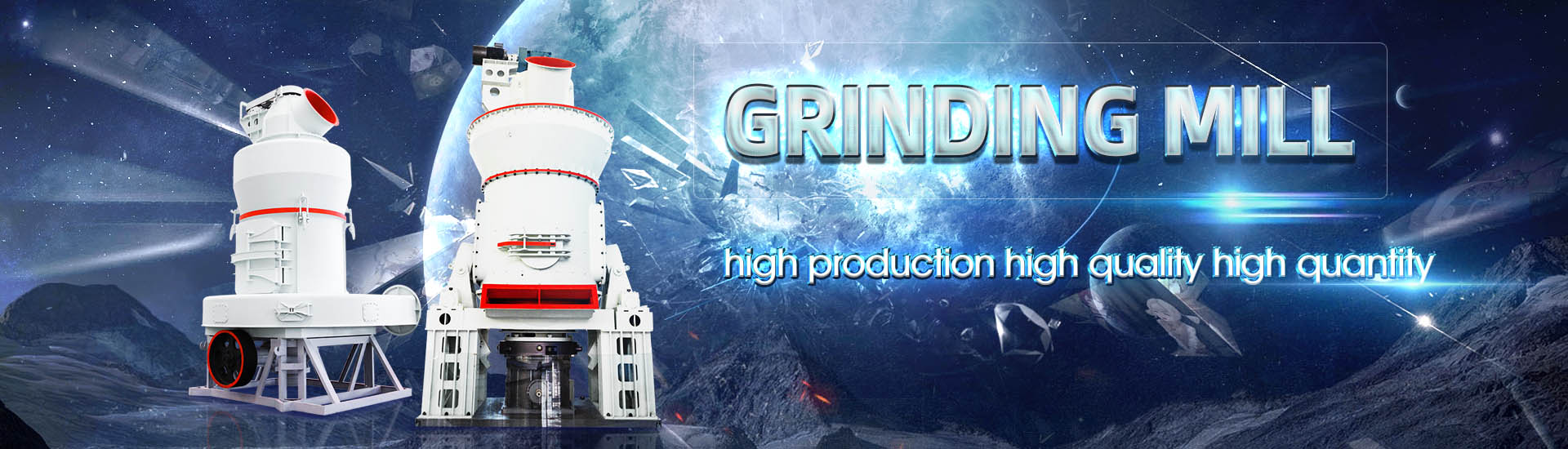
HOME→Grinding mill standard design and manufacturing standard grinding mill standard design and manufacturing standard grinding mill standard design and manufacturing standard
Grinding mill standard design and manufacturing standard grinding mill standard design and manufacturing standard grinding mill standard design and manufacturing standard

How grinding mill design changed over the last 30 years
A wave of grinding mill OEM mergers took place in the 70’s and 80’s During those years, only a handful of OEM’s were competing with one another, and no more than two or three could bid on the large size SAG or ball mills Engineering design offices started spending most of their efforts during those times to merge the 展开Metso Premier™ horizontal grinding mills are customized and optimized grinding solutions built on advanced simulation tools and unmatched expertise A Metso Premier™ horizontal grinding Premier™ Horizontal Grinding Mills Metso2017年2月20日 All Grinding Mill Ball Mill Manufacturers understand the object of the grinding process is a mechanical reduction in size of crushable material 911 Metallurgist is a trusted Grinding Mill Design Ball Mill Manufacturer 911MetallurgistMetso Outotec Select™ horizontal grinding mills classleading performance is the result of careful component selection and design expertise The Select™ horizontal grinding mills are reliable Designed to perform Select™ Horizontal Grinding Mills Metso
.jpg)
A CRITICAL REVIEW OF GRINDING DESIGN PROCEDURES FOR THE
2021年1月8日 There are four main aspects of SAG mill design that will be discussed in this paper The first and most important is the samples that are taken upon which the design is to Ball mill optimisation As grinding accounts for a sizeable share in a cement plant’s power consumption, optimisation of grinding equipment such as ball mills can provide significant cost BALL MILLS Ball mill optimisation Holzinger ConsultingThis document provides guidance on ball mill grinding processes It covers topics such as ball mill design including length to diameter ratios, percent loading, critical speed, and internals Ball Mill Grinding Process HandbookThe paper describes the modeling of a large Ring Motor and the principal results of FEcalculations which such a model, the design goals for a Ring Motor and the evaluation of the Design and dynamic behavior of large Ring Motors for grinding
.jpg)
Grinding Mills 911Metallurgist
Common types of grinding mills include Ball Mills and Rod Mills This includes all rotating mills with heavy grinding media loads This article focuses on ball and rod mills excluding SAG and grinding mills Metso Outotec advances an unrivaled innovation legacy by introducing the Select™ horizontal grinding mills Though the product line is unique, it combines our extensive Designed to perform Select™ horizontal grinding mills Metso2006年1月1日 The relining time also reduced by 375% with the new liners Powell et al, 2006; Rajamani, 2006;Yahyaei et al, 2009;MalekiMoghaddam et al, 2013;MalekiMoghaddam et al, 2015;Cleary and Owen (PDF) Selection and design of mill liners2013年12月22日 The rake angles and the cores of the endmill cutting tools are very important for they control the cutting forces during machining, the strength of the cutting edges, the rigidity of the endmills and the chips removal capability Thus, grinding endmill flutes with accurate rake angles and accurate cores is very crucial in cutting tools’ industry Flutes grinding is normally Fiveaxis rake face grinding of endmills with circulararc generators
