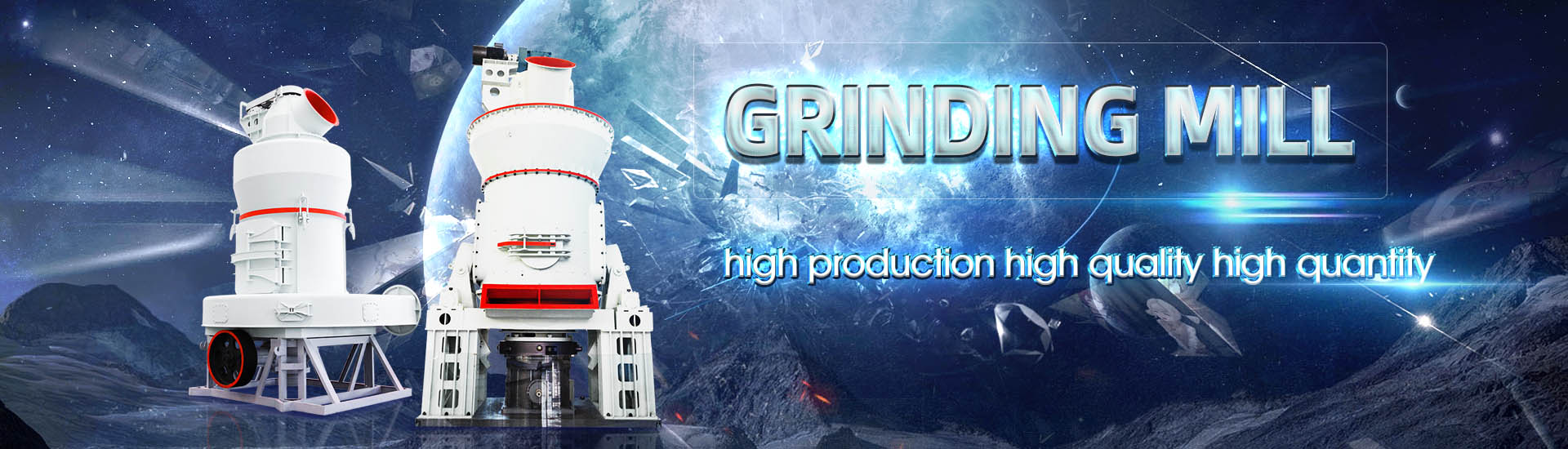
Construction load of ore mill
.jpg)
SAG Mill Design and Benchmarking Using Trends in the JKTech
This paper presents the structure of the latest version of the JKTech autogenous and semiautogenous (AG/SAG) mill specific energy model, which is an adaptation of that previously proposed by Morrell While Morrell’s model is wellknown, historical publications have not 2016年3月21日 Example: A mill in closed circuit with a classifier receives 300 dry tons of crude ore per day, and the percentages of solid are respectively 25, 50, and 84% in the classifier overflow, feed to classifier, and sand, equivalent Common Basic Formulas for Mineral Processing 2012年6月1日 PDF The paper presents an overview of the current methodology and practice in modeling and control of the grinding process in industrial ball mills Find, read and cite all Grinding in Ball Mills: Modeling and Process Control ResearchGate2023年12月12日 Ball mills are used for the second stage of ore grinding in mining operations by proportioning ore piles Controlling the operating conditions of ball mills is one of the key factors for(PDF) Control of ball mill operation depending on ball
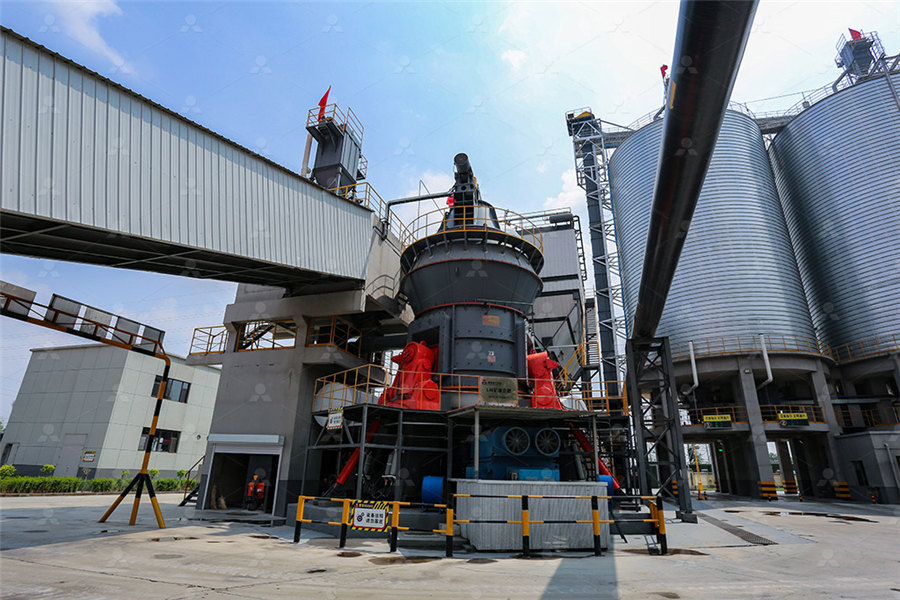
Mechanism characteristic analysis and soft measuring method
2018年11月1日 A mill load is defined as the instantaneous total charge of a ball mill and is composed of a new feed ore, slurry, water, and steel balls inside the mill (Tang et al, 2015a) There are three main steps in designing a good crushing plant: process design, equipment selection, and layout The first two are dictated by production requirements and design Crushing Plant Design and Layout Considerations 911 MetallurgistSpecific energy consumption (SEC) measured in kWh/t is a ratio of the mill drive power to the milling circuit output, without regard to circulating load At the constant size of the cycle feed CALCULATION OF THE REQUIRED SEMIAUTOGENOUS MILL 2023年10月27日 Grinding media play an important role in the comminution of mineral ores in these mills This work reviews the application of balls in mineral processing as a function of the A Review of the Grinding Media in Ball Mills for Mineral Processing
