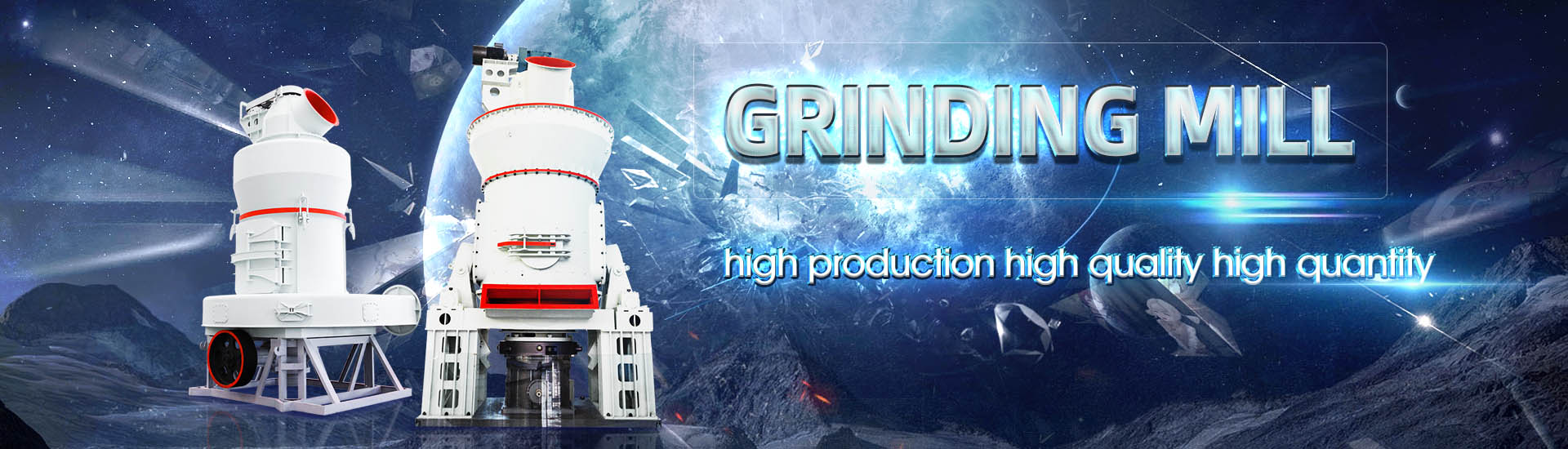
Flue gas cooler steel wall coking
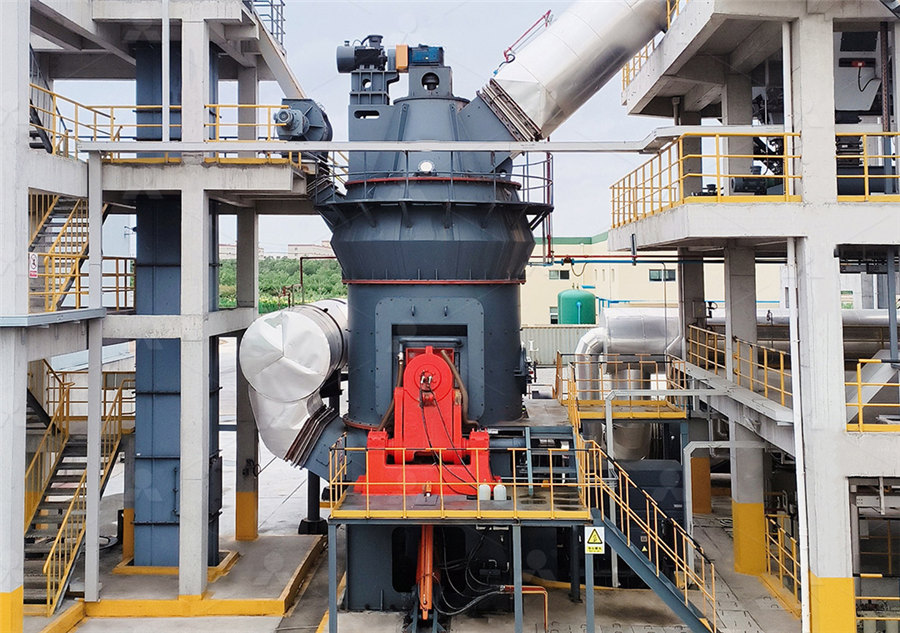
Flue Gas Coolers Wabtec Corporation
Designed to cool hot, dirty flue gas streams for entry into pollution control equipment Air is typically the cooling medium; however, fluids can be used as well Automatic cleaning systems can also be provided for keeping the heat Different from CWQ, the coke dry quenching (CDQ) technology, ie the coke quenching with N 2, insitu pyrolysis gas or flue gas, can recycle the sensible heat of coke, save water, and reduce Dry Quenching an overview ScienceDirect TopicsIn combination with an internal flue gas recirculation system this results in an optimum vertical temperature distribution over the heating walls while reducing the NO X content of the exhaust Coke Plant Technologies ThyssenKrupp2024年3月31日 According to the industrial standard, combined with the data in Tables 2 and 4, it is known that in the coking and sintering processes, coke oven flue gas, sintering waste gas Evaluation of low‐grade waste heat resources in coking and
.jpg)
The Research on Waste Heat Utilization Technology of Coke Oven
waste heat from COG, flue gas, and heat dispersion on the coke surface, which are presented in Table 1 [4–8] Table 1 clearly demonstrates that the waste heat of COG constitutes a 2024年1月1日 The waste heat of coke oven flue gas can be used to produce lowpressure steam The waste gas from producing one ton of coke can generate 01ton 08 MPa saturated Energy Utilization in Coking Process SpringerLinkThe Flue Gas Cooler generates 414barg (600psig) steam at a superheated temperature of 399oC (750oF) A stack gas analyzer measures the quality of the cooled flue gas being vented Welcome to the Fluidized Catalytic Cracking Unit Module 03, Hyundai Steel coke oven batteries are using the COMBIFLAME heating system which consists of special heating flues, equipped with bottom and wall air stage and with internal waste gas re TKISAIST2015PaperUsing modern coke oven technology at
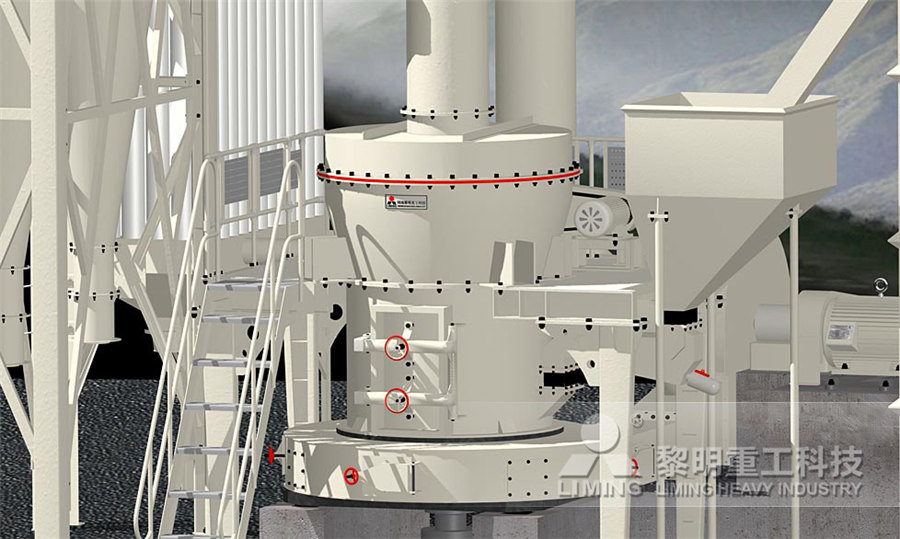
Composition, characteristics, and treatment technologies of
