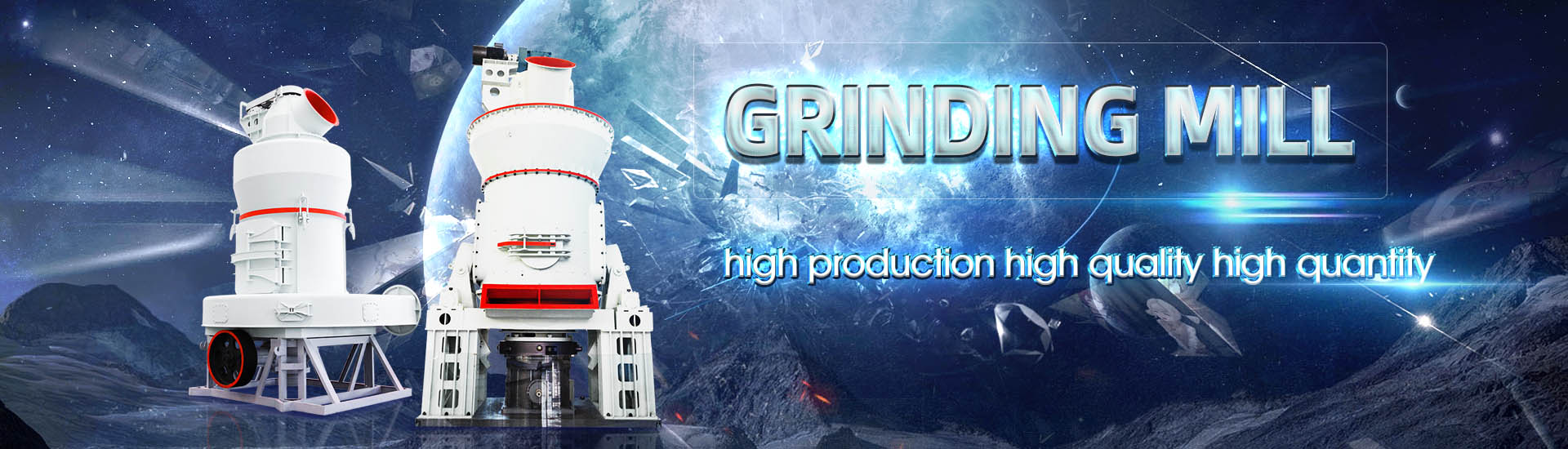
Ore mill particle size distribution coefficient
.jpg)
Effect of Solid Concentration on Particle Size
2024年6月11日 For example, sulfide ores with a particle size of approximately 15–150 μm have higher recovery in flotation plants, while much finer and much coarser particles result in a decline in flotation plant recovery [1]2018年6月1日 In this article, alternative forms of optimizing the milling efficiency of a laboratory scale ball mill by varying the grinding media size distribution and the feed material particle size Effect of ball and feed particle size distribution on the milling 2016年1月1日 A size analysis in mineral processing is primarily used to obtain quantitative data about the individual size and size distribution of particles in the process stream This is Particle Size Estimation and Distributions ScienceDirectFigure 615 Measured and predicted product particle size distribution from a 650HPVTM using a ball mill 110PREDICTING THE PRODUCT PARTICLE SIZE DISTRIBUTION FROM
.jpg)
All About Particles: Modelling Ore Behaviour in Mineral Elements
events undergone by individual ore particles depend on particle properties such as size, shape, mineralogy, and texture For instance, the largest and smallest particles in a tumbling mill 2021年9月5日 Several mathematical models have been developed to predict the PSDs of particulate materials, including lognormal, logistic, Gates–Gaudin–Schuhmann (GGS), and Modeling of Bauxite Ore Wet Milling for the Improvement of 2022年1月1日 In this study, the influence of grinding media diameter, stirrer tip speed, media fulling rate, and powder filling rate on the uniformity of particle size distribution and specific Effect of operating conditions on the particle size distribution and 2023年3月16日 Fractal dimensions for PSD of products were equal (241–263) and (249–260) for chalcopyrite and ilmenite ores, respectively Fractal dimensions of products are increased Fractal approach of particle size distribution description of ball
.jpg)
Research on prediction model of ore grinding particle
