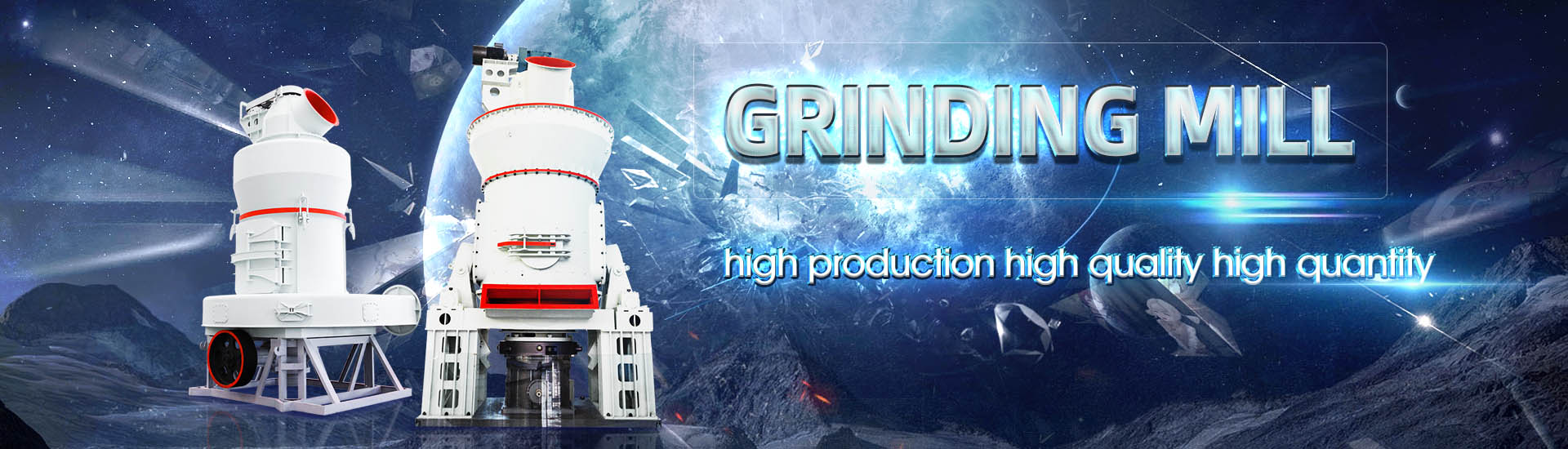
HOME→What is a palatal ore grinding mill What is a palatal ore grinding mill What is a palatal ore grinding mill
What is a palatal ore grinding mill What is a palatal ore grinding mill What is a palatal ore grinding mill
.jpg)
Grinding Mills — Types, Working Principle Applications
Extreme temperatures, impact velocity, mill load, grinding media, ore types, and applications are some of the factors to be considered while installing new liners2023年7月20日 Ore grinding is a process to further reduce and disperse the ore particle size In the mineral processing industry, ore grinding is the particle size preparation before the Ore Grinding SpringerLinkIt is performed in cylindrical steel vessels that contain a charge of loose crushing bodies—the grinding medium—which is free to move inside the mill, thus comminuting the ore particles Grinding Mill an overview ScienceDirect Topics2017年10月3日 Extreme temperatures, impact velocity, mill load, grinding media, ore types, and applications are some of the factors to be considered while installing new liners Ball Mills Grinding Mill Types, Working Principle Applications Savona
.jpg)
Ore Grinding Methods and Process of Ore Grinding
Ore grinding is a process to further reduce and disperse the ore particle size In the mineral processing industry, ore grinding is the particle size preparation before the separation of the Types of mill include the following: Materials recovery facility, processes raw garbage and turns it into purified commodities like aluminum, PET, and cardboard by processing and crushing List of types of mill Wikipedia2016年11月7日 These