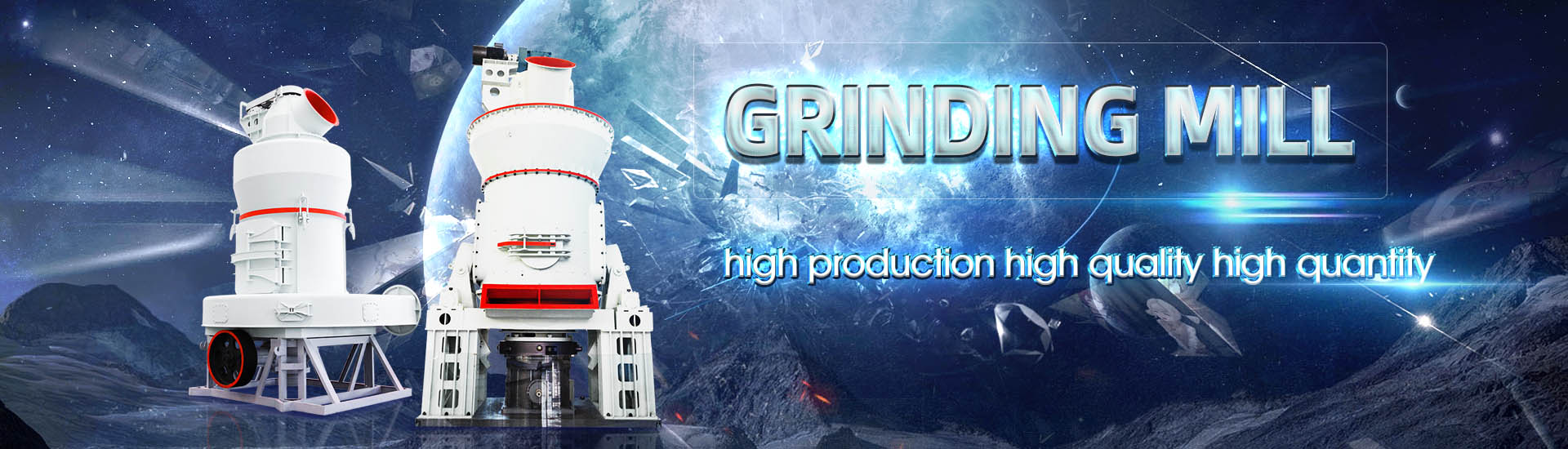
How to control the differential pressure of the coal mill
.jpg)
Modeling and Control of Coal Mill
The pressure drop, across the mill depends on the mill differential pressure of the primary air, and the amount of coal suspended in the air During normal operation, the mill pressure drop is 2012年1月1日 Advanced control strategies using pulverized fuel flow estimation or measurements could significantly improve the performance of plants; in fact performance close to oil fired power plants can be achieved Derivation and validation of a coal mill model for 2015年8月1日 The estimator is designed for controlling the pulverized fuel flow and the particle size distribution at the mill outlet, which is adaptive to the changes in coal grindability Mill Review of control and fault diagnosis methods applied to coal During normal operation, the mill pressure drop is predominately proportional to the primary air differential pressure and a small change in coal mass does not affect the pressure drop (PDF) Modeling and Control of Coal Mill Academia
.jpg)
PRESSURE BALANCING TECHNIQUES TO CONTROL
Pressure balancing is a term used to describe the reduction of absolute pressure difference across the seals and stoppings of an underground mine The objective for such a reduction is particles are carried through the outlet of the coal mill to the burner of the boiler The inputs of the coal mill model are coal flow into the mill, primary air flow, primary air inlet temperature and Modeling and Parameter Identification of Coal MillPoor dynamic performance of coal mill causes difficulties in maintaining the frequency, boiler pressure and temperature of the plant This paper presents development and validation of coal Modeling and outlet temperature control of coal mill using Model 2009年1月1日 This paper presents a coal mill model to be used for improved mill control, which may lead to a more optimal load following capability of power plants fired by pulverized coal Derivation and validation of a coal mill model for control
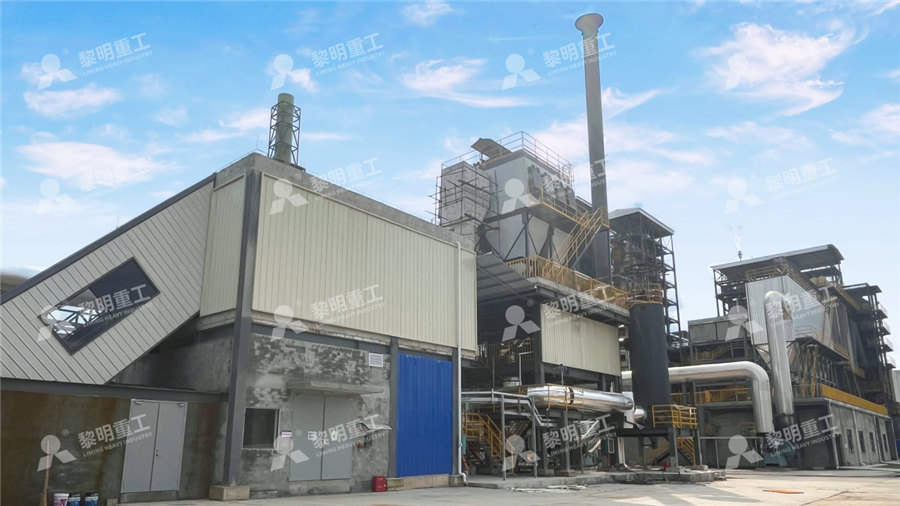
Modeling of Coal Mill System Used for Fault Simulation
2020年4月7日 The primary air system of a coal mill is mainly responsible for two tasks of coal powder drying and transmitting The inlet primary air flow is mainly determined according to the differential pressure and the resistance along the pressure difference between inlet and outlet, the grain size of the raw material [1, 2] For VRM the production capacity denotes both the capacity of grinding and drying of mill The grindability affects the capacity of grinding, type of mill and roller pressure