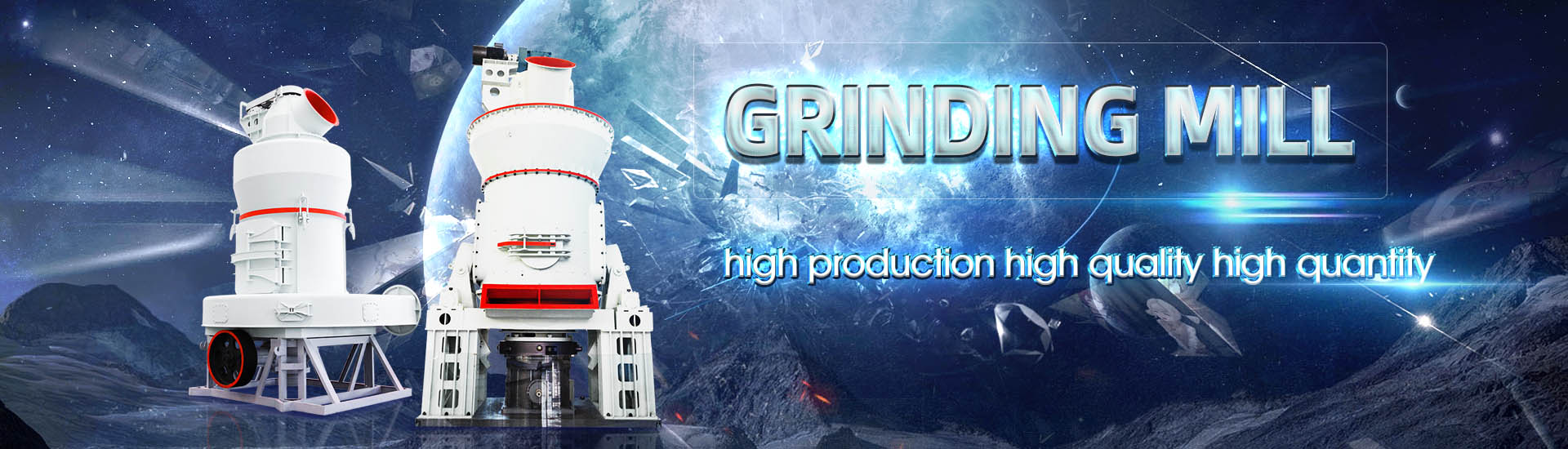
Dry cement raw material mill
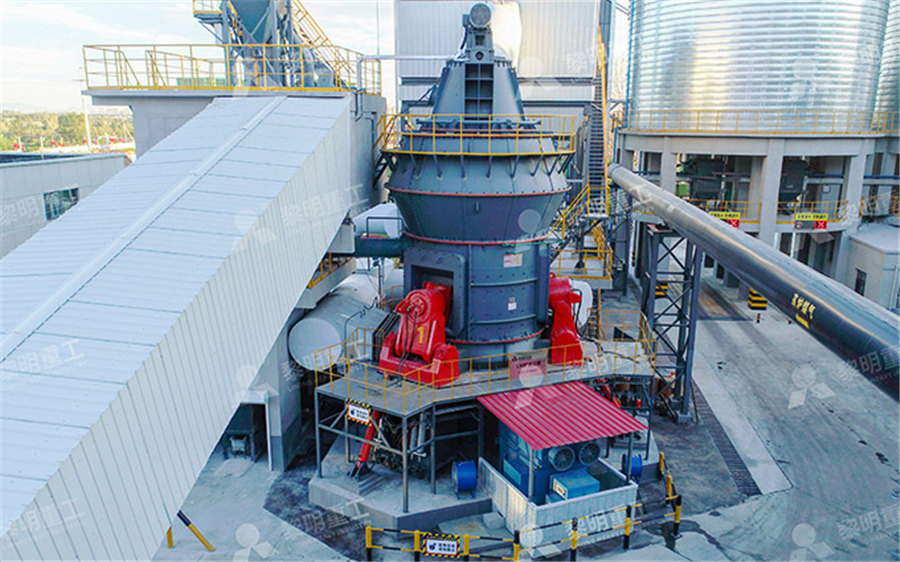
Raw Material DryingGrinding Cement Plant Optimization
Drying of moisture in raw materials is required for effective grinding and subsequent handling of raw meal This is achieved normally by ducting part of the kiln exhaust gas through the mill 2018年2月21日 The ETHammer mill (manufactured by F L Smidth, Copenhagen) is a dryerpulverizer, specially designed for crushing and drying Drying of raw materials INFINITY FOR CEMENT The cement ball mill manufactured by AGICO can complete the drying and grinding of raw materials at the same time After entering the ball mill, materials directly contact with the gas with high temperature, so the heat exchange and Raw Mill – Raw Mill In Cement Plant AGICO Cement For high moisture content of the raw material, the airswept dryinggrinding circuit as shown in Fig 412 is used The raw material is fed into a predrying duct outside the mill for primary drying, so that only predried material enters the Drying of raw materials INFINITY FOR CEMENT
.jpg)
Vertical raw mill Cement Plant
Vertical raw mill is one kind of raw mill, generally used to grind bulk, granular, and powder raw materials into required cement raw meal in the cement manufacturing plantVertical raw mill is an ideal grinding mill that crushing, drying, grinding, Raw mill is generally called cement raw mill, raw mill in cement plant, it refers to a common type of cement equipment in the cement plantIn the cement manufacturing process, raw mill in cement plant grind cement raw materials Raw mill Cement PlantPart Three: Raw Mill Process of Raw Mill The proportioned raw material is feed first to a grinding mill In the mill, particles ground in to very fine sizes In the grinding unit, drying, grinding and mixing takes place simultaneously Hot gas from clinker burning unit is