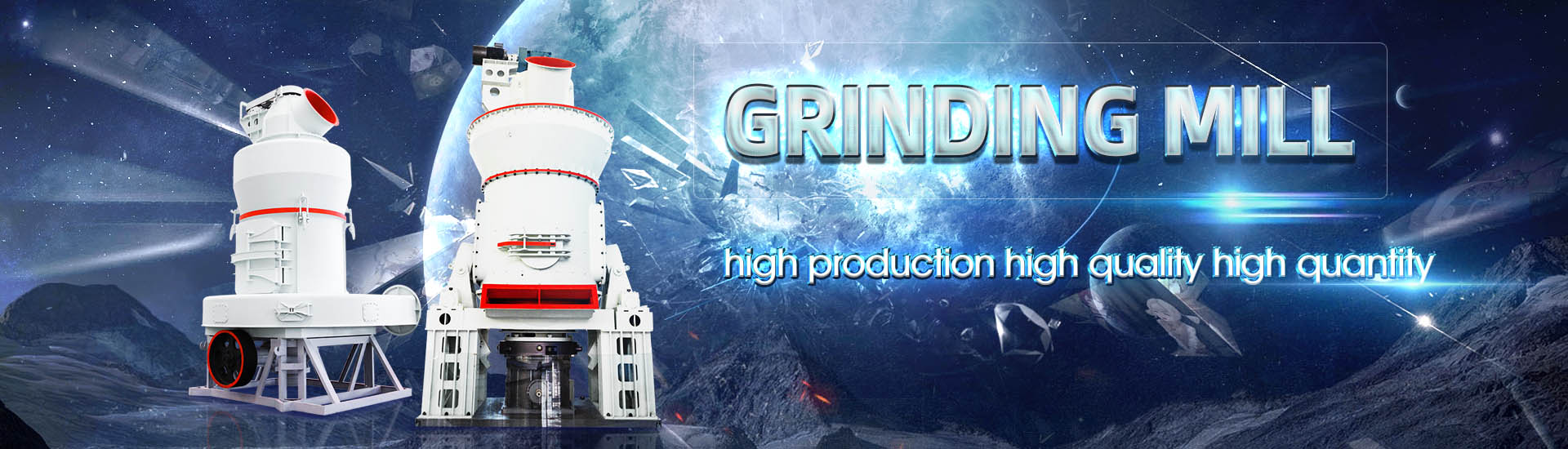
Coal mill fineness
.jpg)
Coal mill pulverizer in thermal power plants PPT
2012年11月17日 The document discusses coal mill/pulverizers used in thermal power plants It describes how pulverized coal is dried, ground, circulated, and classified within the mill to produce a fine powder that is then transported to The coal properties such as volatile components, ash content, hardness, humidity and grinding fineness are the decisive factor for selecting the required mill Basically, coal pulverisers can Coal Mill an overview ScienceDirect Topicscoal and the classification of coal in terms of its fineness1 The comminution or size reduction of coal depends upon its bond nd shape of the coal particle are related to the material’s A Study on 500 MW Coal Fired Boiler Unit’s Bowl Mill Performance 2021年6月1日 Pulverized coal fineness (PCF) is a key parameter in coalfired power plants, demanding accurate and online monitoring This study presents online measurement of PCF Online measurement of pulverized coal fineness on a 300 MWe
.jpg)
Optimisation of coal fineness in pulverisedfuel boilers
2017年11月15日 A method for choosing the optimum fineness of coal in pulverisedfuel boilers is presented This method is based on economic criteria and takes into account variations of ABSTRACT: The paper describes the beneficial application of online coal flow measurement and control and online coal fineness measurement for optimization of the combustion process CPRI Online Coal Flow Balancing and Fineness AdjustmentVarious methods for choosing the fineness of power plant coal dust are reviewed and analytical expressions for determining the fineness are presented It is shown that the use of the yield of Choice of Fineness of Pulverized Coal Springer2013年6月4日 Collura et al [13] utilized model identification and signal processing techniques to develop a coal mill performance monitoring tool based on realtime detection of the fineness ofCoal mill performances optimization through noninvasive online
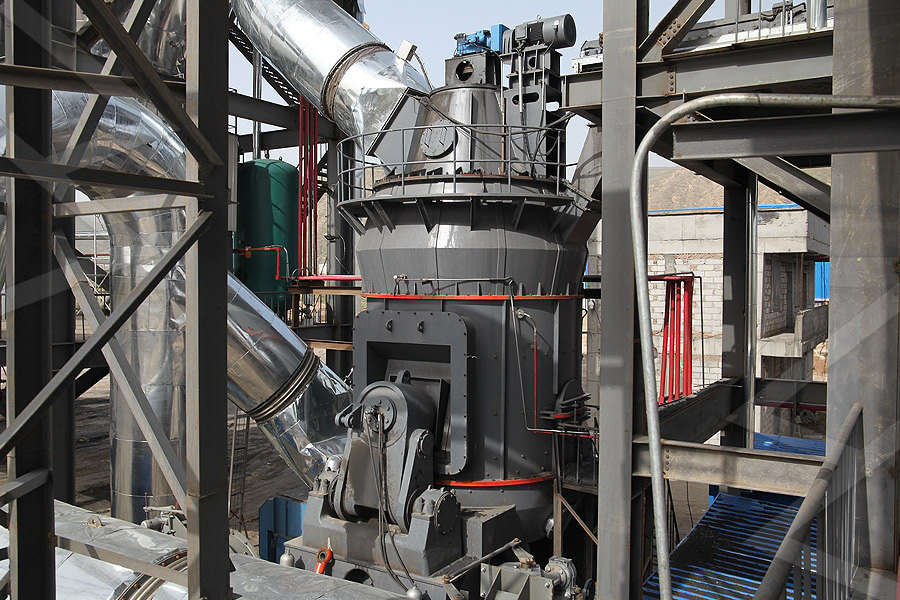
CFD Modeling of MPS Coal Mill for Improved
2009年1月1日 Mill performance has a significant impact on combustion performance indicators such as NO x , CO, unburnt carbon, slagging, fouling, flame stability and boiler capacity The MPStype pulverizerUp to 20% improved coal fineness GE’s PVPRO mill upgrade system uses a patented process for better control of coal fineness and reduced pulverizer wear for extended operations Up to 6x life extension HCX2* ceramic inserted Boiler Mill and