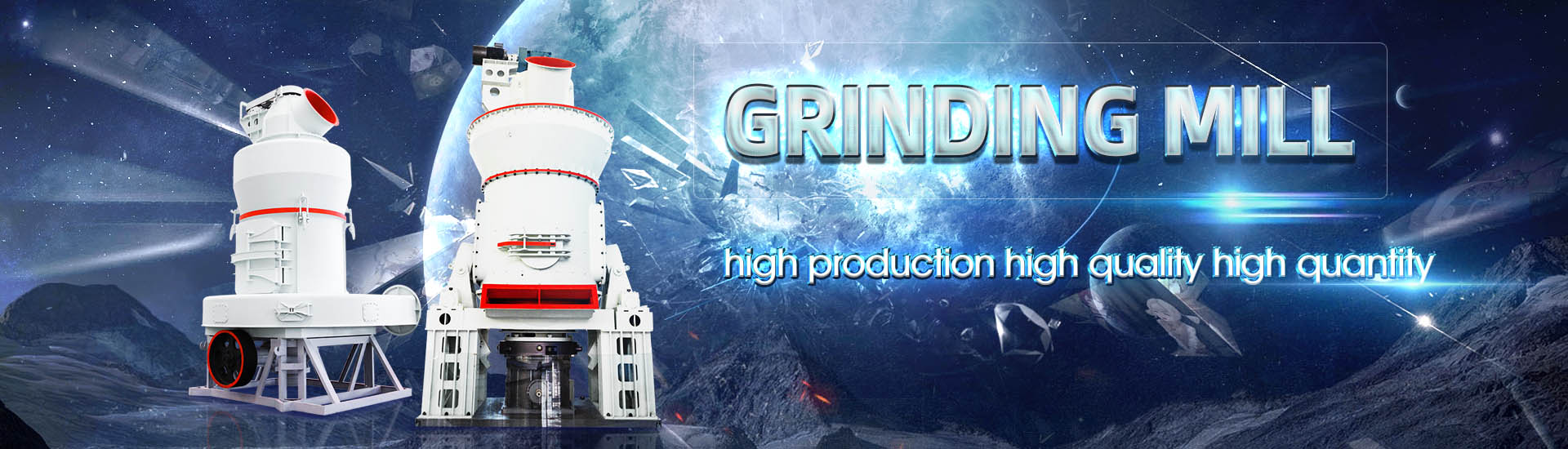
Stirring ball mill
.jpg)
Stirred Mill an overview ScienceDirect Topics
Stirred mills increase the impact forces by inducing larger momentum changes than the tumbling mill They are recognized to be more efficient than tumbling mills, especially for fine grinding 2009年6月1日 Stirred mills are primarily used for fine and ultrafine grinding They dominate these grinding applications because greater stress intensity can be delivered in stirred mills Comparison of energy efficiency between ball mills and stirred The world’s most reliable stirred mill just got bigger Developed as a solution to lower capital expenditure, the Vertimill® 7000’s much larger size allows for more available power One Vertimill 7000 grinding mill, replaces the need for Vertimill® Metso2016年1月1日 Tumbling ball mills are capable of fine grinding to around 20 μm with the energy efficiency increasing with decreasing media size, depending on the feed size For feed sizes, Stirred Mills – Ultrafine Grinding ScienceDirect

Stirred mills Metso
The HIGmill™ comprises a mill body, shaft with grinding rotors, shell mounted stator rings, gearbox, and drive The grinding chamber is filled up to 70% with inert ceramic grinding media 2023年7月10日 Higher power densities and greater grinding effectiveness are making stirred ball mills more and more popular for ultrafine grinding, particularly in the mineral industry, when compared to traditional tumbling ball millsEnergyEfficient Advanced Ultrafine Grinding of 2023年5月18日 Stirred mill relies on highintensity stirring action to effectively drive small grinding medium, and forms multiple compressed rotating media layers, generating pressure Stirred Mill SpringerLinkJM series vertical stirred ball mills is a kind of high efficiency ultrafine ore grinding equipment (also called tower mill or vertical spiral stirred ball mill), mainly adopted for the ultrafine grinding test research, also for the small scale industry Vertical Stirred Ball Mills – ZJH minerals
.jpg)
Stirred Mill Springer
