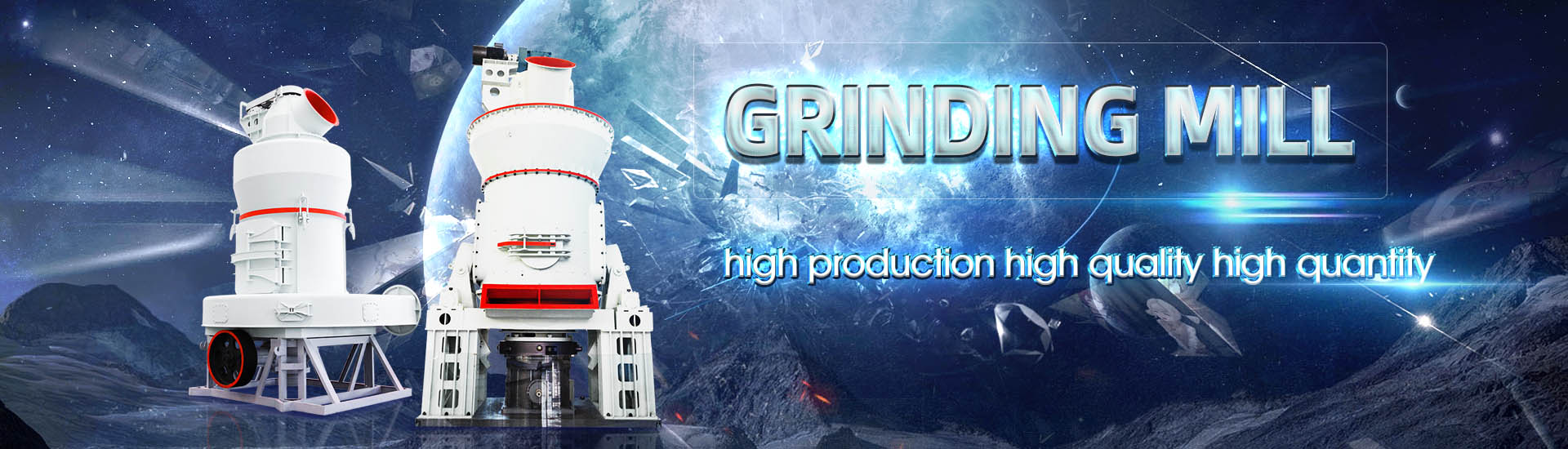
Furnace desulfurization powder making system
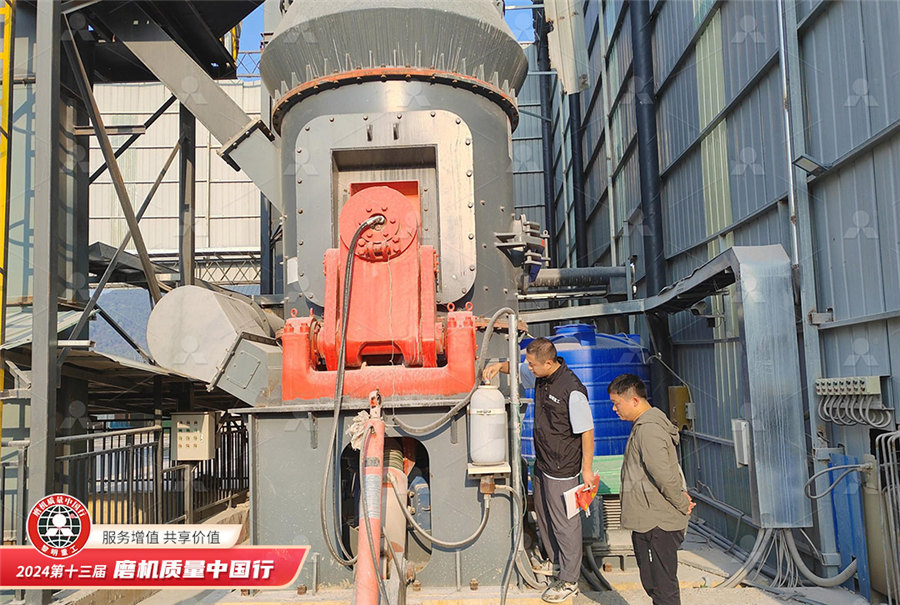
Summary of research progress on industrial flue gas
2022年1月15日 Infurnace calcium injection desulfurization technology sends limestone powder or lime powder gas into the furnace Under high temperature conditions, calcium carbonate Fluegas desulfurization (FGD) is a scrubbing technique that uses an alkaline reagent (typically a sodium or calciumbased alkaline regent) to remove SO2 from flue gas (TriState Synfuels FlueGas Desulphurization an overview ScienceDirect TopicsFlue gas desulfurization is commonly known as FGD and is the technology used for removing sulfur dioxide (SO2) from the exhaust combustion flue gases of power plants that burn coal Flue gas desulfurization IDCOnline2012年10月1日 That development was driven by the introduction of hot metal and steel desulphurization in integrated steelmaking plants A side effect was Desulphurization strategies in oxygen steelmaking
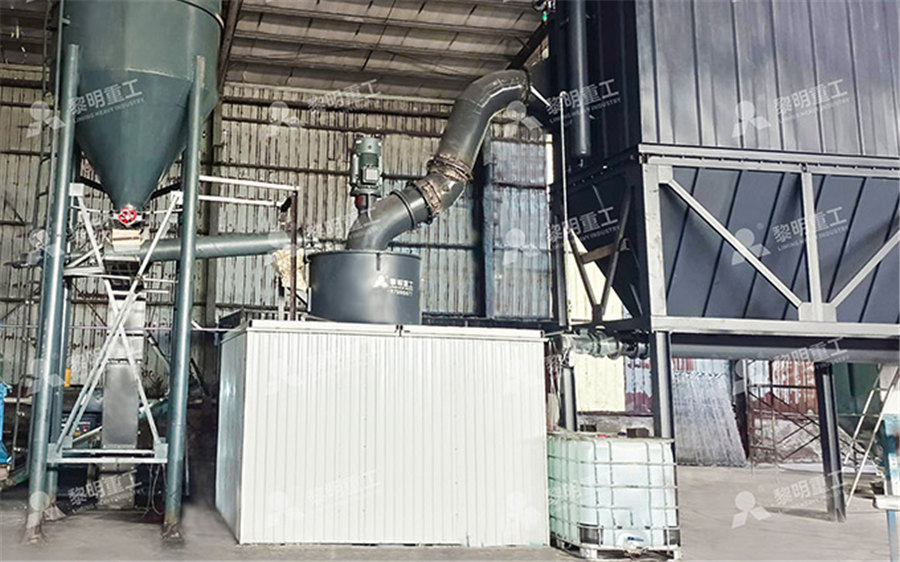
Optimal hot metal desulphurisation slag considering
2021年2月21日 Although there are various processes in the modern steelmaking chain where sulphur can be removed, a dedicated hot metal desulphurisation (HMD) process between the blast furnace (BF) and converter 2022年12月31日 The desulphurization technology in the production of lowcarbon steel in a protective atmosphere, with the addition of synthetic slag and strong desulphurizing agents with additional argon(PDF) INTENSIFICATION OF LOWCARBON STEEL2015年7月27日 The simplest technology is furnace sorbent injection, where a dry sorbent is injected into the upper part of the furnace to react with the sulfur dioxide in the flue gas The Review of Design, Operating, and Financial Considerations in Flue Hot metal desulfurization serves as the main unit process for removing sulfur in blastfurnace based steelmaking The available body of literature on modeling hot metal desulfurization is reviewed to provide an indepth analysis of the A Review of Modeling Hot Metal Desulfurization
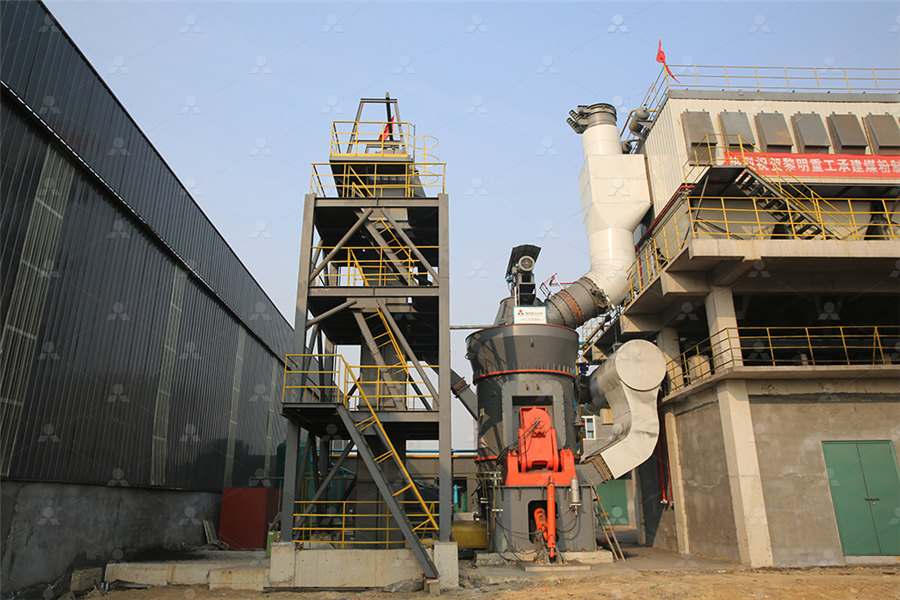
Desulfurization Gypsum Gypsum Powder Fgd Making Machine