2024年4月12日 To study the total particulate matter (TPM) in flue gas emitted by coking plants, a sampling system that could be used to collect filterable particulate matter (FPM) and One of the world's leading chimney manufacturers • Chimneys with brand quality • Flue pipes made of stainless steel, steel or plastic Register Login User login Forgot your Flue gas ducts The perfect connection between heat generator and chimney Grease duct systems for commercial kitchen´s cooking areas Pizza Oven ChimneyJeremias® Exhaust SystemsA common application of economisers in steam power plants is to capture the waste heat from boiler stack gases (sometimes known as flue gas) and transfer it to the boiler feedwater This raises the temperature of the boiler feedwater, lowering the needed energy input, in turn reducing the firing rates needed for the rated boiler outputEconomisers and Flue Gas Coolers Ship Technology7quot; Twin Wall Flues for gas amp; solid fuel Stainless steel insulated flues amp; chimneys Prices include VAT Free delivery on orders over £1007quot; Twin Wall Flue, Stainless Steel Chimney Systems
.jpg)
Stainless Steel Twin Wall Flue For Stoves and Chimney SNH
Free Standing Gas Fires; Wall Mounted Gas Fires; Balanced Flue Fires; Solid Fuel Stoves Hetas Approved Stoves; Defra Approved Stoves; Gas Stoves; After Care Stove Rope Glue; Stove Glass; Fire Lighters Matches; Paint; Stoves; Flues Fittings Stainless Steel Twin Wall Flue TWPro 5 Inch Twin Wall; TWPro 6 Inch Twin Wall; Black Twin Wall Available in a stylish and lowmaintenance black finish, our 6inch twin wall flues are used when there is no constructed chimney available They’re often found in period or new build properties without chimneys, as well as in many conversions and renovations where the chimney stack has been removed or the woodburning stove's desired position is not where the chimney is located6Inch Twin Wall Flue Pipes Stoves Are UsSulfuric acid condensation has long been considered as the major cause of the corrosion issues at the coldend of coalfired boilers However, in a flue gas cooler, where flue gas is cooled to around 90 °C for heat recovery, the influence of chlorides might be underestimated In this article, some elbows of the heat transfer tubes in the flue gas cooler of a coalfired power plant were Investigation on the Corrosion of the Elbows in the Flue Gas Cooler tion at the heating flue sole In addition, the waste gas recirculation at the bottom part of the partition wall of a twin flue recycles waste gas from the downburning into the upburning heating flue Thereby the combustion at the bottom becomes leaner, the flame peak temperature is reduced, and the formation of NOx is further reducedTKISAIST2015PaperUsing modern coke oven technology at Hyundai Steel
