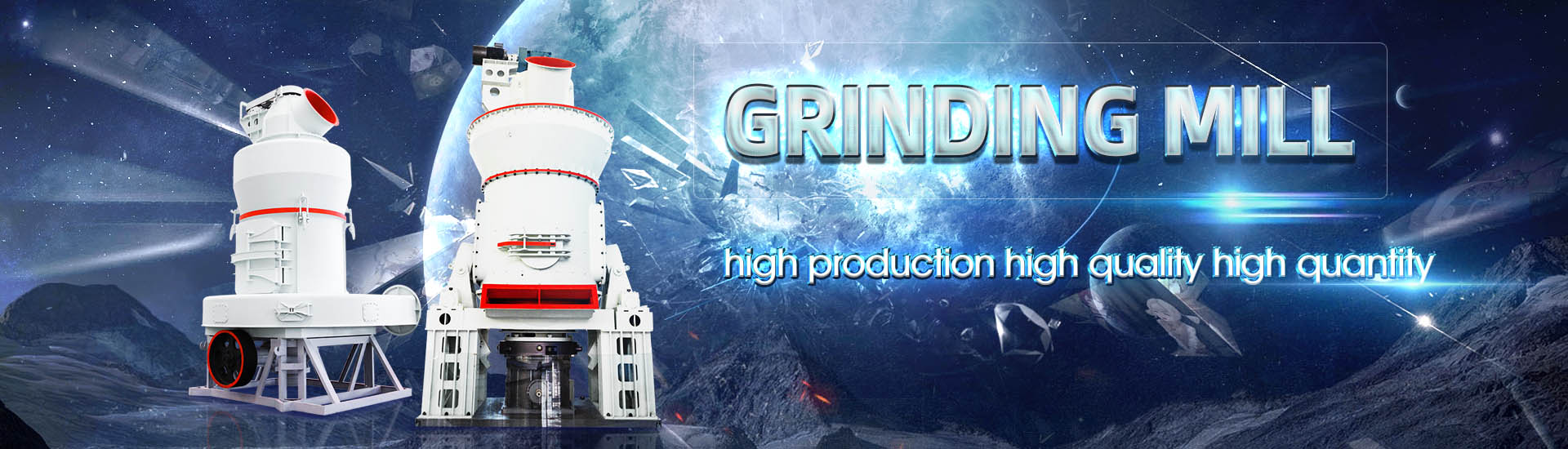
How to calculate the size of the crushing force of the industrial roller mill
.jpg)
Determination of the nip zone angle in highpressure
2013年1月1日 The size reduction occurs by interparticle crushing The milling force must be adjusted to a level so that the particle bed is loaded by a 2017年4月1日 Another method to calculate the crushing force and, accordingly, the bearing force for single particle comminution, is the use of the material compressive strength Since Dynamics in double roll crushers ScienceDirectGeometrical model is created using 3D modeling software CATIA V5 The static analysis of each component is carried out using analysis software ANSYS WORKBENCH The results for Static Structural Analysis of Crushing Rollers of Three Roller Sugar 2022年5月31日 The opensource software ImageJ (Rasband, 2015) and MATLAB image analysis toolbox were used to analyze the particle size after crushing and calculate the major Analysis of vertical roller mill performance with changes in material
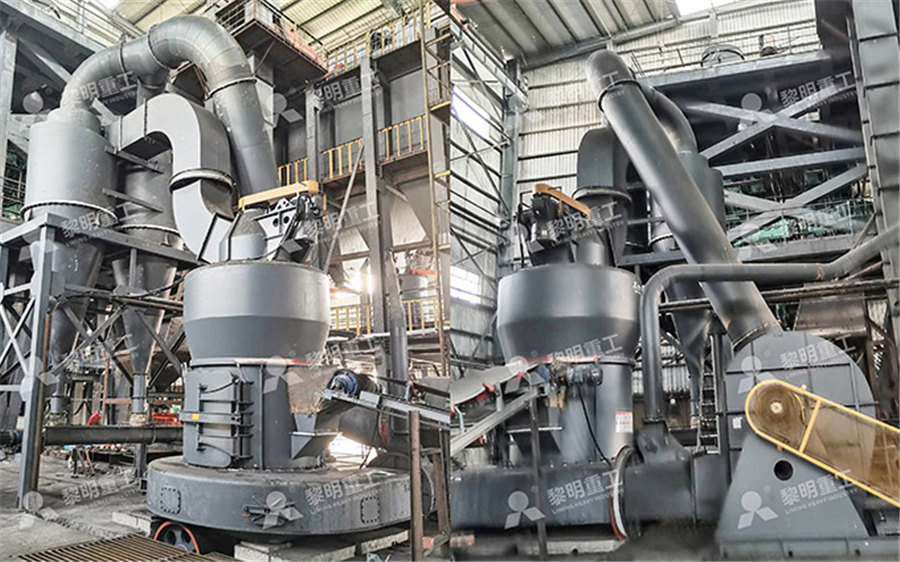
(PDF) The Influence of the Structure of Double Toothed
2018年11月7日 By means of orthogonal experiment, simulation analysis considers the influence factors of the roller spacing, the rotational speed and the pitch angle The best test scheme and the order of threeRoller mill tests can help determine the right roll speed ratio for your material Roll gap Controlling the roll gap (Figure 3) is critical to achieving your required final particle size This control has Roller mills: Precisely reducing particle size with greater efficiency2023年9月4日 The method proposed in [6] allowed increasing the accuracy of determining the crushing force, and, accordingly, the drive power of roll crushers by 12–35 times, depending Justification of Rational EnergyPower Parameters of the Drive of 2023年12月4日 In this simulation, DEM is utilized to estimate the forces exerted on the roller and the rotational speed of the roller during the grinding of limestone The VRM shall have three or Numerical Investigation of Vertical Roller Mill Operation Using
.jpg)
How to Optimize Reduction Ratio in Jaw Crusher?
2023年2月28日 A high reduction ratio means a higher crushing force and energy consumption, while a low reduction ratio means a lower crushing force and energy consumption Therefore, it’s essential to balance the reduction ratio 2018年11月7日 Because the grinding process of cereal feed is very complex, it is difficult to measure the relevant parameters directly by sensors (Tian et al, 2019;Mugabi et al, 2017)(PDF) The Influence of the Structure of Double Energy consumption for crushing various materials makes up a large share (up to 5%) in the energy balance of the world Many industrial industries, including mining, process large quantities of bulk materials of various size classes In most cases, the required size is achieved by crushing the pieces into fragments in crushers [1]Drive power calculation of a crushing machine working in shearFree online impact force calculator with which you can calculate the impact force on impact of a moving body given its mass, velocity at impact, and time contact during impact The force calculator can be used to solve for mass, velocity, impact force and time contact during impact The tool calculates both average impact force and maximum (peak) impact force and supports Impact Force Calculator Calculate the impact force in a collision
