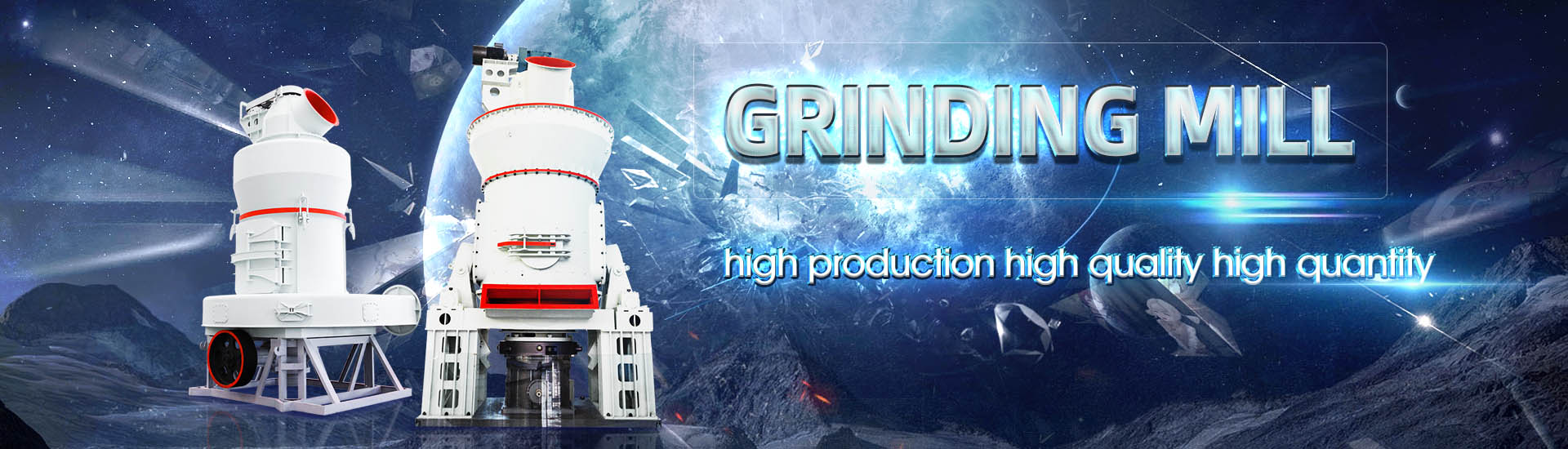
100ton grinding station process flow
.jpg)
Single Double Stage Grinding Circuits 911Metallurgist
2016年4月19日 In order to submit information for use of mill operators, we have prepared comparative flowsheets for 50 Ton, 100 Ton, 200 Ton, 350 Ton and 550 Ton/24 hour plants, • is an online application for closedloop control of a grinding plant This involves integrated process optimisation which is based on a dynamic process model This process model PROCESS OPTIMISATION FOR LOESCHE GRINDING PLANTS2016年4月14日 In order to keep the flowsheet simple, and because of the use of the forced feed type of crusher, we can crush small tonnages up to 100 tons per day with a very simple Crushing Screening Plant Design Factors 911MetallurgistProcess Flow Diagram • A Process Flow Diagram (PFD) illustrates the relationships between major components of a processing plant • They can present the heat balance and material INTRODUCTION TO MINERAL PROCESSING FLOWSHEET DESIGN
.jpg)
Analyzing process parameters for industrial grinding circuit based
2023年9月1日 Based on the machine learning method, this study analyzed the full process parameters (ie, ball mill power, fresh ore feed rate, hydrocyclone feed pump power, 2016年3月11日 By improved efficiency a decrease in energy consumption per ton of crude milled should be achieved Further savings resulting from finer crushing are realized in the Crushing Plant Flowsheet DesignLayout 911Metallurgist2015年7月21日 This article discusses the range of application of ultrafine grinding for processing mineral raw materials and presents examples of the successful use of this technology in the Ultrafine Grinding in Contemporary Flow Diagrams for Mineral Metallic mineral processing typically involves the mining of ore from either open pit or underground mines; the crushing and grinding of ore; the separation of valuable minerals from 1124 Metallic Minerals Processing US EPA
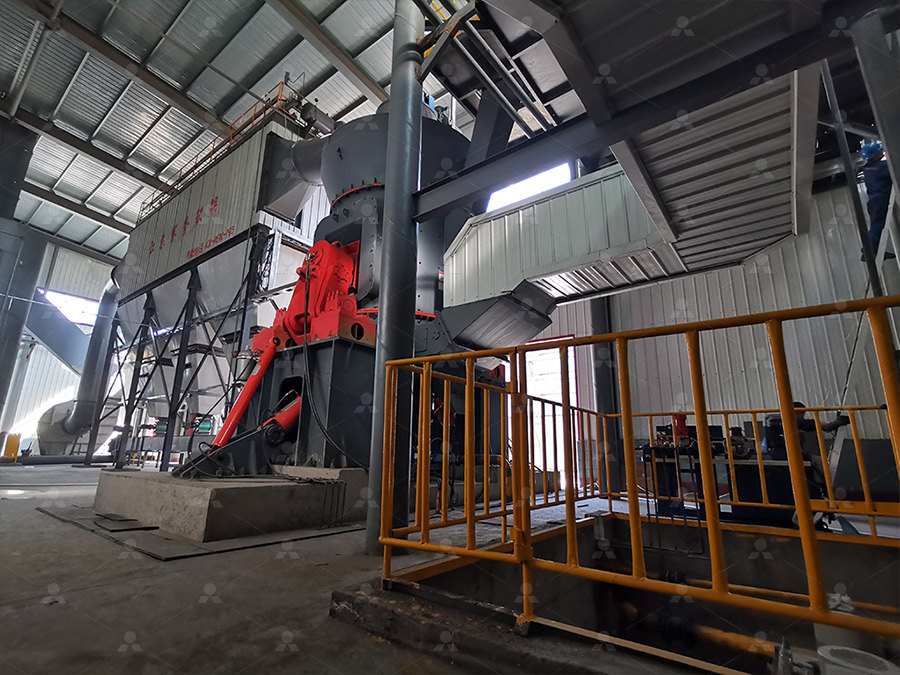
Grinding Parameters SpringerLink