2019年3月28日 The results show that particle size distribution of crushing products under different crushing energies and ore particle sizes is obtained by drop weight test, and the crushing parameters A and b are calculated by fitting Abstract: In this work the ore particle size distribution is estimated from an input image of the ore The normalized weight of ore in each of 10 size classes is reported with good accuracy A Estimating Ore Particle Size Distribution using a Deep 2018年1月1日 "The particle size distribution characteristics of ground product can influence the quality of the classification overflow and the next beneficiation indexes in an ore concentrator Usually, the size distribution of ground product is considered to be determined by that of new ball mill feed However, based on large amounts of data from industrial grinding circuit surveys, The Correlation of Particle Size Distributions between Ground The ground ore from a ball mill is going for classification A size distribution for a hydrocyclone is shown in the table below, where the total weight fraction of the feed reporting to the underflow (U / F) is 652% and the remainder (348%) to Solved The ground ore from a ball mill is going for
.jpg)
Effect of Solid Concentration on Particle Size
2024年6月11日 In this study, the evolution behavior of the particle size distribution during the grinding process was examined with fractal theory According to the distribution index k of the Rosin–Rammler–Benne model, the 2017年2月1日 HPGR effect on the particle size and shape of iron ore pellet feed and broad particle size distribution of HPGR particles the sieve size 0045 mm or with Jar mill offered HPGR effect on the particle size and shape of iron ore pellet feed DOI: 101016/jfuel2021 Corpus ID: ; Quantitative evaluation of the influence of coal particle size distribution on gas diffusion coefficient by image processing methodQuantitative evaluation of the influence of coal particle size 2016年1月1日 The difference in particle size distributions generated by different techniques was shown in testwork on ultrafine grinding of a gold ore Figure 26 shows the laser size distribution of a screened −53 + 38 μm size fraction [7] Estimate the rate of reduction of the 1000 μm feed size during the mill operation 24Particle Size Estimation and Distributions ScienceDirect
