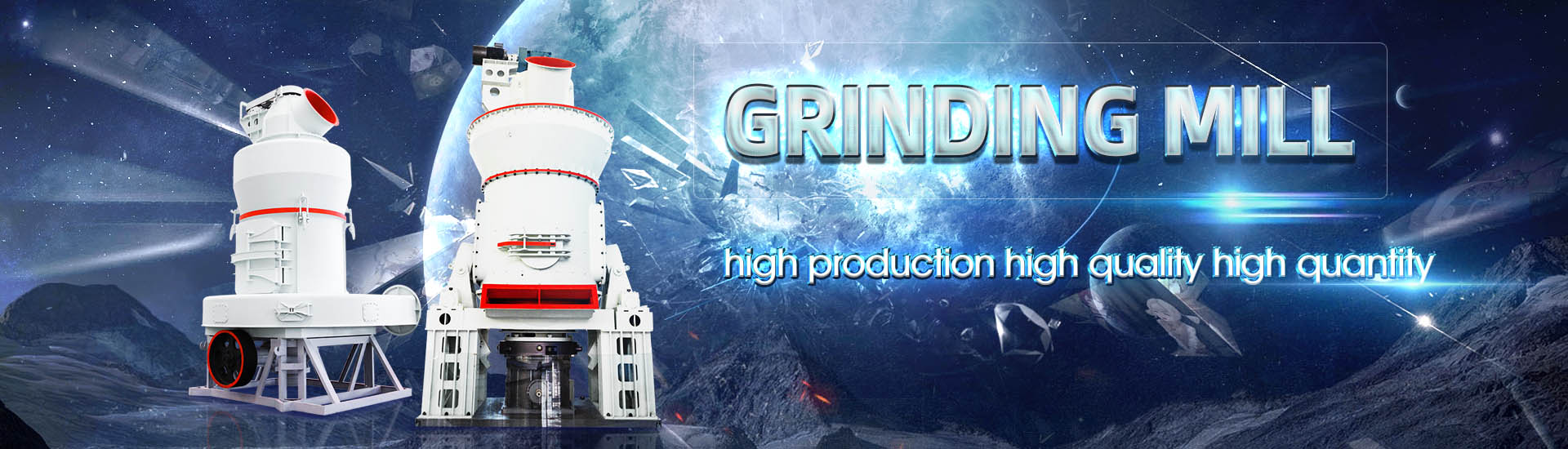
Management of cement grinding
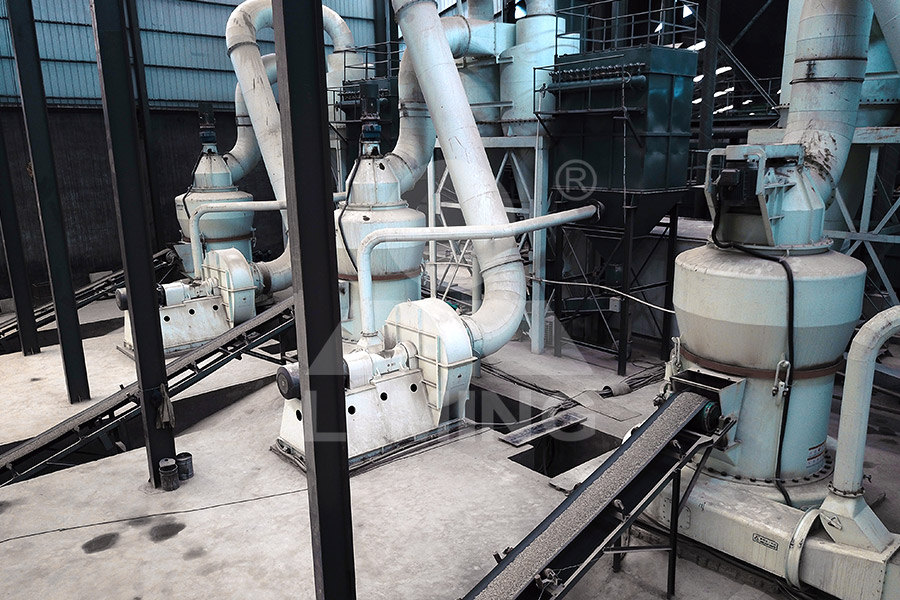
OPTIMIZATION OF CEMENT GRINDING OPERATION IN BALL MILLS
An evaluation of the grinding system and operation includes meaningful and critical inspection of all equipment, components and the process parameters by experts PEC Consulting can help carry out detailed evaluation of existing grinding systems and their2020年10月21日 简单来讲,水泥粉磨系统生产工艺技术的管理研究与讨论对于工艺技术问题解决和生产进步有突出的现实价值,所以论文针对相关内容进行分析,旨在为实践提供帮助与指导 (PDF) 水泥粉磨系统生产工艺技术的管理 ResearchGateHighly energy intensive unit operation of size reduction in cement industry is intended to provide a homogeneous and super fine (30004000 Blain) cement Grinding operation is monitored for Cement Grinding Cement Plant Optimization2004年11月1日 To optimise cement grinding, standard Bond grinding calculations can be used as well as modelling and simulation techniques based on population balance model (PBM) Cement grinding optimisation ScienceDirect
.jpg)
BALL MILLS Ball mill optimisation Holzinger Consulting
common solution to grind raw materials and cement Roller presses are used mainly in combination with a ball mill for cement grinding applications and as finished product grinding raw materials, burning, grinding and quality control are supported by a range of chapters addressing critial topics such as maintenance and plant reporting, alongside a detailed The Cement Plant Operations Handbook International Cement 针对水泥粉磨系统智能化实现路径,提出了由人智操作模式向机智操作模式转变的思路,通过实现从设计到运维全生命周期数字化管理,智能调控粉磨生产运行过程,建立基于神经网络多变量 水泥粉磨系统智能化发展现状及优化途径2023年9月26日 The developed model is validated by applying to a multiunit repairable, imperfectly maintained raw meal grinding system of a cement plantMaintenance Performance Optimization for Critical Subsystems in
.jpg)
EnergyEfficient Technologies in Cement Grinding
2016年10月5日 In this chapter an introduction of widely applied energyefficient grinding technologies in cement grinding and description of the operating principles of the related 2018年7月1日 This study aimed at improving both the energy efficiency and product quality of the end product for a given cement grinding circuit by applying an accurate sampling Energy and cement quality optimization of a cement grinding circuit2018年8月28日 Here, steel balls tumble and crush the clinker into a very fine powder This fine powder