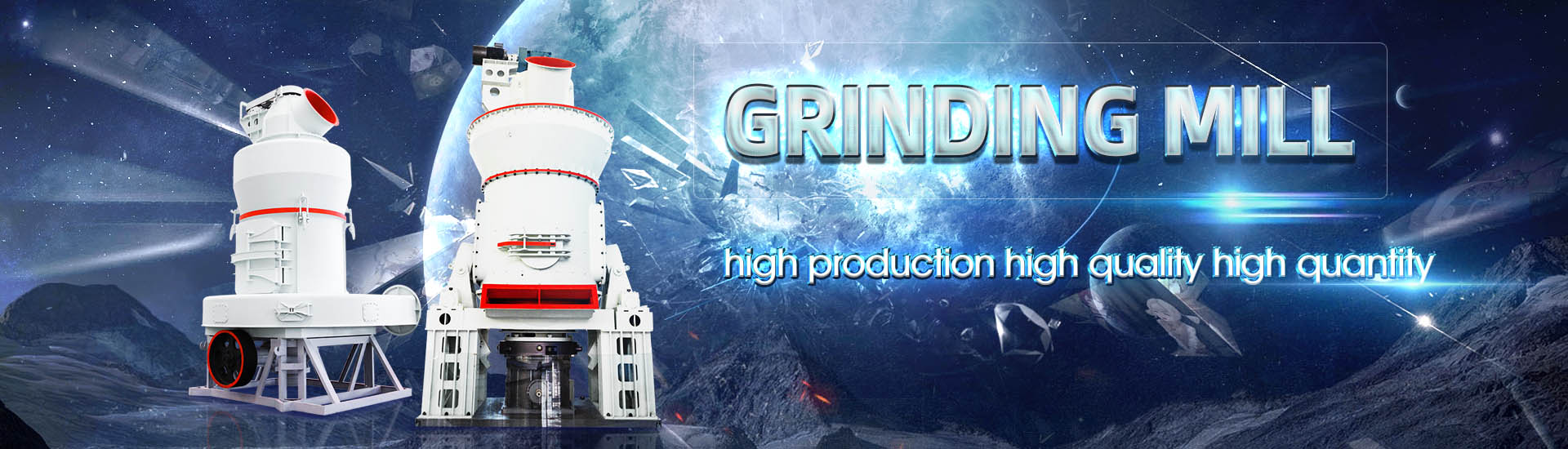
Energysaving space for cement plant grinding equipment
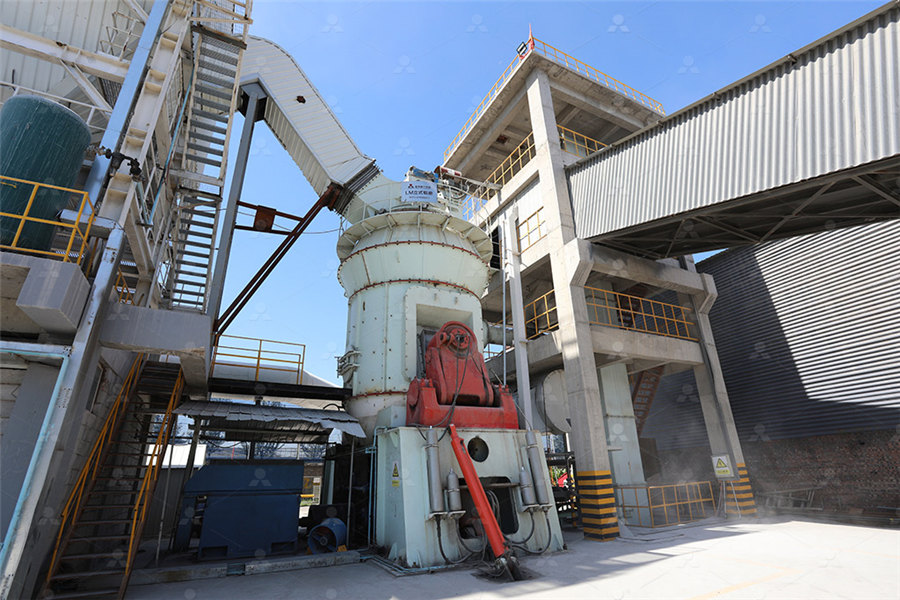
IMPROVING THERMAL AND ELECTRIC ENERGY EFFICIENCY AT
Association of Portland Cement (ABCP), the International Energy Agency (IEA), the Cement Sustainability Initiative (CSI) of the World Business Council for Sustainable Development 2011年5月1日 It has been identified that sizeable amount of energy can be saved and emission can be reduced in raw materials preparation, clinker production, finish grinding, general areas, A critical review on energy use and savings in the cement industries2010年10月1日 Joint grinding system is the preferred cement grinding system of current cement process design, the advantages are high productivity, low energy consumption of system and Applications of Efficient EnergySaving Cement GrindingAs grinding accounts for a sizeable share in a cement plant’s power consumption, optimisation of grinding equipment such as ball mills can provide significant cost and CO 2BALL MILLS Ball mill optimisation Holzinger Consulting

Energy Efficiency Improvement and Cost Saving Opportunities for
We examined over 50 energyefficient technologies and measures and estimated energy savings, carbon dioxide emission savings, investment costs, and operation and maintenance costs for 2016年10月5日 In this chapter an introduction of widely applied energyefficient grinding technologies in cement grinding and description of the operating principles of the related equip‐ ments and comparisons over each other in EnergyEfficient Technologies in Cement GrindingSeveral energy efficient options for cement grinding are available today such as vertical roller mills, roller presses (typically in combination with a ball mill), and clinker pregrinder s with ballOPTIMIZATION OF CEMENT GRINDING OPERATION IN BALL MILLS2015年12月1日 Substantial energy savings have been achieved in recent years, and productrelated emissions of CO 2 and other parameters have also been significantly reduced The Process technology for efficient and sustainable cement production
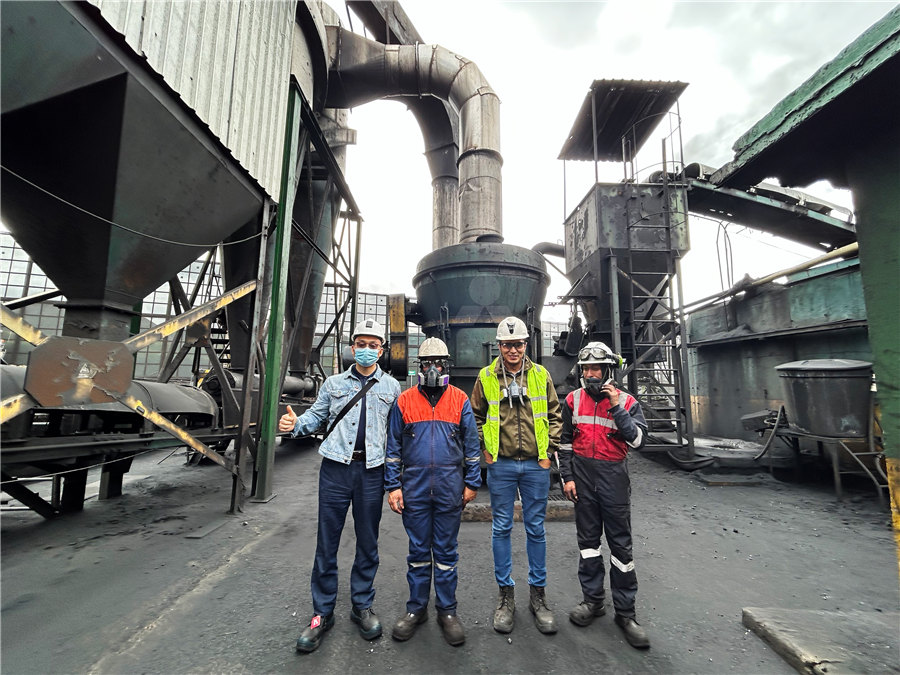
TIPS TO SAVE ENERGY IN CEMENT
Some of the energy efficiency equipment opportunities identified by customers, with a primary Conversion of ball mills to roller mills for both raw materials and finish grinding: energy savings in raw materials preparation can be in the order The replacement of the damper by an ASD was driven by control and maintenance problems at the plant The energy savings may not be materials and, most importantly, for grinding In a typical cement plant, 500700 electric Everything you need to know about