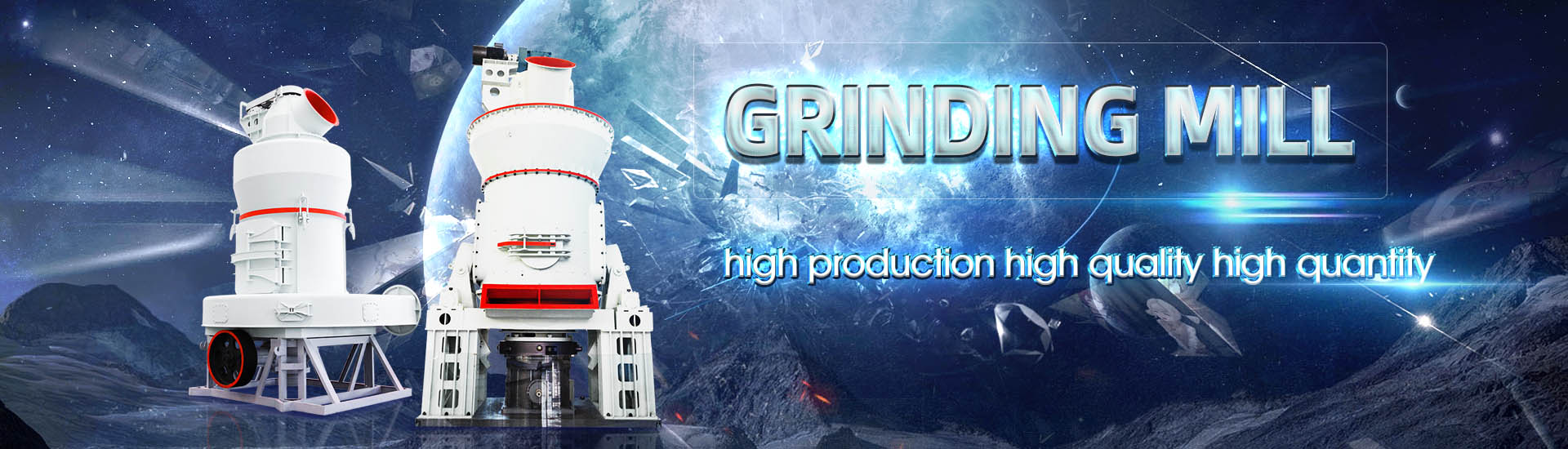
Ore mill particle size control method
.jpg)
Hierarchical Intelligent Control Method for Mineral
2023年8月30日 Mineral particle size is an important parameter in the mineral beneficiation process In industrial processes, the grinding process produces pulp with qualified particle size for subsequent2020年1月1日 Abstract: In this work the ore particle size distribution is estimated from an input image of the ore The normalized weight of ore in each of 10 size classes is reported with Estimating Ore Particle Size Distribution using a Deep 1995年5月1日 It is difficult in runofmine (ROM) milling circuits to control the particle size of the product and other important variables because the ore fed to the mill also acts as the main Specification framework for robust control of a runofmine ore 2024年4月16日 This study presents a comprehensive methodology for calibrating the digital twin of a laboratory ball mill, emphasizing the milling of copper ore through the integration of advanced computer vision techniques Calibrating the Digital Twin of a Laboratory Ball Mill for
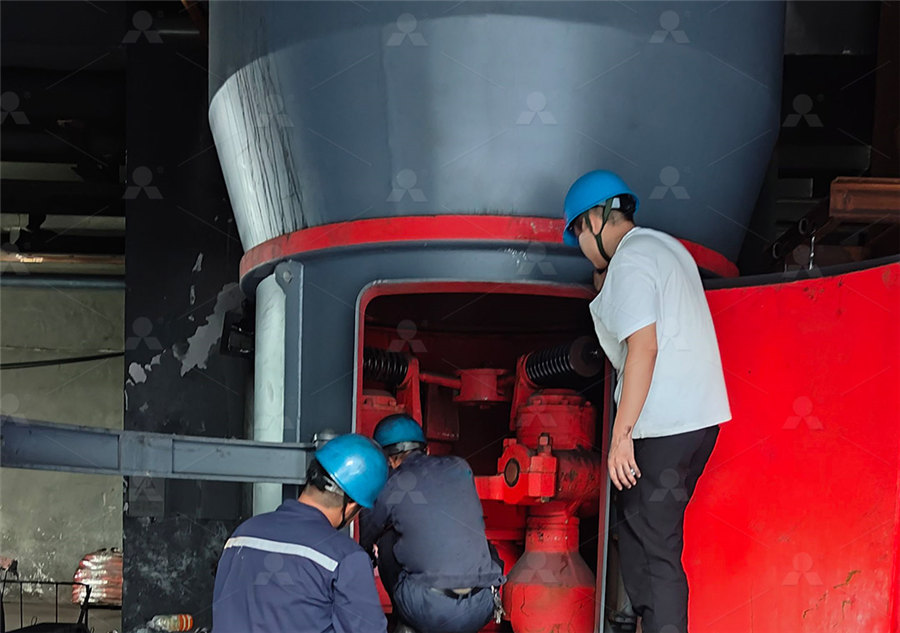
Override and Model Predictive Control of Particle Size and Feed
A new grinding control strategy based on override control (ORC) and model predictive control (MPC) is presented to control product particle size and feed rate in grinding process ORC is 2019年1月1日 Commercial camera systems are available to measure the size distribution of the feed ore to a mill This paper investigates how well basic equipment and algorithms can Feed Size Distribution Feedforward Control for a Grinding Mill Abstract: In this work the ore particle size distribution is estimated from an input image of the ore The normalized weight of ore in each of 10 size classes is reported with good accuracy A Estimating Ore Particle Size Distribution using a Deep 2024年1月1日 The main parameters of grinding and classification process include measurement of millfeeding quantity, mill load measurement, measurement of ore slurry density, Online Measurement and Control for Ore Grinding and Classification
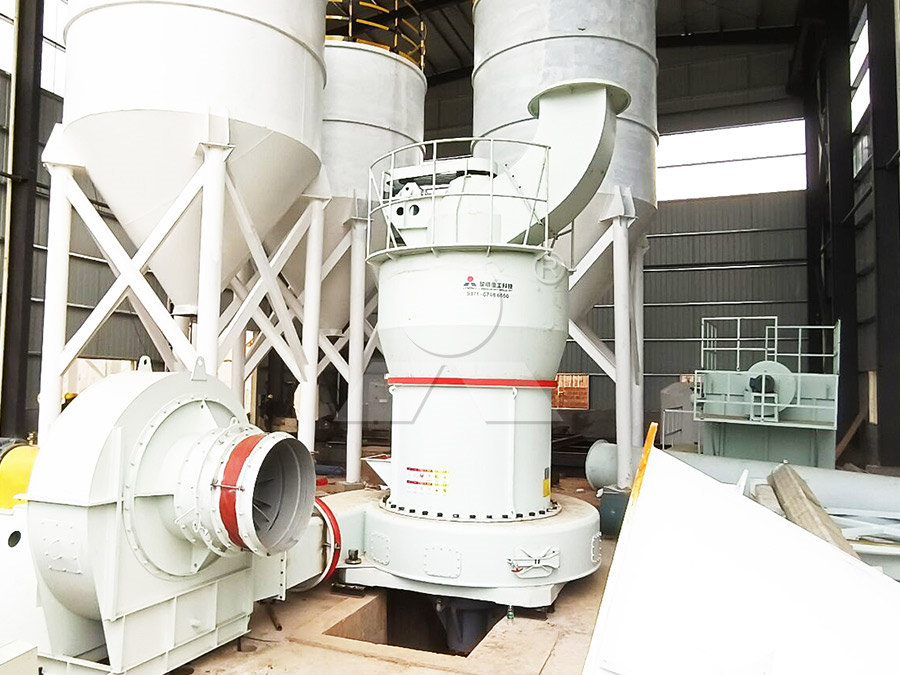
An Ore Image Segmentation Method Based on AttentionUnetGAN