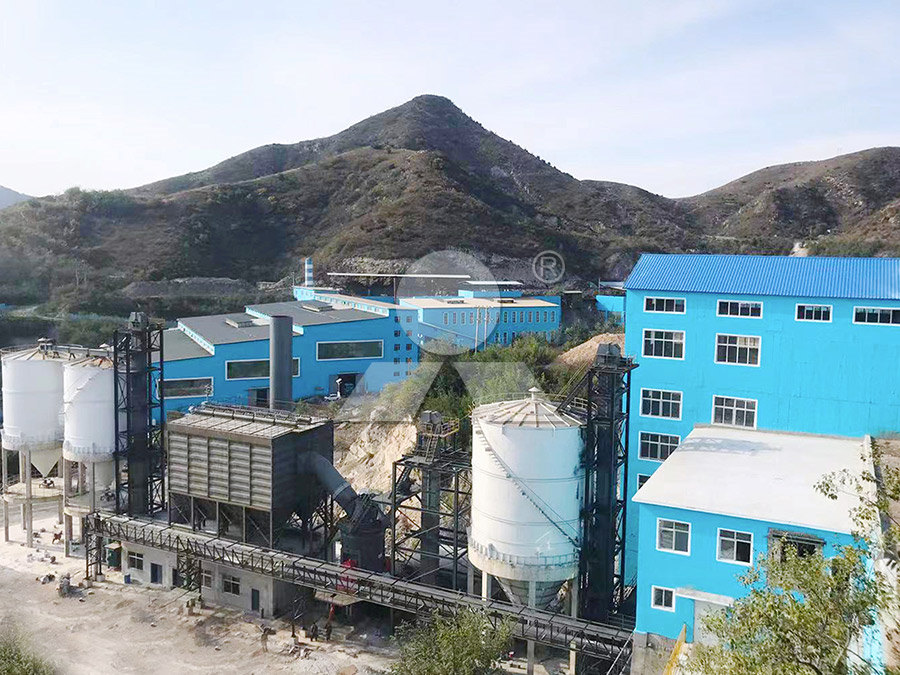
Energy Utilization in Coking Process SpringerLink
2024年1月1日 Heat of Hot Waste Gas The temperature of the waste flue gas from the coke oven at the chimney is about 300 °C, and its heat accounts for about 17% of the coking energy consumption The waste heat of coke oven flue gas can be used to produce lowpressure steamHuadong Boiler provides custom flue gas coolers for various boiler heat exchangers and can help you to save fuel costs How Does Huadong Boiler Produce Flue Gas Coolers? Material selection: 20#Steel, ND Steel, 309S, 12Cr1MoV,15CrMoVG; Standard: Water Wall Panels; Industrial Cyclone Separator; Flue Gas Cooler;Flue Gas Cooler Boiler Parts Huadong BoilerIn this cycle, gas turbine flue gases actually are used as cathode feeding for MCFC While CO 2 is moved from the cathode to anode side, concentrate CO 2 in the anode exhaust Then the CO 2 is concentrated on the anode side of MCFC allowing to easily treat this spent fuel stream in a cryogenic process to split combustible species (routed back to gas turbine combustor) from Carbon Dioxide Separation from Flue Gases: A Technological 2021年5月26日 An exceptional phenomenon has been observed that SO2 and NOx in flue gas can be effectively adsorbed over activated carbon with a surprising capacity at cold temperatures with the presence of oxygenSimultaneous removal of SO2 and NOx from flue gas by low
.jpg)
Convective Heat Transfer Coefficients Table Chart Engineers
Flue gas : Aromatic hydrocarbon and steam : 5 – 10 : Typical values of Evaporator heat transfer coefficients Evaporators heat transfer coefficients Hot Fluid : Cold Fluid : Coolers (no phase change) heat transfer coefficients Cold Fluid : Hot Fluid : Overall U (BTU/hrft 2F) Water : Water : 150 – 300 : Water : Organic solvent : 50 By cooling the flue gases back to 4050 degrees Celsius, the flue gas condenser can save up to 16% on natural gas consumption We are happy to calculate for you what savings are possible for your company, we often already draw up an energy balance by telephoneFlue gas cooler Kuiper Zonen BVHigh quality Corrosion