is considered as cement During grinding gypsum is also added to the mix in small percentage that controls the setting of cement Cement Manufacturing Process The Engineering 2021年4月19日 Grinding of finished cement is performed in a single stage, intergrinding materials with very different grindabilities This intergrinding process has many different interactions among the different components of the finished cement In a context of developing more sustainable and less energy intensive processes, it is important to understand the Resistance to Grinding and Cement Paste Performance of Blends
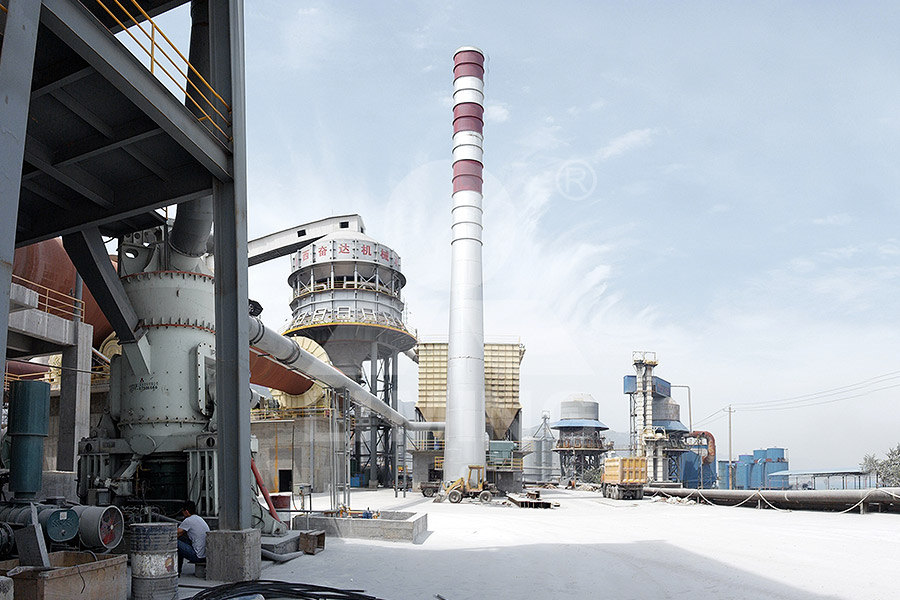
Clinker grinding technology in cement manufacturing
2019年1月3日 Clinker grinding technology is the most energyintensive process in cement manufacturing Traditionally, it was treated as "low on technology" and "high on energy" as grinding circuits use more than 60 per cent of total energy 2024年4月17日 ICR delves into the multifaceted aspects of dust control in cement manufacturing, from environmental and health hazards to regulatory standards and innovative technologies By exploring dust generation sources, control technologies and regulatory frameworks, it highlights the critical importance of effective dust management practices Dust Strategising Dust Management Indian Cement Review2016年10月23日 Exact proportioning is dependent upon their chemical properties before and after calcining to cement clinker For good kiln practice the grind required is 8892% – 200 mesh for standard cement, 99%200 mesh for high early Uniform kiln feed size helps reduce tendency to form kiln rings WET VS DRY Grinding of Cement Wet grinding is generally Cement Grinding 911MetallurgistAt the Cement Grinding Stage, 90 – 95% of the clinker is mixed with gypsum and ground in a Cement Ball Mill to produce quality cement OPC 43 and OPC 53 In case of PPC Cement, there is an addition of Fly AshCement Grinding Unit Process High Quality Cement Grinding
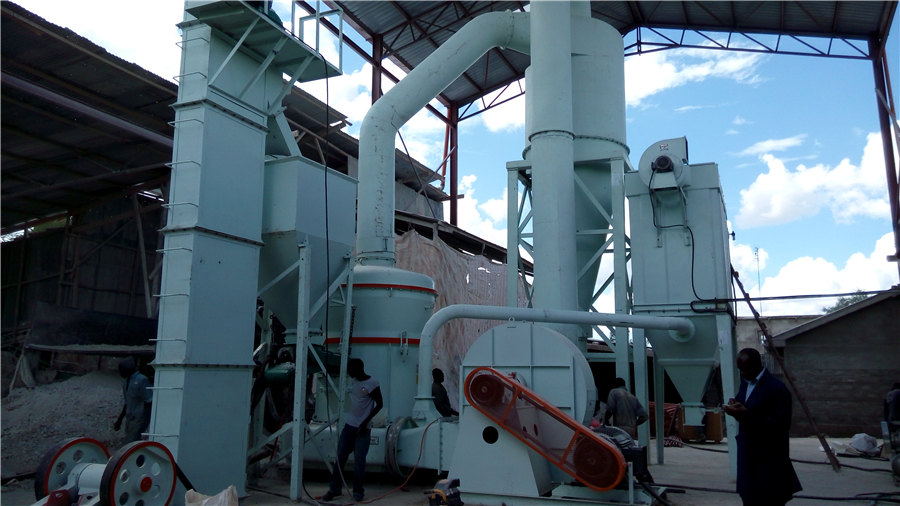
MAINTENANCE IN THE CEMENT INDUSTRY
