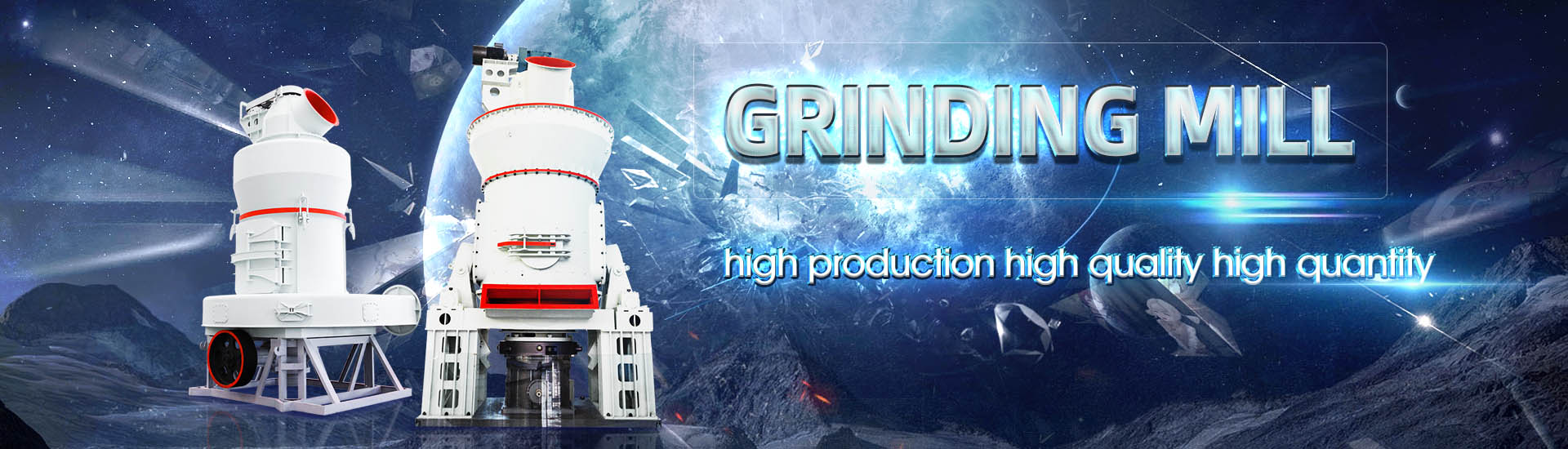
Raw material mill and powder selector
.jpg)
Application of Powder Simulation to Powder Metallurgy
Powder simulations provide a macroscopic interpretation of powder behavior by calculating the motion of individual particles that constitute the powder In this paper, the powder simulation is Abstract— This paper aims the development of highenergy milling equipment for use in powder metallurgy This kind of mill is used to obtain prealloyed powders and/or reduction size of Development of a HighEnergy Mill for Powder Metallurgy2007年1月1日 The fine grinding mills are classified often into five major groups: (1) impact mills, (2) ball media mills, (3) air jet mills, (4) roller mills, and (5) shearing attrition mills from the Chapter 10 Selection of Fine Grinding Mills ScienceDirect2022年11月30日 The optimization models of raw material selection process established in this work for the complex industry can improve production efficiency and product quality In Optimization Model of Raw Material Selection Process for
.jpg)
From Machining Chips to Raw Material for Powder Metallurgy—A
2021年9月20日 The current study reviews the stateoftheart methods for powder production from metal chips considering milling conditions and powder characteristics, mainly the 4S’s, 2016年4月28日 In the simple form, the raw material is milled, or otherwise compacted and impacted with high velocity particles, paddles, balls, or hammers, to generate progressively Powder Selection SpringerLinkVertical roller mills are adopted in 20 cement plants (44 mills) in Japan In the vertical roller mill which is widely used in the raw material grinding process, raw materials input grinding table Vertical roller mill for raw Application p rocess materials2023年6月27日 This review found that ball milling is the best tool for reducing the particle size of recycled metal chips and creating new metal powders to enhance mechanical properties and novelty for mold additive manufacturing Producing Metal Powder from Machining Chips Using
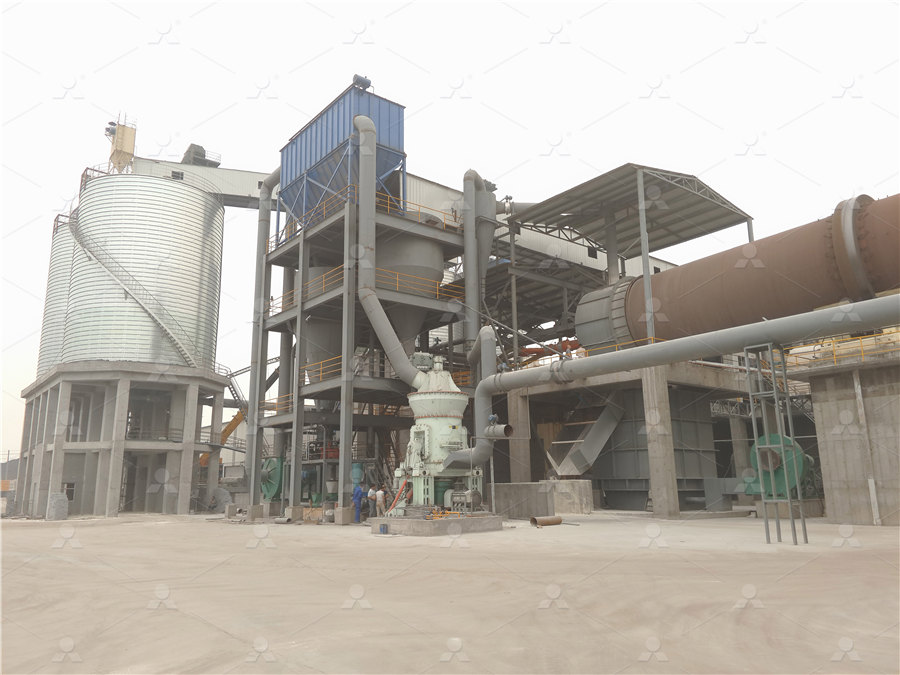
(PDF) From Machining Chips to Raw Material for