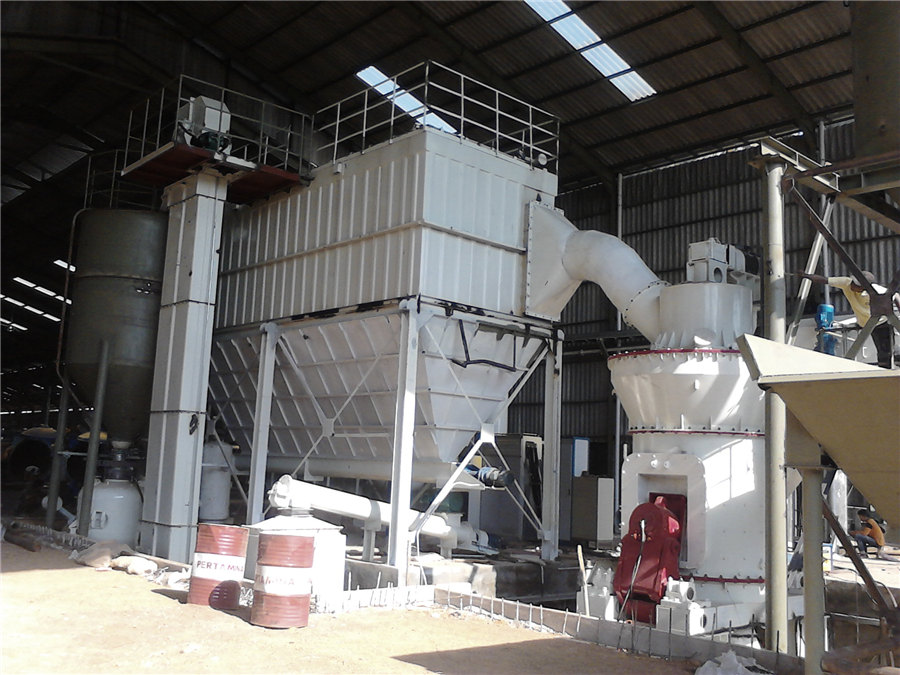
Grinding Mill Computer Model AusIMM
35 Pebble Mill Design This reverts to the Morgärdshammar method and is similar to the AM calculation 36 Tower Mill The tower mill calculation is based on the ball mill design sheet, but is simplified in that the mill design section is omitted A simple tower mill factor of 70% allows the mill power to be estimated MILLCALCv2a 5 19/02/2004Siemens performs electrical and mechanical design of Ring motors in their Dynamowerk factory in Berlin Ring Motor drive a grinding mill without contact between rotating and fixed parts This concept avoids girth gear and pinions, which are used for conventional mill drives The stator of the Ring Motor is wrapped around the mill as a ringDesign and dynamic behavior of large Ring Motors for grinding 2016年6月6日 Grinding Mill Shell Design The majority of these steels are of the 12 Mn standard Hadfield grades The irons used are of two chemistry groups – the NiHard (NiCr) Manufacturing Limitations; Loss of Lifting Profile as Liners Wear; David ; June 6, 2016; 4:21 pm;SAG Mill Liner Design 911Metallurgist2013年8月3日 In Grinding, selecting (calculate) the correct or optimum ball size that allows for the best and optimum/ideal or target grind size to be achieved by your ball mill is an important thing for a Mineral Processing Engineer AKA Metallurgist to do Often, the ball used in ball mills is oversize “just in case” Well, this safety factor can cost you much in recovery and/or mill liner Calculate and Select Ball Mill Ball Size for Optimum Grinding
.jpg)
Mill (grinding) Wikipedia
A mill is a device, often a structure, machine or kitchen appliance, that breaks solid materials into smaller pieces by grinding, crushing, or cutting Such comminution is an important unit operation in many processesThere are many different types of mills and many types of materials processed in them Historically mills were powered by hand or by animals (eg, via a hand crank), 2019年1月3日 Clinker grinding technology is the most energyintensive process in cement manufacturing Traditionally, it was treated as "low on technology" and "high on energy" as grinding circuits use more than 60 per cent of total energy consumed and account for most of the manufacturing cost Since the increasing energy cost started burning the benefits significantly, Clinker grinding technology in cement manufacturingspeed; and in both cases this may be achieved by design by increasing the lifter face angle Traditionally, the number of shell lifters used in a SAG mill is equal to twice the number of the feet in the mill shell diameter (eg, a 34ftdiameter mill shell would have 68 shell lifters) This is also called a 2D shell lining Eliminating someSemiautogenous grinding (SAG) mill liner design and developmentCustomized grinding mill parts including heads, shells, trunnions and liners, main bearings, gears and pinions, Design standard: AGMA 6014 for open gearing Section structure: T or Y design Segments: expanding coverage from Grinding mill spare parts Metso
.jpg)
(PDF) Grinding Media in Ball MillsA Review