passed into the grinding unit to assist the drying and grinding processCement Manufacturing Process INFINITY FOR CEMENT EQUIPMENT2020年8月25日 Dry process of cement There are two methods to choose, drying and grinding the cement raw materials at the same time; or dry cement raw materials firstly, then grind them into raw meal The raw meal will be sent into cement kiln to calcine clinker The semidry process of cement also belongs to the dry process of cement, add certain water into Cement Production Process Cement Manufacturing Process AGICO CEMENT
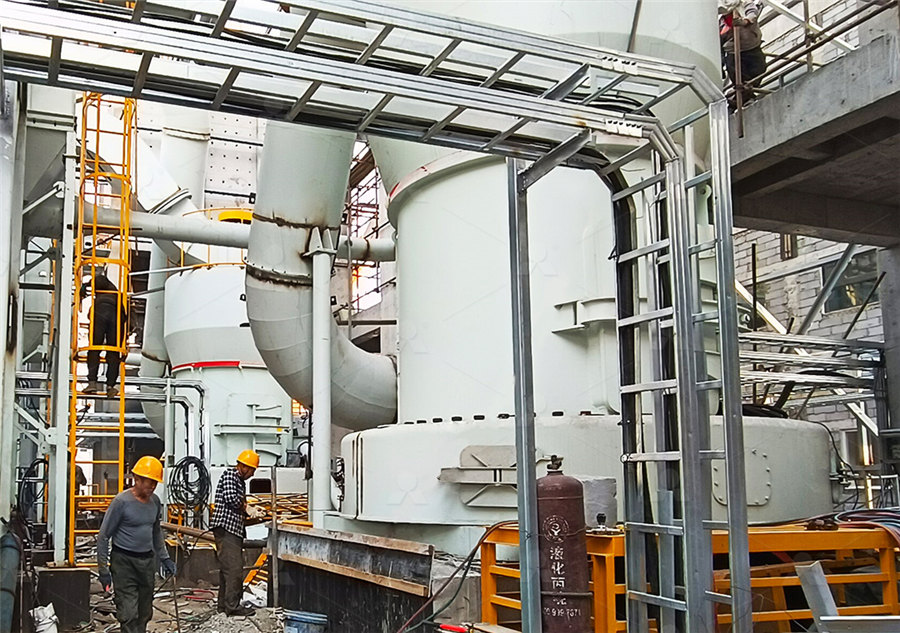
How Does a Raw Mill Work in a Cement Industry
2024年2月23日 Raw mill is generally called cement raw mill, raw mill in cement industry, it refers to a common type of cement equipment in the cement plant Skip to content HOME ABOUT US This grinding system can dry 6% to 7% of the raw AGICO Cement supplies cement equipment for cement raw material production as you need, such as cement mill, cement crusher, onestop turnkey project, welcome to contact! Skip to content +86 Preparation Of Cement Raw Material Cement Mill, Cement The main difference to cement mill operation is the need to dry rawfeed and assure transport of stightly moist materialwithin a mill Blending silos are prone to internal buildup of dead material, particularly if raw meal is wet or aeration defective Periodic (one to two years) Raw milling and blending INFINITY FOR CEMENT EQUIPMENT2024年11月23日 Cement Extraction, Processing, Manufacturing: Raw materials employed in the manufacture of cement are extracted by quarrying in the case of hard rocks such as limestones, slates, and some shales, with the aid of blasting when necessary Some deposits are mined by underground methods Softer rocks such as chalk and clay can be dug directly by Cement Extraction, Processing, Manufacturing Britannica
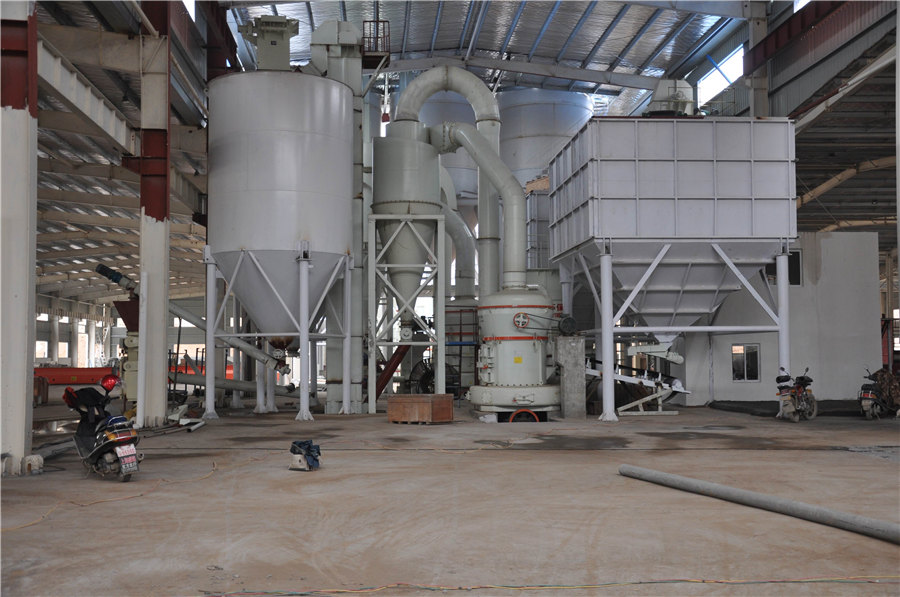
