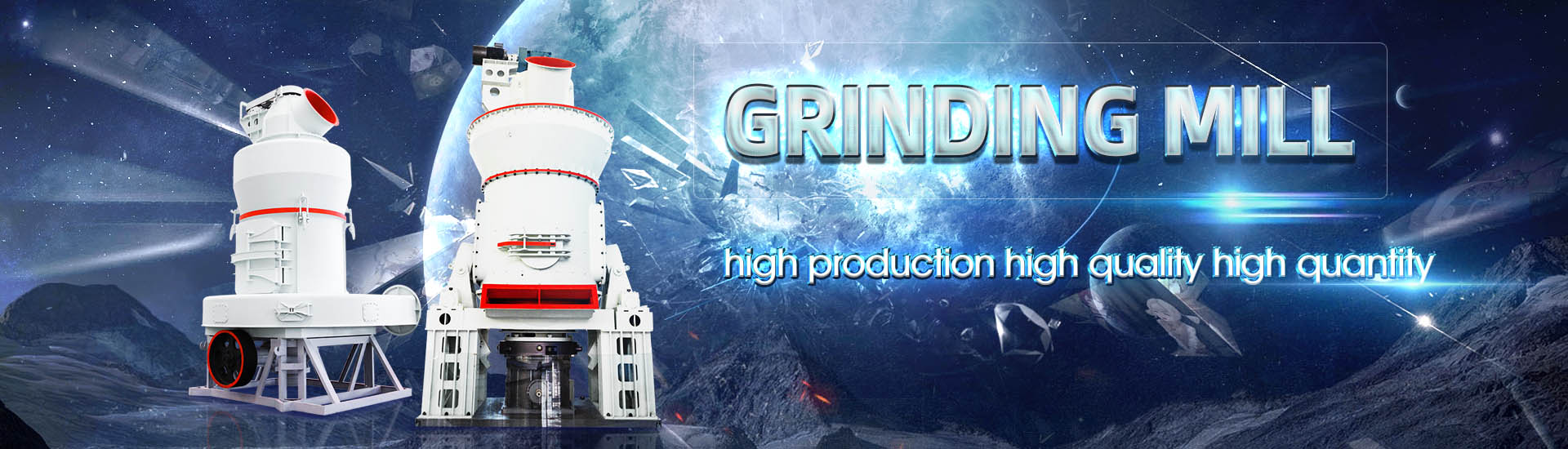
Beijing imported coarse and fine twoinone ore grinding machine
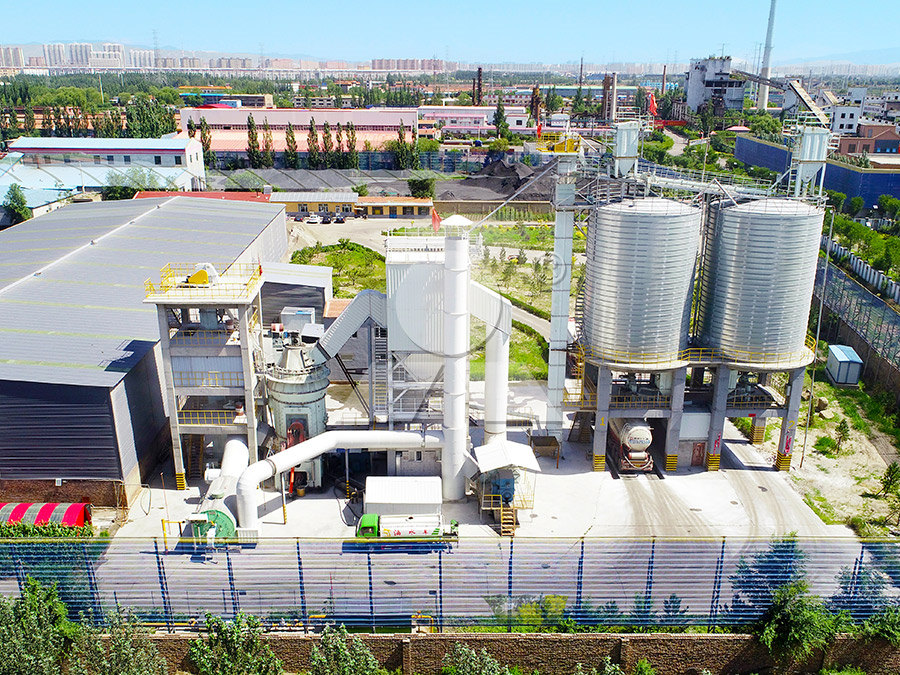
Ore Grinding SpringerLink
2023年7月20日 According to the particle sizes of grinding products, the grinding process is divided into coarse grinding, medium grinding, fine grinding, microfine grinding, and ultrafine According to the particle fi sizes of grinding products, the grinding process is divided into coarse grinding, medium grinding, ne grinding, micro ne grinding, and ultrane fi fi fi grinding Ore Grinding Methods and Process of Ore Grinding2017年9月1日 The objective of this work is to assess the influence of fine grinding in ball mills and stirred mills on valuable mineral liberation and particle shape characteristics of UG2 ore, a Fine grinding: How mill type affects particle shape characteristics 2023年7月27日 When processing soft ore with much mud and high viscosity, the rod milling process can replace the shorthead cone crusher for fine crushing and grind the ore from Rod Grinding Process SpringerLink
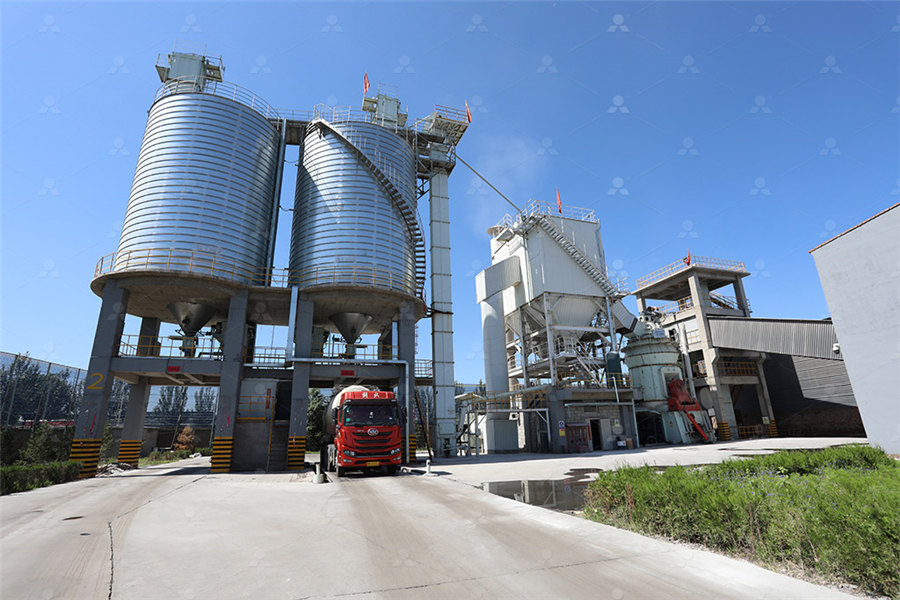
Coarse Mill MadeinChina
China Coarse Mill wholesale Select 2024 high quality Coarse Mill products in best price from certified Chinese Mill manufacturers, Grinder Machine suppliers, wholesalers and factory on China Ore Grinder Machine wholesale Select 2024 high quality Ore Grinder Machine products in best price from certified Chinese Machine Supplies manufacturers, Z Machine suppliers, Ore Grinder Machine MadeinChinaChina Coarse Fine Grinding Mill wholesale Select 2024 high quality Coarse Fine Grinding Mill products in best price from certified Chinese Surface Grinding Machine manufacturers, Steel Coarse Fine Grinding Mill MadeinChina2019年9月1日 In a feasibility study, dry grinding of magnetite ore for particle production from 50 mm to 90 µm was performed by using HPGR Results showed that two stages HPGR followed A comparative study on the effects of dry and wet grinding on
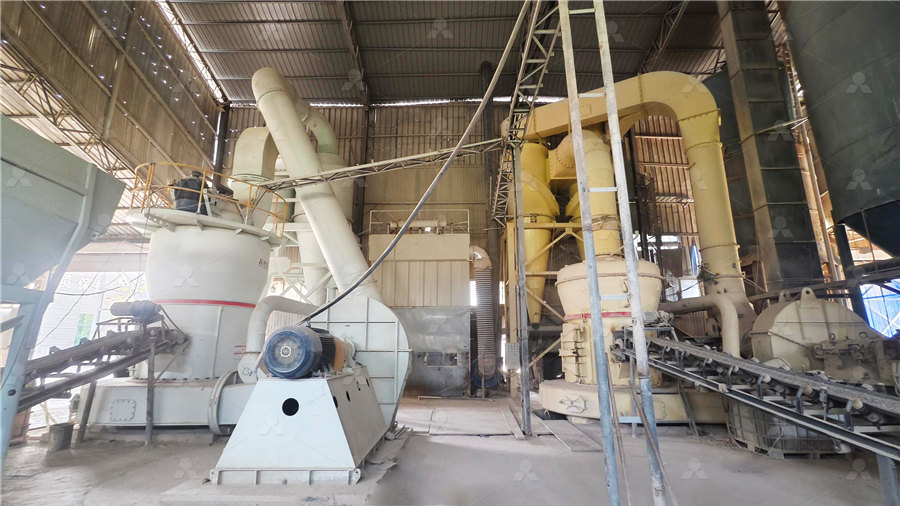
Ultrafine Grinding an overview ScienceDirect Topics