Stirred mill uses a stirring device to drive the grinding medium to move, generating grinding, shocking, and shearing effect on grinding materialsIn discussions on high energy ball milling, the more generic term "ball mills" is often used in place of the terms "stirred ball mills" or "Attritors," but the differences between the types of mills are quite distinct And, depending on your High Energy Ball Milling Stirred Ball Mill Stirred 2014年1月16日 Starch laurate, a kind of high fatty acid starch ester, was directly produced by mechanical activation (MA)assisted solidphase synthesis (MASPS) technology with a customized stirring ball mill as reactor The starch laurates with different degrees of substitution (00148–00412) were obtained under different reaction conditions Fourier transform infrared A Green Technology for the Preparation of High Fatty Acid Starch Lab stirred ball mill mainly consist of jar with inner grinding media, stirring device and other auxiliary devices such as recycling device, cooling device, timing device, speed adjusting controller, and etcLab Stirred Ball Mill
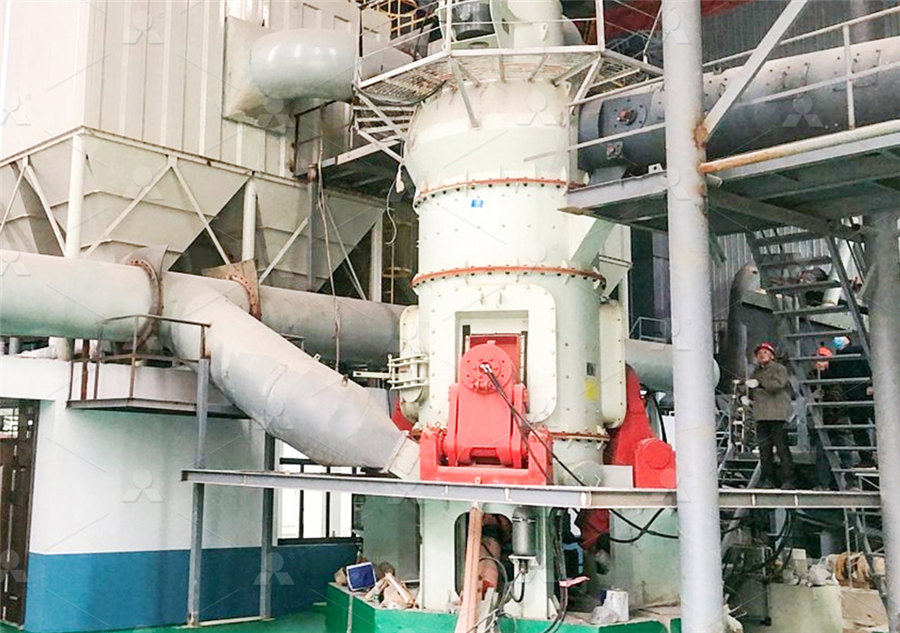
Stirred Mill Springer
utilization efficiency is high Stirred mill relies on highintensity stirring action to effectively drive small grinding medium, and forms multiple compressedrotating medialayers,generatingpressure and torsional force, which plays a more effective role than the shocking and grinding force generated in the ball mill in crushing materials It 2023年11月1日 This paper demonstrates the feasibility of using a ceramic medium stirring mill to reduce the energy consumption of grinding operations through an industrial verification experiment Compared with the original twostage ball milling process, the cost of grinding power consumption is significantly reduced by about 5016%, which provides a reference for the Energy conservation and consumption reduction in grinding 2020年7月1日 Mechanochemistry has a long history in the everyday life and in laboratoryscale chemical syntheses [27]In the laboratory, mechanochemically assisted reactions are usually carried out either in planetary or in vibrating ball mills, where the reagents are loaded in a milling jar and movement of balls generates the mechanical force to the reagents [28, 29]Stirring or milling? First synthesis of Rh(I)(diNheterocyclic 2009年6月1日 At product sizes finer than 80% passing 75 μm, the efficiency of ball mill grinding rapidly decreasesThe practical limit to ball mill product fineness is considered to be 40–45 μm (Gao and Weller, 1994)Although ball mills can still be found in the regrind circuits in a number of mineral processing plants, their energy consumption is high, and size reduction efficiency is parison of energy efficiency between ball mills and stirred mills