The capacity of the mill is calculated Using G K * D 251PROCESS CONTROL FOR CEMENT GRINDING IN VERTICAL ROLLER MILL 2009年9月20日 A control oriented model was then developed by Fan (1994) and Fan and Rees (1994) In 2009, coal flow and outlet temperature of mill were modelled using mass and heat balance equations for startup Modeling and Parameter Identification of Coal Millspace and the layout of the mill furniture which rarely affords optimum positioning of the system hardware but various modeling concepts are deployed to achieve the optimum design taking all parameters into consideration Additionally, the thermal characteristics of different Mill applications are such that each system configuration isFundamentals of Roll Cooling and Control of Flatness at Lechler
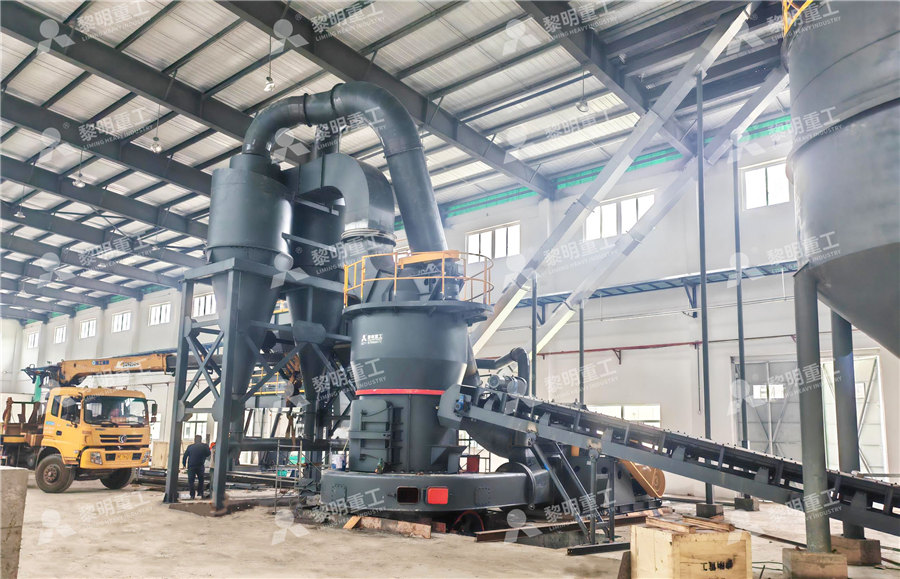
Improved Coal Fineness Improves Performance, Reduces Emissions
2011年10月1日 Utilizing engineering ingenuity and today’s developing computational fluid dynamics tools, a new classifier design is now available that significantly improves fineness from pulverizers without 2021年1月29日 The mill differential pressure is the difference between pressure a t mill inlet and mill outlet representing currently loading condition of the VRM Changes in the differential pressure when theIncrease productivity of vertical roller mill using seven QC tools2016年1月18日 Next, the paper estimates the coal outlet mass flow of the coal mill by using extended Kalman filter (EKF), and the result is compared with the coal flow instruction Finally, we take the estimation of coal outlet mass flow as the new controlled variable and use inferential predictive control method to solve the coal mill control problemsThe Inferential predictive control method of coal mill IEEE The inputs of the coal mill model are coal flow into the mill, primary air flow, primary air inlet temperature and primary air differential pressure, which are used inModeling and Parameter Identification of Coal Mill ResearchGate
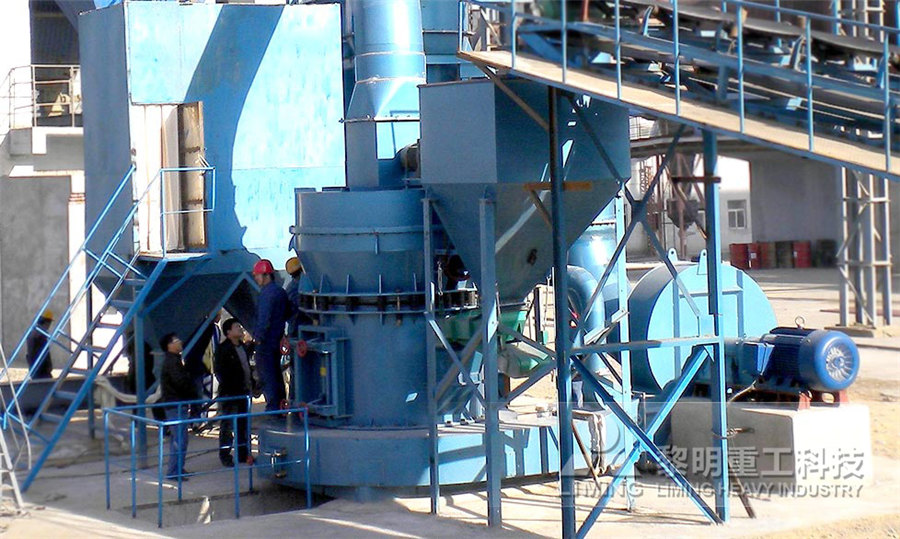
Pulverised Coal Flow measurement in Thermal Power Plant
Pulverised Coal, Primary Air, Mill Differential Pressure, Fitness Function, Raw Coal 1 INTRODUCTION In coal fired power plants, pulverised coal (PF) flow from coal mills is to be measured accurately for maximising combustion modelling and control specialists is 2020年4月7日 proportional to the differential pressure of the mill and the amount of coal powder stored in the mill [18] However, in case of coal blockage fault, the amount of coal p owder stored in the mil l Modeling of Coal Mill System Used for Fault Simulation• Mill motor speed • Mill air flow/mill differential