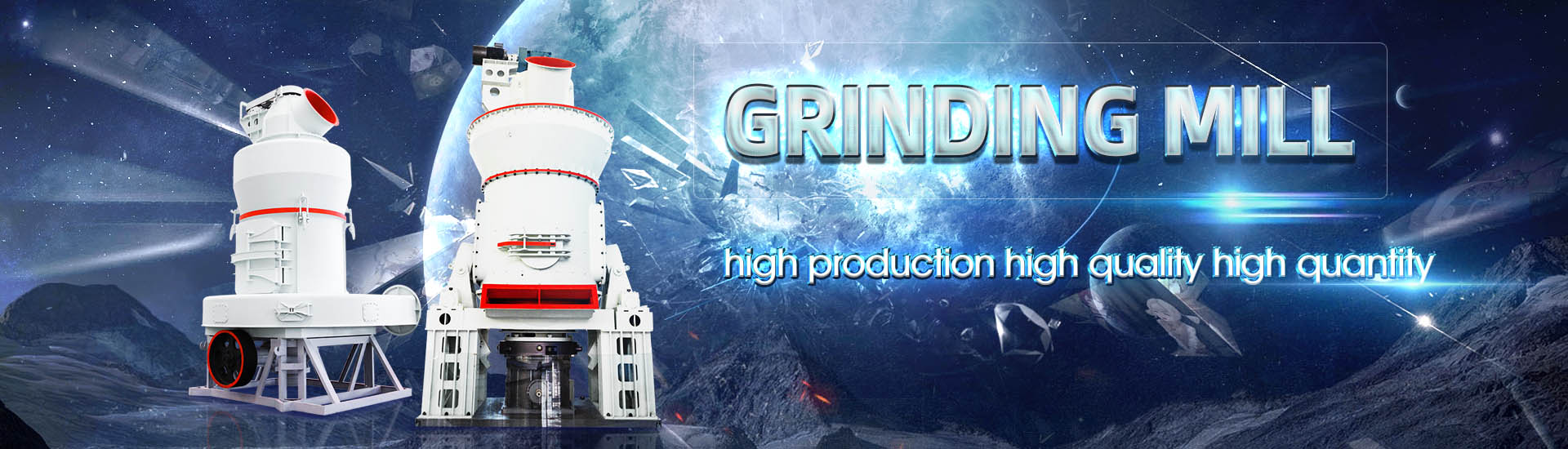
JCM energysaving circulating coarse powder mill
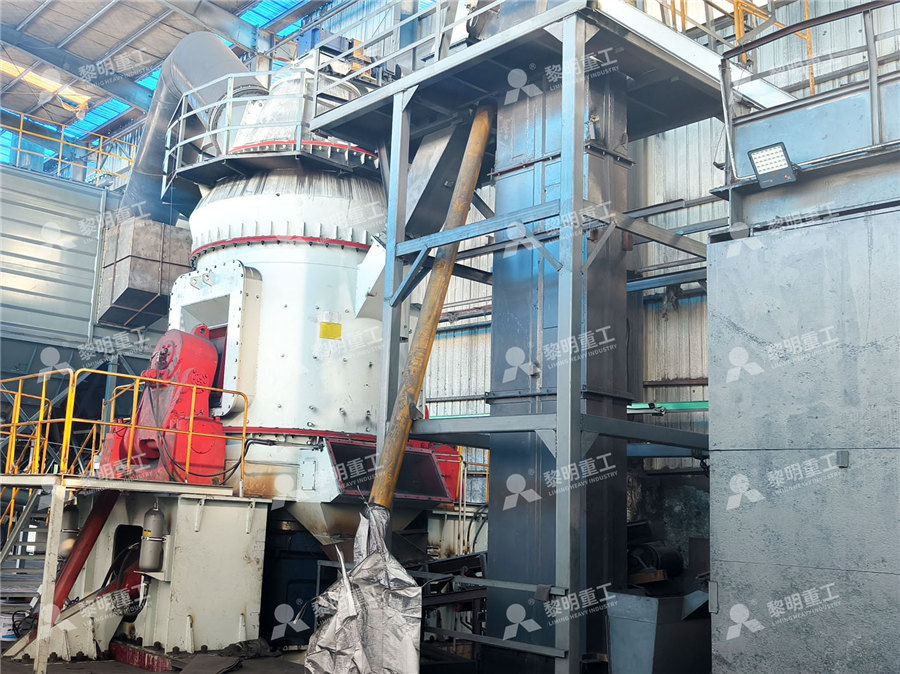
Original Research PaperSize reduction performance evaluation of
2023年1月1日 About 40% of energy could be saved by using HPGRstirred mill circuit than the HPGRball mill circuit The present research findings state that the two stages of HPGR It showed that, working at coarser feed (high circulating loads), RGM could be more efficient than balls, thus lowering the power consumption of tumbling mills The mass of undersize products A Comparative Study of Energy Efficiency in Tumbling Mills with2023年6月14日 Compared with the general flat spiral jet mill and reverse jet mill, it can save energy by 30–40% Fluidized bed reverse jet mill is one of the equipment widely used in dry Jet Mill SpringerLinkVertical stirred milling is a wellrecognized technology for the secondary, regrind and fine grinding applications and are increasingly replacing coarser ball mill applications in secondary and RECENT DEVELOPMENTS IN COARSE GRINDING USING VERTICAL
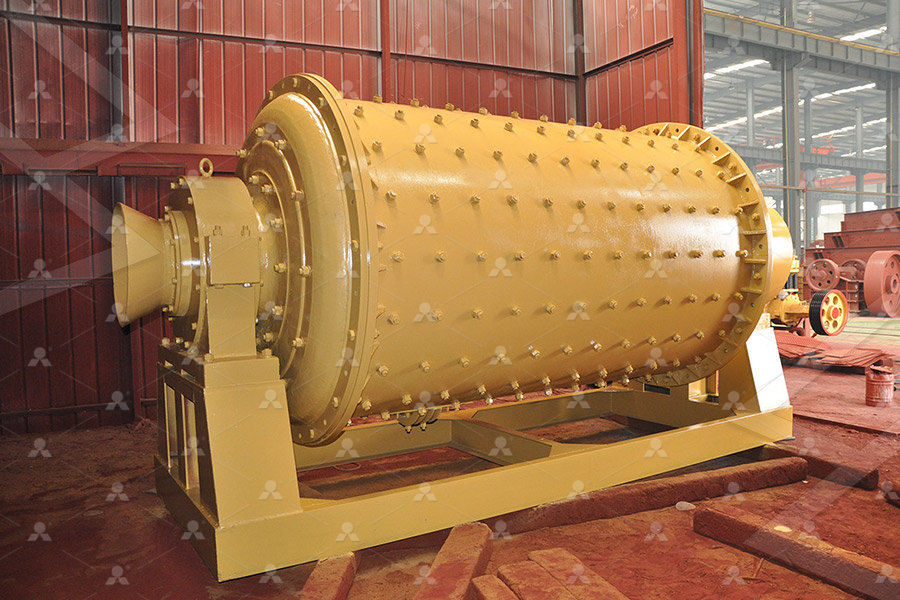
Comparison of energy efficiency between ball mills and stirred
2009年6月1日 They dominate these applications because greater stress intensity can be delivered in stirred mills leading to better energy efficiency over ball mills in fine and ultrafine 2023年11月1日 The successful application of the ceramic medium stirring mill to replace the twostage ball mill has established a new research direction and solution for the energy saving Energy conservation and consumption reduction in grinding Grinding media play an important role in the comminution of mineral ores in these mills This work reviews the application of balls in mineral processing as a function of the materials used to Comparison of energy efficiency between ball mills and stirred 2023年7月10日 The present literature review explores the energyefficient ultrafine grinding of particles using stirred mills The review provides an overview of the different techniques for EnergyEfficient Advanced Ultrafine Grinding of Particles Using
.jpg)
neTZsCH Fluidized Bed Jet Mill CGs