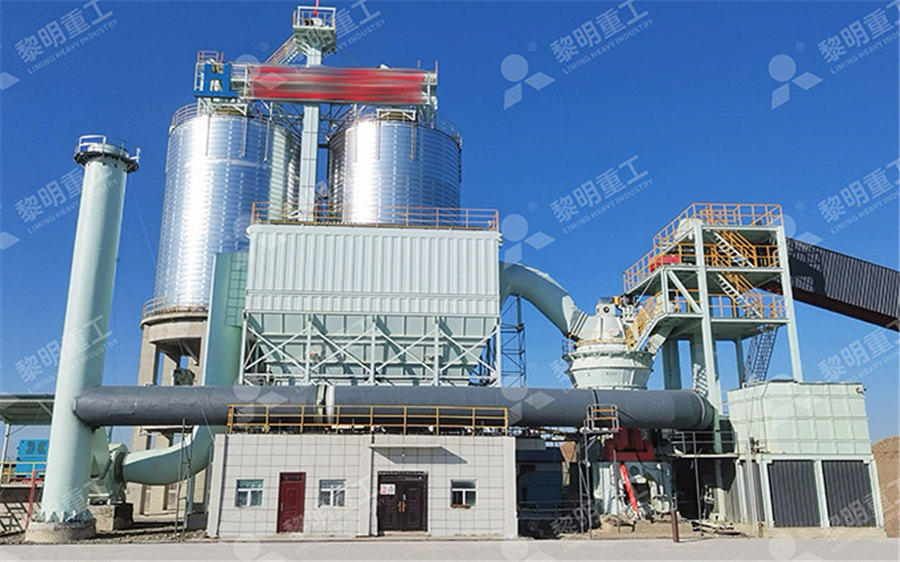
PreProcessing to Increase the Capacity of SAG Mill
2022年6月6日 Ore hardness and size distribution are key factors that dictate the required grinding energy for providing the stipulated product size and throughput for a given installation These two factors, combined with mill dimensions and American Journal of Engineering Research (AJER) 2017 w w w a j e r o r g Page 143 Figure 3; Hammer Mill, Front view Figure 4; Hammer Mill, Top view Figure 5a; Hammer Mill Figure 5b; Hammer Mill III RESULTS AND DISCUSSIONS Table I: Results Obtained from the Calculation S/No PARAMETERS SYMBOL VALUE UNITImprovement on the Design,Construction and Testing of Hammer MillFigure 3(a)—Pilot SAG mill Ecs vs Ball Load, Reproduced from Morrell (2006a); (b) SAG Mill Ecs vs Ball Load for ‘OpenCircuit’ SAG Mills in JKTech Database 0 2 4 6 8 10 12 14 16 18 20 0 2 4 6 8 10 12 14 SAG mill Ecs (kWh/t) Ball load (%) 0 5 10 15 20 SAG mill Ecs (kWh/t) Ball load (%) Coarse feed, uncrushed pebbles Very soft ores, Axb >80SAG Mill Design and Benchmarking Using Trends in the JKTech 2015年2月21日 For example your ball mill is in closed circuit with a set of cyclones The grinding mill receives crushed ore feed The pulp densities around your cyclone are sampled and known over an 8hour shift, allowing to Circulating Load Calculation Formula 911Metallurgist
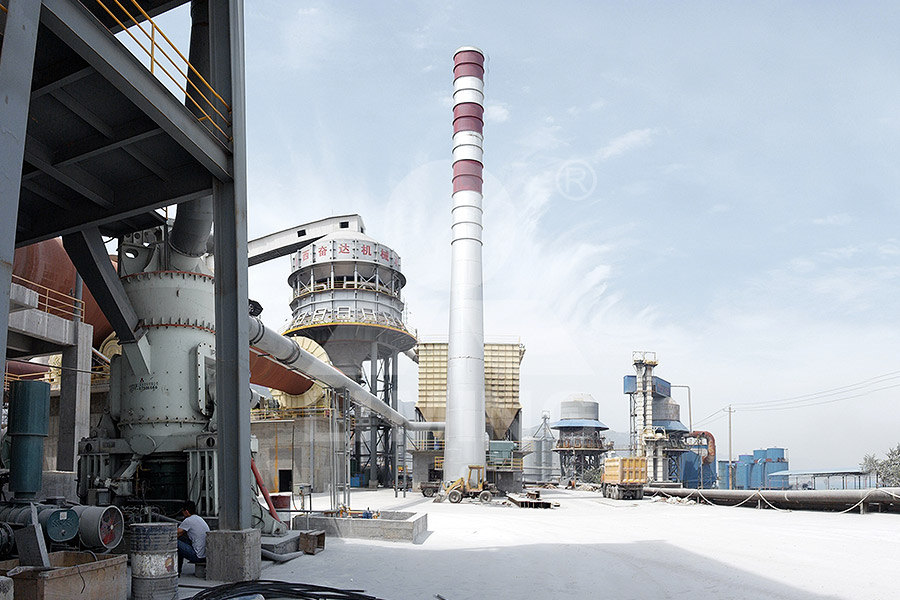
Understanding the SAG Mill in Copper Ore Mining Process
The rod mill is another type of grinding mill used in the copper ore mining process This machine uses steel rods as the grinding media instead of balls, which are commonly used in ball mills The rods grind the ore by tumbling within the mill, similar to the action of a rotating drumSize, hardness and density of ore particles according to M M Protodiakonov scale It is a system that can measure ore content on 4 inputs and includes realtime measurement of pulp