Abstract: In the milling process, ore particle size is an important indicator that affects the efficiency and stability of the mill, accurate and realtime detection of ore particle size is significant for 1995年5月1日 It is difficult in runofmine (ROM) milling cir cuits to control important variables including the particle size of the product because the ore fed to the mill also acts as the main grinding medium Independent control of the amount, size and hard ness of the grinding medium present in the mill is therefore not possibleSpecification framework for robust control of a runofmine ore 2023年12月12日 properties of ores in the mill (mass, size, hardness, density and granulometric com position of particles): characteristics of grinding agents (mass, density, size(PDF) Control of ball mill operation depending on ball 2020年1月1日 Estimating Ore Particle Size Distribution using a Deep but a neural network is used to estimate the particle size distribution Both methods used traditional “shallowâ (2012) Dual particle filters for state and parameter estimation with application to a runofmine ore mill Journal of Process Control, 22, 710â Estimating Ore Particle Size Distribution using a Deep Convolutional
.jpg)
Control of ball mill operation depending on ball load and ore
Control of the filling level of the mill by an ultrasonic sensor Size, hardness and density of ore particles according to M M Protodiakonov scale It is a system that can measure ore content on 4 inputs and includes realtime measurement of pulp density The rate at which fresh ore from the belt conveyor enters the mill2017年3月20日 An effect of a grinding method, that is ball mill and high pressure grinding rolls (HPGR), on the particle size, specific surface area and particle shape of an iron ore concentrate was studiedPhysicochemical Problems of Mineral Processing Investigation Download scientific diagram Iron ore particle size distribution from publication: Impact Load Behavior between Different Charge and Lifter in a LaboratoryScale Mill The impact behavior Iron ore particle size distribution Download Scientific Diagram2012年4月1日 Request PDF Dual particle filters for state and parameter estimation with application to a runofmine ore mill Measurements are not readily available for grinding mills owing to the nature of Dual particle filters for state and parameter estimation with