2023年4月23日 ment of grinding media which results in collisions is affected by mill design, mill speed, mill filling and grinding media properties[14] The collision impact cause pa rticle breakage due to the Bühler’s horizontal hammer mill is for pregrinding and postgrinding in animal feed production, including pet foods and fish feed, as well as grain milling and other material size reduction processes automation, fans, filters and safety Horizontal Hammer Mill Grinding System Bühler 2017年6月9日 A survey of the literature pertaining to wet grinding of materials to the minus 2micrometer size range indicated that there was no generally accepted method in use; therefore, cursory tests were made to evaluate standard grinding methods and to Attrition Grinding Mill Design 911Metallurgist2022年12月29日 The flute plays an important role in the design process for tools The complexity of the cutting edge is increasing continuously Thus, it is difficult to grind flute precisely and efficiently This paper presents a practical grinding method for the flute of tools It solves the issue of how to grind the flute with the complex edge by standard wheels It is summarized as A novel grinding method for the flute with the complex edge by standard
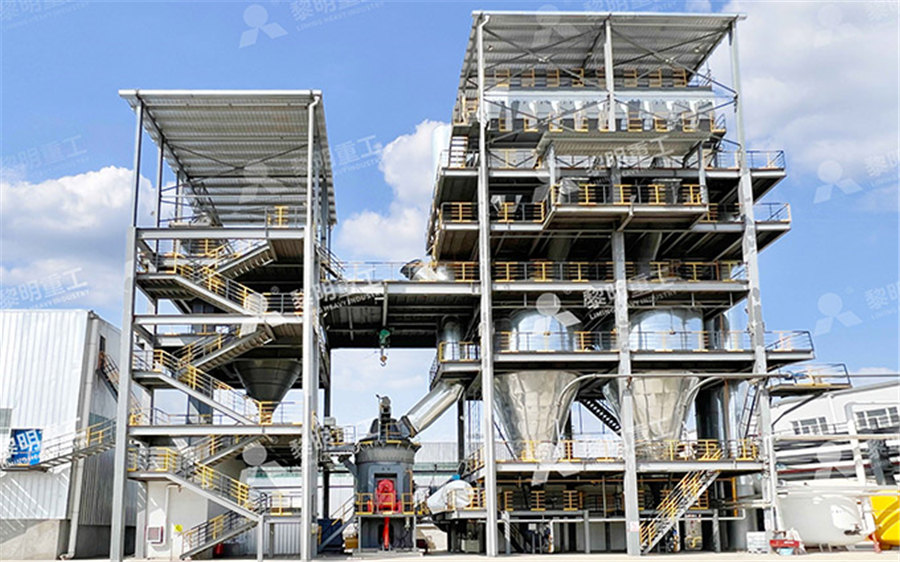
Grinding Mills and Pulverizers Selection Guide: Types, Features
Video credit: shsbjq / CC BYSA 40 Specifications Important specifications when selecting grinding mills and pulverizers include, The size of the mill can range from pilot/lab to production, eg, 35 to 1600 cu ft; Feed size, material, and hardness of feed must be considered; Output size ranges; Mills can handle dry or wet input, or both; Mills operate in batches or continuously2020年6月29日 Grinding, or abrasive machining, once performed on conventional milling machines, lathes and shapers, are now performed on various types of grinding machines Grinding machines have advanced in design, construction, rigidity and application far more in the last decade than any other standard machine tool in the manufacturing industryChapter 17: Grinding Methods and Machines American Machinist2015年6月19日 The basic parameters used in ball mill design (power calculations), rod mill or any tumbling mill sizing are; material to be ground, characteristics, Bond Work Index, bulk density, specific density, desired mill tonnage capacity DTPH, operating % solids or pulp density, feed size as F80 and maximum ‘chunk size’, product size as P80 and maximum and finally the type of Ball Mill Design/Power Calculation 911Metallurgist2007年1月1日 entitled “Standard Calculation Methods for Milling is a size reduction process of grinding grains into [10], sugar production [11], and facility design of flour mill [12] Design Considerations for the Construction and Operation of
.jpg)
Machining 101: What is Grinding? Modern Machine Shop
2021年7月3日 Made in the USA Season 2 Episode 6: Why, and How, Hardinge is Reshoring Machine Tool Production In this episode of Made in the USA, several executives and senior staff at Hardinge give their firstperson account of how they formulated the plan to shift the manufacturing of its milling and turning product lines from its Taiwan plant to its plant in Elmira, 2008年3月1日 Grinding wheels are the abrasive tools used to grind the solid carbide endmill cutters where standard wheels are largely used in manufacturing due to the cost effectivenessEnd mill design and machining via cutting simulationThese advanced simulation tools provide a comprehensive view to not only optimize your Premier™ horizontal grinding mill design, Metso's Standard Control System provides all control functions required for the safe operation of Premier™ Horizontal Grinding Mills Metso2013年1月1日 Coverage includes abrasives and superabrasives, wheel design, dressing technology, machine accuracy and productivity, machine design, highspeed grinding technology, cost optimization, ultra Principles of Modern Grinding Technology