Fluidized Bed Jet Mill Type CGS 180 for milling air consumption of 11 660 m3/h The grinding gas nozzles can be delivered in various executions and are selected to suit the desired fineness 2013年12月18日 Grinding activities in general (including coarse, intermediate, and fine grinding) account for 05 pct of US primary energy use, 38 pct of total US electricity consumption, Energy Use of Fine Grinding in Mineral Processing2021年9月27日 Stage 1: Crushing The large attapulgite is initially crushed and processed by the crusher According to the size of attapulgite raw materials and different output requirements, crushers of corresponding specifications can be selected, such as jaw crusher, impact crusher, cone crusher, etc Stage 2: Grinding After crushing, the attapulgite is evenly lifted from the Attapulgite Ultrafine Powder Grinding MillSaving energy with the The unique grinding process eJet®, for which a patent has been applied, makes the use of air jet mills significantly more efficient through adapted grinding conditions and an optimized process Energy savings of up to 30 % for eg minerals or amorphous chemical products, are convincing arguments!neTZsCH Fluidized Bed Jet Mill CGs
.jpg)
Sepiolite Superfine Powder Grinding Mill SBM
2021年9月29日 Sepiolite superfine powder grinding mill is a highefficiency, energysaving, lowconsumption, and environmentally friendly industrial nonmetallic ore mill We also have a coarse powder mill (08mm), wet mill (325 A vertical roller mill is an energysaving mill that meets market demand It has a low operating cost and highcost performance Home; construction, chemical industry, and other industries to make powder, especially for materials such as cement clinker, coal powder, while the coarse material is recirculated for further grinding 4Energysaving and Efficient Vertical Roller Mill Fote Machinery2016年10月5日 In this chapter an introduction of widely applied energyefficient grinding technologies in cement grinding and description of the operating principles of the related equipments and comparisons over each other in terms of grinding efficiency, specific energy consumption, production capacity and cement quality are given A case study performed on a EnergyEfficient Technologies in Cement Grinding IntechOpen2023年8月15日 Supplementary Relationship between Circulating Load and Classification Efficiency in Closed Circuit Ball Mills(PDF) Supplementary Relationship between Circulating Load and