.jpg)
SIZE REDUCTION BY GRINDING METHODS By ResearchGate
6 Autogenous mill: Autogenous or autogenic mills are socalled due to the selfgrinding of the ore: a rotating drum throws larger rocks of ore in a cascading motion which causes impact breakage of DOI: 101109/TII2020 Corpus ID: ; Mesoscale Particle Size Predictive Model for Operational Optimal Control of Bauxite Ore Grinding Process @article{Lu2020MesoscalePS, title={Mesoscale Particle Size Predictive Model for Operational Optimal Control of Bauxite Ore Grinding Process}, author={Shaowen Lu and Tianyou Chai}, journal={IEEE Transactions on Mesoscale Particle Size Predictive Model for Operational Optimal 2020年11月1日 Tracking the mill performance showed that the mill power consumption decreased from 949 to 663 kWh/t (a nearly 30% reduction), P80 of the mill product decreased from 611 to 355μm, and the mill Ore particles segmentation using deep learning methodsFurthermore, being unable to monitor the particle size online in most of concentrator plants, it is difficult to realize the optimal control by adopting traditional control methods based on mathematical models In this paper, an intelligent optimal control method with twolayer hierarchical construction is presentedIntelligent optimal control system for ball mill grinding process
.jpg)
Measurement and Control for Ore Grinding and Classification
2024年1月1日 The process control mainly includes ore feeding, grinding density, mill load, level in sump, cyclone feeding density and pressure force, cyclone overflow density and particle size, and so forth Grinding and classification process is a dynamic circulation system with complex mechanismmanagement, grate hole and mill liner wear, screen and trommel wear, hydrocyclone wear will all contribute towards improved particle size control Keywords: Ma¶aden, crusher, mill, SAG, hydrocyclone 1 Introduction Alumina production is a hightonnage, lowprofit margin operation where alumina must beAA04 Bauxite Particle Size Requirements for the BayerBall mills are progressively used to grind