Resistant Steel Boiler Membrane Water Wall Panels For Thermal Power from China, Flue Gas Cooler Contact Us 86 they are used to absorb the radiant heat by the flame and high temperature flue gasThey are the main form of heating surfaces for the various modern boilers, Corrosion Resistant Steel Boiler Membrane Water Wall Panels Gas Flue Blocks certified to BS EN 1858:2008 Under the new BS EN 152871 twin wall stainless steel system chimneys certified to BS EN 18561:2009 can also be used as connecting flue pipe Page 6 Stainless Steel Terminals, Birdguards AntiDowndraught TerminalsGeneral Guidance on the selection and installation of flues and
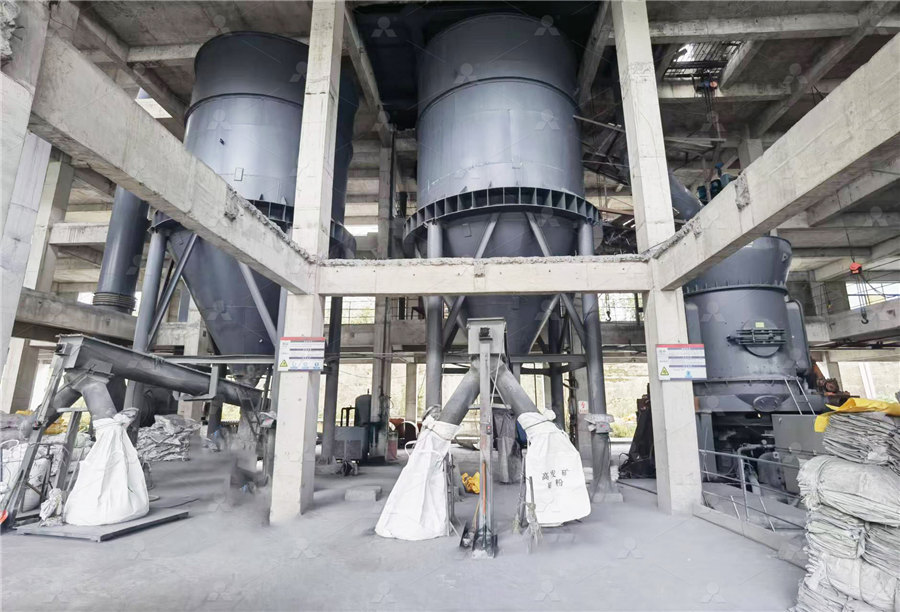
Control of Zinccontaining Dust Agglomerates in Basic Oxygen
the dry flue gas cleaning system can satisfy the requirements of current steelmaking cleaner production Furthermore, compared with BOF wet flue gas cleaning system, the dry flue gas cleaning system consumes less electricity and has no secondary pollution6,7) As shown in Fig 1, BOF dry flue gas cleaning systemRIGID SECTIONAL, SINGLE WALLED STAINLESS STEEL FLUE SYSTEMS Single walled stainless steel flues can usually be used for any part of the flue that runs internally on appliances where flue gas temperatures are relatively low, around 70°C, and there is no risk of rapid cooling of combustion gasses or burn hazards from touchingMetal flue systems Vulcan2023年7月21日 The recovery and utilisation of waste heat from flue/exhaust gases (RU/WHFG) could potentially provide sustainable energy while curbing pollutant emissions Over time, the RU/WHFG research landscape has gained significant traction and yielded innovative technologies, sustainable strategies, and publications However, critical studies highlighting Recovery and utilisation of waste heat from flue/exhaust gases: a 2020年11月16日 reheating furnaces in the steel industry: determination of the thermal powers in the combustion of coke oven gas, linzdonawitz gas and blast furnace gas November 2020 DOI: 1026678/ABCMENCIT2020 (PDF) REHEATING FURNACES IN THE STEEL INDUSTRY
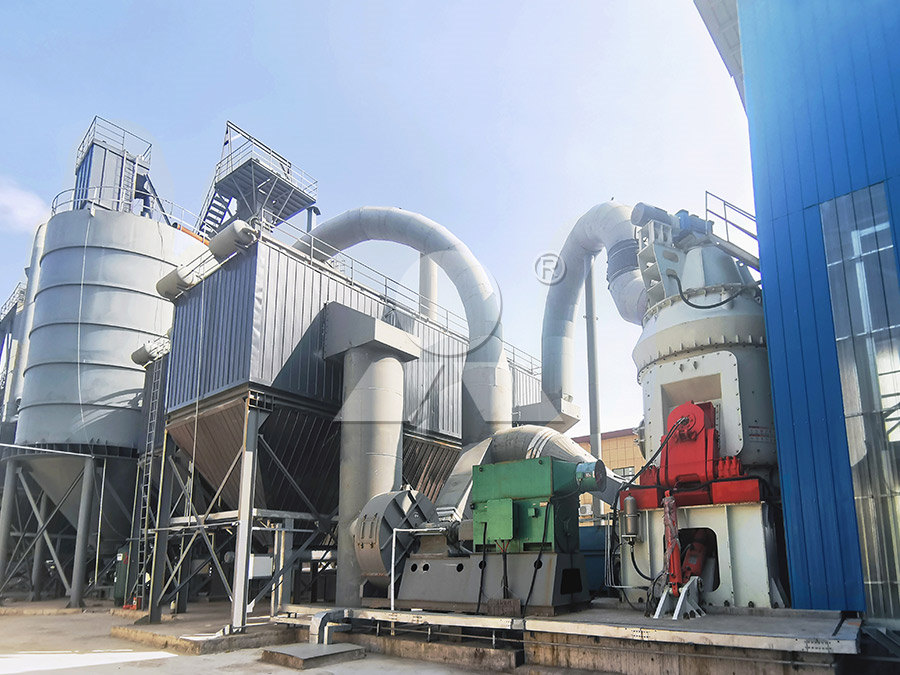
ABYSS Flue Gas Analyser AquaGas Pty Ltd