2021年9月20日 Chips are obtained by subtractive processes such as machining workpieces and until recently considered as waste However, in recent years they are shown to have great potential as sustainable rawThis article examines how powder testing can be integrated with manufacturing and quality operations and used to optimize raw material selection and process optimization, sharing results of some inhouse projects at GlaxoSmithKline (GSK)Integrating powder characterization into raw material 2023年12月28日 During the material grinding process, they can be adsorbed on the material’s surface, accelerate the crack expansion during material crushing, and reduce the occurrence of fine powder The mutual bonding between them Factors Affect The Output and Quality of Ball Mills And the threestage mill of raw material, coal powder, and cement products accounts for about 70% of the total electricity consumption per ton of cement The three mills all involveA Survey and Analysis on Electricity Consumption of Raw Material Mill
.jpg)
Mill Scale: A Potential Raw Material for Iron and Steel Making
2015年1月20日 A substantial quantity of mill A scale,containing very high percentage of iron is generated during processing of steel towards production of various long and flat products In an integrated steel plant, though the major part of mill scale is recycled for inhouse consumption, no commercial process for its utilization is so far available for the secondary sector Thus, it is Vertical raw mill is one kind of raw mill, generally used to grind bulk, granular, and powder raw materials into required cement raw meal in the cement manufacturing plantVertical raw mill is an ideal grinding mill that crushing, drying, grinding, grading transfer set in one It can be widely used in cement, electric power, metallurgy, chemical industry, nonmetallic ore, and other industriesVertical raw mill Cement PlantRaw material tube mill Mixed raw materials Pregrinder Coarse powder Coarse powder Product Separ ator 70 5 Item Classification of powder returned from raw material separator Application process Raw material process Background When raw materials are ground in a closed circuit by a doublerotator mill, grids remainVertical roller mill for raw Application p rocess materials2024年9月4日 alwepo, Raymond Mill is an industrial equipment used to grind raw materials into fine powder This equipment is commonly used in industries such as mining, metallurgy, chemistry, and construction materials Its efficient grinding process and ease of operation make Raymond Mill a suitable choice for meeting the needs of raw material grindingWhat is Raymond Mill? How Does It Work? alwepo
.jpg)