2019年1月1日 The basic process parameters in grinding processes are the cutting speed v c, the feed velocity v f, the depth of cut a e, and the width of cut a p (see Fig 1, see also The new cement grinding process includes mixed material crushing, cement batching station, pregrinding, high fine grinding, fine powder separation, dust treatment, automatic control and other technologies, so that cement high yield, Cement Grinding Station Solution Ball Mill and 2024年1月18日 Plan and document processes Unclear processes lead to disengaged team members, low morale, and tasks that fall through the cracks Instead, mapping out your process gives your team a better understanding of What is process flow? Plus, how you can visualize itThe process is called a drying /grinding process, Actual heat input per ton required varies depending on: kiln feed chemical variations; kiln feed mass flow into the kiln; Oil temperature, pressure and flow rate are monitored by the Cement Manufacturing Process INFINITY FOR
.jpg)
Flow chart for different grinding process ResearchGate
Bovine skin was incubated with plant enzymes bromelain (B) and zingibain (Z) at the level of 0, 5, 10, 15, 20 and 25 unit/g of skin and gelatin was extracted at 60 °C for 6 h2024年11月24日 MTG Grinding Station: $1255 185 Tixes Card price last updated on 24 Nov Get the latest decks and the updated prices from multiple sources in our site≫ MTG Grinding Station decks and prices November 2024During a machining process with a trackbound cutting edge engagement, the cutting edge of the grain penetrates the workpiece upon a flat path and, after a phase of elastic deformation, triggers plastic flow of the workpiece material (Fig 3)Due to the shape of the cutting edge, the angle between the cutting edge contour and the workpiece surface is very small at the beginning of Grinding Process SpringerLinkThe machine is available in 25, 50 and 100 ton clamping forces The Cframe clamping unit is the most ergonomic for the operator, providing unobstructed access to their work area Rigid CFrame Parallel Die Opening, uniform die clamping, easy die access Smart Controls™ – Process control, with real time injection graphingMPI 55 Series CFrame with Smart Controls™ MPI Systems
.jpg)
Grinding SpringerLink