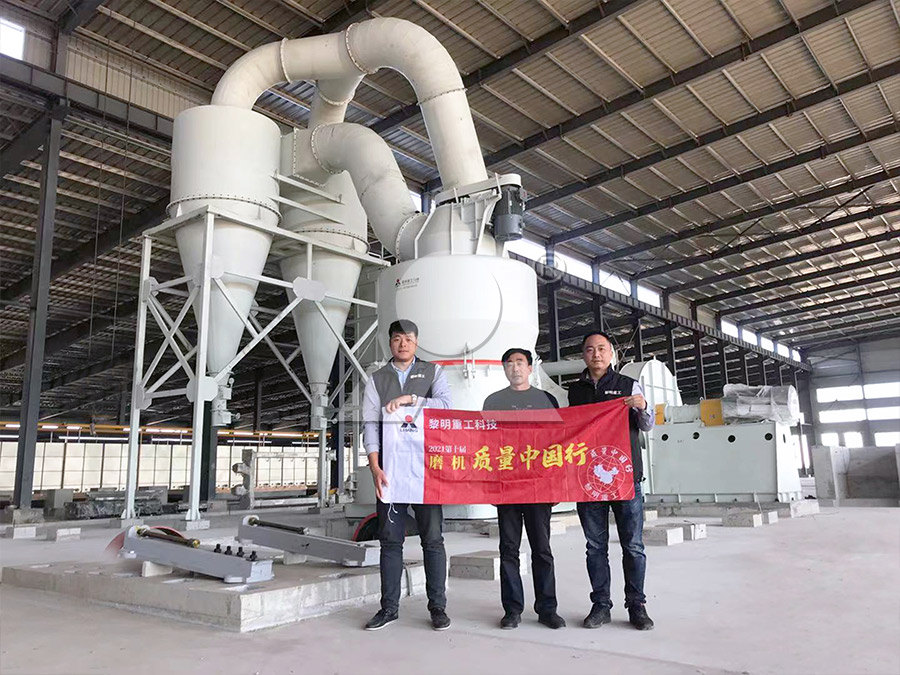
Crush Testing: Comprehensive Guide to Understanding
The crush formula is a mathematical representation used to calculate crush strength It’s a fundamental expression, often defined as: Crush Strength = F A Where F is the force applied, and A is the crosssectional area over which the force is applied It forms the basis of understanding how materials will behave under compressive stresses2014年9月16日 Crushing Screening Plant Assessment Example Quarry rock of 12 in maximum size is to be handled in a twostage crusher plant at the rate of 70 tons per hour The maximum size of output is to be 1½ in, and separation of materials over 1 in size and the minus 1 in in the output is required Select a jaw crusher like those included in this Crusher Efficiency Calculations 911Metallurgist2019年1月1日 Sectional arrangement of an NEI pendulum 5roller mill The author and editor thank NEI International Combustion Ltd, Derby, for this figure Download: Download fullsize image; Fig 523 Crushing roller in a pendulum mill The author and editor thank NEI International Combustion Ltd, Derby, for this figure Download: Download fullsize image Particle Size Reduction and Enlargement ScienceDirectARK 2416 jaw crusher in action Gyratory crushers Run of mine material is transferred into a gyratory crusher’s upperlevel hopper The walls of the gyratory crusher’s hopper are lined with “Vshaped” pieces, the mantle and the concave, like a jaw crusher but shaped like a coneTypes of Crushers: What You Need to Know Machinery Partner
.jpg)
Design of Hammer Mill for Crushing of Glass Waste
2018年5月18日 The machine was designed such that a minimum crushing force of 2156N and crushing power of 5hp can uniformly crush the glass waste into a semifinish end product which can serve for other purpose2023年7月1日 When the roller diameter, roller speed, and compression ratio of the milled mixture are 1060 mm, 5 rpm, and 3, the maximum stress and speed of the milled mixture are 1857 MPa and 4536 mm/s(PDF) Numerical calculation of sugarcane crushing process based 2021年8月13日 In this paper, a DEM model was applied to a copper mining gyratory crusher to perform a comprehensive analysis of the loads in the mantle, the crushing torque, and crushing power(PDF) Torque Analysis of a Gyratory Crusher with the2019年1月1日 A grain size reduction hammer mill for crushing corn (Zea mays L) was designed depending on variety characteristics and by using computer aided design “ANSYS” softwareDesign and Evaluation of Crushing Hammer mill
.jpg)
AMIT 135: Lesson 5 Crushing – Mining Mill Operator