Desulfurization Gypsum Gypsum Powder Fgd Making Machine, Find Details and Price about Gypsum Powder Machine Gypsum Powder Making Machine from Desulfurization Gypsum Gypsum Powder Fgd Making Machine Yurui (Shandong) Stable quality: adopt latest hot air boiling furnace technology and cooling system , improve the quality of the product 32022年2月6日 A kinetic model for hot metal pretreatment process was developed The coinjection of soluble magnesium and insoluble lime, and both of the transitory and permanent contact reaction zones were considered in the present model That is, the model covers all the general features of hot metal desulfurization in the submerged powder injection, practiced at Kinetic Simulation of Hot Metal Pretreatment: Desulfurization 2018年12月19日 desulfurization sorbents for infurnace desulfurization purposes were analyzed A particle size analyzer (PSA, LS13320, Beckman coulter, USA) and scanning electron microscope (SEM, S4300,Utilization of CFBC Fly Ash as a Binder to Produce In Circulating fluidized bed combustion (CFBC) power generation technology is known to efficiently reduce the emission of air pollutants, such as SO2 and NO2, from coal combustion however, CFBC coal ash contains high contents of free CaO, making it difficult to recycle This research has been conducted to find ways to use the selfhardening property of CFBC coal ash, one of its Utilization of CFBC Fly Ash as a Binder to Produce InFurnace
.jpg)
Increasing SOx removal efficiencies in Dry Sorbent Injection Systems
into large scale commercial FGD systems, has occurred mostly since the 1970s The technology for FGD has broadly been: (A) wetscrubbing systems (B) wet sulfuric acid systems (C) spraydry scrubbing systems (D) drysorbent injection systems Even if the chemistry behind each system is more or less the same, using a sorbent (usually,FGD System The waste gas is processed by the FGD system, and the SO2, SO3, HCl, HF, and H2S in the flue gas are effectively removed The desulfurization byproduct desulfurization ash of the semidry FGD system is a freeflowing dry powder mixture, without secondary pollution, and can be further comprehensively utilizedFGD System for Sale Semidry Flue Gas DesulfurizationCurrent LFUbased steel desulfurization technologies typically involve a significant increase in slag basicity (up to 45–50 units) by adding steelmaking lime (CaO) and/or by using refining mixtures containing fluorspar (CaF2) It should be noted that the abovementioned desulfurization technologies, realized in both furnaces and REDUCING THE COST OF STEEL DESULFURIZATION DURING Hot metal desulfurization serves as the main unit process for removing sulfur in blastfurnacebased steelmaking Hot metal desulfurization is commonly conducted in a ladle or a torpedo car,[1] using a desulfurization reagent that is either injected into the metal bath or added on top of it[2] From the thermodynamicA Review of Modeling Hot Metal Desulfurization Wiley Online