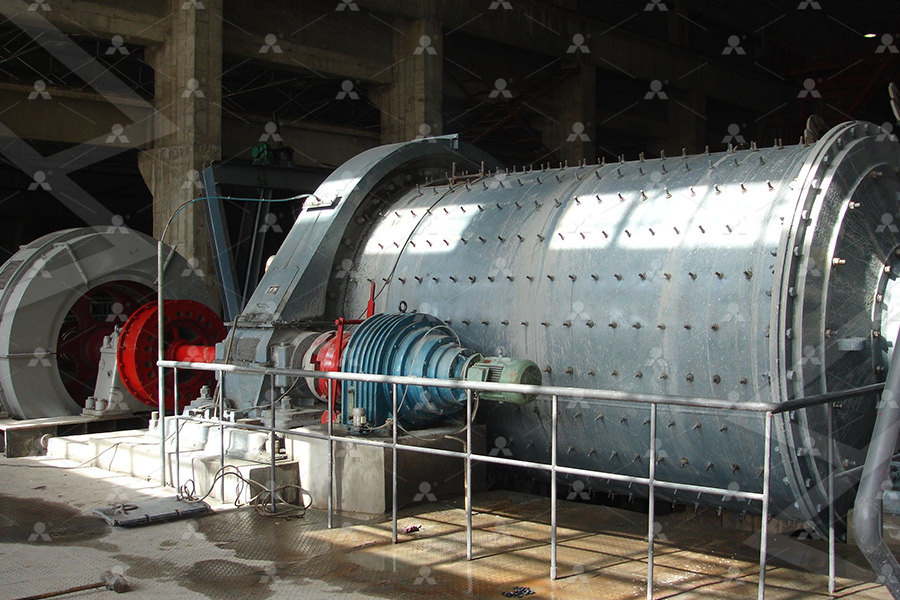
Ball mill witeg Labortechnik GmbH
Ideal for: Grinding and mixing crystalline chemicals, inks, paints, pigments, plants, racks, and soils Features: antistatic rubber roller: keeps jars/pots centered ergonomic and compact design NBR roller with pot guide ring programmable options: 10 steps and 6 programs storage function for the set values of temperature and timer soundproof cabinet for safety and minimum noise (optional Stirring ball mill Family Cites Families (11) * Cited by examiner, † Cited by third party; Publication number Priority date Publication date Assignee Title; DEC2 (en) * : : Hosokawa Alpine Ag: Agitator ball mill EPB1 (en) * : EPA1 Stirring ball mill Google PatentsTianchuang's attention to details is definitely the best, and the small stirring ball mill is excellent! It’s Time To Take Your Action To Inquiry Us China Tencan has numerous excellent engineering and technical personnel, and has established longterm and stable cooperative relationships with lots of customers throughout the worldQuality Tencan Laboratory Ball Mills Price China Changsha 2023年11月1日 The research of ceramic media stirring mill instead of ball mill is beneficial to solve the problems of production efficiency and quality of beneficiation products in Gongchangling Concentrator In this study, in order to achieve energy saving and consumption reduction in grinding operations, Energy conservation and consumption reduction in grinding
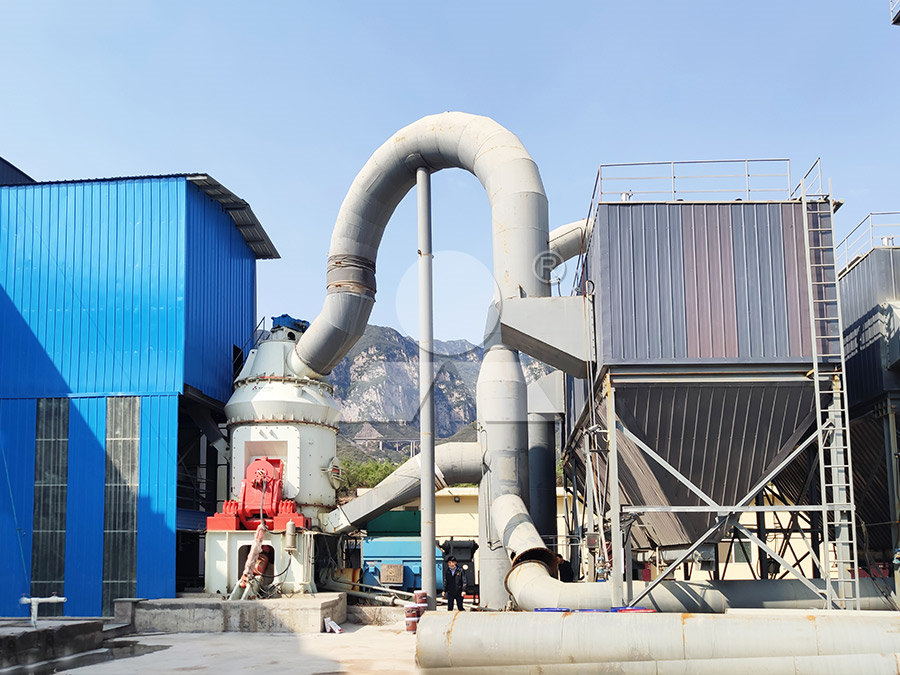
Optimization Test of Stirred Mill for Mixed Magnetic Concentrate
The raw ore is mainly fine disseminated hematite and magnetite in Donganshan Sintering Plant The field problems are low efficiency of ball milling and low monomer dissociation etc In this research, the process optimization and comparison of magnetic concentrate ball milling and ceramic ball stirring grinding were carried out The results show that the optimum conditions of 2021年4月27日 The spindle driven the agitator do high speed rotating, make the grinding medium to do irregular movement https://tmaxcn/stirringballmillstircasStirring ball mill YouTubeAbstract: The flake silver powders were grinded by stirring ball milling with different milling aids at different milling times, using the precursors in different specific surface areas The physical properties and electrical conductivity