Coal Pulverizer Performance GE Steam 2017年8月1日 In order to optimize coal fineness in coal mill, series of tests were conducted on 650 [th 1 ] pulverized fuel boiler [8]Optimisation of coal fineness in pulverisedfuel boilersFine coal leaves the mill with the gas stream, the coal fineness is adjusted by altering the angle of the separator vanes, or the rotor speed Coal drying is ensured by controlling the coal mill inlet temperature, to give a target mill exit temperature, usually between 70 and 900CCOAL PREPARATION AND FIRING INFINITY FOR CEMENT EQUIPMENT
.jpg)
Pulverizer Fineness
Mill Inerting and Pulverizer/Mill Explosion Mitigation Richard P Stormrichardstorm@innovativecombustion (205) 4530236 2013 Annual Meeting Coal Mills are the Heart of a Coal Fired Plant Maximum capacity, reliability and performance of your operation rely on the critical roles that your coal mills coal mill kwh/t 92 Table 2 with graph represents the Pulveriser mill performance parameters [4] Item Unit BMCR 90% BMCR 60% BMCR 30% BMCR 1 Coal Fineness(% through 200mesh) % 20 20 20 20 2 Mill Operating Nos 5 4 3 2 3 Total Mill outlet air flow (including seal air) t/h 7104 6843 4443 2262 4 Mill outlet temp °C 65 65 65 65Pulveriser Mill Performance Analysis Optimisation in SuperEffect of fineness Maximum Mill capacity vs PF fineness at 12 % Raw coal moisture and at Coal HGI 100110 3300 3400 3500 3600 3700 3800 3900 4000 4100 65 70 75 80 85 Mill output at raw coal moisture and at Coal HGI 100110 31Pulverizer Plant OM Aspects2011年8月1日 Pulverizers prepare raw fuel by grinding it to a desired fineness and mixing it with the just the right amount of air before sending the mixture to boiler burners for combustion In Part I of Pulverizers 101: Part I POWER Magazine
.jpg)
Pulverizer Fineness and Capacity Enhancements at Danskammer
RPM is programmed to follow mill coal flow to obtain a desired fineness vs mill load rela tionship; manual override with manual control of classifier speed from the control room is also provided; instrumentation for monitoring drive assembly oil bath temperature and oil2010年10月7日 The next step in this plant is to upgrade the mill to improve coal fineness to 75% passing a 200mesh sieve Proper Coal Velocity Is EssentialPulverized Coal Pipe Testing and Balancing POWER MagazineWhile all these are regarding the mill performance, the coal fineness and mill out let temperature also affect the boiler performance The coal fineness has an effect on the combustion performance like the bottom ash percentage combustibles when the plus 50 mesh