.jpg)
American National Standard Safety Requirements for Grinding
American National Standard B119 from manufacturing, marketing, purchasing, or using products, processes, or procedures not conforming to the standards However, users, distributors, regulatory 6 Design and construction Being a grinding mill OEM supplier, we know inside and out how mills work and how to best design liners to fit your specific conditions Improved safety through mill liner design, installation methods and modern tools Reduced total cost of MillMapper™ is the patented industry standard in mill liner condition monitoring and 3D modelingMill lining solutions for horizontal MillThe second primary function of a liner is to transfer rotary motion of the mill to the grinding media and charge After all, it is the interface between the mill and the grinding charge Although work on the grinding action in mills was published 100 years ago (White 1905 and Davis 1919), the firstThe Selection and Design of Mill Liners 911 Metallurgist2017年4月1日 @article{Habibi2017AGA, title={A Generic and Efficient Approach to Determining Locations and Orientations of Complex Standard and Worn Wheels for Cutter Flute Grinding Using Characteristics of Virtual Grinding Curves}, author={Mohsen Habibi and Zezhong C Chen}, journal={Journal of Manufacturing Science and Engineeringtransactions of The Asme A Generic and Efficient Approach to Determining Locations and
.jpg)
Grinding Machines SpringerLink
2015年1月1日 As grinding machines belong to the class of machines for the material removal with geometrically nondefined cutting edges, those machines can be classified in correlation to the classification of the different process technologies with geometrically nondefined cutting edges as it is given in DIN 8589, parts 11, 12, and 13 (DIN 858911 2003; DIN 858912 2003; 2016年10月5日 1 Introduction Cement is an energyintensive industry in which the grinding circuits use more than 60 % of the total electrical energy consumed and account for most of the manufacturing cost []The requirements for the cement industry in the future are to reduce the use of energy in grinding and the emission of CO 2 from the kilns In recent years, the production EnergyEfficient Technologies in Cement Grinding IntechOpen2018年7月19日 The detailed design procedure for a hammer mill machine is presented The system designed is a modification to the conventional hammer mill with a circular bottom casing and a semicircular screen(PDF) Design, construction and performance evaluation of a The major design feature of the tower mill is a central agitator screw, the only moving machine compo nent in contact with the slurry and steel media, which allows size reduction by attrition This arrangement reduces energy consumption in fine grinding of minerals by 25% to 50% when compared to traditional horizontal ball mills for the same feed and product sizeFlexible, efficient grinding systems – FLS
.jpg)
Optimization of simplified grinding wheel geometry for the