density The rate at which fresh ore from the belt conveyor enters the mill From the electromagnetic measurement of the consumption water coming to the millControl of ball mill operation depending on ball load and ore VRM and ball mill circulating load Page 1 of 1 Sep 07, 2011 Re: VRM and ball mill circulating load Mainly in USA, the term circulating load is more often used than the circulation load is percentage of coarse return in relation to fines it can be calculated by : Coarse return TPH X 100 / Mill output range of cirulating load in a conventional close circuit ball mill is around %circulating load formula in ball mill Sebocom ConstructionStudy with Quizlet and memorize flashcards containing terms like Heavy timber, and its subcategory of construction, had its origins in medieval England, Mill construction fell out of favor around WWI with the arrival of , In mill construction, exterior loadbearing and nonloadbearing walls are , usually either brick or stone and moreBuilding Construction Ch 8 Heavy Timber and Mill Construction
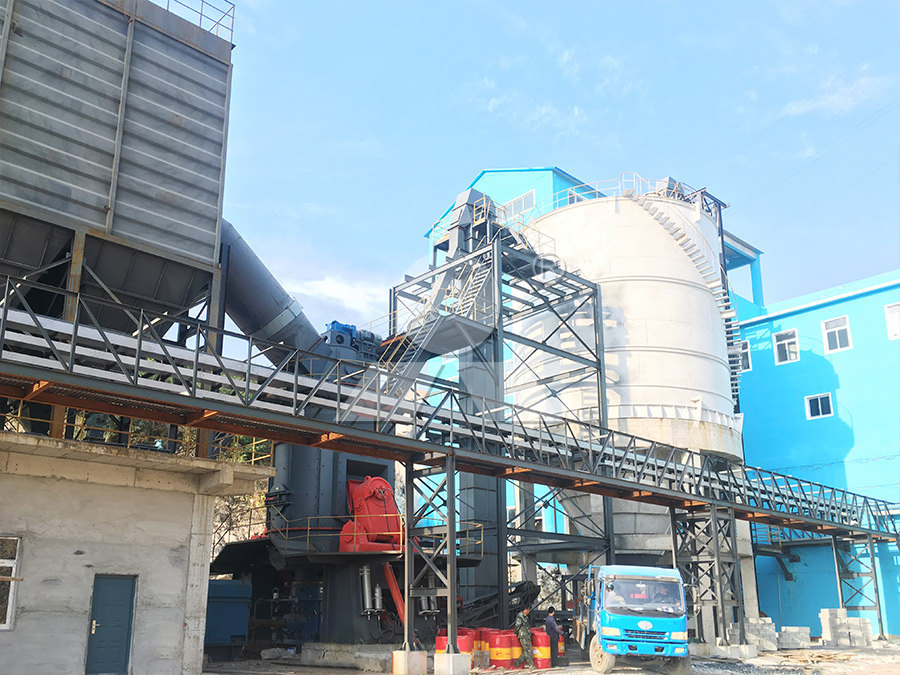
Construction of a SAG mill with the stator and the rotor
Fig 1 shows the construction of a SAG mill [2] It consists of a rotating hollow cylinder of about 12 m in diameter Two sets of bearings in ringshaped structures support the cylinder to let it Since for the ball mill design we are using 80% passing, the required value of C2 for the ball mill will be equal to120 C3 is the correction factor for mill diameter and is given as; 𝐶𝐶3 = 244 𝐷𝐷 02 (3) However, it is important to note that C3 =0914 vessel used in producing the ball mill was got from aDesign, Construction and Performance Analysis of a 5 KgLaboratory Ball Mill2018年6月29日 The SAG milling of ores with markedly variable grinding rates presents definite process control challenges Decisions must be made regarding the selection of the most appropriate combination of mill volumetric load level, percent solids, and mill speed for the combination of ore types being processed at the moment Circuit DescriptionEffect