percentage goes up It has been very well established that in the case of tangential firing system, the Boiler Performance and Mill Outlet Temperature Bright Hub 3 Precise Control and Automation: Bellian Machinery's coal mills feature advanced control systems that enable precise control over various operational parameters Operators can adjust grinding variables, such as coal flow and mill rotation speed, in realtime to achieve the desired coal fineness and optimize mill performanceCoal Mill in Thermal Power Plant: Enhancing Efficiency and
.jpg)
Effects of Mill Performance on Unburnt Carbon in Coalfired Boilers
Coal particulate fineness for (a) mill 20 and (b) mill 40: Finer sized particles are normally preferred as the smaller surface area allows the volatiles (from coal particulates) to be consumed faster, resulting in a higher devolatilization and heat release rate [6]2021年3月31日 24 mill performance monitoring using non iso kinetic technique • dirty pitot testing to be carried out before and after mill overhaul • non iso kinetic sampling to be used for routine checking of fineness • pf fineness data to be Effect of Coal Quality and Performance of Coal Illustration of the “grinding zone” on a MPS mill Horsepower/Ton Consumption Below is a typical HP/ton consumption chart based on our experience However, keep in mind that power consumption varies with mill types but are also largely influenced by coal feed rate, HGI variations, spring pressures, coal fineness,Pulverizer Capacity is not simply “tons throughput per hour!”2021年3月12日 Depending on the material to be ground, throughput rates of 5200 t/h can be achieved in a fineness range between 1% R0063 mm and 25% R0090 mm Thus, the MPS coal grinding mill device for fresh material is arranged in this area where the fresh feed is also mixed with the grits rejected from the classifier (Figure 1)MPS mills for coal grinding AYS Engineering
%3C1PGHL[2}HK_]YT.jpg)
Choice of Fineness of Pulverized Coal Springer
Keywords: fineness of coal dust, milling, yield of volatiles, porosity, heat of combustion of volatiles, fuel For ballmill pulverizers of type ShBM the parameter n, which characterizes the uniformity of the granulometric composition of the dust, ranges within 07 – 13 for hammerThe Raymond Bowl Mill is considered the finest vertical roller mill available for pulverizing coal The typical Raymond bowl mill system is designed to simultaneously dry, pulverize, and classify solid fuels to Easily adjustable fineness – externally adjustable classifier permits selection of