2022年2月28日 Generally, grinding process efficiency can mainly be improved by either improving the grinding behavior of the material being ground or enhancing the grinding machines Recently, the use of additives socalled grinding aids, which is applied in a small amount of 001–025 wt% related to the mass of product, has reduced these problems and been 2020年5月1日 Cement industry consumes a huge amount of electrical energy that is about 100 kWh/t (kWh per ton (10 3 kg) of cement) [16]In a cement plant, about twothirds of the total electrical energy is used for particle size reduction of raw materials and clinker [17]There is a diverse range of options to decrease the production expenses as well as CO 2 emissions that Energy and exergy analyses for a cement ball mill of a new Nevertheless, the process is relatively simple: locate or create (minimal) breaks in the stone, remove the stone using heavy machinery, secure the stone on a vehicle for transport, and move the material to storage A flow diagram of typical quarrying operations is shown in Figure 1 Figure 1 Process flow diagram for limestone quarrying operationsLimestone Quarrying and Processing: A LifeCycle InventoryThe FlowMatic® 07 big bag filling mobile station is the best solution for loading under multiple silos or hygienic processes requiring a complete wash down of the material loading areaThe mobile FlowMatic® 07 big bag filling station is Big bag filling FlowMatic 07 Palamatic Process
.jpg)
Cement Grinding Unit Cement Grinding Plant
AGICO Cement is a cement equipment manufacturer supplies EPC projects for cement grinding station with a simple process, easy operation, low The coarse powder is returned to the stable flow weighing bin the output is increased by 2016年3月21日 Pulp Densities Pulp densities indicate by means of a tabulation the percentages of solids (or liquidtosolid ratio) in a sample of pulp This figure is valuable in two ways—directly, because for each unit process and operation in Common Basic Formulas for Mineral Processing 2014年8月26日 The grinding fluid flow field was simulated and studied by using the volume of fluid multiphase flow model of FLUENT Hou ZB, Komanduri R (2003) On the mechanics of the grinding process–part I Stochastic nature of the grinding process Int J Mach Tools Manuf 43(15):1579–1593Modeling and simulation of useful fluid flow rate in grindingBag dump stations (also known as sack tip trays) are a very common piece of material handling equipment in production plants for various industries You may think that if you have seen one bag dump then you have seen them all One cannot be blamed for this, however, there is actually a fairly wide range of designs and functionalities when it comes to the simple need to unload How to choose a bag dump station in 4 easy questions