of Mill Volumetric Load Level % Solids Speed on SAG Mill 2022年10月8日 Hammer mill is used in the Pharmaceuticals, Food beverage, and Cosmetic industries to Reduce material particle size Working Principle: The principle of the Hammer mill is based on the Impact between a rapidly moving Hammer Mill; Usage, Construction, Working
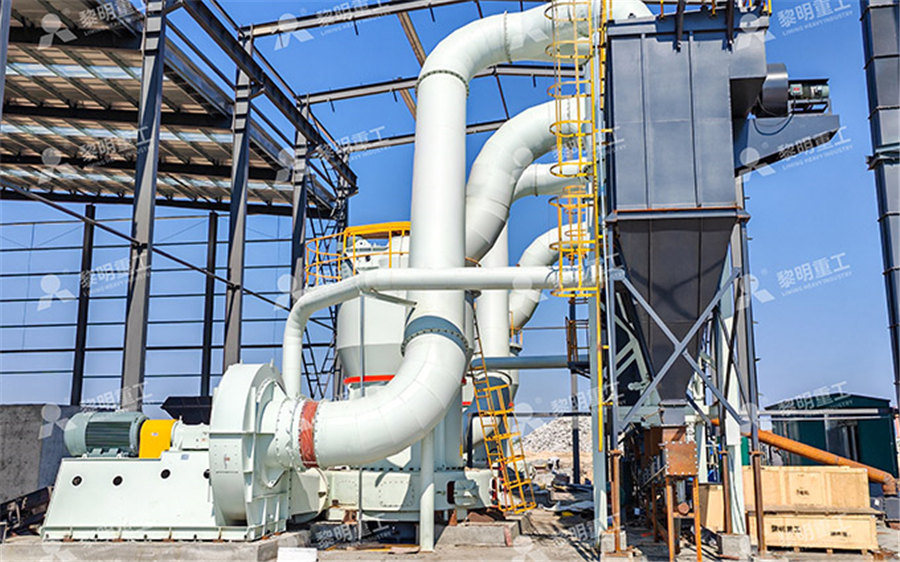
AISE TR 13 Guide For The Design and Construction
AISE TR 13 Guide for the Design and Construction of Mill Buildings 2003 Free download as PDF File (pdf), Text File (txt) or read online for free Scribd is the world's largest social reading and publishing site2015年6月19日 The basic parameters used in ball mill design (power calculations), rod mill or any tumbling mill sizing are; material to be ground, characteristics, Bond Work Index, bulk density, specific density, desired mill Ball Mill Design/Power Calculation 911Metallurgist2016年2月1日 The purpose of this study is to understand how ore loss and dilution affect the mine call factor, with the aim of subsequently improving the quality of ore mined and fed to the millMonitoring ore loss and dilution for minetomill integration in overflow and circulation load to ball mill are the two key indexes for grinding process Grinding particle size represents the quality index of ball mill grinding production, and circulation load indicates the grinding throughput index Only when the two indexes are controlled within their required ranges, will the grinding process operate Intelligent optimal control system for ball mill grinding process
.jpg)
Choosing the Right Grinding Mill: SAG Mill vs Ball Mill JXSC
2024年7月2日 Sag Mill is a kind of heavy duty equipment used in the ore crushing and grinding industry Its working principle is to utilize the impact and grinding effect of a small amount of steel balls and the material itself to crush the ore Through the rotation of the cylinder, large pieces of ore are gradually broken into smaller particles in the collision between the steel balls and the 5 Construction, Working and Maintenance of