processes for the reduction of the particle size of a granular material are known as “milling” or “grinding” and it appears that these names are used interchangeably, Grinding Mills – Common Types 911 MetallurgistGrinding mills operate on the principle of breaking down ore particles into smaller sizes through the action of abrasion The primary types of grinding mills include ball mills, rod mills, Understanding the operation of grinding mills in the mining and
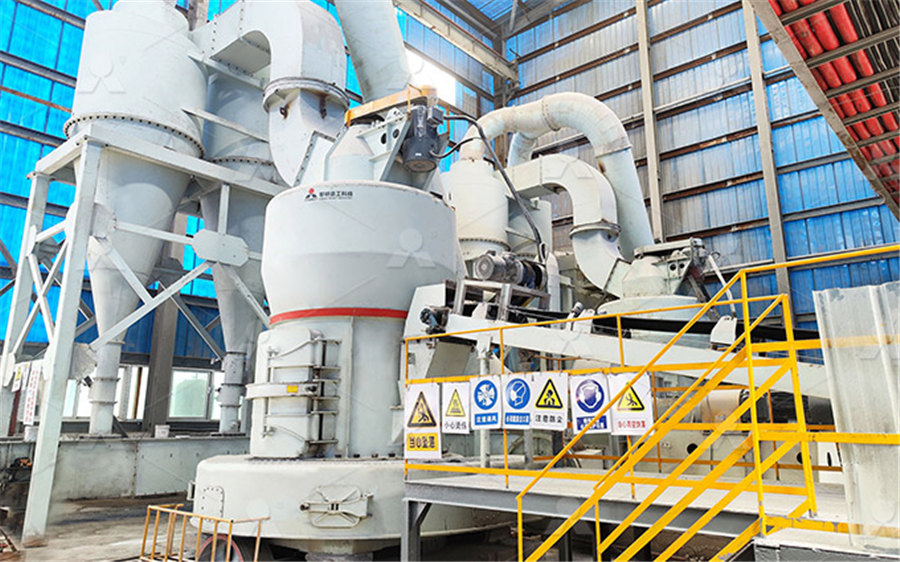
Ball mill Wikipedia
A ball mill, a type of grinder, is a cylindrical device used in grinding (or mixing) materials like ores, chemicals, ceramic raw materials and paints Ball mills rotate around a horizontal axis, partially 2021年7月3日 Precision grinding is a middleground between metal removal and part size control, and serves as the basis for creep feed grinding, slot grinding and highefficiency deep grinding In ultraprecision grinding, little to no actual Machining 101: What is Grinding? Modern Machine 2024年7月12日 Grinding media, also known as grinding medium, are essential in ball mills, as they help to reduce the size of the ore particles through both attrition and impact We mainly use a ball mill for mixing and grinding What Is a Ball Mill and How Does It Work? Certified 2017年5月8日 A lifter mill of 6 ft diameter, revolving at 187 rpm, is grinding coal The body of the mill is divided into two sections: one section, 75 ft long, being charged with 5 tons of steel balls, of 2 in average diameter, and the Grinding Mill Power 911Metallurgist
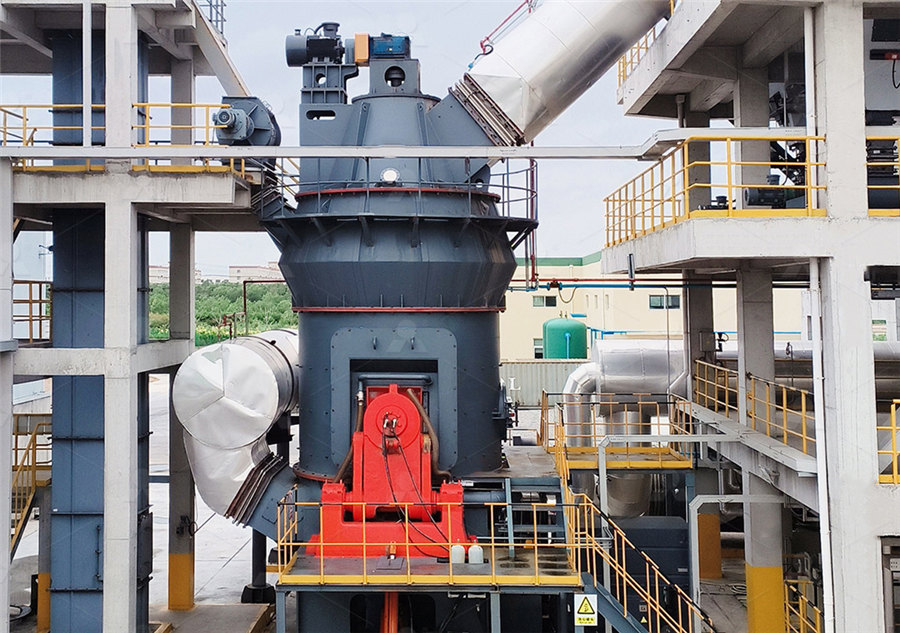
How to choose a suitable ore powder grinding mill?