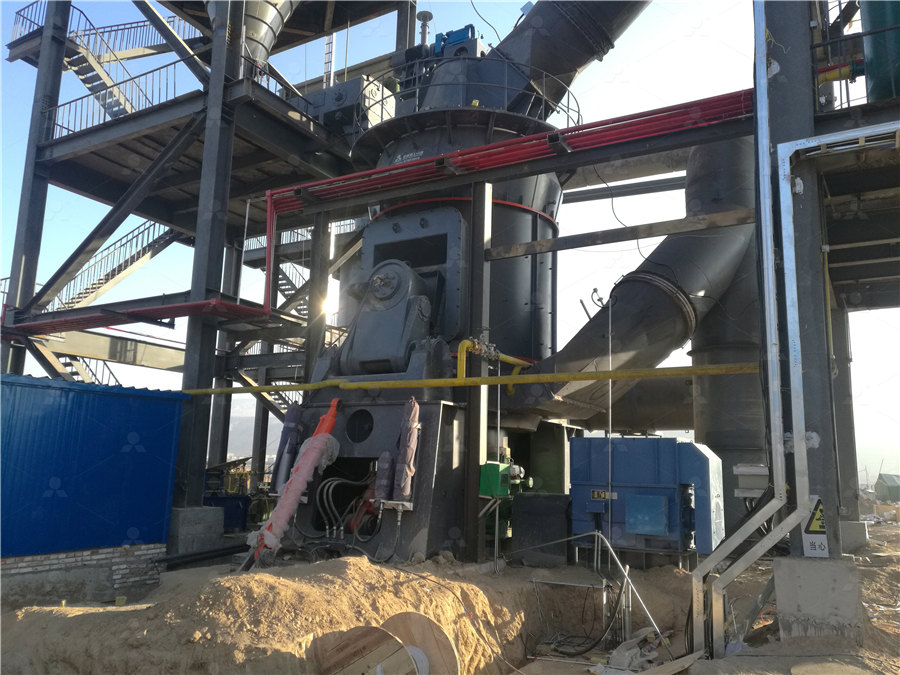
machinery ball mill for aluminium sulphate production 100 ton
2013年4月1日 Ball Mill Cost for 100 ton Cement Production 300~5000 ton per day cement clinker grinding plant alumina beneficiation cost and process – beltconveyers Below is some information about the products equipment, 3000 mt of Alumina per day2016年1月23日 With this flow configuration a large portion, approximately 70%, of the gold and silver dissolved in the grinding circuit will flow via the thickener overflow directly to the precipitation circuit The four 80 meter diameter x 85 meter high leach tanks are sized for a total retention time of 48 hours at 45% solidsGold Process Description 911MetallurgistThe process can also optimize the flow coefficient or improve the high and low cycle fatigue strength of certain pieces Process Abrasive Flow Machining works by the back and forth flow under pressure of an abrasive laden, viscoelastic compound or abrasive media, through a holding fixture and over the area to be polished, deburred and radiusedAbrasive Flow Machining Systems Winbro Flow GrindingRecently, the vertical roller mill having great grinding performance is widely applied to the raw material grinding process However, tube mill, which has about 30% poor grinding performance as power consumption, has been still used many existing cement plant The improvement of this tube mill grinding system is highly expected DescriptionsVertical roller mill for raw Application p rocess materials
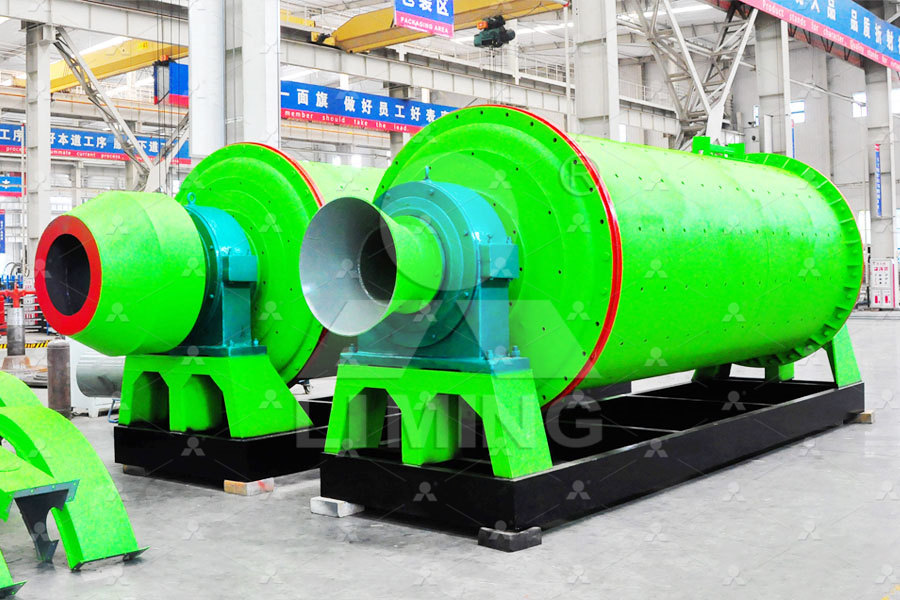
Gold Extraction Recovery Processes 911Metallurgist
2016年2月29日 Small miners employ this process due to alluvial deposits contain free gold, the process is fast and efficient, the final product has a high gold grade and recoveries are between 80 to 95%, commercialization is fast and simple without brokers, the process is simple and is not necessary a big investment or very special technical knowledge, the mercury can be reused If you're looking for a way to visualize your business processes and increase efficiency, process flow charts are a great tool to use These process diagrams show