.jpg)
Comparison of energy efficiency between ball mills and stirred
2009年6月1日 At product sizes finer than 80% passing 75 μm, the efficiency of ball mill grinding rapidly decreasesThe practical limit to ball mill product fineness is considered to be 40–45 μm (Gao and Weller, 1994)Although ball mills can still be found in the regrind circuits in a number of mineral processing plants, their energy consumption is high, and size reduction efficiency is lowChina Coarse Mill wholesale Energy Saving: Energy Saving Certification: CE, ISO, FDA 1 / 4 Favorites Gypsum European Powder Grinding Mill Coarse Powder Hammer Milll Aggregate Coarse Powder Grinder Mill for Sale US$ 500050000 / Piece 1 Piece (MOQ)Coarse Mill MadeinChinaFind your powder mill easily amongst the 104 products from the leading brands (Fritsch GmbH, NETZSCH, BOHLE, rotor food coarse powder laboratory mill FNG00 Final grain size: 1 µm 500 µm Energy saving, good sealing performance and stable quality Powder mill, Powder grinding mill All industrial manufacturersJCM is a fullyintegrated renewable energy Independent Power Producer developing and operating clean energy projects in South Southeast Asia and subSaharan Africa IMPACT Our portfolio of clean energy projects have significant, measurable and positive impact PROJECTSJCM Power
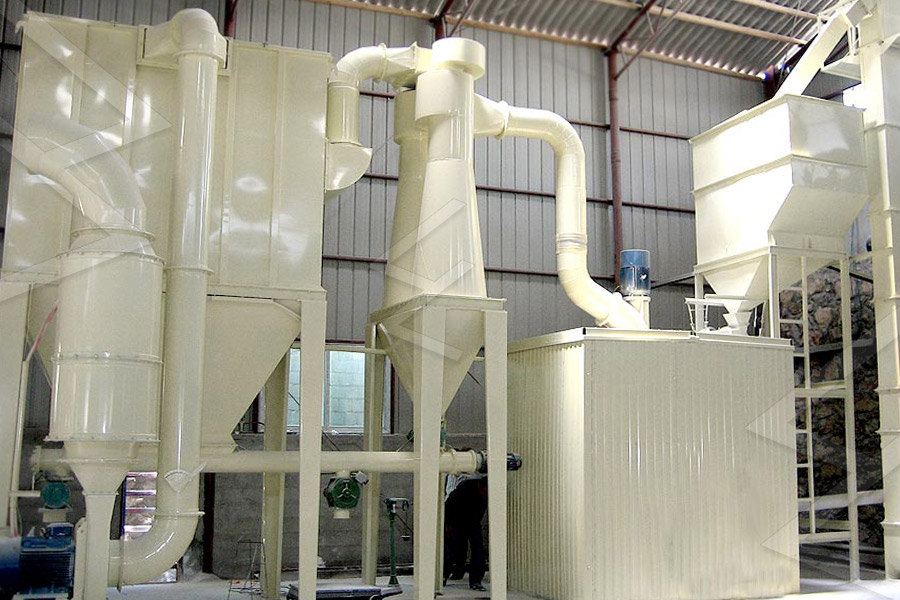
Quartz Industrial Powder Grinder Machine SBM
2021年10月11日 Quartz industrial powder grinder machine can be used to further grind quartz sand into quartz powder, and its fineness can be adjusted freely between 1503000 mesh The industrial grinding mills independently and mill dimensions etc However, the energy efficiency in the coarse grinding chamber is extremely poor and there is limitation to improve both performances for coarse and fine grinding on the same mill by ball size selection etc Therefore, a new system was proposed and developed by installing a pregrinder,Vertical roller mill for raw Application p rocess materialsThe composition of the coarse powder hammer mill 1 Frame part: It consists of side panels, front box components, rear box weldments, etc 2 The rotating part of the eccentric shaft: It is mainly composed of the movable jaw, the eccentric Hammer Mill PCC Coarse Powder Grinding Mill2021年10月13日 The fluorite