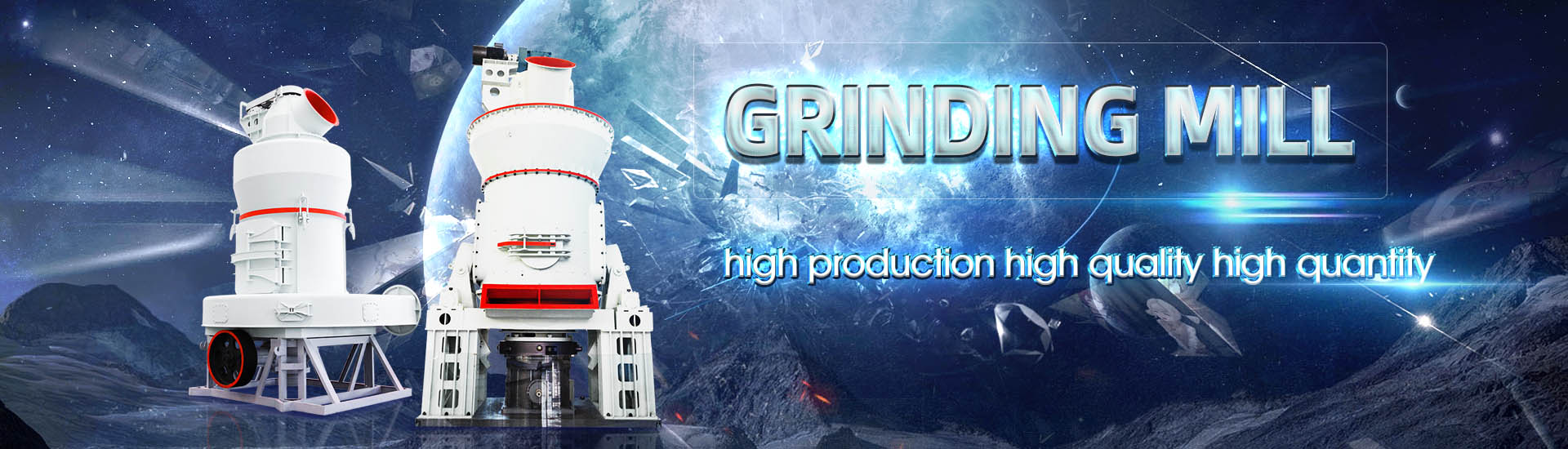
Process flow of slag iron processing equipment
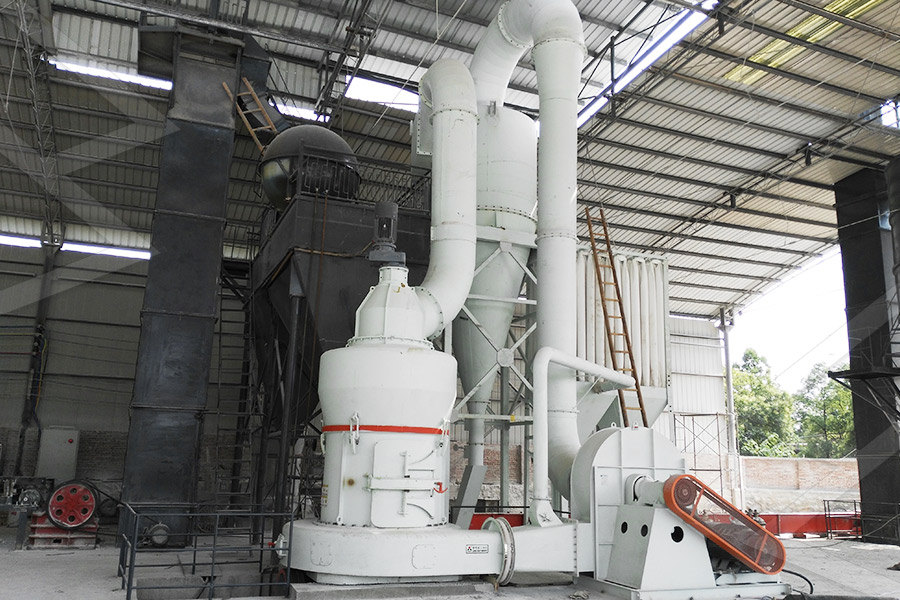
Development of the Complete Utilization Process of Steelmaking
Figure 1 illustrates our intended process Steelmaking slag is supplied to the reduction process along with carbon materials and slag modifiers The reduced slag is used in the same way as 2019年6月18日 Gravimetric, magnetic, floatation, pyrometallurgical and hydrometallurgical treatments are discussed for processing of charge chrome, steel, copper smelter, brass smelter, tin, incineration,(PDF) Metallurgical Processing Strategies for Metals Figure 7 and 8 the process flow diagram of a granulator and heat recovery system for superheated steam production is shown The process parameters shown in these figures are exemplary for aProcess flow diagram of a dry slag granulation system 2023年11月20日 Various studies have also suggested that the constituents present in steel slag can be recovered by three major approaches: (a) mechanical separation, (b) acid leaching, and (c) carbothermic reduction The process A Review on Environmental Concerns and
.jpg)
The potential utilization of slag generated from iron
2019年10月29日 The large volume production of slag from iron and steelmaking process and the tightened regulation on the slag disposal urge engineers and researchers to explore the way which can massively use the slag2005年2月1日 Environmental concerns and economic realities demand that slag production in iron and steelmaking processes can be reduced and that slag can be effectively utilized Discover the world's(PDF) Industrial uses of slag The use and reuse of iron 2014年1月1日 Iron and steelmaking has traditionally been based on linking a series of continuous and batch operations through proper scheduling of the feed/product transfer and Application of Slag Engineering Fundamentals to ScienceDirect2023年3月1日 In this study, chemical analysis, Xray diffraction, and scanning electron microscopy were used to analyze the changes in phase composition and morphology during Efficient separation of iron elements from steel slag based on
.jpg)
Iron and SteelMaking Process SpringerLink
2020年6月10日 The direct reduction process of iron oxide by solid carbon is highly endothermic in nature and occurs when the molten slag flows over incandescent coke in the bosh region at When iron ore is extracted from a mine, it must undergo several processing stages Six steps to process iron ore 1 Screening We recommend that you begin by screening the iron ore to separate fine particles below the crusher’s CSS The six main steps of iron ore processing Multotecheat recovery equipment such as CDQ (coke dry quenching) were constructed subsequently In this study, we propose combining a twin roll method for slag solidification and a packed bed method for heat exchange from slag to air in order to realize efficient recovery of the sensible heat of slag, which has low thermal conductivityDevelopment of Continuous Steelmaking Slag Solidification Process 2019年12月9日 Metallurgical slags are produced at a massive rate of over 750 Mt/year, and carry a thermal energy equivalent to 40 Mt/year of coal The potential mineral and thermal energy values of slags are in the order of $22 b and $3–6 b per year Such attractive figures, together with tightening legislation on disposal of slag and the carbon footprint associated with the loss Granulation and Heat Recovery from Metallurgical Slags