2019年11月14日 A simple geometric and optimal method is adopted for the fiveaxis CNC grinding of the endmill cutters In this research, initially a simplified parametric profile of the grinding wheel is constructed using line segments and circular arcs The equation of the wheel sweptsurface in fiveaxis grinding is derived Then subjected to the flute profile design, the 2021年11月23日 These grinders are used for grinding round and hollow jobs whether the internal surface of this job is completely round, ditched round, or is in taper Small grinding wheels of 3 cm to 5 cm, are used in such grinders 14 Types of Grinding Machines [Working, Diagram2021年7月12日 Over the years, alternative procedures to the Bond grindability test have been proposed aiming to avoid the need for the standard mill or to reduce and simplify the grinding procedure Some of them use the standard mill, while others are based on a nonstandard mill or computation techniques Therefore, papers targeting to propose a better alternative claim to A Review of Alternative Procedures to the Bond Ball Mill Standard 2017年7月20日 Crusher product is typical feed to a ball mill using large diameter balls but not much grinding of 2025 mm ore can be accomplished in an autogenous mill Autogenous plus Pebble Mill are an excellent technique if the ore is uniformly hard and competent but it has not been popular because the porphry copper orebodies do not consistently produce sufficient Autogenous Grinding Semi Autogenous Grinding Circuits
.jpg)
Rod Mills: Efficient Grinding Solutions for Mining
2016年6月1日 The Steel Head Rod Mill (sometimes call a bar mill) gives the ore dressing engineer a very wide choice in grinding design He can easily secure a standard Steel Head Rod Mill suited to his particular problem The successful operation of any grinding unit is largely dependent on the method of removing the ground pulpPAES 216:2004 B53 76 The hammer mill shall be free from manufacturing defects that may be detrimental to its operation 77 Any uncoated metallic surfaces shall be free from rust and shall be painted properly 78 The hammer mill shall be free from sharp edges and surfaces that may injure the operator 79 Belt cover or guard and provisions for belt tightening and adjustments PHILIPPINE AGRICULTURAL ENGINEERING STANDARD PAES 216: The document provides standard operating procedures for a ball mill It lists 18 steps for operating the ball mill, including connecting power, loading materials and grinding media, starting and stopping the mill, and unloading processed materials It also provides important notes on dry and wet grinding operations, as well as specifications for the ball mill such as a capacity of up to Ball Mill: Standard Operating Procedure PDF Mill (Grinding)2022年11月30日 2 Not suitable for lowmelting sticky or plasticlike material due to heat generation in the mill head as a result of mill fouling 3 The mill may be choked if the feed rate is not controlled, leading to damageHammer Mill: components, operating principles, types, uses,
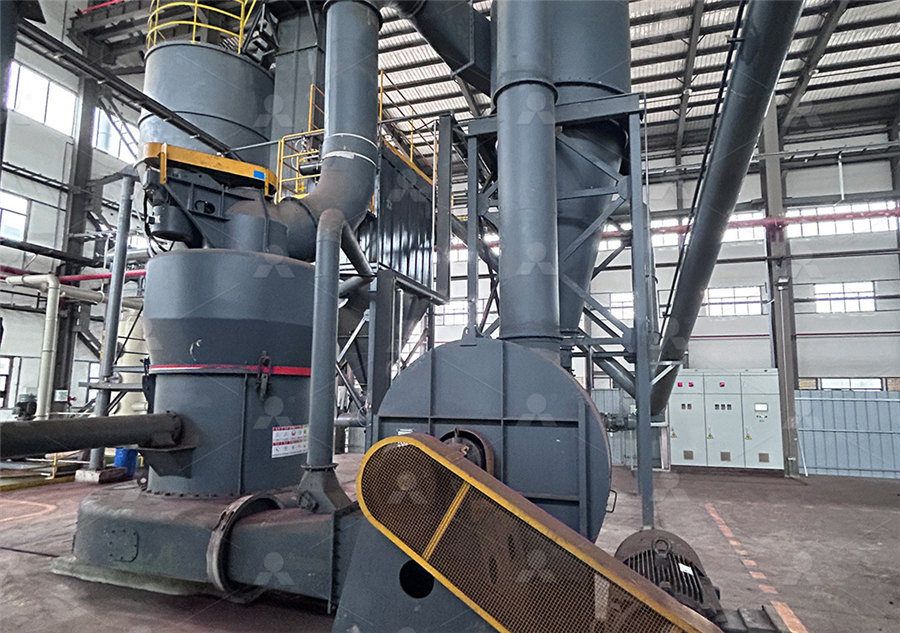
Cement grinding optimisation ScienceDirect
2004年11月1日 Grinding occurs at the beginning and the end of the cement making process Approximately 15 tonnes of raw materials are required to produce 1 tonne of finished cementThe electrical energy consumed in the cement making process is in order of 110 kWh/tonne and about 30% of which is used for the raw materials preparation and about 40% for the final cement