Everything you need to know about cement Materials Preparation and Raw
material in the mill is not affected by the material moisture, although some loss in grinding efficiency was observed when the fresh material at the mill inlet had moisture of more than 68% The Horomill used as a raw mill is claimed to combine the effectiveness of the vertical roller mill and the roller press with a very low pressure drop in the circuit2020年3月1日 SEM photograph (Â200), unmilled Al without CNTs for rotation speeds of (ab) 100 and (cd) 150 rpm at different milling times of 5 and 15 minAl/CNT nanocomposite fabrication on different property of raw material 2024年9月18日 This article is about ball mill grinding effect and its Trend: In the current cement industry, coal grinding and raw material crushing have shifted from ball 5 cement grinding system is as follows: a Φ17×11m roller press (with a configured power of 1800 kW) + V1000 type powder selector semifinal Research on the Influence of Speed and Filling Rate on Ball Mill 2024年9月26日 2 Ultrafine mill Get the Latest Price As an advanced grinding mill combining crushing, grading, and static pressure, the ultrafine mill excels in both fineness and environmental performance It is mainly used to produce ultrafine gypsum powder or micronlevel particles, and is widely used in industries requiring highfineness powders, such as chemicals, coatings, and Upgrade Your Process: 3 Best Gypsum Powder Mills
.jpg)
Micro Powder Grinding Mill
The cagetype powder selector in the SCM Ultrafine Grinding Mill incorporates German technologies, significantly enhancing the precision of powder separation Moreover, a multihead cagetype powder selector can be tailored to meet specific user 2023年8月31日 Introduction Metal powders are finely divided metal particles that are used in a variety of manufacturing processesMetal powders can be made from various metals like iron, aluminum, copper, nickel, and more They How to Make Metal Powder Additive Manufacturing 2024年8月31日 (1) Properties of powder raw materials The properties of powder raw materials are mainly acidity, alkalinity, surface structure and functional groups, adsorption and chemical reaction characteristics, etc Surface modifiers that can react chemically or chemically adsorb with the surface of powder particles should be selected as much as possible powder raw materials,Fujian Longyi Powder Equipment Our bestinclass OK™ Mill is a globally successful vertical roller mill solution for grinding raw material, cement and slag Its cuttingedge design features consistently deliver the highest quality products with the greatest efficiency It is affordable to install and cost effective to operate over your cement plant’s lifetimeOK™ Raw and Cement Mill