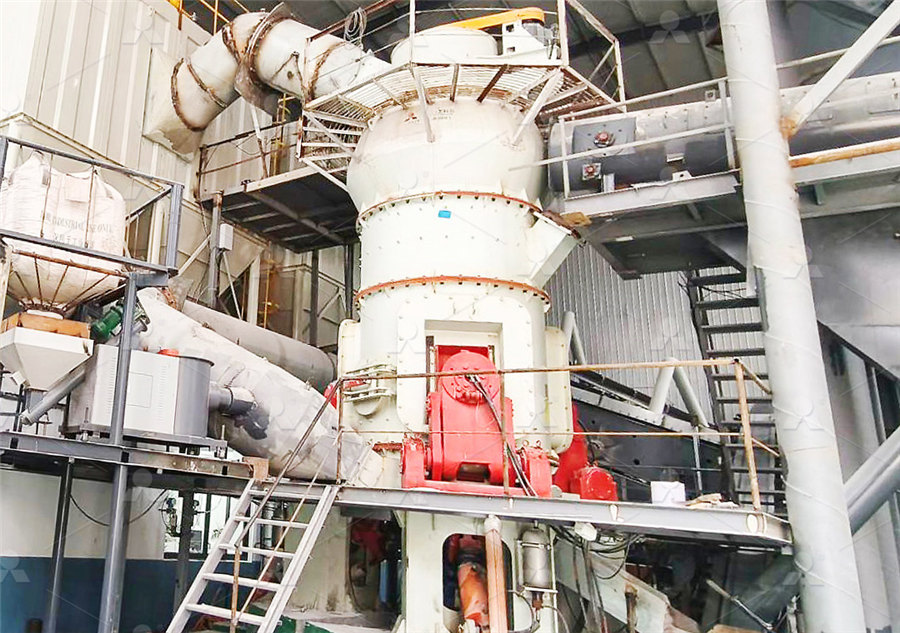
The particle size distribution analysis of the iron ore concentrate
For this purpose, six samples (pure calcite, pure magnetite, pure quartz, marmarite rock, travertine rock, and copper ore) with identical particle size distribution were comminuted by HPGR at 2022年3月30日 With the increasing awareness of sustainable mining, the cement tailings backfill (CTB) method has been developed rapidly over the past decades In the CTB technique, the two main mechanical properties engineers were concerned with are the rheological properties of CTB slurry and the resulting CTB strength after curing Particle size distribution (PSD) of tailings A Particle Size Distribution Model for Tailings in Mine Backfill2017年7月4日 In the higher range of mill speeds, the onset of cataracting of the media and the material in the empty space of the mill (as discussed in the section on holdup, there this phenomenon is reflected in higher holdup) leads to a reduced frequency of particle/ particle and particle/media interactions, again resulting in a decrease in the dispersion coefficientRod Mill Grinding 911Metallurgist2016年3月21日 Material in process often cannot be weighed without a disturbance of continuity; consequently, mill control must depend upon the sampling of material in flux From these samples the essential information is derived by means of analyses for metal content, particle size distribution, and content of water or other ingredient in the ore mon Basic Formulas for Mineral Processing Calculations
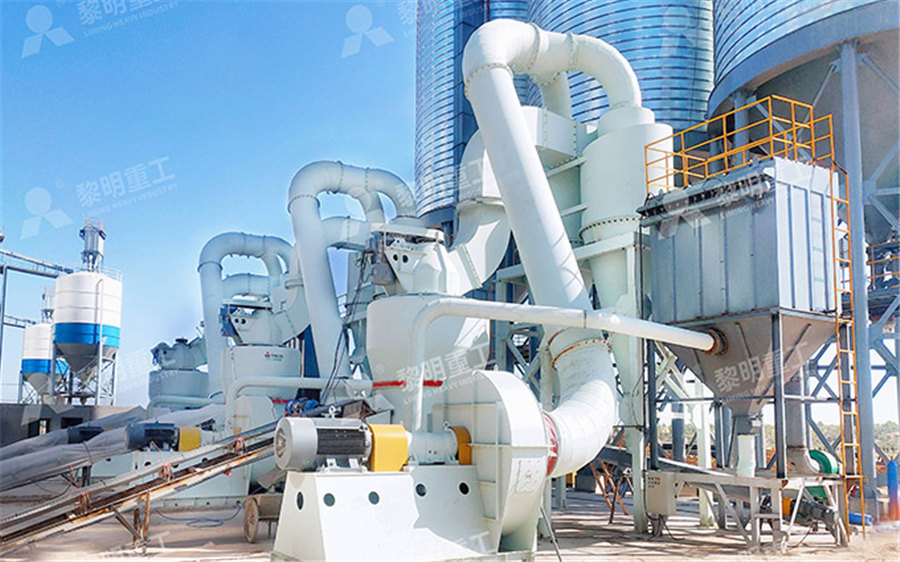
Assessment of different energybased breakage distribution
2024年11月1日 This study aimed at assessing various energybased breakage distribution functions B ij within the context of a population balance model (PBM) of copper ore milling in a wet stirred media mill (WSMM) First, drop weight impact tests were performed to determine the size distribution parameters, t nSecond, various t n models called t nfitted and t nregenerated 2022年6月30日 The raw ore exploited from the mining