fine powder grinding mill is stable, energysaving, environmentally friendly, intelligent, and efficient, and is the first choice for processing fluorite Coarse powder grinding mill is engaging in crushing various rocks and stones with comprehensive strength not higher than 320 MPA into coarse powder and small Fluorite Fine Powder Grinding Mill SBM Ultrafine Powder
.jpg)
Roller Mill Springer
R Roller Mill Xiao Xiao1, Huang Lilong2 and Xu Kuangdi3 1Changsha Research Institute of Mining and Metallurgy, Changsha, China 2Changsha Research Institute of Mining and Metallurgy, Changsha, China 3Chinese Academy of Engineering, Beijing, China Roller mill is a type of grinding equipment for crushing materials by pressure between two or① Integrated design, less comprehensive investment The machine integrates crushing, grinding, powder selection, conveying, and packaging The system is simple, and the layout is compact The floor area is about 50% of the ball mill system, and it can be arranged in the open air, greatly reducing investment costsStone Powder Making Machine2021年4月29日 percentage of coarse solids in the mill, a high circulating load results in a much more Industrial tests with innovative energy saving grinding bodies J Powder Technol 2008, 182, 113 (PDF) A Comparative Study of Energy Efficiency in ResearchGate2021年11月3日 Phosphate mineral powder grinding mills are processing equipment for phosphate rock powders Choosing a highefficiency, intelligent, energysaving, and environmentally friendly phosphate rock powder mill can greatly enhance the market competitiveness of phosphate rock powders and create more great valuePhosphate Mineral Powder Grinding Mill SBM Ultrafine Powder
.jpg)
Air Classifying Mill
MIKRO ACM® AIR CLASSIFYING MILL The Mikro ACM® Air Classifying Mill is an air swept mechanical impact mill with a dynamic air classifier designed to grind an extensive range of materials down to a D97 of 20 microns The Mikro ACM® Air Classifying Mill is available in a range of sizes and can be supplied for laboratory use or large It is mainly suitable for micro powder processing of noninflammable and explosive brittle materials with medium and low hardness and Mohs hardness ≤6, such as calcite, limestone, dolomite, kaolin, bentonite, talc, mica, magnesite, Barite, gypsum, graphite, fluorite, phosphate