of flake silver powders were investigated by laser particle size distribution (PSD) instrument, scanning electron microscope (SEM), specific surface area 搅拌球磨磨制片状银粉工艺研究 USTBMSE Supplies also can offer industrial attritor stirred ball mills with the volume up to 600L Please Contact Us for quotation In addition to attritor stirred ball mills, you can use our Planetary Ball Mills to produce fine powders SKU MA0807 MA0808 MA0809 MA0810 Container Volume (L) 1 MSE PRO Lab Attritor Stirred Ball Mill MSE Supplies LLC
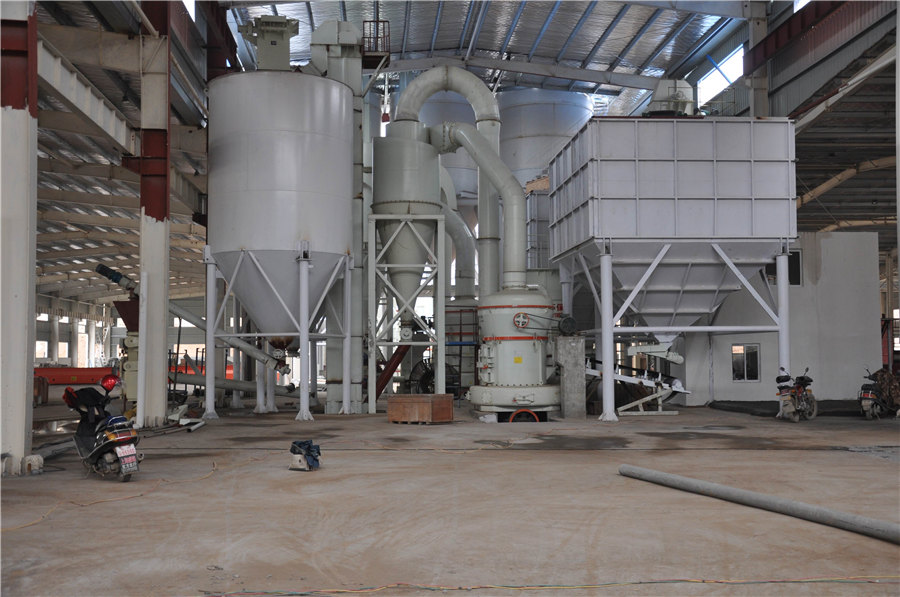
Vertical mills for fine grinding – FLS
Vertical mills such as the FLS Tower Mill or the VXPmill and ball mills are commonly used for fine grinding in industries like mining, cement, and chemical processing These mills reduce material into finer particles, making them ideal for applications where fine to ultrafine grinding is required , such as in regrinding of ore in mining or producing fine powdersThe technical features of JM stirred ball mill 11, high ability of fine grinding, to grinding the material to be 1μm or more fine 12, High efficiency and energy saving, more than 50% energy saving compared with horizontal ball mill, the working efficiency is 10 Vertical Stirred Ball Mills – ZJH minerals1 Stirring or milling? First synthesis of Rh(I)(diNheterocyclic carbene) complexes both in solution and in a ball mill Sourav De a,b, Ferenc Joó a,c, Henrietta Horváth c, Antal Udvardy a, *, Csilla Enik ő Czégéni c, * aUniversity of Debrecen, Department of Physical Chemistry, POBox 400, Debrecen, H 4002 HungaryStirring or milling? First synthesis of Rh(I)(diNheterocyclic Bead mill working principle for dry cement grinding One crucial characteristic of this mill is the high energy density, 1020 times higher than of a ball mill, and the resulting very compact design The beadstirring elements on the shaft inside the fixed shell reach a tip speed of 5 polysius® booster mill
.jpg)
Laboratory Mixer Mill MM 400 RETSCH
Some chemical reactions require the frictional forces of a planetary ball mill, while other reaction types need energy input through impact – that is where the Mixer Mill MM 400 comes into play The sample volumes available for research applications are often very low2014年1月27日 Figure 1 FTIR spectra of (a) native cassava starch, (b) MApretreated starch (t = 1 h), (c) starch laurate (DS = 00256, t = 1 h), and (d) starch