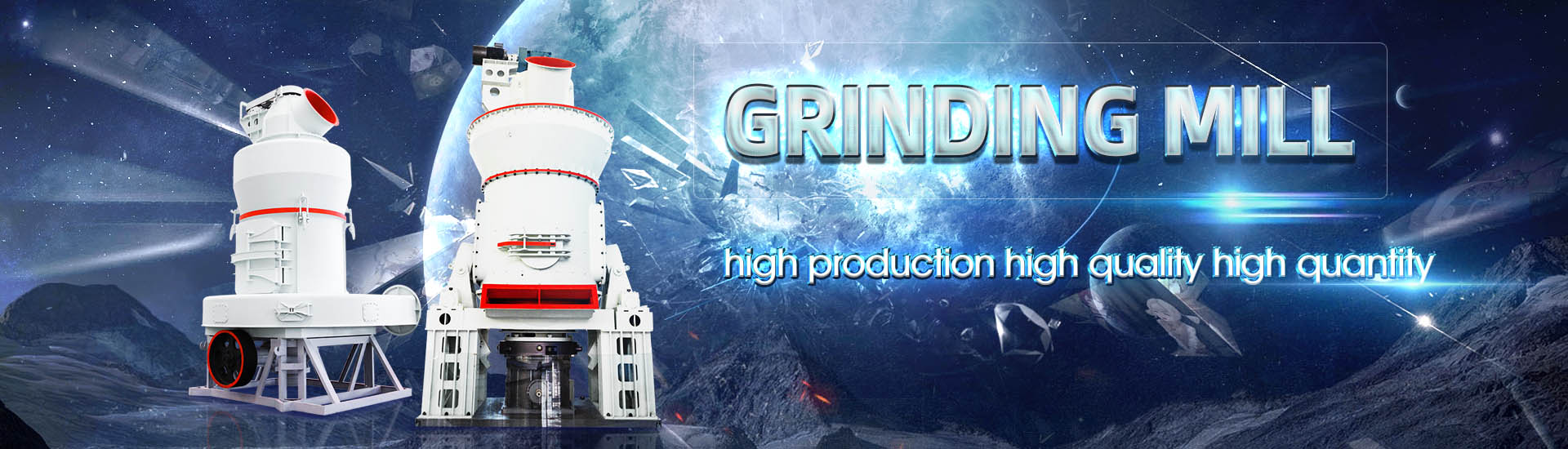
Purpose of hot metal slag powder

Basic Oxygen Steelmaking Slag: Formation, Reaction,
Basic oxygen steelmaking (BOS) slag, a product of hot metal element (eg, Si, Mn, Fe, P) oxidation and flux (eg lime, dolomite) dissolution, plays a critical role in the production of highquality crude steel, although its behavior inside the Steelmaking slag includes the following: slag produced in the hotmetal pretreatment processes (desiliconization, dephosphorization, desulfurization, etc), slag flowing out from the converter Processing and Reusing Technologies for Steelmaking Slag2023年5月15日 The hot molten steel slag is poured into the hot smothering device, and the appropriate amount of intermittent water spray cooling makes it produce saturated steam, Comprehensive utilization of steel slag: A review ScienceDirect2005年2月1日 Steelmakers have made attempts to reduce slag volumes in the individual unit processes and to strive towards slagless steelmaking by recycling slags internally A much improved understanding of(PDF) Industrial uses of slag The use and reuse of iron
.jpg)
BOF Steel Slag: Critical Assessment and Integrated Approach for
2021年9月24日 During steel production, the impurities in the hot metal react with the fluxes forming the steel slag Chemical constituents of this steel slag (SS) are relevant to 2011年10月26日 Steel slag is a byproduct of the steelmaking and steel refining processes This paper provides an overview of the different types of steel slag that are generated from basicoxygenfurnace (BOF) steelmaking, electricarc Chemical, Mineralogical, and Morphological Properties 2018年2月20日 Hot slag was modified to enhances its properties or prepare high valueadded products Disposing hazardous solid waste and recovering valuable metals by modification Modifying hot slag and converting it into valueadded materials: A 2021年2月21日 In this study, the optimal HMD slag composition is investigated, considering both the sulphur removal capacity and the iron losses In part I the theory is discussed and in part II the optimal slag is validated with plant data, Optimal hot metal desulphurisation slag considering
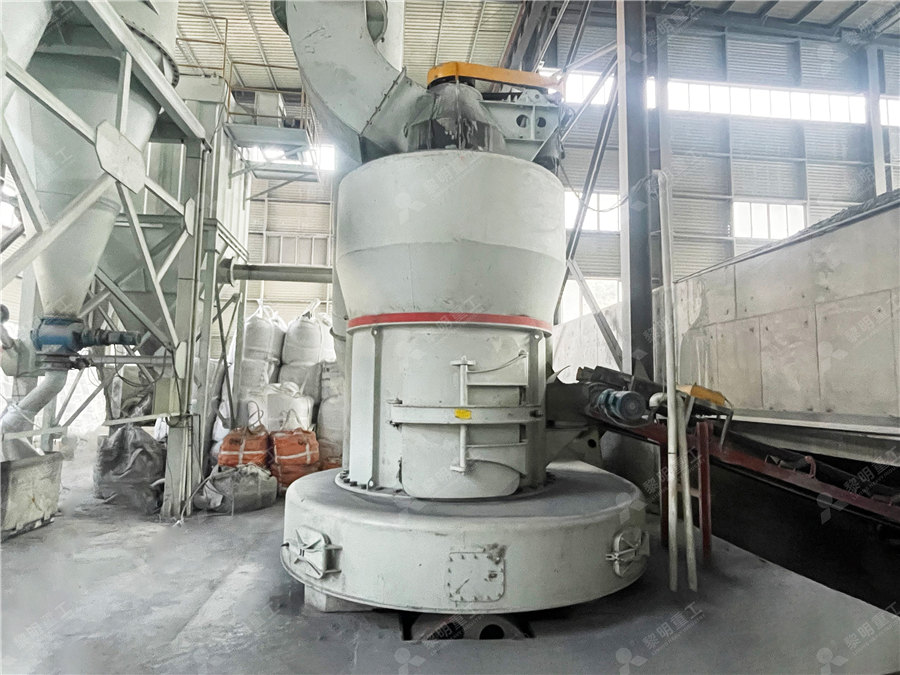
Slag SpringerLink