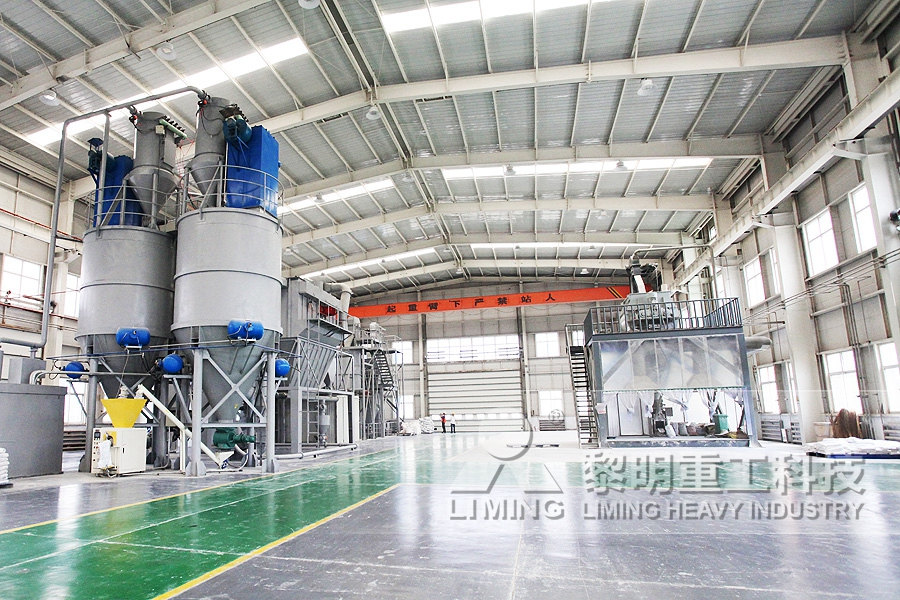
A Review on Environmental Concerns and Technological
2023年11月20日 Mineral process wastes, such as metallurgical slags nowadays, are of significant metals and materials resources in the circular economy The usability of ironmaking slag is well established; however, steel slag still needs to be utilized due to various physicochemical constraints In this context, we have reviewed the global steel slag 2023年9月4日 Jig machine: processing 30 (2)~05mm coarse iron ore; Shaking table: separating 2~0037mm fine iron ore particles; Spiral chute: processing 01037mm iron ore with low mud content 4 Iron ore dewatering equipment The iron ore mine dewatering operation divides into two parts: concentrate mine dewatering and tailings mine dewatering The Iron Ore Beneficiation Plant Equipment For Mining ProcessIn this regard, electric arc furnace (EAF) steel slag, ie, a waste product coming from the metallurgical processing generated during iron making, can be reused as highquality aggregate in Flowchart of iron and steelmaking processes [8] ResearchGate2024年4月1日 Carbon mineralization technology has emerged as a promising method for permanently sequestering CO 2 by transforming it into a thermodynamically stable solid carbonate material Recently, alkaline industrial waste, particularly from steel and ironmaking processes, has been identified as a proper feedstock due to its high potential for CO 2 storage and the Carbon mineralization of steel and ironmaking slag: Paving the
.jpg)
Modeling of LF refining process: a review Journal of Iron and
2023年11月15日 With the increasing demand for energy conservation and emission reduction, more attentions have been paid to the intelligentization, greenization and low carbonization during the transformation and upgrading of steelmaking plants Ladle furnace (LF) refining is one of the key procedures in steelmaking process and has been widely used in steelmaking plants for its 2023年11月8日 The process of titanium slag production is the process of smelting ilmenite concentrate in arc orethermal furnaces (OTF) in a semiclosed mode with the use of a powder mixture to obtain titanium slag of a specified content of iron oxide, as well as associated metalTitanium Slag Production Process: Technologies To Improve The iron ore production has significantly expanded in recent years, owing to increasing steel demands in developing countries However, the content of iron in ore deposits has deteriorated and lowgrade iron ore has been processed The fines resulting from the concentration process must be agglomerated for use in iron and steelmaking This chapter shows the status of the Iron Ore Pelletizing Process: An Overview IntechOpen3 Steelmaking Slag Processing Technology The iron/steel slag processing flow is schematically shown in Fig 2 Steelmaking slag is subjected to the following four processes: ① solidify and cooling of the hot molten slag, ② crushing and magnetic separation treatment of the slag to recover the metal iron,Processing and Reusing Technologies for Steelmaking Slag
.jpg)
RECOMMENDED GUIDELINE FOR IRON STEEL SECTOR