the ores for particle size reduction and to liberate valuable minerals grinding process [18] It is often hard to control the PSD in the end product In a combined mineral processing, BBM and laboratory ball mill (LBM) 2 Experimental Method 21 Samples In the present study, Estimation of Grinding Time for Desired Particle Size Distribution2011年1月1日 Grade control programs aim to deliver economic tonnes to the mill via accurate definition of ore and waste The foundation of a successful program is high quality sampling supported by geology and Design of grade control sampling programs for underground gold mines
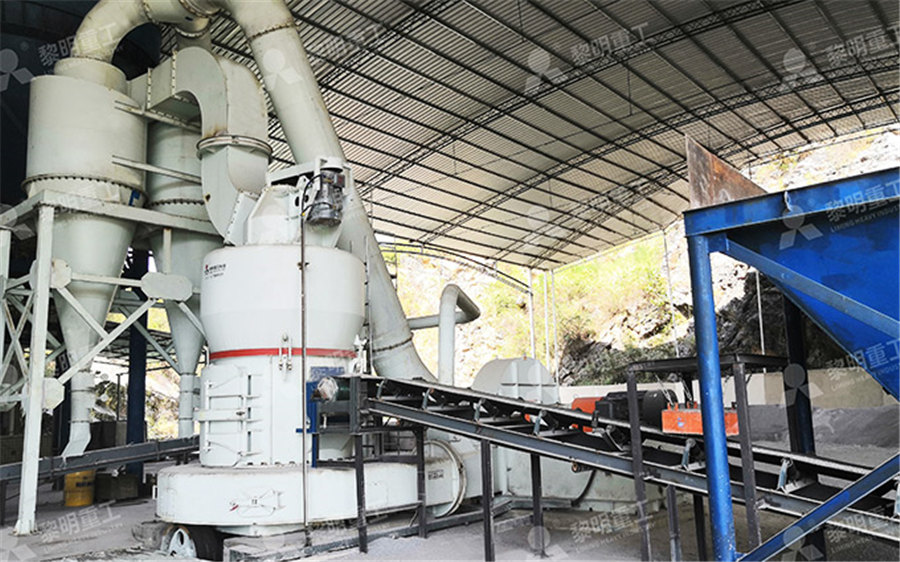
How to Control a SAG Grinding Mill Circuit 911Metallurgist
2017年8月5日 Measurement and control of the rate of addition of new feed and water to the primary mill is relatively easy Instrumentation is simple, accurate and reliable If the primary mill is run in open circuit, the only additional information the operator needs to properly control this circuit is the particle size distribution in the mill dischargeEffect of ball and feed particle size distribution on the milling efficiency of a ball mill: An attainable region approach N Hlabangana a, G Danha b, *, E Muzenda b a Department of Chemical Engineering, National University of Science and Technology, P O Box AC 939, Ascot Bulawayo, Zimbabwe b Department of Chemical, Materials and Metallurgical Engineering, College of Effect of ball and feed particle size distribution on the milling The shape of crushed ore affects the product particle size in a ball mill grinding circuit It has also been proposed that green pellet quality is directly related to the amount of fine particles in a pelletizing plant (Dwarapudi et al, 2008; Umadevi et al, 2008; Gul et al, 2014; Van der Meer, 2015) Particle size distributionInvestigation on the particle size and shape of iron ore pellet feed 2017年3月4日 Size control is th e / Hammer mill we propose a method for tracking the ore particle size distribution on the conveyor based on the UNet neural network that was trained on the dataset SIZE REDUCTION BY CRUSHING METHODS ResearchGate
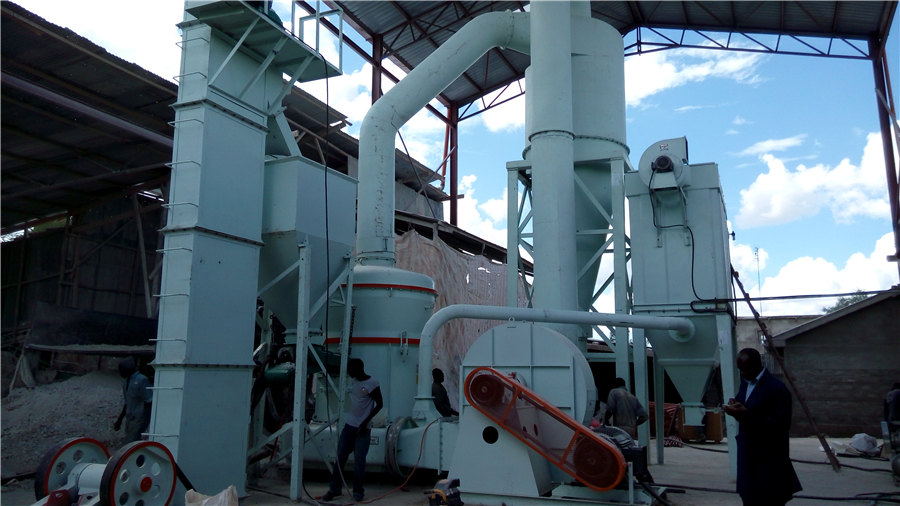
Controlling Particle Size through Agglomeration FEECO