rock, potassium ore, etc Micro powder grinding mill is double in capacity compare with Energy Micro Powder Grinding Mill2019年3月8日 Thermal energy savings from process control systems may vary between 25 percent and 10 percent, and the typical savings are estimated at between 25 percent and 5 percent 17IMPROVING THERMAL AND ELECTRIC ENERGY 2022年5月23日 Venugopal (2022): Modeling and application of stirred mill for the coarse grinding of PGE bearing chromite ore, Separation Science and Technology, DOI: 101080/2022Modeling and application of stirred mill for the coarse grinding of
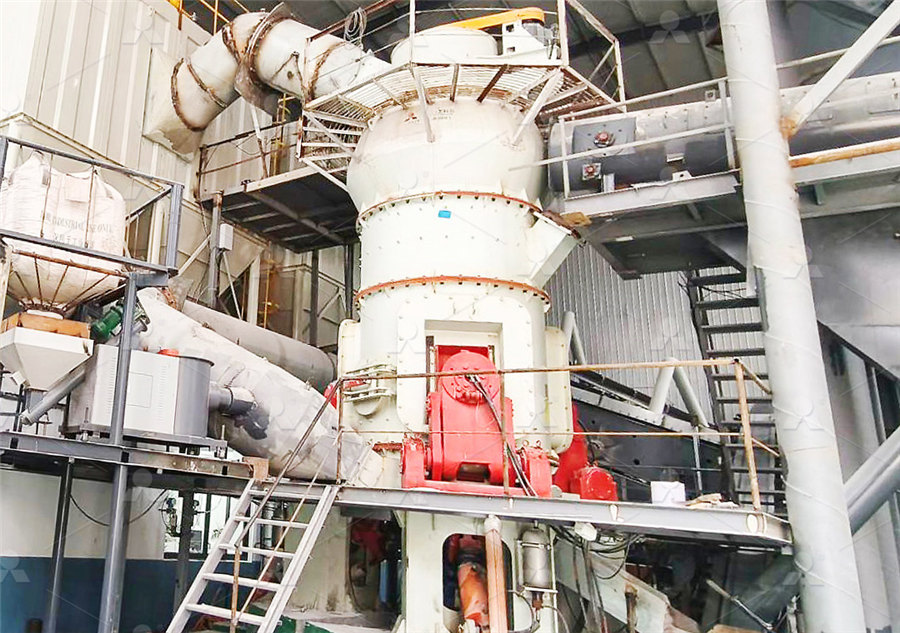
Calcium Carbonate Ultrafine Powder Vertical Mill
2 More energysaving multihead powder selection technology SBM adopts PLC control system and multihead powder selection technology in this mill, which completely solves the two problems of “high precision and accurate cutting powder diameter and quick switching of different production requirements”Energy consumption of the coarse coal Generally, energy input of a roller mill during grinding processing is calculated by the following equation (Xie et al, 2015b): ∫E= (𝑝) 𝑡=∫(𝐹∙ ∙𝑟∙𝑛𝑏) 𝑡 0 𝑡 0 𝑡 (1) where Eis the energy input of the mill (J), p is the power draw(Js1), F is the rollerResponse of energysize reduction to the control of circulating 2008年1月1日 The characteristics and the development of a new planetary ball mill are introduced Firstly, based on the material fatigue damage accumulation theory, the energysaving mechanism of the planetary Development of planetary mill and its energysaving mechanismA Strong Energy Portfolio for a Strong America Energy efficiency and clean, renewable energy will mean a stronger economy, a cleaner environment, and greater energy independence for America Working with a wide array of state, community, industry, and university partners, the US Department of Energy’s Office of Energy Efficiency andITP Mining: MinetoMill Optimization Energygov
.jpg)
VM Series Coarse Powder Vertical Mill Grinding Mill Fertilizer