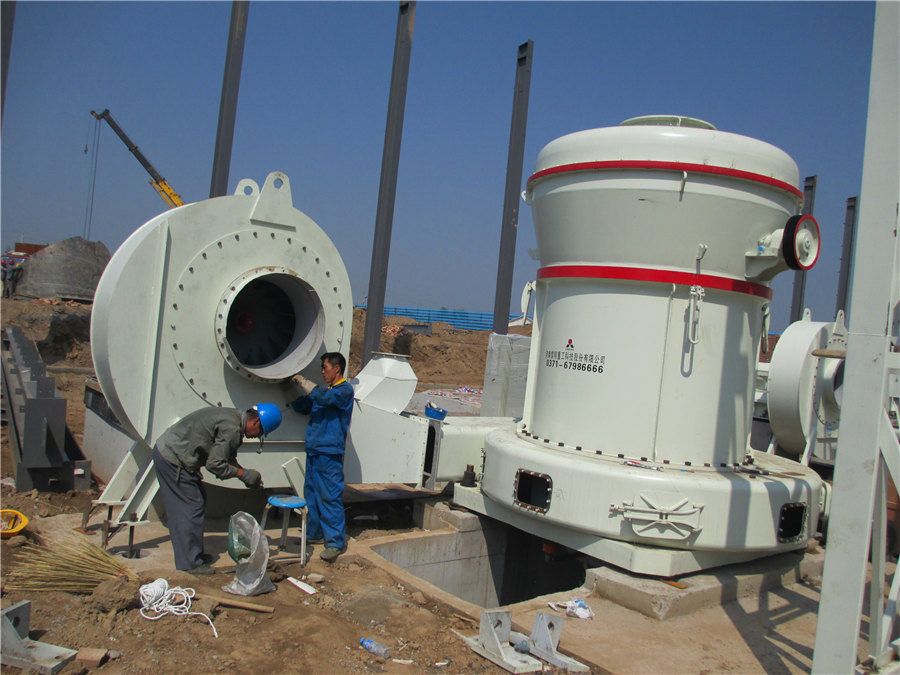
Raw Material Mill with Excellent Performance Fote Machinery
The raw material mill consists of feeding part, discharging part, gyre part, transmission part, Negative pressure in the working process can avoid the phenomenon of powder leaking The material drying degree can reach 6–8% because of heat preserving method adopted Parameter Product specification (m) Milling form: Transmission form:2023年12月14日 Material: NdFeB scrap Capacity: 40,000 tons/year Finished product particle size: 300 mesh Finished product use: rare earth materials Main equipment: MTW European version mill NdFeB Grinding Production Line Production Process The onsite raw materials are transported to the European version of the primary mill via a belt conveyor for grinding and NdFeB Powder Making Process Grinding Plant JXSC Mineral2010年1月1日 Then, using the ultrapure magnetite concentrate as raw material, highpurity reduced iron powder with Fe grade of 9906% was prepared by Höganäs process, of which bulk density, mobility and Elaboration of iron powder from mill scale ResearchGateThe pellet iron ore concentrate fine grinding pelletizing system comprises a feeding belt conveyer, a raw material ore bin, a vibrating funnel, a feed chute, a ball mill, a finished product ore groove, described powder selector is held with ball mill discharging mouth respectively by CNA Pellet iron ore concentrate fine Google Patents
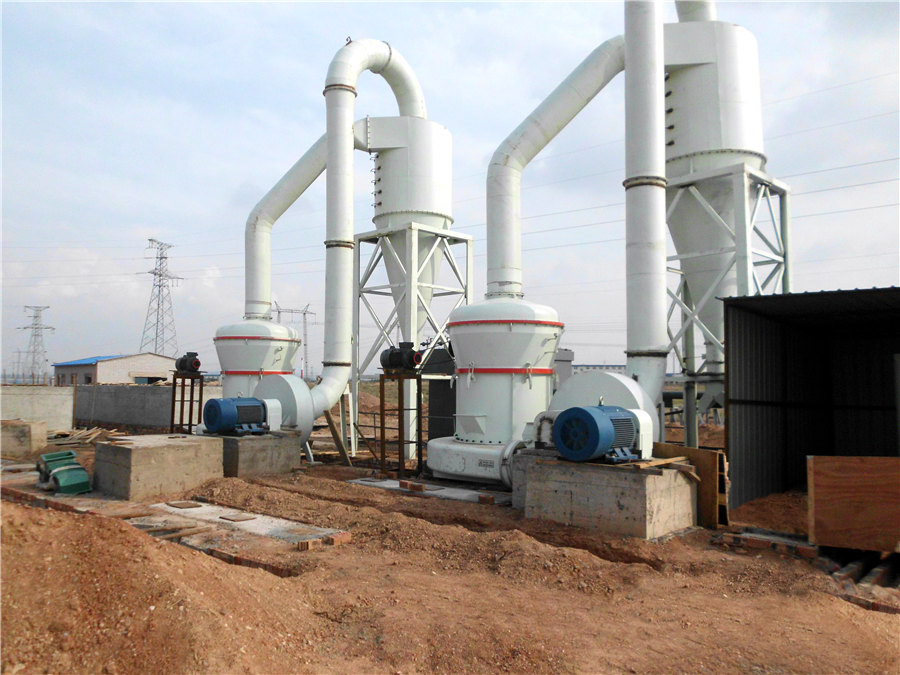
From Machining Chips to Raw Material for Powder Metallurgy—A
2021年9月20日 Chips are obtained by subtractive processes such as machining workpieces and until recently considered as waste However, in recent years they are shown to have great potential as sustainable raw materials for powder technologies Powder production from metal chips, through the application of solidstate processes, seems to be an alternative to powder or slightly sintered cake or strongly sintered cake depending on the temperature of reduction Obtained cake is ground to minus 100 microns by simple hand grinding using pistil