2024年1月1日 Its important functions are: (1) absorb oxide impurities in gangue to separate it from metal or matte; (2) remove sulfur, phosphorus, and other harmful components from iron Stavian Industrial Metal Joint Stock Company is a leading enterprise in Vietnam in the field of industrial metal and oil are removed from the metal surface using a hot alkali solution, mild acidic bath, or biological cleaning bath Epoxies, vinyls, StepbyStep Explanation of the Hot Dip Galvanizing magnesium reagents in powder or granular form are used to remove sulfur via slagliquid metal reactions done under reducing conditions, where sulfur is transferred out of the steel through the slagmetal interface, and into the slag Slag is an ionic solution made up of oxides and fluxesDesulfurizing Steel: Magnesium is the Reagent of Choice(2) Reaction between metal, slag, and solid lime: In this experiment, a solid lime rod is immersed into molten slag and hot metal (Fig 2(B)) (3) Reaction between metal and slag: In this experiment, slag and metal are melted without the immersion of a solid lime rod (Fig 2(C)) To produce the slag, reagentgrade SiO2, CaCO3, Al2O3, and MgO Influence of Solid CaO and Liquid Slag on Hot Metal Desulfurization
.jpg)
Properties and Uses of Steelmaking Slag – IspatGuru
2018年11月14日 Fig 1 Processing of steelmaking slag As steelmaking slag is formed, it is in a molten or redhot state at temperatures ranging from 1,300 deg C to 1,700 deg C This slag is immediately subjected to the cooling process upon removal Usually, this is performed in a cooling yard by air cooling and moderate water sprinkling2023年11月21日 High sulfur content in hot metal desulfurization slag is one of the major barriers for recycling of the slag in the ironmaking and steelmaking process How to effectively remove sulfur from the hot metal desulfurization slag is a crucial step for improving its recyclability Thermodynamic analysis shows that CO2 is a better oxidation gas for sulfur removal from the Treatment of Hot Metal Desulfurization Slag With CO2017年3月22日 R Boom and R R Beisser: ‘Hot metal desulphurization to control the sulphur balance at Hoogovens IJmuiden’ In: WK Lu, editor Proceedings McMaster Symposium on Iron and Steelmaking No 11, Developments in Hot Metal Preparation for Oxygen Steelmaking; 1983 May 2526; Hamilton, Canada Hamilton: McMaster University; 1983 p 68–95Sulphur removal in ironmaking and oxygen steelmaking4 67 mainly in the transitory reaction zone However, as the removal and stabilization of sulfides 68 after the desulfurization reaction occurs in the permanent contact reaction zone, 69 consideration of this zone, involving top slag, is also very important to simulate the HMP 70 process 71 72 Fig 1–Schematic diagram of hot metal pretreatment with powder injectionKinetic Simulation of Hot Metal Pretreatment: Desulfurization