The definition of fine and ultrafine grinding varies, but fine grinding is often considered to take place below P 80 values (the size that 80 wt% of particles pass below) of 100 μm [7] and 2013年12月18日 Fine grinding, to P80 sizes as low as 7 μm, is becoming increasingly important as mines treat ores with smaller liberation sizes This grinding is typically done using stirred Energy Use of Fine Grinding in Mineral Processing2024年2月26日 Oxidised pellets have become an indispensable highquality charge for blast furnaces Nevertheless, highquality pellet feeds are becoming scarcer and scarcer To broaden the range of sources of pellet feeds and Grinding of Australian and Brazilian Iron Ore Fines for 2013年12月18日 Fine grinding, to P80 sizes as low as 7 μm, is becoming increasingly important as mines treat ores with smaller liberation sizes This grinding is typically done using stirred mills such as the Isamill or Stirred Energy Use of Fine Grinding in Mineral Processing
.jpg)
Reducing Grinding Energy and Cost Magnetite Iron Ore
Reducing Grinding Energy and Cost Magnetite Iron Ore Design Case Study A Jankovic and W Valery Metso Process Technology Innovation, PO Box 1028, Eagle Farm Qld, 4009, AustraliaAutonomous grinding algorithms with future prospect towards SMART manufacturing: A comparative survey Md Riaz Pervez, Paolo Dario, in Journal of Manufacturing Systems, 2022 21 Grinding operation Grinding is a metal removal process with the help of bonded, coated or free abrasive grain tools Apart from all other machining operations, the ‘Grinding’ is the last Fine Grinding an overview ScienceDirect Topics2022年4月12日 The relationship between the dosage of PAM500 and the percentages of the product size fractions using different grinding concentrations Study on Grinding Additives in Cassiterite–Polymetallic Sulfide Ore 2011年5月1日 Request PDF Simulation of the grinding of coarse/fine (heterogeneous) systems in a ball mill Comminution studies have been carried out by grinding narrowly sized fractions of single mineral feedsSimulation of the grinding of coarse/fine (heterogeneous) systems in
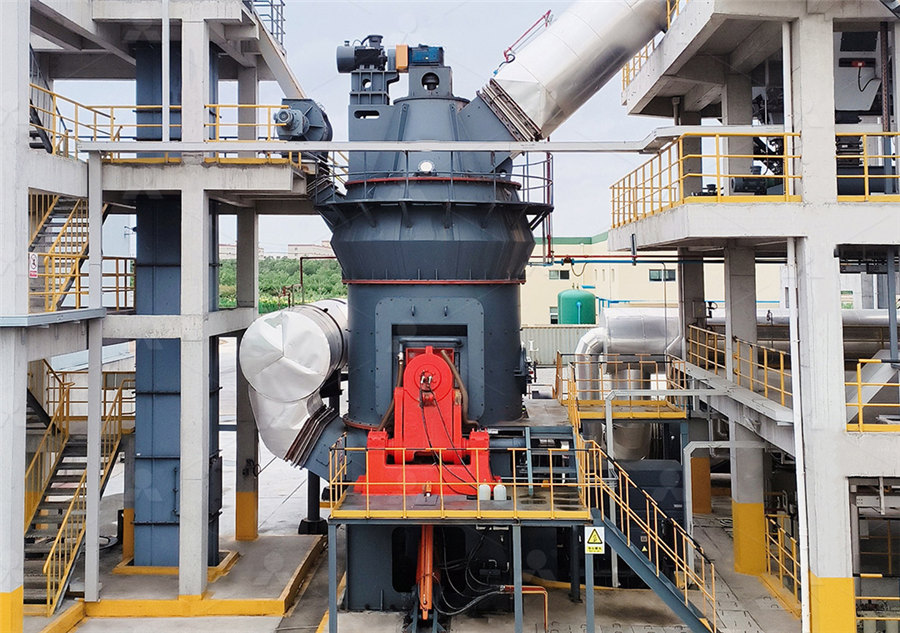
Comparison of energy efficiency between ball mills and stirred