and mortar and stored for further analysis 23 Characterization and Analysis Mill scale raw material and Iron powder samples obtainedDirect Reduction Recycling of Mill Scale Through Iron Powder 2024年5月9日 Unqualified powder is classified by the powder selector and returned to the main mill for regrinding until it reaches the required fineness requirements 3 Fine processing and modificationBentonite processing technology — from raw materials to products2019年6月22日 Introduction: Raw milling is one of the most important and integral component of cement production process; it is the stage which produces the most important intermediate product ieOptimizing Raw Mills Performance ; the Materials
.jpg)
Calcium Carbonate Ultrafine Powder Vertical Mill
SBM high quality calcium carbonate ultrafine powder vertical mill is widely used in many fields +17 [ Calcium carbonate is a common filler material used to increase the whiteness, after grinding continue moving to the edge of grinding plate until they are brought away by the airflow and enter the powder selectormaterials into a powder mixture of raw materials called Raw Meal The material consists of 8805% limestone; 1005% clay; Komposisi Raw Material masuk Raw Mill Tabel 4ANALISIS EFISIENSI PERALATAN DAN HEAT LOSS PADA RAW MILL 2024年2月23日 The operation of the cement raw mill is a critical step in cement production By grinding the raw materials into a fine powder, these powders can be more easily mixed with other cement ingredients and burn more evenly during the cement clinker process Therefore, the efficient operation of the cement raw mill directly impacts the production efficiency and quality How Does a Raw Mill Work in a Cement Industry1 A 5000t/d cement production line EPC turnkey project in South Africa adopts GRMR5341 raw material vertical mill of CHAENG 2 A 5000t/d cement production line in Henan, China adopts GRMR5341 raw material vertical mill of CHAENG 5000t/d cement production line of Henan Meng Electric Group adopts GRMR5341 raw material vertical mill of CHAENGVertical Raw Mill CHAENG
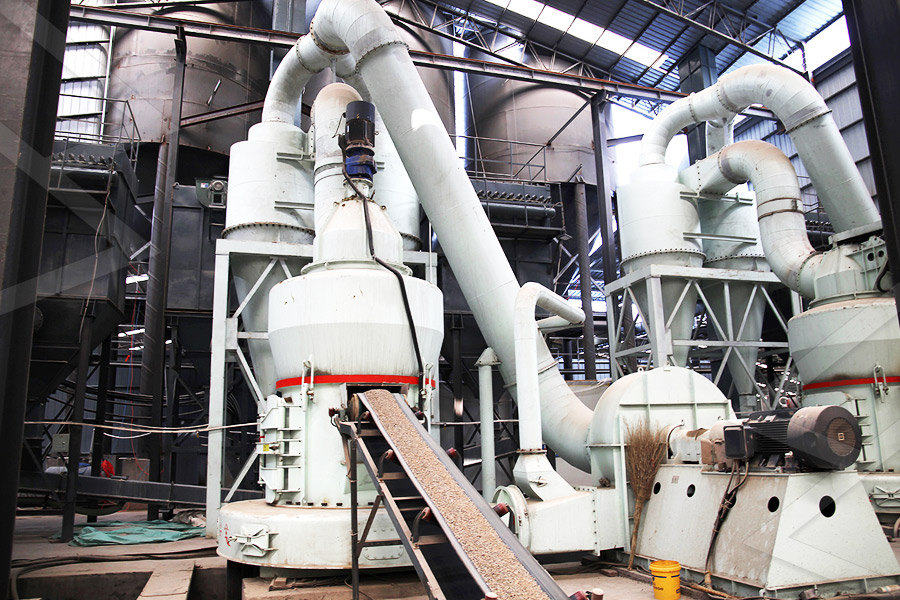
Design and Fabrication of a Simple Laboratory Ball Mill for Powder