Maintenance in the cement industry is one of the contributors to the production cost and represent typical 15 – 25 percent of total manufacturing expenditure Many companies have tried to use standard production methods to control maintenance costsRaw material and cement grinding are the first and the last major process steps during cement production The energy demand of these two processes amounts to up to ~70% of the electrical energy used in a cement plant For you as participant, this training will help to obtain a better understanding of the comminution processes as well as the equipment used for grindingGrinding Technology in Cement Production2023年9月26日 case study, in this case, a cement grinding plant The study provides a pragmatic reference model framework to practitioners that enhances maintenance decisionmaking by identifyingMaintenance Performance Optimization for Critical Subsystems in Cement The purpose of the training is to Identify and understands necessary known and unknown information towards the completed cycle of the grinding system, whether is a ball or vertical mill Throughout the course the lectures are supplemented with exercises and case studies, allowing the participants to relate the course material to their cement grinding facility and as a result CEMENT GRINDING COURSE The Cement Institute
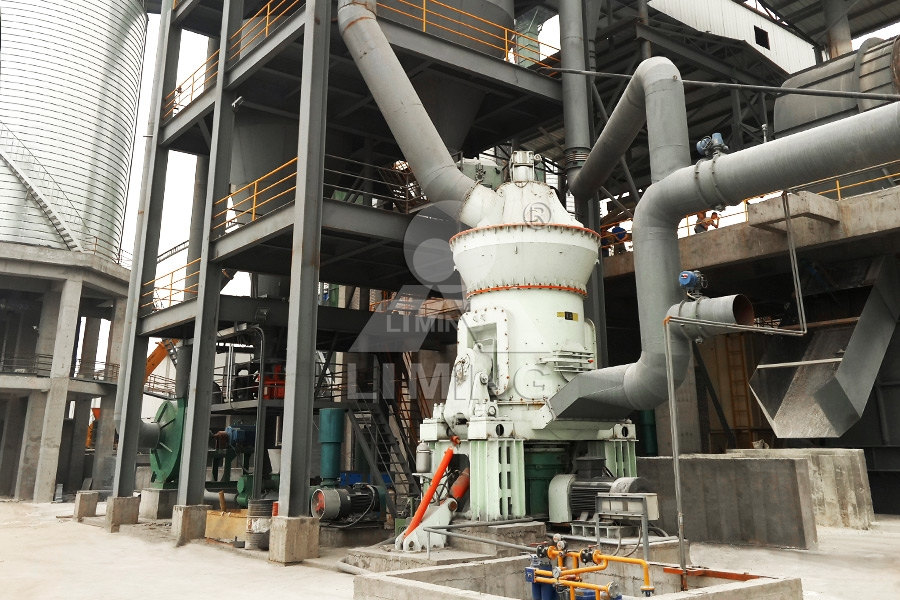
Fives Project management for cement and mineral grinding
Expert solutions, from equipment supply to complete plant delivery Fives is renowned for its extensive experience in industrial plant project management and has installed more than 80 complete cement production lines around the world We bring our original equipment manufacturer (OEM) expertise and our engineering, procurement and construction (EPC) 2019年6月19日 Yonge D, Shanmugam H Assessment and Mitigation of Potential Environmental Impacts of Portland Cement Concrete Highway Grindings No WARD 6281 Diamond Grinding Slurry Handling Best Management Practices, 2013 Google Scholar 11 International Grooving and Grinding AssociationConcrete Grinding Residue: Management Practices and Reuse for 2023年4月13日 Is Concrete Grinding Worth It For Commercial Properties? While grinding can be costeffective, the longterm effects and risk of additional damage to the concrete may outweigh the upfront lower cost and quick Concrete Grinding: Everything You Need to Knowand cement Roller presses are used mainly in combination with a ball mill for cement grinding applications and as finished product grinding units, as well as raw ingredient grinding equipment in mineral applications This paper will focus on the ball mill grinding process, its tools and optimisation possibilities (see Figure 1) The ball millBALL MILLS Ball mill optimisation Holzinger Consulting