.jpg)
Flux (metallurgy) Wikipedia
Rosin used as flux for soldering A flux pen used for electronics rework Multicore solder containing flux Wire freshly coated with solder, held above molten rosin flux In metallurgy, a flux is a chemical reducing agent, flowing agent, or purifying agent Fluxes may have more than one function at a time They are used in both extractive metallurgy and metal joining2024年1月1日 Slag is not only required in the smelting process in the furnace, but also indispensable for secondary refining of steel, hot metal pretreatment, and steel continuous casting The name of “slag” is not precise enough, but it is still being used Slag that has been melted into a liquid state at high temperature is called drossSlag SpringerLink2021年8月10日 Basic oxygen steelmaking (BOS) slag, a product of hot metal element (eg, Si, Mn, Fe, P) oxidation and flux (eg lime, dolomite) dissolution, plays a critical role in the production of highquality crude steel, although its behavior inside the BOS vessel (formation and reaction with metal droplets and gas) is still not clear and its recycling has always been challengingBasic Oxygen Steelmaking Slag: Formation, Reaction, and measured as a function of slag composition at 1200 ~ To avoid excessive Na20 loss by reaction with carbon, the initial slagmetal interfacial area was increased by using a powder mixture of slag and metal to reduce the time for the equilibrium The results indicate that Soda slag system for hot metal dephosphorization Springer
.jpg)
The Carbon Cost of Slag Production in the Blast Furnace: A
2016年2月5日 The quality of raw materials (iron ore, coal, and coke) has a clear impact on the carbon emissions of the hot metal production in steel making So far, very little work has been done to measure and quantify this impact Yet for benchmarking, technology choice and general carbon optimization are important elements The total slag production of a blast furnace gives minimize volumes of unusable slag that would otherwise be disposed in slag dump facilities DHMS is a byproduct of the desulphurization of hot metal (also referred to as pigiron) which is produced in the blast furnace by reducing hematite (Fe2O3) into sponge Fe using coke as a reducing agent and adding fluxes such as lime for slag formationProcess Design for the Magnetic Recovery of Iron from Desulphurised Hot Welcome to the Atlas Pressed Metals FAQ and HowTo Guide, your onestop resource for answers to common questions and