2018年12月3日 A laboratory ball mill The produced milled coconut shell are demonstrated in Figure 46 For the testing, we use about 100 gram of coconut shell chips2021年1月22日 In the whole process of cement production, the electricity consumption of a raw material mill accounts for about 24% of the total Based on the statistics of the electricity consumption of the raw material mill system of 1005 production lines in China between 2014 and 2019, it is found that the average electricity consumption of the raw material preparation A Survey and Analysis on Electricity Consumption of Raw Material Mill Committed to providing “superfine powder EPC overall solution”, ultrafine powder analysis and research, raw material inspection and analysis, determination of product model and process, complete equipment manufacturing, installation and commissioning, worker training, delivery production and aftersales service, with more than 1,000 kinds of raw materials grinding and Classifying and Ball Mill Production Line ALPA Powder TechnologyRaw material ball mill, also called raw meal ball mill, is important grinding equipment in cement production process After being crushed, the raw meal enters the raw material mill The raw meal is grinded into fine powder by the motion and squeezing of steel balls The raw material mill manufactured by Great Wall Machinery can meet the raw material supply of 250~2500t dRaw material mill Great Wall
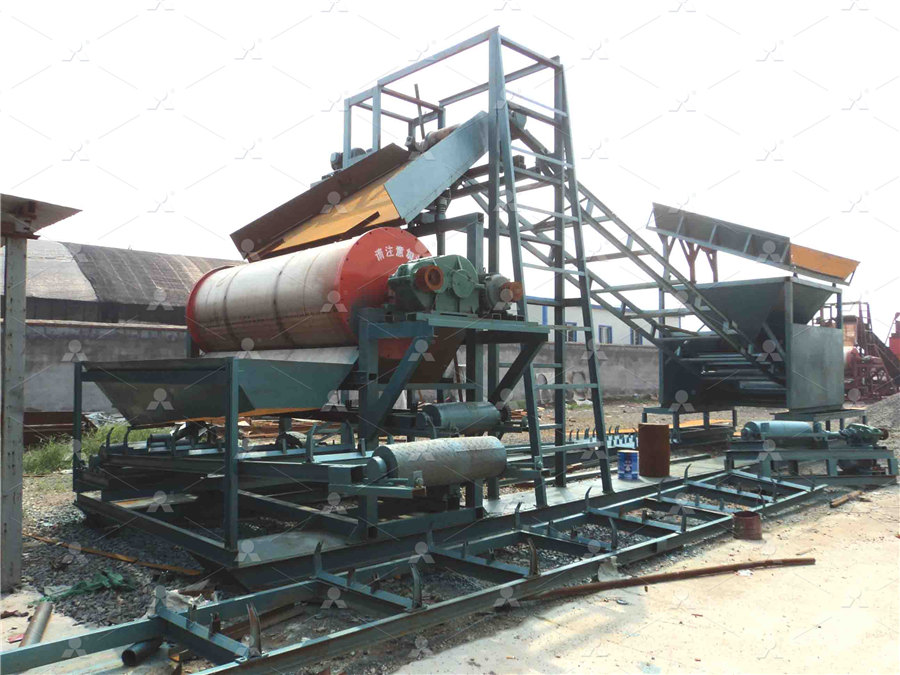
Powder Crusher, Powder Mixing Machine, Grinder,
Jiangyin Powder Mill Technology Co, Ltd Is mainly application in a full range of powder field, from the unit to the system, from the crushing, conveying, mixing, sieving to granulation, relates to production areas including food additives, 2022年4月6日 4 Grinding of Limestone and Additives: • Limestone and additives are mixed in required proportions so that the specified composition of the final product is maintained properly and ground in the raw mill (VRM / ball mill) to a fine powder • From raw materials to 8 steps of cement manufacturing, read2 More EnergySaving MultiHead Powder Separating Technology SBM adopted PLC control system and multihead powder separating technology in this grinding mill, which completely solve two problems, ie “highprecision and accurate CLUM Series Ultrafine Vertical Roller Mill2021年6月29日 mill rejects in a pilot scale vertical stirred mill,” Powder T echnology, vol 139, no 2, pp 165174, 2004 Traditional way is the solid phase synthesis of raw material mixtureEffects of Mill Speed and Air Classifier Speed on Performance of
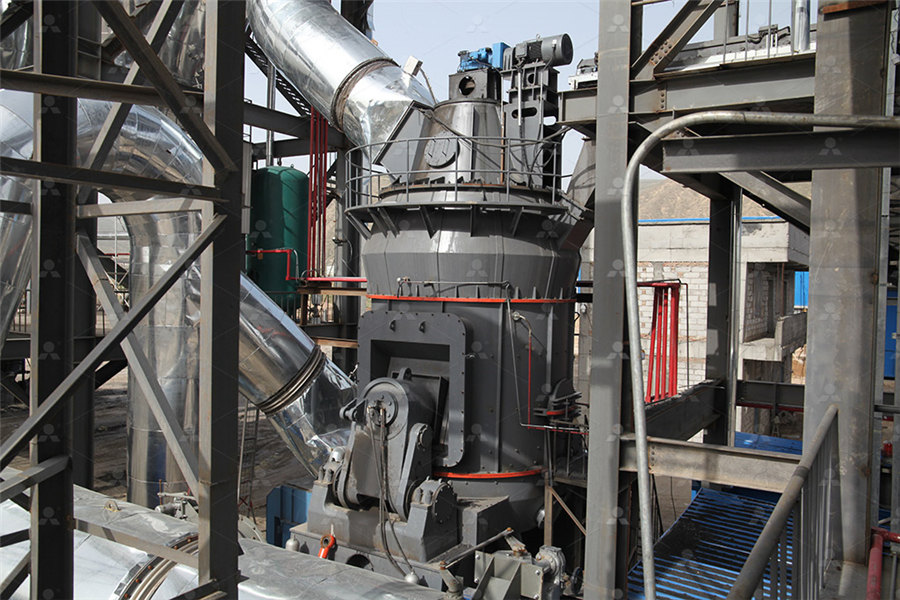