site for the mineral processing plant is a loose particle group with a maximum particle size of 1500 ∼ 1000 mm (openpit mining) or 600 ∼ 400 mm (underground mining), while the separation particle size of the concentrator is usually 02 ∼ 01 mm or finer [Yu et al, 2021; Guo et al, 2021], which suggests that the particle size of Characterization of chalcopyrite ore under high voltage pulse 2017年3月20日 An effect of a grinding method, that is ball mill and high pressure grinding rolls (HPGR), on the particle size, specific surface area and particle shape of an iron ore concentrate was studiedPhysicochemical Problems of Mineral Processing 2011年1月31日 The fineness of the product was evaluated by the median particle size in undersize distribution, and the shape of the particle size distributions by three different size ratios calculated using 10 Influence of dry and wet grinding conditions on fineness and
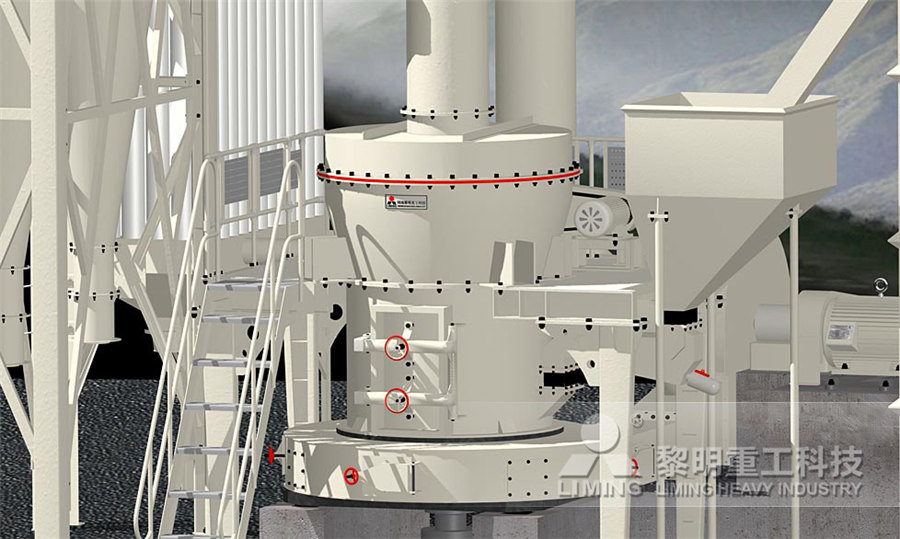
Particle size distribution analysis of iron ores/% ResearchGate
Download Table Particle size distribution analysis of iron ores/% from publication: Ore blending ratio optimisation for sintering based on iron ore properties and cost The iron ore blend for Download scientific diagram Particle size distribution of iron ore tailings from publication: Evaluation of Flotation Collectors in Developing Zero Waste Technology for Processing Iron Ore Particle size distribution of iron ore tailings2019年10月1日 Request PDF Wet and dry grinding of coal in a laboratoryscale ball mill: Particlesize distributions In this study, experimental data for wet and dryground coal samples under wet and dry Wet and dry grinding of coal in a laboratoryscale ball mill: Particle 2023年8月5日 With the increase of the pressure on the roll surface, the uniformity coefficient of the middle material increases, the particle size distribution is more concentrated, the crushing ratio increases, the output particle size becomes finer, and the finegrained part of the middle material after the crushing accounts for the majority; As the Factors affecting the particle size of the highpressure roller mill
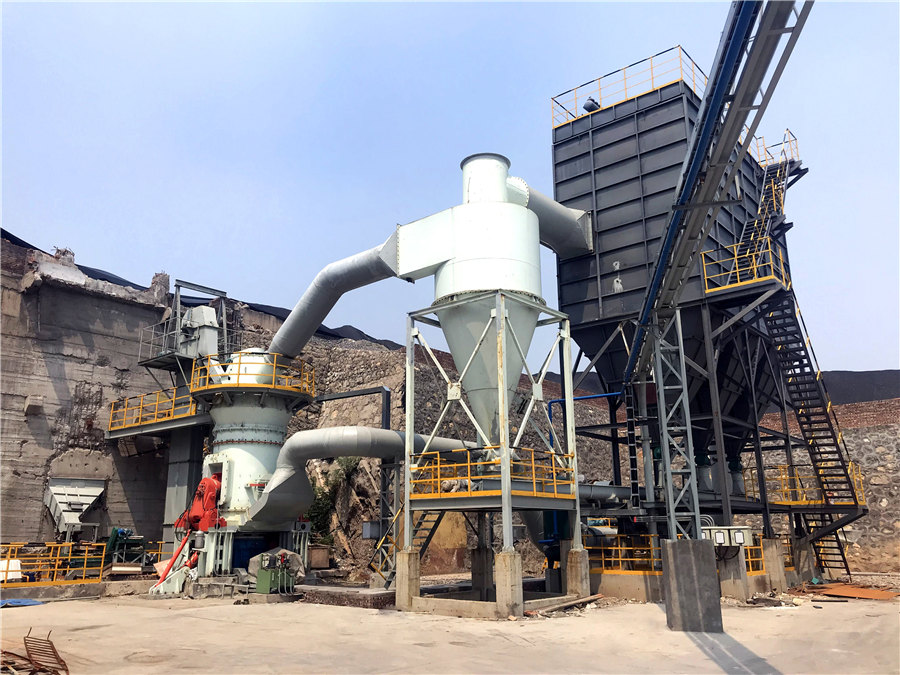