Image: Synthetic gypsum pellets that have been processed with a pin mixerdisc pelletizer combination setup MicroPelletizing Category: Tumble Growth/NonPressure/Agitation Agglomeration Process: Wet Equipment Used: Pin Mixer, Pug Mill Micropelletizing is a process similar to pelletizing, but with a focus on producing agglomerates in the range of 70 mesh to 2024年4月26日 The crushed ore obtained from the crushing stage is typically in larger size fractions and needs to be further processed through screening 2 Screening Screening is the process of separating the crushed ore into various Iron Ore Processing: From Extraction to Manufacturing2021年1月19日 Moisture of bulk material has a significant impact on energetic efficiency of dry grinding, resultant particle size distribution and particle shape, and conditions of powder transport As a consequence, moisture needs to be MeasurementBased Modelling of Material 2023年6月1日 The process control mainly includes ore feeding, grinding density, mill load, level in sump, cyclone feeding density and pressure force, cyclone overflow density and particle size, and so forth Grinding and classification process is a dynamic circulation system with complex mechanismMeasurement and Control for Ore Grinding and Classification
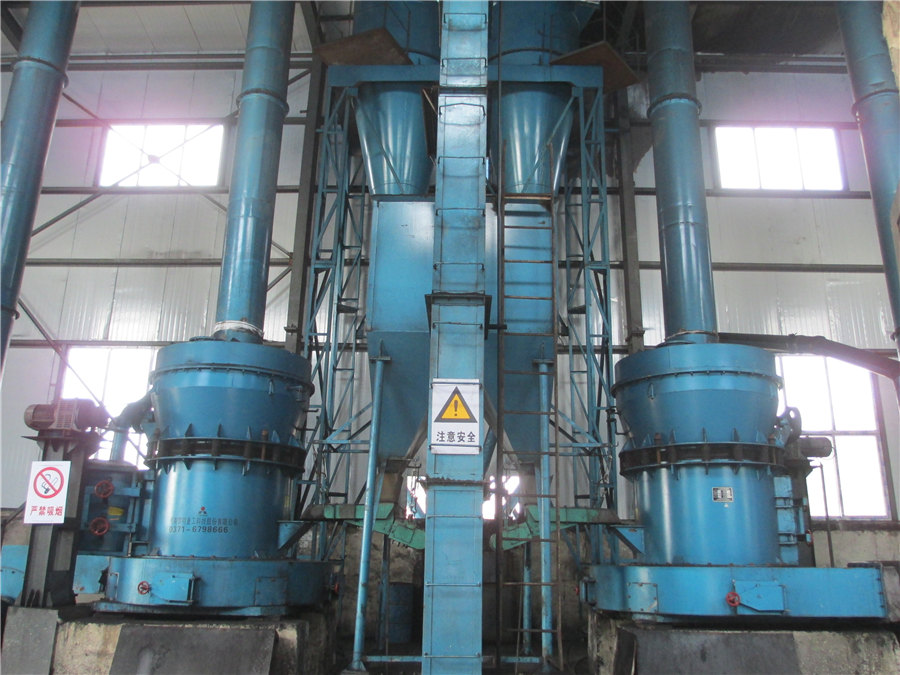
Analysis and validation of a runofmine ore grinding mill circuit
2013年4月1日 A simple and novel nonlinear model of a runofmine ore grinding mill circuit, developed for process control and estimation purposes, is validated3 Size reduction of ores is normally done in order to liberate the value minerals from the host rock This means that we must reach the liberation size, normally in the interval 100 – 10 micron SIZE REDUCTION BY CRUSHING METHODS By ResearchGateCrushing, a form of comminution, one of the unit operations of mineral processing Mineral processing is the process of separating commercially valuable minerals from their ores in the field of extractive metallurgy [1] Depending on the processes used in each instance, it is often referred to as ore dressing or ore milling Beneficiation is any process that improves (benefits) the Mineral processing Wikipedia2019年1月1日 Feeder, mill and