2023年10月17日 Factors for choosing a suitable ore powder grinding mill 1 Raw material characteristics: Different raw materials have different hardness, humidity and grinding and crushing properties, and the corresponding ore powder grinding mill needs to be selected to meet the processing requirements 2 Production capacity: Determine the required processing Grinding Mills Barry A Wills, James A Finch FRSC, FCIM, PEng, in Wills' Mineral Processing Technology (Eighth Edition), 2016 71 Introduction Grinding is the last stage in the comminution process where particles are reduced in size by a combination of impact and abrasion, either dry, or more commonly, in suspension in waterGrinding Mill an overview ScienceDirect Topics2017年7月20日 Autogenous grinding is favored when the ore is quite competent and a fine grind is required The Union Corporation in a paper on the reduction works at the Kinross Mine gives some data on grinding mill performance with and without grinding balls being used as supplemental mediaAutogenous Grinding Semi Autogenous Grinding Circuits2024年4月26日 The choice of grinding mill depends on factors such as the desired product size, capacity requirements, and energy consumption b Autogenous and SemiAutogenous Mills: In some cases, autogenous (AG) and semiautogenous (SAG) mills are used for grinding These mills utilize the ore itself as the grinding media, reducing the need for additional Iron Ore Processing: From Extraction to Manufacturing
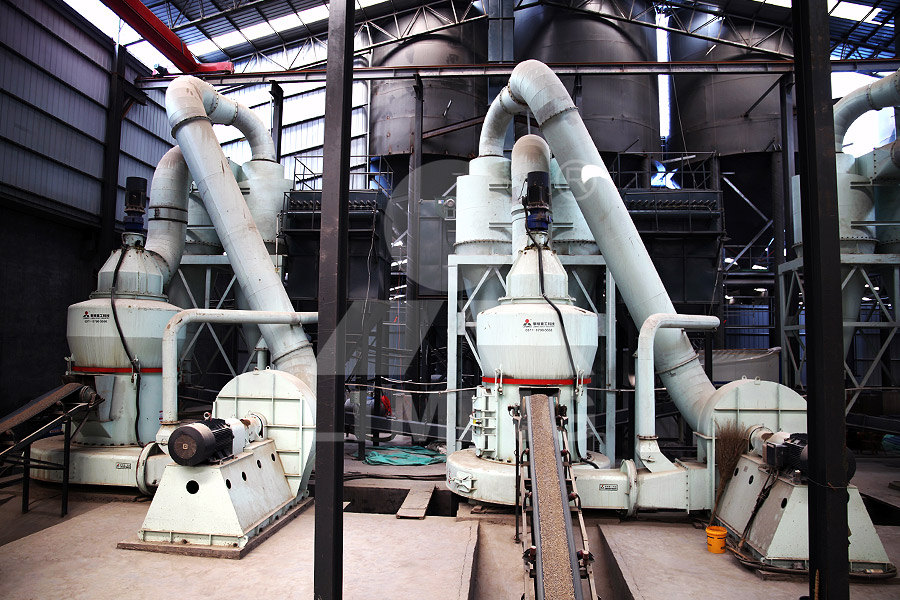
Semi Autogenous Grinding Mill ScienceDirect Topics
An autogenous mill of ID 67 m and an effective grinding length of 21 m was fed with ore of SG 38 to 20% of its volume The mill was operated continuously 24 hours per day at 1200 t per day and 75% of the critical speed The solids in the mill charge were at 80% solids Estimate:12016年7月8日 UNTIL THE THIRD THEORY OF COMMINUTION of “Work Index” method of determining crushing and grinding mill size was introduced, there was no way of accurately figuring the most applicable, most economical size of crushing and grinding mill Naturally, with little or no factual operating data