AP42, Appendix B2 Generalized Particle Size Distributions
B21 Rationale For Developing Generalized Particle Size Distributions Unprocessed Ores Category number: 3 Particle size (µm) ≤25 ≤6 ≤10 Generic distribution, Cumulative percent equal to or less than the size: 15 34 51 Gas fired a Rotary ore dryer a Oil fired a Roller mill 4 Coal fired a Impact mill 4product particle size distributions that are comparable across projects and ore types The authors have access to a database of ball mill and rod mill work index tests from commercial laboratories The Bond rod mill feed PSD models’ accuracy was Particle size distribution regressions for common laboratory 2022年9月1日 to 8 show coefficients x0 and k of the RRSB distributions as a function of the average angular velocity (Figure 6), power consumption (Figure 7), and specific comminution energy (Figure 8)EnergyDependent Particle Size Distribution Models 2021年1月22日 The wet grinding of iron ore powder was investigated using a stirred media mill In this study, the fitting degree of four cumulative undersize distribution functions was compared and the Impact of ball filling rate and stirrer tip speed on milling iron ore
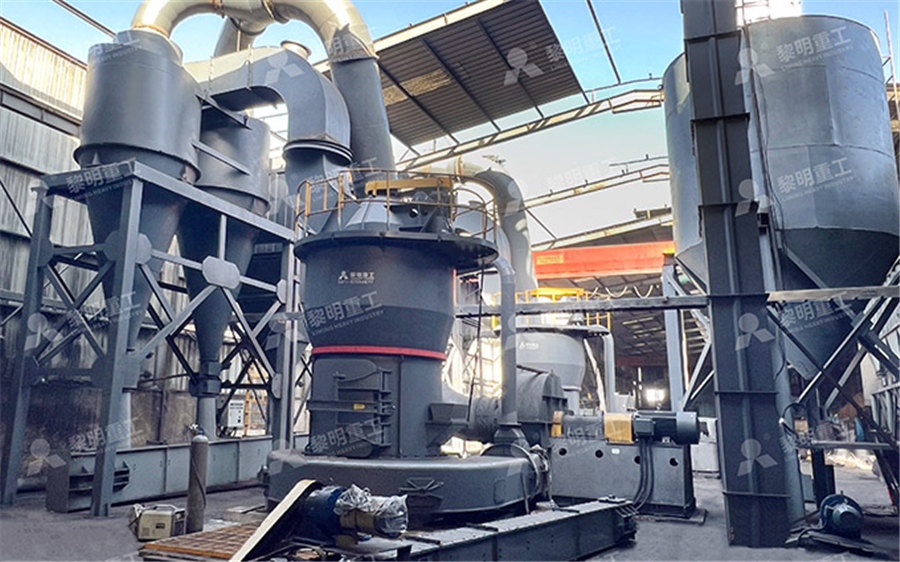
Particle size distribution of the tailings ResearchGate
Download scientific diagram Particle size distribution of the tailings from publication: Mill tailings based composites as paste backfill in mines of Ubearing dolomitic limestone ore This 2022年11月25日 neural networks (ANNs) to predict the particle size distributions (PSDs) of mill products PSD is one of the key sources of information after milling since it significantly affects the subsequentPrediction of Particle Size Distribution of Mill Products Using VTM mill processing copper ore Figure 612 Particle size distributions from a sampling survey around a 650HPVTM circuit 106 Figure 613 Breakage and selection functions curves for the Vertimill fresh feed sample from testing using a ball mill PREDICTING THE PRODUCT PARTICLE SIZE DISTRIBUTION Download scientific diagram Iron ore particle size distribution from publication: Impact Load Behavior between Different Charge and Lifter in a LaboratoryScale Mill The impact behavior Iron ore particle size distribution Download Scientific Diagram
