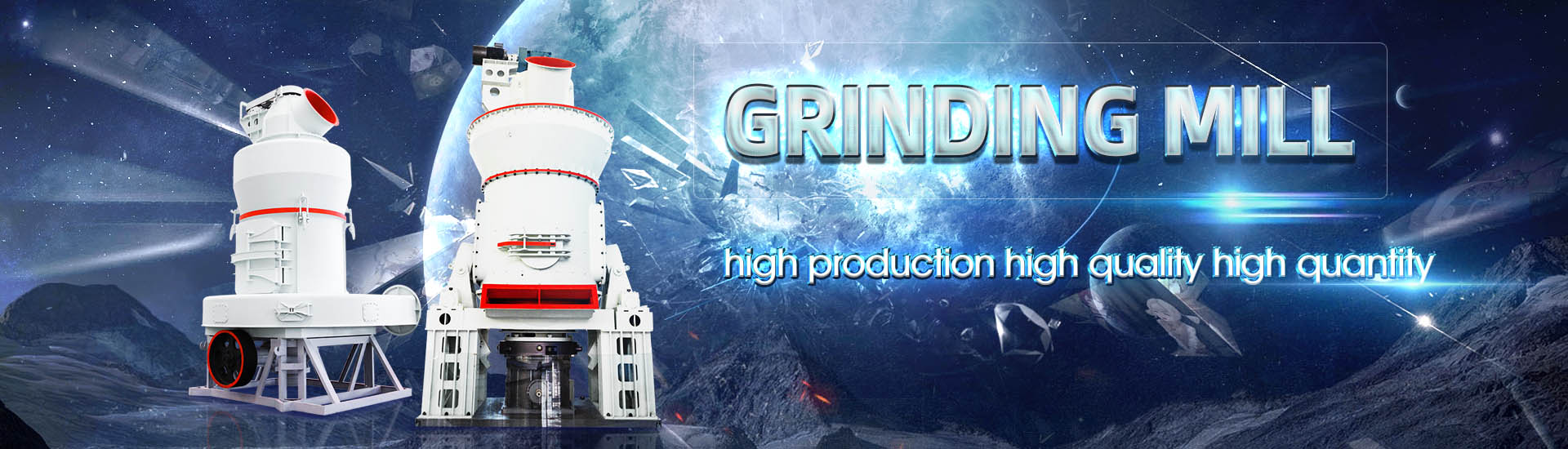
Cement raw material grinding process diagram
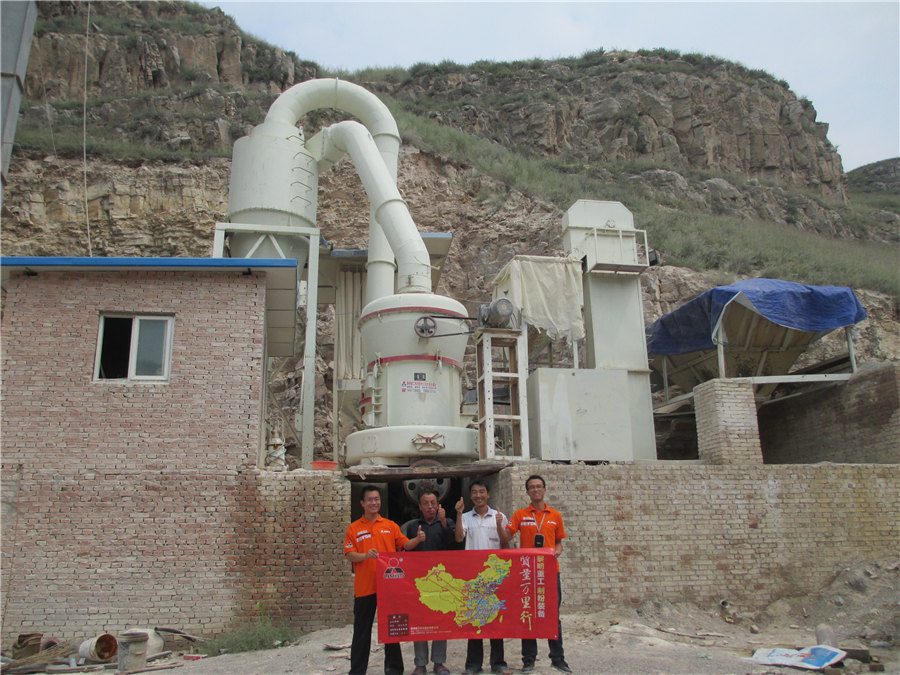
116 Portland Cement Manufacturing US Environmental
A diagram of the process, which encompasses production of both portland and masonry cement, is shown in Figure 1161 As shown in the figure, the process can be divided into the following The purpose of this study is to examine the production process, its economic support, raw material availability, demand, process modification, optimization steps to implement the productionTypical cement manufacturing process flow diagram 2014年6月10日 This document discusses Portland cement and the cement manufacturing process It begins with an overview of what cement is and how it is used to make concrete It then describes the industrial process for Cement manufacturing process PPT Free DownloadThe whole process of cement manufacturing in Messebo Cement plant which consists of two separate Cement Production lines can be summarized into the following processes ;as can be CEMENT PRODUCTION AND QUALITY CONTROL A Cement
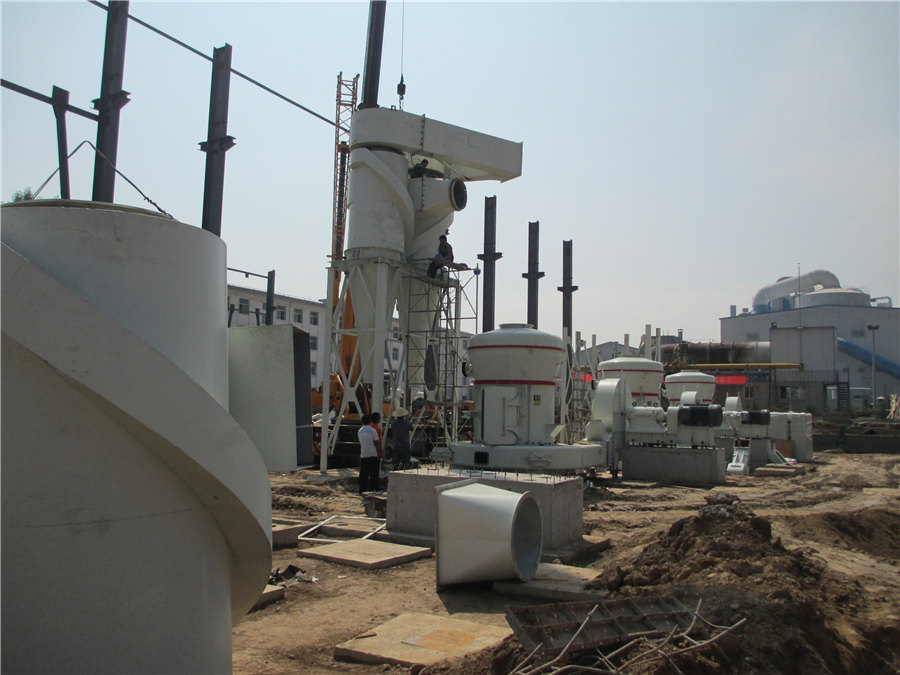
Manufacture of Cement Materials and Manufacturing
Manufacture Process of Cement The manufacture procedures of Portland cement is described below Mixing of raw material; Burning; Grinding; Storage and packaging; 1 Mixing of raw material The major raw materials used in the 1971年8月17日 As shown in the figure, the process can be divided into the following primary components: raw materials acquisition and handling, kiln feed preparation, pyroprocessing, 116 Portland Cement Manufacturing US EPAThere are six main stages of the cement manufacturing process The raw cement ingredients needed for cement production are limestone (calcium), sand and clay (silicon, aluminum, iron), How Cement is Made Cement Manufacturing Processcommon solution to grind raw materials and cement Roller presses are used mainly in combination with a ball mill for cement grinding applications and as finished product grinding BALL MILLS Ball mill optimisation Holzinger Consulting