pressure • Temperature after the mill • Pressure before the mill • Grinding stock feed • Classifier speed • Mill fan speed • Water spraying • Hot gas • Fresh air Manipulated variables Disturbance variable Process measured value RelauchLMmaster 6 250814 11:47PROCESS OPTIMISATION FOR LOESCHE GRINDING PLANTS2018年5月2日 The mill model for the steadystate milling process can be described by numerous equations [16, 17], containing five algebraic equations describing primary air flow based on pressure differences and air density, coal Detection of Malfunctions and Abnormal Working
.jpg)
Derivation and validation of a coal mill model for
520 P Niemczyk et al / Control Engineering Practice 20 (2012) 519–530 Nomenclature Dpmill mc mpc mcair mass of unground coal on the table (kg) mass of pulverized coal on the table (kg) mass of pulverized coal carried by pressure at mill inlet (mbar] (lower than the ambient press therefore also called ,draught”)differential pressure of bag filter [mbar]position of fan damper[%]position of recirculation air damper [%]position of fresh air damper [%] PROCESS TRAINING for operators of Vertical RAW Mills520 P Niemczyk et al / Control Engineering Practice 20 (2012) 519–530 Nomenclature Dpmill mc mpc mcair mass of unground coal on the table (kg) mass of pulverized coal on the table (kg) mass of pulverized coal carried by primary air (kg) wc wpc wout wret mass mass mass mass flow flow flow flow of of of of the dry raw coal to the mill (kg/s) pulverized coal (kg/s) pulverized coal Derivation and validation of a coal mill model for controlmodeling and control algorithms for individual coal mills However, there is still a lack ofresearch on mechanistic models and control strategies for the complete Additionally, equations for mill differential pressure and mill current are formulated within Optimization of the pulverized system of the coalfired power
.jpg)
Five essentials for optimizing hammermill operations
Controls include the differential pressure across the filters, the differential pressure to the fan inlet, monitoring of the material level inside the unit (do not use the filter receiver as a storage unit), and performance of the collected material discharge system 5 Ensure proper fan selectionThe estimator is designed for controlling the pulverized fuel flow and the particle size distribution at the mill outlet, which is adaptive to the changes in coal grindability Mill differential pressure and mill motor current are used as the observable variables while coal feed flow and classifier speed are used as the control variablesCoal Pulverizers an overview ScienceDirect Topics1999年7月1日 Fig 8 and