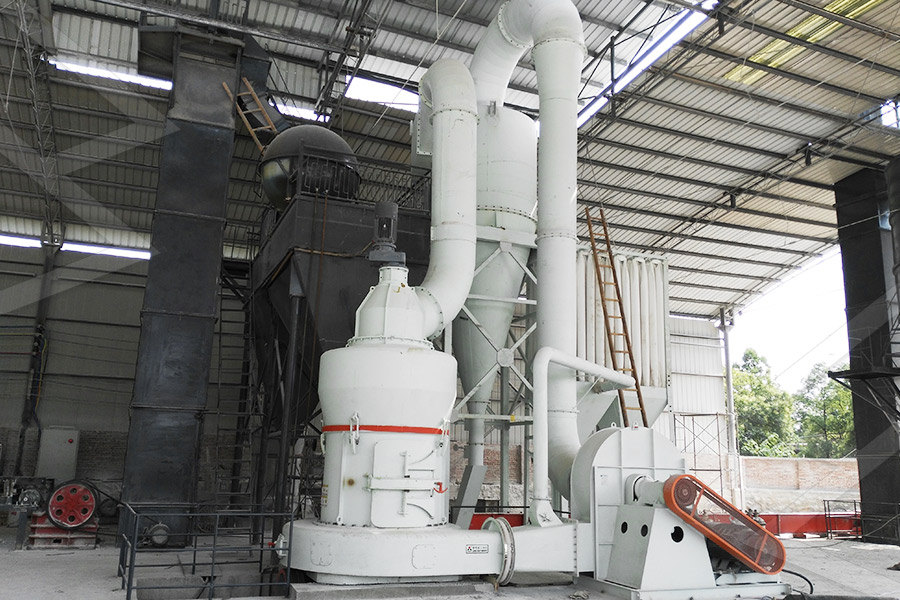
Particle size analysis and distribution ResearchGate
2015年8月21日 Particle Size Distribution is usually expressed from the technique by which it is determined Particle Technology Labs compressibility, flow function coefficient, cohesion, 2019年3月28日 In the ball mill, the main grinding method was the impact of the steel ball medium with the finer ore particles, and the Ecs was high because the weight of the single steel ball was significantly Research on prediction model of ore grinding particle size distribution2009年6月1日 Biomass particle size impacts handling, storage, conversion, and dust control systems Switchgrass (Panicum virgatum L) particle size distributions created by a knife mill were determined for Knife mill operating factors effect on switchgrass particle size A new method, staged flotation for effectively increasing the recovery of ultrafine copper oxide ore with a new type of collector (ZH1, C35 carbon chain xanthate) is proposed for the first timeParticle size distribution (PSD) of the mill feed
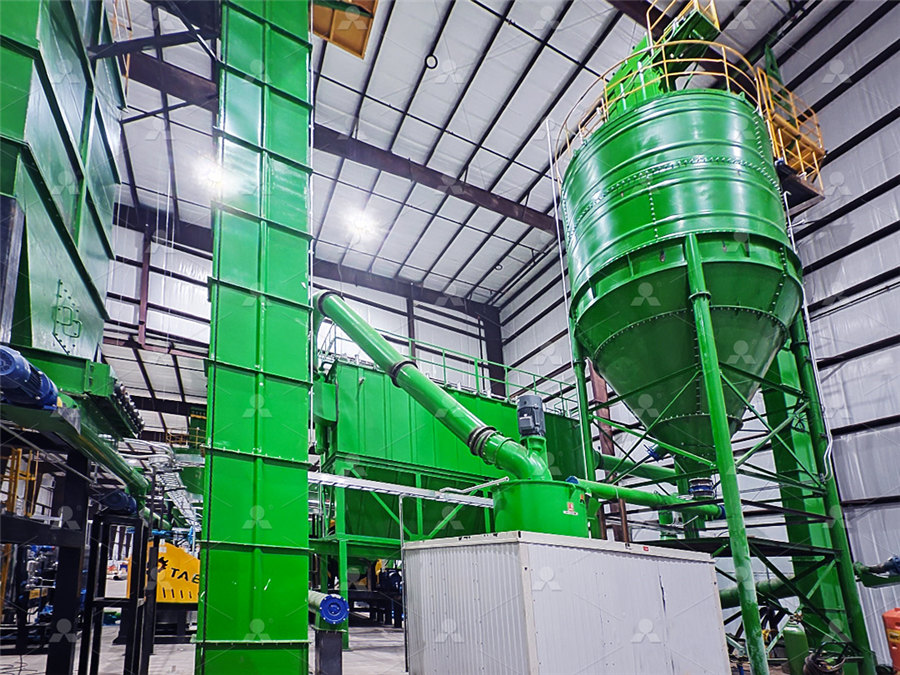
HPGR effect on the particle size and shape of iron ore pellet feed
Particle size distribution Sieve analysis A Retsch (AS200) analytical sieve shaker was used to determine the size distribution of each sample in the range of 53–500 µm Hundred grams of riffled 2021年8月9日 The obtained fractal dimensions of the particle size distributions for the particles crushed by the jaw, cone, and roll crushers were in the range of (216–238), (213–231), and (223–246 Fractal dimension of crushing products: effects of feed size 2021年1月19日 Moisture of bulk material has a significant impact on energetic efficiency of dry grinding, resultant particle size distribution and particle shape, and conditions of powder transport As a consequence, moisture needs to be MeasurementBased Modelling of Material 2024年9月15日 Prediction of particle size distribution of grinding products using artificial neural network approach the coefficient of determination between the predicted and true labels for the PSD improved to approximately 099 Both ores were ground using a hammer mill and sieved to conduct singlefraction grinding testsPrediction of particle size distribution of grinding products using