Fitted with on board BTU calculation, the ABYSS flue gas analyser fulfils the requirements of medium to large scale combustion plants including coal fired power stations, biomass gasification or pyrolysis, offgas from steel and iron plant, Blast furnace, Coking, Converter, Direct Iron Ore Smelting Reduction, Endo Exo Gas Generators for KC is a twin wall insulated chimney flue system designed for use with stoves and fireplaces which are burning wood, solid fuel, gas or oil 200mm diameter We are now open on Saturdays between 9AM and 1PM for all your stove and flue needs!KC Twin Wall Insulated Chimney Flue System for Stoves2022年11月16日 Heat of Hot Waste Gas The temperature of the waste flue gas from the coke oven at the chimney is about 300 °C, and its heat accounts for about 17% of the coking energy consumption The waste heat of coke oven flue gas can be used to produce lowpressure steamEnergy Utilization in Coking Process SpringerLinkThe material of the entire steam boiler flue gas system must be suitable for temperatures up to 350°C If the boiler is equipped with a fourth pass or a waste heat boiler for utilisation of the waste heat in flue gases from a CHP module or Flue gas system Bosch Steam boiler planning
.jpg)
Cooling of flue gas by cascade of polymeric hollow fiber heat
2022年8月1日 Hollow fibers in gas – liquid application are typically arranged in layers where each layer is formed by fibers with constant pitch as shown in Fig 1An important question arises over what the optimal pitch between the hollow fibers should be so that the cooling performance of the heat exchanger in W/m 2 is maximized The cooling performance is scaled by the active 2023年6月25日 Coalfired power generation remains an important part of China’s current energy supply Energy saving, emission reduction, and efficiency improvement are the main directions of technological innovation for coalfired power plants in the context of “Carbon Peak and Neutrality” [1]Installing a flue gas cooler (or economizer) in front of the electric precipitator is important Airside thermal–hydraulic performance evaluation of flue gas coolers 2020年12月10日 Sulfuric acid condensation has long been considered as the major cause of the corrosion issues at the coldend of coalfired boilers However, in a flue gas cooler, where flue gas is cooled to Investigation on the Corrosion of the Elbows in the Flue Gas Cooler 2023年10月18日 1 Directorate of Coke Facilities, Kardemir Iron and Steel Co, Karabuk, Turkey 2 Energy Systems Engineering Department, Karabuk University, Karabuk, Turkey * Corresponding author: Received: 18 October 2023 Accepted: 19 December 2023 Abstract In this study, the energy view of an oven of a 70oven coke battery An applied study on energy analysis of a coke oven