.jpg)
Feasibility study of an infurnace calcium spraying desulfurization
2012年7月1日 To solve such problems of a largecapacity boiler as a frequent change in coal quality, a small design allowance for the wetmethod desulfurization system, a large work load and a high cost of an systems and process technologies develop and advance Magnesium and magnesium alloy granules and powders are blended into reagents that are designed to achieve consistent results when preparing iron for steelmaking Companies that make magnesium reagents must meet standards as strict as those met by the steelmakers who use themDesulfurizing Steel: Magnesium is the Reagent of ChoiceExperimental method of compressive strength test Sustainability 2018, 10, 4854 6 of 17 224 Compressive Strength Test of CaBased Desulfurization Sorbents The desulfurization efficiency of infurnace desulfurization sorbents decreases as their particles become increasingly pulverized by particle collisions and the corresponding frictionUtilization of CFBC Fly Ash as a Binder to Produce InFurnace 2018年12月11日 This study investigates the effect of desulfurization slag (DS) and gypsum (G) on the compressive strength and microstructure properties of blast furnace slag(BFS) based alkaliactivated systems(PDF) Compressive Strength and Microstructure
.jpg)
(PDF) Experimental Study on Desulfurization and
2023年2月16日 In this paper, the effects of B(w(CaO)/w(SiO2)) and w(MgO)/w(Al2O3) on the desulfurization ability of a CaOSiO2MgOAl2O3 quaternary blast furnace slag system were studied by using a doublelayer 2024年2月12日 In this paper, TiO2 catalysts doped with different Fe contents (FeTiO2 catalysts) were prepared by coprecipitation method and the Fe loading capacity was optimized, and then the integrated Experimental study on integrated desulfurization and Nature2022年3月29日 The blast furnace gas, a lowcalorific value fuel, is worthy of recycling However, the sulfuric contents in blast furnace gases would cause pipeline corrosion and air pollution that are adverse to reutilization of blast