Optimization of A Fully AirSwept Dry Grinding Cement Raw Meal
Optimization of a Fully Airswept Dry Grinding Cement Raw Meal Ball Mill Closed Circuit Capacity With the Aid Free download as PDF File (pdf), Text File (txt) or read online for free This document discusses optimizing the production capacity of a fully airswept industrial scale twocompartment cement ball mill through simulation The mill has two compartments, with the first Mixing and Blending for the manufacturing of cement Dry Process In the dry process of cement manufacturing, workers first mine and crush raw materials such as limestone, clay, and sand, then transport them to a grinding mill StepbyStep Guide to the Manufacturing of Cement2015年4月1日 1 Introduction Airswept raw meal ball mills introduced by the cement mill manufacturers FLSmidth ® (Smidth, 2002), Polysius ® (Polysius, 2002) and KHD Humboldt Wedag® are the most commonly used onesKHD Humboldt Wedag® manufactured fully airswept raw meal mills which have two compartments used for drying and grinding processesOptimization of a fully airswept dry grinding cement raw meal 2015年1月1日 Vertical cement mill (vertical mill) is a machine that plays an important role in the raw meal production process of the newtype dry cement, and it is a set breakage, drying, grinding, transport in one []Raw material grinding process is a vital and energy consumption link in the cement productionModeling Based on the Extreme Learning Machine for Raw Cement Mill
.jpg)
Vertical Roller Mill Operation in Cement Plant
The vertical roller mill (VRM) is a type of grinding machine for raw material processing and cement grinding in the cement manufacturing processIn recent years, the VRM cement mill has been equipped in more and more cement plants around the world because of its features like high energy efficiency, low pollutant generation, small floor area, etc The VRM cement mill has