.jpg)
TWPro 5 Inch Twin Wall Stainless Steel Flue SNH Tradecentre
TWPro 5 Inch Twin Wall stainless steel insulated flue for stoves and chimney systems 25 Year Warranty Approved Miflue partner South East BranchBenefits of flue gas cooler Flue gas loss (q2), leading cause of heat loss in boiler, contributes about 6070% of the total It is mainly decided by flue gas temperature and volume Normally when flue gas temperature increases every 1215℃, q2 will increase 1%, accordingly, coal consumption will increase 1224g/kWhBoiler flue gas cooler in power plantDelayed Coking Operational Optimization RIO DE JANEIRO 29 Sept –3 Oct 2014 • FW employs a three prong – Single thickness drum wall – Optimized crotch radius for weld build up hot box cone/straight wall firing/flue gas limited • Low draft could Delayed Coking Operational Optimization Refining Community2024年10月16日 1 Material Quality Stainless Steel Grades: The quality of the stainless steel used in the flue is vital for its longevity and performanceLook for flue systems made with highgrade stainless steel, such as 316L for the inner layer (resistant to corrosion from acidic flue gases) and 304 for the outer layer (durable and weatherresistant)Choosing the Right Twin Wall Stainless Steel Flue System
.jpg)
The Research on Waste Heat Utilization Technology of Coke Oven Gas
of an annular jacket to the outer wall of the ascension pipe, facilitating heat exchange between water and utilization of primary cooler The waste heat of flue gas 250~300°C17% Low temperature waste heat Flue gas waste heat boiler; Iron and Steel Company; Coking plant of Hangang Nanjing Huadian Co, Ltd Coiltype waste heat utilization2023年8月31日 In the 1860s, Belgian E Koppe et al developed the down draft coke oven (Fig 2) in which the coking chamber was separated with the combustion chamberIt is also known as the externally heated coke oven, in which the coal gas generated by coal in the coking chamber was introduced into the combustion chamber, and the air was inhaled from the furnace topCoke Oven SpringerLinkCooking Cooking Balanced flue gas fire