the steps of a process and help you identify areas where improvements Creating a Process Flow Chart: A StepbyStep GuideDownload scientific diagram Flow chart of grinding procedure from publication: Grinding Wheel Loading Evaluation by Using Acoustic Emission Signals and Digital Image Processing In the Flow chart of grinding procedure Download The base of the station is adapted to the installation of guards and a top extraction setEach version of the grinding and welding station consists of a working table with a top made of 8 mm thick metal sheet The guarded and Grinding and welding station SOG GPPH Group
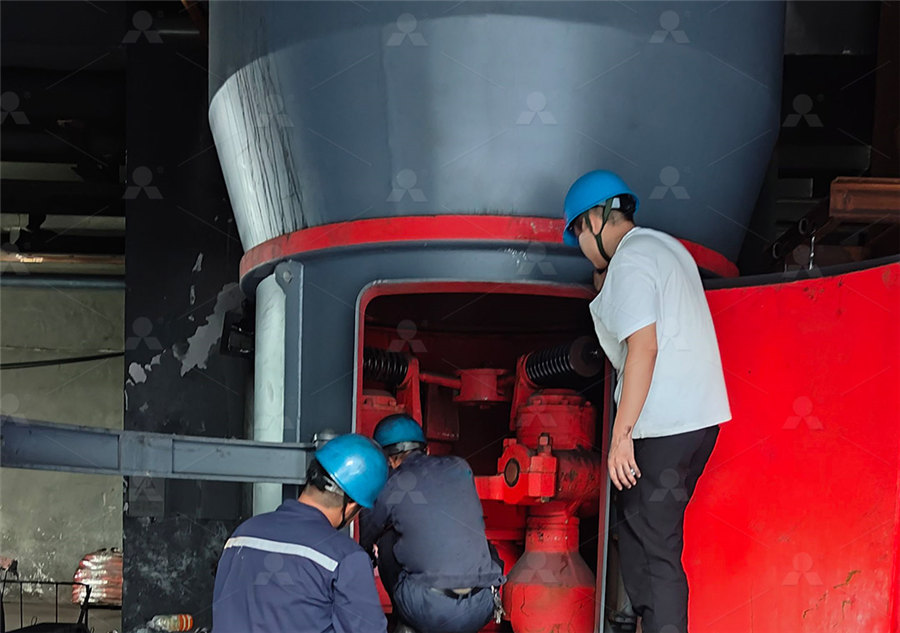
Grinding and welding station SOG GPPH Group
The base of the station is adapted to the installation of guards and a top extraction setEach version of the grinding and welding station consists of a working table with a top made of 8 mm thick metal sheet The guarded and top extraction versions of the sanding and welding workstation are equipped with hinged doors on both sides, making it practical to place larger Three flow patterns can occur in a bin: mass flow, funnel flow, and expanded flow In mass flow ( Figure 6a ), the entire bed of solids is in motion when material is discharged from the outlet This behavior prevents the formation of stagnant material and ratholes, affords a firstin/firstout flow sequence, and ensures a more uniform velocity profile during operationDesigning Hoppers, Bins, and Silos for Reliable Flow AIChE2009年1月1日 The design outcome is a process flowsheet that specifies the required equipment and their arrangements in the beneficiation plant The iron ore beneficiation plants normally include a series Processing of Magnetite Iron Ores–Comparing Grinding OptionsFinished parts are loaded on the exit conveyor Each grinding station is equipped with inprocess gaging to control the gear’s thickness According to Nagel, its SPV clamp bore gear grinder differs from conventional grinding operations Instead of depending on rigid fixturing as well as the accuracy of the grinding wheel’s position relativeClamp Bore Face Grinding and Honing Creates HigherQuality
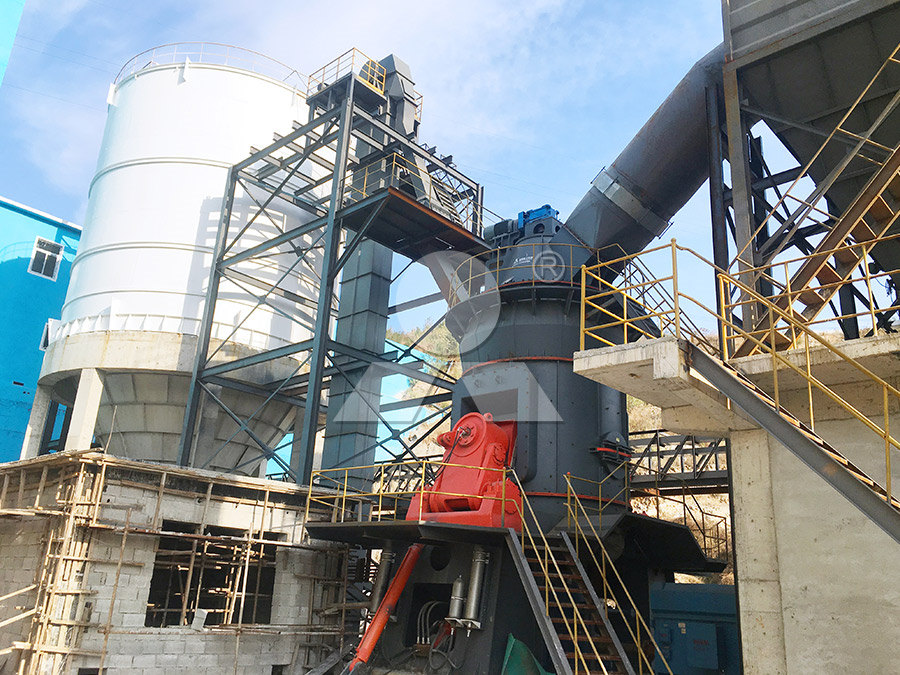
BALL MILLS Ball mill optimisation Holzinger Consulting