46.jpg)
Raw Material DryingGrinding Cement Plant Optimization
Drying of moisture in raw materials is required for effective grinding and subsequent handling of raw meal This is achieved normally by ducting part of the kiln exhaust gas through the mill Providing a comprehensive guide to the entire cement production process from raw material extraction to the finished product, the industry’s favourite technical reference book is now fully The Cement Plant Operations Handbook International Cement 2024年11月23日 Cement Extraction, Processing, Manufacturing: Raw materials employed in the manufacture of cement are extracted by quarrying in the case of hard rocks such as limestones, slates, and some shales, with the Cement Extraction, Processing, ManufacturingIn raw grinding, a ball mill with a high efficiency separator is used to achieve uniform particle size in raw mix for the next stages of the manufacturing process At the Cement Grinding Stage, 90 – 95% of the clinker is mixed with gypsum Cement Grinding Unit Process High Quality
.jpg)
Raw Material DryingGrinding Cement Plant Optimization
Dry Grinding: Open circuit Ball mill, closed circuit Ball mill, vertical roller mill, Roll Press or Roll press in circuit with ball mill However, it would be seen that the most significant process and types used for raw material grinding operations in modern cement industry are: Process: Dry Closed circuit drygrinding Type of mill: Ball and 2014年6月10日 Evolution of the cement Process • Wet process easiest to control chemistry better for moist raw materials • Wet process high fuel requirements fuel needed to evaporate 30+% slurry water • Dry process kilns less fuel requirements • Preheater/Precalciner further enhance fuel efficiency allow for high production ratesCement manufacturing process PPT Free Download SlideShareDownload scientific diagram The cement raw material blending process and its control system from publication: Modeling and Optimization of Cement Raw Materials Blending Process This paper The