Fig 9 gives a comparison of 7 hours automatic control (Fig 8) aJld 5 hours manual control (Fig 9)of mill 1 11 can be seen that, the outlet temperalUre and differential pressure under automatic control are much smoother than those under manual control, and the average of the feeder speed under automatic control is about to percent higher than that under Intelligent Control of CoalPulverizing Systems With BallTube Mill 1997年8月1日 For safe operation, the mill dP (mill bowl differential pressure) has to be kept within a certain range The existing mill control is a simple coaVair mass/mass control loop, as shown in Fig2a, which controls the air to coal ratio in a predefined range for efficient coal grinding, coal moisture drying and mill operation safety (Fig2b)Analysis of coal Mill Dynamic Characteristics Under Normal and
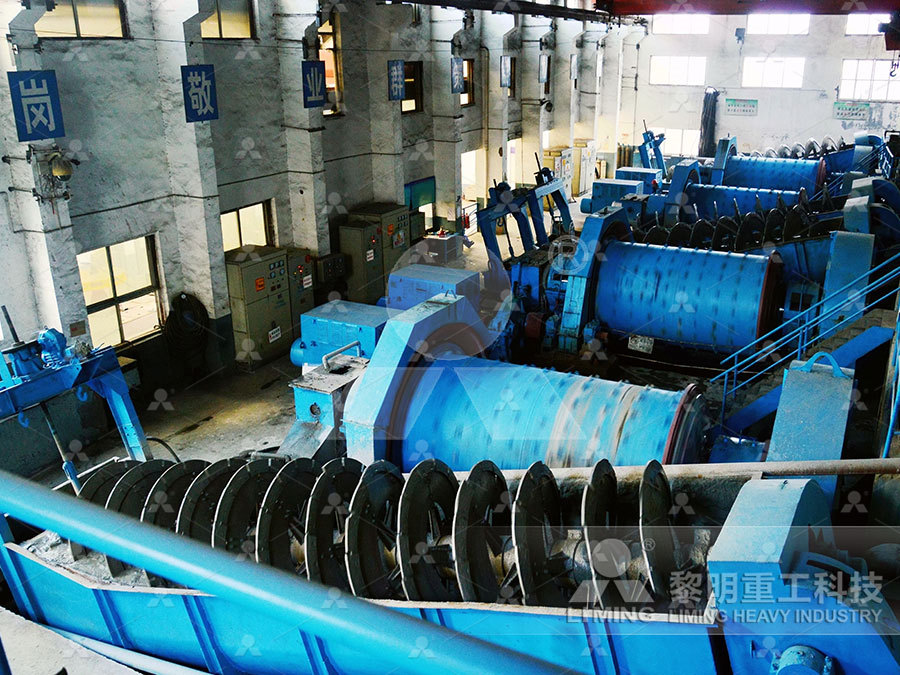
Dynamic classifiers: a fine way to help achieve lower emissions
2004年4月8日 Analysis of the results shows the mill pressure differential and the mill power consumption are a little higher with the dynamic classifier fitted A significant fraction of the increases measured is due to the harder coal being ground, 49 v 52 HGI, during the post conversion guarantee test at a nominal coal flow of 36 t/h2020年4月7日 The primary air system of a coal mill is mainly responsible for two tasks of coal powder drying and transmitting The inlet primary air flow is mainly determined according to the differential pressure and the resistance along the Modeling of Coal Mill System Used for Fault 2016年9月1日 Obtained results indicate that grinding pressure, primary air (PA) temperature and mill motor current have a tendency to rise by increasing coal feeding mass flow rates for all used coalOperational parameters affecting the vertical roller mill Mill drive power or mill differential pressure to control mill feed rate Inlet gas temperature Outlet gas temperature Outlet gas flow Few countable salient Features of Vertical Mills They are air swept mills, therefore has a higher drying capacity to handle an aggregate moisture of up to 20% in raw materialsCoal Grinding Cement Plant Optimization
.jpg)
Analysis of the Coal Milling Operations to the Boiler Parameters
2020年4月2日 The fo ur air control dampers at the inlet o f the mill control A differential pressure measurement was install ed multisegm ent coal mill model using an evolution ary computatio n primary air differential pressure, which are used in practice as control inputs to improve the coal mill performance The grinding motor power consumption can be considered as an additional input variable for a heating source The measured output