Crushers for Crushing Bulk Materials practicalmaintenance In a nonreversible hammer mill with screen bars, shown in above figure, material is broken first by impact between hammers and breaker plates and then by a scrubbing action (shear and attrition) of material against screen barsConstruction, Working and Maintenance of Crushers for Crushing 2023年4月23日 Comminution is a very important and resultdetermining step in mineral processing This is because further downstream processes in the beneficiation chain depend entirely on it(PDF) Grinding Media in Ball MillsA Review ResearchGateOre Characteristics Ore characteristics are a critical element in both crusher selection and plant design Dry ores require greater provisions for dust suppression and collection, including dust enclosures around screens, sealing on conveyor skirts, and vacuum and washdown systems Wet, sticky ores canCrushing Plant Design and Layout Considerations 911 Metallurgist
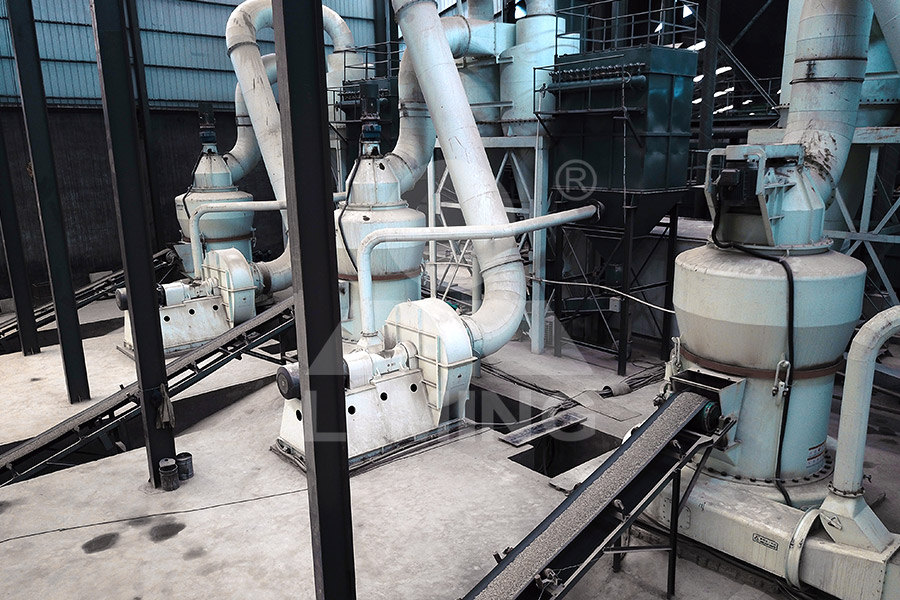
Chapter 8 Heavy Timber and Mill Construction Flashcards
Study with Quizlet and memorize flashcards containing terms like Heavy timber and its subcategory of construction, had its origins in medieval England "Half Timber" homes utilized exposed large dimension, hand hewn structural members connected with mortise and tenon joints, exterior walls feature the exposed wood members, with brick or plaster filling the The operation treats the PGM bearing UG2 ore type and produces a final concentrate enriched with PGM’s The concept was to treat the finer silicate rich fraction in the IsaMill and the coarser chromite rich fraction through the ball mill This 22 Mill load behaviour Optimisation of an industrial scale ball mill using an online pulp 2018年4月17日 Mill Sizing: After laboratory and pilot plant testing confirm the feasibility of autogenous or semiautogenous grinding, it can be used to establish the exact grinding circuit and mill sizeIn the pilot plant tests, the tare power of the pilot plant mills should be determined before and after each test run The tare