correlated in useful form, it was easy enough, even for the Equipment Sizing: Crusher or Grinding Mill 911Metallurgist2015年8月6日 It affects retention time and helps distribute the ore throughthe mill so each piece of rock will come in contact with the surface of the rods The % solids by volume of the rod mill discharge Rod mill grinding efficiencies have been shown to increase in the range of 5 to 15% with more dilute discharge slurry (ie, Ball Rod Mill Density – How Water Impacts GrindingGrinding Mills: Ball Mill Rod Mill Design PartsCommon types of grinding mills include Ball Mills and Rod Mills This includes all rotating mills with heavy grinding media loads This article focuses on ball and rod mills excluding SAG and AG Grinding Mills 911Metallurgist
.jpg)
Calculate and Select Ball Mill Ball Size for Optimum
2013年8月3日 In Grinding, selecting (calculate) the correct or optimum ball size that allows for the best and optimum/ideal or target grind size to be achieved by your ball mill is an important thing for a Mineral Processing Engineer AKA A Wet Pan Mill also known as an amalgamation grinding mill, or gold grinder mill, is a versatile ore grinding pan mill for wet materials It’s the best replacement for a mediumsmall capacity ball mill, owing to its excellent performance for wet Wet Pan Mill Ore Grinding Equipment JXSC Machine2024年5月17日 A SAG (SemiAutogenous Grinding) mill is a giant rotating cylinder filled with grinding media and the ore being reduced As the mill rotates, the grinding media lifts and the impact crushes the feed material SAG mill control refers to the practice of managing the mill load, which is the amount of material inside the mill at any given timeA guide to SAG Mill management2016年6月1日 So from that you can see why it is called a wet tumbling mill The ore is ground wet and the mill revolves This causes the grinding media inside of it to tumble grinding the ore Historically there has been three basic ways of grinding Rod Mills: Efficient Grinding Solutions for Mining
.jpg)
Grinding Mill an overview ScienceDirect Topics