variables are mill differential pressure and outlet temperature The coal mill model isModeling and Parameter Identification of Coal Mill2024年4月12日 Other indicators of performance include pressure differential, inlet temperature, temperature differential, exhaust gas flow rate, cleaning mechanism operation and fan current The Compliance Assurance Monitoring (CAM) Technical Guidance Document (TGD) is a source of information on monitoring approaches for different types of control devicesMonitoring by Control Technique Fabric Filters US EPA2021年8月1日 pressure is not less than 33 Automatic alarm when the differential pr essure of coal mill bowl is too it will cause high temperature at the out let of the coal mill, and the thermal control (PDF) Fault analysis and optimization technology of HP
.jpg)
Derivation and validation of a coal mill model for control
2009年1月1日 In order to acquire the valid set of parameters a proper cost function Q should be designed Normalized signals from available mill measurements, ie mill power, mill differential pressure, mill outlet temperature and pulverized coal flow, are used to calculate the fitness of each parameter set according to equation (9)2017年6月1日 This study aimed to master the operating characteristics of a pulverizing system, improve the output control precision of the system, and reduce the fluctuation amplitude of the main operating parameters of coalfired units A nonlinear dynamic model of a directfired pulverizing system that considers the effect of coal moisture on the energy balance of a coal Optimization control of a pulverizing system on the basis of the 2006年5月15日 Primary airflow has a major impact on the efficiency, capacity, and cleanliness of pulverized coal–fired generation Inaccurate measurements that underestimate primary airflow levels can lead to How accurate primary airflow measurements improve plant performance2012年5月1日 Jin et al established the dynamic relation between coal mill differential pressure and pulverized coal stored in the mill [9], and Zeng et al modeled moisture content in pulverized coal by Derivation and validation of a coal mill model for control
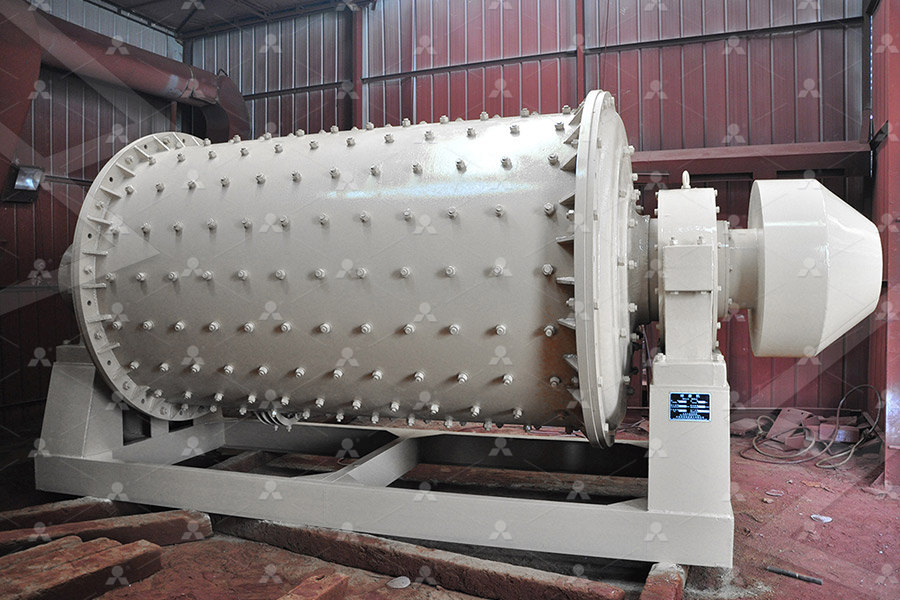
PRESSURE BALANCING TECHNIQUES TO CONTROL SPONTANEOUS COMBUSTION
Using this method, the differential pressure across an isolation seal or set of seals is equalized by an external pressure source such as a fan, compressed air, or pressurized fluid This requires the establishment of pressure chambers, the injection of inert gases, and monitoring for pressure differentials and combustion2013年8月1日 Coal mills are used to grind and dry the raw coal containing moisture