cyclone parameters Parameter Value Description αf 0055 Fraction fines in the feed ore αr 0465 Fraction rock in the feed ore αP 10 Fractional power reduction per fractional reduction from maximum mill speed αφf 001 Fractional change in kW/fines produced per change in fractional filling of mill αspeed 071 Fraction of critical mill Feed Size Distribution Feedforward Control for a Grinding Mill
.jpg)
Supervisory expert control for ball mill grinding circuits
2008年4月1日 These control methods involve decentralized PID control and multivariable predictive control of particle size and circulating load (Pomerleau, Hodouin, Desbiens, Gagnon, 2000), adaptive control of particle size (Najim, Hodouin, Desbiens, 1995), model predictive control of particle size and circulating load (Ramasamy, Narayanan, Rao, 2005) and 2008年1月1日 The ground ore in the mill the problems that arise here are obtaining representative sample from the bulk and finding a rapid method of particle size Particle size control in Robust Nonlinear Model Predictive Control of a RunofMine Ore 2010年9月1日 The assessment indicated increase of around 18% in the ore feed rate, while variation in the particle size distribution was reduced, as a result of the formulated fuzzyMPC control scheme Grinding circuit modeling and simulation of particle size control 2013年9月9日 The optimum particle size is of utmost importance when considering inhalers Tiny particles may be expelled from the bronchioles along with air without causing any noticeable impact, whereas much METHODS OF SIZE REDUCTION AND FACTORS AFFECTING SIZE
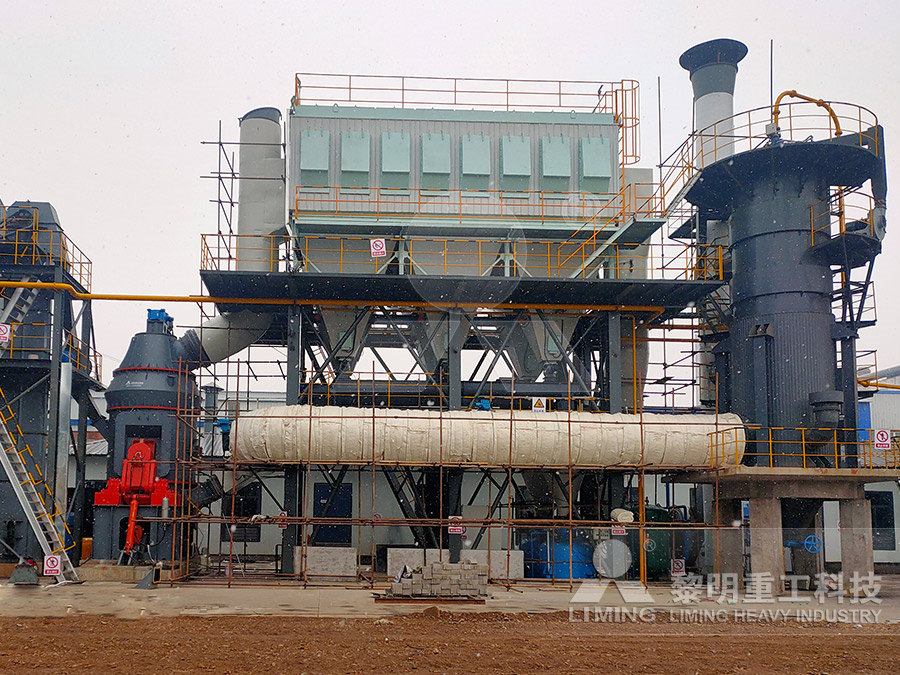
Research on prediction model of ore grinding particle size distribution
2019年3月28日 In the ball mill, the main grinding method was the impact of the steel ball medium with the finer ore particles, and the Ecs was high because the weight of the single steel ball was significantly Mineral Processing Errol G Kelly, in Encyclopedia of Physical Science and Technology (Third Edition), 2003 IIA Fracture Mechanics Ore particles are normally heterogeneous, polycrystalline materials, and under most conditions behave as brittle materials; that is, until fracture occurs, any strain (deformation) induced