To achieve this objective an attempt is made to stabilize the operation by principally controlling the process variables The main disturbances in a grinding circuit are: 1 change in ore characteristics (ore feed rate, grindability, feed particle size distribution, mineral composition and mineral characteristics like abrasiveness, hardness), 22023年7月20日 Therefore, the rod mill is mostly used for coarse grinding of the previous period of ball mill, or grinding of brittle materials and materials against overcrushing, such as tungsten and tin ore before gravity separation; and (3) autogenous mill – it refers to the materials which themselves are collided and ground mutually to be crushed when the grinding mill rotates, and Ore Grinding SpringerLink2020年1月27日 Grinding mills are production critical equipment, continuously grinding crushed ore to liberate valuable metals ahead of the concentration process Numerous factors must be considered when selecting a mill liner design, including required grinding action, mill size as well as ore and grinding media characteristics, among othersKey considerations when selecting a mill lining systemTable 1: Power Intensity of Different Grinding Devices Ball Mill is a 56m D x 64m L @ 26MW Tower Mill is a 25m D x 25m L @ 520KW Table 2: Mill Comparison of Media Size, Power Intensity, number of grinding media The ability to use smaller media is probably the dominant impact on grinding efficiency ItFine Grinding as Enabling Technology – The IsaMill
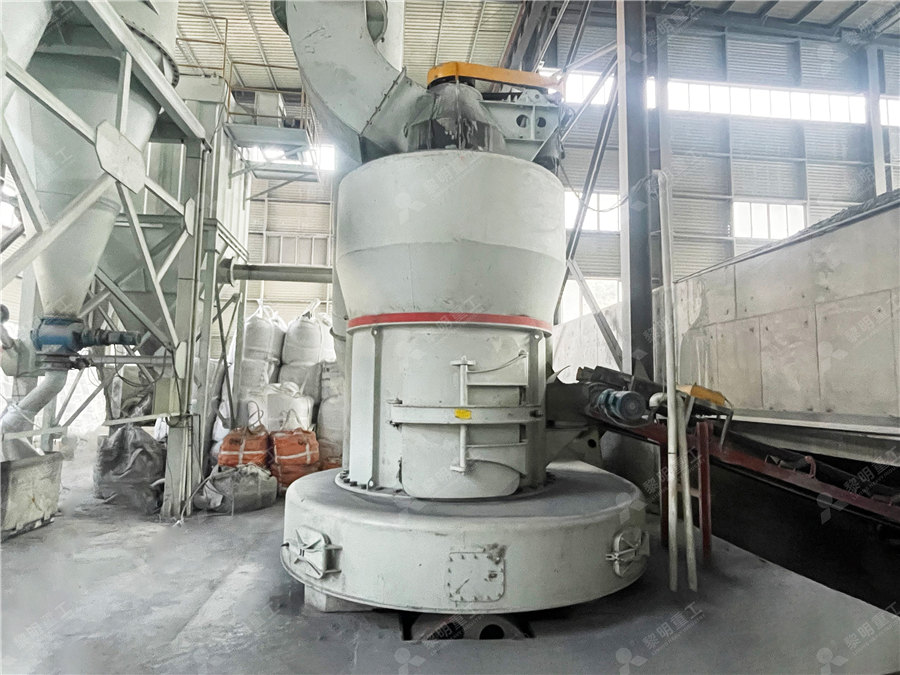
AMIT 135: Lesson 6 Grinding Circuit – Mining Mill Operator
Autogenous Grinding (AG) Mill Wet or dry; Primary, coarse grinding (up to 400 mm feed size) Grinding media is grinding feed; AG/SAG mills are normally used to grind runoffmine ore or primary crusher product Wet grinding in an AG/SAG mill is accomplished in a 2024年8月8日 In mining, a copper processing plant struggled with inefficient ore grinding using standard steel balls, leading to poor mineral recovery rates After analyzing their milling conditions, they opted for highdensity steel balls, which Ball Mill Success: A StepbyStep Guide to Choosing 2020年3月10日 Materials are added to the ball mill, at which