laurate (DS = 00398, t = 1 h) "A Green Technology for the Preparation of High Fatty Acid Starch Esters: SolidPhase Synthesis of Starch Laurate Assisted by Mechanical Activation with Stirring Ball Mill as Reactor"Figure 1 from A Green Technology for the Preparation of High TOB NEW ENERGY supply customizable stirring ball mills grinder milling equipment for Lithiumion battery research grid view list view Stirred Ball Mill for Laboratory TOB New Energy provides 30L capacity stirred ball mill for laboratory, we can also provide 5L and 10L models, Stirring Ball Mill,Stirred Mill,Laboratory Stirred Ball MillCompared to conventional horizontal ball mills, BGRIMMMAT grinding and scrubbing equipment is suitable for fine particle grinding with energy saving by 20–40% Skip to content EXCELLENCE IN SEPARATION TECHNOLOGIES BBBEE contact Attrition Mills Technology and Experience Roytec Global
.jpg)
Highefficiency and energyconservation grinding technology using
2022年1月1日 A pilotscale grinding technology of ceramic medium stirred mill was proposed in this study Based on the specific productivity and grinding efficiency, the appropriate grinding parameters were ascertained as follows: material ball ratio of 07, ceramic ball medium size ratio (10 mm: 15 mm: 20 mm = 3:2:5), stirring speed of 110 rpm, grinding concentration of 50%, Run the method for stirring ball mill and perform the stirring ball mill of the method US14/573,882 USB2 (en) : : Method for operating an agitator bead mill and agitator bead mill therefor Applications Claiming Priority (2) Application Number Priority Date Filing Date Title WOA3 Method for operating a stirred ball mill and 2016年5月30日 A comparative study was carried out for an alloy of Al 50 (Ni 75 Mo 25) 50 processed by two different high energy ball mills A SPEX and Simoloyer mill were usedDESIGN AND FABRICATION OF MINI BALL MILL ResearchGate2011年4月1日 Stirred ball mills are frequently used for ultrafine and nanogrinding in food, pharmaceutical and chemical industry, but only few investigations have been published on empirical or scaleup Empirical and scaleup modeling in stirred ball mills
.jpg)
Mill (grinding) Wikipedia