a 2022年9月1日 It is a hardened mixture mixed with essentially the same raw materials (cement, aggregate and supplementary cementitious material) but lower water content as compared to conventional concrete Performance and properties of dry concrete are closely related to the raw materials dosage, preparation technique, curing regimes and curingA comprehensive review on dry concrete: Application, raw material The cement raw material mixtures are ground, dried, and classified in the Pfeiffer vertical roller mill For drying the material, hot gases are directed into the mill Product fineness can be adjusted within a wide range (0063 to 02 mm)Raw mills for all requirements Gebr Pfeifferfor limestone and cement raw material 1937 400 Loesche mills have already been sold for coal, phosphate and cement raw material 1939 The largest Loesche mill at this time is an LM 16 with two steel springloaded rollers, a grinding track diameter of 1,600 mm and product throughput of 22 t/h 1948 The company in Teltow is nationalised; the companyFOR CEMENT RAW MATERIAL
.jpg)
Cement Mill Cement Ball Mill Vertical Cement Mill Factory
In general, cement mill can both apply for dry cement production and wet cement production Commonly, there are three hot types of cement mill in the cement industry: cement ball mill, Raymond mill, and vertical cement mill AGICO Cement can supply cement mill according to Wear rate is the same for raw material and cement Different for slurry grinding (6 times more) This value can change a lot depending on the cement Mill type: cement mill, dry process raw mill, wet process raw mill Diaphragm location: Raw mill: transfer diaphragm at the drying chamber outlet, intermediate, peripheral Everything you need to know about clinker/cement GrindingIn conclusion, the application of VRM technology in both the raw material grinding process and the cement grinding process has