fineness from 70% to 95% through 200 mesh Raymond Bowl Mill designed and built for flexibility Qlar2015年12月1日 Acceptable standards for best lowNO x burner performance are coal fineness of 75% passing a 200mesh sieve and less than 01% remaining on a 50mesh sieve Fuel balance should be within the range Coal Pulverizer Maintenance Improves Boiler CombustionThe MPS mill also grinds, dries, calcines, and classifies gypsum without any problem, all in a single machine, for any fineness requested and considering individual requirements The MPS vertical roller mill built to last, MPS 200 BK coal mill, Krimzement Bakhchisarayski, Ukraine MPS 3070 BK coal mill, Jaypee Cement Balaji, IndiaCoal mill, gypsum mill, clay mill, etc Pfeiffer MPS mills
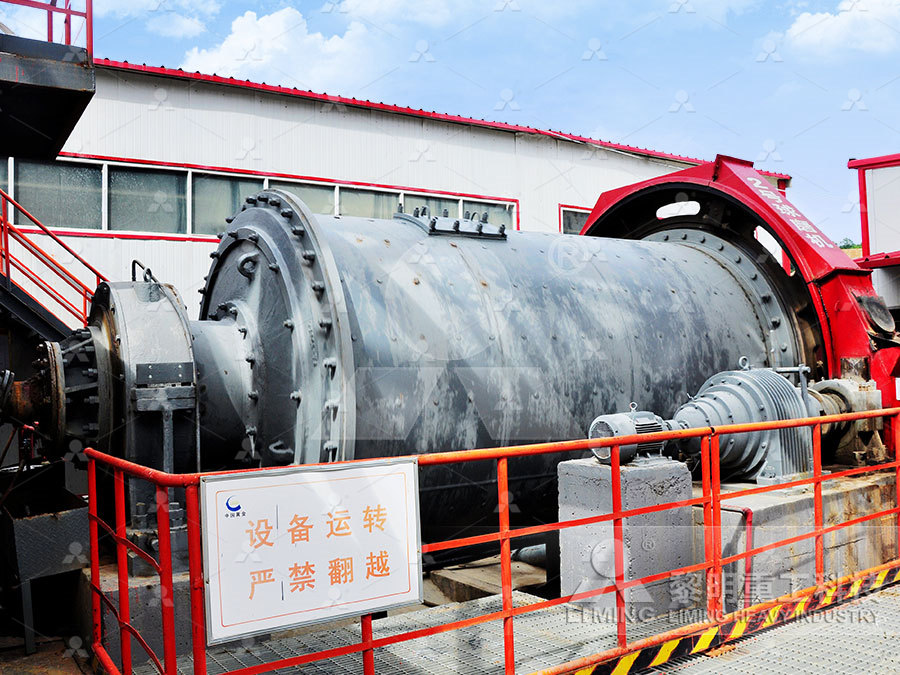
ATOX® Coal Mill FLSmidth Cement
Our ATOX® Coal Mill has large rollers with great grinding capability of virtually all types of raw coal The rollers work harmoniously with a highlyefficient separator and feed sluice to consistently and reliably deliver coal meal to your desired fineness and moisture levelIntroduction This article concerns itself with vertical grinding mills used for coal pulverization only (coal pulverizers), although vertical grinding mills can and are used for other purposes The 3D model in the saVRee database represents a Vertical Grinding Mill (Coal Pulverizer) Explained2019年12月9日 By consent among interested parties, it may be used for evaluation of coal fineness in preparation, pneumatic transfer systems, etc Scope 11 This test method covers the determination of the fineness by sieve analysis of coal sampled from a dry pulverizing operationStandard Test Method for Sampling and Fineness Test of Pulverized CoalThe ATOX coal mill is suited for various installation types, whether inert or noninert, and direct or indirect firing systems An inert system designed for indirect firing is the most common solution for cement plants Equipped with the highefficiency RAKM dynamic separator, the ATOX coal mill will grind any type of coal to the required finenessATOX COAL MILL
.jpg)
Coal Mill in Cement Plant
The pulverized coal with acceptable fineness is discharged from the mill with air, and the unqualified pulverized coal is returned to the mill for further grinding Advantages Compared with ball mill, the advantages of vertical mill include simple operation, high grinding efficiency, low noise, small floor area, strong drying capacity, and low energy consumption2015年8月1日 Mill problems originate mainly due to poor controls or faults occurring