cement raw material blending process and its control system4 天之前 The manufacture of Portland cement is a complex process and done in the following steps: grinding the raw materials, mixing them in certain proportions depending upon their purity and composition, and burning them to sintering in a kiln at a temperature of about 1350 to 1500 ⁰C During this process, these materials partially fuse to form nodular shaped clinker by Manufacturing of Portland Cement – Process and Materials
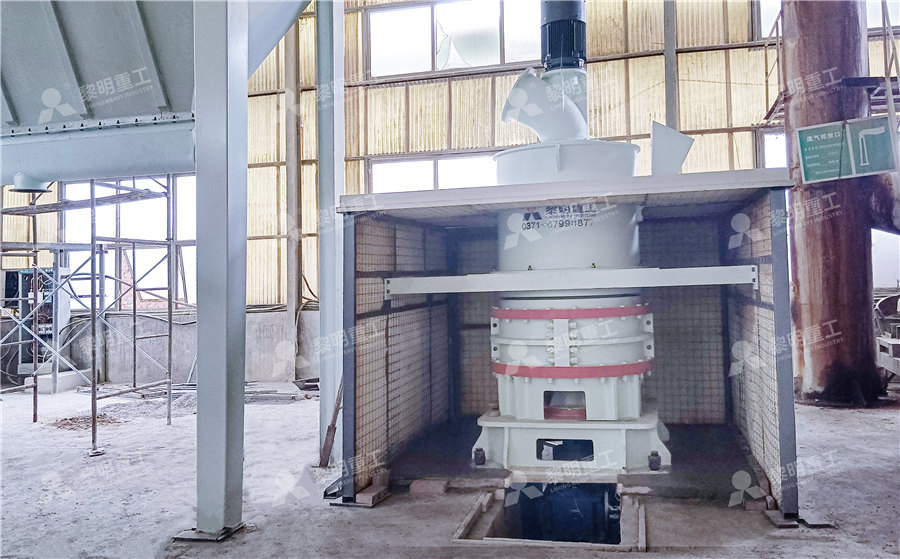
A Comprehensive Guide to the Cement Manufacturing Process
2024年9月5日 2 Raw material grinding After crushing, the raw materials are carried to a grinding mill and made into a fine powder This is done using equipment such as ball mills or vertical roller mills The grinding process ensures the correct particle size of raw material and its homogeneous constitution, which is so critical for product quality 3 2020年8月25日 Cement raw material preparation: Limestone is main raw materials for cement manufacturing, and most cement plants are located next to the quarry to reduce the transportation cost; Using explosion or getter loader to mine raw materials; sending raw materials to the cement crusher to crush or hammer; crushed raw materials are stored to prevent from environment Cement Production Process Cement Manufacturing Process AGICO CEMENTRaw Grinding: Initially, a ball mill with a highefficiency separator is utilized to ensure uniform particle size in the raw mix, essential for the subsequent stages of the manufacturing process Clinker Grinding: The main process in cement grinding units involves grinding the clinker into a fine powder using a cement ball mill or vertical StepbyStep Guide to the Manufacturing of Cement PRACTICAL 2024年9月10日 Steps of Cement Manufacturing The steps involved in cement manufacturing are as follows: Quarrying: Raw materials such as limestone and clay are extracted from quarries or mines; Crushing and Grinding: The extracted raw materials are crushed and ground into a fine powder; Blending: The crushed and ground raw materials are blended in specific proportions Cement Manufacturing Process: Know Extraction, Processing