2009年6月1日 At product sizes finer than 80% passing 75 μm, the efficiency of ball mill grinding rapidly decreasesThe practical limit to ball mill product fineness is considered to be 40–45 μm (Gao and Weller, 1994)Although ball mills can still be found in the regrind circuits in a number of mineral processing plants, their energy consumption is high, and size reduction efficiency is low2017年7月1日 Also, fine grinding has a negative impact on reverse flotation of iron ores due to high entrainment of the ultrafine hematite particles into the froth (Lima et al, 2012(Lima et al Innovations in the flotation of fine and coarse particles2009年6月1日 Stirred mills are used in fine and ultrafine grinding where the liberation occurs at very fine sizes [11] [12] [13][14][15][16][17] The stirred media mills are introduced in different process Comparison of energy efficiency between ball mills and stirred 2019年2月5日 High Pressure Grinding Roll (“HPGR”) technology is applied in a broadening range of minerals processing applications for relatively wet or moist materialsCONSIDERATIONS FOR MULTISTAGE HPGR GRINDING IN IRON ORE GRINDING
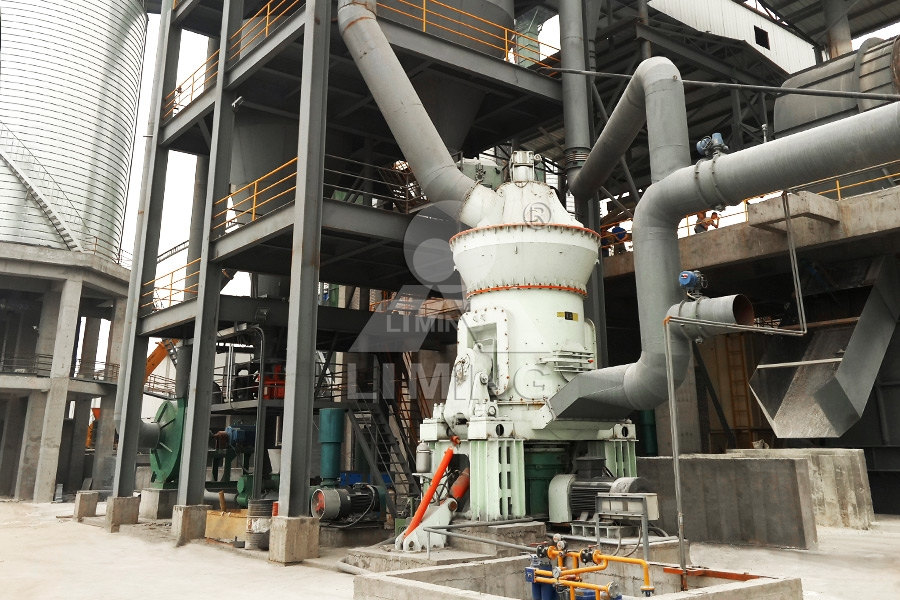
(PDF) A comprehensive review on the grinding process:
June 2022; ARCHIVE Proceedings of the Institution of Mechanical Engineers Part C Journal of Mechanical Engineering Science 19891996 (vols 203210) 236(2):年7月7日 The recovery of gold by ore leaching is influenced by the size of the particles and the chemical environment The effect of particle size on the dissolution of gold is usually studied using mono Effect of Particle Size and Grinding Time on Gold 2024年2月26日 In this work, the grinding, settling and filtering behaviour of Brazilian and Australian iron ore fines are studied and compared, with the aim of discovering the internal relationship between the (PDF) Grinding of Australian and Brazilian Iron Ore Fines for Low 2014年1月1日 Cg, respectively [11] Furthermore, the proximate analysis of Ningi graphite reveals that its ash content (8851 wt%) compares favorably with the lowgrade graphite of eastern India (8989% wt Beneficiation of low grade graphite ore of eastern India by two