VM series vertical mill is an energysaving advanced grinding equipment that integrates drying, grinding, classification and conveying VM vertical mill has advantages of high grinding efficiency, low power consumption, large feed granularity, easy product fineness adjustment, simple equipment process, small footprint, low noise, low dust, easy operation and maintenance, low 2021年9月30日 Chalk micro powder mill can grind nonmetallic ores into fine powder up to 6000 meshes large processing capacity, energysaving, and consumption reduction Pyrophyllite industrial powder grinding mills can grind nonmetallic ores such as pyrophyllite into a coarse powder or fine powder up to 6000 mesh See More >>Chalk Micro Powder Mill SBM Ultrafine Powder TechnologyCoarse Crusher With Dust Collector; Pin Mill Menu Toggle Cyclone Gains Flour Mill For Your Powder Processing Task: Since it features a simple structure, firm and stable operation and good crushing effect, energysaving circulating water systemsCyclone Gains Flour Mill YindaHigh energy utilization rate, low operating cost, grinding particle size range D50: 0510μm The revolution of dry milling technology, the milled particle size can reach submicron or nanometer level, which greatly improves the energy utilization efficiency and realizes low carbon, energy saving, environmental protection and resource recycling by supersonic steam jet millSupersonic Steam Jet Mill ALPA Powder Equipment
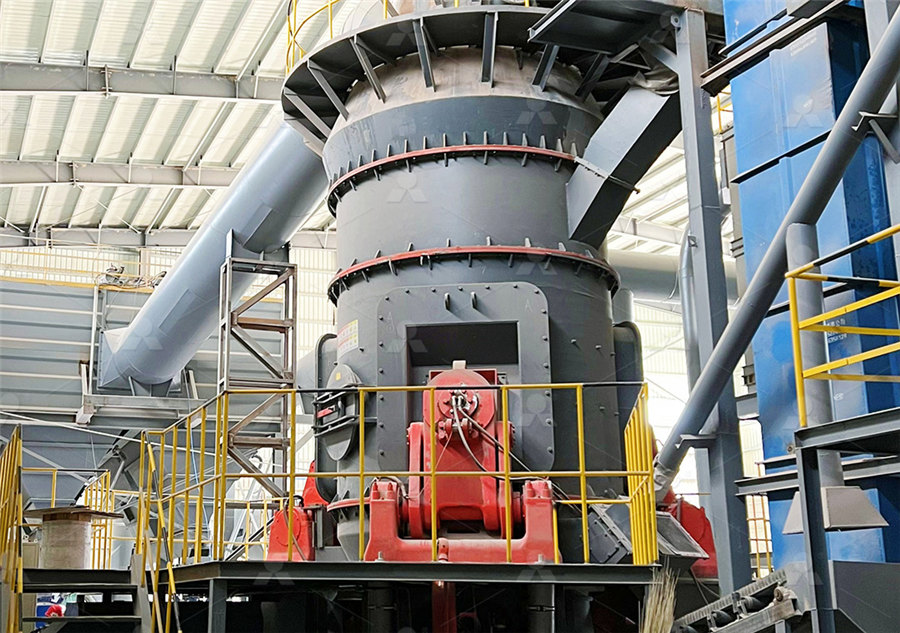
Enhancing the Grinding Efficiency of a Magnetite
2024年1月31日 Ceramic ball milling has demonstrated remarkable energysaving efficiency in industrial applications However, there is a pressing need to enhance the grinding efficiency for coarse particles This paper introduces a 2017年1月17日 Other process activities, such as spraying the ore with water for dust control or the fact that runofmine ore moisture is approximately 2%5% are not generally considered (Bleiwas, 2012a)Breaking down energy consumption in industrial 2019年3月27日 A good jet mill not only own high production efficiency and energy saving, but also has reasonable structural design, easy maintenance and cleaning, long service life and reasonable price of parts In the field of ultrafine powder technology research and equipmentJet Mill ALPA Powder TechnologyThe Circulating Load Formula is a crucial aspect to understand in the world of ball milling It helps determine the efficiency and effectiveness of the mill operation, allowing for optimization and improvement In simple terms, the circulating load can be defined as the mass of coarse material returned to the mill per unit of fresh feedhow to calculate circulating load in ball mill – stone cruxder