power should be for the empty millAutogenous and SAG SemiAutogenous Mill Design Calculationsthe required SAG comminution of test ore material Specific energy consumption (SEC) measured in kWh/t is a ratio of the mill drive power to the milling circuit output, without regard to circulating load At the constant size of the cycle feed and discharge, SEC is a prime characteristic of material grindability in a certain ore pretreatment CALCULATION OF THE REQUIRED SEMIAUTOGENOUS MILL
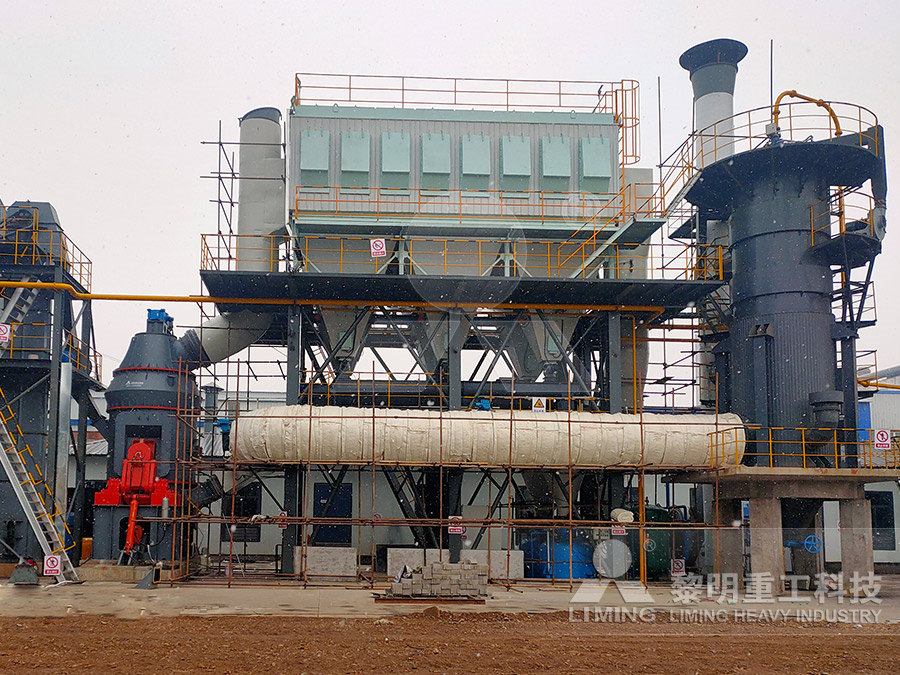
Estimate Charge Volume of a Grinding Mill (Method 1)
2015年10月15日 The load estimation method has you physically measure distances in the mill Follow the charts below and pull them into this calculator 911 Metallurgist is a trusted resource for practical insights, solutions, and support in mineral processing engineering, helping industry professionals succeed with proven expertise Estimate Charge Volume of a Grinding Mill 2016年6月3日 The peak load at the mill with the crusher running is 126 Hp, with a feed rate of 50 tons per day All mill equipment is motor driven through “V” to “V” drives except the ball mill which has a “V” to flat drive The mill reset magnetic switches are away from dust and dirt on an upper platform in the roof trusses above all equipmentMineral Processing Plant Design Construction Example2014年5月8日 Mill Construction Construction Methods Both concrete and steel construction are used for the construction of the mill portion of a flour milling facility Typically, large mills are constructed using precast The walls of these types of facilities are typically nonload bearing precast and tiltup or alternatively, insulated Design Considerations for the Construction and Operation of 2012年4月17日 Effect of Slurry Density on Load Dynamic and Milling Performances in an Iron Ore Ball Mill Online Estimation of Inmill Slurry Density April 2012 DOI: 1013140/2146258561(PDF) Effect of Slurry Density on Load Dynamic and Milling Performances
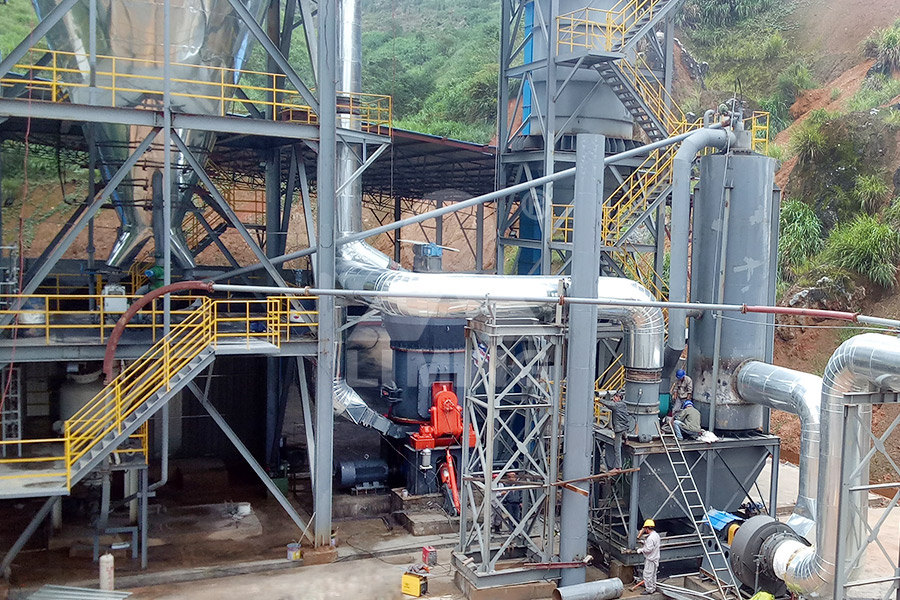
(PDF) Supplementary Relationship between Circulating Load and