.jpg)
Firstorder and secondorder breakage rate of coarse particles
2016年1月1日 It has been observed by many authors that the breakage rates of coarse particles in a ball mill slow down with increasing grinding time and deviate from the first order2022年5月23日 Grinding experiments were conducted in a laboratoryscale stirred mill on a lowgrade PGE bearing chromite ore HighPressure Grinding Rolls (HPGR) product of −1 mm was used as feed material to Modeling and application of stirred mill for the coarse grinding Grinding plants worldwide are installed with KHD`s VSeparator and operate nearly maintenancefree In 2007 a redesign of the VSeparator into a compact version was introducedCase Study of Dry HPGR Grinding and Classification in Ore Ore grinding is one of the key stages in the mining process Its where the ore is reduced to a fine powder, which can then be used in other stages of the extraction process HOME; Milling time and speed are two important factors that affect ore grinding performance in ball millsFactors affecting ores grinding performance in ball mills
.jpg)
BENEFICIATION OF LOW GRADE GRAPHITE ORE OF EASTERN INDIA BY TWO
approach is supposed to retain the flake size of coarse, free and liberated graphite, if available, during primary coarse grinding and rougher flotation stage with minimal grinding energy costs as against the usual practice of single stage grinding in the case of many ores A final concentrate of 897% weight recovery with 580% ash and 9213% Request PDF On Mar 15, 2015, Mathis Reichert and others published Research of iron ore grinding in a verticalrollermill Find, read and cite all the research you need on ResearchGateResearch of iron ore grinding in a verticalrollermill2022年4月1日 Zanin et al, (2021) developed a model to calculate bed porosity and apparent density for two feed specific gravities (porphyry copper ore: 27 kg/m 3 and hematite hosted copper ore: 38 kg/m 3) and particle size values (coarse: −600 + 150 µm and fine: −210 + 75 µm) through Richardson and Zaki models modified by introducing more suitable settling rate equationTechnological assessments on recent developments in fine and coarse 2017年3月7日 These are machines used for separating coarse a nd fine particles of granular material temporarily suspended in water The coarse particles settle to the bottom of a vessel and are sc raped up(PDF) ORE SEPARATION BY CLASSIFICATION