Energy Efficiency solution Introduction A modular cement grinding plant is the new trend in the application of cement grinding unitsThe grinding equipment and other related machines are preassembled in separate modules that can be transported in Modular Mobile Cement Grinding Plant Up To Vertical roller mill manufacturers Vertical roller mill or VRM is a largescale grinding equipment designed for pulverizing cement raw meal, cement clinker, slag, coal, fly ash, limestone, and other hard grinding materialIt integrates grinding, drying, separation, and conveying in one machine The equipment is widely used in many industries such as cement, electric power, metallurgy VRM In Cement Plant Maximize Energy Saving CNBMSINOMA
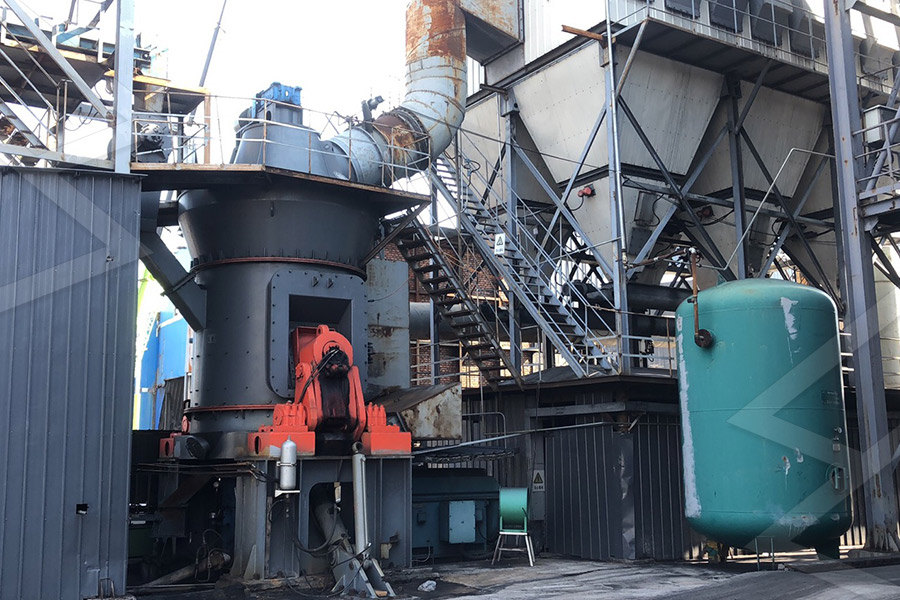
Practical advises to save costs in your Cement plant (complete
Recently, especially from 1980s, grinding system using the vertical roller mill, which has effective grinding performance, is developed and applied in the cement grinding process Descriptions Basic equipment structure of the vertical roller mill for cement grinding is the same as the vertical roller mill of raw material and coal grindingsThe choice between a vertical roller mill and a ball mill for cement grinding ultimately depends on the specific needs and constraints of the cement plant VRMs offer significant energy savings, finer product control, and reduced maintenance costs, making them an attractive option for modern cement plants focused on efficiency and sustainabilityVertical roller mill vs ball mill for cement grinding: Comparison For a grinding plant designed for an output of 80 t of portland cement per hour a roller mill with a grinding bowl diameter of 41 m is required The total power consumption of the grinding plant is 265 kWh/t, cor responding to a 20 % saving in comparison with a plant incorporating a ball millRoller mills INFINITY FOR CEMENT EQUIPMENTBhatty, J, Miller, F and Kosmatka, S 2004 Innovations in Portland cement manufacturing [81] Buzzi, S, Sassone, G, 1993 Optimization of clinker cooler operation [82] Birch E Energy savings in cement kiln systems energy efficiency in the cement industry Elsevier Applied Science; 1990 118–128 [83] Cowi, C 1993An overview of energy savings measures for cement industries
.jpg)
EnergyEfficient Technologies in Cement Grinding