stepbystep instructions on various aspects of Powder Metallurgy Whether you're new to the field or an experienced professional, you'll find valuable information here to help you navigate the world of Powder MetallurgyFrequently Asked Questions Atlas Pressed Metals2020年3月3日 Highphosphorous hot metal created difficulty for refining in top blown process that leads to develop rotary oxygen process of steelmaking The basic principles are (i) CO gas is burned inside the vessel, generating heat transfer to the lining of vessel and (ii) rotation of converter to get heat transfer from lining of vessel to molten bathOxygen Steelmaking Processes SpringerLink
.jpg)
Handling of Hot Metal in Blast Furnace Iron Making IspatGuru
2016年2月10日 blast furnace, Hot metal, hot metal runner, ladle, lime milk, PCM, Pig iron, skimmer, slag, Torpedo ladle, Handling of Hot Metal in Blast Furnace Iron Making Hot metal (HM) is produced by the reduction of descending ore burden by the ascending reducing gases in a blast furnace (BF) It is liquid in nature and gets collected in the hearth of the BFwhere A slag is the nominal metal–slag interfacial area, β L is the metalside mass transfer coefficient of the permanent reaction, m ˙ p is the particle feed rate, ρ S is the slag density, f p, b is the fraction of CaC 2 particles which reside inside the bubbles at the metal–bubble interface, β p is the mass transfer coefficient of the penetrated particles, t p, res is the residence A Review of Modeling Hot Metal Desulfurization Visuri 年6月10日 Corrosionresistant towards hot metal and slag Excellent thermal shock resistance Resistance to penetration of hot metal in refractory bricks Addition of carbon in alumina refractory improves its thermomechanical properties with respect to corrosion resistance, nonwetting towards hot metal and slag and thermal shock resistanceRefractory for Hot Metal Transport and Desulfurizationhot metal to the slag [7] Qiu Lin [8] developed a novel tech min, lime powder injection amount is 255–336 kg and the iron balls amount is 400–2000 kg; The dephosphorizationHot metal dephosphorization process using calcium ferrite slag
.jpg)
Development of Hot Metal Dephosphorization with CaO Powder