2023年8月15日 The ball mill used in Nanshan Mine is MQY2736 ball mill, the diameter (R) of the ball mill is 27 m and the length (L) is 36 m The internal liner of th e ball m ill is calculated as 01 m, then 2020年10月9日 As one of the machines widely used in mining, a semiautogenous grinding (SAG) mill can significantly improve the roughing efficiency of rock But the SAG mill still faces the obstacles of significant energy consumption and empirical operation parameters In order to obtain the optimal operation parameters of a SAG mill, in this paper, the discrete element Operation Analysis of a SAG Mill under Different Conditions2017年4月2日 Cost of Installation of loading chutes Table 31 gives typical costs of building and installing loading chutes The costs shown cover single chutes and are to be considered for the most part as approximate and not directly comparable, since they were obtained from various sources without reference to any standard form for segregation of cost itemsUnderground Ore Loading Chutes; Ore Chute DesignProtected construction having all major building elements with at least a 1hour fireresistance rating Exception: nonload bearing interior walls and partitions having no rating TYPE VB (ISO 1): A woodframed building having no fireresistance ratings This is the most commonly seen ISO 1 Construction Classification
.jpg)
Effect of Water Density on Grinding Mill 911Metallurgist
2015年7月29日 The more water that is added, the faster the ore will go through the mill This means the time it has to be ground will be reduced and a poor grind will result At the other extreme, if not enough water is used, the ore will not be able to flow through the mill The result is the ore will not be able to move into the rod load2024年4月26日 Learn about the key stages in iron ore processing, including crushing, screening, and beneficiation techniques for optimal resource utilization +86 ; xlyin@ The choice of grinding mill depends on factors such as the desired product size, capacity requirements, and energy consumption b Autogenous