grinding process, its tools and optimisation possibilities (see Figure 1) The ball mill comminution process has a high electrical energy consumption, especially when those systems are in combination with first or secondgeneration classifiers This is particularly relevant in terms of the2020年2月1日 Request PDF Energy and exergy analyses for a cement ball mill of a new generation cement plant and optimizing grinding process: A case study Nowadays, ball mills are used widely in cement Energy and exergy analyses for a cement ball mill of a new The process design criteria define the project’s production requirements, and typically include those shown in Table 1 Table 1 Production requirements Process Description General Ore Characteristics Operating Schedule General Primary crushing Fines crushing Storage reclaim Maximum rock size in the feed Ore types, compressive strengthsCrushing Plant Design and Layout Considerations 911 Metallurgist2013年5月1日 Grinding, a complicated machining process which has been extensively studied and documented in order to understand the subtleties of the operation being performed in different methodologies and Influence of Process Parameters on Grinding A Review
.jpg)
Grinding Wheel Process Flow Diagram [classic] Creately
Grinding Wheel Process Flow Diagram [classic] by Matthew James Edit This Template Use Creately’s easy online diagram editor to edit this diagram, collaborate with others and export results to multiple image formats Edit This Template 2015年7月21日 This article discusses the range of application of ultrafine grinding for processing mineral raw materials and presents examples of the successful use of this technology in the concentration of polymetallic ores and the hydrometallurgy of gold A description is given of the principle of operation of bead mills and their main technological parameters (the size of the Ultrafine Grinding in Contemporary Flow Diagrams for Mineral 3 PALM OIL PROCESSING 3 1 General processing description Research and development work in many disciplines biochemistry, chemical and mechanical engineering and the establishment of plantations, which provided the opportunity for largescale fully mechanised processing, resulted in the evolution of a sequence of processing steps designed to extract, 3 PALM OIL PROCESSING Food and Agriculture OrganizationThe contained drum reconditioning