221 Hot metal dephosphorization by normal blowing (1) Changes in hot metal temperature and composition during blowing Figure 3 shows the change in hot metal temperature The temperature at the end of blowing was roughly 1613 K in any of the Heats Figure 4 shows the change of [P] in hot metal during the blowing2024年1月4日 The mixtures can be complex and vary, so a welder must have the right flux for the welding metal and position But for stick or fluxcored welding, the flux is “preinstalled” as long as the electrode/wire for the joint is right What is Flux in Welding What Does It Do? Weld Guruapplied to hot metal dephosphorization by converter Figure 48) shows the result presented by Sumitomo Metal in 2011 The application of LDAC to hot metal dephosphorization is an effective measure to improve the slagging ratio In addition, the blown lime powder directly reacts with FeO, formed at hot spots, and enhances the dephosphorizationReview Dissolution Behavior of Lime into Steelmaking Slag J 2024年4月28日 Steel slag is a byproduct of the steel industry and usually contains a high amount of fCaO and fMgO, which will result in serious soundness problems once used as a binding material and/or aggregates To A Review on the Carbonation of Steel Slag: Properties,
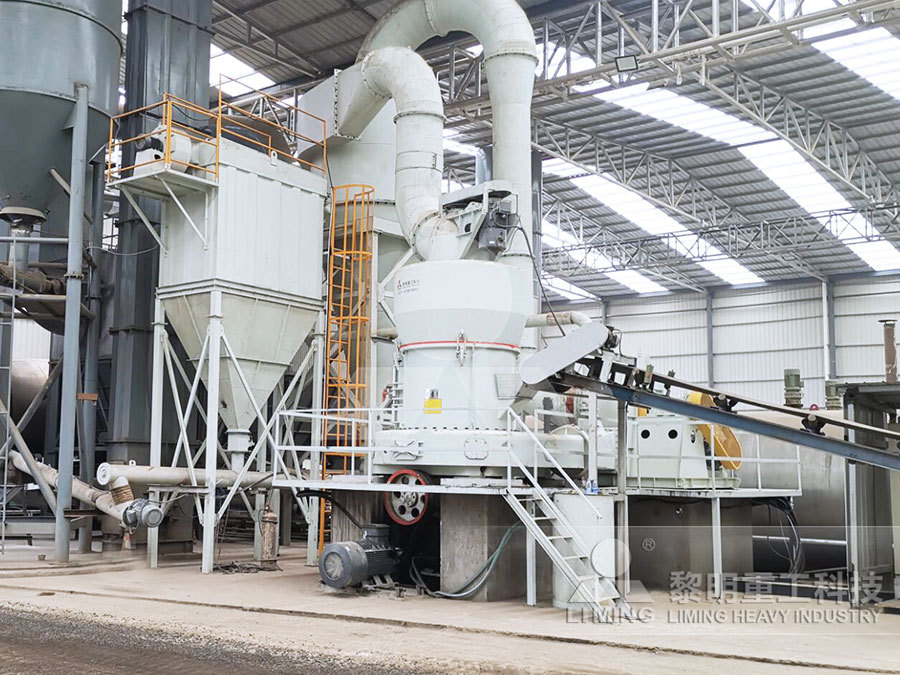
Processing and Reusing Technologies for Steelmaking Slag
Steelmaking slag contains about 1040wt% metal iron (excluding iron oxides), which is derived from the refining process or from some processing vessel (eg, the converter, hot metal/molten steel ladle, or tundish) It is advantageous to separate this iron from the slag for the purpose of using the iron recovered as a substitute for2009年10月1日 About 7 to 9kg waste slag is produced per ton hot metal treated in the Kanbara Reactor (KR) desulfurization process, and the waste slag contains approximately 40–60 % CaO and large amounts of Development of Slag Recycling Process in Hot Metal2023年7月4日 Depending on the equipment used, hot metal pretreatment process can be hot metal trough continuous treatment process, hot metal tank blowing process, mechanical stirring process, or special furnace process 1 Hot metal trough continuous treatment This is a simple hot metal pretreatment process, including casting process and blowing processHot Metal Pretreatment SpringerLink2018年8月1日 To solve the problem of steel slag, two different efforts have been made The first effort is to reduce the amount of steel slag A hot metal pretreatment can be used to remove silicon (Si), P, and S before the decarburization of pig ironSteel slag in China: Treatment, recycling, and management
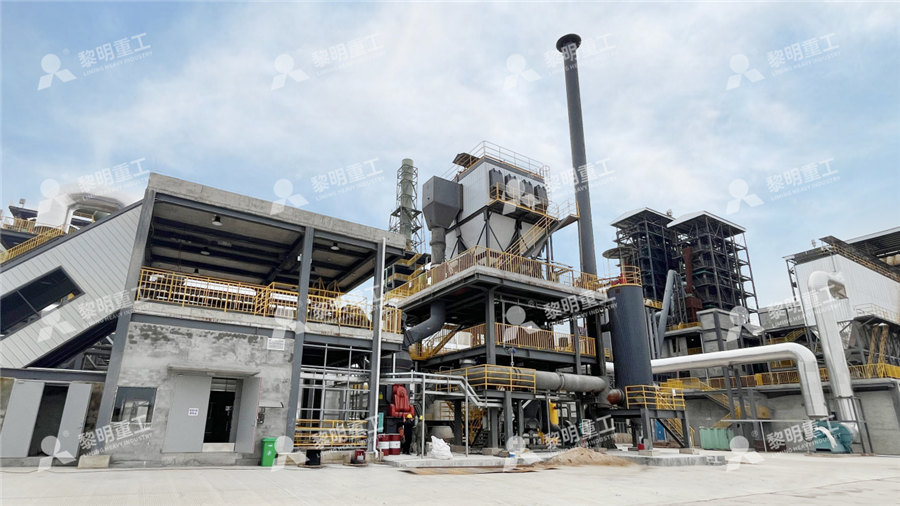
Recovery of Metals from Copper Smelting Slag Using Coke and