is proportional to the applied stressOre Particle an overview ScienceDirect Topicsefficient processing and better control of particle shape and range of size “Nanometer level” refers to particles smaller than 1 micron (1 micron = 1,000 nanometers) The average nano size is 200500 nanometers These particle size ranges are often achieved using media milling or jet milling NANOMILLINGMILLING METHODS COMPARISON GUIDE Custom Processing Figure 1: Nonlinear model predictive control stockpiles as ore feed and whether a secondary grinding stage is used or not In [16] and [17] the mill speed is used as an additional MV to reduce mill power consumption, and to independently control quality and throughput One of the most common advanced process control methods is model Hybrid nonlinear model predictive control of a runofmine ore
.jpg)
Intro to Size Reduction Schutte Hammermill
finished particle size is the screen Any material that enters the grinding chamber must be reduced to a size small enough to pass through the screen that covers the mill's discharge opening Because of this the screen size generally provides 70% or more of the control over the finished particle sizeof mill feed size Image analysis methods were used to quantify the effect of feed size on mill throughput and showed the inpit crushers to be an integral step in the preparation of feed to the AG/SAG mills In the case of Highland Valley, optimal feed size for mill throughput requires a balance between blasting and runofmine crushing WhileThe Importance of Primary Crushing in Mill Feed Size Optimizationgiven in Figure 3, for a 125 mm top size of the ore There is an upwards skewness of the distribution A 3 kg sample of this ore at 125 mm top size would have a relative standard deviation (RSD) of 113 per cent To reduce the RSD to two per cent, the sample mass required would be 95 kg Now reduce the particle size to 2 mm top size; this The Simple Facts about Sampling Gold Ores Progradex2015年11月30日 This method eliminates parts of the valuable particles transform the ore to the mill to record flow rate in the same it is not possible to control particle size reduction ratio(PDF) Effects of Flow Rate, Slurry Solid Content and Feed Size