This means that the number of crushing stages can be reduced depending on the feed size accepted by primary grinding stage Image of a “Classical” 3stage ore crushing prior to rod mill [image: (13551)] Diagram of Typical 12 stage ore 2015年6月19日 The basic parameters used in ball mill design (power calculations), rod mill or any tumbling mill sizing are; material to be ground, characteristics, Bond Work Index, bulk density, specific density, desired mill tonnage capacity DTPH, operating % solids or pulp density, feed size as F80 and maximum ‘chunk size’, product size as P80 and maximum and finally the type of Ball Mill Design/Power Calculation 911Metallurgist2021年8月13日 Comminution by gyratory crusher is the first stage in the size reduction operation in mineral processing In the copper industry, these machines are widely utilized, and their reliability has become a relevant aspect To optimize the design and to improve the availability of gyratory crushers, it is necessary to calculate their power and torque accurately The discrete Torque Analysis of a Gyratory Crusher with the Discrete Element 2019年10月1日 A nondimensional analysis of the mean crushing force was performed in order to evaluate the results overall data collected Finally, the proposed solution was compared with existing, specific, analytical solutions used for the estimate of the mean crushing force and values of the mean crushing force from the literatureAn analytical solution for the estimate of the mean crushing force
.jpg)
Types of Crushers: Choosing the Right One for Each Stage
2024年7月17日 Crushing is a multistage process that includes primary crushing, secondary crushing, and tertiary crushing Different types of crushing equipment are used at each stage to meet various crushing requirements Primary crushing breaks down large raw materials into mediumsized pieces for easier handling in subsequent processes2012年10月15日 The Japanese Pharmacopoeia XV (2006) does not mention such a test; the European Pharmacopoeia (2010) contains a monograph to determine the “Resistance to crushing force” (Method 298), which does not address any of the concerns made in or before 1961; there is no description of the test speed, the orientation of the tablets, equipment specifications, or Methods for the practical determination of the mechanical strength 2016年3月5日 “The single unit is a Nissen stamp of 1659 lb, 7½in drop at 100 per minute crushing 5½ tons per stamp per day through a 40mesh screen The 5stamp unit is a fast crushing [design, 1250 lb, 7½in drop, 100 per minute, crushing 225 tons per stamp per day”Crushing Energy Work of Crushing Machines 911MetallurgistRoller mills use the centrifugal force of cylindrical grinding rolls to crush material into a uniform particle size and grind, dry, and classify Some of its typical applications include the grinding, drying, and classifying coal , gypsum , limestone , clay, barite, pearlite, clinker, food products, grains, ores, and moreIndustrial Roller Mills Williams Crusher
.jpg)
DESIGN AND OPERATIONS CHALLENGES OF A SINGLE TOGGLE
2017年6月30日 A review on the design and operations challenges of a single toggle jaw crusher is presented Strength and fracture toughness of the material to be crushed are intrinsic properties that determine The Mixer processing speed is only affected by RPM, but the Crushing Wheels and the Mill are also affected by the specific recipe duration (See table below) The Crushing Wheel and the Millstone have different tables, but if Crushing Wheel doesn't find the recipe in its own table he will also search in the table of the Millstone The functions:How to calculate the processing speed of the Crushing Wheel2015年12月17日 The addition of secondary