The Cement Manufacturing Process Thermo Fisher
2023年12月20日 Cement manufacturing is a complex process that begins with mining and then grinding raw materials that include limestone and clay, to a fine powder, called raw meal, which is then heated to a sintering temperature as with the extraction of raw materials and ending with the finished product From raw materials to cement Extracting raw materials Crushing and transportation Raw material preparation I: Storage and homogenisation Raw material preparation II: Drying and raw grinding Burning The burning of the raw meal at approx 1,450°C is carried outFrom raw materials to cementThe whole process of cement manufacturing in Messebo Cement plant which consists of two separate Cement Production lines can be summarized into the following processes ;as can be seen in the process and Quality flow diagram below; 1 3 Proportioning 4 Raw material Grinding and Transportation 5 Raw meal storage, homogenization and CEMENT PRODUCTION AND QUALITY CONTROL A Cement manufacturing Processvertical roller grinding mills for grinding: • Coal • Cement raw material • Clinker / granulated slag • Industrial minerals, and • Ores The core elements of these plants are the Loesche vertical mills for drygrinding the abovementioned grinding stock Loesche has PROCESS OPTIMISATION FOR LOESCHE GRINDING PLANTS
.jpg)
Flow chart of the grinding and blending process
Download scientific diagram Flow chart of the grinding and blending process from publication: Effective Optimization of the Control System for the Cement Raw Meal Mixing Process: I PID Tuning The block diagram of the production process of cement is given The production of clinker in a kiln is a key process in the production of cement The raw materials used in this process are also responsible for up to 60% of the total of emissions of the cement production process [PCA] In addition, grinding and Cement Production