and to transport the pulverized coal air mixture to the boiler Poor dynamic performance of coal mill causes difficulties in Modeling and outlet temperature control of coal mill using 2021年11月9日 Table 3 presents the power consumption and differential pressure of the roller mill The ratios were calculated by dividing the power consumption or differential pressure of the blend tests with those of the control (coal only) Compared to milling coal alone, the power consumption increased as the TP content increasedMilling Characteristics of Coal and Torrefied Biomass Blends in a 2015年2月1日 Wei and Wang established a simple model for the mill Genetic algorithm was used to optimize the parameters of the model, and the multistage modelling method was proposed to match the conditions during start up and shut down [1]Shin and Li presented a model with two particle sizes and pressure drop dynamics [2]However, the effect of coal Modelling and control of pulverizing system considering coal
.jpg)
Ratio Control and MeteredAir Combustion Processes
By Allen Houtz 1 and Doug Cooper A ratio control strategy can play a fundamental role in the safe and profitable operation of fired heaters, boilers, furnaces and similar fuel burning processes This is because the airtofuel ratio in the combustion zone of these processes directly impacts fuel combustion efficiency and environmental emissions2 COAL MILL MODELLING In thermal power plant, pulverization of coal is carried out by coal mill Raw coal is moved from the storage to the mill by conveyor mechanism The type of coal mill envisaged for our model is bowl mill which is shown in Fig1 Raw coal is introduced near the centre of the grinding table through the coal feed pipePulverised Coal Flow measurement in Thermal Power Plantused to calculate the particle size distributions and flowrates of each stream Statistical adjustment of the raw data was made by reconciliation procedurePerformance Evaluation of Vertical Roller Mill in Cement Grinding: The counter pressure reduces the noise generated by the mill and is adjustable depending on the coal properties and required coal fineness During operation, both pressures are adjusted proportionately to the feeder speed by means of pressure control valves to achieve an optimized grinding force characteristic throughout the mill load rangeCOAL PULVERIZER DESIGN UPGRADES TO MEET THE DEMANDS
.jpg)
Review of Control and Fault Diagnosis Methods Applied to Coal
2015年5月7日 Blockage in a coal mill results in an increase in differential pressure (DP) and mill current and a decrease The inability of the coal mill control structure to monitor and control pulverized