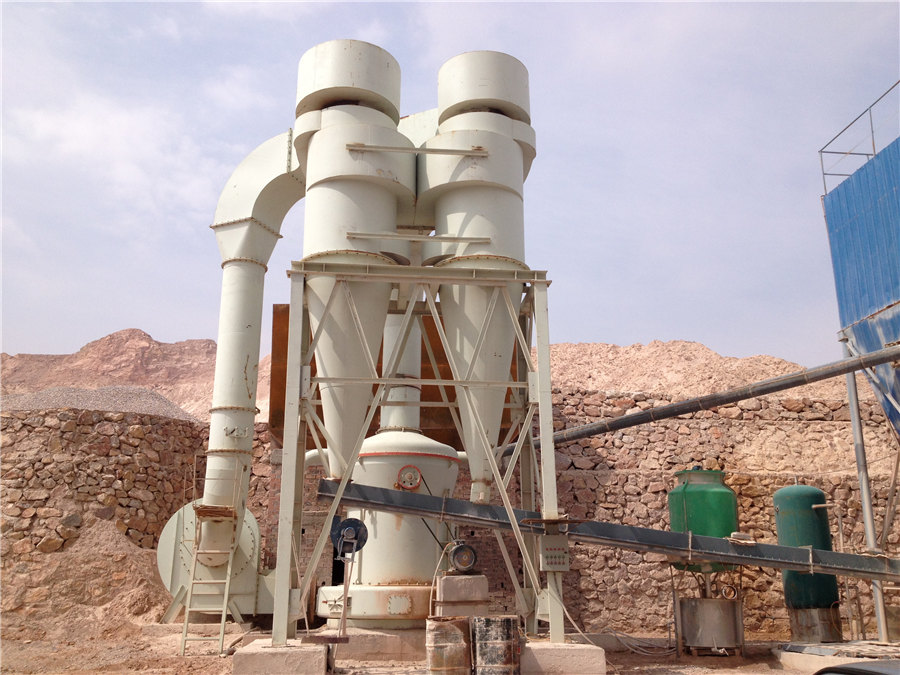
Pulverized Coal Preparation Pulverized Coal Grinding Plant Coal
Our Pulverized Coal Preparation Production Line is composed of Raw Coal Storage Transportation System, Grinding System, Dust Collecting System, Electrical Instrument Automation System By the consideration of safety protection for equipment and system, explosion venting valve and nitrogen protection port are adopted at hot air inlet pipeline of Air Vertical coal mill is the coal milling machine SBM designed for coal grinding process Coal mill operationCoal grinding millCoal milling machine Get Info; Coal MillBall Mill,Ball Mill Supplier,Ball Mill For Sale, Coal mill is an important auxiliary equipment for coalpowder furnace, it has three methods to crush the coal lump and grind them grinding process in coal KOOKSBall mills for cement raw material and coal equipped with a drying compartment adequately air swept with hot gas (2535M/sec above the ball it would be seen that the most significant process and types used for raw material grinding operations in modern cement industry are: Process: Dry Closed circuit drygrinding Type of mill: Ball and Raw Material DryingGrinding Cement Plant Optimization2022年12月19日 The longflame coal used in the test was obtained from Inner Mongolia, China The proximate analysis result of coal sample is presented in Table1 Table 1 Proximate analysis of coal sample (air dried) M ad (%) A ad (%) V ad (%) FC ad (%) 538 2013 3524 3925 Due to the high content of raw coal ash, the density composition of raw coal and theProduction of UltraClean Coal by the Combined Method of Grinding
.jpg)
Optimization of operating conditions on ultrafine coal grinding
2022年4月16日 This study investigated ultrafine coal grinding performance of four low to moderatecost grinding media in a laboratory stirred mill Kinetic grinding tests showed that silica beads generated