and Semi Iron Ore Processing: From Extraction to Manufacturing2016年3月18日 Storage—Ore storage in the coarse ore bin and the fine ore bin is designed to meet the requirements of the customary 5 days per week mine operation and 7 days mill operation Fine ore bin capacity is such that the crushing plant Small Mineral Processing Plant Design / Construction2016年6月6日 Mill reversibility for reduced liner scrap loss and balanced wear Some fully autogenous mill operators have found that this feature reduces liner consumption by approximately ten percent (10%) compared with undirectionally rotated mills Variable speeds for the mill to prevent throwing balls against exposed liners at reduced ore volume loadSAG Mill Liner Design 911Metallurgist
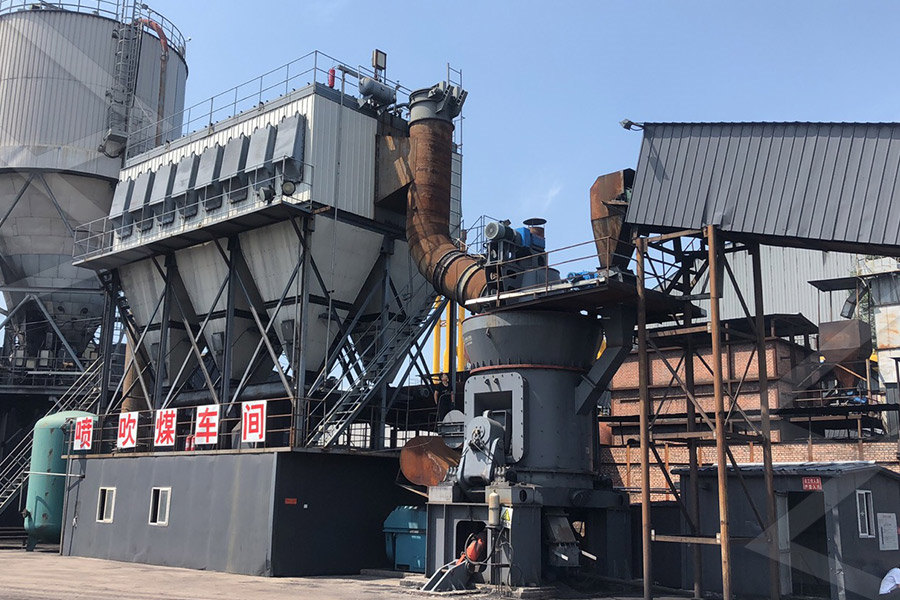
(PDF) Optimization of inmill ball loading and slurry solids
2012年12月1日 The inmill load volume and slurry solids concentration have significant influence on the ball mill product size and energy expenditure Hence, better energy efficiency and quality grind can only 2017年10月26日 The following are factors that have been investigated and applied in conventional ball milling in order to maximize grinding efficiency: a) Mill Geometry and Speed – Bond (1954) observed grinding efficiency to be a function of ball mill diameter, and established empirical relationships for recommended media size and mill speed that take this factor into Factors Affecting Ball Mill Grinding Efficiency 911MetallurgistDesign Loads During Construction Horizontal Construction Load, C H • Wheeled vehicles transporting materials, 20% for a single vehicle, or 10% for 2 or more vehicles of a fully loaded vehicle weight • Equipment reactions, calculated or rated horizontal loads (whichever are greater)Design Loads on Structures During Construction ASCE 3714Download scientific diagram Construction of a SAG mill with the stator and the rotor separately mounted from publication: Control of Large SalientPole Synchronous Machines Using Synchronous Construction of a SAG mill with the stator and the rotor