for cavity wall installation; Heat output: 2146kW; Efficiency: 86%; Discreet Smartslide control operation; Inbuilt convector box for cooler wall temperatures; Reflective black glass; Easy to install, easy to Elgin Hall Elsie 960BF Balanced Flue Gas Fire Stoves Are Us2021年1月18日 Ecomak has precisely engineered Forced Draught Coolers for cooling gases from 1200 deg C to 250 deg C Ecomak Systems / Posted on 18/01/2021 16/01/2022 / 0 CompanyGas Coolers Ecomak
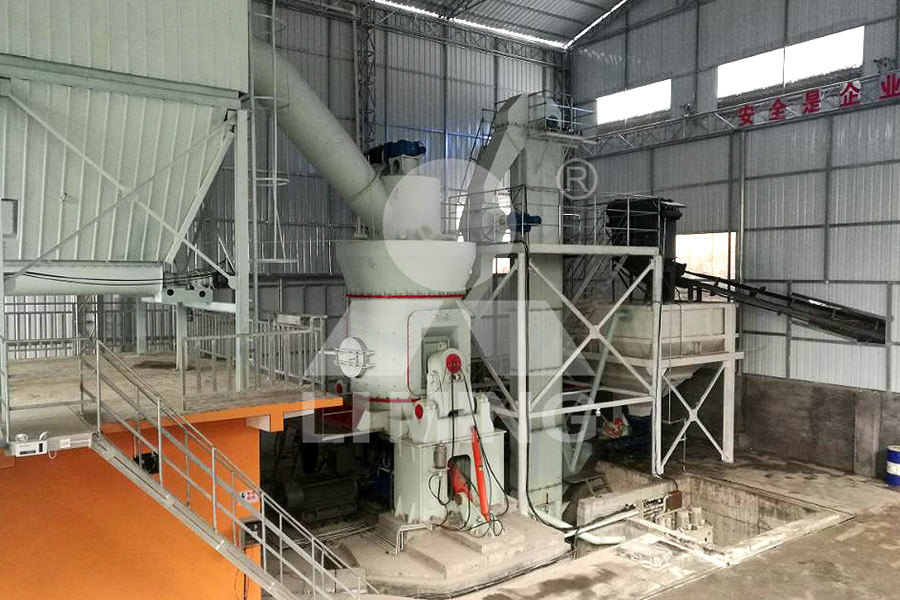
Numerical simulation of NO emission reduction in coke oven
in a coking plant The volume fraction of the main components of the flue gas before entering the chimney was measured: CO2/0206, O2/0054, H2O/0057, N2/0685, and the NOx concentration in the flue gas was 400mg/m3 The mass flow rate at the inlet of the established geometric model was 00075kg/s, and the outlet was the pressure boundaryStoves Outdoor Cooking Wood Burning Multifuel Stoves Gas Electric Stoves Outdoor Cooking KW Pro is a high quality, multifuel, stainless steel twin wall chimney system designed for use with all solid fuel, wood, coal, Gas Flue Liner 100mm; Gas Flue Liner 125mm; Gas Flue Liner 150mm; Gas Flue Liner 175mm;KW Pro Twin Wall Flue 200mm Storm Collar Painted BlackSDS dry desulfurization technology is often used for dry quenching flue gas and coke oven flue gas desulfurization in the coking process Fig 16 Sealed platinum tubes with 02 mm wall thickness are reported to withstand internal pressures on the order of 10 6 Pa [2] 311 Annular cooler in iron and steel industryDry Quenching an overview ScienceDirect TopicsTubular, heating or cooling: Gas at atmospheric pressure inside and outside tubes: 5 35: 1 6: Gas at high pressure inside and outside tubes: 150 500: Cooling of air or flue gas: 60 180: 10 30: Cooling of hydrocarbon gas: 200 450: 35 80: Condensation of low pressure steam: 700 850: 125 150: Condensation of organic vapors Overall Heat Transfer Coefficient Table Charts and Equation
.jpg)
US Refinery – FCCU Flue Gas CoolerIndeck Keystone Energy
2014年12月4日 From 710,000 lb / hr FCCU flue gas flow at 1035 º F and 230 º F feedwater: HP superheated steam flow is 68,500 lb / hr – Design pressure is 750 psig LP steam flow is 29,500 lb / hr – Design pressure is 125 psig Flue gas design pressure is 5 psig – Tube and membrane wall construction