Demystified: StepbyStep Process and AGICO Cement is a cement grinding plant manufacturer, we'd like to helps you learn more about cement grinding plant and cement grinding machines Skip to content +86 Cement Grinding Plant Overview Cement Grinding Unit AGICO Cementcommon solution to grind raw materials and cement Roller presses are used mainly in combination with a ball mill for cement grinding applications and as finished product grinding units, as well as raw ingredient grinding equipment in mineral applications This paper will focus on the ball mill grinding process, its tools and optimisationBALL MILLS Ball mill optimisation Holzinger Consulting
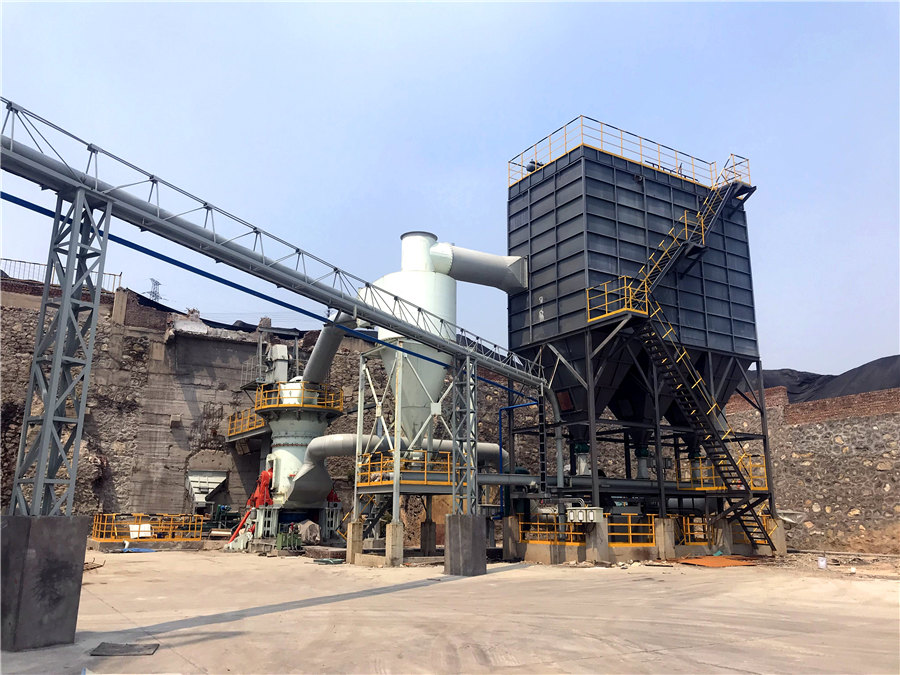
Wet Process Of Cement Manufacturing With Flow Chart
As the perflow diagram of the wet process of cement manufacturing, The manufacturing process of cement consists of, Raw materials grinding Mixing this material in certain proportions depending upon their purity and, Preparing Composition2023年7月10日 The cement manufacturing process involves the extraction and processing of raw materials, such as limestone, clay, and shale, which are then heated in a kiln at high temperatures to form clinkerCement Manufacturing Process and Its Environmental Impact2021年4月29日 Cement is first used in the tunnel construction in the Thames River in 1828 Manufacturing Process of Cement There are four stages in this whole process • Mixing of raw material • Burning • Grinding • Storage and Cement Manufacturing Process2016年1月20日 In the surveyed cement plant, three balances are established between input and output material in the raw mill, clinker production, and cement grinding system 248 t, 469 t, and 341 t of materials are required to produce a ton of the product in raw material preparation, clinker production, and cement grinding stages; waste gases account for the largest proportion of the Analysis of material flow and consumption in cement production process
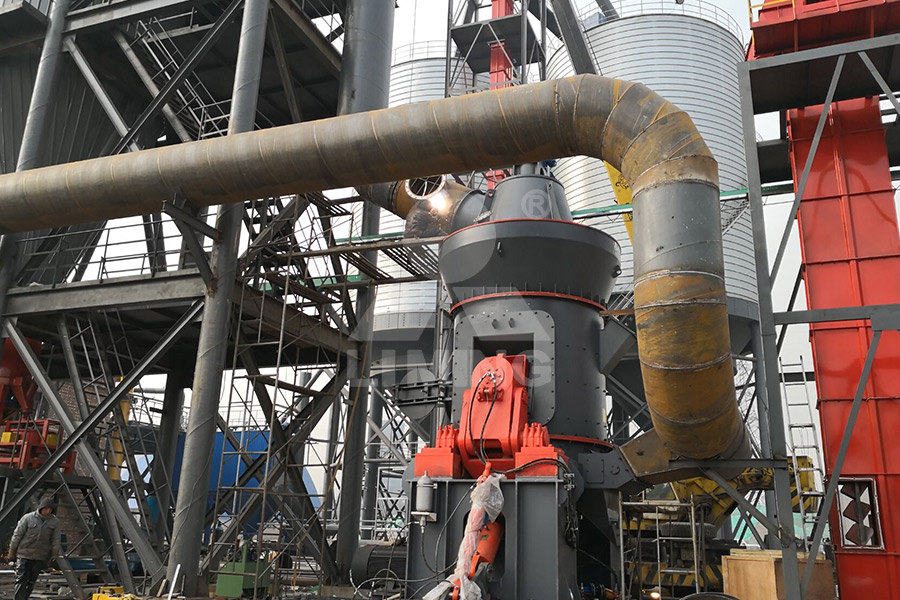
What is the Manufacturing Process of Portland Cement?