.jpg)
EnergyDependent Particle Size Distribution Models for MultiDisc Mill
2022年9月1日 The purpose of this paper was to develop models for the particle size distribution –Bennet distribution can be used to describe the particle size distribution of biomaterials ground in a multidisc mill Coefficient x 0 for RRSB distributions In the studies of ref [69,70], the energy–size reduction model for ores 2020年1月3日 In this study, two sulphide ores of differing textures were comminuted to various size distributions using impact and particlebed breakage mechanisms in a hammer mill and a pistondie compression Estimation of Grinding Time for Desired Particle Size Distribution and 2013年9月1日 At the Old Tailings Dam (OTD), Savage River, Western Tasmania, 38 Mt of pyritic tailings were deposited (1967 to 1982) and have since been generating acid and metalliferous drainage (AMD)Particle Size Distribution Effects that should be considered when Download scientific diagram Simulated breakage rates for a copper ore as a function of particle and steel ball size for a ball mill (top) and DEM median impact energy and collision frequency as Simulated breakage rates for a copper ore as a function of particle
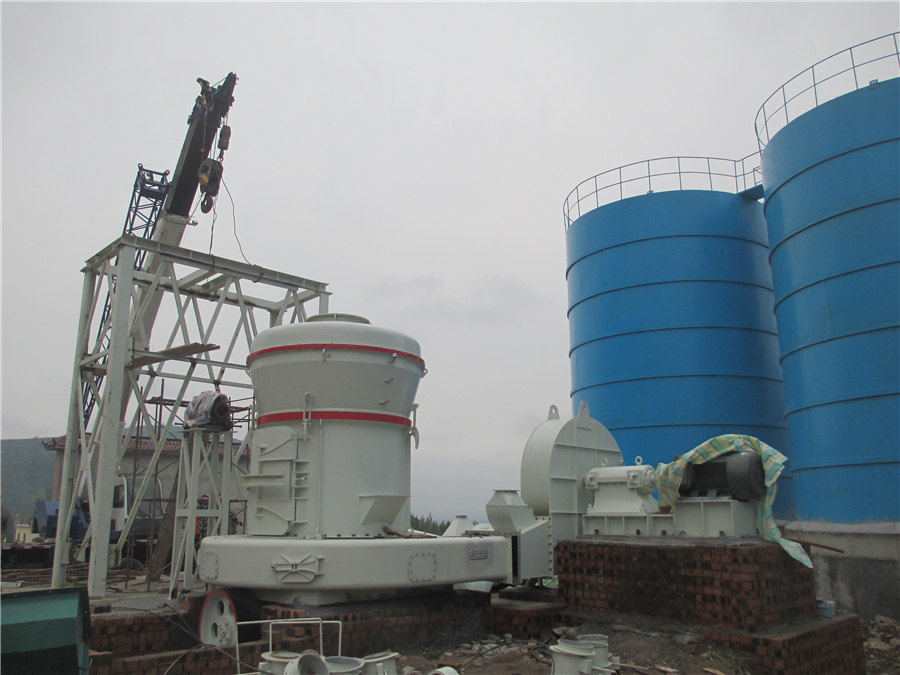
On Predicting Roller Milling Performance IV: Effect of
2003年1月31日 Request PDF On Predicting Roller Milling Performance IV: Effect of Roll Disposition on the Particle Size Distribution from First Break Milling of Wheat The breakage equation for roller milling Effect of ball and feed particle size distribution on the milling efficiency of a ball mill: An attainable region approach N Hlabangana a, G Danha b, *, E Muzenda b a Department of Chemical Engineering, National University of Science and Technology, P O Box AC 939, Ascot Bulawayo, Zimbabwe b Department of Chemical, Materials and Metallurgical Engineering, College of Effect of ball and feed particle size distribution on the milling