A mill is a device, often a structure, machine or kitchen appliance, that breaks solid materials into smaller pieces by grinding, crushing, or cutting Such comminution is an important unit operation in many processesThere are many different types of mills and many types of materials processed in them Historically mills were powered by hand or by animals (eg, via a hand crank), stirring ball mill搅拌式球磨机 3)attritor milling搅拌球磨 4)stirred media mills搅拌磨机 1Mathematical model was established for the motion of grinding beads in the circular section of grinding chamber of new stirred media mills with a rotation rat cage建立了鼠笼式搅拌磨机研磨介质在研磨室圆截面内运动状态的数学模型 ,用四阶RungeKutta法求解 搅拌球磨机,ballstirring mill英语短句,例句大全 X技术网2023年5月15日 During ball milling, solids constantly undergo stress, aggregation, and agglomeration, which allows the material to interact and experience various chemical reactions under mechanical forces [15]In a highenergy mill, the material to be milled is placed in a hollow cylindrical container and a milling medium, ie, balls generally made of stainless steel, Ballmilling: A sustainable and green approach for starch 2024年9月1日 The influence of the direction of the stirring shaft on the grinding performance was investigated by Fukui et al [19] based on the DEM Oliveira et al [28] used a mechanical mill model originally developed for ball mills and the DEM to Performance analysis of vertical stirred mill based on multi
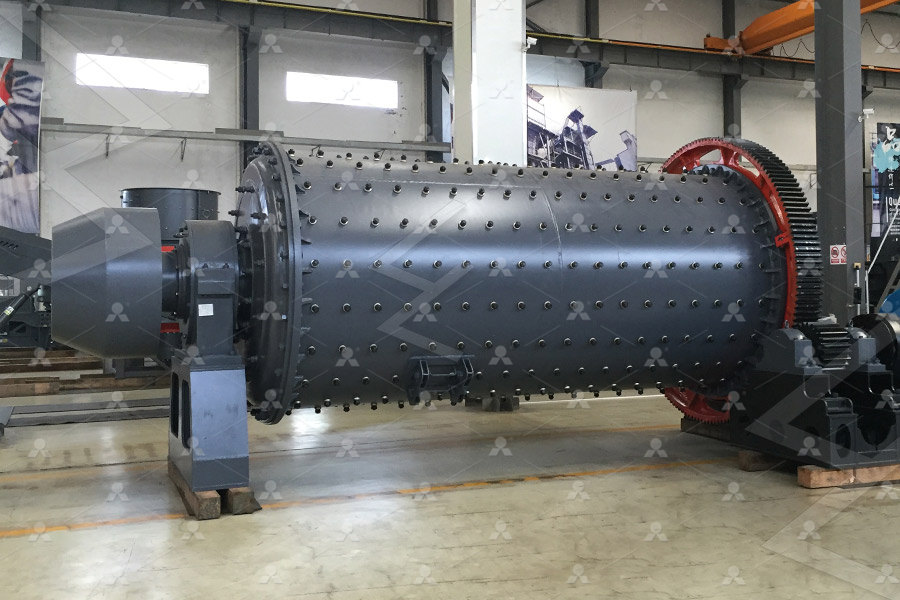
Highefficiency and energyconservation grinding technology using
2022年1月1日 A pilotscale grinding technology of ceramic medium stirred mill was proposed in this study Based on the specific productivity and grinding efficiency, the appropriate grinding parameters were ascertained as follows: material ball ratio of 07, ceramic ball medium size ratio (10 mm: 15 mm: 20 mm = 3:2:5), stirring speed of 110 rpm, grinding concentration of 50%, Stirred Media Mills: These mills use a stirring mechanism to agitate the grinding media, creating a more efficient grinding process Ball mill grinding machines are valuable tools in various industries, offering efficient and reliable grinding Ball Mill Grinding Machines: Working Principle, Types, mills equalling the ball mill efficiency could lie in the region of F80 = 3 to 4mm The vertical gravity induced mill has a recommended efficiency factor to 080 (ie 20% energy benefit) or higher when feeding the Vertimill with coarse feed F80 = 26mm (Hounde 2019) Ballantyne (2021) determined that the scaleup couldRECENT DEVELOPMENTS IN COARSE GRINDING USING VERTICAL STIRRED MILLSPolymer Bulletin, 2014, 71(2): 453464(SCI、EI收录) Yanjuan Zhang, Tao Gan, Huayu Hu, Zuqiang Huang*,et al A Green Technology for the Preparation of High Fatty Acid Starch Esters: SolidPhase Synthesis of Starch Laurate Assisted by 黄祖强 广西大学 化学化工学院 XMOL科学知识平台