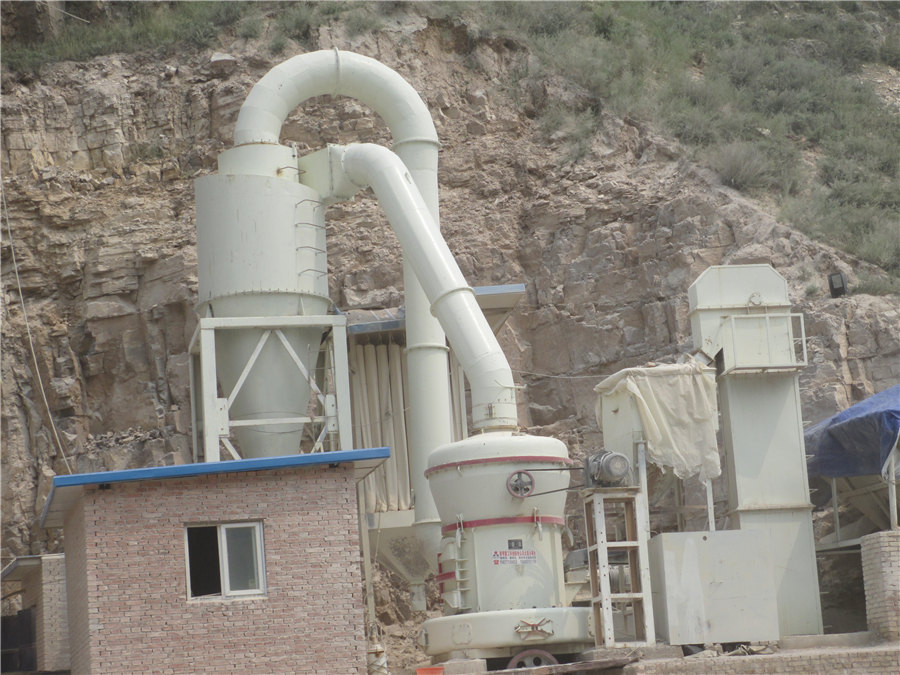
StepbyStep Guide to the Manufacturing of Cement
Temperature Management: The raw mix is fed into the kiln and gradually heated by contact with hot gases from the combustion of kiln fuel Clinker Grinding: The main process in cement grinding units involves grinding the clinker into a fine powder using a 2014年3月1日 Based on a dynamical model of the grinding process in closed circuit mills, efficient efforts have been made to optimize PID controllers of cement milling The process simulation is combined with an autoregressive model of the errors between the actual process values and the computed ones Long term industrial data have been used to determine the Optimizing the control system of cement milling: process consume a considerable amount of water to stabilise the grinding bed against excessive vibrations A key enabler of lowering water spray is the use of an appropriate grinding aid product designed for use in VRMs Using two cement industry case studies, GCP explains how its grinding aid products for VRMs can save water, fuel and CO 2WATER MANAGEMENT Making VRM cement production greenerDalmia Cement is a leading cement Dr Rajan is a PhD from IIT Delhi, in the area of Leadership, a postgraduate in business management from XLRI, Jamshedpur and an Bengal Cement Works (06 MnT) and at Belgaum Cement (09 MnT) Commissioning of a new Grinding Unit Meenakshi Cement Works at Tamil Nadu with 2 MnT Made a tectonic shift in About Us Dalmia Cement
.jpg)
Cement grinding aids
TAVERO® HEA2® is one of the most effective dispersants yet developed for use as a grinding aid/pack set inhibitor for portland cement and other hydraulic cements HEA2 greatly improves the efficiency of the grinding process by reducing the surface energy forces which cause agglomeration of the newly fractured cement particles2020年8月25日 A full cement production process includes the cement crushing process, raw mill process, clinker process, and cement grinding process, cement packing process, and related process Find more! Skip to content +86 s about blog contact EN ES Menu Menu Home;Cement Production Process Cement Manufacturing Process AGICO CEMENT3 2019 Cement Concrete Road made at Solapur grinding