2016年10月5日 In this chapter an introduction of widely applied energyefficient grinding technologies in cement grinding and description of the operating principles of the related equip‐ ments and comparisons over each other in terms of grinding efficiency, specific energy consumption, production capacity and cement quality are given A case study per‐ formed on a Improving Thermal and Electric Energy Efficiency at Cement Plants: International Best Practice iii LIST OF FIGURES Figure 1: Cement Production Process Flow Schematic and Typical Energy Efficiency Measures 2 Figure 2: Rotary Cement Kiln (Dry Process with Cyclonic Preheaters) 4 Figure 3: Schematic Depiction of Control Points and Parameters in a Kiln System Control IMPROVING THERMAL AND ELECTRIC ENERGY EFFICIENCY AT CEMENT The cement factory cost reduction method can be discussed from site selection, cement equipment selection, and cement plant layout, three aspects Skip to raw material preparation, clinker calcination, and cement grinding the 46 Cement Factory Cost Cement Plant Cost AGICO Thermal Energy Saving Opportunities In Cement Plant 61 Lower dispersion box height in riser duct and increase heat transfer in Preheater The Preheater system is one of the major areas for potential reduction in thermal energy Everything you need to know about Thermal Energy
.jpg)
Cement Grinding Unit Cement Grinding Plant
Cement grinding unit is a key link in cement plant To achieve energy saving and consumption reduction in the cement industry, we must proceed from the cement grinding unit Through a series of research and analysis, the following seven Using highefficiency separators in grinding processes helps reduce overgrinding, optimizing particle size distribution and improving overall grinding efficiency This reduces energy consumption in both raw and finished cement production Reference: Energy Efficiency Improvement and Cost Saving Opportunities for Cement Making10 Most Effective EnergySaving Techniques in the Cement The success of the waste heat recovery system prompted the plant to explore additional energysaving opportunities across its operations 7 Challenges and Solutions in Cement Plant Optimization While the benefits of cement plant process optimization are clear, the journey to achieving optimal performance is not without its challengesCement Plant Process Optimization: Unlocking Efficiency and 2 REVIEW FOR ENERGY SAVING IN CEMENT KILN 21 Modeling Balance of Cement Kiln The share of energy consumed in a cement clinker kiln plant attains 7078% of the overall energy consumed in the process of cement production as a whole The residual (2230%) is the share of electrical energy On the other hand,Different Possible Ways for Saving Energy in the Cement
.jpg)
Energy Efficiency Improvement and Cost Saving Opportunities for Cement