unit integrates a big bag unhooking solution equipped with a glove box The biulk bag is placed on the unloading station by an electric hoist, which is controlled by the packaging operator The gravity discharge allows for a safe flow of the powder being handled For installation constraints, our design office can propose the implementation of Contained drum packaging from 1 ton bulk bags Palamatic Process
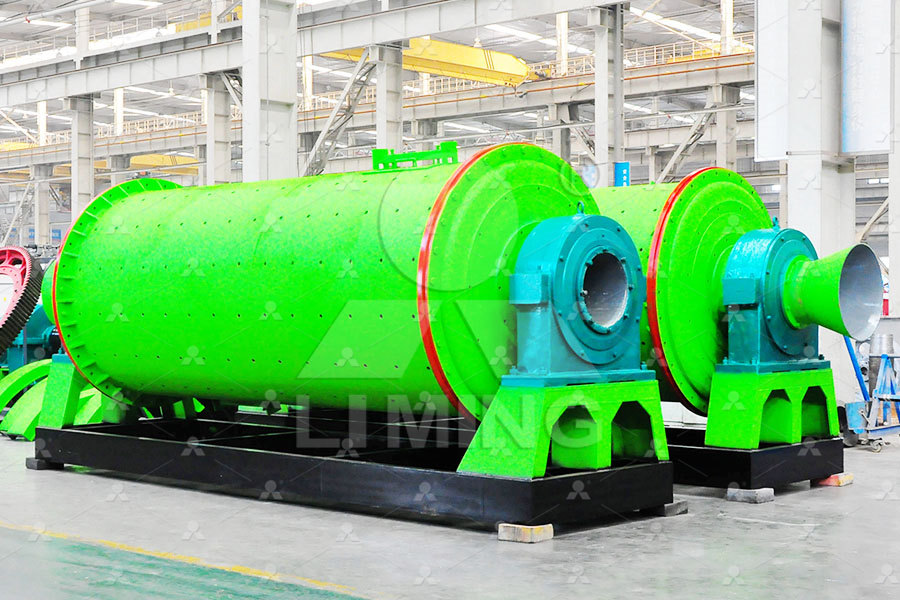
Modeling and Simulation of the Single Grain Grinding Process of
2014年7月11日 Modeling and Simulation of the Single Grain Grinding Process of the NanoParticle Jet Flow of Minimal Quantity Lubrication July 2014 The Open Materials Science Journal 8(1):5562Process flow CKP type Vertical roller grinding mill is mainly composed of motor, reducer, grinding disc, grinding roller, hydraulic device Jiangsu Pengfei Group EPC project Anhui wanwei annual output 2 million tons grinding station technical transformation Production process and main equipment of cement plantCKP vertical pregrinding mill911 Metallurgist can enter the scene and see what you have become blind to We can fix issues in ways you never thought possible Our fresh eyes will open new opportunities for your plant Each mineral processing plant has varied ore types, mining equipment, (crusher, ball mill, flotation, tailings), and management (operating) philosophyThe evaluation and prioritization of variables Metallurgists Mineral Processing Engineers 911Metallurgist2016年3月11日 By improved efficiency a decrease in energy consumption per ton of crude milled should be achieved Further savings resulting from finer crushing are realized in the concentration or mineral recovery phase of a process These benefits are rather difficult to quantify due to the varying complexities of the concentrators and benefication processesCrushing Plant Flowsheet DesignLayout 911Metallurgist
.jpg)
The six main steps of iron ore processing Multotec
Efficient grinding means that there will be minimal recirculation material from a cyclone cluster or screening after milling, which decreases the kWhr per ton ground This step involves the material being retained inside the mill for a specific time (with or without grinding balls) which is calculated by applying Bond’s work index to the process calculation