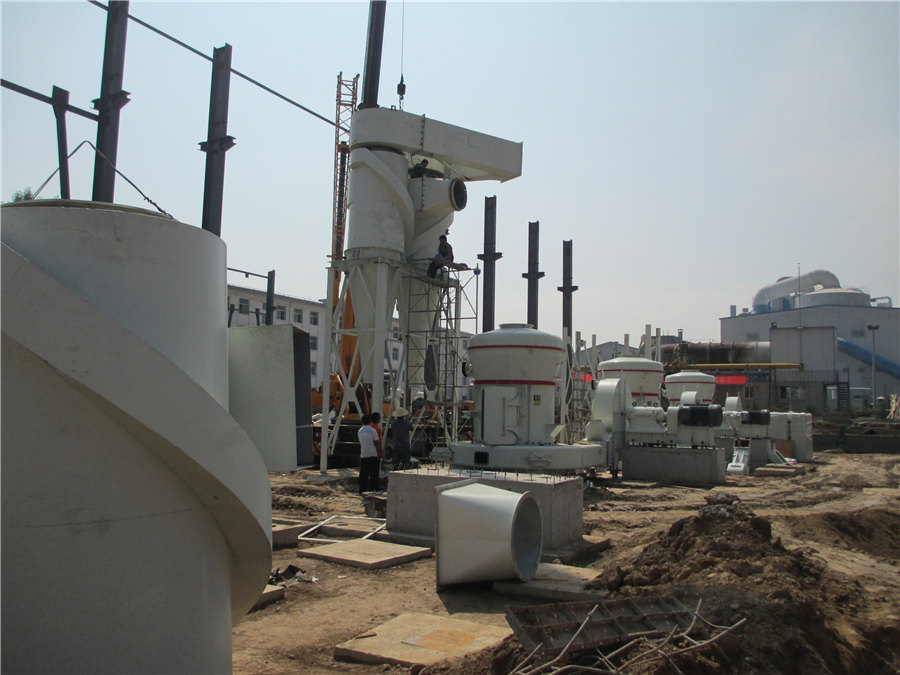
CLRM series Raymond mill SBM Ultrafine Powder Technology
CLRM series Raymond mill Discharge fineness: 80500 mesh Feed size: 35 mm Output: 135 t/h Materials: Quartz, feldspar, barite, carbonate calcite, limestone, talc, ceramics, iron ore, emery, bauxite, phosphate rock, coal and other materials, a total of about 400 kinds of materialsAn evaluation of Relo grinding media (RGM, Reuleaux tetrahedronshaped bodies) performance versus standard grinding media (balls) was made through a series of grinding tests, including a slight modification of the standard Bond test procedure Standard Bond tests showed a reduction in the Bond ball mill work index (wi) of the mineral sample used in this study when using Relo A Comparative Study of Energy Efficiency in Tumbling Mills withJanuary 2007, two complete grinding circuit surveys were performed followed by a SAG mill crash stop and grindout After stopping the mill, a SAG mill feed sample was also collected from Conveyor parison of SAG mill feed size throughputs2022年4月1日 Previous researches showed that the energy consumed by the movement of grinding media and material accounted for 74%–80% of the total energy, while only less than 1% of the energy input was virtually used to create new surface, and the remaining part lost in forms of sound energy and heat energy within a mass of collision and friction (Fuerstenau and The first attempt of applying ceramic balls in industrial tumbling mill
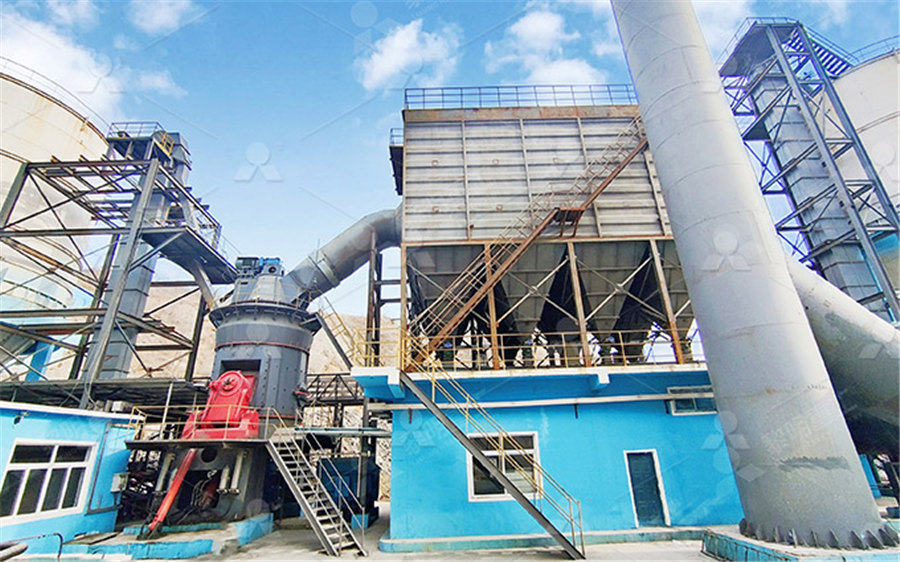
The new generation combustion technology for energy saving circulating
2009年8月1日 The influence of furnace bed pressure drop on the performance of circulating fluidized bed coalfired boiler was analyzed, and the design theory and method were proposed for the energy saving 2019年4月15日 Relative mill availability has not been considered in this cost evaluation, but it can also represent a considerable saving The ball mill availability ranges between 9496% whereas that of the rod mill ranges between 9294% particularly because of Coarse Grinding in a Ball Mill 911Metallurgist