2024年2月29日 With the purpose of recovering the metal values, in this study the copper slag was reduced by coke and biochar at 1250 °C in an argon gas atmosphere using the isothermal reduction/drop quenching technique The phase compositions of metal, matte, and slag were determined using electron probe microanalysis (EPMA) The effects of reduction time and 2016年2月29日 Gold and silver form an alloy that is heavier than the slag and sinks to the bottom of the furnace Once the smelting is complete, the slag is removed and the precious metals are casted in ingots The slag contains gold and silver and must be reprocessed in order to minimize the losses of precious metalsGold Smelting Refining Process 911Metallurgist2020年1月29日 A study was carried out to examine effects of calcium ferrite slag on dephosphorization of hot metal in the steelmaking BOF, with aims to pick up the speed of slagforming, increase the slag Effects of calcium ferrite slag on dephosphorization of hot metal 2024年11月1日 Nevertheless, the residual slag after leaching may not be suitable for steelmaking production, leading to highgrade sensible heat loss Y Li [49] further investigated the metallurgical slag ranging from 1450 to 1650 °C represented significant secondary energy potential and developed a method to directly modify the hot slag into highvalueadded Recent research progress on recycling metallurgical waste slag
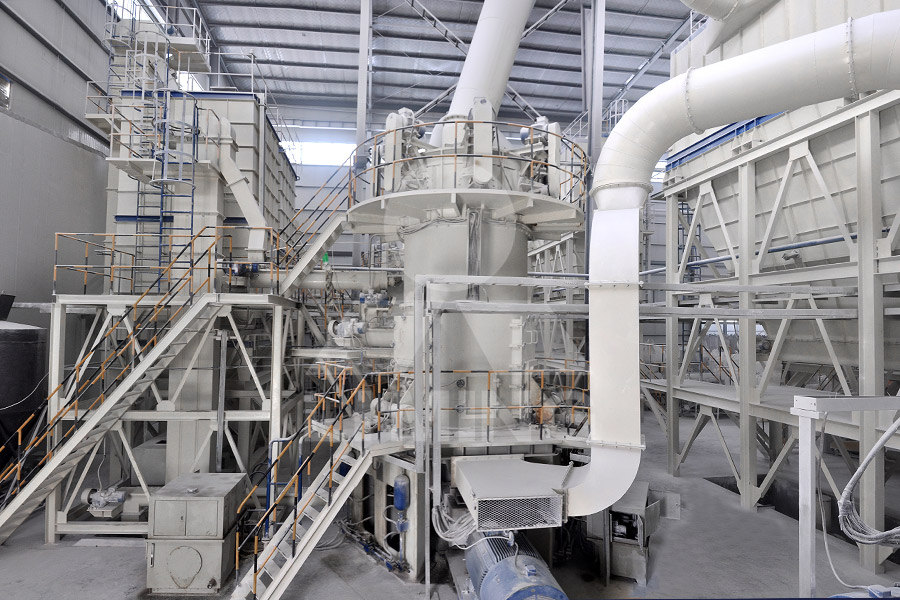
Review Dissolution Behavior of Lime into Steelmaking Slag J
applied to hot metal dephosphorization by converter Figure 48) shows the result presented by Sumitomo Metal in 2011 The application of LDAC to hot metal dephosphorization is an effective measure to improve the slagging ratio In addition, the blown lime powder directly reacts with FeO, formed at hot spots, and enhances the dephosphorization2024年8月11日 The desulfurization capacity of top slag in the process of predesulfurization of hot metal containing vanadium and titanium was researched The top slag system of CaOSiO2MgOAl2O3TiO2VOx that was formed by blast furnace slag and a CaO desulfurization agent reduced the sulfur in hot metal from 008 wt% to 002 wt% It was found that the Influence of Top Slag Containing TiO2 and VOx on Hot Metal Pre Removing welding slag is a mechanical process, completed with chipping hammers, wire brushes or wheels, or needle scaler Some filler metals, however, are formulated with selfpeeling slag that releases from the weld on its own Slag’s purpose is twofold It protects the weld from oxidation and contamination from the atmosphereEverything You Should Know About Weld Slag (And