In the Furnace Hot Metal (along with slag) is processed from the raw materials ii) Cast House: In the Cast House, Hot Metal slag are tapped from the Furnace tap hole and after flowing through a system of refractory lined troughs / runners flow into Hot Metal Ladles / Torpedoes Slag Pots, placed on the iron slagQuebec Iron and Titanium (QIT Fer et Titane) in Sorel, Canada where coarse ilmenite is smelted to produce a highTiO2 slag and pig iron in similar furnaces This technology was adapted for RBM to process the fine ilmenite concentrate mined on the north coast of KwaZuluNatal5 The process generates very little in the way of waste productsHeavy Mineral Processing at Richards Bay Minerals SAIMM2019年5月23日 Li ZL, Li BS, Lü JF (2016) Current status and innovation of steel slag processing technology and equipment Mining Processing Equipment 44(2):1–6 Google Scholar Li BX, Wang YF, Zhong M (2016) Practice of producing superfine steel slag powder by ball milling double closed circuit process Cement Engineering 4:33–36Comprehensive Utilization Technology of Steel Slag2017年3月20日 With steady operation in a large furnace, the loss of iron in the slag should not exceed 4 per cent, of the total iron charged, depending on the amount of carbon desired in the product, but if a pig steel containing less than 025 per cent, carbon is produced there will probably be a greater loss of iron in the slagPig Iron Manufacturing Process 911Metallurgist
.jpg)
A literature review of titanium slag metallurgical processes
2012年1月1日 Basic procedure of ilmenite smelting and rational Ti slag grade in pyrometallurgical process have been summarized and analyzed The rational Ti slag grade is related to reduction degree, FeO 2024年3月17日 The main stages of the steel making process flow chart include iron ore extraction and processing, smelting in a blast furnace or electric arc furnace, primary steelmaking in a basic oxygen furnace or through electric arc refining, secondary metallurgy for quality control and adjustment, continuous casting, as well as the final rolling and finishing processesA Visual Guide: Steel Making Process Chart Cabaro Group2019年8月23日 Iron processing description from its geology mineral property to how to extract mineral from rock and placer deposit, related processing plant flow chart and layout design The price of the complete iron process plant or single iron equipment is varied by capacity, layout, raw material Contact us! Get a quick, Iron Processing Equipment, Process Flow, Cases JXSC Machine2021年11月11日 This processing plant is for the slag to recovery the Ferrochrome The process is as follows The wheel loader or excavator feeds the raw slag to the hopper There is an electromagnetic vibration feeder under the hopper, which can feed the material to the belt conveyor more evenly The client requires iron removal equipment to remove the big Fe Recycle Metal From Slag: The Recycling Process JXSC Machine
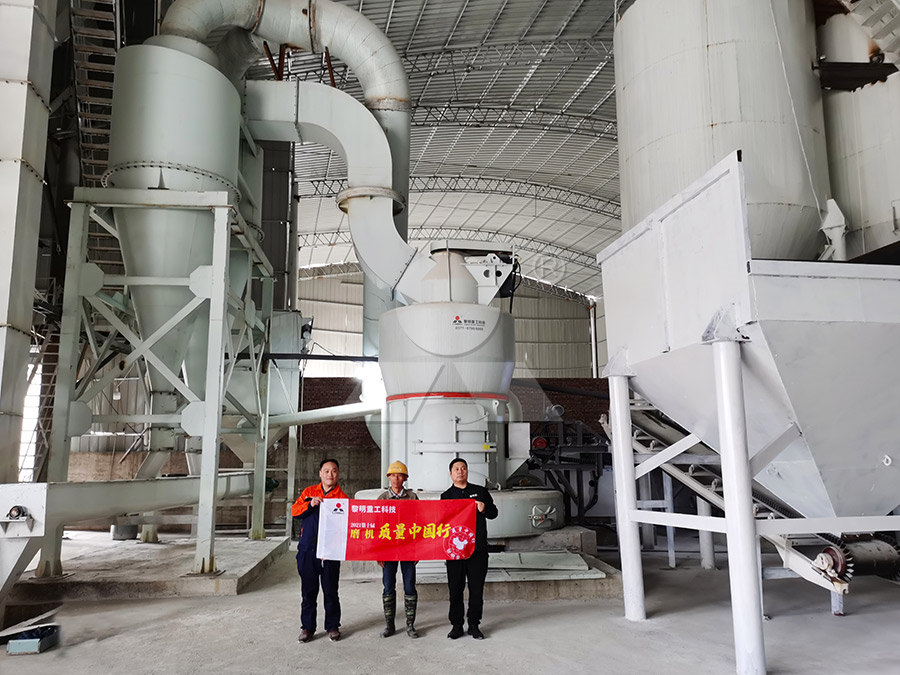
Direct reduced iron process tecscience