revolutionized the cement industry VRMs offer several advantages over traditional grinding mills, including energy efficiency, product consistency, and ecofriendlinessApplication of Vertical Roller Mill in Cement ProductionSINOMALY produces cement raw material grinding mills in various specifications These machines are suitable for grinding mill production lines with an output of 2500t/d, 3200t/d, 4000t/d, 5000t/d, 6000t/d and 8000t/d The vertical grinding Vertical Roller Mill for Cement Raw Material
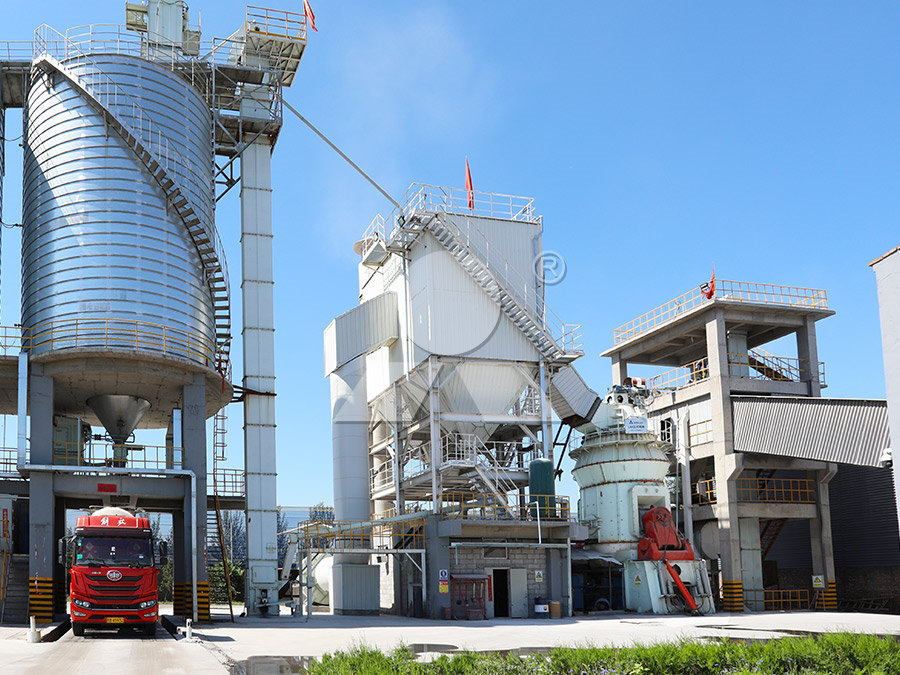
The Cement Plant Operations Handbook International Cement
passivation – 13 Cement quality – 14 Setting time – 15 ASTM cement types and specifications – 16 European EN 197 cement specification – 17 Composite cements (intergrinds and blends) – 18 Supersulphated cement – 19 Calcium aluminate cement (CAC) – 20 Shrinkagecompensating cements (SCC) – 21 ISO 9001:2000 Quality 8Stage of Cement Manufacture There are six main stages of the cement manufacturing process Stage 1: Raw Material Extraction/Quarry The raw cement ingredients needed for cement production are limestone (calcium), sand and clay (silicon, aluminum, iron), shale, fly ash, mill scale, and bauxite The ore rocks are quarried and crushed into smaller pieces of about 6 inchesHow Cement is Made Cement Manufacturing Process2015年4月1日 Request PDF Optimization of a fully airswept dry grinding cement raw meal ball mill closed circuit capacity with the aid of simulation Production capacity of a fully airswept industrial Optimization of a fully airswept dry grinding cement raw meal The OKTM Mill skilfully comminutes raw material, cement and slag It features a patented roller and table design and concrete mill stands instead of traditional, heavy steel structures The OKTM Mill’s flexible design makes it possible to operate it with a number of rollers out of service while still reaching 60 to 70 percent of the normal operation output, minimising production lossesVertical roller mills FLSmidth Cement