Ore Grinding Methods and Process of Ore Grinding
mill is mostly used for coarse grinding of the previous period of ball mill, or grinding of brittle materials and materials against overcrushing, such as tungsten and tin ore before gravity sepa Metallurgical Industry Press, Beijing 2 Ore Grinding Title: 2016年6月3日 The higher cost of grinding to produce fine pulps is well known, and is generally advanced by practical operators as the argument against fine grinding The higher reagent cost to treat fine pulps may not be obvious at first sight, yet, when it is realized that the consumption of many reagents is in direct proportion to the surface of minerals in the pulp, this statement Coarse and Fine Particle Flotation Recovery 911MetallurgistMinerals 2020, 10, 1115 3 of 16 for the ImageNet dataset [24–26] Many research studies on rock image recognition and classification based on deep learning have achieved high accuracy [8,27,28]A New Belt Ore Image Segmentation Method Based on the reduction, from coarse ore grinding down to pellet feed preparation In closed circuit operation, fine grinds can be achieved using HPGR in combination with dry or wet classification or a partial CONSIDERATIONS FOR MULTISTAGE HPGR GRINDING IN IRON ORE
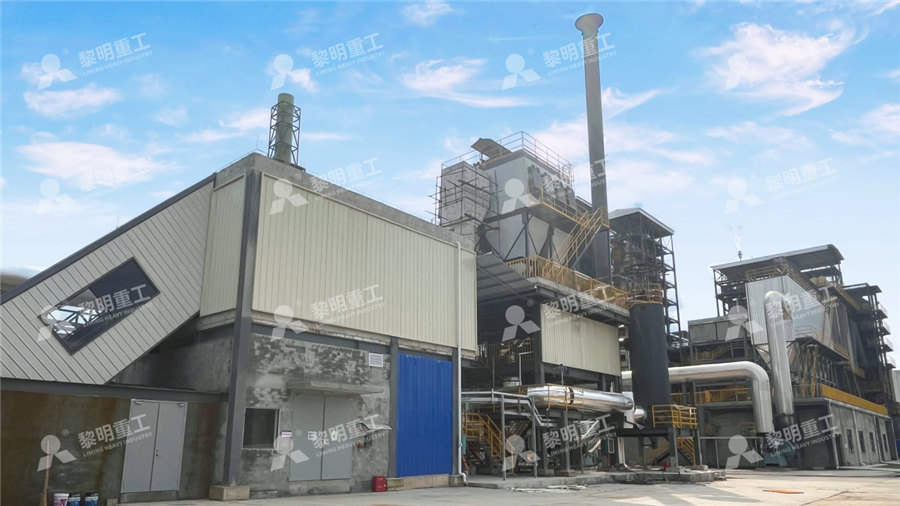
Magnetite Ore Stage Grinding and Magnetic Separation Process
2023年11月21日 Magnetite ore is one of the important sources of iron ore and is a highly magnetic mineral Its embedded state is divided into coarsegrained, coarse and finegrained, finegrained and finegrained When processing magnetite, one of the commonly used beneficiation processes is the fine screening and regrinding process However, the drawback The results of the analyses clearly shows that using a sieve of +180µm and its bottom 180µm, the best time for grinding 05kg of Itakpe iron ore with 3kg of grinding media and a mill speed of 92 rpm is 8 