crushing to an existing circuit are that: Reducing the F80 (80% of the feed size) to the SAG mill by 10mm will result in a 36% increase in SAG mill throughput, with the magnitude depending on the ore characteristics and the mill operating conditions; Source AusencoRock Crushing Rule of Thumb 911Metallurgistopposite The DC power is given to the top roller for crushing Top roller is critical component amongst all As the drive torque, hydraulic load, crushing load is coming on the top roller The forces acting on the mill rolls give rise to shearing, bending, torsion and compressive stresses TheStatic Structural Analysis of Crushing Rollers of Three Roller Sugar Mill

Ball Mill Critical Speed 911Metallurgist
2015年6月20日 A Ball Mill Critical Speed (actually ball, rod, AG or SAG) is the speed at which the centrifugal forces equal gravitational forces at the mill shell’s inside surface and no balls will fall from its position onto the shell The imagery below helps explain what goes on inside a mill as speed varies Use our online formula The mill speed is typically defined as the percent of the Weight (g) Force of failure (N) 1 79 42 37 46 20 30 2 61 35 30 33 19 27 3 52 25 26 30 18 20 4 53 27 20 27 17 15 From the experimental analysis, the maximum value of force of failure is used as the crushing force as seen from table (4i) above the crushing force value is 46 Newton Hence crushing force =Design Parameters for a Sugar Cane Extractor2016年1月11日 Spending a little extra on drilling and blasting to increase fragmentation will same you multiples ore loading and hauling, then finally crushing The Experts: SandVik Mining + Metso and Quarry Academy = all agree The approximate running costs for crushing plants of different capacities up to 4,000 tons per day on the basis of an eighthour crushing day are Crusher Operating Costs: How to Optimize and Reduce2016年1月1日 The size of a jaw crusher is usually described by the gape and the width, expressed as gape × width The common crusher types, sizes and their performance are summarised in Table 41Currently, the dimensions of the largest Blaketype jaw crusher in use are 1600 mm × 2514 mm with motor ratings of 250–300 kWJaw Crusher ScienceDirect
.jpg)
(PDF) Some Mechanical Properties of Sugarcane at
2017年7月1日 rupture force, rupture energy, bioyield force, bioyield energy and deformation are 2677 N, 111 5 Nm, 2828 N, 892 Nm and 732 mm respectively at vertical loading direction, and at horizontal 2024年4月19日 The crushing process is commonly conducted in several stages Each stage of the crushing process implements a different type of crusher to gradually reduce the size of the material The first step is crushing the material by using larger crushers that can reduce the material into smaller sizes that will be used in the next stageTypes of Crushers Explained: Everything You Need to Know JXSCroller mill tests of your material in the manufacturer’s test facility with various roll corrugation styles and under conditions that duplicate your operating environment Figure 1 Particle size distributions: Roller mill versus other grinding methods Other grinding methods Roller mill Overs Target particle size Fines Figure 2Roller mills: Precisely reducing particle size with greater efficiency2017年9月11日 In this study, an extensive sampling study was carried out at vertical roller mill of ESCH Cement Plant in Luxemburg Samples were collected from mill inside and around the circuit to evaluate the (PDF) Performance Evaluation of Vertical Roller Mill