From raw material selection to the final grinding and packaging stages, each step plays a pivotal role in determining the performance and durability of the cement One of the prevalent challenges in the manufacturing process is maintaining Download scientific diagram Sankey diagram of cement grinding system from publication: Analysis of material flow and consumption in cement production process Cement production, which is Sankey diagram of cement grinding system ResearchGateThe vertical roller mill (VRM) is a type of grinding machine for raw material processing and cement grinding in the cement manufacturing processIn recent years, the VRM cement mill has been equipped in more and more cement plants around the world because of its features like high energy efficiency, low pollutant generation, small floor area, etc The VRM cement mill has a Vertical Roller Mill Operation in Cement PlantDownload scientific diagram Process flow diagram for the cement manufacturing process, showing electricity and heat consumption or inputs [39] from publication: Energy Savings Associated with Process flow diagram for the cement manufacturing process,
.jpg)
IELTS Writing Task 1: process diagram answer IELTS Simon
2018年10月25日 Here's my full answer for the process diagram task below The diagrams below show the stages and equipment used in the cementmaking process, and how cement is used to produce concrete for building purposes (This task comes from Cambridge IELTS book 8) The first diagram illustrates the process of cement manufacture, and the second diagram shows the 2023年2月1日 Raw material blending is an important process affecting cement quality The aim of this process is to mix a variety of materials such as limestone, shale (clay), sandstone and iron to produce CEMENT RAW MATERIALS BLENDING PROCESS BY USING 2021年3月3日 Cement is produced by a hightemperature (about 1500 °C) reaction in a rotary kiln of carefully proportioned and blended ratios of lime (CaO), silica (SiO 2), alumina (Al 2 O 3), and iron oxide (Fe 2 O 3)The production of cement is a chemical process requiring an accurate blend of the previously cited four key organic oxides and the limitation of several undesirable Cement SpringerLink2016年10月5日 Multicompartment ball mills and air separators have been the main process equipments in clinker grinding circuits in the last 100 years They are used in grinding of cement raw materials (raw meal) (ie limestone, clay, iron ore), cement clinker and cement additive materials (ie limestone, slag, pozzolan) and coalEnergyEfficient Technologies in Cement Grinding IntechOpen
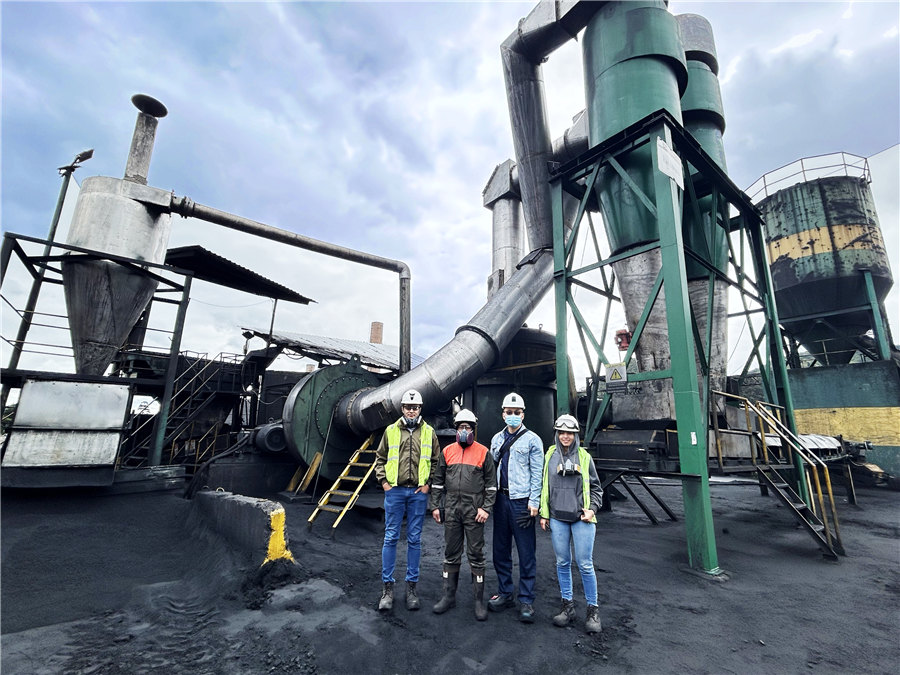
Know All About Cement Manufacturing Process in India mycem cement