minutes, yielding 1710% fines and 8290% coarse, 08 mill critical speed measured 1520% fines and 8480% coarse Grinding mediatoore (PDF) Reducing Grinding Energy and Cost Magnetite Iron Ore 2015年3月15日 Furthermore, ore textures become more complex and the valuables are more finegrained, compared to ores of the last decades, requiring additional grinding for sufficient mineral liberation These trends may lead to a four times higher energy consumption for the comminution of the main metal ores in the year 2030 compared with today (Norgate and Research of iron ore grinding in a verticalrollermillThe IsaMill operated at 19 MW, below the 25 MW design for the fine grinding application The mill has a potential to draw the full power in the coarse grinding application by optimising feed density and mill components In particular the media appeared too fine for this coarse grinding duty In hindsight 4 mm media was required (Pease et al (PDF) Comparison of energy efficiency between ball mills and
.jpg)
Grinding Modeling and Energy Efficiency in Ore/Raw
2022年8月31日 The order of influencing factors of the two ores is as follows: grinding time > filling ratio > grinding concentration For Tongkeng ore, the optimized grinding conditions are grinding time 54 min, grinding concentration In the industry, screening or sieving is widely used to evaluate particle size distribution in granular materials and powders In case of coarse crushing the size reduction ratios is below 8:1 and in fine grinding it is more than 100:1 Solids Size Reduction1: Grinding – Unit Operations in Food both fine and coarse particle sizes Keywords Flotation Coarse particle flotation Fine particle flotation Flotation hydrodynamics Flotation cells O ¸Sahbaz A Uçar C Karagüzel (B) Mining Engineering Department, Dumlupinar University, 43270 Kütahya, Türkiye email: Ç EmerAdvanced Techniques on Fine and Coarse Particle Flotation2016年10月28日 Sintering is an agglomeration process that fuses iron ore fines, fluxes, recycled products, slagforming elements and coke The purpose of sintering is to obtain a product with suitable Iron Ore Sintering: Raw Materials and Granulation ResearchGate