within the milling system As discussed by GQ Fan and NW Rees [3], the control of mills remains very simple in most of the power plants due to the fact that the mill system is highly nonlinear with strong coupling among the variables and it is very difficult to measure some important Review of control and fault diagnosis methods applied to coal 2021年6月1日 Pulverized coal fineness (PCF) Coal powder from the mill D and B of #4 unit are measured Default areaweight fineness results, using the equivalent circle diameter to estimate the sieve size, is with absolute R 90 errors of Online measurement of pulverized coal fineness on a 300 Mill Fineness Ash Analysis Report(4 x 600 MW) November 2016 Free download as Excel Spreadsheet (xls / xlsx), PDF File (pdf), Text File (txt) or read online for free This document contains data from the analysis of fly ash and bottom ash samples from four power generation units, as well as coal mill fineness data from eight mills across four unitsMill Fineness Ash Analysis Report (4 X 600 MW) November
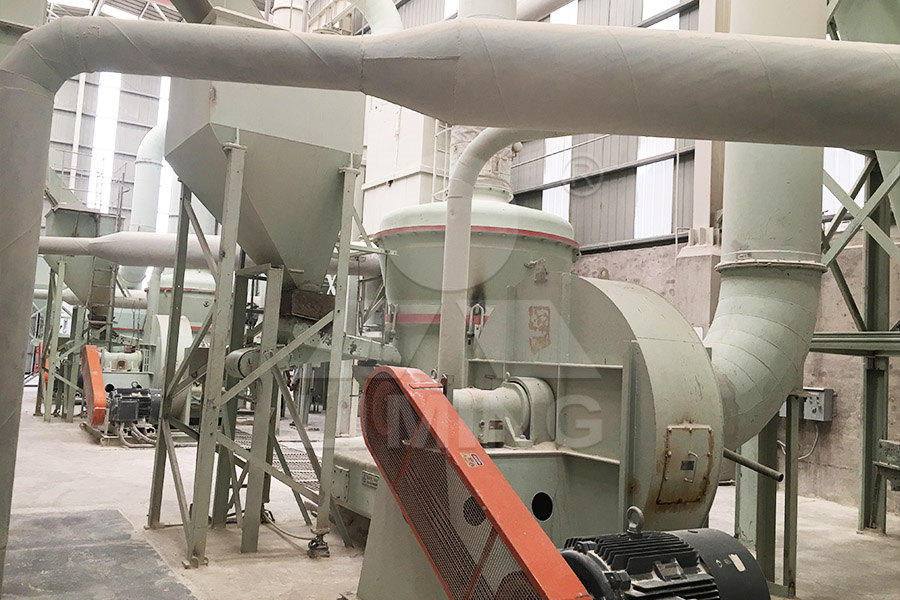
Raymond® Bowl Mill Coperion
The Raymond® Bowl Mill is considered the finest vertical rollermill available for pulverizing coal Each bowl mill system is designed to achieve thebest solution forthe Easily adjustable fineness–externally adjustable classifier permits selection of fineness from 70% to 95% through 200 mesh without stopping the system High turndown Request PDF On Jun 4, 2013, Stefano Collura and others published Coal mill performances optimization through noninvasive online coal fineness monitoring Find, read and cite all the research Coal mill performances optimization through noninvasive online coal 2017年11月15日 The work is based on tests of pulverisers of a 650 t/h pulverized fuel boiler (OP 650) in a Polish power plant On the basis of these studies, relationships were derived between the fineness of the produced pulverized fuel and operating parameters, the efficiency of the boiler and parameters of the milling system, eg, energy consumption of the mill and its fanOptimisation of coal fineness in pulverisedfuel boilersThis paper was brief, but hopefully has shown the importance of one aspect, mill performance, on many coal quality related issues At first glance one might not consider the influence mill fineness has on mill capacity, slagging and opacity; this paper has shown that it does indeed, and mill performance is only one of many areas of considerationCoping With Coal Quality Impacts on Power Plant Coal
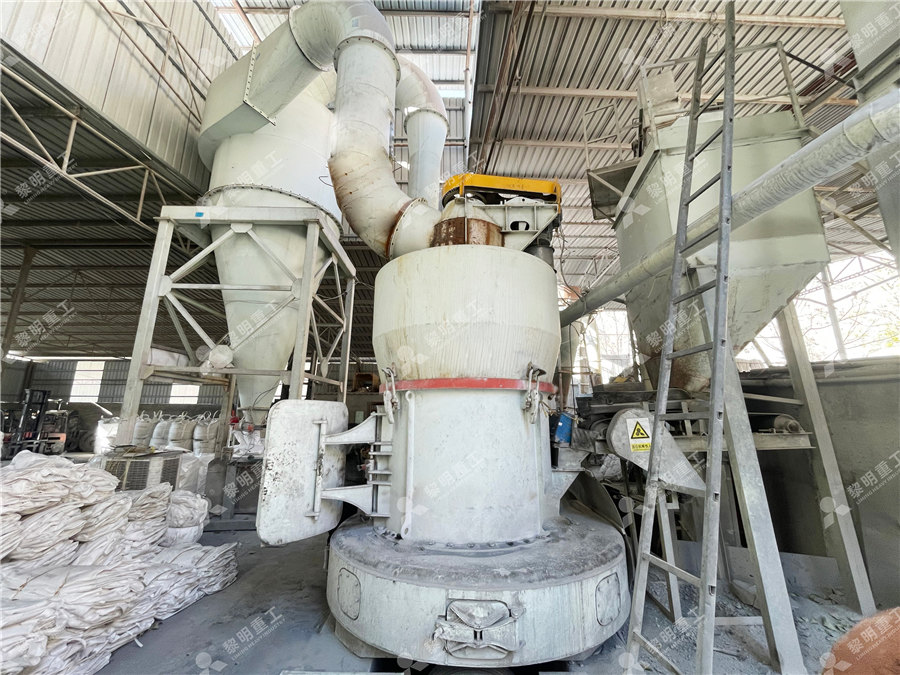