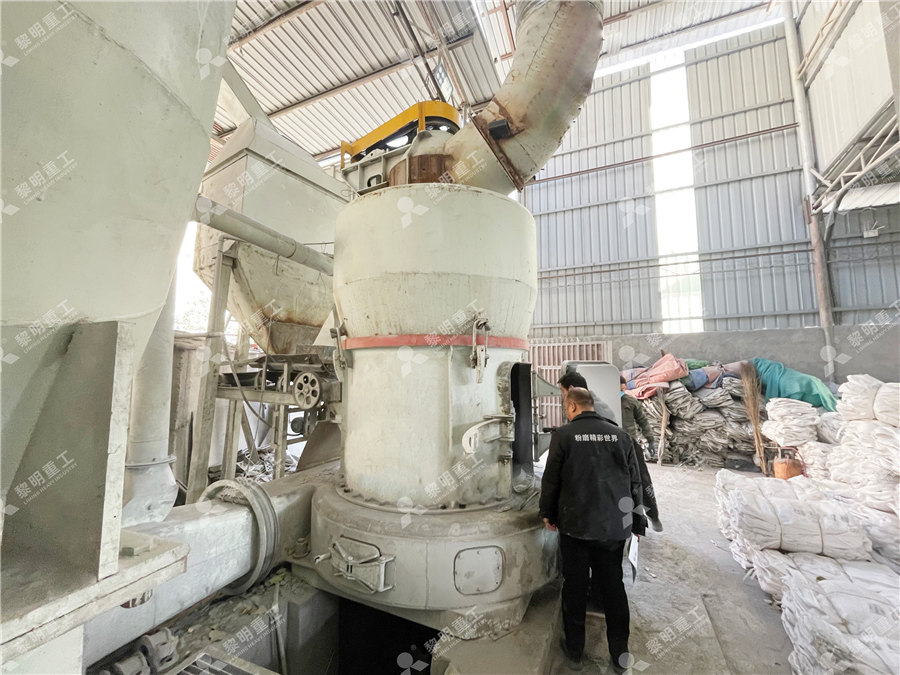
Grinding ball data INFINITY FOR CEMENT EQUIPMENT
Consequently, dry mills need more mill volume than comparable wet mills [69a] In Germany, an excess figure of 10 % is generally considered for dry grinding in contrast to the energy consumption for wet grinding [69b] It is known that cement raw material is much less abrasive than cement clinker2015年4月7日 Following topics are mentioned: Plant scale surveying and analysis of the results Material characterization tests: standard bond work index and drop weight tests Grinding/classification performance analysis of the cement raw material circuit Mathematical modelling of airswept ball mill Mathematical modelling of air classifier used in Optimization of cement raw material ball mill dry grinding: An G Raw material transfer 12 H Raw material grinding/drying 13 I Clinker cooler 14 J Clinker piles 15 K Clinker transfer 16 L Clinker grinding 17 M Cement silos 18 N Cement load out 19 O Raw mill feed belt 24 P Raw mill weigh hopper 25 Q Raw mill air seperator 26 R Finish grinding mill feed belt 27 S Finish grinding mill 116 Portland Cement Manufacturing US Environmental The springloaded roller grinding mill for grinding coal was intro duced by Loesche in the 1920’s Since the end of the 1930’s Loesche mills have also been used for grinding cement raw material The biggest breakthrough in this field of application took place in the 1960’s Soon after this the cement industry expressed the desire to2 µm 5 µm Loesche
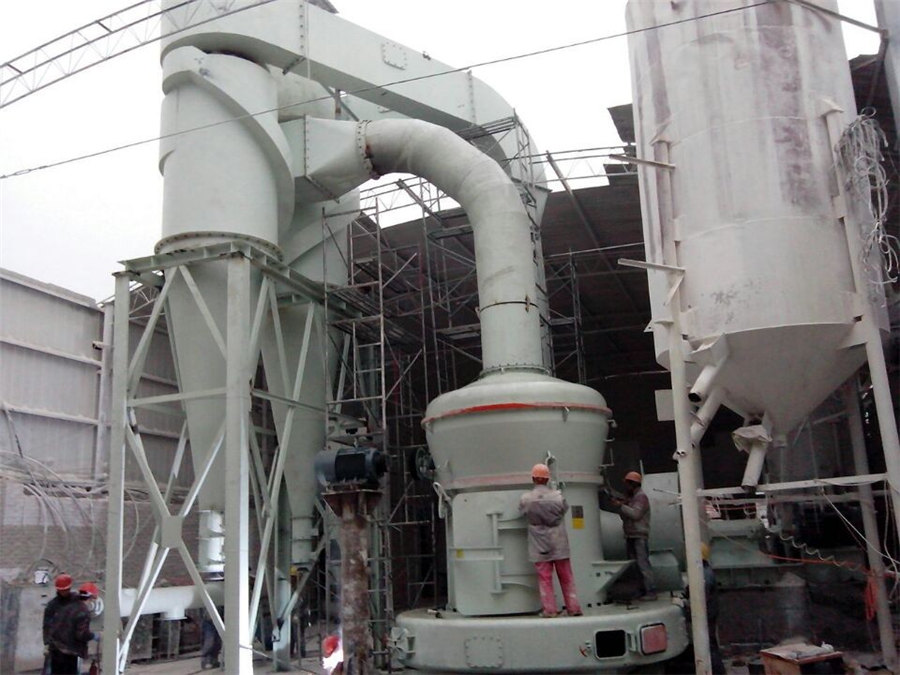
Dry Process Of Cement Production 3005000TPD AGICO CEMENT