Why)2019年2月13日 The dephosphorization plays an important role in the converter steelmaking process In view of this importance, many studies on the hot metal dephosphorization have been carried out [1,2,3], including reaction mechanism and the factors affecting the dephosphorization rate such as lime property, slag composition and temperature and so on [4, 5]The Study of Hot Metal Dephosphorization by Replacing Part of
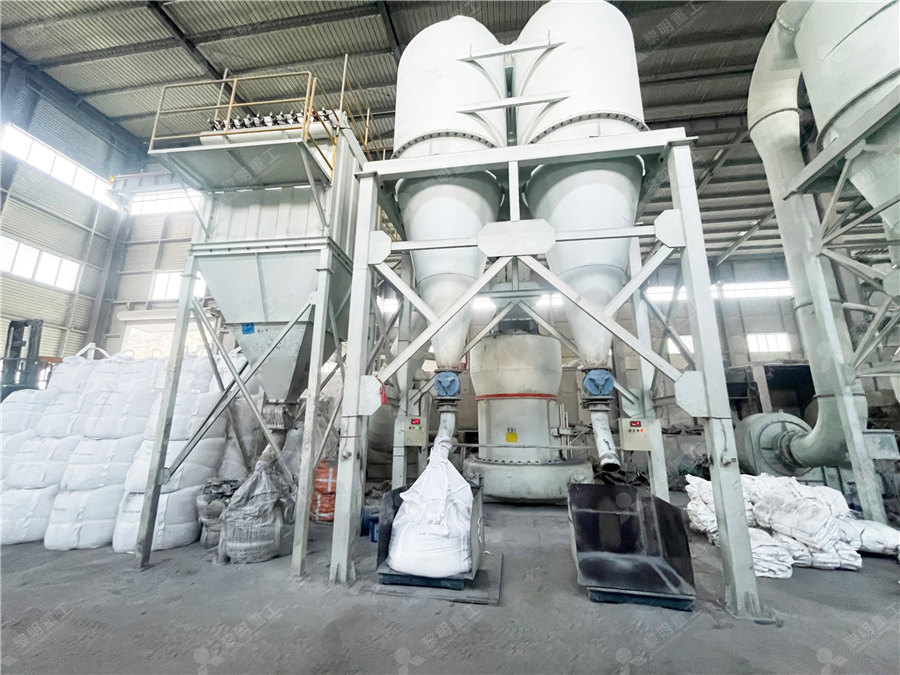
A Review on Environmental Concerns and Technological
2023年11月20日 Mineral process wastes, such as metallurgical slags nowadays, are of significant metals and materials resources in the circular economy The usability of ironmaking slag is well established; however, steel slag still needs to be utilized due to various physicochemical constraints In this context, we have reviewed the global steel slag 2021年2月21日 Introduction Since the early days of iron and steelmaking, sulphur is considered as an unwanted impurity that needs to be removed [Citation 1]Although there are various processes in the modern steelmaking chain where sulphur can be removed, a dedicated hot metal desulphurisation (HMD) process between the blast furnace (BF) and converter (or Optimal hot metal desulphurisation slag considering iron loss 2021年4月7日 Removal of sulphur takes place by two methods: 1use of basic slag and 2 injection of active agents 1Basic slag for desulphurisation Desulphurization using basic slag can be brought about by two mechanism: 1 Reaction takes place between basic synthetic or refining slag (which is added to the empty ladle) and the liquid steel being tappedDesulphurization of Steel Metal World InsightCarbon dioxide sequestration using steel slag—modeling and experimental investigation Smitha Gopinath, Anurag Mehra, in Carbon Dioxide Sequestration in Cementitious Construction Materials, 2018 41 Introduction Steel slag is an industrial waste that is generated during the production of steel In the production of steel, oxides of metal impurities in the iron combine Steel Slag an overview ScienceDirect Topics
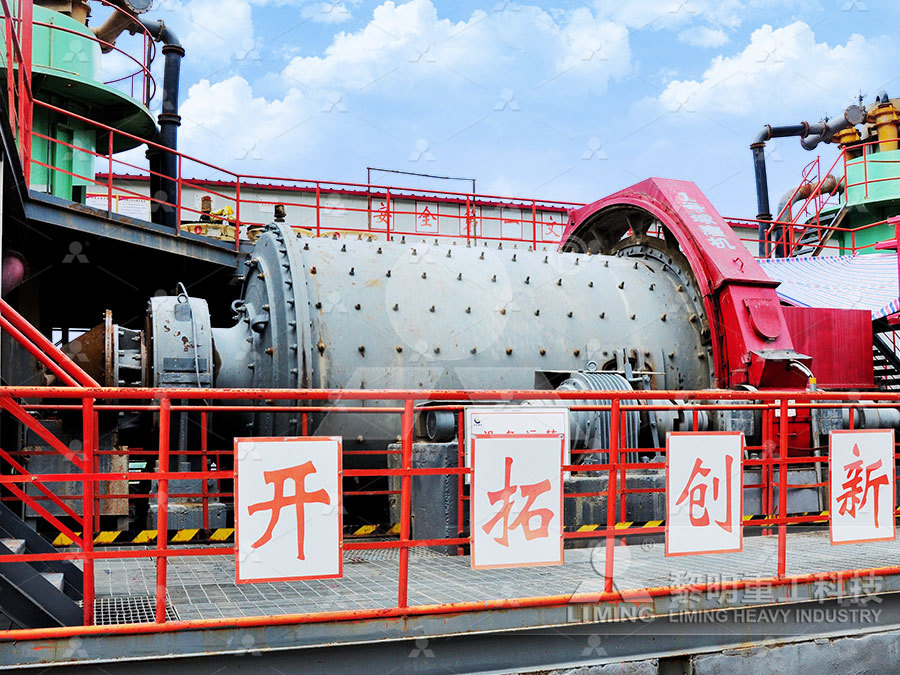
Effect of Slag Melting Behavior on MetalSlag Separation Temperature
around cohesive zone Therefore, purpose of this study is to clarify the effect of slag melting behavior on metalslag separation behavior In order to simulate the behavior around cohesive zone, electrolytic iron powder, carbon powder, and synthetic slag were prepared as reduced iron, residual carbon and slag components, respectively