point the balls knock around inside the mill How a Ball Mill Works Ball mills work by using balls to grind materials Materials such as iron ore, pain and ceramics are added to What Is a Ball Mill? Blog Posts OneMonroe2017年2月13日 In all ore dressing and milling Operations, including flotation, cyanidation, gravity concentration, and amalgamation, the Working Principle is to crush and grind, often with rod mill or ball mill, the ore in order to liberate the Ball Mills 911Metallurgist
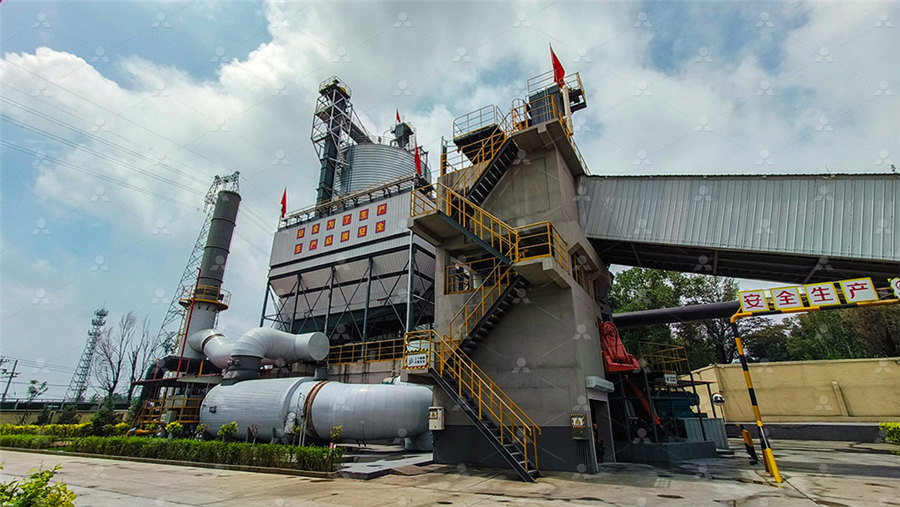
Ball Mill Rod Mill Design 911Metallurgist
2016年4月22日 In all ore dressing and milling processes, including flotation, cyanidation, gravity concentration, and amalgamation, it is necessary to crush and grind, often with rob mill ball mills, the ore in order to liberate the minerals In the chemical and process industries, grinding is an important step in preparing raw materials for subsequent treatmentMill drives are critical components of coal grinding mills, responsible for transmitting power from the motor to the grinding media Mill drives can be designed as gearless or geared systems, depending on the specific application and grinding requirements Mill Control SystemsWhat is a Coal Grinding Mill2017年10月26日 The following are factors that have been investigated and applied in conventional ball milling in order to maximize grinding efficiency: a) Mill Geometry and Speed – Bond (1954) observed grinding efficiency to be a function of ball mill diameter, and established empirical relationships for recommended media size and mill speed that take this factor into Factors Affecting Ball Mill Grinding Efficiency2016年10月12日 Stockpiling of ore ahead of the mill can aid in smoothing out some of the fluctuations although it must be stored in such a manner that no segregation occurs In operating a grinding circuit, like any other unit process, variables key to the performance must be dealt with Below are some of the principal variables affecting control of grinding Closed Circuit Grinding VS Open Circuit Grinding
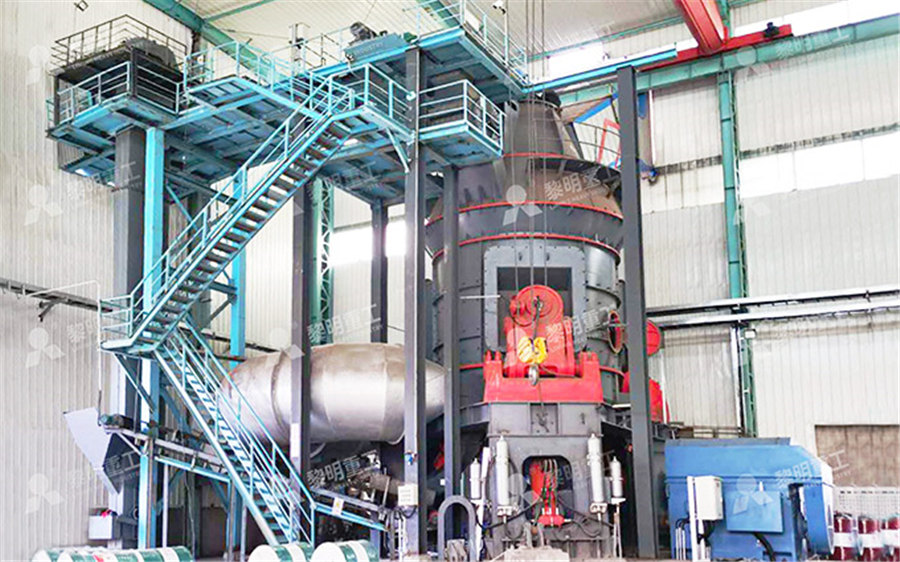
What are the types of industrial grinding mills?