PDF On Aug 1, 2013, Ernst Worrell and others published Energy Efficiency Improvement and Cost Saving Opportunities for Cement Making An ENERGY STAR® Guide for Energy and Plant Managers Find Cement grinding process mainly includes the mixed materials crushing, material batching, pregrinding, fine grinding, powder classification, dust collecting, automatic control, and other technologies, making cement production high yield and high quality, in line with the requirements of energysaving and emission reductionCement Grinding Unit Clinker Grinder AGICO CementEnergy Efficiency Improvement and Cost Saving Opportunities for Cement Making An ENERGY STAR® Guide for Energy and Plant Managers August 2013 ENERGY STAR is a US Environmental Protection Agency Program helping organizations and individuals fight climate change through superior energy efficiency Document Number 430R13009Energy Efficiency Improvement and Cost Saving Opportunities for Cement The VSK cement plant is always a good solution for small and medium scale cement manufacturing It features small floor occupation, low capital investment, and easy installation AGICO provides vertical shaft kiln cement plants from 50 TPD to 300 TPD In our plants, we adopt modern vertical shaft kilns, which has a high degree of energysaving and automation, Automatic VSK Cement Plant – Vertical Shaft Kiln Cement Plant
.jpg)
Cement Grinding Units Cement Plant Equipment
All types of cement grinding mills such as cement ball mills, vertical roller mills, roller presses, and various related equipment form a highly efficient production line Closed circuit grinding systems equipped with an OSepa separator are Table 5 EnergyEfficiency Opportunities Applicable to Vertical Shaft Kilns 17 Table 6 Energy Efficiency Measures for Final Grinding of Products in Cement Plants 19 Table 7 Energy Efficiency Measures for Plant Wide Measures in Cement Plants 21 Table 8Energy Efficiency Improvement Opportunities for the Cement 2023年11月1日 The design of the cement grinding system is also focused on “energy saving”, because the cement grinding part accounts for about 45% of the electricity AGICO CEMENT supplies EPC projects for both cement plant 8 Tips For Cement Plant DesignGrinding is a highly energy intensive process in the cement industry Approximately 60 – 70 % of the total electrical energy used in a cement plant is utilised for the grinding of raw materials, coal and clinker Various technological improvements from the conventional ball mills in this area include: High efficiency separators (HES)Modern Processing Techniques to minimize cost in Cement
.jpg)
A critical review on energy use and savings in the cement industries