unit as per Consent to operate condition 19,983,025 AAQMS maintenance and Calibration, Environment Monitoring report Opacity meter upgradation, DG report, Water tanker for tree plantation etc 1,081,984 21,065,009 4 2020 Cement Concrete Road made at Solapur grinding unitZuari Cement Limited Energy Management 2021 (Solapur Grinding Maintenance Department’s Goals and Success Factors Maintenance management Fulfillment of maintenance activities; Reliability debottlenecking Failure documentation, Root Cause Analyses (RCAs), Maintenance Task Maintenance Management System The Cement
.jpg)
About Shree Cement Shree Cement
First Grinding Unit comes up in Khushkhera, Rajasthan, He is a Director in The Marwar Textile (Agency) Pvt Ltd, Shree Global FZE, Shree Enterprises Management Ltd, Shree International Holding Ltd and Union Cement 2024年2月17日 The Plant’s Management Team (PMT), definition and responsibility – Cement Plant commercial goals, objectives, and target – Production and Maintenance management – Understanding of production and Maintenance KPIs – Understanding economic, environmental and social KPIs – Calculation of production costs and operating profit Calculation of CEMENT KEY PERFORMANCE INDICATORS (KPI’s The Cement 2019年3月8日 251 Process Control and Management in Finish Grinding final cement grinding and mixing operation at the site Others ship some or all of their clinker production to standalone cementIMPROVING THERMAL AND ELECTRIC ENERGY EFFICIENCY AT CEMENT 2,000 cement production plants in operation across the globe in more than 160 countries; this is in addition to 500+ clinker grinding facilities The predicted global growth of consumption of cement is estimated at around 45%, year on year, in relation to the present global cement production capacity which is more than 4 billion tons per annumTHE NEED FOR EFFECTIVE RISK MITIGATION IN CEMENT
.jpg)
Energy and cement quality optimization of a cement grinding circuit
2018年7月1日 Among the industries, the nonmetallic industry was reported as the third largest energy user and accounted for about 12% of the global energy use [1]Within this portion, cement industry had the majority of the utilization with 85–12% [1], [2]US Energy Information Administration (EIA) [7] named cement industry as the most energy intensive among the Two of our grinding units, Arakkonam