LM vertical roller mill will make a stunning appearance at bauma
LM vertical roller mill, referred to as vertical mill, integrates multiple functions such as crushing, drying, grinding, powder selection, and transportation, showing high grinding efficiency and strong drying capacity At the same time, the fineness adjustment is convenient, the noise is properly controlled, the power consumption is low, the process flow is simple, and the wear is smallJiangyin Powder Mill Technology Co, Ltd Is mainly application in a full range of powder field, from the unit to the system, from the crushing, conveying, mixing, sieving to granulation, relates to production areas including food additives, baking ingredients, pharmaceutical intermediate, health food, chemical raw materials and other industriesAbout Us Jiangyin Powder Mill Technology Co, Ltd is a 2016年11月7日 If then the raw material is fed in at the large end of the mill and the ground product removed at the smaller end, the powder in its progression through the mill is ground by progressively small balls and in consequence the theoretical ideal of a constant ratio between ball size and particle size during grinding is, to some extent, attainedGrinding Mills Common Types 911MetallurgistAfter the cement raw material is crushed, it will be sent into the raw mill for further grinding until a certain degree of fineness is reached, and then enter the clinker calcination process From the production experience of many cement plants, the selection of cement equipment , especially raw mill, will directly affect the project investment, production schedule and economic benefitsRaw Mill – Raw Mill In Cement Plant AGICO Cement Raw Mill
.jpg)
Understanding the Difference Between Raw Mill and Cement Mill
A raw mill is a type of grinding mill that is used to grind raw materials into a fine powder This powder can then be used as a raw material for the production of cement The raw materials that are fed into a raw mill include limestone, clay, shale, and iron orecalled so used as raw material metal powder It can also be used as a raw material a metal and ceramics composite materials The main steps of powder metallurgy are: powder production, mixing, compacting and sintering When necessary, after the sintering step can occur secondary operations like machining, milling and others Currently the Development of a HighEnergy Mill for Powder Metallurgy