furnace gases Therefore, desulfurization technologies of blast furnace gas are necessary, which have been recently attracting much attention This article A Review on Desulfurization Technologies of Blast Furnace Gases 2020年11月1日 The potential advantages of this system are as follows: 1) The process is costeffective due to the recycling of carbon–sulfur carrier with synchronous decarbonation and desulfurization; 2) The MMLP drives BFG into a mixture of H 2 and N 2, which could be raw materials for ammonia synthesis; 3) The simultaneously desorbed mixture of SO 2 and CO 2 Synergistic decarbonization and desulfurization of blast furnace
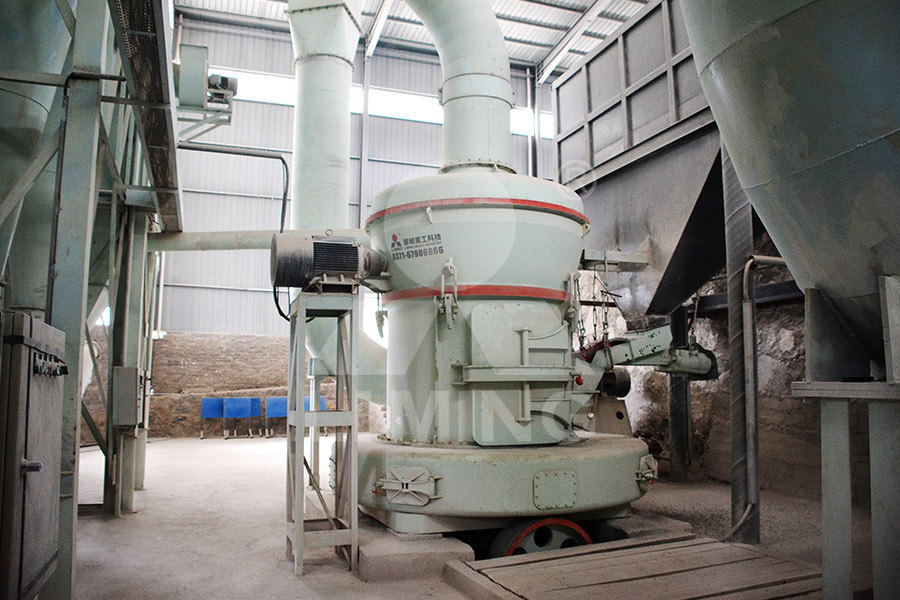
Sintering Furnaces for Powder Metallurgy Thermcraft
Sintering furnaces are widely available for a broad range of processing and manufacturing applications in which a material must be carefully densified through sustained stages of heating Mineralogical deposits are commonly formed through natural sintering, where atomic diffusion causes particles in geological samples to fuse into highdensity ore Understanding of this 2024年1月1日 An injection lance is used to insert powder injection into molten steel from the top of the ladle close to the ladle bottom, with argon or nitrogen as the carrier gas, and inject powder into the molten steel for desulfurization, deoxidation, and inclusion deformation treatment to produce clean steelSecondary Refining of Molten Steel SpringerLinkWe are ISO 9001 QC certified manufacturer, supplier and exporter of Detergent Making Machine, Detergent Production Line, Detergent Powder Plant, Detergent Powder Packing Machine, Detergent Powder Plant, etc at market leading price We also provide full support after sale service after the saleDetergent Making Line,Detergent Production Line 2023年12月13日 If deep desulfurization is required active desulfurizing agents are injected into the melt through the injection lance or in form of cored wire Besides refining operations Ladle Furnace (LF) may serve as a buffer station before Continuous casting Ladle refining SubsTech
.jpg)
Desulfurization and denitrification experiments in SDA system:
2020年1月2日 An integrated and effective method to realize simultaneous desulfurization and denitrification by the Spray Dryer Absorption (SDA) method combined with the NaClO 2 was carried out in this paper The optimum conditions on desulfurization were verified, as well as the cooperative effect and removal mechanism between SO 2 and NO was speculated The 2023年9月8日 A stable and efficient operation of the ironmaking blast furnace is prerequisite to reduce the greenhouse gas emission JSW Steel, Salem have been proposed many projects to reduce greenhouse gas Blast Furnace process optimization for sustainable Iron 2023年10月31日 A kinetic model of the RH desulfurization process was established based on the twofilm theory, considering the desulfurizer addition in the RH vacuum chamber and the slag desulfurization in the ladle The kinetic model was used to predict the variation of the sulfur content in the molten steel during the RH desulfurization process, which was in good Kinetic Model of Desulfurization During RH Refining Process2021年8月2日 In this paper, the effects of B(w(CaO)/w(SiO2)) and w(MgO)/w(Al2O3) on the desulfurization ability of a CaOSiO2MgOAl2O3 quaternary blast furnace slag system were studied by using a doublelayer (PDF) Desulfurization Ability of Blast Furnace Slag Containing
)D`ERF`389RMI4.jpg)
Industry Leading Fume Extraction System Manufacturer India for
Flue gas desulfurization system manufacturers are instrumental in providing effective solutions for controlling sulfur oxide emissions Maan Global Industries, a leading Flue Gas Desulfurization system manufacturer in Mumbai, Delhi, Pune, Noida, Hyderabad, Nashik, Chennai, Bengaluru, Kolkata, excels in designing and manufacturing systems that 2024年1月10日 It offers a smaller physical size and lower initial cost than wet desulfurization systems, making it a practical option for upgrading existing plants to meet stricter flue gas cleaning standards 16Modeling based on machine learning to investigate flue gas High Heat Efficiency Direct Type Hot Air Furnace for Dailychemical, Building Material Product Description The gas(oil) fired hot air furnace is mainly composed of a burner and a combustion chamber Compared with coalburning and biomass burning hot furnaceThe flue gas produced by the furnace is clean , but the fuel cost is highHot Air Furnace Manufacturer,Supplier,ExporterIt is a page of the detail of KR Hot Metal Desulfurization System of Steel PlantechDesign, manufacturing, installation, sales and aftersales servicing of steelmaking machinery, nonferrous metal producing machinery, and cokemaking machinery as well as related equipment for use in Japan and overseasKR Hot Metal Desulfurization System Steel Plantech