Cement Works and Ginigera Cement Works, have achieved the feat of operating solely on green energy We aim to enable this for the full year Our grinding unit, Arakkonam Cement Works in Tamil Nadu, achieved carbon emission reduction of 16500+ tons in six months of 100 per cent green energy usageEnergy Management UltraTech Cementwould be a length of 135 m and a diameter of 25 m, with a speed of approximately 20 revolutions per minute Such a mill would normally have a load of approximately 90 tons of grinding media, graduated from 90 mm to 60 mm in the first chamber, 50 mm to 15 mm in the second chamber and 15 mm down in the final chamberAn Introduction to Clinker Grinding and Cement Storage2017年12月19日 Diamond grinding of Portland cement concrete (PCC) pavement surfaces, a maintenance operation carried out to remove irregularities, generates a highpH, highalkalinity slurry (water, concrete Characterisation and management of concrete grinding residuals
.jpg)
Everything you need to know about Cement Kiln Dust
In terms of quarrying, crushing, grinding, etc, dust represents a significant investment that can be directly translated into additional requirements for raw 261, 266, and 270, Standards for the Management of Cement Kiln Dust; Modern dryprocess cement plants with an efficient grinding and pyro processing system, typically consume less than 700 kcal/kgcl of thermal energy and 100 kWh/mt of electrical energy Older plants with inefficient systems, combined PERFORMING A CEMENT PLANT OPERATIONS AUDIT2017年12月19日 The chemical composition of concrete grinding residue makes it a useful product for some soil amendment purposes at appropriate land application rates, and though not hazardous, it is sufficiently elevated that precautions need to be taken around aquatic ecosystems Concrete grinding residue is the waste product resulting from the grinding, Characterisation and management of concrete grinding residuals5 Case Studies: Successful Moisture Management in Cement Plants 51 Case Study: Rotary Dryer Implementation in a Middle Eastern Cement Plant A cement plant in the Middle East faced issues with high moisture content in its raw materials, leading to frequent mill stoppages and reduced outputRaw Mill Moisture Content Management: A Comprehensive Guide
.jpg)
Impacts of Cement Production on the Environment with Practical