Proportioning of raw materials Grinding Storing and Blending Burning of raw mix Clinker grinding along with gypsum – Cement Grinding Storing Discover the detailed steps of the cement manufacturing process in India Heidelberg Cement offers insights into modern techniques and industryleading practices mycem Cement Who Are We 2020年9月26日 Grinding; Storage; Mixing: The mixing of raw materials can be done either with dry process or wet process In dry process the calcareous and argillaceous materials are grinded to the required size and then they are Cement Manufacturing Process Chemical 2023年10月19日 Clinker grinders are an important part of the cement manufacturing process They are used to grind clinker into a fine powder and are typically located at the end of the cooler in a cement plant Clinker is a nodular Clinker Grinding Techniques in Cement The succeeding cyclones and separators perform the particle separation The oversize particles are returned to the mill or are ground in a separate ball mill to the required size This subsequent grinding of cement raw materials is sometimes indispensable Comminution of cement raw materials cannot be completely performed by autogenous grindingDrying of raw materials INFINITY FOR CEMENT EQUIPMENT
.jpg)
Rawmill Wikipedia
A mediumsized dry process roller mill A raw mill is the equipment used to grind raw materials into "rawmix" during the manufacture of cement Rawmix is then fed to a cement kiln, which transforms it into clinker, which is then ground to make cement in the cement millThe raw milling stage of the process effectively defines the chemistry (and therefore physical properties) of the Brundick, H, “Drying and grinding of extremely moist cement raw materials in the Loesche mill,” ZKG International, No2, 1998, pages 6471Brundick, Horst, and Schäfer, HeinzUllrich, “Loesche mills for clinker grinding,” Asian Cement and Construction Everything you need to know about cement Materials Preparation and Raw 2015年8月1日 The results show that approximately 248t, 469t, and 341t of materials are required to produce a ton of the product in raw material preparation, clinker production, and cement grinding stages Analysis of material flow and consumption in cement production processThe two diagrams illustrate the process, equipment, and materials used in cement production, and how cement is used in the production of concrete as raw material for building purposes The initial step of this process shows the use of limestone and clay as raw materials which are then crushed into fine powderIELTS Diagram: Model Answer Band Score 9 with Tips
.jpg)
The Cement Manufacturing Process
2017年8月15日 The materials reach temperatures of 2500°F to well above 3000°F in the kiln Rotary kilns are divided into two groups, dryprocess and wetprocess, depending on how the raw materials are prepared In wetprocess kilns, raw materials are fed into the kiln as a slurry with a moisture content of 30 to 40 percent2020年10月5日 12 Working In case of continuously operated ball mill, the material to be ground is fed from the left through a 60° cone and the product is discharged through a 30° cone to the right As the shell rotates, the balls are lifted up on the rising side of the shell and then they cascade down (or drop down on to the feed), from near the top of the shellCement industry : grinding process of ball mill PPT SlideShare