.jpg)
EFFICIENT PROCESS OF HOT METAL LADLE DESULFURIZATION
blast furnaces or by outoffurnace desulfurization Hot metal with sulfur content below 00100015% can be produced only by outoffurnace desulfurization Technical processes of outoffurnace desulfurization have become widely used throughout the world since 19701980s Materials based on СаО, СаС 2, Na 2 CO 32000年7月31日 Emissions Control Strategies for Power Plants Bruce G Miller, in Coal Energy Systems, 2005 Dry Flue Gas Desulfurization Technology Dry FGD technology includes lime or limestone spray drying; dry sorbent injection, including furnace, economizer, duct, and hybrid methods; and circulating fluidizedbed scrubbersDry Flue Gas Desulfurisation Technology ScienceDirect2023年6月30日 3721 Test Materials and Their Properties The raw materials used in the experiment are mainly iron tailings, granulated blast furnace slag (GBFS) and desulfurization ash (DA) The iron tailings are from Daguoshan beneficiation plant of Ansteel Group Mining Company, and the main mineral phases are quartz, feldspar, mica, amphibole, chlorite, etcStudy on the Preparation of Green LowCarbon BakingFree Bricks 2019年9月16日 Vlcek et al [], Yi et al [], and Mihok et al [] have addressed the use of steelmaking slag, but very little focus was given to the reuse of LF slag as a flux in steelmakingMost steel industries with LF in secondary steelmaking operations use synthetic slag/fluxes []Characterization studies carried out on LF slags by a few researchers [1, 10] Recycling Ladle Furnace Slag as Flux in Steelmaking: A Review
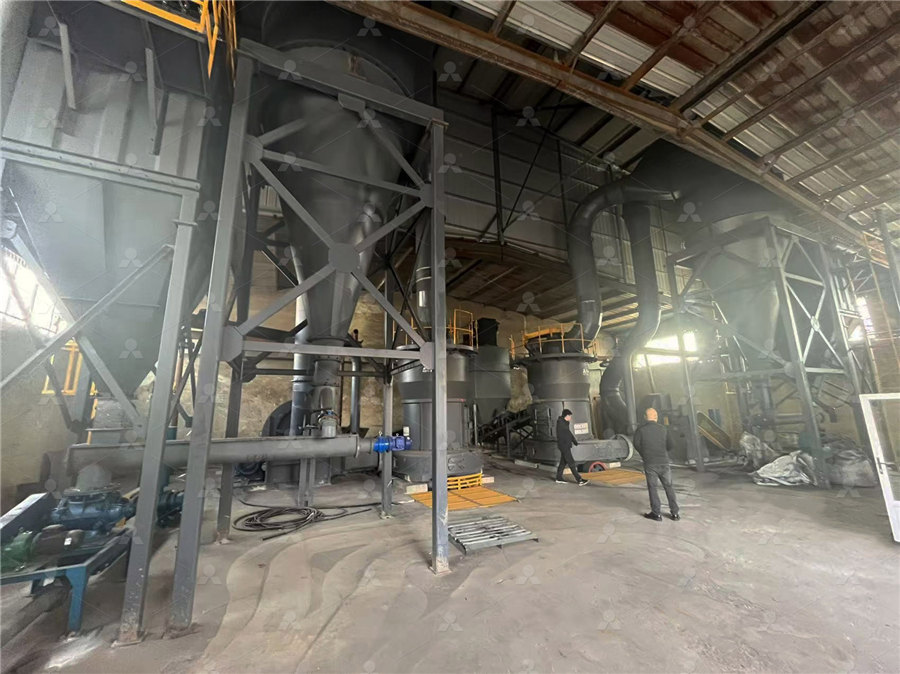
CNA Method for dephosphorization and Google
The invention provides a method for dephosphorization and desulphurization in the process of steel production in an induction furnace, which is characterized by comprising the following steps of: during the smelting period and the initial period of total meltdown of charging materials, controlling the temperature of molten steel to below 1,450 EDG C, performing be adopted in blast furnace hot blast stoves, rolling steel heat treatment furnace, lime kilns, dolomite kilns, as well as captive power plants In the meantime, deacidication devices should be also installed for purication systems of blast furnace gases so as to make the concentration of puried H 2 S lower than 10 