2011年5月1日 The typical electrical energy consumption of a modern cement plant is about 110–120 kWh per tonne of cement [19] The main thermal energy is used during the burning process, while electrical energy is used for cement grinding [20] Fig 1 shows electrical and thermal energy flow in a cement manufacturing process2019年3月8日 Savings in the Cement Industries,” Renewable and Sustainable Energy Reviews 15, no 4 (2011): 2,042–60 Figure 2 : Rotary Cement Kiln (Dry Process with Cyclonic Preheaters)IMPROVING THERMAL AND ELECTRIC ENERGY EFFICIENCY AT CEMENT Electrical energy accounts for up to 20% of the energy consumption of a cement plant One of the main opportunities for energy saving is the installation of highly efficient systems for transporting raw materials and fuel Highly efficient grinding equipment saves energy without compromising product qualityCement plant modernization ESFC Investment GroupEnergy Efficiency: Our Energysaving Complete Cement Clinker Grinding Station Plant can reduce energy consumption by 15% and increase capacity by 30%, making it an ideal choice for users like "John" who are looking to minimize their operational costsEnergysaving Complete Cement Clinker Grinding Station Plant
[GYQ0R)ZQ]ESS4NJ.jpg)
Energy and cost savings by retrofitting a stateoftheart dry grinding
Cemtec was awarded a contract for the replacement of the dynamic separator in a cement grinding plant in Germany with a modern third generation separator (Cemtec CTC0075) Included in the scope was the dismantling of the old separator, adapting the existing separator building and equipment, and installation of new equipmentModular mobile grinding plant is suitable for small and mediumsized clinker grinding demand Energy savings; Lower deviation risk; Movable solution; Short time to market, AGICO CEMENT supplies EPC projects for both cement plant and single cement plant equipment CONTACT INFO +86 s 19F, Suite B, Modular Mobile Grinding Plant, Portable Grinding Plant Cement Grinding mills are mainly used to grind the clinker and raw materials in the cement plant It is also called cement grinding equipment or cement mill AGICO provides the cement ball mill, rod mill, energysaving, and stable output Grinding Mill Grinding Equipment Cement Mill2018年7月1日 Among the industries, the nonmetallic industry was reported as the third largest energy user and accounted for about 12% of the global energy use [1]Within this portion, cement industry had the majority of the utilization with 85–12% [1], [2]US Energy Information Administration (EIA) [7] named cement industry as the most energy intensive among the Energy and cement quality optimization of a cement grinding circuit
.jpg)
Everything you need to know about clinker/cement