2021年7月7日 It is an industrial grinding mill with extremely highcost performance for enterprises such as ore grinding powder The YGM Raymond mill produced by SBM is also an efficient automatic milling device The grinding fineness is not as high as that of an ultrafine mill, generally around 600 meshes, but it can grind higher hardness ore materials, and the price is 2020年6月23日 The installed motor power for a grinding mill is a key indicator, along with the physical dimensions of the mill itself, of the capacity of the mill to process tonnes of ore When an overflow mill is not drawing all available motor power during normal operation, this can indicate that there is potential to increase the mill throughput or Converting a ball mill from overflow to grate discharge Metso2019年4月16日 Conference: Applying a Successful Technology from the Cement Industry: Advantages of Grinding Ore in a VerticalRollerMill; At: Antalya, Türkey(PDF) LEARNING FROM OTHER INDUSTRIES; WHY THE VRMHGM ultrafine grinding mill can process nonmetallic ores with Mohs hardness less than 7 The equipment has stable operation, simple operation, long service life, low carbon and environmental protection There are 5 models of HGM SBM Ore Ultrafine Grinding Mill
.jpg)
Understanding the operation of grinding mills in the mining and
1 Grindability: The grindability of the ore affects the efficiency of the grinding mill Harder ores require more energy and longer grinding times, which can impact the mill's performance and operational costs 2 Media andliner Wear: The condition of the grinding media and liners affects the mill's efficiency2021年11月26日 Spodumene grinding mill machine is mainly used for lithium pyroxene grinding, which can easily deal with ore grinding with hardness below Mohs hardness level 7 It occupies a small area and saves 30% – 50% of energy consumption compared with ordinary mills and ball mills The main types are pendulum Raymond mill and vertical mill IWhat is a spodumene grinding mill? – gkmillSAG MILL TESTING AN OVERVIEW OF THE TEST PROCEDURES AVAILABLE TO CHARACTERIZE ORE GRINDABILITY AUTHOR: FO VERRET, G CHIASSON AND A MCKEN SGS KEYWORDS Comminution, grindability, grinding, SAG mill, AG mill, milling, HPGR, work