mg/Nm 3A Review on Desulfurization Technologies of Blast Furnace Gases 2022年9月30日 Ladle furnace (LF) slag plays an important role in modern steel making in terms of quality and productivity The major challenge of using LF slag is its dusting problem The polymorphic transformation of βdicalcium silicate (monoclinic) to γdicalcium silicate (Orthorhombic) at about 450 °C is the leading cause of its disintegration Hydration of slag, A Review on Stabilization of Ladle Furnace SlagPowdering Issue2022年2月6日 A kinetic model for hot metal pretreatment process was developed The coinjection of soluble magnesium and insoluble lime, and both of the transitory and permanent contact reaction zones were considered in the present model That is, the model covers all the general features of hot metal desulfurization in the submerged powder injection, practiced at Kinetic Simulation of Hot Metal Pretreatment: Desulfurization
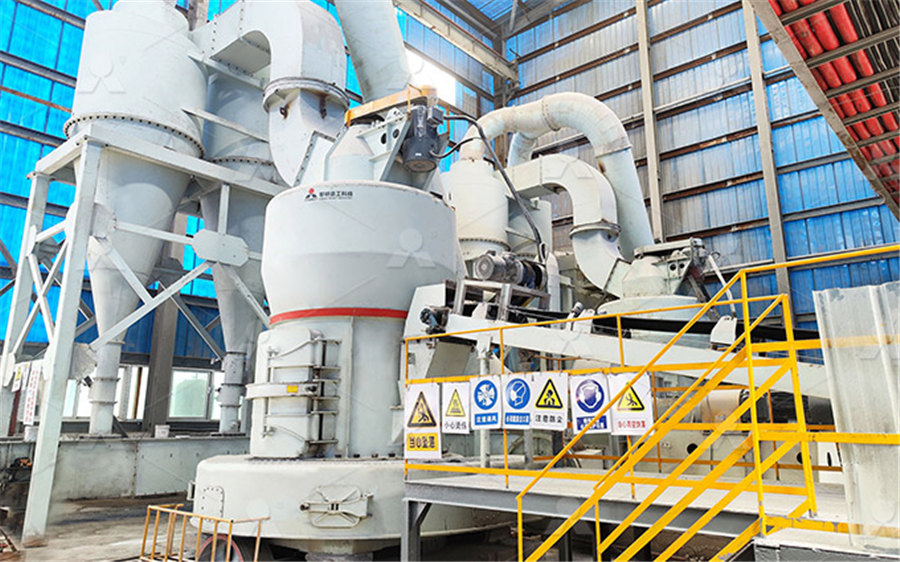
Investigation of Circulation Flow and SlagMetal Behavior in an
2020年2月3日 A combined method of mathematical and physical modeling was used to investigate the circulation flow and slagmetal behavior in industrial SSRF and RH The circulation flow of molten steel was simulated by using the coupled mathematical model The results indicate that two different circulation modes are presented separately in SSRF and RH The incomplete cement and lime kilns, metal smelters, petroleum refineries, glass furnaces, and H 2 SO 4 manufacturing facilities Approximately 85% of the FGD systems installed in the US are wet systems, 12% are spray dry and 3% are dry systems Emission Stream Characteristics: a Combustion Unit Size: SO 2 scrubbers have been applied combustion units firing Air Pollution Control Technology Fact Sheet US EPA2015年2月18日 Understanding Electric Arc Furnace Steel Making Operations Electric arc furnace (EAF) steel making technology is more than hundred years old Though De Laval had patented an electric furnace for the melting and refining of iron in 1892 and Heroult had demonstrated electric arc melting of ferro alloys between 1888 and 1892, the first industrial Understanding Electric Arc Furnace Steel Making OperationsAuthors AIST April 2013 1 Feature Article Desulfurization Strategies in Oxygen Steelmaking This paper explains the control of hot metal sulfur comingDesulfurization Strategies in Oxygen Steelmaking ResearchGate