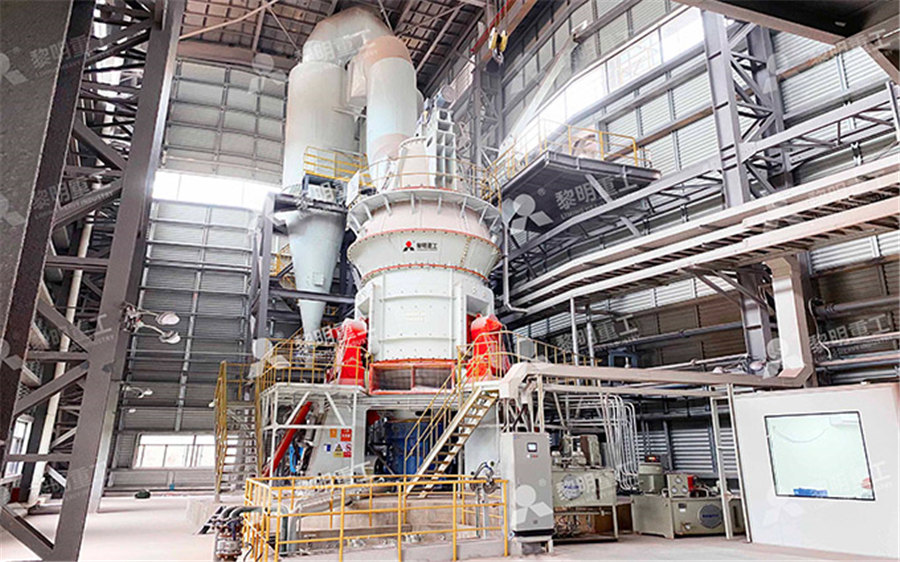
Simulation of the grinding of coarse/fine (heterogeneous)
2011年5月8日 Coarse/fine ratios from 1:0 to 1:57 Download: Download fullsize image; Fig 2 The production of dolomite fines as a function of the grinding time for two different feed compositions (coarse/fine ratios of 1:0 and 1:3) The coarse fraction is 10 × 14 mesh, and the fine fraction is −100mesh dolomite2019年7月8日 One stage grading process with checking grading operation is the most widely used The ore is directly fed into the grinding machine, and the optimum particle size for the ore is generally 620 mm Particle checking classifier separates the ground material into qualified products and unqualified products, the unqualified materials are sent back to grinding millOne Stage VS Two Stage Grinding Circuit JXSC MachineCoarser Grinding: Economic Benefits and Enabling Technologies Robert Maron1*, Jaime Sepulveda2, Adam Jordens1, Christian O’Keefe1, Henry Walqui1 1 CiDRA Minerals Processing, USA 2 J‐Consultants, Ltd ABSTRACT Coarser grinding and coarse particle recovery are receiving increased attention as a potentialCoarser Grinding: Economic Benefits and Enabling CiDRA2013年8月1日 PDF Sintering is a process by which a mixture of iron ores, fl uxes and coke is agglomerated in a sinter plant to manufacture a sinter product of a Find, read and cite all the research you (PDF) Iron ore sintering Part 1 Theory and practice of the sintering
.jpg)
Interactive effect of minerals in the flotation of complex ores:
(1) Fine valuable minerals adhere to the coarse gangue minerals, which leads to the passive loss of valuable minerals In hematite (Fe 2 O 3) flotation, for example, fine hematite particles can be adsorbed on the surface of quartz, resulting in a reduction of hematite recovery [19];(grinding) Crushing: coarse 1500 – 500 350 – 100 43 – 5 average 350 – 100 100 – 20 35 – 5 fine 100 – 20 20 – 5 5 – 4 Grinding: coarse 20 – 5 5 – 01 4 – 50 fine 5 – 01 01 – 005 and less The efficiency of crushing is determined by the mass of the crushed material obtained atReengineering of the ore preparation production process in the