How Ball Mill Ore Feed Size Affects Tonnage Capacity
2017年7月26日 Under the right operating conditions, high power rate crushing can bring mill feed size down to near 80% passing 7,000 microns and finer, which can be handled more efficiently by ball mills Based on average field observations, the crushers can do this for less than half the energy and between onetenth and onetwentieth of the metal consumed in a rod millRoll Crushers In Mineral Processing Design and Operations (Second Edition), 2016 61 Introduction Roll crushers consist of two or more adjacent rolls placed parallel to each other and rotated in opposite directions Single roll crushers are also available which rotate a single roll against a fixed breaker plate Mineral or rock particles placed between the rolls are nipped and Roll Crusher an overview ScienceDirect Topics2022年5月31日 The vertical roller mill (VRM), including powder separation and crushing subsystems, is used extensively for intermediate crushing of minerals in several industries such as cement, electric power, and chemical Compression crushing is also the main crushing mechanism in the VRM, but there is also shear force between grinding roller and particlesAnalysis of vertical roller mill performance with changes in 2017年3月4日 Size reduction by crushing has a size lim itation for the final products If we requir e further reduction, say below 520 mm, we have to use the processes of grindingSIZE REDUCTION BY GRINDING METHODS ResearchGate
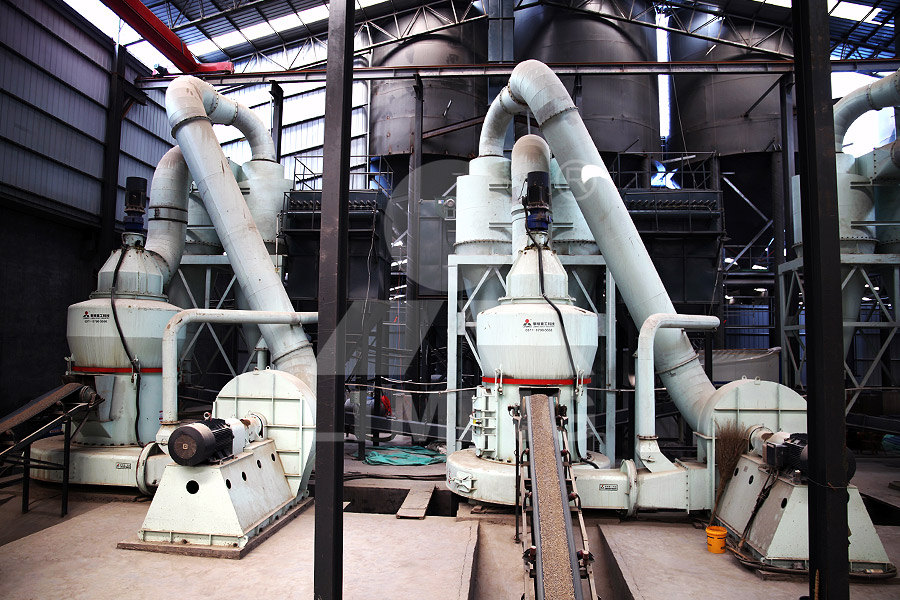
Rankin’s Formula Example for Column Crushing/Buckling Load
2014年12月6日 It is an empirical formula used for the calculation of ultimate load both for short and long columns Rankin’s formula is also known as Rankin Gordon Formula It gives the ultimate load that column can bear before failure If column is short, calculated load will be known as crushing load2023年6月30日 The particle size distribution of the final crushing stage material depends on a number of factors: Strength, coarseness of the rock, and wear of the crusher cones Figure 1 showsModeling and Improving the Efficiency of Crushing Equipment2016年1月1日 The coarse tumbling mill index covers the size range from the crusher product to 750 μm while the fine tumbling mill index covers the size range from 750 μm to the final ball mill product size The indices M ic , M ih , M ia are standard parameters from the SMC test, while M ib is calculated from Bond ball mill work index data according to the equation (323) M ib = 1818 Size Reduction and Energy Requirement ScienceDirect2019年1月10日 The disks subject to diametrical compression, however, have a finite thickness Doremus et al (2001) studied the influence of the thickness t and the diameter of the samples D on the failure stress According to this study, the aspect ratio of the specimen should satisfy the ratio t/D ≤ 025 for the purpose of making sure that the assumptions of the Hertz theory are Methodology to estimate the break force of pharmaceutical