A Comparison of Three Types of Coal Pulverizers Babcock Power
The BTM is a lowspeed mill that primarily grinds coal by impact and attrition The VRM is a medium speed mill that grinds coal by compression and, because of the low coal inventory in the mill and flat grinding surfaces, develops shearing action as well For both mills a constant centrifugal force is maintained The speedThe mill outputs, pulverised coal fineness and distribution tests were carried out and evaluated from the data measured during plants tests A mathematical spreadsheet was used to observe mill performance when operating parameters are varied A mill’s heat balance evaluation was done using an Excel spreadsheetPerformance optimisation of vertical spindle coal pulverisers2014年1月1日 Two mill systems are employed for most coal grinding applications in the cement industry These are, on the one hand, vertical roller mills (VRM) that have achieved a share of almost 90% and, on (PDF) MPS mills for coal grinding ResearchGateOnce normal coal flow is applied to the mill, a full mill test should be conducted This should include isokinetic coal sampling and dirty airflow measurements through each fuel line to determine air fuel balance and coal fineness Primary airflow “HotK” calibrations of the primary airflow measuring element should also be conductedThe Storm Approach to Coal Pulverizer Optimization
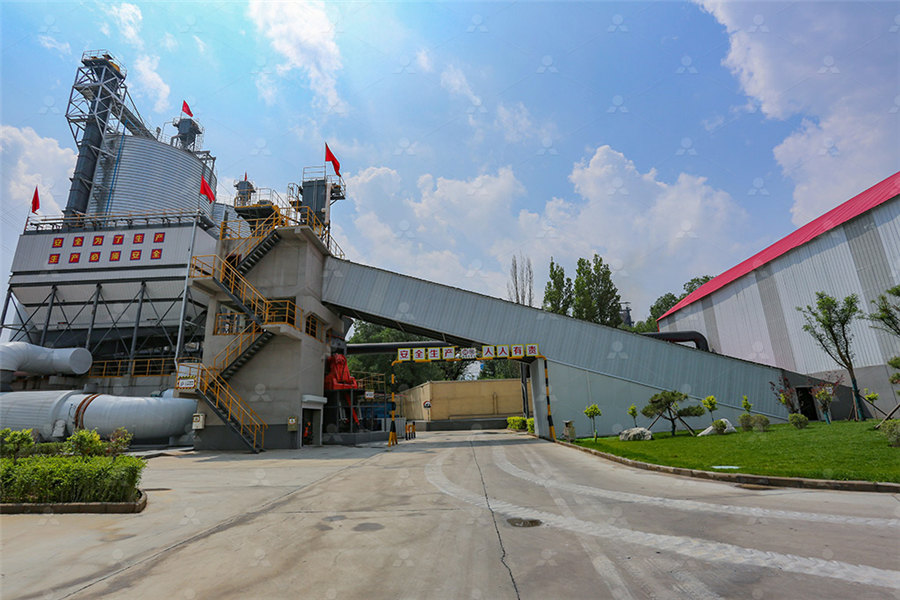
Dynamic classifiers: a fine way to help achieve lower emissions
2004年4月8日 There have been very few conversions of UK coal mills from static to dynamic classifiers But test experience with a dynamic classifier at Powergen's RatcliffeonSoar power station has demonstrated significant fineness gain, especially at the coarse end of the particle size distribution curve, and minimal effect on mill coal throughput and operability, with greatly Coal Fineness: It is understood generally that the finer we grind, the easy it is for burning Coal Mill Safety parameters: Position of Explosion vents Operational readiness of quick shutoff dampers Inertization section readiness (N2, CO2 pressure in bars) Mill Inlet Temperature (0 C)Coal Grinding Cement Plant OptimizationAn overwhelming majority of coal fired boilers utilize a pulverized coal firing system These systems utilize a pulverizer or mill to grind coal to a desired fineness and subsequently transport the coal to the burners using air as a transport medium Air utilized to transport coal to the burners is considered “Primary Air”Innovative Combustion Technologies, Inc