index, pilot plant INTRODUCTION The resistance of ore samples to breakage (or hardness) is SAG Mill Testing Test Procedures to Characterize Ore Grindability2015年7月1日 Crushing reduces particle size of runofmine ore to such a level that grinding mill can further grind it until the mineral and gangue is substantially produced as separate MINUTION: Liberation, Crushing, Grinding
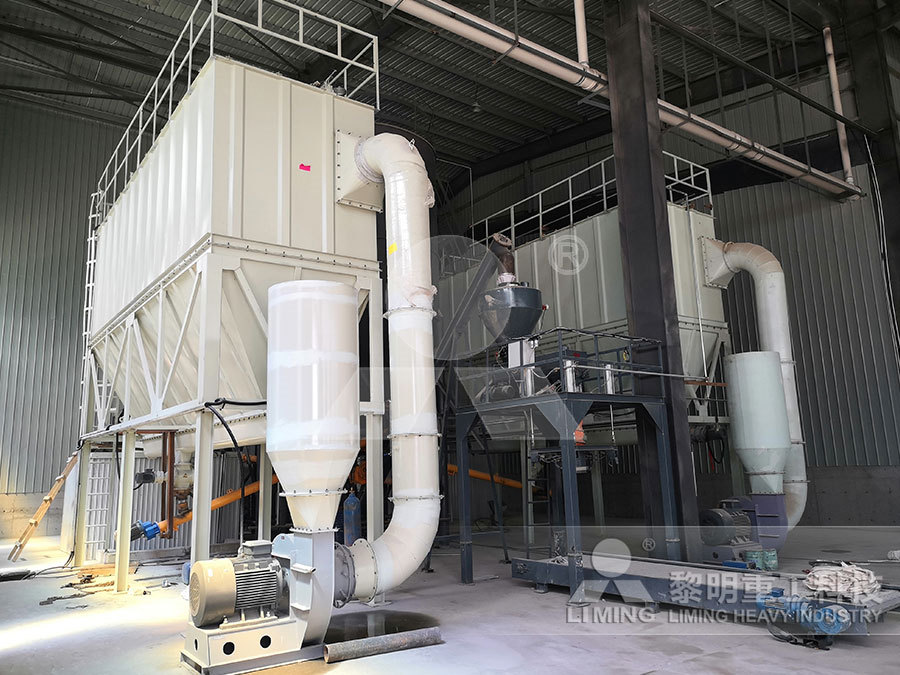
How to Size Design a Regrind Ball Mill 911Metallurgist
2018年4月8日 Referring to Table VI the L/D can be between 175 and 20 or even greater Referring to Table VII a 305 meter (10 foot) by 305 meter (10 foot) overflow ball mill with a 40 percent by mill volume ball charge, new liners and 50 mm (2″) balls draws 491 HP Using equation 5 there will be a loss of 055 Kw (074 Hp) per metric tonnes of ballsIn this study, a fuzzy logic selftuning PID controller based on an improved disturbance observer is designed for control of the ball mill grinding circuit The ball mill grinding circuit has vast Relationship between SAG mill power draw, bearing pressure and 2015年4月15日 For each ball mill grinding step, a Bond ball mill grindability test for Work Index at one mesh size coarser than the desired 80% passing size and at the mesh size of or just finer than the 80% passing size If 50 mm x 75 mm (2″ x 3″) ore lumps are available an impact crushing Work Index testWhat Ore Testing is Required For Mill SelectionThe product from the AG mill is usually fed directly to a ball mill, which operates in a closed circuit with a cyclone Differences Between SAG and AG Mill Grinding media: SAG mills use steel balls as the grinding media, while AG mills use the ore itself as the grinding media Size: SAG mills are larger in diameter and shorter in length than What is the Difference Between SAG and AG Mill? ball mills
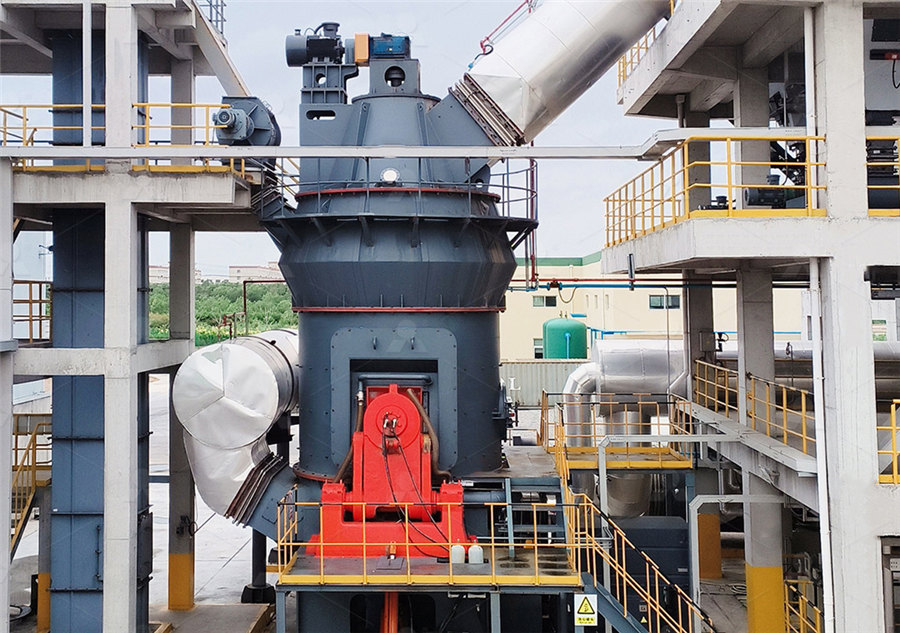
The six main steps of iron ore processing Multotec
This step involves the material being retained inside the mill for a specific time (with or without grinding balls) which is calculated by applying Bond’s work index to the process calculation This index takes into account the material ore hardness and feed size, mill speed, material recirculation, desired fineness, etc