majority of cement is shipped in large quantities to clients via trucks, railways, and bags, typically weighting 50 kg each Most cement is used in concrete as an essential material in the construction industry [38, 40] There are two types of processes used in cement production: the dry process and the wet process [38]UBE gratefully acknowledges the provision of support by Chinfon Cement Corporation during the commissioning of the UM464CR mill The data from Chinfon Cement is published in this paper with the kind permission of Chinfon Cement management Table 2 Comparison of Performance for PCB40 Cement Grinding Mill #4 Mill #5 MillENERGY EFFICIENT VRM TECHNOLOGY FOR CEMENT AND SLAG GRINDING Chemical process industries are running under severe constraints, and it is essential to maintain the endproduct quality under disturbances Maintaining the product quality in the cement grinding process in the presence of clinker heterogeneity is a challenging task The model predictive controller (MPC) poses a viable solution to handle the variability This paper addresses the Predictive Controller Design for a Cement Ball Mill GrindingGrinding Aids Free download as Powerpoint Presentation (ppt / pptx), PDF File (pdf), Text File (txt) or view presentation slides online Grinding aids are additives used to improve the grinding efficiency of cement mills They help reduce electricity consumption and increase production rates Common grinding aids include amines, alcohols, and polycarboxylate ethersGrinding Aids For Cement: Prepared By: Shyam R Anandjiwala
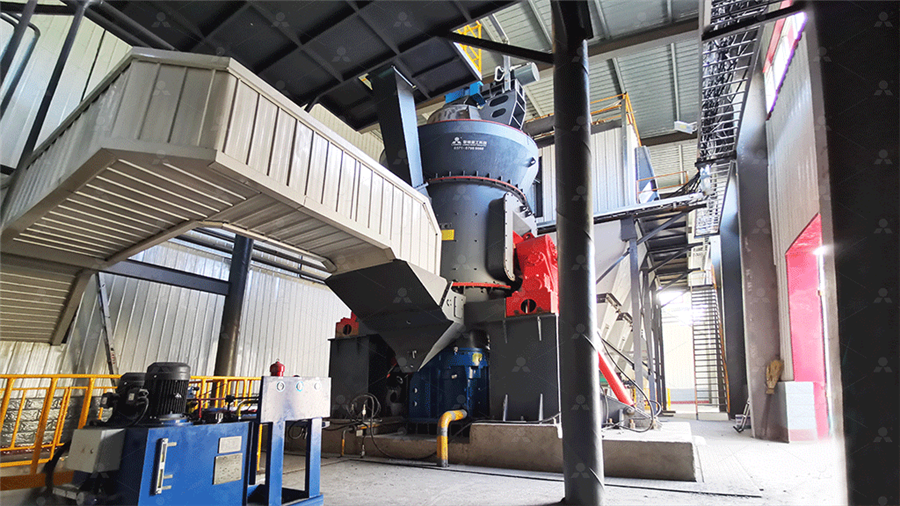
A Case Study on Evaluation of Energy Management System by
2021年11月30日 In this select cement industry, energy performance is checked, there is a continuous improvement is identified by reporting green rating project, and life cycle energy assessment, energy performance (5%) over an improvement period, the total energy cost saving over an improvement in year 20 lakh USD, and the cost implement for energy management is 22 Environmental Management Systems (EMS) All plants must have an environmental management system in place to ensure that all environmental impacts and risks are effectively managed and mitigated Integrated cement plants (incl quarries and related captive power plants), grinding stations and AFR preCement Environmental Directive Holcim