At present, cement production mainly uses a new dry cement production method, which is mainly reflected in the raw material has been preheated by the high temperature of the preheater and the high temperature of the exhaust gas before entering the kiln, and nearly 90% of the calcium carbonate in the raw material is decomposed into calcium oxide in the decomposition furnace2021年1月1日 The hot gas and dry fine ground material are fed to the mill outlet to a separator, which separates the fine and coarse The second, called reject, is sent to the mill inlet via an air slide for further grinding so vertical roller mills can also grind the white cement raw material Review on vertical roller mill in cement industry its performance Hot gas generators: These systems introduce hot air or gas into the raw mill to dry materials during the grinding process, improving overall efficiency 32 Optimizing Raw Mill Operations Adjusting operational parameters in the raw Raw Mill Moisture Content Management: A 2023年12月26日 The new type of dryprocess cement production process includes four main sections: Prehomogenization of raw materials, homogenization of raw materials, clinker firing, cement grinding, etc Raw 6 Cement Equipment For Dryprocess Cement
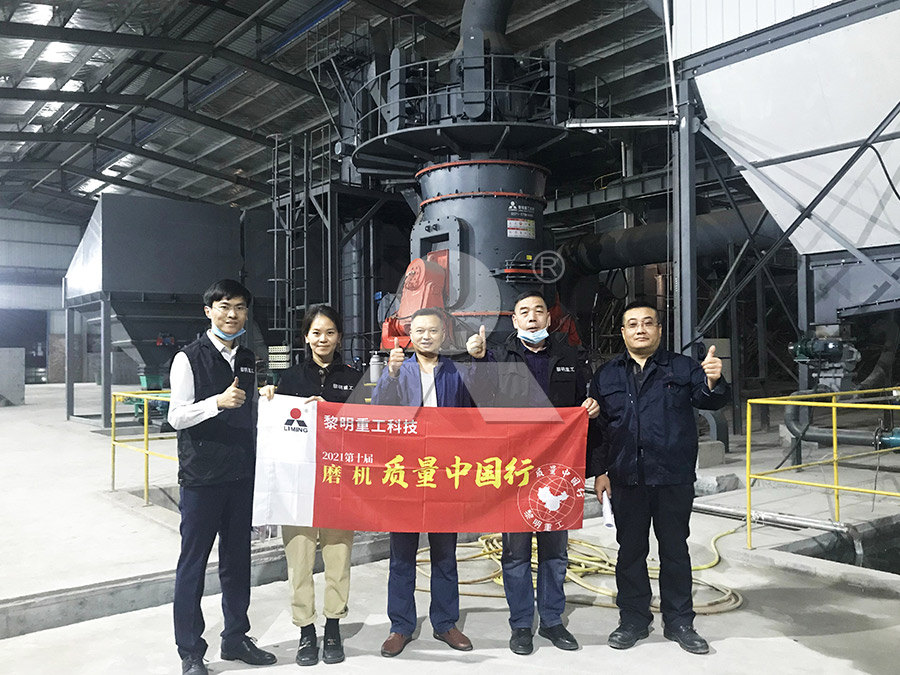
Cement Mill Cement Grinding Machine AGICO Cement Grinding Mill
Raw mill is the grinding equipment applied in the raw material preparation processIn the wet process of cement production, raw materials should be ground into raw slurry with a water content of 30% – 40% While in the dry process of cement production, they will be ground into dry powder in a cement raw mill2016年10月5日 The moisture of the mill feed (cement raw material) can amount to 15–18 % The fineness of the mill product can be adjusted in the range between 94 and 70 % passing 170 mesh Tiggesbaumker P Trends and developments in dry raw material and clinker grinding Ciments, Betons, Platres, Chaux 1982; No 7445/83: 272284 11EnergyEfficient Technologies in Cement Grinding IntechOpenVertical raw material grinding has been