2018年6月21日 The direct reduced iron process and hydrogen (\(H2\)) are blown into the furnace at temperatures of approx 1000 °C and flow through the iron ores The reduction of iron oxides takes place according to (electric arc process) By turning the furnace, the slag can first be poured off and by turning it again in the other Process variables, factors and Process interaction Air flow rates; Kiln hot gases pass upward in countercurrent to fed meal flow The hot gases have vital role in controlling thermo chemical process These gases can be divided into two Cement Manufacturing Process INFINITY FOR Iron processing Smelting, Refining, Alloying: The primary objective of iron making is to release iron from chemical combination with oxygen, and, since the blast furnace is much the most efficient process, it receives the most attention Iron processing Smelting, Refining, Alloying2024年11月1日 Based on the above analysis, the following improvement suggestions were put forward: (1) In terms of electrode research, the use of inexpensive graphite electrodes had a good effect on steel slag treatment, and hightemperature ceramic electrodes and iron erosionresistant electrodes (ZrB 2) were gradually being exploited; (2) In terms of equipment, the existing Recent research progress on recycling metallurgical waste slag
.jpg)
Modelling copper smelting – the flash smelting plant, process
2019年11月12日 Request PDF Modelling copper smelting – the flash smelting plant, process and equipment The effectivity of present copper smelting technologies have their roots in industrial and laboratory offer technology and equipment for the entire nickel and cobalt production chain from mine to metal, with a project scope ranging from equipment packages to turnkey plant delivery We have several processing alternatives for nickel and cobalt raw materials, ranging from pyrometallurgical to hydrometallurgical approachesHydrometallurgical nickel and cobalt plants and processes2023年9月8日 solutions have been proposed for the blast furnace, for example, hig hly oxygenenriched or hydrogenrich operationBlast Furnace process optimization for sustainable Iron making2017年1月7日 Flow chart of dry granulation and waste heat recovery process for slag developed by Central Iron Steel Research Institute (CISRI) Figures available via license: Creative Commons Attribution (PDF) Process and Equipment Design for the Dry Slag
.jpg)
Copper Mining and Processing: Processing Copper Ores
Copper processing is a complicated process that begins with mining of the ore (less than 1% copper) and ends with sheets of 9999% pure copper called cathodes, which will ultimately be made into products for everyday useThe most common types of ore, copper oxide and copper sulfide, undergo two different processes, hydrometallurgy and pyrometallurgy, respectively, The reject of waste recycling plant (WRP) ie LD Slag fines (0 6 mm) after metal recovery does not contain much of metallic iron, but this contains substantial quantity of calcium bearing Flow diagram of processing of LD slag in Waste Recycling plant process begins with drilling a hole, called the taphole, into the clayfilled iron notch at the base of the hearth During casting, molten iron flows into runners that lead to transport ladles Slag also flows into the clayfilled iron notch at the base of the hearth During casting, molten iron flows into runners that lead to transport ladles125 Iron And Steel Production US EPASteelmaking slag, or steel slag, is a byproduct from the production of steel during the conversion of hot metal to crude steel in a basic oxygen furnace, or during the melting of scrap in an EAFThe slag is generated as a melt and is a complex solution of silicates and oxides that solidify upon cooling 11 Depending on the specific steel production process, three different types of steel Steelmaking Slag an overview ScienceDirect Topics