Everything you need to know about clinker/cement Grinding if You read and understand this article , you will be ready to be a cement grinding area manager FEED AND FEED SYSTEM Feed Temperature Plants with satellite coolers Cement Vertical Mill Cement vertical mill is a kind of highefficiency and closedcircuit grinding equipment, which integrates crushing, drying, grinding, and grading functions In recent years, it has been widely used in new dry cement production lines and gradually replaced ball mill as the main cement equipment in large cement plantsIt not only has a high energy utilization rate and 5 Costsaving Tips for Portland Cement Manufacturers2024年4月26日 Grinding and milling account for 58% of cement/concrete energy consumption These operations have an energy efficiency ranging from 6 to 25% and also offer a large opportunity for energy saving The following figure presents the cement production process Cement production processEnergy Efficiency and Saving in the Cement IndustryHowever, electric energy is mainly used to operate both raw materials (33%) and clinker crushing and grinding (38%) equipment Electrical energy 2053 2054 Table 19 Summary of energy savings in finish grinding Energy saving Oktay Z, Hepbasli A Energetic and exergetic assessment of a trass mill process in a cement plant Energy (PDF) A critical review on energy use and savings in the cement
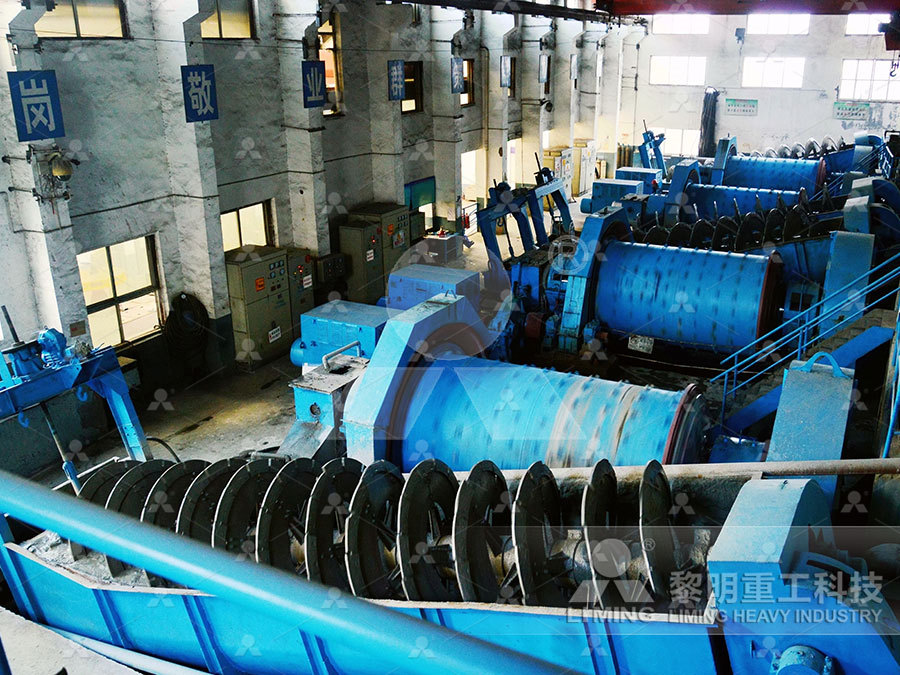
BALL MILLS Ball mill optimisation Holzinger Consulting
As grinding accounts for a sizeable share in a cement plant’s power consumption, optimisation of grinding equipment such as ball mills can provide significant cost and CO 2 emission benefits to the cement producer n by Thomas Holzinger, Holzinger Consulting, Switzerland BALL MILLS 1 FEBRUARY 2021 INTERNATIONAL CEMENT REVIEW T2022年9月19日 Holcim is investing in new energy initiatives at its Mannersdorf cement plant to significantly reduce its carbon footprint The company plans to install a €10 million clinker cooler system, which aims to cut heat consumption and decrease CO2 emissions by 18,000 tonnes annually, with completion expected in early 2025Cement industry is giving a major thrust to energysaving projects2018年4月1日 Cement, as a very basic raw material for infrastructure, consumes high energy during its production process [1][2][3] Note that a large amount of energy was consumed in order to grind cement into Energy and cement quality optimization of a cement grinding 2010年10月1日 Download Citation Applications of Efficient EnergySaving Cement Grinding Technology and Equipment Joint grinding system is the preferred cement grinding system of current cement process Applications of Efficient EnergySaving Cement Grinding