widely used in dry process cement plants The raw material preparation system of the 2 500 t/d cement production line can adopt the vertical mill with the disc diameter of 3 400 mm as the main grinding machineRaw Material Preparation in Cement Manufacturing Plant AGICOCement Ball Mills Manufactured By AGICO Cement ball mill: the cement ball mill grinding system produced by AGICO merges drying, grinding, classifying into a single It can both grind the raw material and finished cement product in the cement plant, has the advantages of strong adaptability to materials, continuous production, large crushing ratio, easy to adjust the speed, Dry Process Of Cement Manufacturing Dry Cement AGICO
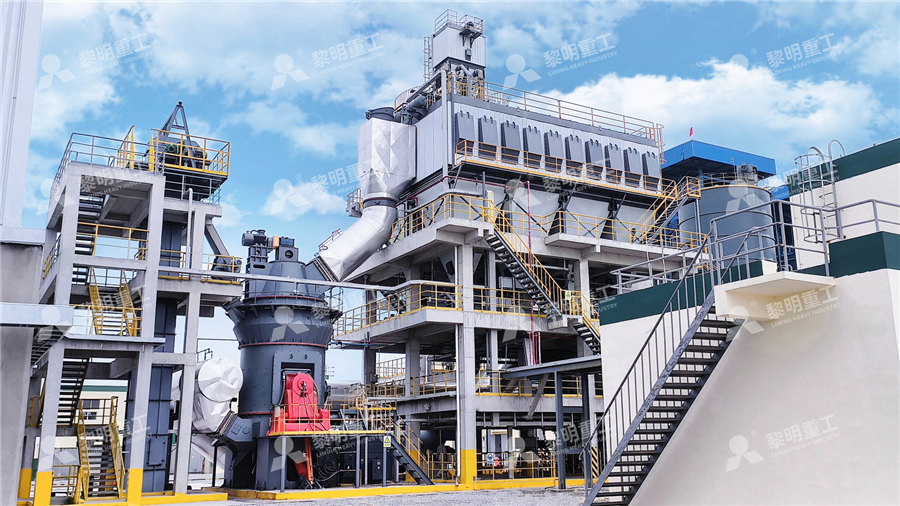
Optimization of cement raw material ball mill dry grinding
2015年4月7日 Following topics are mentioned: Plant scale surveying and analysis of the results Material characterization tests: standard bond work index and drop weight tests Grinding/classification performance analysis of the cement raw material circuit Mathematical modelling of airswept ball mill Mathematical modelling of air classifier used in This agitational method is known to provide high blending efficiency for dry material Brundick, H, “Drying and grinding of extremely moist cement raw materials in the Loesche mill,” ZKG International, No2, 1998, pages 6471Brundick, Horst, and Schäfer, “Raw material control,” World Cement, October 1998, Everything you need to know about cement Materials Preparation and Raw 2015年4月1日 Airswept raw meal ball mills introduced by the cement mill manufacturers FLSmidth ® (Smidth, 2002), Polysius ® (Polysius, 2002) and KHD Humboldt Wedag® are the most commonly used ones KHD Humboldt Wedag® manufactured fully airswept raw meal mills which have two compartments used for drying and grinding processesOptimization of a fully airswept dry grinding cement raw meal