.jpg)
Lab Stirring Ball Mill Introduction And Operation JXSC Mining
2024年2月21日 Operation Test After completing the stirring ball mill installation, confirm there is no jamming phenomenon and start testing The machine should undergo a 24 hour noload and a 56 hour load test Empty load test; The noload test machine must meet the following requirements without feeding2019年1月10日 An effective mechanical activation (MA) + metal salt (MAMS) technology was applied to pretreat sugarcane bagasse (SCB), a typical kind of lignocellulosic biomass, in a stirring ball mill Chlorides and nitrates of Al and Fe showed better synergistic effect with MA, especially AlCl3, ascribing to the interaction between metal salt and oxygencontaining groups induced Overcoming biomass recalcitrance by synergistic pretreatment SJM3L is a compact stirring ball mill with water cooling jacket 3L jarIt is used in building materials, coatings, chemicals, medicine, food, pesticides, electronics, metallurgy, ceramics, pigments, lithium batteries, rare earths, phosphors and other fields for material's grinding and crushing to 01um powderSJM3L Laboratory Vertical Stirring Ball MillDownload scientific diagram Types of mills for highenergy milling: Aball mill, Bplanetary mill, Cvibration mill, Dattritor (stirring ball mill), Epin mill, Frolling mill 4k Modified from Types of mills for highenergy milling: Aball mill, Bplanetary mill
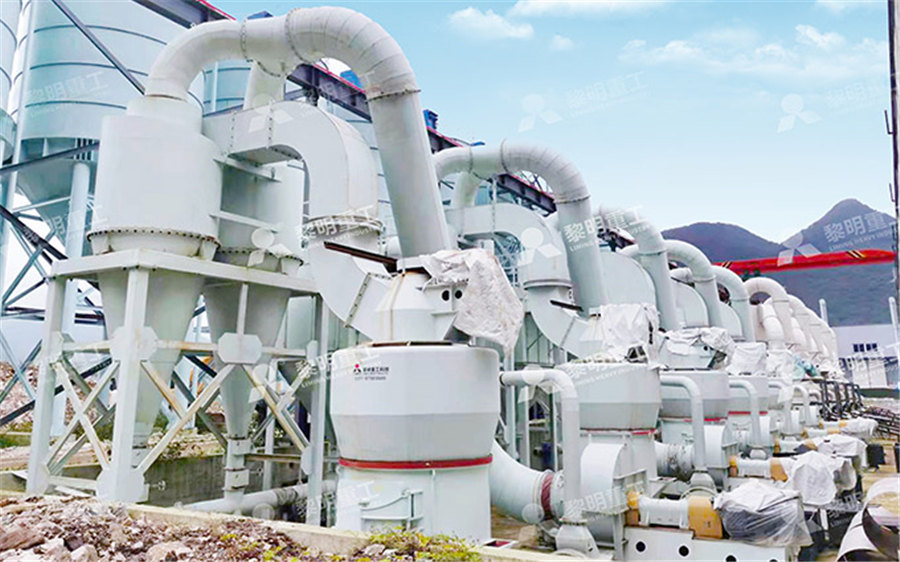
Stirred media mills in the mining industry: Material grindability
2020年6月1日 Ball mills have traditionally been used for fine grinding of minerals, and in these cases smaller ball sizes than in conventional grinding are used to increase contact area and decrease collision intensity [15], and lower mill speeds are used to cause the media to cascade rather than cataract, Ball Mills are the most effective laboratory mills for rapid batchwise comminution of mediumhard, soft, brittle, fibrous, temperaturesensitive and moist samples down to the finest particle size The comminution of the material to be ground takes place through impact and friction between the grinding balls and the inside wall of the grinding bowl respectively the mortarBall Mills – fritsch