.jpg)
(PDF) ironsteel making From start to finish
PDF On Dec 27, 2019, Mr Bhavesh R Rana published ironsteel making From start to finish Find, read and cite all the research you need on ResearchGate2016年2月29日 Slag appearance is a good indicator of the process Although iron minerals have influence on color slag, it is possible to draw some conclusions according to the color For example, a blue color is symptom of copper Gold Smelting Refining Process 911MetallurgistPDF On Jul 11, 2018, Sandra Lúcia de Moraes and others published Iron Ore Pelletizing Process: An Overview Find, read and cite all the research you need on ResearchGateIron Ore Pelletizing Process: An Overview ResearchGate2019年10月29日 Along with iron and steel production, large amount of slag is generated Proper management on the iron and steelmaking slag is highly demanded due to the high cost of direct disposal of the slag to landfill, which is the most adopted management approach In this article, the potential application of iron and steelmaking slag has been reviewed, which included the The potential utilization of slag generated from iron and
.jpg)
Blast Furnace Process an overview ScienceDirect Topics
Slag and iron are separated in the main trough, where the melts settle, iron flows under the skimmer stone and slag stands behind the skimmer stone and is directed to granulating device or slag pit The hot metal flows through the skimmer, which separates the slag from the hot metal to ladles or torpedo cars to be transported to hot metal treatment (eg, desulfurization) and hot 2011年10月27日 EAF Slag Process The BOS process needs to be fed with molten iron, whereas the Electric Arc Furnace (EAF) can operate with a feed consisting partly or entirely of solid metal such as scrap This gives rise to two significant differences in the slag, which is otherwise fairly similar in chemical compositionBasics of slag production Article on the slag industry from Global Slag2015年2月5日 The combination of (1) sustainable supply of biomass and its processing to produce charcoal, biooil and other renewable energy; (2) utilisation of charcoal as partial replacement for coal and coke products in ironmaking and steelmaking; (3) recovery of highgrade waste heat from molten slag and (4) conversion of molten BF slag into a Portland cement Development of LowEmission Integrated Steelmaking Process2022年10月20日 Iron ore handling, which may account for 20–50% of the total delivered cost of raw materials, covers the processes of transportation, storage, feeding, and washing of the ore en route to or during its various stages of treatment in the mill Since the physical state of iron ores in situ may range from friable, or even sandy materials, to monolithic deposits with hardness of Iron Ore Processing, General SpringerLink
.jpg)
Dry slag granulation: producing valuable byproducts from waste
By converting low value aircooled blast furnace slag into a high value material for the cement/construction industry, this process turns a waste product into wealth We are partnering with Beijing MCC Equipment Research Design Corporation (MCCE) to commercialise the dry slag granulation technology